Page 833 of 1463
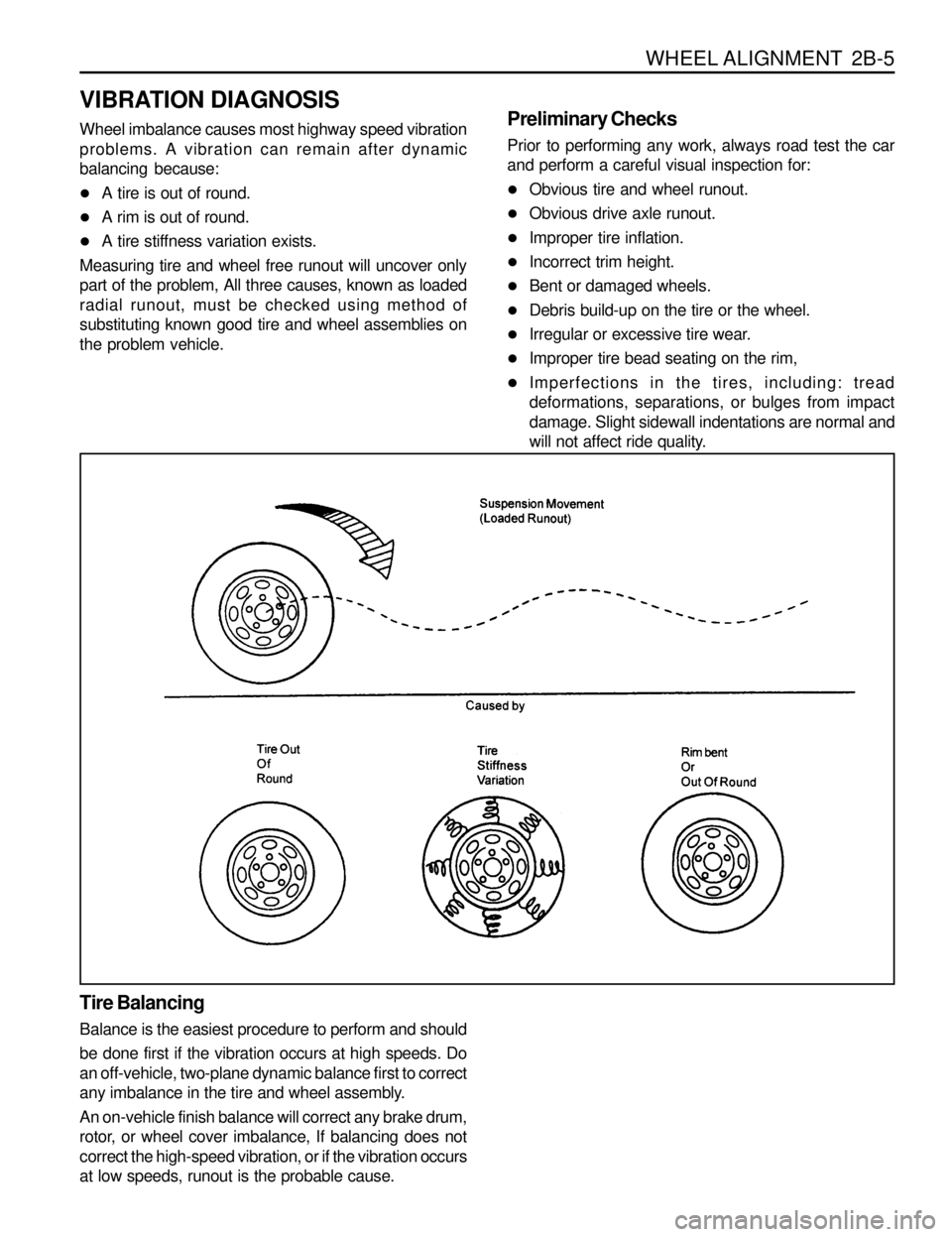
WHEEL ALIGNMENT 2B-5
VIBRATION DIAGNOSIS
Wheel imbalance causes most highway speed vibration
problems. A vibration can remain after dynamic
balancing because:
lA tire is out of round.
lA rim is out of round.
lA tire stiffness variation exists.
Measuring tire and wheel free runout will uncover only
part of the problem, All three causes, known as loaded
radial runout, must be checked using method of
substituting known good tire and wheel assemblies on
the problem vehicle.
Preliminary Checks
Prior to performing any work, always road test the car
and perform a careful visual inspection for:
lObvious tire and wheel runout.
lObvious drive axle runout.
lImproper tire inflation.
lIncorrect trim height.
lBent or damaged wheels.
lDebris build-up on the tire or the wheel.
lIrregular or excessive tire wear.
lImproper tire bead seating on the rim,
lImperfections in the tires, including: tread
deformations, separations, or bulges from impact
damage. Slight sidewall indentations are normal and
will not affect ride quality.
Tire Balancing
Balance is the easiest procedure to perform and should
be done first if the vibration occurs at high speeds. Do
an off-vehicle, two-plane dynamic balance first to correct
any imbalance in the tire and wheel assembly.
An on-vehicle finish balance will correct any brake drum,
rotor, or wheel cover imbalance, If balancing does not
correct the high-speed vibration, or if the vibration occurs
at low speeds, runout is the probable cause.
Page 834 of 1463
2B-6 WHEEL ALIGNMENT
MAINTENANCE AND REPAIR
ON VEHICLE SERVICE
WHEEL ALIGNMENT
Vehicle Height
1. Check the tire for proper inflation.
2. Measure ‘A’ from the center of the lower arm rear mounting
bolt end to the ground.
3. Measure ‘B’ from the center of the steering knuckle shaft to
the ground.
4. If the difference between ‘A’ and ‘B’ is not within specification,
adjust vehicle height using torsion bar height control bolt.
‘B’ - ‘A’
Notice
Before wheel alignment, adjust vehicle height first.
31 - 36mm
Toe-in
1. Measure toe-in.
Specification0 - 4mm
2. If toe-in is not within specification, loosen the tie rod nuts
and adjust it by turning the tie rod.
Page 835 of 1463
WHEEL ALIGNMENT 2B-7
Camber
1. Remove the free wheel hub.
2. Measure camber with a wheel alignment equipment.
3. If camber measurements are not within specification, adjust
it by increasing or decreasing the number of adjusting shims
(1) inserted between the upper arm shaft and cross bracket.
Camber Change
Notice
Difference between the left and right should be adjusted
within 30’.
Specification0°±30’
Caster
1. Remove the free wheel hub.
2. Measure caster with a wheel alignment equipment and a
turning radius gauge.
Specification2° 30’ ± 30’
Adjusting Shims
1.6 Iarge
3.2 largeIncreasing 1 ea
+ 19’
+ 38’Decreasing 1 ea
- 19’
- 38’
Page 836 of 1463
2B-8 WHEEL ALIGNMENT
Increasing 1ea
- 11’
- 43’
3. If caster measurements are not within specification, adjust
it by increasing 1ea (rear) or decreasing 1ea (front).
Caster Change
Notice
Difference between the left and right should be adjusted
within 30’.
0.4 small
1.6 small
Decreasing 1ea
+ 11’
+ 43’
FRONT
Adjusting Shims
Increasing 1ea
+ 11’
+ 43’ 0.4 small
1.6 small
Decreasing 1ea
- 11’
- 43’
REAR
Adjusting Shims
Page 837 of 1463
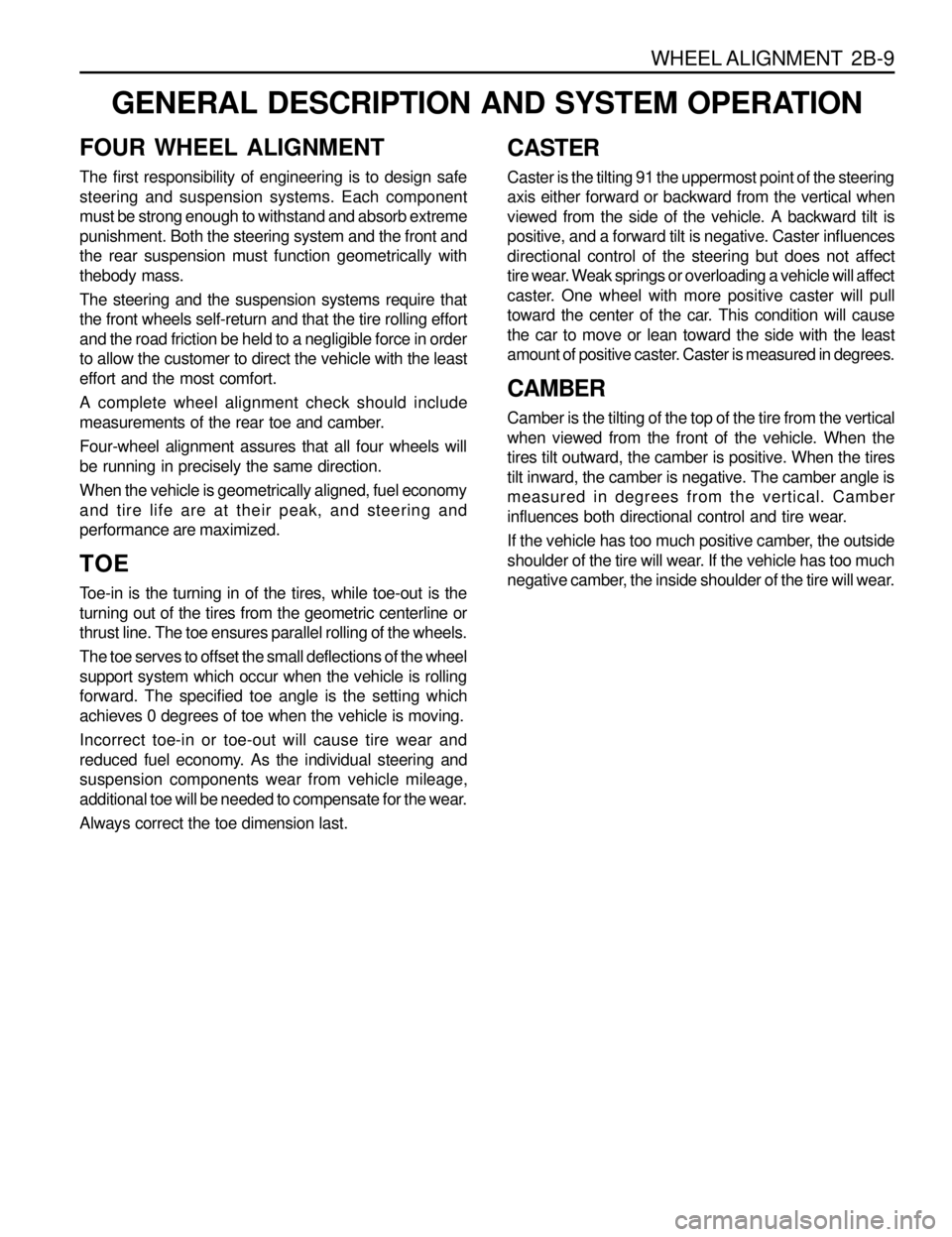
WHEEL ALIGNMENT 2B-9
GENERAL DESCRIPTION AND SYSTEM OPERATION
FOUR WHEEL ALIGNMENT
CASTER
Caster is the tilting 91 the uppermost point of the steering
axis either forward or backward from the vertical when
viewed from the side of the vehicle. A backward tilt is
positive, and a forward tilt is negative. Caster influences
directional control of the steering but does not affect
tire wear. Weak springs or overloading a vehicle will affect
caster. One wheel with more positive caster will pull
toward the center of the car. This condition will cause
the car to move or lean toward the side with the least
amount of positive caster. Caster is measured in degrees.
CAMBER
Camber is the tilting of the top of the tire from the vertical
when viewed from the front of the vehicle. When the
tires tilt outward, the camber is positive. When the tires
tilt inward, the camber is negative. The camber angle is
measured in degrees from the vertical. Camber
influences both directional control and tire wear.
If the vehicle has too much positive camber, the outside
shoulder of the tire will wear. If the vehicle has too much
negative camber, the inside shoulder of the tire will wear. The first responsibility of engineering is to design safe
steering and suspension systems. Each component
must be strong enough to withstand and absorb extreme
punishment. Both the steering system and the front and
the rear suspension must function geometrically with
thebody mass.
The steering and the suspension systems require that
the front wheels self-return and that the tire rolling effort
and the road friction be held to a negligible force in order
to allow the customer to direct the vehicle with the least
effort and the most comfort.
A complete wheel alignment check should include
measurements of the rear toe and camber.
Four-wheel alignment assures that all four wheels will
be running in precisely the same direction.
When the vehicle is geometrically aligned, fuel economy
and tire life are at their peak, and steering and
performance are maximized.
TOE
Toe-in is the turning in of the tires, while toe-out is the
turning out of the tires from the geometric centerline or
thrust line. The toe ensures parallel rolling of the wheels.
The toe serves to offset the small deflections of the wheel
support system which occur when the vehicle is rolling
forward. The specified toe angle is the setting which
achieves 0 degrees of toe when the vehicle is moving.
Incorrect toe-in or toe-out will cause tire wear and
reduced fuel economy. As the individual steering and
suspension components wear from vehicle mileage,
additional toe will be needed to compensate for the wear.
Always correct the toe dimension last.
Page 838 of 1463
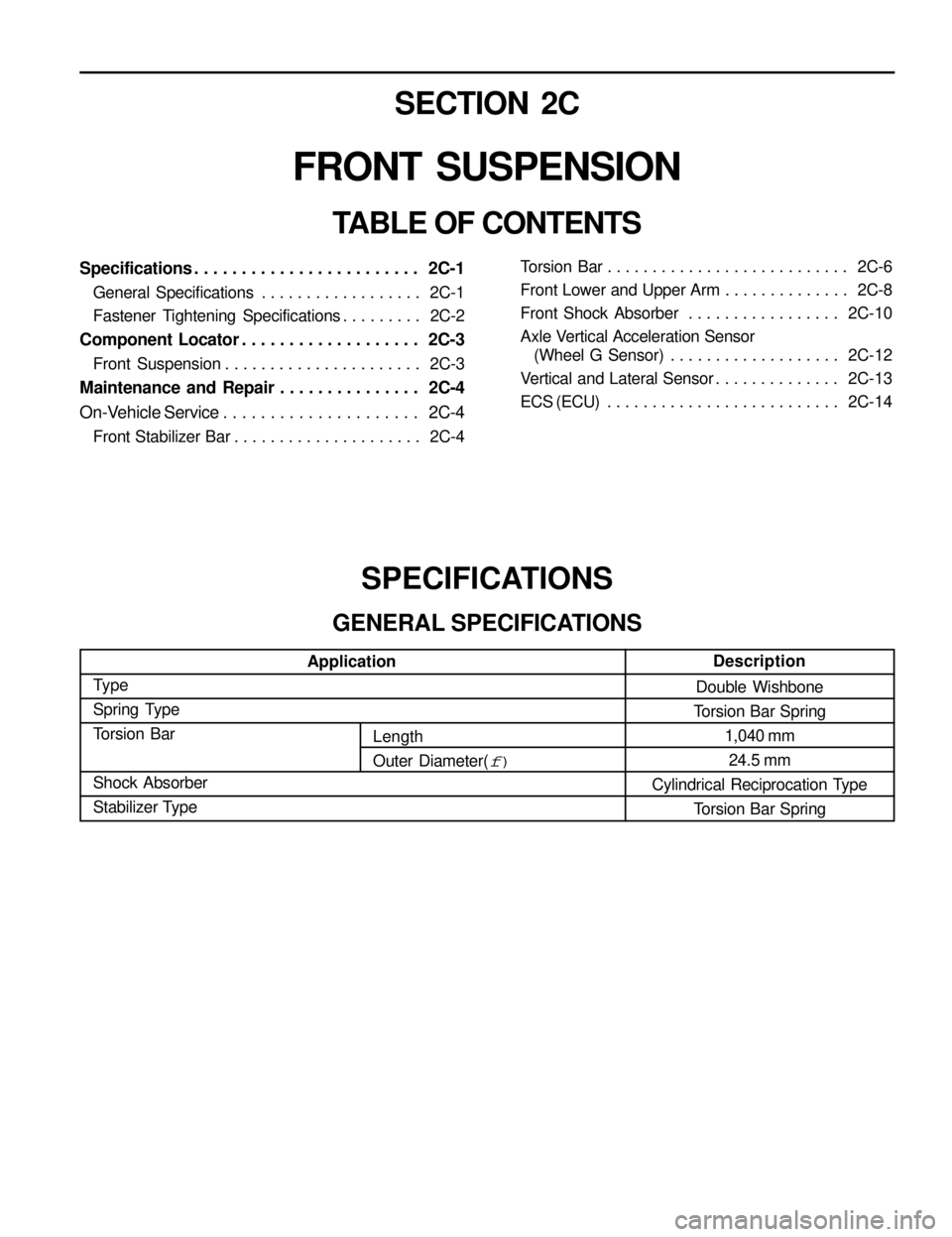
SECTION 2C
FRONT SUSPENSION
TABLE OF CONTENTS
SPECIFICATIONS
GENERAL SPECIFICATIONS
Type
Spring Type
Torsion Bar
Shock Absorber
Stabilizer TypeDouble Wishbone
Torsion Bar Spring
1,040 mm
24.5 mm
Cylindrical Reciprocation Type
Torsion Bar Spring
Specifications . . . . . . . . . . . . . . . . . . . . . . . . 2C-1
General Specifications . . . . . . . . . . . . . . . . . . 2C-1
Fastener Tightening Specifications . . . . . . . . . 2C-2
Component Locator . . . . . . . . . . . . . . . . . . . 2C-3
Front Suspension . . . . . . . . . . . . . . . . . . . . . . 2C-3
Maintenance and Repair . . . . . . . . . . . . . . . 2C-4
On-Vehicle Service . . . . . . . . . . . . . . . . . . . . . 2C-4
Front Stabilizer Bar . . . . . . . . . . . . . . . . . . . . . 2C-4
ApplicationDescription Torsion Bar . . . . . . . . . . . . . . . . . . . . . . . . . . . 2C-6
Front Lower and Upper Arm . . . . . . . . . . . . . . 2C-8
Front Shock Absorber . . . . . . . . . . . . . . . . . 2C-10
Axle Vertical Acceleration Sensor
(Wheel G Sensor) . . . . . . . . . . . . . . . . . . . 2C-12
Vertical and Lateral Sensor . . . . . . . . . . . . . . 2C-13
ECS (ECU) . . . . . . . . . . . . . . . . . . . . . . . . . . 2C-14
Length
Outer Diameter(
f)
Page 839 of 1463
2C-2 FRONT SUSPENSION
Application
Torque Arm BoltNlm
40 - 60
60 - 80
FASTENER TIGHTENING SPECIFICATIONS
Stabilizer Bar
Application
Stabilizer Bar Retaining Nut
Stabilizer Bar Link Nut
Lower Arm NutNlm
30 - 45
60 - 80
16 - 22
Torsion Bar
Lower and Upper Arm
Application
Upper Arm Nut
Upper Arm End Castle Nut
Lower Arm Nut
Lower Arm End Castle NutNlm
120 - 140
80 - 150
150 - 180
120 - 180
Steering Knuckle and Drive Shaft
Application
Brake Caliper Hose Bolt
Brake Caliper Mounting Bolt
Tie Rod Retaining Nut
Upper Arm Retaining Nut
Lower Arm Retaining NutNlm
25 - 35
85 - 105
35 - 45
80 - 150
120 - 180
M10
M12
Page 840 of 1463
FRONT SUSPENSION 2C-3
COMPONENT LOCATOR
FRONT SUSPENSION
1 Shock Absorber
2 Upper Arm
3 Steering Knuckle
4 Lower Arm5 Stabilizer Bar Link
6 Stabilizer Bar
7 Suspension Bumper