Page 1049 of 1463
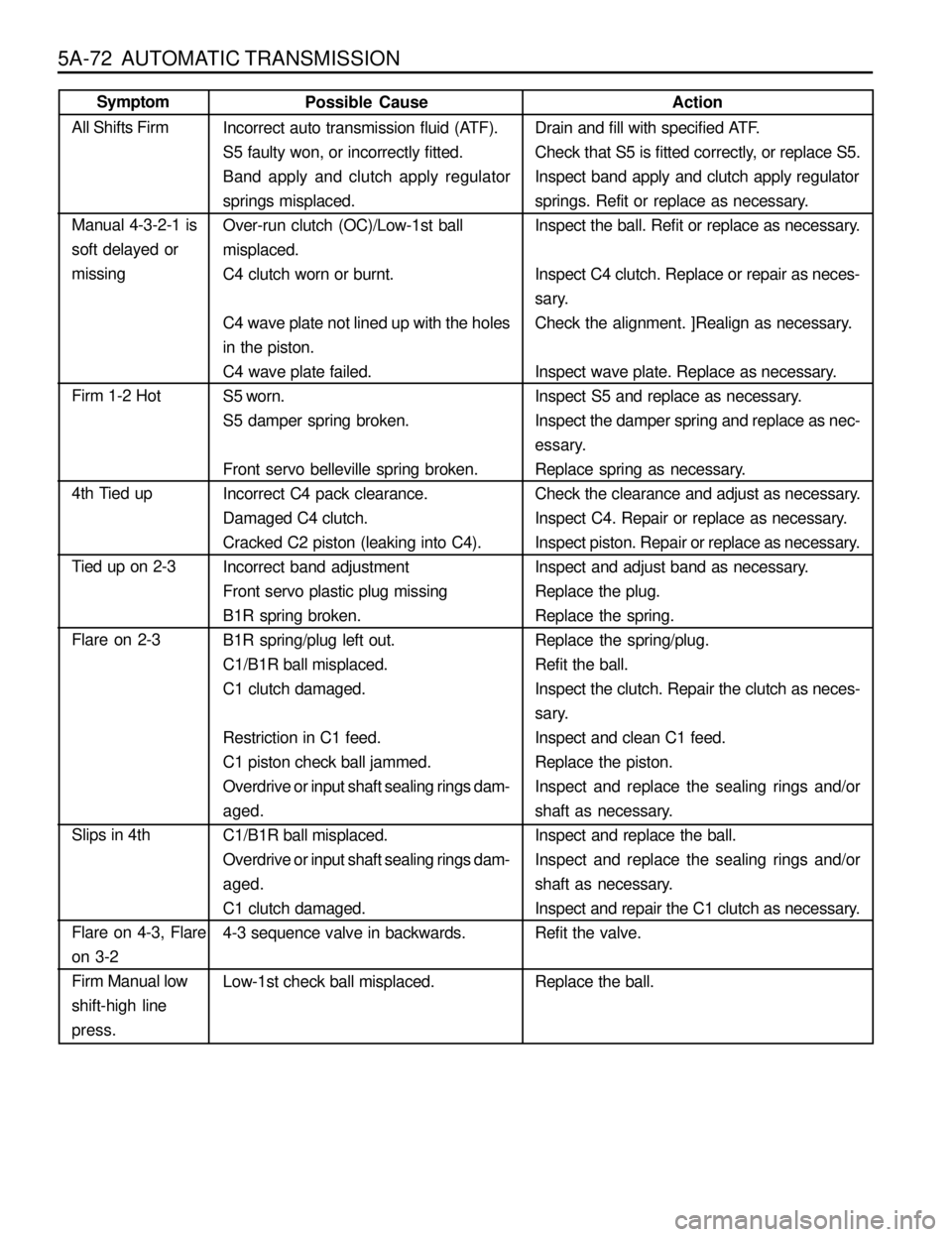
5A-72 AUTOMATIC TRANSMISSION
Action
Drain and fill with specified ATF.
Check that S5 is fitted correctly, or replace S5.
Inspect band apply and clutch apply regulator
springs. Refit or replace as necessary.
Inspect the ball. Refit or replace as necessary.
Inspect C4 clutch. Replace or repair as neces-
sary.
Check the alignment. ]Realign as necessary.
Inspect wave plate. Replace as necessary.
Inspect S5 and replace as necessary.
Inspect the damper spring and replace as nec-
essary.
Replace spring as necessary.
Check the clearance and adjust as necessary.
Inspect C4. Repair or replace as necessary.
Inspect piston. Repair or replace as necessary.
Inspect and adjust band as necessary.
Replace the plug.
Replace the spring.
Replace the spring/plug.
Refit the ball.
Inspect the clutch. Repair the clutch as neces-
sary.
Inspect and clean C1 feed.
Replace the piston.
Inspect and replace the sealing rings and/or
shaft as necessary.
Inspect and replace the ball.
Inspect and replace the sealing rings and/or
shaft as necessary.
Inspect and repair the C1 clutch as necessary.
Refit the valve.
Replace the ball. Possible Cause
Incorrect auto transmission fluid (ATF).
S5 faulty won, or incorrectly fitted.
Band apply and clutch apply regulator
springs misplaced.
Over-run clutch (OC)/Low-1st ball
misplaced.
C4 clutch worn or burnt.
C4 wave plate not lined up with the holes
in the piston.
C4 wave plate failed.
S5 worn.
S5 damper spring broken.
Front servo belleville spring broken.
Incorrect C4 pack clearance.
Damaged C4 clutch.
Cracked C2 piston (leaking into C4).
Incorrect band adjustment
Front servo plastic plug missing
B1R spring broken.
B1R spring/plug left out.
C1/B1R ball misplaced.
C1 clutch damaged.
Restriction in C1 feed.
C1 piston check ball jammed.
Overdrive or input shaft sealing rings dam-
aged.
C1/B1R ball misplaced.
Overdrive or input shaft sealing rings dam-
aged.
C1 clutch damaged.
4-3 sequence valve in backwards.
Low-1st check ball misplaced.Symptom
All Shifts Firm
Manual 4-3-2-1 is
soft delayed or
missing
Firm 1-2 Hot
4th Tied up
Tied up on 2-3
Flare on 2-3
Slips in 4th
Flare on 4-3, Flare
on 3-2
Firm Manual low
shift-high line
press.
Page 1050 of 1463
AUTOMATIC TRANSMISSION 5A-73
Table 6.2.3 - Shift Quality Faults
Action
Check the resistance. Replace the inhibitor
switch as necessary.
Inspect and replace the sensor as necessary.
Inspect and adjust the band as necessary.
Inspect and replace the’0’rings as necessary.
Inspect, repair or replace S5 as necessary.
Inspect, repair or replace S1 or S4 as neces-
sary.
Inspect, repair or replace the BAR as neces-
sary.
Inspect and repair as necessary.
Inspect and clean CCCV.
Inspect, repair or replace as necessary. Possible Cause
Faulty inhibitor switch.
Faulty throttle position sensor.
Incorrect front band adjustment.
Damaged front servo piston’0’rings.
Faulty or damaged variable pressure so-
lenoid (S5).
Faulty S1 or S4 solenoid.
Faulty band apply regulator valve (BAR).
Misassembled front servo return spring.
Jammed converter clutch control valve
(CCCV).
Faulty solenoid 7.Symptom
Harsh 1-2 shift
stalls when Drive
or Reverse
selected Shudder
on Rolldown
Page 1051 of 1463
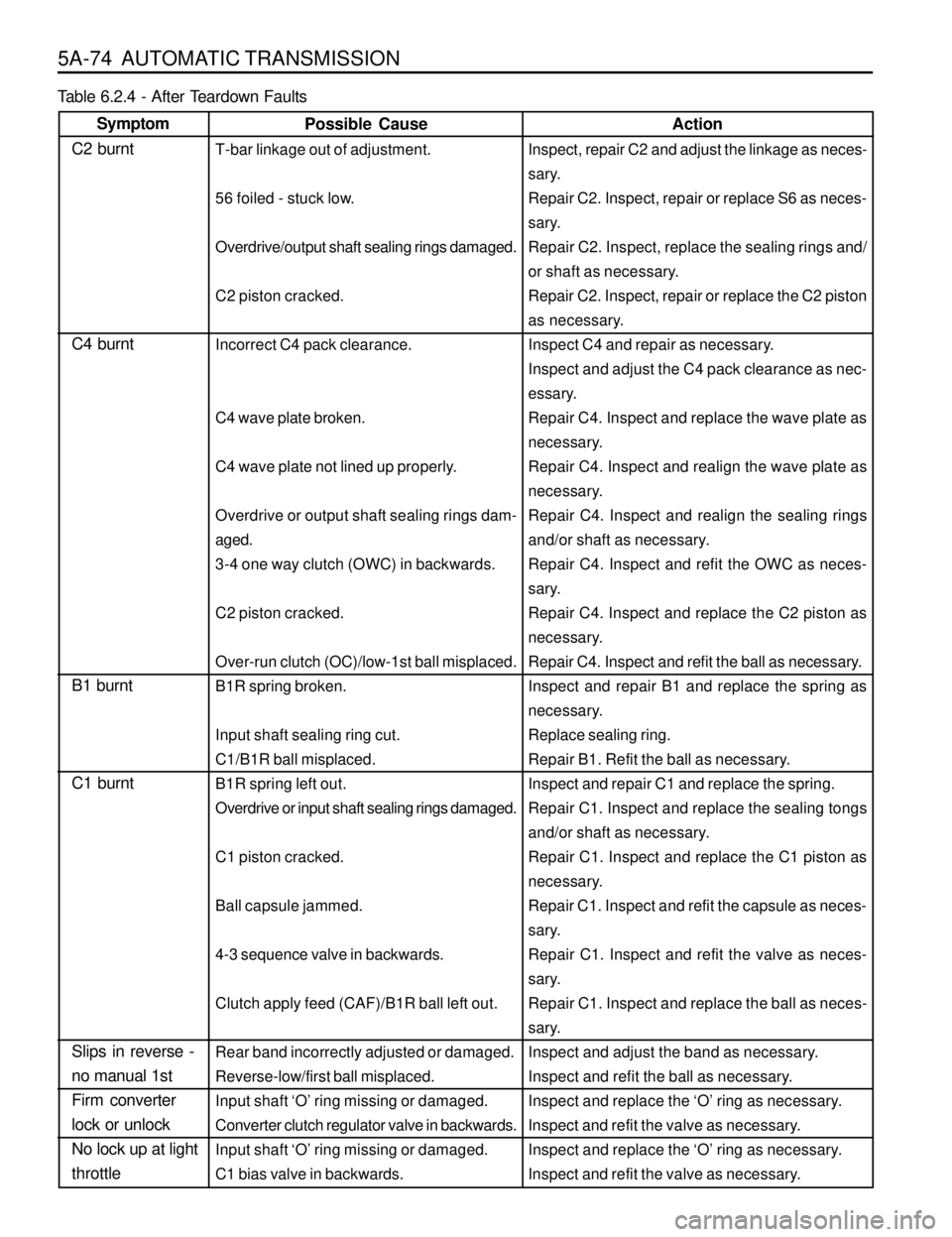
5A-74 AUTOMATIC TRANSMISSION
Action
Inspect, repair C2 and adjust the linkage as neces-
sary.
Repair C2. Inspect, repair or replace S6 as neces-
sary.
Repair C2. Inspect, replace the sealing rings and/
or shaft as necessary.
Repair C2. Inspect, repair or replace the C2 piston
as necessary.
Inspect C4 and repair as necessary.
Inspect and adjust the C4 pack clearance as nec-
essary.
Repair C4. Inspect and replace the wave plate as
necessary.
Repair C4. Inspect and realign the wave plate as
necessary.
Repair C4. Inspect and realign the sealing rings
and/or shaft as necessary.
Repair C4. Inspect and refit the OWC as neces-
sary.
Repair C4. Inspect and replace the C2 piston as
necessary.
Repair C4. Inspect and refit the ball as necessary.
Inspect and repair B1 and replace the spring as
necessary.
Replace sealing ring.
Repair B1. Refit the ball as necessary.
Inspect and repair C1 and replace the spring.
Repair C1. Inspect and replace the sealing tongs
and/or shaft as necessary.
Repair C1. Inspect and replace the C1 piston as
necessary.
Repair C1. Inspect and refit the capsule as neces-
sary.
Repair C1. Inspect and refit the valve as neces-
sary.
Repair C1. Inspect and replace the ball as neces-
sary.
Inspect and adjust the band as necessary.
Inspect and refit the ball as necessary.
Inspect and replace the ‘O’ ring as necessary.
Inspect and refit the valve as necessary.
Inspect and replace the ‘O’ ring as necessary.
Inspect and refit the valve as necessary.
Possible Cause
T-bar linkage out of adjustment.
56 foiled - stuck low.
Overdrive/output shaft sealing rings damaged.
C2 piston cracked.
Incorrect C4 pack clearance.
C4 wave plate broken.
C4 wave plate not lined up properly.
Overdrive or output shaft sealing rings dam-
aged.
3-4 one way clutch (OWC) in backwards.
C2 piston cracked.
Over-run clutch (OC)/low-1st ball misplaced.
B1R spring broken.
Input shaft sealing ring cut.
C1/B1R ball misplaced.
B1R spring left out.
Overdrive or input shaft sealing rings damaged.
C1 piston cracked.
Ball capsule jammed.
4-3 sequence valve in backwards.
Clutch apply feed (CAF)/B1R ball left out.
Rear band incorrectly adjusted or damaged.
Reverse-low/first ball misplaced.
Input shaft ‘O’ ring missing or damaged.
Converter clutch regulator valve in backwards.
Input shaft ‘O’ ring missing or damaged.
C1 bias valve in backwards.
Symptom
C2 burnt
C4 burnt
B1 burnt
C1 burnt
Slips in reverse -
no manual 1st
Firm converter
lock or unlock
No lock up at light
throttle
Table 6.2.4 - After Teardown Faults
Page 1052 of 1463
AUTOMATIC TRANSMISSION 5A-75
SELF DIAGNOSIS TEST
1. Turn the ignition switch to “OFF” position.
2. Connect the scanner harness connector to the engine
compartment diagnosis socket.
3. Turn the ignition switch to “ON” position.
4. Select “Electronics control vehicle diagnosis” from the
function selection display and press “Enter”.
5. Select “Musso(98 face lift)” from the vehicle model selection
model selection display and press “Enter”.
6. Select “Transmission control unit(TCU)” from the control
system selection and press “Enter”.
7. Select “Self-diagnosis” from diagnosis items.
Notice
Check sensor output value displays if necessary.
8. Determine the fault code and check the detective Items.
Notice
Refer to sefadf3fnosfs list.
Page 1053 of 1463
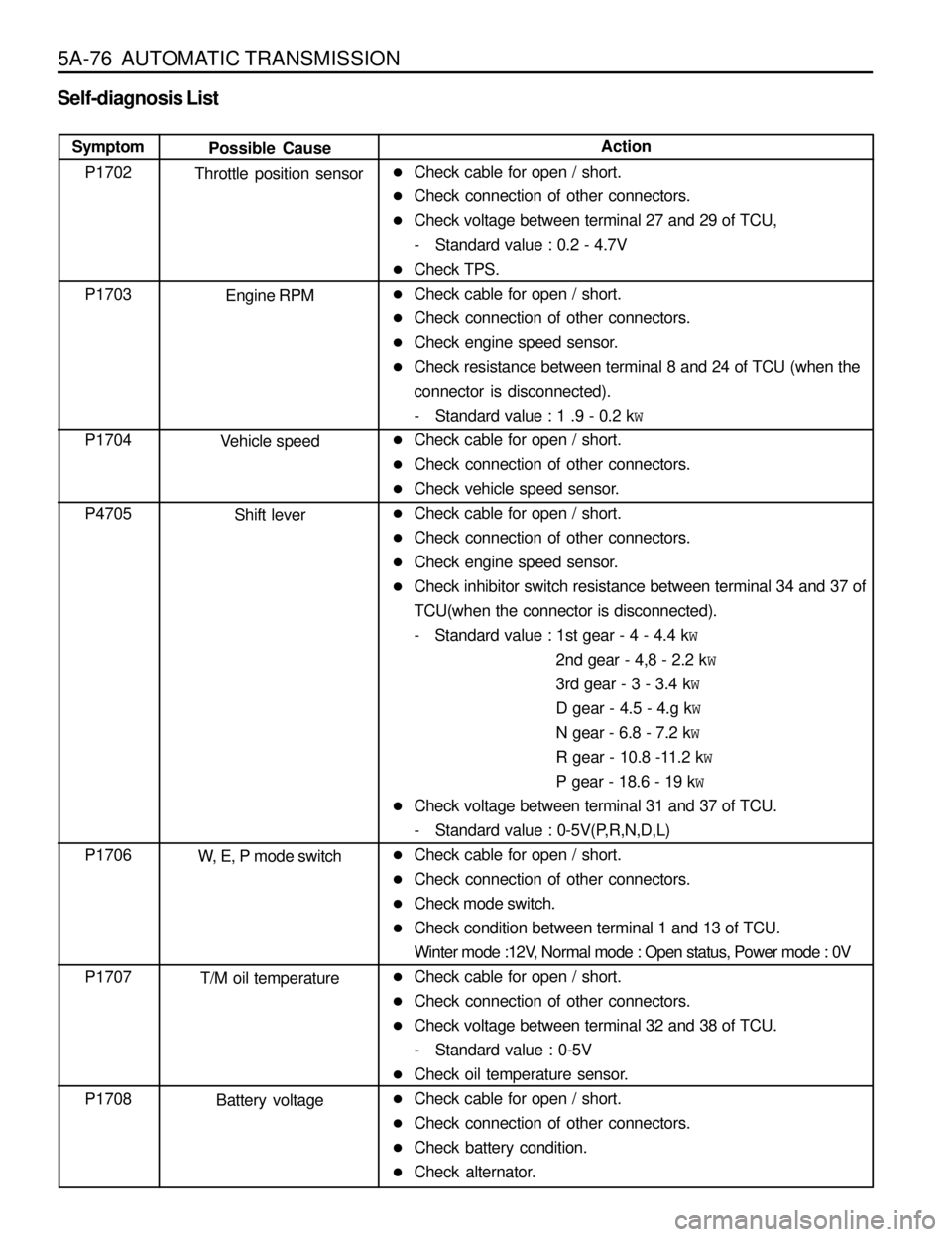
5A-76 AUTOMATIC TRANSMISSION
Action
lCheck cable for open / short.
lCheck connection of other connectors.
lCheck voltage between terminal 27 and 29 of TCU,
- Standard value : 0.2 - 4.7V
lCheck TPS.
lCheck cable for open / short.
lCheck connection of other connectors.
lCheck engine speed sensor.
lCheck resistance between terminal 8 and 24 of TCU (when the
connector is disconnected).
- Standard value : 1 .9 - 0.2 k
W
lCheck cable for open / short.
lCheck connection of other connectors.
lCheck vehicle speed sensor.
lCheck cable for open / short.
lCheck connection of other connectors.
lCheck engine speed sensor.
lCheck inhibitor switch resistance between terminal 34 and 37 of
TCU(when the connector is disconnected).
- Standard value : 1st gear - 4 - 4.4 k
W
2nd gear - 4,8 - 2.2 kW
3rd gear - 3 - 3.4 kW
D gear - 4.5 - 4.g kW
N gear - 6.8 - 7.2 kW
R gear - 10.8 -11.2 kW
P gear - 18.6 - 19 kW
lCheck voltage between terminal 31 and 37 of TCU.
- Standard value : 0-5V(P,R,N,D,L)
lCheck cable for open / short.
lCheck connection of other connectors.
lCheck mode switch.
lCheck condition between terminal 1 and 13 of TCU.
Winter mode :12V, Normal mode : Open status, Power mode : 0V
lCheck cable for open / short.
lCheck connection of other connectors.
lCheck voltage between terminal 32 and 38 of TCU.
- Standard value : 0-5V
lCheck oil temperature sensor.
lCheck cable for open / short.
lCheck connection of other connectors.
lCheck battery condition.
lCheck alternator. Possible Cause
Throttle position sensor
Engine RPM
Vehicle speed
Shift lever
W, E, P mode switch
T/M oil temperature
Battery voltage Symptom
P1702
P1703
P1704
P4705
P1706
P1707
P1708
Self-diagnosis List
Page 1054 of 1463
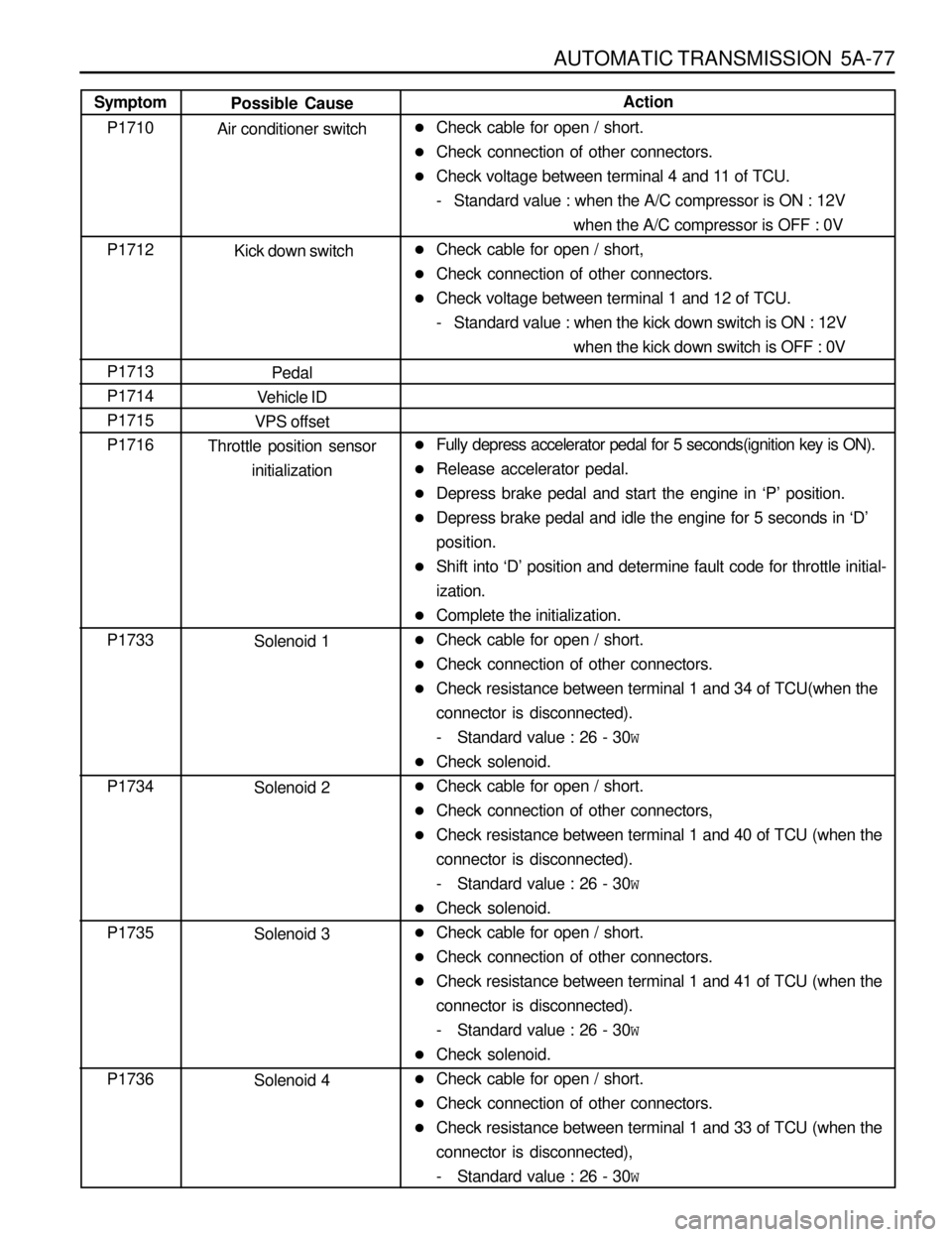
AUTOMATIC TRANSMISSION 5A-77
Action
lCheck cable for open / short.
lCheck connection of other connectors.
lCheck voltage between terminal 4 and 11 of TCU.
- Standard value : when the A/C compressor is ON : 12V
when the A/C compressor is OFF : 0V
lCheck cable for open / short,
lCheck connection of other connectors.
lCheck voltage between terminal 1 and 12 of TCU.
- Standard value : when the kick down switch is ON : 12V
when the kick down switch is OFF : 0V
lFully depress accelerator pedal for 5 seconds(ignition key is ON).
lRelease accelerator pedal.
lDepress brake pedal and start the engine in ‘P’ position.
lDepress brake pedal and idle the engine for 5 seconds in ‘D’
position.
lShift into ‘D’ position and determine fault code for throttle initial-
ization.
lComplete the initialization.
lCheck cable for open / short.
lCheck connection of other connectors.
lCheck resistance between terminal 1 and 34 of TCU(when the
connector is disconnected).
- Standard value : 26 - 30
W
lCheck solenoid.
lCheck cable for open / short.
lCheck connection of other connectors,
lCheck resistance between terminal 1 and 40 of TCU (when the
connector is disconnected).
- Standard value : 26 - 30
W
lCheck solenoid.
lCheck cable for open / short.
lCheck connection of other connectors.
lCheck resistance between terminal 1 and 41 of TCU (when the
connector is disconnected).
- Standard value : 26 - 30
W
lCheck solenoid.
lCheck cable for open / short.
lCheck connection of other connectors.
lCheck resistance between terminal 1 and 33 of TCU (when the
connector is disconnected),
- Standard value : 26 - 30
W
Possible Cause
Air conditioner switch
Kick down switch
Pedal
Vehicle ID
VPS offset
Throttle position sensor
initialization
Solenoid 1
Solenoid 2
Solenoid 3
Solenoid 4 Symptom
P1710
P1712
P1713
P1714
P1715
P1716
P1733
P1734
P1735
P1736
Page 1055 of 1463
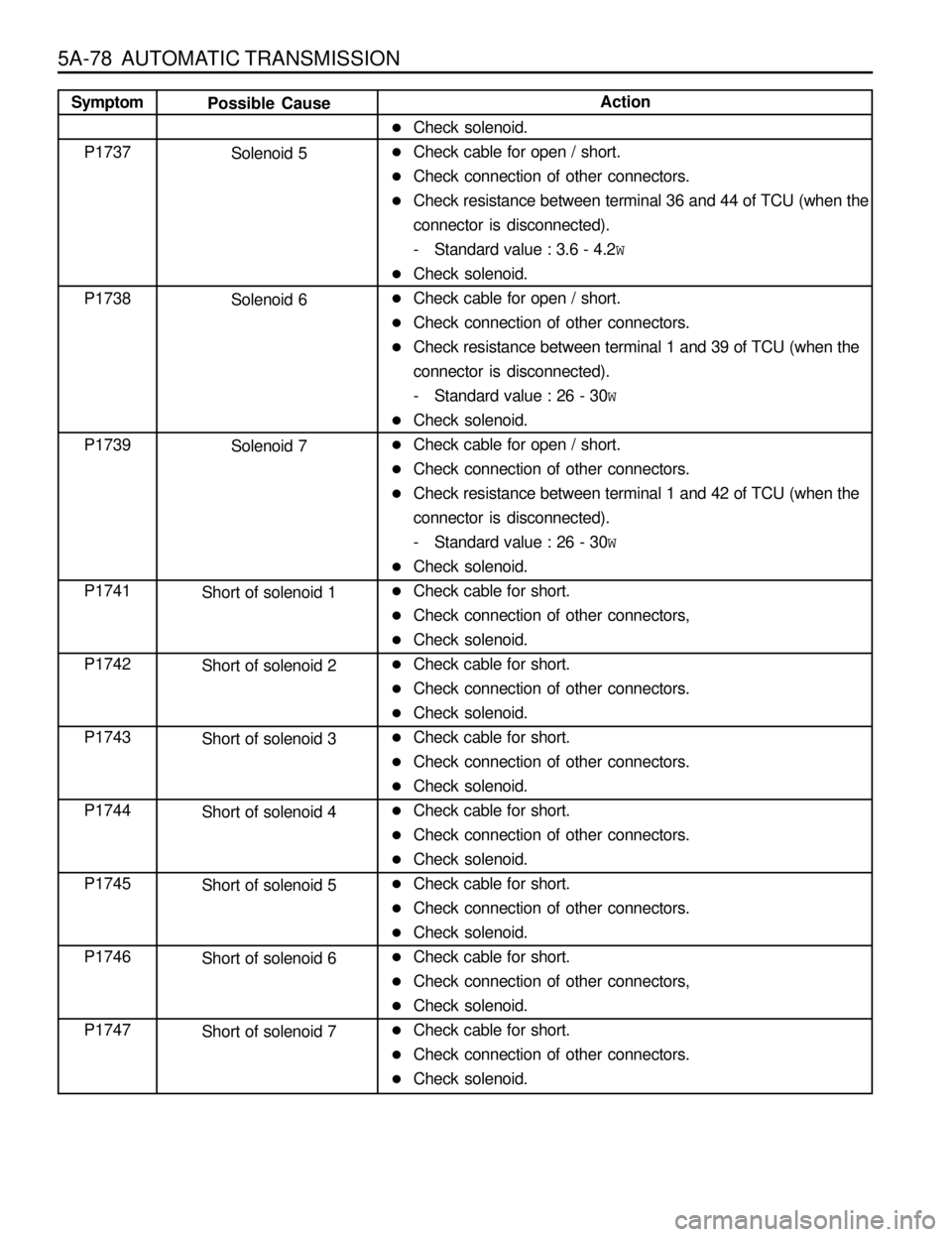
5A-78 AUTOMATIC TRANSMISSION
Action
lCheck solenoid.
lCheck cable for open / short.
lCheck connection of other connectors.
lCheck resistance between terminal 36 and 44 of TCU (when the
connector is disconnected).
- Standard value : 3.6 - 4.2
W
lCheck solenoid.
lCheck cable for open / short.
lCheck connection of other connectors.
lCheck resistance between terminal 1 and 39 of TCU (when the
connector is disconnected).
- Standard value : 26 - 30
W
lCheck solenoid.
lCheck cable for open / short.
lCheck connection of other connectors.
lCheck resistance between terminal 1 and 42 of TCU (when the
connector is disconnected).
- Standard value : 26 - 30
W
lCheck solenoid.
lCheck cable for short.
lCheck connection of other connectors,
lCheck solenoid.
lCheck cable for short.
lCheck connection of other connectors.
lCheck solenoid.
lCheck cable for short.
lCheck connection of other connectors.
lCheck solenoid.
lCheck cable for short.
lCheck connection of other connectors.
lCheck solenoid.
lCheck cable for short.
lCheck connection of other connectors.
lCheck solenoid.
lCheck cable for short.
lCheck connection of other connectors,
lCheck solenoid.
lCheck cable for short.
lCheck connection of other connectors.
lCheck solenoid. Possible Cause
Solenoid 5
Solenoid 6
Solenoid 7
Short of solenoid 1
Short of solenoid 2
Short of solenoid 3
Short of solenoid 4
Short of solenoid 5
Short of solenoid 6
Short of solenoid 7 Symptom
P1737
P1738
P1739
P1741
P1742
P1743
P1744
P1745
P1746
P1747
Page 1056 of 1463
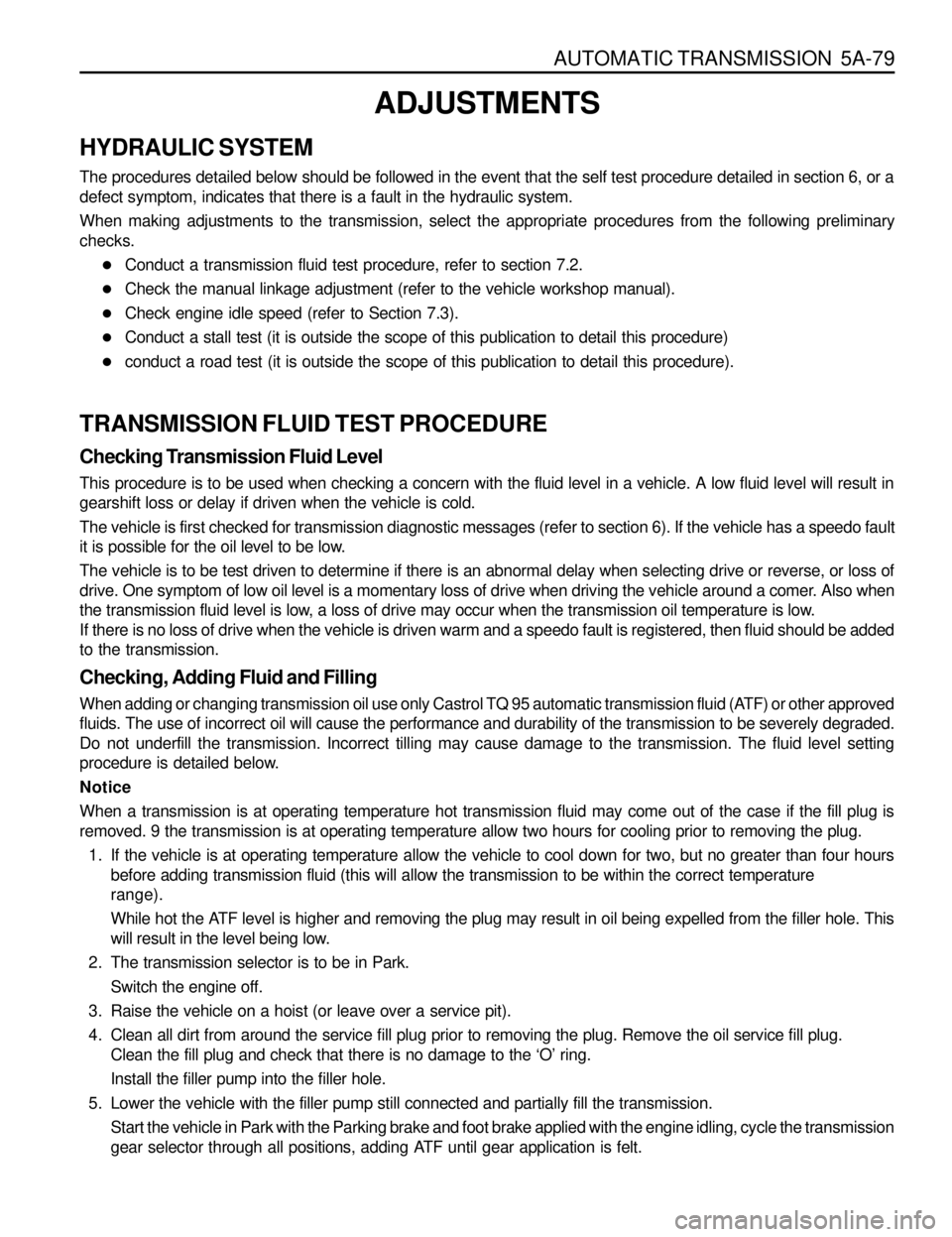
AUTOMATIC TRANSMISSION 5A-79
ADJUSTMENTS
HYDRAULIC SYSTEM
The procedures detailed below should be followed in the event that the self test procedure detailed in section 6, or a
defect symptom, indicates that there is a fault in the hydraulic system.
When making adjustments to the transmission, select the appropriate procedures from the following preliminary
checks.
lConduct a transmission fluid test procedure, refer to section 7.2.
lCheck the manual linkage adjustment (refer to the vehicle workshop manual).
lCheck engine idle speed (refer to Section 7.3).
lConduct a stall test (it is outside the scope of this publication to detail this procedure)
lconduct a road test (it is outside the scope of this publication to detail this procedure).
TRANSMISSION FLUID TEST PROCEDURE
Checking Transmission Fluid Level
This procedure is to be used when checking a concern with the fluid level in a vehicle. A low fluid level will result in
gearshift loss or delay if driven when the vehicle is cold.
The vehicle is first checked for transmission diagnostic messages (refer to section 6). If the vehicle has a speedo fault
it is possible for the oil level to be low.
The vehicle is to be test driven to determine if there is an abnormal delay when selecting drive or reverse, or loss of
drive. One symptom of low oil level is a momentary loss of drive when driving the vehicle around a comer. Also when
the transmission fluid level is low, a loss of drive may occur when the transmission oil temperature is low.
If there is no loss of drive when the vehicle is driven warm and a speedo fault is registered, then fluid should be added
to the transmission.
Checking, Adding Fluid and Filling
When adding or changing transmission oil use only Castrol TQ 95 automatic transmission fluid (ATF) or other approved
fluids. The use of incorrect oil will cause the performance and durability of the transmission to be severely degraded.
Do not underfill the transmission. Incorrect tilling may cause damage to the transmission. The fluid level setting
procedure is detailed below.
Notice
When a transmission is at operating temperature hot transmission fluid may come out of the case if the fill plug is
removed. 9 the transmission is at operating temperature allow two hours for cooling prior to removing the plug.
1. If the vehicle is at operating temperature allow the vehicle to cool down for two, but no greater than four hours
before adding transmission fluid (this will allow the transmission to be within the correct temperature
range).
While hot the ATF level is higher and removing the plug may result in oil being expelled from the filler hole. This
will result in the level being low.
2. The transmission selector is to be in Park.
Switch the engine off.
3. Raise the vehicle on a hoist (or leave over a service pit).
4. Clean all dirt from around the service fill plug prior to removing the plug. Remove the oil service fill plug.
Clean the fill plug and check that there is no damage to the ‘O’ ring.
Install the filler pump into the filler hole.
5. Lower the vehicle with the filler pump still connected and partially fill the transmission.
Start the vehicle in Park with the Parking brake and foot brake applied with the engine idling, cycle the transmission
gear selector through all positions, adding ATF until gear application is felt.