Page 2177 of 2627
SPECIAL TOOLS
TRANSFER CASE NV271/NV273
Handle, Universal - C-4171
Remover - L-4454
Installer, Bearing - 6953
Installer, Pump Housing Seal - 7888
Installer, Bearing - 8128
Cup - 8148
Installer - 8151
Installer - 8152
21 - 474 TRANSFER CASE - NV271DR
TRANSFER CASE - NV271 (Continued)
Page 2178 of 2627
Installer - 8891
Socket - 9033
Installer, Bearing - 9035
Installer, Seal - 9036
Installer, Seal - 9037
DRTRANSFER CASE - NV271 21 - 475
TRANSFER CASE - NV271 (Continued)
Page 2179 of 2627
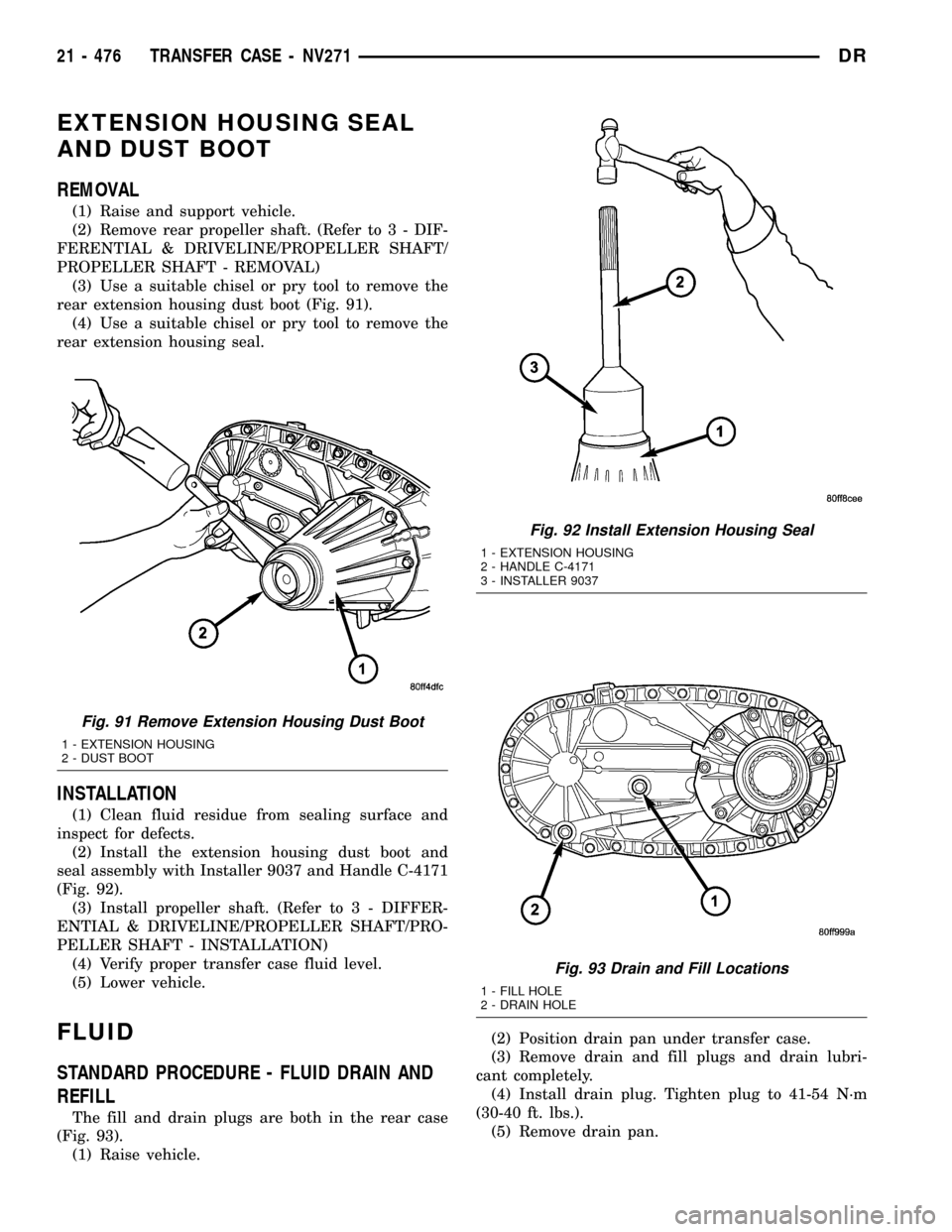
EXTENSION HOUSING SEAL
AND DUST BOOT
REMOVAL
(1) Raise and support vehicle.
(2) Remove rear propeller shaft. (Refer to 3 - DIF-
FERENTIAL & DRIVELINE/PROPELLER SHAFT/
PROPELLER SHAFT - REMOVAL)
(3) Use a suitable chisel or pry tool to remove the
rear extension housing dust boot (Fig. 91).
(4) Use a suitable chisel or pry tool to remove the
rear extension housing seal.
INSTALLATION
(1) Clean fluid residue from sealing surface and
inspect for defects.
(2) Install the extension housing dust boot and
seal assembly with Installer 9037 and Handle C-4171
(Fig. 92).
(3) Install propeller shaft. (Refer to 3 - DIFFER-
ENTIAL & DRIVELINE/PROPELLER SHAFT/PRO-
PELLER SHAFT - INSTALLATION)
(4) Verify proper transfer case fluid level.
(5) Lower vehicle.
FLUID
STANDARD PROCEDURE - FLUID DRAIN AND
REFILL
The fill and drain plugs are both in the rear case
(Fig. 93).
(1) Raise vehicle.(2) Position drain pan under transfer case.
(3) Remove drain and fill plugs and drain lubri-
cant completely.
(4) Install drain plug. Tighten plug to 41-54 N´m
(30-40 ft. lbs.).
(5) Remove drain pan.
Fig. 91 Remove Extension Housing Dust Boot
1 - EXTENSION HOUSING
2 - DUST BOOT
Fig. 92 Install Extension Housing Seal
1 - EXTENSION HOUSING
2 - HANDLE C-4171
3 - INSTALLER 9037
Fig. 93 Drain and Fill Locations
1 - FILL HOLE
2 - DRAIN HOLE
21 - 476 TRANSFER CASE - NV271DR
Page 2180 of 2627
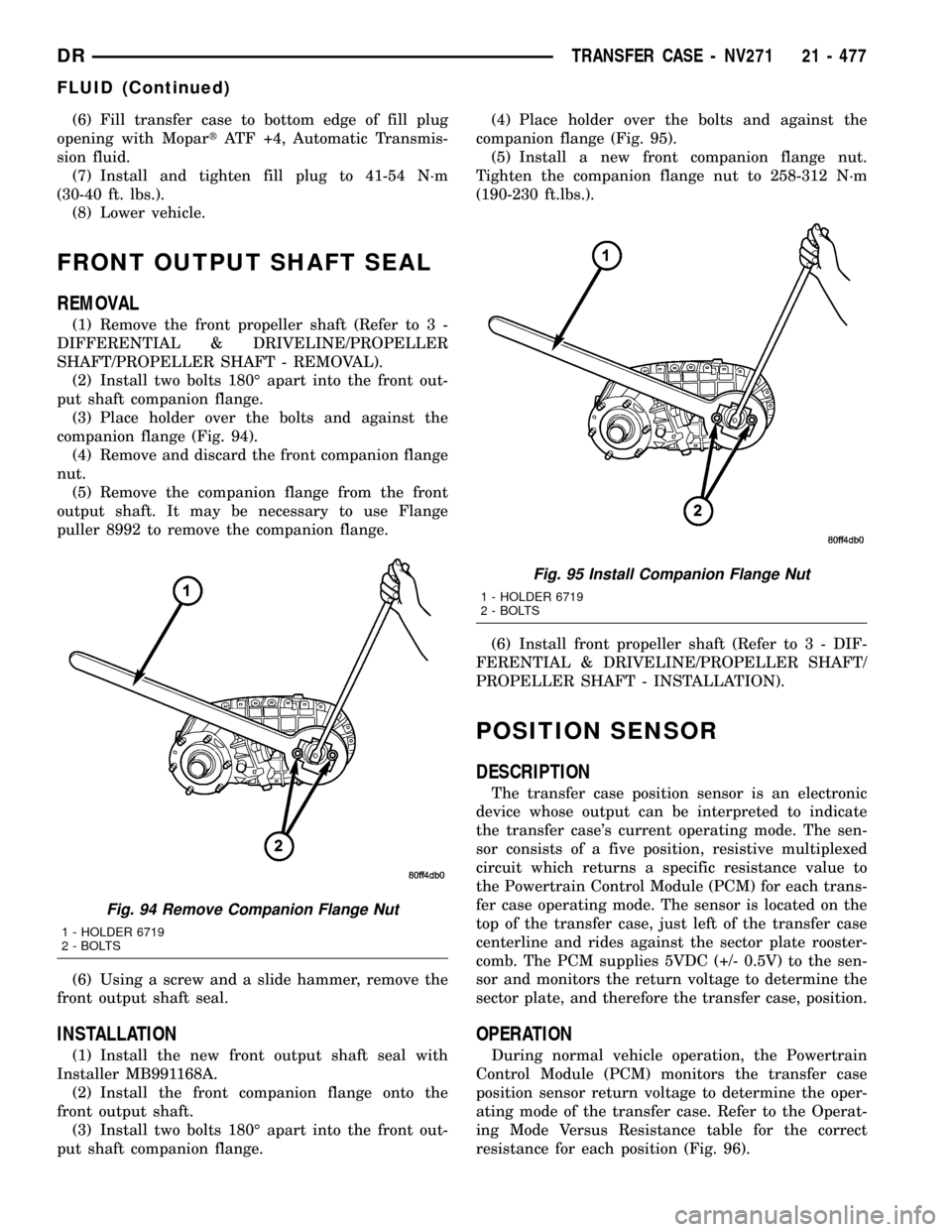
(6) Fill transfer case to bottom edge of fill plug
opening with MopartATF +4, Automatic Transmis-
sion fluid.
(7) Install and tighten fill plug to 41-54 N´m
(30-40 ft. lbs.).
(8) Lower vehicle.
FRONT OUTPUT SHAFT SEAL
REMOVAL
(1) Remove the front propeller shaft (Refer to 3 -
DIFFERENTIAL & DRIVELINE/PROPELLER
SHAFT/PROPELLER SHAFT - REMOVAL).
(2) Install two bolts 180É apart into the front out-
put shaft companion flange.
(3) Place holder over the bolts and against the
companion flange (Fig. 94).
(4) Remove and discard the front companion flange
nut.
(5) Remove the companion flange from the front
output shaft. It may be necessary to use Flange
puller 8992 to remove the companion flange.
(6) Using a screw and a slide hammer, remove the
front output shaft seal.
INSTALLATION
(1) Install the new front output shaft seal with
Installer MB991168A.
(2) Install the front companion flange onto the
front output shaft.
(3) Install two bolts 180É apart into the front out-
put shaft companion flange.(4) Place holder over the bolts and against the
companion flange (Fig. 95).
(5) Install a new front companion flange nut.
Tighten the companion flange nut to 258-312 N´m
(190-230 ft.lbs.).
(6) Install front propeller shaft (Refer to 3 - DIF-
FERENTIAL & DRIVELINE/PROPELLER SHAFT/
PROPELLER SHAFT - INSTALLATION).
POSITION SENSOR
DESCRIPTION
The transfer case position sensor is an electronic
device whose output can be interpreted to indicate
the transfer case's current operating mode. The sen-
sor consists of a five position, resistive multiplexed
circuit which returns a specific resistance value to
the Powertrain Control Module (PCM) for each trans-
fer case operating mode. The sensor is located on the
top of the transfer case, just left of the transfer case
centerline and rides against the sector plate rooster-
comb. The PCM supplies 5VDC (+/- 0.5V) to the sen-
sor and monitors the return voltage to determine the
sector plate, and therefore the transfer case, position.
OPERATION
During normal vehicle operation, the Powertrain
Control Module (PCM) monitors the transfer case
position sensor return voltage to determine the oper-
ating mode of the transfer case. Refer to the Operat-
ing Mode Versus Resistance table for the correct
resistance for each position (Fig. 96).
Fig. 94 Remove Companion Flange Nut
1 - HOLDER 6719
2 - BOLTS
Fig. 95 Install Companion Flange Nut
1 - HOLDER 6719
2 - BOLTS
DRTRANSFER CASE - NV271 21 - 477
FLUID (Continued)
Page 2181 of 2627
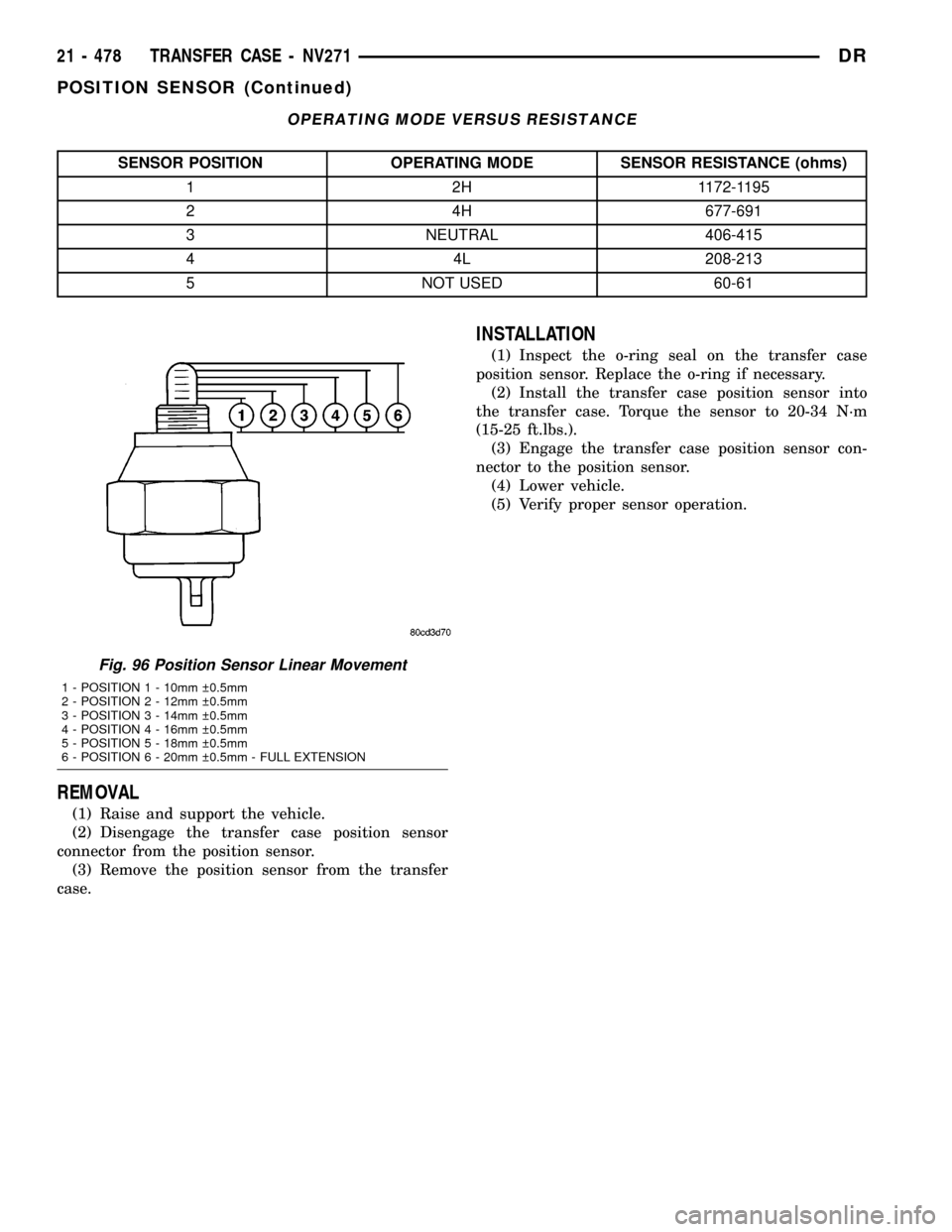
OPERATING MODE VERSUS RESISTANCE
SENSOR POSITION OPERATING MODE SENSOR RESISTANCE (ohms)
1 2H 1172-1195
2 4H 677-691
3 NEUTRAL 406-415
4 4L 208-213
5 NOT USED 60-61
REMOVAL
(1) Raise and support the vehicle.
(2) Disengage the transfer case position sensor
connector from the position sensor.
(3) Remove the position sensor from the transfer
case.
INSTALLATION
(1) Inspect the o-ring seal on the transfer case
position sensor. Replace the o-ring if necessary.
(2) Install the transfer case position sensor into
the transfer case. Torque the sensor to 20-34 N´m
(15-25 ft.lbs.).
(3) Engage the transfer case position sensor con-
nector to the position sensor.
(4) Lower vehicle.
(5) Verify proper sensor operation.
Fig. 96 Position Sensor Linear Movement
1 - POSITION 1 - 10mm 0.5mm
2 - POSITION 2 - 12mm 0.5mm
3 - POSITION 3 - 14mm 0.5mm
4 - POSITION 4 - 16mm 0.5mm
5 - POSITION 5 - 18mm 0.5mm
6 - POSITION 6 - 20mm 0.5mm - FULL EXTENSION
21 - 478 TRANSFER CASE - NV271DR
POSITION SENSOR (Continued)
Page 2182 of 2627
SHIFT LEVER
REMOVAL
(1) Shift transfer case into 2H.
(2) Raise and support the vehicle.
(3) Loosen adjusting trunnion lock bolt and slide
shift rod out of trunnion. If rod lacks enough travel
to come out of trunnion, push trunnion out of shift
lever.
(4) Lower vehicle.
(5) Remove transfer case shifter knob cap.
(6) Remove nut holding shifter knob to shift lever.
(7) Remove shifter knob.
(8) Remove the shift boot from the shifter console.
(9) Remove the bolts securing the shifter mecha-
nism to the floor pan (Fig. 97).
(10) Separate shift lever mechanism from the vehi-
cle.
Fig. 97 Transfer Case Shifter
1 - SHIFTER BOOT 4 - SHIFTER MECHANISM
2 - SHIFTER KNOB 5 - ALIGNMENT PIN
3 - SHIFTER CONSOLE 6 - TRANSFER CASE
DRTRANSFER CASE - NV271 21 - 479
Page 2183 of 2627
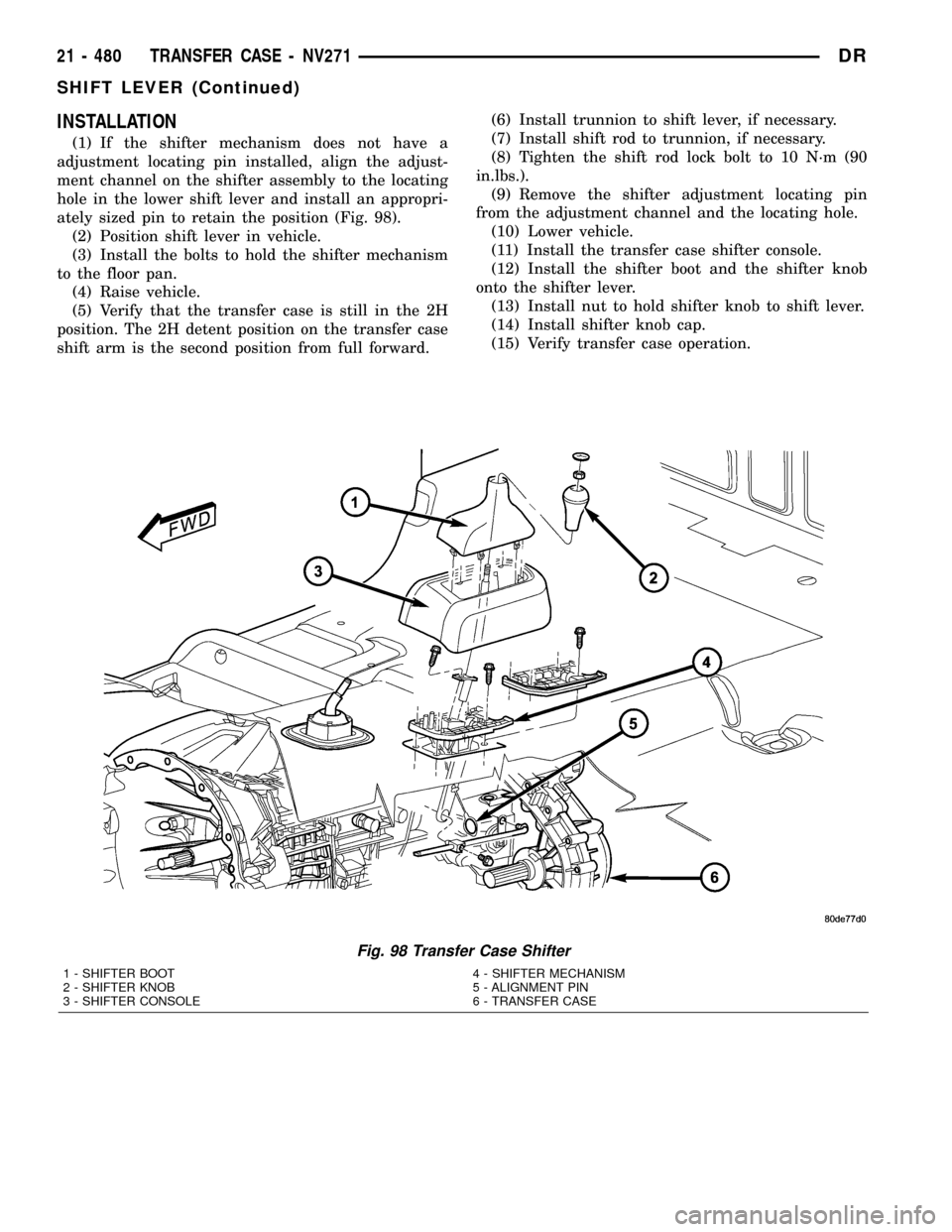
INSTALLATION
(1) If the shifter mechanism does not have a
adjustment locating pin installed, align the adjust-
ment channel on the shifter assembly to the locating
hole in the lower shift lever and install an appropri-
ately sized pin to retain the position (Fig. 98).
(2) Position shift lever in vehicle.
(3) Install the bolts to hold the shifter mechanism
to the floor pan.
(4) Raise vehicle.
(5) Verify that the transfer case is still in the 2H
position. The 2H detent position on the transfer case
shift arm is the second position from full forward.(6) Install trunnion to shift lever, if necessary.
(7) Install shift rod to trunnion, if necessary.
(8) Tighten the shift rod lock bolt to 10 N´m (90
in.lbs.).
(9) Remove the shifter adjustment locating pin
from the adjustment channel and the locating hole.
(10) Lower vehicle.
(11) Install the transfer case shifter console.
(12) Install the shifter boot and the shifter knob
onto the shifter lever.
(13) Install nut to hold shifter knob to shift lever.
(14) Install shifter knob cap.
(15) Verify transfer case operation.
Fig. 98 Transfer Case Shifter
1 - SHIFTER BOOT 4 - SHIFTER MECHANISM
2 - SHIFTER KNOB 5 - ALIGNMENT PIN
3 - SHIFTER CONSOLE 6 - TRANSFER CASE
21 - 480 TRANSFER CASE - NV271DR
SHIFT LEVER (Continued)
Page 2184 of 2627
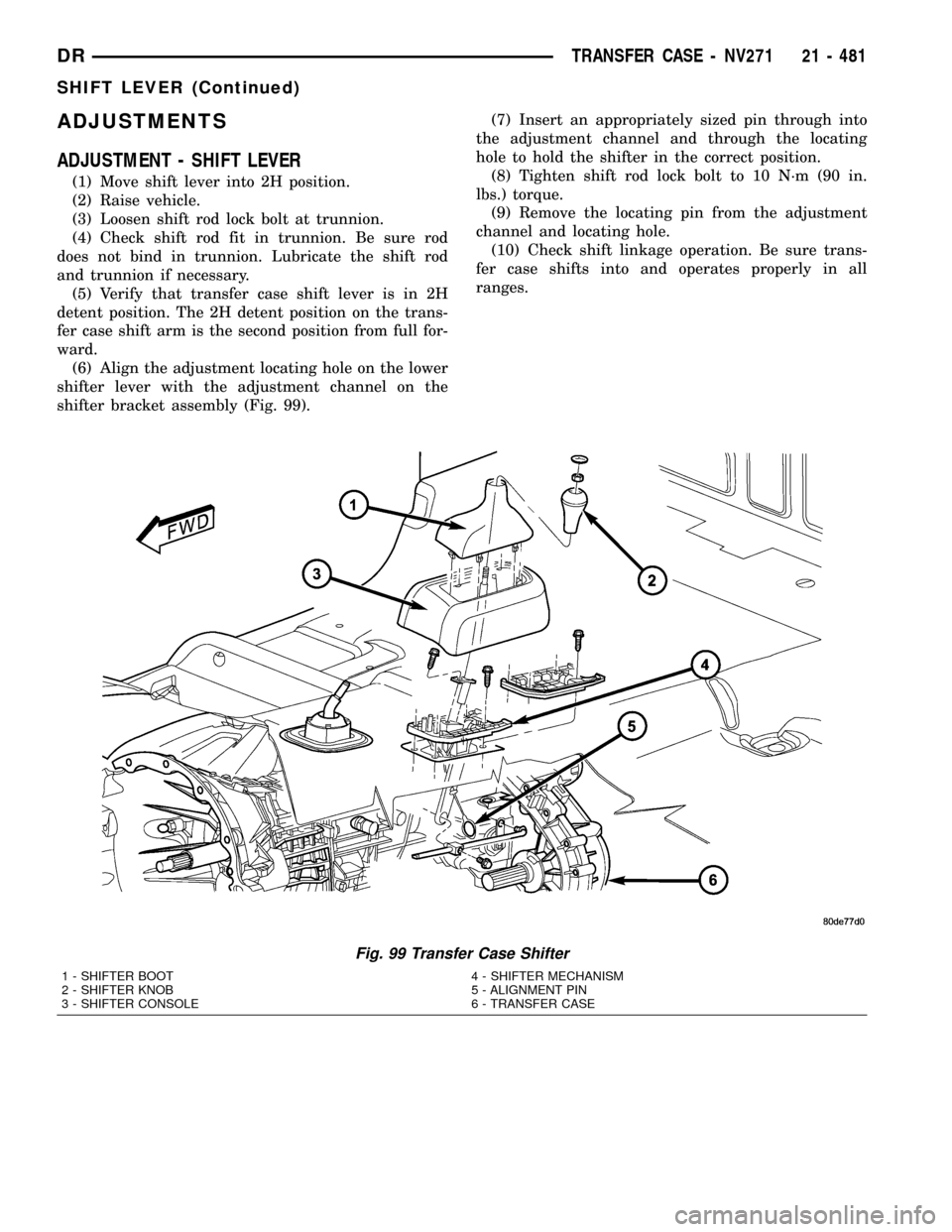
ADJUSTMENTS
ADJUSTMENT - SHIFT LEVER
(1) Move shift lever into 2H position.
(2) Raise vehicle.
(3) Loosen shift rod lock bolt at trunnion.
(4) Check shift rod fit in trunnion. Be sure rod
does not bind in trunnion. Lubricate the shift rod
and trunnion if necessary.
(5) Verify that transfer case shift lever is in 2H
detent position. The 2H detent position on the trans-
fer case shift arm is the second position from full for-
ward.
(6) Align the adjustment locating hole on the lower
shifter lever with the adjustment channel on the
shifter bracket assembly (Fig. 99).(7) Insert an appropriately sized pin through into
the adjustment channel and through the locating
hole to hold the shifter in the correct position.
(8) Tighten shift rod lock bolt to 10 N´m (90 in.
lbs.) torque.
(9) Remove the locating pin from the adjustment
channel and locating hole.
(10) Check shift linkage operation. Be sure trans-
fer case shifts into and operates properly in all
ranges.
Fig. 99 Transfer Case Shifter
1 - SHIFTER BOOT 4 - SHIFTER MECHANISM
2 - SHIFTER KNOB 5 - ALIGNMENT PIN
3 - SHIFTER CONSOLE 6 - TRANSFER CASE
DRTRANSFER CASE - NV271 21 - 481
SHIFT LEVER (Continued)