Page 1697 of 2627
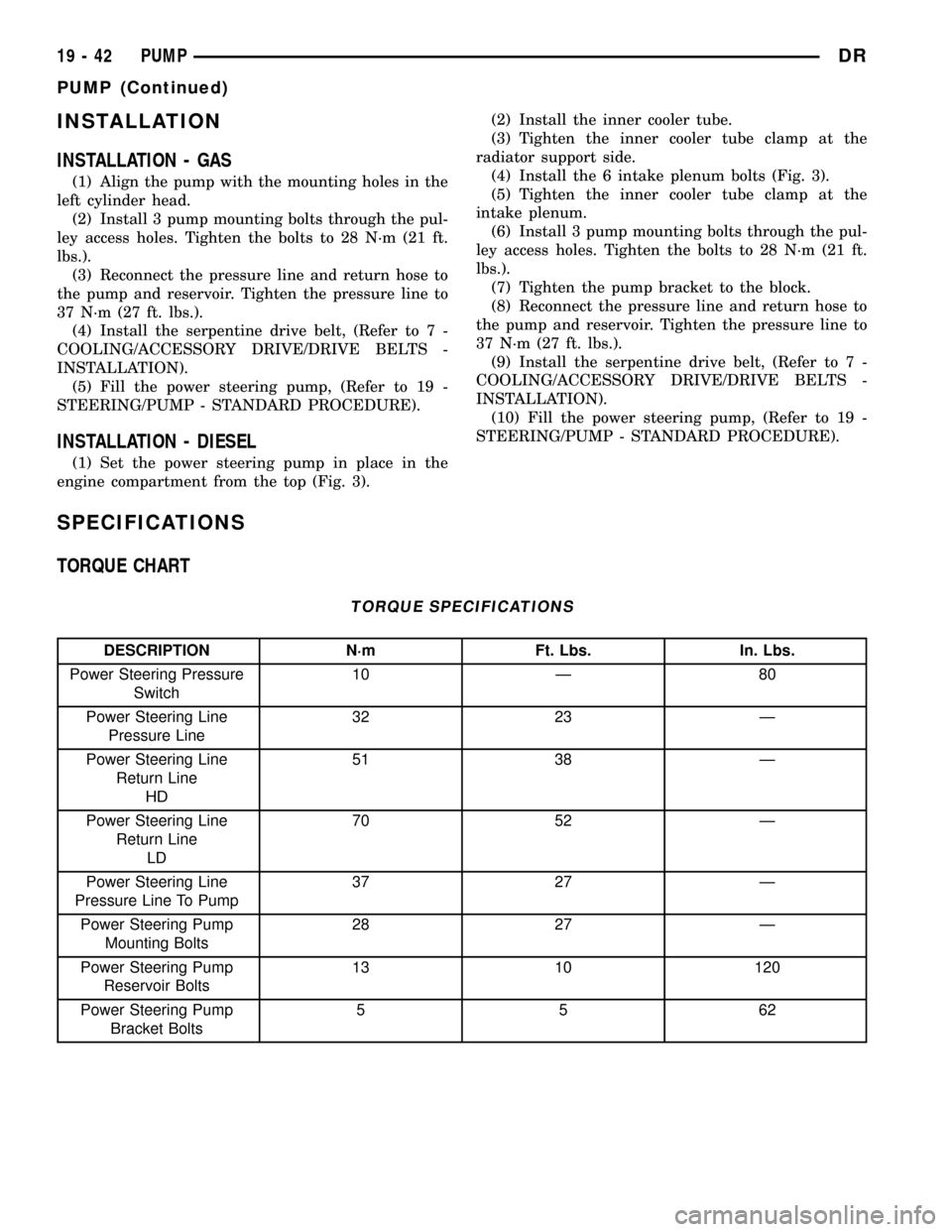
INSTALLATION
INSTALLATION - GAS
(1) Align the pump with the mounting holes in the
left cylinder head.
(2) Install 3 pump mounting bolts through the pul-
ley access holes. Tighten the bolts to 28 N´m (21 ft.
lbs.).
(3) Reconnect the pressure line and return hose to
the pump and reservoir. Tighten the pressure line to
37 N´m (27 ft. lbs.).
(4) Install the serpentine drive belt, (Refer to 7 -
COOLING/ACCESSORY DRIVE/DRIVE BELTS -
INSTALLATION).
(5) Fill the power steering pump, (Refer to 19 -
STEERING/PUMP - STANDARD PROCEDURE).
INSTALLATION - DIESEL
(1) Set the power steering pump in place in the
engine compartment from the top (Fig. 3).(2) Install the inner cooler tube.
(3) Tighten the inner cooler tube clamp at the
radiator support side.
(4) Install the 6 intake plenum bolts (Fig. 3).
(5) Tighten the inner cooler tube clamp at the
intake plenum.
(6) Install 3 pump mounting bolts through the pul-
ley access holes. Tighten the bolts to 28 N´m (21 ft.
lbs.).
(7) Tighten the pump bracket to the block.
(8) Reconnect the pressure line and return hose to
the pump and reservoir. Tighten the pressure line to
37 N´m (27 ft. lbs.).
(9) Install the serpentine drive belt, (Refer to 7 -
COOLING/ACCESSORY DRIVE/DRIVE BELTS -
INSTALLATION).
(10) Fill the power steering pump, (Refer to 19 -
STEERING/PUMP - STANDARD PROCEDURE).
SPECIFICATIONS
TORQUE CHART
TORQUE SPECIFICATIONS
DESCRIPTION N´m Ft. Lbs. In. Lbs.
Power Steering Pressure
Switch10 Ð 80
Power Steering Line
Pressure Line32 23 Ð
Power Steering Line
Return Line
HD51 38 Ð
Power Steering Line
Return Line
LD70 52 Ð
Power Steering Line
Pressure Line To Pump37 27 Ð
Power Steering Pump
Mounting Bolts28 27 Ð
Power Steering Pump
Reservoir Bolts13 10 120
Power Steering Pump
Bracket Bolts5562
19 - 42 PUMPDR
PUMP (Continued)
Page 1698 of 2627
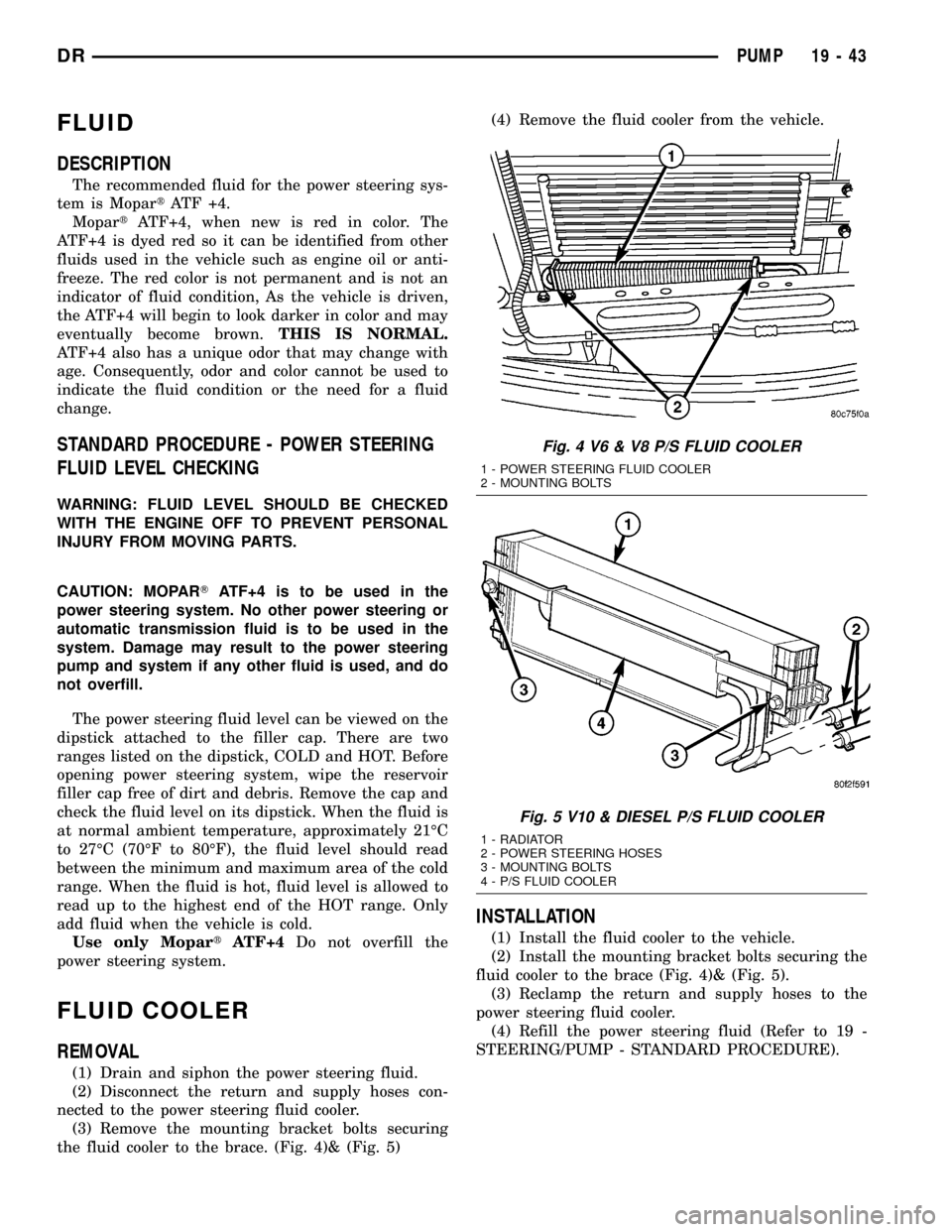
FLUID
DESCRIPTION
The recommended fluid for the power steering sys-
tem is MopartATF +4.
MopartATF+4, when new is red in color. The
ATF+4 is dyed red so it can be identified from other
fluids used in the vehicle such as engine oil or anti-
freeze. The red color is not permanent and is not an
indicator of fluid condition, As the vehicle is driven,
the ATF+4 will begin to look darker in color and may
eventually become brown.THIS IS NORMAL.
ATF+4 also has a unique odor that may change with
age. Consequently, odor and color cannot be used to
indicate the fluid condition or the need for a fluid
change.
STANDARD PROCEDURE - POWER STEERING
FLUID LEVEL CHECKING
WARNING: FLUID LEVEL SHOULD BE CHECKED
WITH THE ENGINE OFF TO PREVENT PERSONAL
INJURY FROM MOVING PARTS.
CAUTION: MOPARTATF+4 is to be used in the
power steering system. No other power steering or
automatic transmission fluid is to be used in the
system. Damage may result to the power steering
pump and system if any other fluid is used, and do
not overfill.
The power steering fluid level can be viewed on the
dipstick attached to the filler cap. There are two
ranges listed on the dipstick, COLD and HOT. Before
opening power steering system, wipe the reservoir
filler cap free of dirt and debris. Remove the cap and
check the fluid level on its dipstick. When the fluid is
at normal ambient temperature, approximately 21ÉC
to 27ÉC (70ÉF to 80ÉF), the fluid level should read
between the minimum and maximum area of the cold
range. When the fluid is hot, fluid level is allowed to
read up to the highest end of the HOT range. Only
add fluid when the vehicle is cold.
Use only MopartATF+4Do not overfill the
power steering system.
FLUID COOLER
REMOVAL
(1) Drain and siphon the power steering fluid.
(2) Disconnect the return and supply hoses con-
nected to the power steering fluid cooler.
(3) Remove the mounting bracket bolts securing
the fluid cooler to the brace. (Fig. 4)& (Fig. 5)(4) Remove the fluid cooler from the vehicle.
INSTALLATION
(1) Install the fluid cooler to the vehicle.
(2) Install the mounting bracket bolts securing the
fluid cooler to the brace (Fig. 4)& (Fig. 5).
(3) Reclamp the return and supply hoses to the
power steering fluid cooler.
(4) Refill the power steering fluid (Refer to 19 -
STEERING/PUMP - STANDARD PROCEDURE).
Fig. 4 V6 & V8 P/S FLUID COOLER
1 - POWER STEERING FLUID COOLER
2 - MOUNTING BOLTS
Fig. 5 V10 & DIESEL P/S FLUID COOLER
1 - RADIATOR
2 - POWER STEERING HOSES
3 - MOUNTING BOLTS
4 - P/S FLUID COOLER
DRPUMP 19 - 43
Page 1699 of 2627
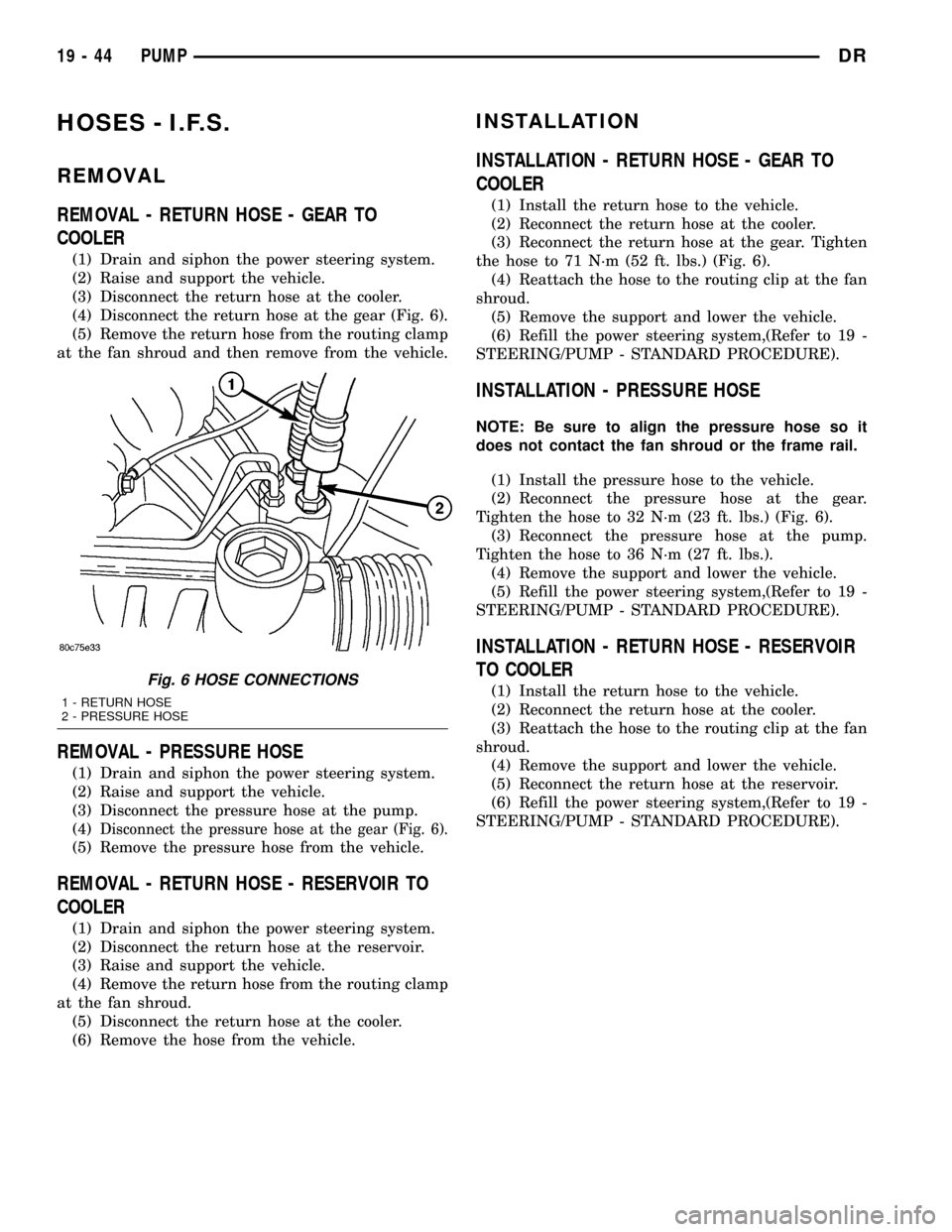
HOSES - I.F.S.
REMOVAL
REMOVAL - RETURN HOSE - GEAR TO
COOLER
(1) Drain and siphon the power steering system.
(2) Raise and support the vehicle.
(3) Disconnect the return hose at the cooler.
(4) Disconnect the return hose at the gear (Fig. 6).
(5) Remove the return hose from the routing clamp
at the fan shroud and then remove from the vehicle.
REMOVAL - PRESSURE HOSE
(1) Drain and siphon the power steering system.
(2) Raise and support the vehicle.
(3) Disconnect the pressure hose at the pump.
(4)
Disconnect the pressure hose at the gear (Fig. 6).
(5) Remove the pressure hose from the vehicle.
REMOVAL - RETURN HOSE - RESERVOIR TO
COOLER
(1) Drain and siphon the power steering system.
(2) Disconnect the return hose at the reservoir.
(3) Raise and support the vehicle.
(4) Remove the return hose from the routing clamp
at the fan shroud.
(5) Disconnect the return hose at the cooler.
(6) Remove the hose from the vehicle.
INSTALLATION
INSTALLATION - RETURN HOSE - GEAR TO
COOLER
(1) Install the return hose to the vehicle.
(2) Reconnect the return hose at the cooler.
(3) Reconnect the return hose at the gear. Tighten
the hose to 71 N´m (52 ft. lbs.) (Fig. 6).
(4) Reattach the hose to the routing clip at the fan
shroud.
(5) Remove the support and lower the vehicle.
(6) Refill the power steering system,(Refer to 19 -
STEERING/PUMP - STANDARD PROCEDURE).
INSTALLATION - PRESSURE HOSE
NOTE: Be sure to align the pressure hose so it
does not contact the fan shroud or the frame rail.
(1) Install the pressure hose to the vehicle.
(2) Reconnect the pressure hose at the gear.
Tighten the hose to 32 N´m (23 ft. lbs.) (Fig. 6).
(3) Reconnect the pressure hose at the pump.
Tighten the hose to 36 N´m (27 ft. lbs.).
(4) Remove the support and lower the vehicle.
(5) Refill the power steering system,(Refer to 19 -
STEERING/PUMP - STANDARD PROCEDURE).
INSTALLATION - RETURN HOSE - RESERVOIR
TO COOLER
(1) Install the return hose to the vehicle.
(2) Reconnect the return hose at the cooler.
(3) Reattach the hose to the routing clip at the fan
shroud.
(4) Remove the support and lower the vehicle.
(5) Reconnect the return hose at the reservoir.
(6) Refill the power steering system,(Refer to 19 -
STEERING/PUMP - STANDARD PROCEDURE).Fig. 6 HOSE CONNECTIONS
1 - RETURN HOSE
2 - PRESSURE HOSE
19 - 44 PUMPDR
Page 1700 of 2627
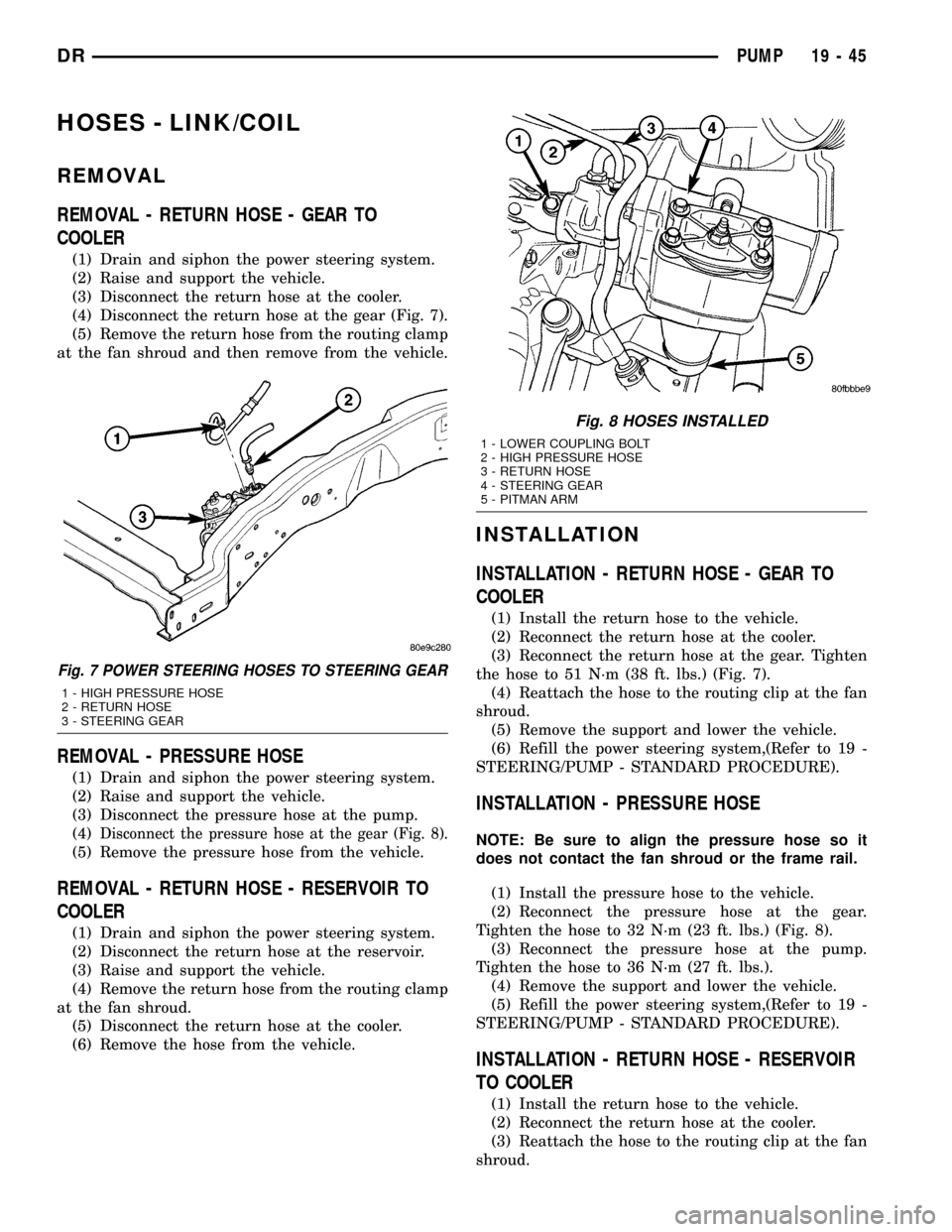
HOSES - LINK/COIL
REMOVAL
REMOVAL - RETURN HOSE - GEAR TO
COOLER
(1) Drain and siphon the power steering system.
(2) Raise and support the vehicle.
(3) Disconnect the return hose at the cooler.
(4) Disconnect the return hose at the gear (Fig. 7).
(5) Remove the return hose from the routing clamp
at the fan shroud and then remove from the vehicle.
REMOVAL - PRESSURE HOSE
(1) Drain and siphon the power steering system.
(2) Raise and support the vehicle.
(3) Disconnect the pressure hose at the pump.
(4)
Disconnect the pressure hose at the gear (Fig. 8).
(5) Remove the pressure hose from the vehicle.
REMOVAL - RETURN HOSE - RESERVOIR TO
COOLER
(1) Drain and siphon the power steering system.
(2) Disconnect the return hose at the reservoir.
(3) Raise and support the vehicle.
(4) Remove the return hose from the routing clamp
at the fan shroud.
(5) Disconnect the return hose at the cooler.
(6) Remove the hose from the vehicle.
INSTALLATION
INSTALLATION - RETURN HOSE - GEAR TO
COOLER
(1) Install the return hose to the vehicle.
(2) Reconnect the return hose at the cooler.
(3) Reconnect the return hose at the gear. Tighten
the hose to 51 N´m (38 ft. lbs.) (Fig. 7).
(4) Reattach the hose to the routing clip at the fan
shroud.
(5) Remove the support and lower the vehicle.
(6) Refill the power steering system,(Refer to 19 -
STEERING/PUMP - STANDARD PROCEDURE).
INSTALLATION - PRESSURE HOSE
NOTE: Be sure to align the pressure hose so it
does not contact the fan shroud or the frame rail.
(1) Install the pressure hose to the vehicle.
(2) Reconnect the pressure hose at the gear.
Tighten the hose to 32 N´m (23 ft. lbs.) (Fig. 8).
(3) Reconnect the pressure hose at the pump.
Tighten the hose to 36 N´m (27 ft. lbs.).
(4) Remove the support and lower the vehicle.
(5) Refill the power steering system,(Refer to 19 -
STEERING/PUMP - STANDARD PROCEDURE).
INSTALLATION - RETURN HOSE - RESERVOIR
TO COOLER
(1) Install the return hose to the vehicle.
(2) Reconnect the return hose at the cooler.
(3) Reattach the hose to the routing clip at the fan
shroud.
Fig. 7 POWER STEERING HOSES TO STEERING GEAR
1 - HIGH PRESSURE HOSE
2 - RETURN HOSE
3 - STEERING GEAR
Fig. 8 HOSES INSTALLED
1 - LOWER COUPLING BOLT
2 - HIGH PRESSURE HOSE
3 - RETURN HOSE
4 - STEERING GEAR
5 - PITMAN ARM
DRPUMP 19 - 45
Page 1701 of 2627
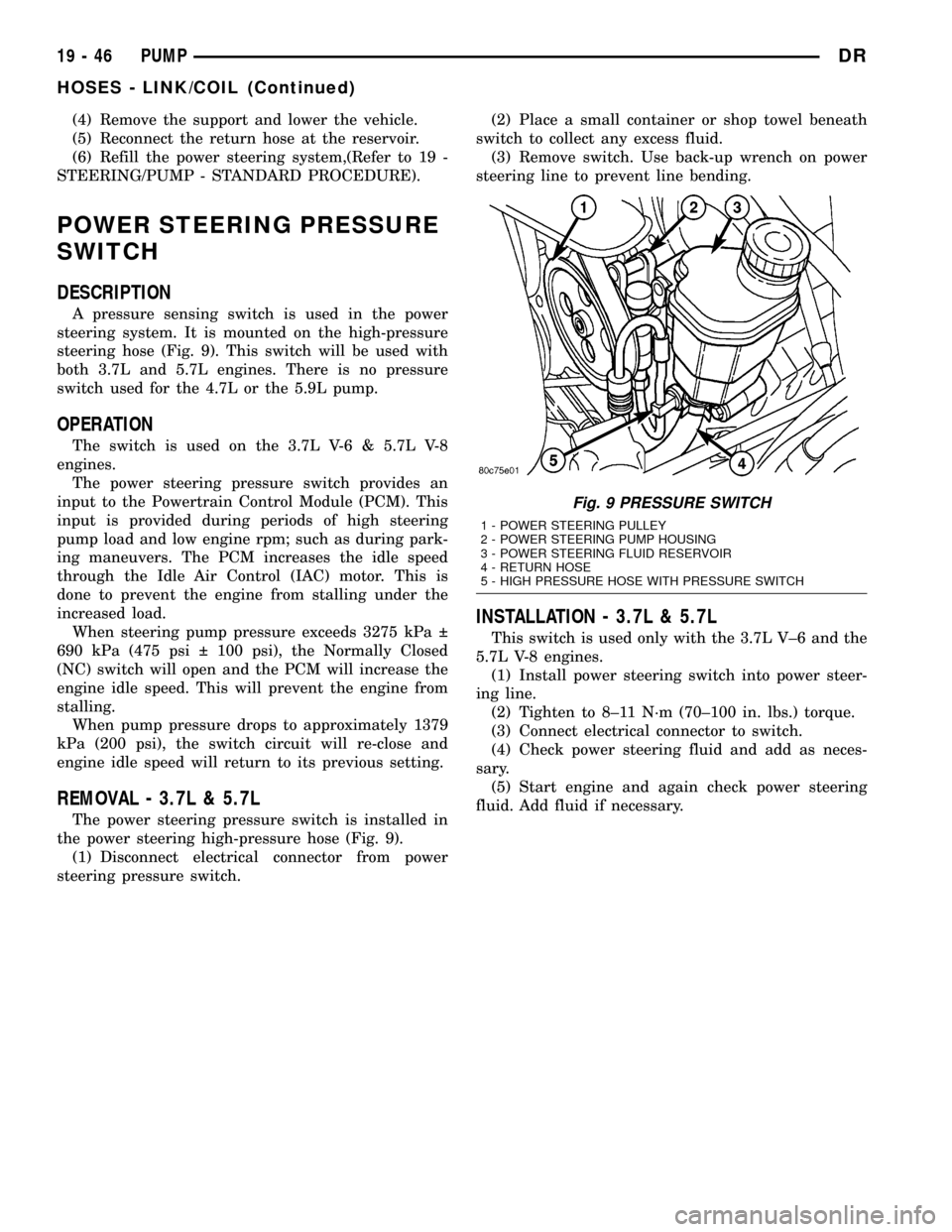
(4) Remove the support and lower the vehicle.
(5) Reconnect the return hose at the reservoir.
(6) Refill the power steering system,(Refer to 19 -
STEERING/PUMP - STANDARD PROCEDURE).
POWER STEERING PRESSURE
SWITCH
DESCRIPTION
A pressure sensing switch is used in the power
steering system. It is mounted on the high-pressure
steering hose (Fig. 9). This switch will be used with
both 3.7L and 5.7L engines. There is no pressure
switch used for the 4.7L or the 5.9L pump.
OPERATION
The switch is used on the 3.7L V-6 & 5.7L V-8
engines.
The power steering pressure switch provides an
input to the Powertrain Control Module (PCM). This
input is provided during periods of high steering
pump load and low engine rpm; such as during park-
ing maneuvers. The PCM increases the idle speed
through the Idle Air Control (IAC) motor. This is
done to prevent the engine from stalling under the
increased load.
When steering pump pressure exceeds 3275 kPa
690 kPa (475 psi 100 psi), the Normally Closed
(NC) switch will open and the PCM will increase the
engine idle speed. This will prevent the engine from
stalling.
When pump pressure drops to approximately 1379
kPa (200 psi), the switch circuit will re-close and
engine idle speed will return to its previous setting.
REMOVAL - 3.7L & 5.7L
The power steering pressure switch is installed in
the power steering high-pressure hose (Fig. 9).
(1) Disconnect electrical connector from power
steering pressure switch.(2) Place a small container or shop towel beneath
switch to collect any excess fluid.
(3) Remove switch. Use back-up wrench on power
steering line to prevent line bending.
INSTALLATION - 3.7L & 5.7L
This switch is used only with the 3.7L V±6 and the
5.7L V-8 engines.
(1) Install power steering switch into power steer-
ing line.
(2) Tighten to 8±11 N´m (70±100 in. lbs.) torque.
(3) Connect electrical connector to switch.
(4) Check power steering fluid and add as neces-
sary.
(5) Start engine and again check power steering
fluid. Add fluid if necessary.
Fig. 9 PRESSURE SWITCH
1 - POWER STEERING PULLEY
2 - POWER STEERING PUMP HOUSING
3 - POWER STEERING FLUID RESERVOIR
4 - RETURN HOSE
5 - HIGH PRESSURE HOSE WITH PRESSURE SWITCH
19 - 46 PUMPDR
HOSES - LINK/COIL (Continued)
Page 1702 of 2627
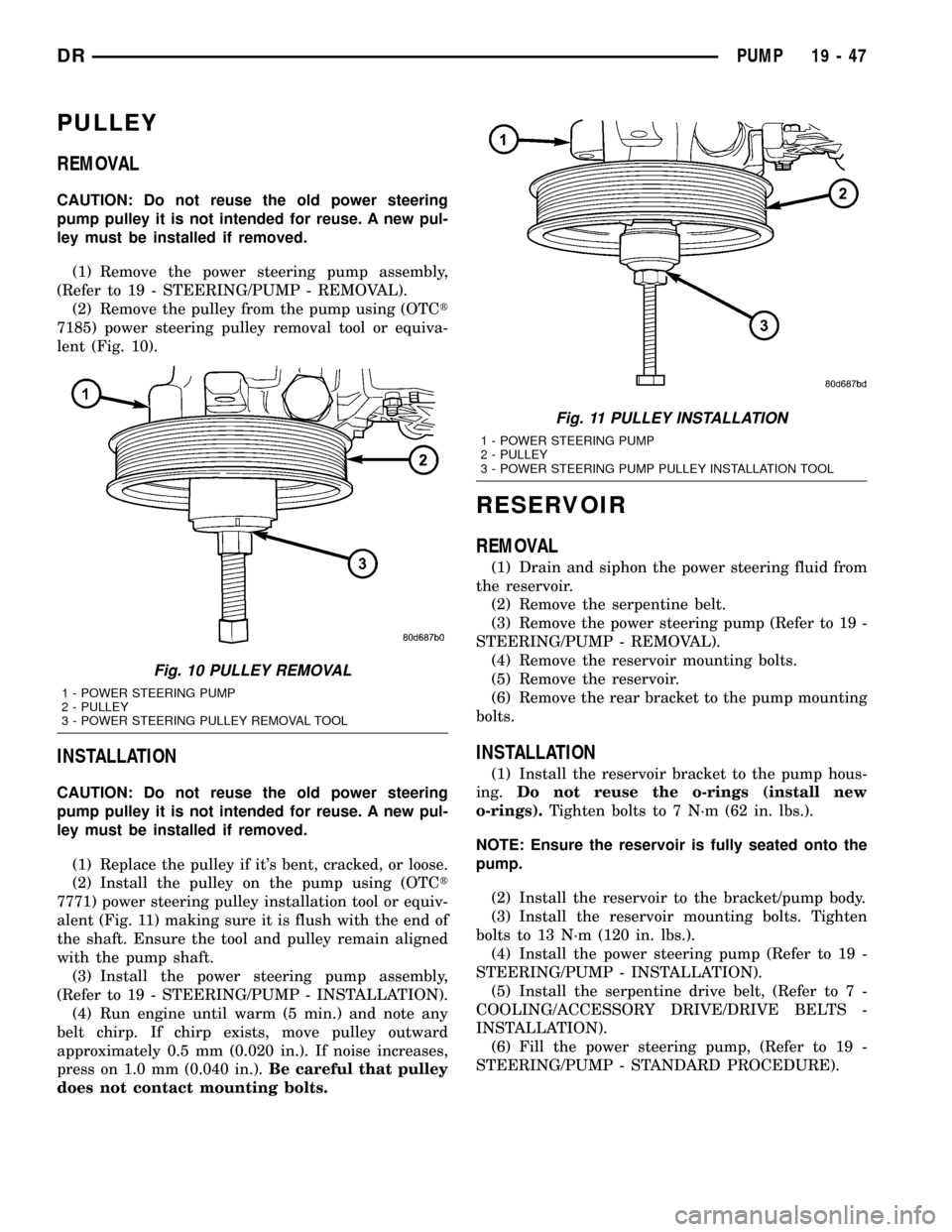
PULLEY
REMOVAL
CAUTION: Do not reuse the old power steering
pump pulley it is not intended for reuse. A new pul-
ley must be installed if removed.
(1) Remove the power steering pump assembly,
(Refer to 19 - STEERING/PUMP - REMOVAL).
(2) Remove the pulley from the pump using (OTCt
7185) power steering pulley removal tool or equiva-
lent (Fig. 10).
INSTALLATION
CAUTION: Do not reuse the old power steering
pump pulley it is not intended for reuse. A new pul-
ley must be installed if removed.
(1) Replace the pulley if it's bent, cracked, or loose.
(2) Install the pulley on the pump using (OTCt
7771) power steering pulley installation tool or equiv-
alent (Fig. 11) making sure it is flush with the end of
the shaft. Ensure the tool and pulley remain aligned
with the pump shaft.
(3) Install the power steering pump assembly,
(Refer to 19 - STEERING/PUMP - INSTALLATION).
(4) Run engine until warm (5 min.) and note any
belt chirp. If chirp exists, move pulley outward
approximately 0.5 mm (0.020 in.). If noise increases,
press on 1.0 mm (0.040 in.).Be careful that pulley
does not contact mounting bolts.
RESERVOIR
REMOVAL
(1) Drain and siphon the power steering fluid from
the reservoir.
(2) Remove the serpentine belt.
(3) Remove the power steering pump (Refer to 19 -
STEERING/PUMP - REMOVAL).
(4) Remove the reservoir mounting bolts.
(5) Remove the reservoir.
(6) Remove the rear bracket to the pump mounting
bolts.
INSTALLATION
(1) Install the reservoir bracket to the pump hous-
ing.Do not reuse the o-rings (install new
o-rings).Tighten bolts to 7 N´m (62 in. lbs.).
NOTE: Ensure the reservoir is fully seated onto the
pump.
(2) Install the reservoir to the bracket/pump body.
(3) Install the reservoir mounting bolts. Tighten
bolts to 13 N´m (120 in. lbs.).
(4) Install the power steering pump (Refer to 19 -
STEERING/PUMP - INSTALLATION).
(5) Install the serpentine drive belt, (Refer to 7 -
COOLING/ACCESSORY DRIVE/DRIVE BELTS -
INSTALLATION).
(6) Fill the power steering pump, (Refer to 19 -
STEERING/PUMP - STANDARD PROCEDURE).
Fig. 10 PULLEY REMOVAL
1 - POWER STEERING PUMP
2 - PULLEY
3 - POWER STEERING PULLEY REMOVAL TOOL
Fig. 11 PULLEY INSTALLATION
1 - POWER STEERING PUMP
2 - PULLEY
3 - POWER STEERING PUMP PULLEY INSTALLATION TOOL
DRPUMP 19 - 47
Page 1703 of 2627
Page 1704 of 2627
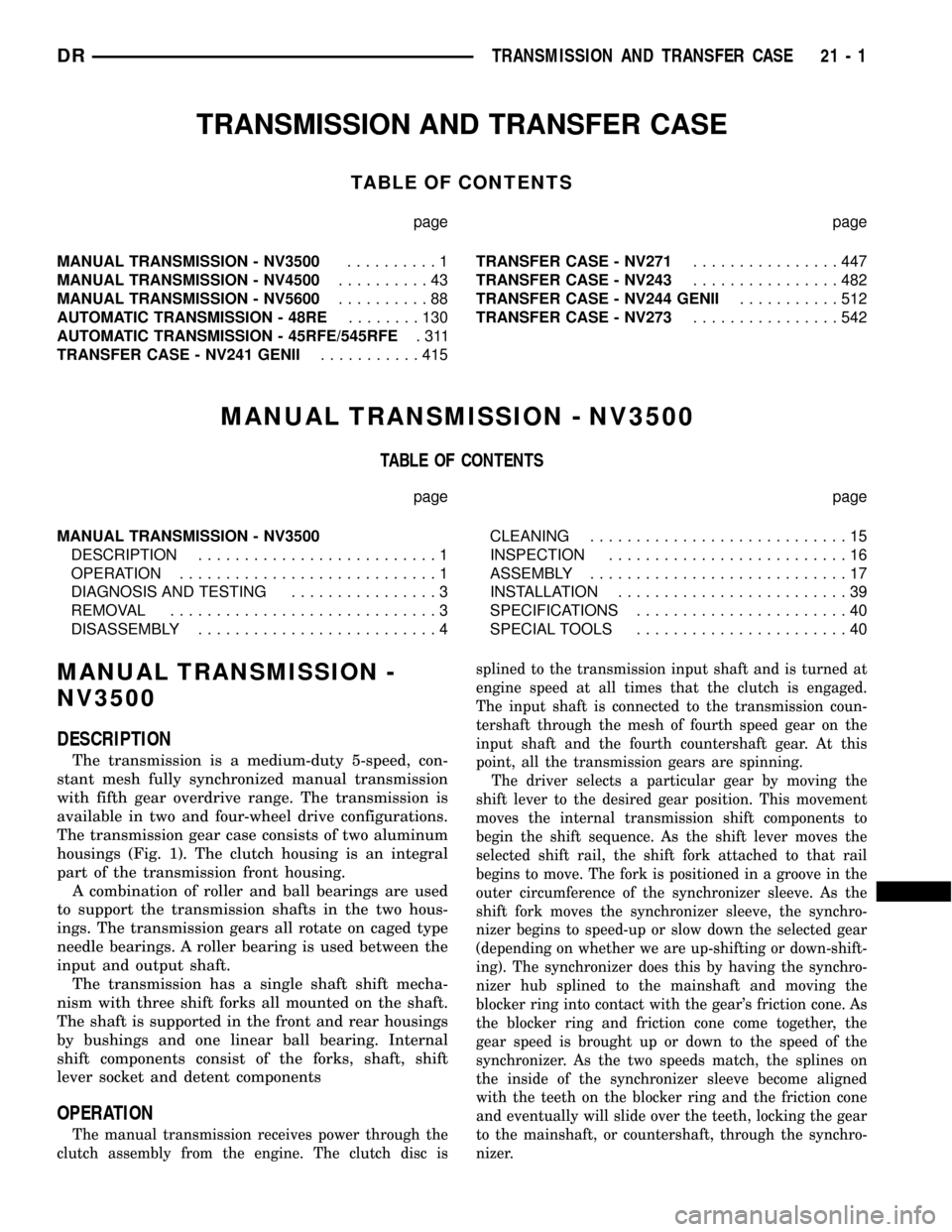
TRANSMISSION AND TRANSFER CASE
TABLE OF CONTENTS
page page
MANUAL TRANSMISSION - NV3500..........1
MANUAL TRANSMISSION - NV4500..........43
MANUAL TRANSMISSION - NV5600..........88
AUTOMATIC TRANSMISSION - 48RE........130
AUTOMATIC TRANSMISSION - 45RFE/545RFE.311
TRANSFER CASE - NV241 GENII...........415TRANSFER CASE - NV271................447
TRANSFER CASE - NV243................482
TRANSFER CASE - NV244 GENII...........512
TRANSFER CASE - NV273................542
MANUAL TRANSMISSION - NV3500
TABLE OF CONTENTS
page page
MANUAL TRANSMISSION - NV3500
DESCRIPTION..........................1
OPERATION............................1
DIAGNOSIS AND TESTING................3
REMOVAL.............................3
DISASSEMBLY..........................4CLEANING............................15
INSPECTION..........................16
ASSEMBLY............................17
INSTALLATION.........................39
SPECIFICATIONS.......................40
SPECIAL TOOLS.......................40
MANUAL TRANSMISSION -
NV3500
DESCRIPTION
The transmission is a medium-duty 5-speed, con-
stant mesh fully synchronized manual transmission
with fifth gear overdrive range. The transmission is
available in two and four-wheel drive configurations.
The transmission gear case consists of two aluminum
housings (Fig. 1). The clutch housing is an integral
part of the transmission front housing.
A combination of roller and ball bearings are used
to support the transmission shafts in the two hous-
ings. The transmission gears all rotate on caged type
needle bearings. A roller bearing is used between the
input and output shaft.
The transmission has a single shaft shift mecha-
nism with three shift forks all mounted on the shaft.
The shaft is supported in the front and rear housings
by bushings and one linear ball bearing. Internal
shift components consist of the forks, shaft, shift
lever socket and detent components
OPERATION
The manual transmission receives power through the
clutch assembly from the engine. The clutch disc issplined to the transmission input shaft and is turned at
engine speed at all times that the clutch is engaged.
The input shaft is connected to the transmission coun-
tershaft through the mesh of fourth speed gear on the
input shaft and the fourth countershaft gear. At this
point, all the transmission gears are spinning.
The driver selects a particular gear by moving the
shift lever to the desired gear position. This movement
moves the internal transmission shift components to
begin the shift sequence. As the shift lever moves the
selected shift rail, the shift fork attached to that rail
begins to move. The fork is positioned in a groove in the
outer circumference of the synchronizer sleeve. As the
shift fork moves the synchronizer sleeve, the synchro-
nizer begins to speed-up or slow down the selected gear
(depending on whether we are up-shifting or down-shift-
ing). The synchronizer does this by having the synchro-
nizer hub splined to the mainshaft and moving the
blocker ring into contact with the gear's friction cone. As
the blocker ring and friction cone come together, the
gear speed is brought up or down to the speed of the
synchronizer. As the two speeds match, the splines on
the inside of the synchronizer sleeve become aligned
with the teeth on the blocker ring and the friction cone
and eventually will slide over the teeth, locking the gear
to the mainshaft, or countershaft, through the synchro-
nizer.
DRTRANSMISSION AND TRANSFER CASE 21 - 1