Page 2145 of 2627
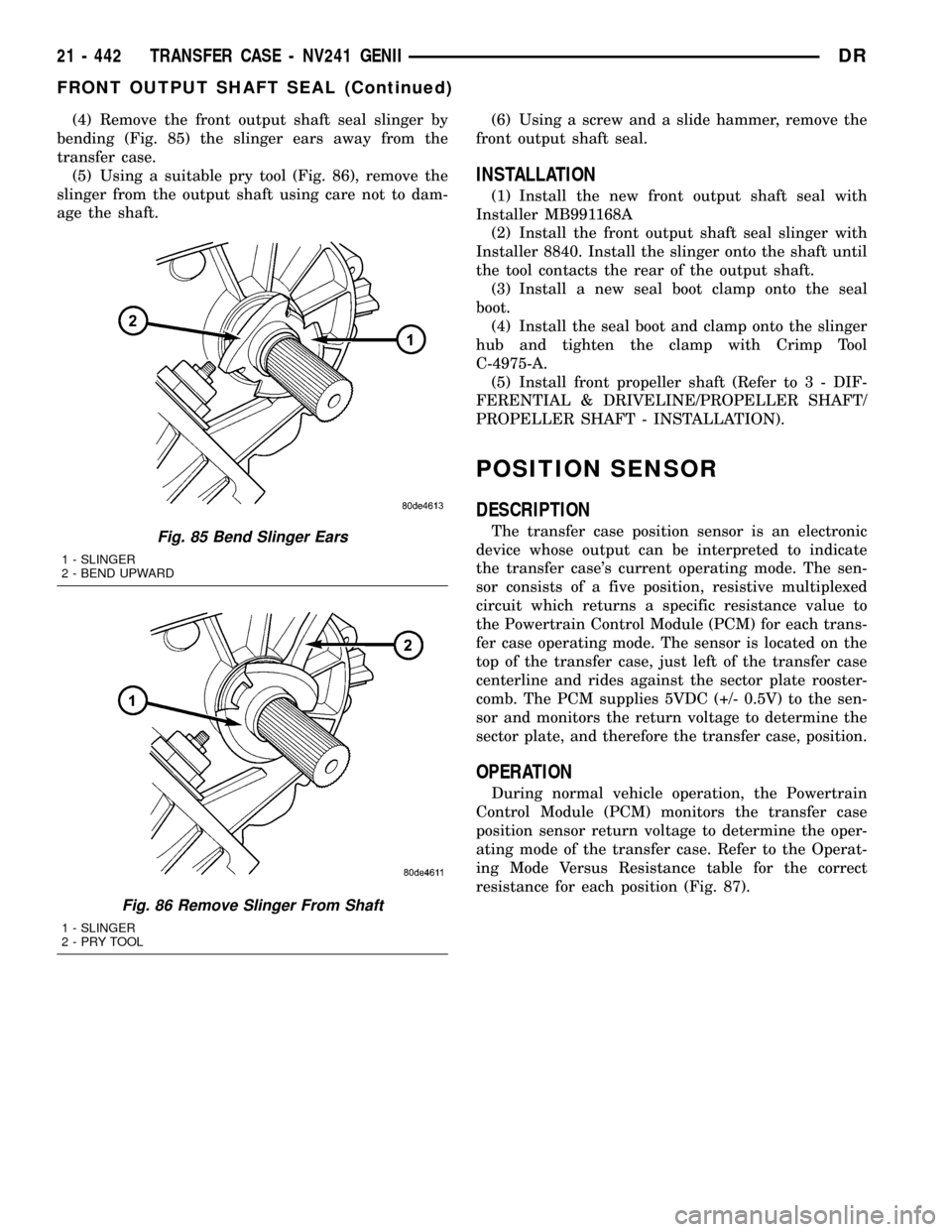
(4) Remove the front output shaft seal slinger by
bending (Fig. 85) the slinger ears away from the
transfer case.
(5) Using a suitable pry tool (Fig. 86), remove the
slinger from the output shaft using care not to dam-
age the shaft.(6) Using a screw and a slide hammer, remove the
front output shaft seal.
INSTALLATION
(1) Install the new front output shaft seal with
Installer MB991168A
(2) Install the front output shaft seal slinger with
Installer 8840. Install the slinger onto the shaft until
the tool contacts the rear of the output shaft.
(3) Install a new seal boot clamp onto the seal
boot.
(4) Install the seal boot and clamp onto the slinger
hub and tighten the clamp with Crimp Tool
C-4975-A.
(5) Install front propeller shaft (Refer to 3 - DIF-
FERENTIAL & DRIVELINE/PROPELLER SHAFT/
PROPELLER SHAFT - INSTALLATION).
POSITION SENSOR
DESCRIPTION
The transfer case position sensor is an electronic
device whose output can be interpreted to indicate
the transfer case's current operating mode. The sen-
sor consists of a five position, resistive multiplexed
circuit which returns a specific resistance value to
the Powertrain Control Module (PCM) for each trans-
fer case operating mode. The sensor is located on the
top of the transfer case, just left of the transfer case
centerline and rides against the sector plate rooster-
comb. The PCM supplies 5VDC (+/- 0.5V) to the sen-
sor and monitors the return voltage to determine the
sector plate, and therefore the transfer case, position.
OPERATION
During normal vehicle operation, the Powertrain
Control Module (PCM) monitors the transfer case
position sensor return voltage to determine the oper-
ating mode of the transfer case. Refer to the Operat-
ing Mode Versus Resistance table for the correct
resistance for each position (Fig. 87).
Fig. 85 Bend Slinger Ears
1 - SLINGER
2 - BEND UPWARD
Fig. 86 Remove Slinger From Shaft
1 - SLINGER
2-PRYTOOL
21 - 442 TRANSFER CASE - NV241 GENIIDR
FRONT OUTPUT SHAFT SEAL (Continued)
Page 2146 of 2627
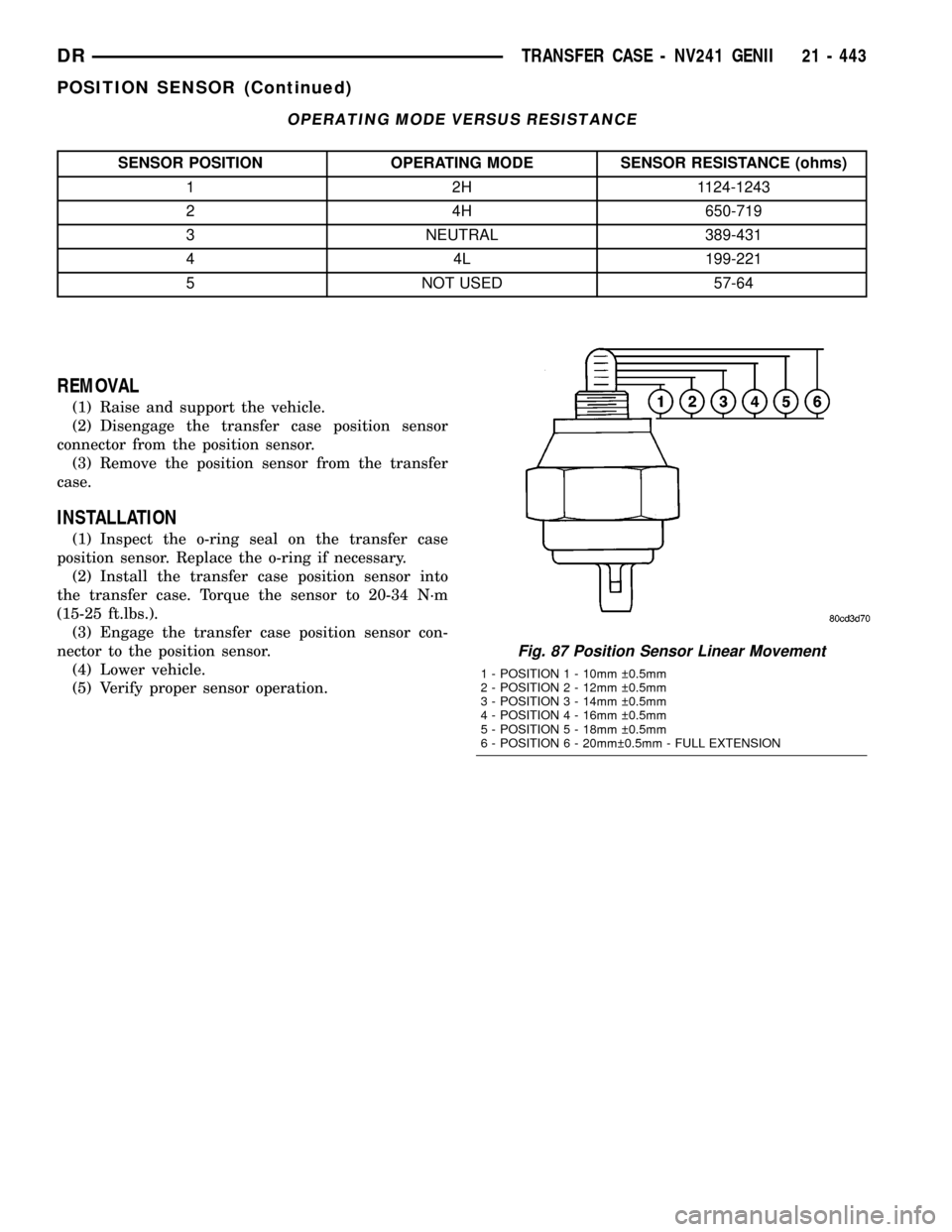
OPERATING MODE VERSUS RESISTANCE
SENSOR POSITION OPERATING MODE SENSOR RESISTANCE (ohms)
1 2H 1124-1243
2 4H 650-719
3 NEUTRAL 389-431
4 4L 199-221
5 NOT USED 57-64
REMOVAL
(1) Raise and support the vehicle.
(2) Disengage the transfer case position sensor
connector from the position sensor.
(3) Remove the position sensor from the transfer
case.
INSTALLATION
(1) Inspect the o-ring seal on the transfer case
position sensor. Replace the o-ring if necessary.
(2) Install the transfer case position sensor into
the transfer case. Torque the sensor to 20-34 N´m
(15-25 ft.lbs.).
(3) Engage the transfer case position sensor con-
nector to the position sensor.
(4) Lower vehicle.
(5) Verify proper sensor operation.
Fig. 87 Position Sensor Linear Movement
1 - POSITION 1 - 10mm 0.5mm
2 - POSITION 2 - 12mm 0.5mm
3 - POSITION 3 - 14mm 0.5mm
4 - POSITION 4 - 16mm 0.5mm
5 - POSITION 5 - 18mm 0.5mm
6 - POSITION 6 - 20mm 0.5mm - FULL EXTENSION
DRTRANSFER CASE - NV241 GENII 21 - 443
POSITION SENSOR (Continued)
Page 2147 of 2627
SHIFT LEVER
REMOVAL
(1) Shift transfer case into 2H.
(2) Raise and support the vehicle.
(3) Loosen adjusting trunnion lock bolt and slide
shift rod out of trunnion. If rod lacks enough travel
to come out of trunnion, push trunnion out of shift
lever.
(4) Lower vehicle.
(5) Remove transfer case shifter knob cap.
(6) Remove nut holding shifter knob to shift lever.
(7) Remove shifter knob.
(8) Remove the shift boot from the shifter console.
(9) Remove the bolts securing the shifter mecha-
nism to the floor pan (Fig. 88).
(10) Separate shift lever mechanism from the vehi-
cle.
Fig. 88 Transfer Case Shifter
1 - SHIFTER BOOT 4 - SHIFTER MECHANISM
2 - SHIFTER KNOB 5 - ALIGNMENT PIN
3 - SHIFTER CONSOLE 6 - TRANSFER CASE
21 - 444 TRANSFER CASE - NV241 GENIIDR
Page 2148 of 2627
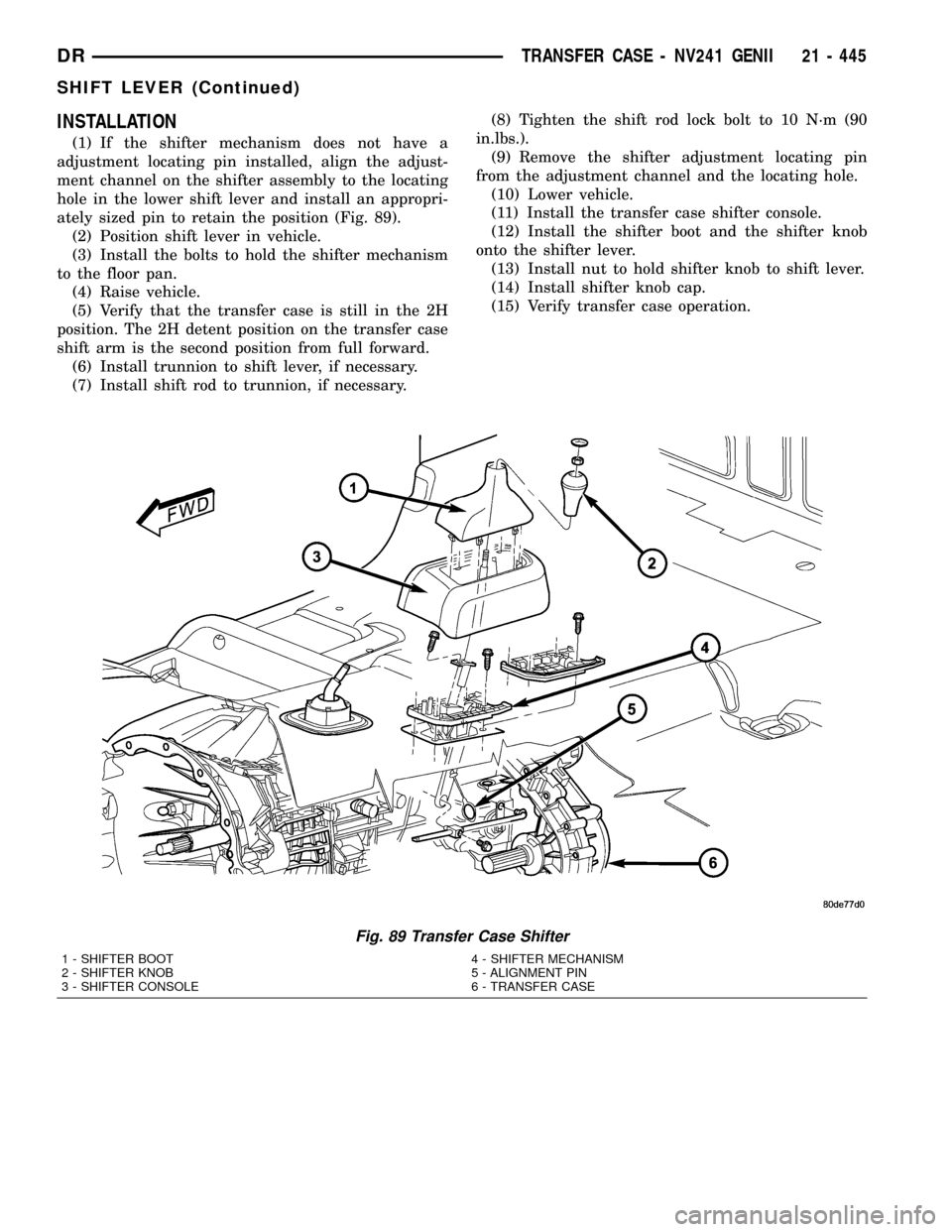
INSTALLATION
(1) If the shifter mechanism does not have a
adjustment locating pin installed, align the adjust-
ment channel on the shifter assembly to the locating
hole in the lower shift lever and install an appropri-
ately sized pin to retain the position (Fig. 89).
(2) Position shift lever in vehicle.
(3) Install the bolts to hold the shifter mechanism
to the floor pan.
(4) Raise vehicle.
(5) Verify that the transfer case is still in the 2H
position. The 2H detent position on the transfer case
shift arm is the second position from full forward.
(6) Install trunnion to shift lever, if necessary.
(7) Install shift rod to trunnion, if necessary.(8) Tighten the shift rod lock bolt to 10 N´m (90
in.lbs.).
(9) Remove the shifter adjustment locating pin
from the adjustment channel and the locating hole.
(10) Lower vehicle.
(11) Install the transfer case shifter console.
(12) Install the shifter boot and the shifter knob
onto the shifter lever.
(13) Install nut to hold shifter knob to shift lever.
(14) Install shifter knob cap.
(15) Verify transfer case operation.
Fig. 89 Transfer Case Shifter
1 - SHIFTER BOOT 4 - SHIFTER MECHANISM
2 - SHIFTER KNOB 5 - ALIGNMENT PIN
3 - SHIFTER CONSOLE 6 - TRANSFER CASE
DRTRANSFER CASE - NV241 GENII 21 - 445
SHIFT LEVER (Continued)
Page 2149 of 2627
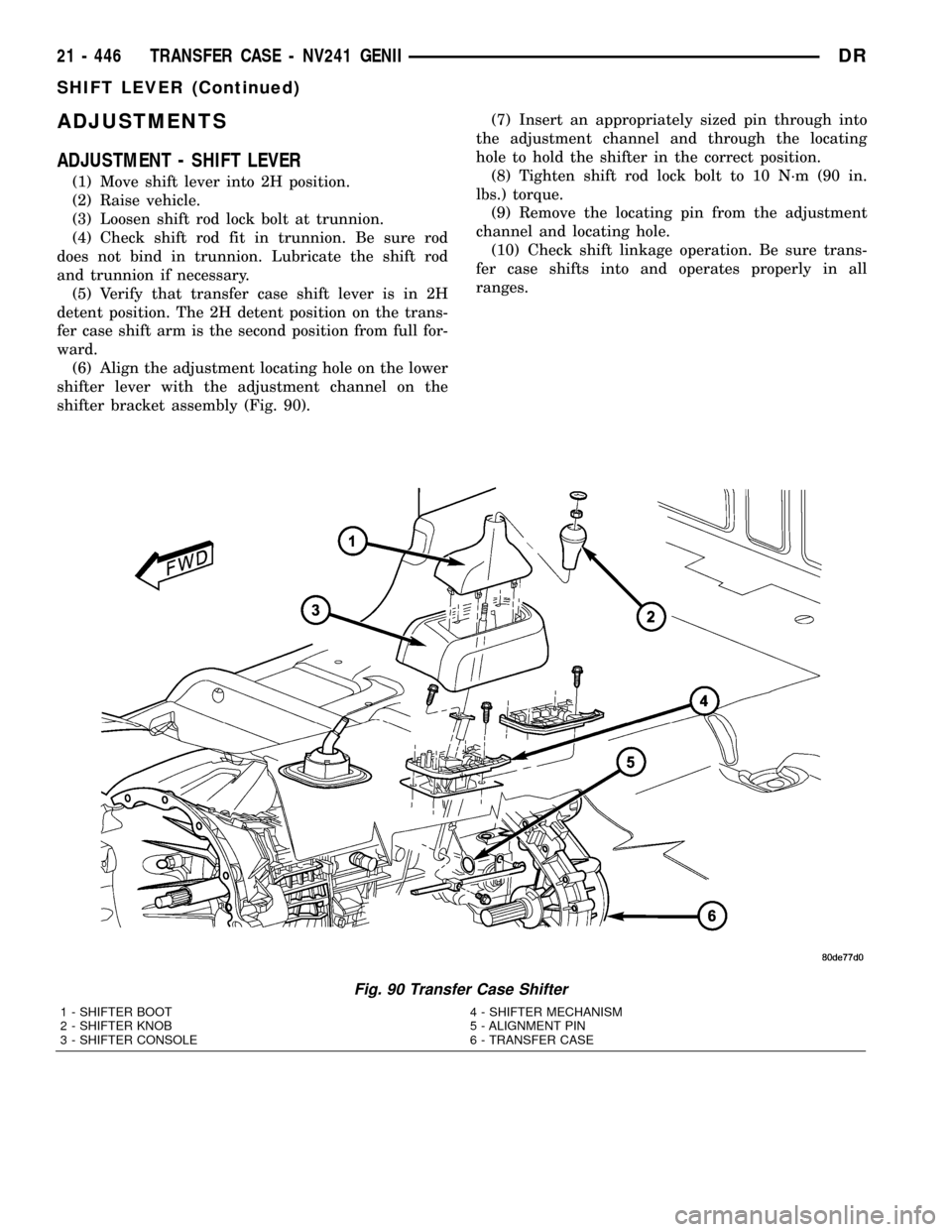
ADJUSTMENTS
ADJUSTMENT - SHIFT LEVER
(1) Move shift lever into 2H position.
(2) Raise vehicle.
(3) Loosen shift rod lock bolt at trunnion.
(4) Check shift rod fit in trunnion. Be sure rod
does not bind in trunnion. Lubricate the shift rod
and trunnion if necessary.
(5) Verify that transfer case shift lever is in 2H
detent position. The 2H detent position on the trans-
fer case shift arm is the second position from full for-
ward.
(6) Align the adjustment locating hole on the lower
shifter lever with the adjustment channel on the
shifter bracket assembly (Fig. 90).(7) Insert an appropriately sized pin through into
the adjustment channel and through the locating
hole to hold the shifter in the correct position.
(8) Tighten shift rod lock bolt to 10 N´m (90 in.
lbs.) torque.
(9) Remove the locating pin from the adjustment
channel and locating hole.
(10) Check shift linkage operation. Be sure trans-
fer case shifts into and operates properly in all
ranges.
Fig. 90 Transfer Case Shifter
1 - SHIFTER BOOT 4 - SHIFTER MECHANISM
2 - SHIFTER KNOB 5 - ALIGNMENT PIN
3 - SHIFTER CONSOLE 6 - TRANSFER CASE
21 - 446 TRANSFER CASE - NV241 GENIIDR
SHIFT LEVER (Continued)
Page 2150 of 2627
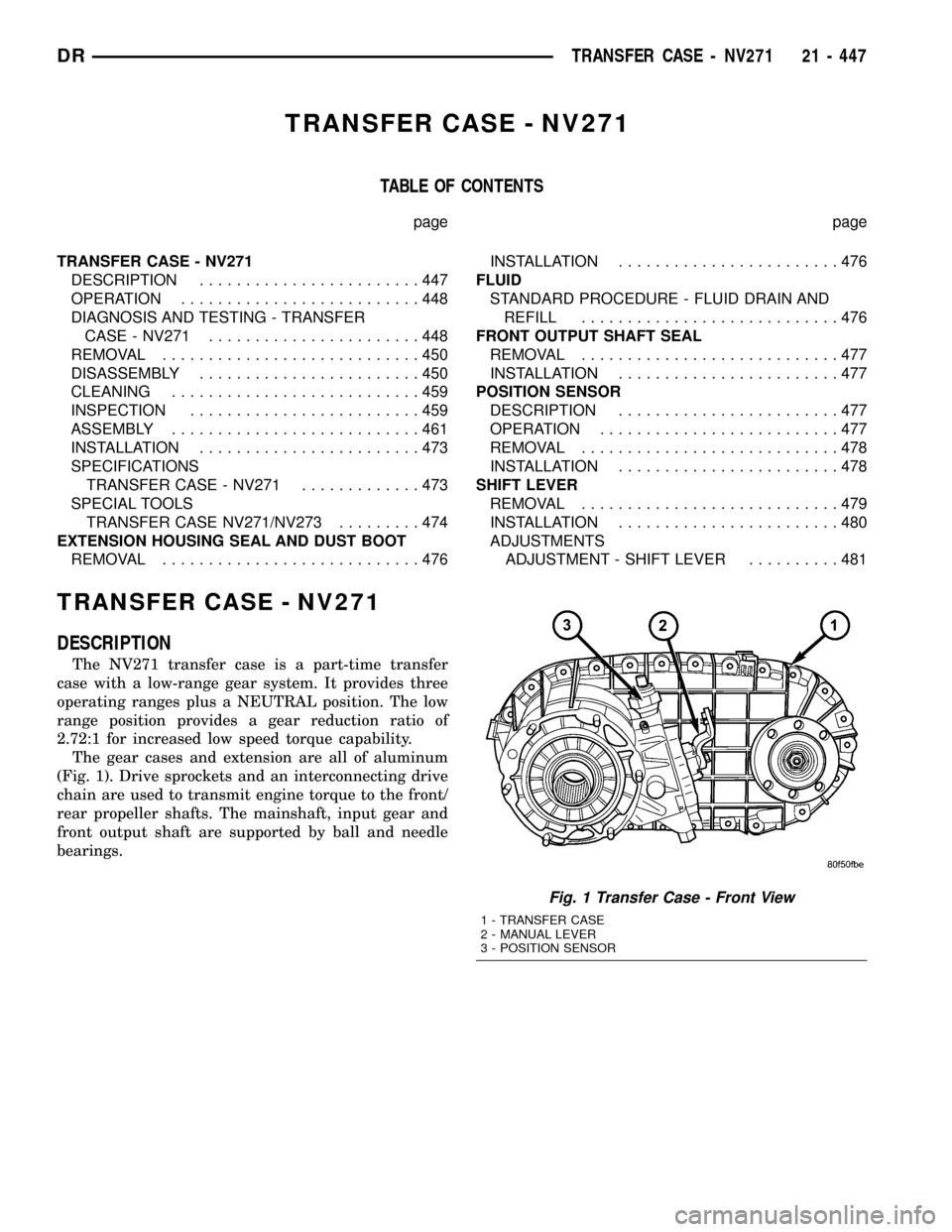
TRANSFER CASE - NV271
TABLE OF CONTENTS
page page
TRANSFER CASE - NV271
DESCRIPTION........................447
OPERATION..........................448
DIAGNOSIS AND TESTING - TRANSFER
CASE - NV271.......................448
REMOVAL............................450
DISASSEMBLY........................450
CLEANING...........................459
INSPECTION.........................459
ASSEMBLY...........................461
INSTALLATION........................473
SPECIFICATIONS
TRANSFER CASE - NV271.............473
SPECIAL TOOLS
TRANSFER CASE NV271/NV273.........474
EXTENSION HOUSING SEAL AND DUST BOOT
REMOVAL............................476INSTALLATION........................476
FLUID
STANDARD PROCEDURE - FLUID DRAIN AND
REFILL............................476
FRONT OUTPUT SHAFT SEAL
REMOVAL............................477
INSTALLATION........................477
POSITION SENSOR
DESCRIPTION........................477
OPERATION..........................477
REMOVAL............................478
INSTALLATION........................478
SHIFT LEVER
REMOVAL............................479
INSTALLATION........................480
ADJUSTMENTS
ADJUSTMENT - SHIFT LEVER..........481
TRANSFER CASE - NV271
DESCRIPTION
The NV271 transfer case is a part-time transfer
case with a low-range gear system. It provides three
operating ranges plus a NEUTRAL position. The low
range position provides a gear reduction ratio of
2.72:1 for increased low speed torque capability.
The gear cases and extension are all of aluminum
(Fig. 1). Drive sprockets and an interconnecting drive
chain are used to transmit engine torque to the front/
rear propeller shafts. The mainshaft, input gear and
front output shaft are supported by ball and needle
bearings.
Fig. 1 Transfer Case - Front View
1 - TRANSFER CASE
2 - MANUAL LEVER
3 - POSITION SENSOR
DRTRANSFER CASE - NV271 21 - 447
Page 2151 of 2627
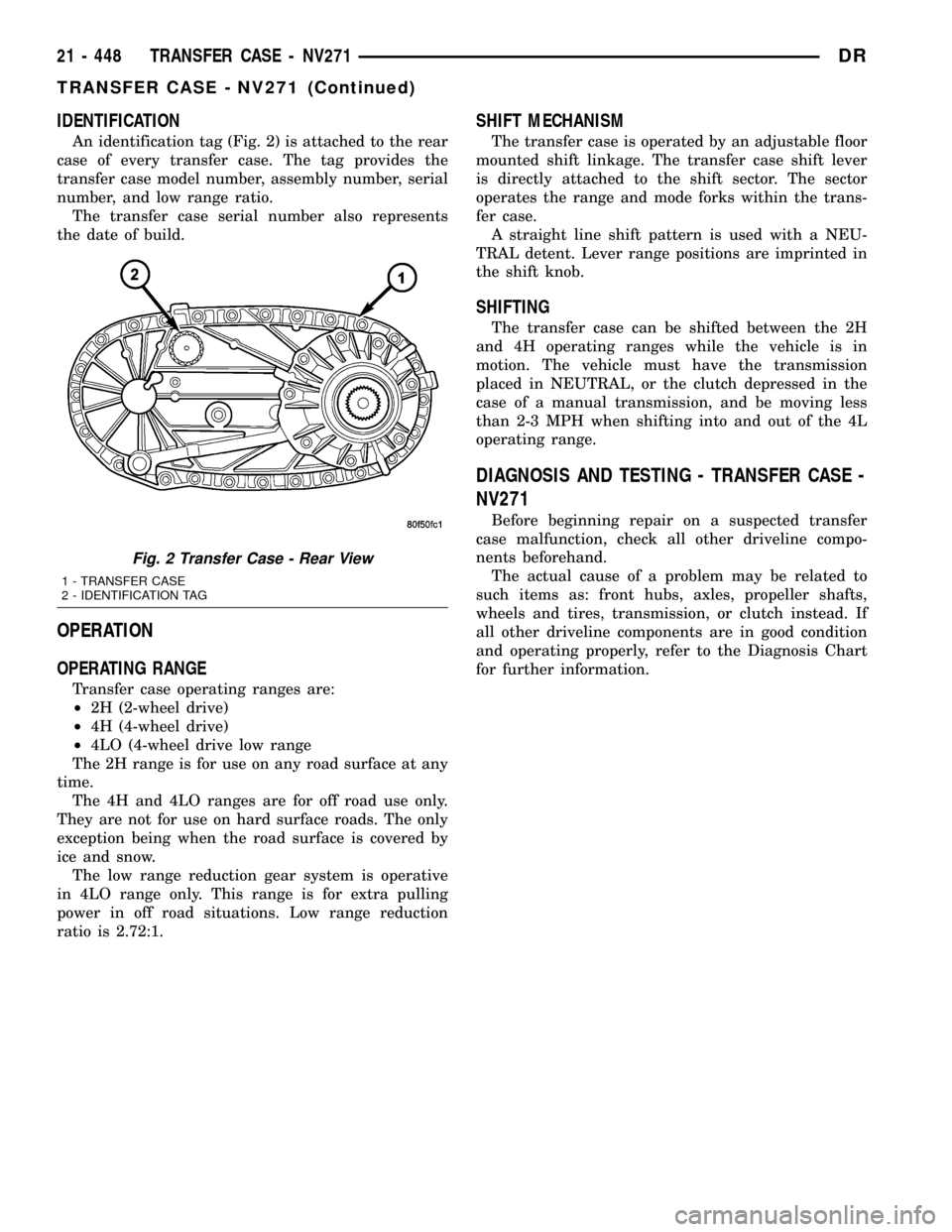
IDENTIFICATION
An identification tag (Fig. 2) is attached to the rear
case of every transfer case. The tag provides the
transfer case model number, assembly number, serial
number, and low range ratio.
The transfer case serial number also represents
the date of build.
OPERATION
OPERATING RANGE
Transfer case operating ranges are:
²2H (2-wheel drive)
²4H (4-wheel drive)
²4LO (4-wheel drive low range
The 2H range is for use on any road surface at any
time.
The 4H and 4LO ranges are for off road use only.
They are not for use on hard surface roads. The only
exception being when the road surface is covered by
ice and snow.
The low range reduction gear system is operative
in 4LO range only. This range is for extra pulling
power in off road situations. Low range reduction
ratio is 2.72:1.
SHIFT MECHANISM
The transfer case is operated by an adjustable floor
mounted shift linkage. The transfer case shift lever
is directly attached to the shift sector. The sector
operates the range and mode forks within the trans-
fer case.
A straight line shift pattern is used with a NEU-
TRAL detent. Lever range positions are imprinted in
the shift knob.
SHIFTING
The transfer case can be shifted between the 2H
and 4H operating ranges while the vehicle is in
motion. The vehicle must have the transmission
placed in NEUTRAL, or the clutch depressed in the
case of a manual transmission, and be moving less
than 2-3 MPH when shifting into and out of the 4L
operating range.
DIAGNOSIS AND TESTING - TRANSFER CASE -
NV271
Before beginning repair on a suspected transfer
case malfunction, check all other driveline compo-
nents beforehand.
The actual cause of a problem may be related to
such items as: front hubs, axles, propeller shafts,
wheels and tires, transmission, or clutch instead. If
all other driveline components are in good condition
and operating properly, refer to the Diagnosis Chart
for further information.
Fig. 2 Transfer Case - Rear View
1 - TRANSFER CASE
2 - IDENTIFICATION TAG
21 - 448 TRANSFER CASE - NV271DR
TRANSFER CASE - NV271 (Continued)
Page 2152 of 2627
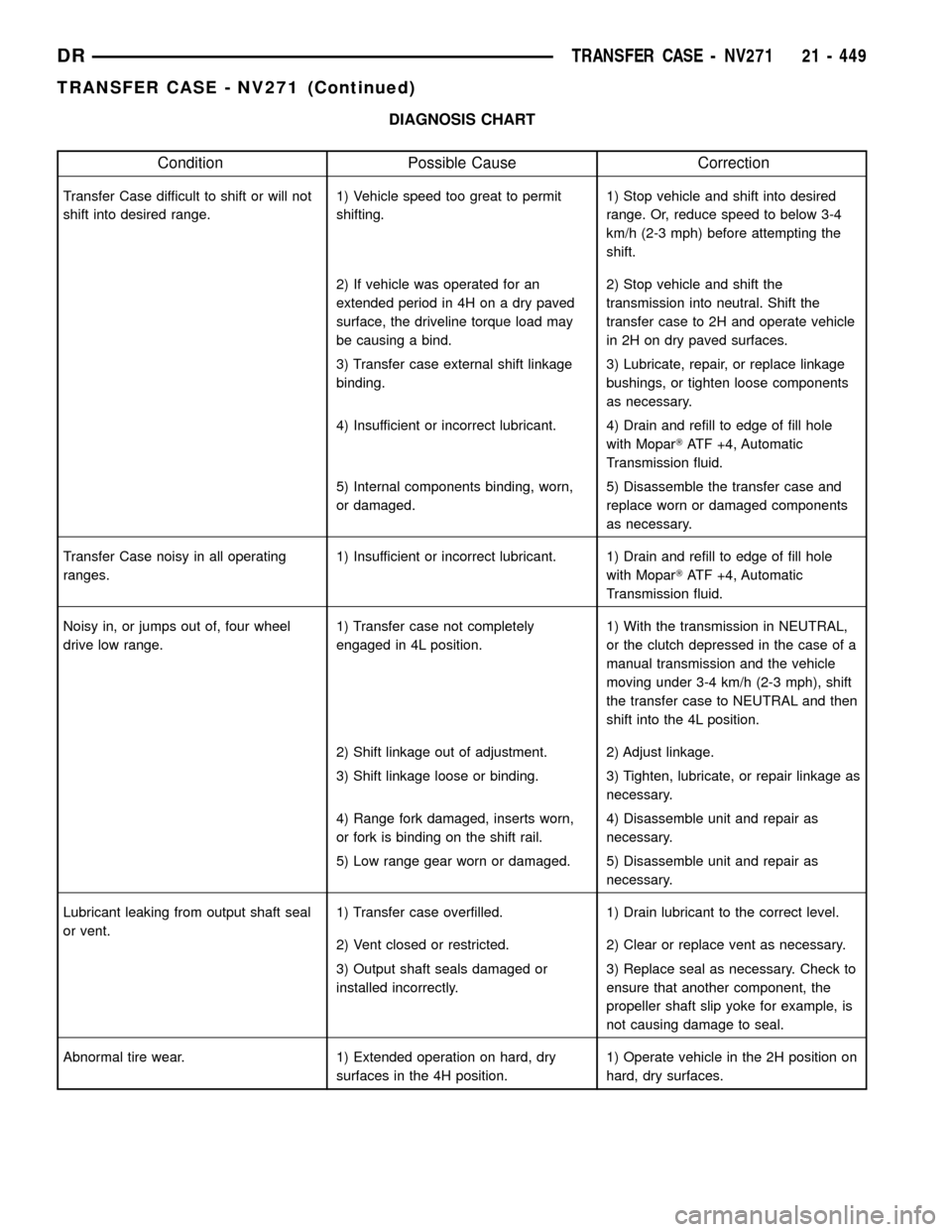
DIAGNOSIS CHART
Condition Possible Cause Correction
Transfer Case difficult to shift or will not
shift into desired range.1) Vehicle speed too great to permit
shifting.1) Stop vehicle and shift into desired
range. Or, reduce speed to below 3-4
km/h (2-3 mph) before attempting the
shift.
2) If vehicle was operated for an
extended period in 4H on a dry paved
surface, the driveline torque load may
be causing a bind.2) Stop vehicle and shift the
transmission into neutral. Shift the
transfer case to 2H and operate vehicle
in 2H on dry paved surfaces.
3) Transfer case external shift linkage
binding.3) Lubricate, repair, or replace linkage
bushings, or tighten loose components
as necessary.
4) Insufficient or incorrect lubricant. 4) Drain and refill to edge of fill hole
with MoparTATF +4, Automatic
Transmission fluid.
5) Internal components binding, worn,
or damaged.5) Disassemble the transfer case and
replace worn or damaged components
as necessary.
Transfer Case noisy in all operating
ranges.1) Insufficient or incorrect lubricant. 1) Drain and refill to edge of fill hole
with MoparTATF +4, Automatic
Transmission fluid.
Noisy in, or jumps out of, four wheel
drive low range.1) Transfer case not completely
engaged in 4L position.1) With the transmission in NEUTRAL,
or the clutch depressed in the case of a
manual transmission and the vehicle
moving under 3-4 km/h (2-3 mph), shift
the transfer case to NEUTRAL and then
shift into the 4L position.
2) Shift linkage out of adjustment. 2) Adjust linkage.
3) Shift linkage loose or binding. 3) Tighten, lubricate, or repair linkage as
necessary.
4) Range fork damaged, inserts worn,
or fork is binding on the shift rail.4) Disassemble unit and repair as
necessary.
5) Low range gear worn or damaged. 5) Disassemble unit and repair as
necessary.
Lubricant leaking from output shaft seal
or vent.1) Transfer case overfilled. 1) Drain lubricant to the correct level.
2) Vent closed or restricted. 2) Clear or replace vent as necessary.
3) Output shaft seals damaged or
installed incorrectly.3) Replace seal as necessary. Check to
ensure that another component, the
propeller shaft slip yoke for example, is
not causing damage to seal.
Abnormal tire wear. 1) Extended operation on hard, dry
surfaces in the 4H position.1) Operate vehicle in the 2H position on
hard, dry surfaces.
DRTRANSFER CASE - NV271 21 - 449
TRANSFER CASE - NV271 (Continued)