Page 2017 of 2627
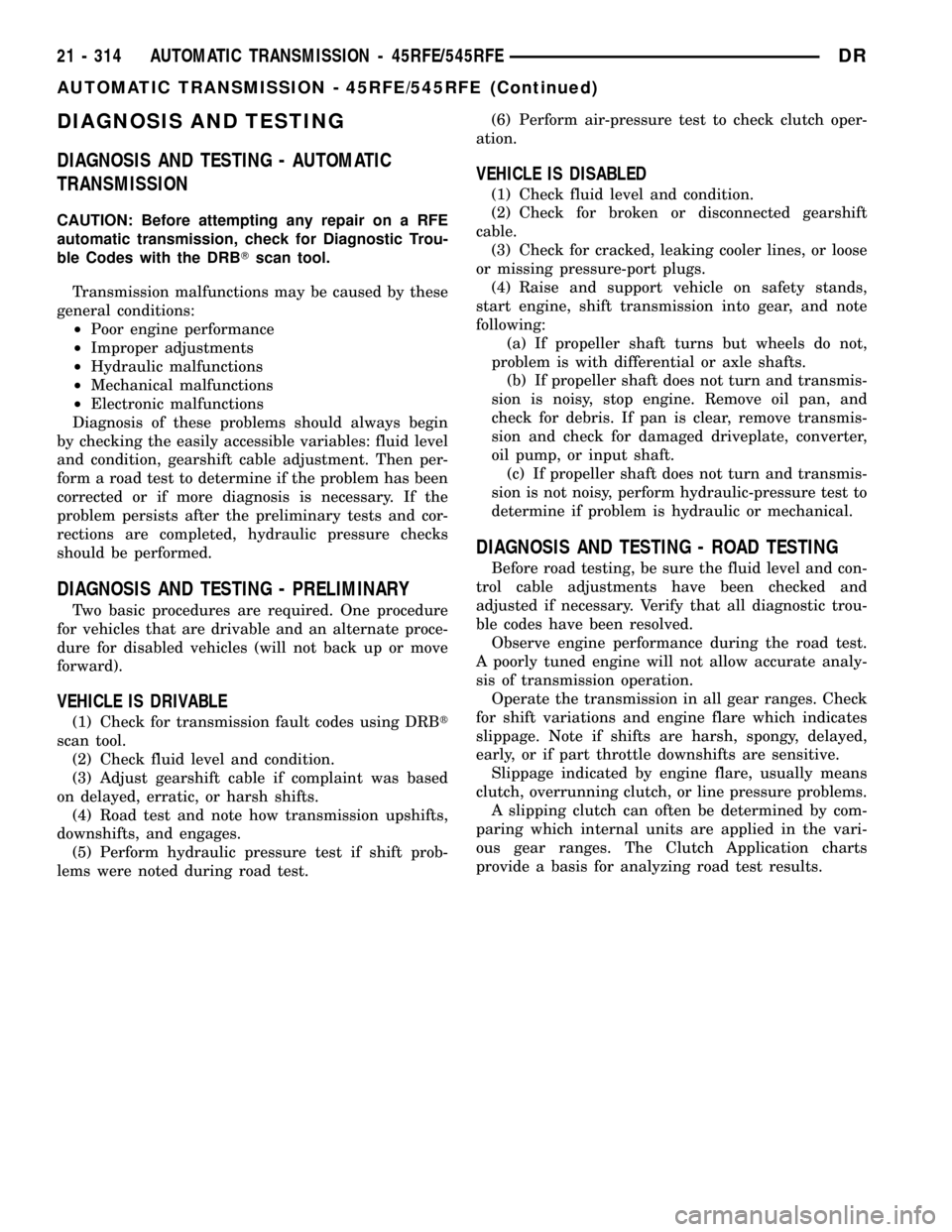
DIAGNOSIS AND TESTING
DIAGNOSIS AND TESTING - AUTOMATIC
TRANSMISSION
CAUTION: Before attempting any repair on a RFE
automatic transmission, check for Diagnostic Trou-
ble Codes with the DRBTscan tool.
Transmission malfunctions may be caused by these
general conditions:
²Poor engine performance
²Improper adjustments
²Hydraulic malfunctions
²Mechanical malfunctions
²Electronic malfunctions
Diagnosis of these problems should always begin
by checking the easily accessible variables: fluid level
and condition, gearshift cable adjustment. Then per-
form a road test to determine if the problem has been
corrected or if more diagnosis is necessary. If the
problem persists after the preliminary tests and cor-
rections are completed, hydraulic pressure checks
should be performed.
DIAGNOSIS AND TESTING - PRELIMINARY
Two basic procedures are required. One procedure
for vehicles that are drivable and an alternate proce-
dure for disabled vehicles (will not back up or move
forward).
VEHICLE IS DRIVABLE
(1) Check for transmission fault codes using DRBt
scan tool.
(2) Check fluid level and condition.
(3) Adjust gearshift cable if complaint was based
on delayed, erratic, or harsh shifts.
(4) Road test and note how transmission upshifts,
downshifts, and engages.
(5) Perform hydraulic pressure test if shift prob-
lems were noted during road test.(6) Perform air-pressure test to check clutch oper-
ation.
VEHICLE IS DISABLED
(1) Check fluid level and condition.
(2) Check for broken or disconnected gearshift
cable.
(3) Check for cracked, leaking cooler lines, or loose
or missing pressure-port plugs.
(4) Raise and support vehicle on safety stands,
start engine, shift transmission into gear, and note
following:
(a) If propeller shaft turns but wheels do not,
problem is with differential or axle shafts.
(b) If propeller shaft does not turn and transmis-
sion is noisy, stop engine. Remove oil pan, and
check for debris. If pan is clear, remove transmis-
sion and check for damaged driveplate, converter,
oil pump, or input shaft.
(c) If propeller shaft does not turn and transmis-
sion is not noisy, perform hydraulic-pressure test to
determine if problem is hydraulic or mechanical.
DIAGNOSIS AND TESTING - ROAD TESTING
Before road testing, be sure the fluid level and con-
trol cable adjustments have been checked and
adjusted if necessary. Verify that all diagnostic trou-
ble codes have been resolved.
Observe engine performance during the road test.
A poorly tuned engine will not allow accurate analy-
sis of transmission operation.
Operate the transmission in all gear ranges. Check
for shift variations and engine flare which indicates
slippage. Note if shifts are harsh, spongy, delayed,
early, or if part throttle downshifts are sensitive.
Slippage indicated by engine flare, usually means
clutch, overrunning clutch, or line pressure problems.
A slipping clutch can often be determined by com-
paring which internal units are applied in the vari-
ous gear ranges. The Clutch Application charts
provide a basis for analyzing road test results.
21 - 314 AUTOMATIC TRANSMISSION - 45RFE/545RFEDR
AUTOMATIC TRANSMISSION - 45RFE/545RFE (Continued)
Page 2018 of 2627
45RFE CLUTCH APPLICATION CHART
SLP UD OD R 2C 4C L/R OVERRUNNING
P±PARKON
R±REVERSEON ON
N-NEUTRALON
D±OVERDRIVE
FIRSTON ON* ON
SECONDON ON
SECOND PRIMEON ON
THIRDON ON
FOURTHON ON
LIMP-INON ON
2±FIRSTON ON* ON
SECONDON ON
LIMP-INON ON
1±LOWON ON ON
*L/R clutch is on only with the output shaft speed below 150 rpm.
545RFE CLUTCH APPLICATION CHART
SLP UD OD R 2C 4C L/R OVERRUNNING
P±PARKON
R±REVERSEON ON
N-NEUTRALON
D±OVERDRIVE
FIRSTON ON* ON
SECONDON ON
SECOND PRIMEON ON
THIRDON ON
FOURTHON ON
FIFTHON ON
LIMP-INON ON
2±FIRSTON ON* ON
SECONDON ON
LIMP-INON ON
1±LOWON ON ON
*L/R clutch is on only with the output shaft speed below 150 rpm.
DRAUTOMATIC TRANSMISSION - 45RFE/545RFE 21 - 315
AUTOMATIC TRANSMISSION - 45RFE/545RFE (Continued)
Page 2019 of 2627
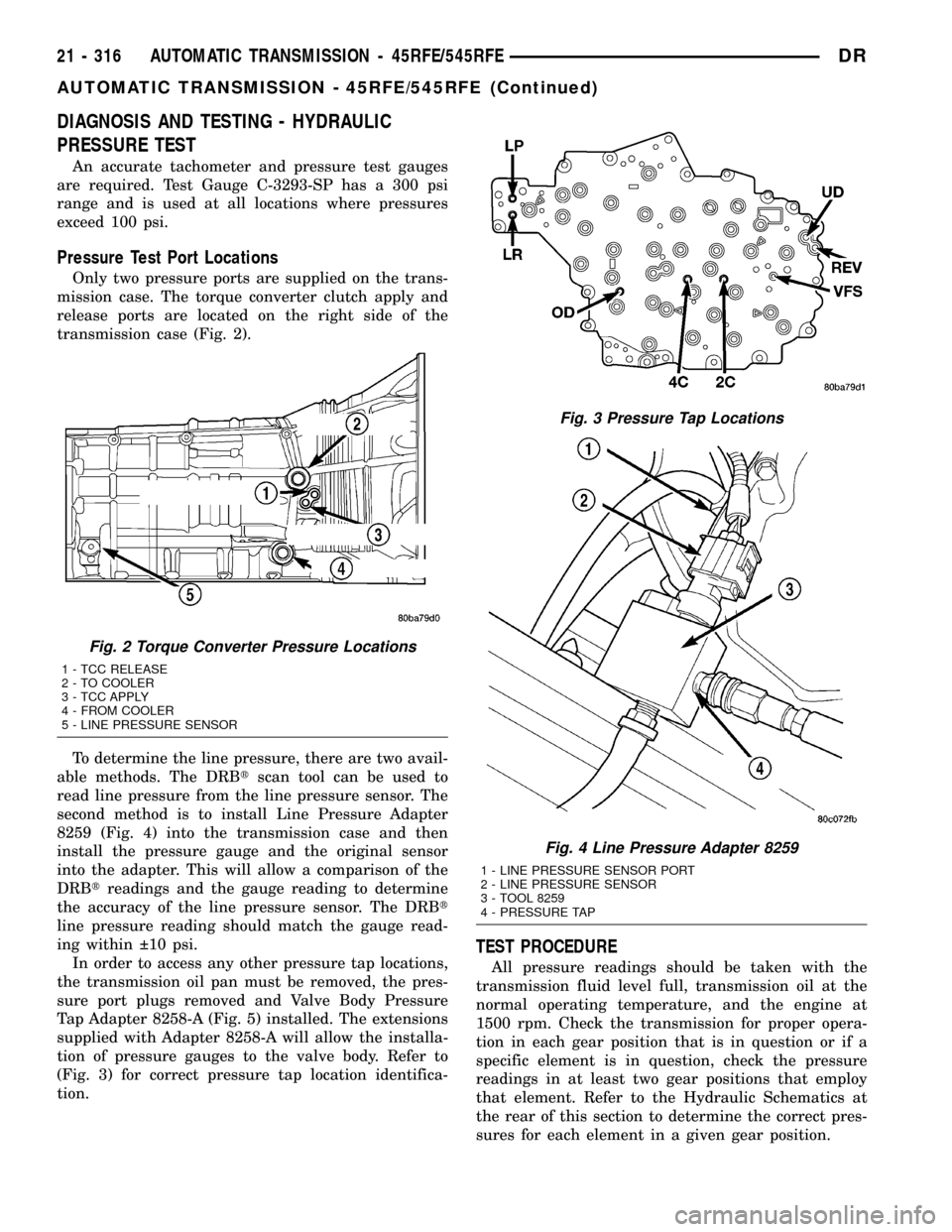
DIAGNOSIS AND TESTING - HYDRAULIC
PRESSURE TEST
An accurate tachometer and pressure test gauges
are required. Test Gauge C-3293-SP has a 300 psi
range and is used at all locations where pressures
exceed 100 psi.
Pressure Test Port Locations
Only two pressure ports are supplied on the trans-
mission case. The torque converter clutch apply and
release ports are located on the right side of the
transmission case (Fig. 2).
To determine the line pressure, there are two avail-
able methods. The DRBtscan tool can be used to
read line pressure from the line pressure sensor. The
second method is to install Line Pressure Adapter
8259 (Fig. 4) into the transmission case and then
install the pressure gauge and the original sensor
into the adapter. This will allow a comparison of the
DRBtreadings and the gauge reading to determine
the accuracy of the line pressure sensor. The DRBt
line pressure reading should match the gauge read-
ing within 10 psi.
In order to access any other pressure tap locations,
the transmission oil pan must be removed, the pres-
sure port plugs removed and Valve Body Pressure
Tap Adapter 8258-A (Fig. 5) installed. The extensions
supplied with Adapter 8258-A will allow the installa-
tion of pressure gauges to the valve body. Refer to
(Fig. 3) for correct pressure tap location identifica-
tion.
TEST PROCEDURE
All pressure readings should be taken with the
transmission fluid level full, transmission oil at the
normal operating temperature, and the engine at
1500 rpm. Check the transmission for proper opera-
tion in each gear position that is in question or if a
specific element is in question, check the pressure
readings in at least two gear positions that employ
that element. Refer to the Hydraulic Schematics at
the rear of this section to determine the correct pres-
sures for each element in a given gear position.
Fig. 2 Torque Converter Pressure Locations
1 - TCC RELEASE
2 - TO COOLER
3 - TCC APPLY
4 - FROM COOLER
5 - LINE PRESSURE SENSOR
Fig. 3 Pressure Tap Locations
Fig. 4 Line Pressure Adapter 8259
1 - LINE PRESSURE SENSOR PORT
2 - LINE PRESSURE SENSOR
3 - TOOL 8259
4 - PRESSURE TAP
21 - 316 AUTOMATIC TRANSMISSION - 45RFE/545RFEDR
AUTOMATIC TRANSMISSION - 45RFE/545RFE (Continued)
Page 2020 of 2627
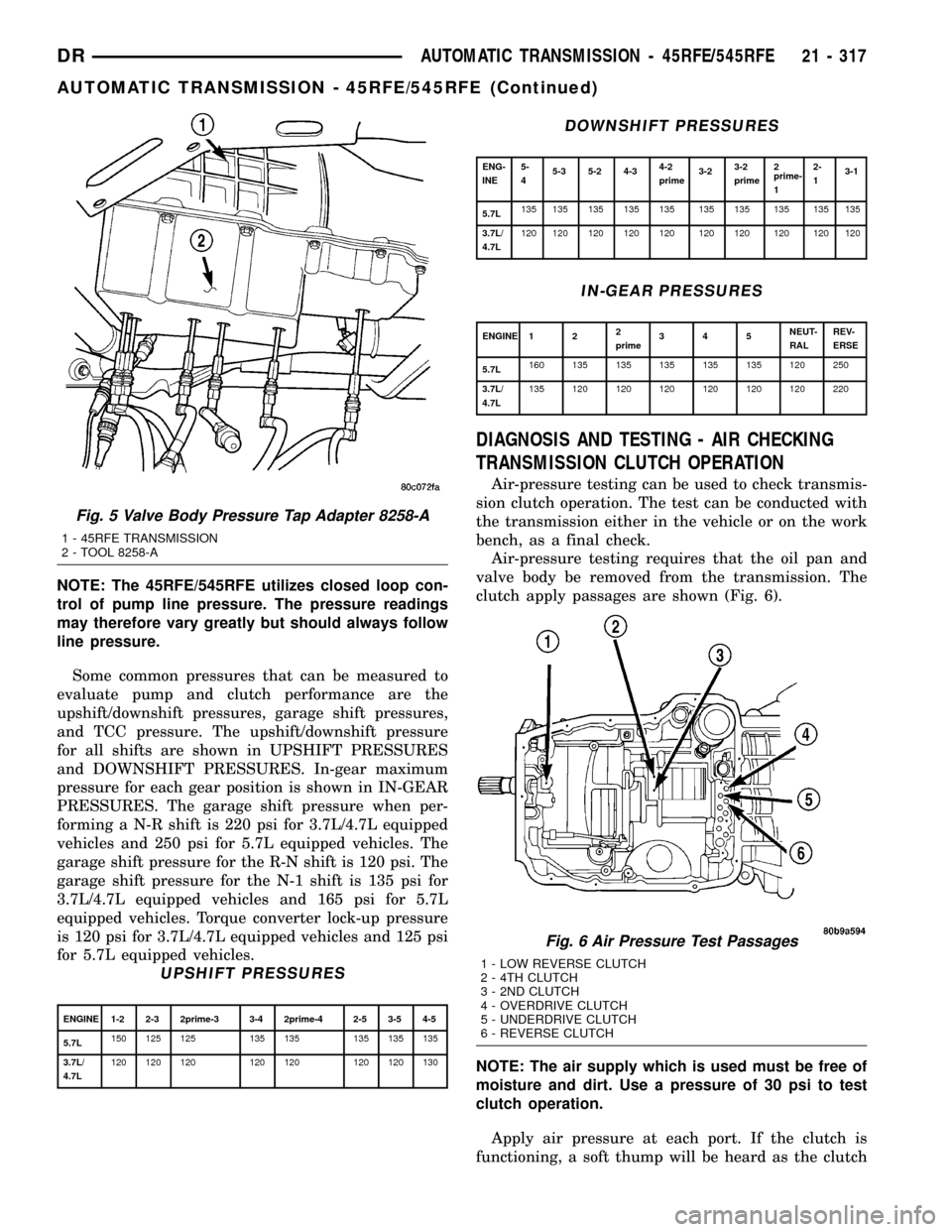
NOTE: The 45RFE/545RFE utilizes closed loop con-
trol of pump line pressure. The pressure readings
may therefore vary greatly but should always follow
line pressure.
Some common pressures that can be measured to
evaluate pump and clutch performance are the
upshift/downshift pressures, garage shift pressures,
and TCC pressure. The upshift/downshift pressure
for all shifts are shown in UPSHIFT PRESSURES
and DOWNSHIFT PRESSURES. In-gear maximum
pressure for each gear position is shown in IN-GEAR
PRESSURES. The garage shift pressure when per-
forming a N-R shift is 220 psi for 3.7L/4.7L equipped
vehicles and 250 psi for 5.7L equipped vehicles. The
garage shift pressure for the R-N shift is 120 psi. The
garage shift pressure for the N-1 shift is 135 psi for
3.7L/4.7L equipped vehicles and 165 psi for 5.7L
equipped vehicles. Torque converter lock-up pressure
is 120 psi for 3.7L/4.7L equipped vehicles and 125 psi
for 5.7L equipped vehicles.
UPSHIFT PRESSURES
ENGINE 1-2 2-3 2prime-3 3-4 2prime-4 2-5 3-5 4-5
5.7L150 125 125 135 135 135 135 135
3.7L/
4.7L120 120 120 120 120 120 120 130
DOWNSHIFT PRESSURES
ENG-
INE5-
45-3 5-2 4-34-2
prime3-23-2
prime2
prime-
12-
13-1
5.7L135 135 135 135 135 135 135 135 135 135
3.7L/
4.7L120 120 120 120 120 120 120 120 120 120
IN-GEAR PRESSURES
ENGINE 1 22
prime345NEUT-
RALREV-
ERSE
5.7L160 135 135 135 135 135 120 250
3.7L/
4.7L135 120 120 120 120 120 120 220
DIAGNOSIS AND TESTING - AIR CHECKING
TRANSMISSION CLUTCH OPERATION
Air-pressure testing can be used to check transmis-
sion clutch operation. The test can be conducted with
the transmission either in the vehicle or on the work
bench, as a final check.
Air-pressure testing requires that the oil pan and
valve body be removed from the transmission. The
clutch apply passages are shown (Fig. 6).
NOTE: The air supply which is used must be free of
moisture and dirt. Use a pressure of 30 psi to test
clutch operation.
Apply air pressure at each port. If the clutch is
functioning, a soft thump will be heard as the clutch
Fig. 5 Valve Body Pressure Tap Adapter 8258-A
1 - 45RFE TRANSMISSION
2 - TOOL 8258-A
Fig. 6 Air Pressure Test Passages
1 - LOW REVERSE CLUTCH
2 - 4TH CLUTCH
3 - 2ND CLUTCH
4 - OVERDRIVE CLUTCH
5 - UNDERDRIVE CLUTCH
6 - REVERSE CLUTCH
DRAUTOMATIC TRANSMISSION - 45RFE/545RFE 21 - 317
AUTOMATIC TRANSMISSION - 45RFE/545RFE (Continued)
Page 2021 of 2627
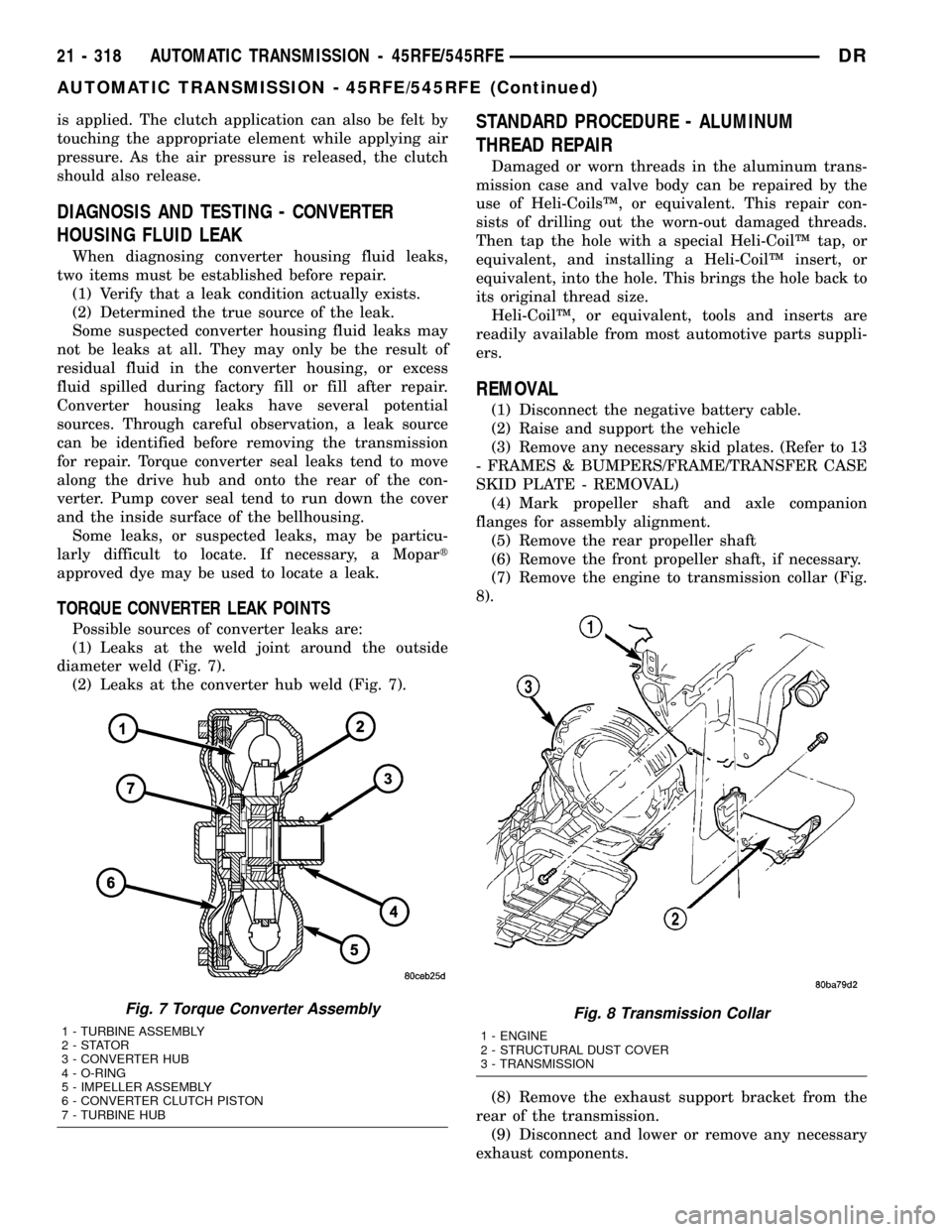
is applied. The clutch application can also be felt by
touching the appropriate element while applying air
pressure. As the air pressure is released, the clutch
should also release.
DIAGNOSIS AND TESTING - CONVERTER
HOUSING FLUID LEAK
When diagnosing converter housing fluid leaks,
two items must be established before repair.
(1) Verify that a leak condition actually exists.
(2) Determined the true source of the leak.
Some suspected converter housing fluid leaks may
not be leaks at all. They may only be the result of
residual fluid in the converter housing, or excess
fluid spilled during factory fill or fill after repair.
Converter housing leaks have several potential
sources. Through careful observation, a leak source
can be identified before removing the transmission
for repair. Torque converter seal leaks tend to move
along the drive hub and onto the rear of the con-
verter. Pump cover seal tend to run down the cover
and the inside surface of the bellhousing.
Some leaks, or suspected leaks, may be particu-
larly difficult to locate. If necessary, a Mopart
approved dye may be used to locate a leak.
TORQUE CONVERTER LEAK POINTS
Possible sources of converter leaks are:
(1) Leaks at the weld joint around the outside
diameter weld (Fig. 7).
(2) Leaks at the converter hub weld (Fig. 7).
STANDARD PROCEDURE - ALUMINUM
THREAD REPAIR
Damaged or worn threads in the aluminum trans-
mission case and valve body can be repaired by the
use of Heli-CoilsŸ, or equivalent. This repair con-
sists of drilling out the worn-out damaged threads.
Then tap the hole with a special Heli-CoilŸ tap, or
equivalent, and installing a Heli-CoilŸ insert, or
equivalent, into the hole. This brings the hole back to
its original thread size.
Heli-CoilŸ, or equivalent, tools and inserts are
readily available from most automotive parts suppli-
ers.
REMOVAL
(1) Disconnect the negative battery cable.
(2) Raise and support the vehicle
(3) Remove any necessary skid plates. (Refer to 13
- FRAMES & BUMPERS/FRAME/TRANSFER CASE
SKID PLATE - REMOVAL)
(4) Mark propeller shaft and axle companion
flanges for assembly alignment.
(5) Remove the rear propeller shaft
(6) Remove the front propeller shaft, if necessary.
(7) Remove the engine to transmission collar (Fig.
8).
(8) Remove the exhaust support bracket from the
rear of the transmission.
(9) Disconnect and lower or remove any necessary
exhaust components.
Fig. 7 Torque Converter Assembly
1 - TURBINE ASSEMBLY
2-STATOR
3 - CONVERTER HUB
4 - O-RING
5 - IMPELLER ASSEMBLY
6 - CONVERTER CLUTCH PISTON
7 - TURBINE HUB
Fig. 8 Transmission Collar
1 - ENGINE
2 - STRUCTURAL DUST COVER
3 - TRANSMISSION
21 - 318 AUTOMATIC TRANSMISSION - 45RFE/545RFEDR
AUTOMATIC TRANSMISSION - 45RFE/545RFE (Continued)
Page 2022 of 2627
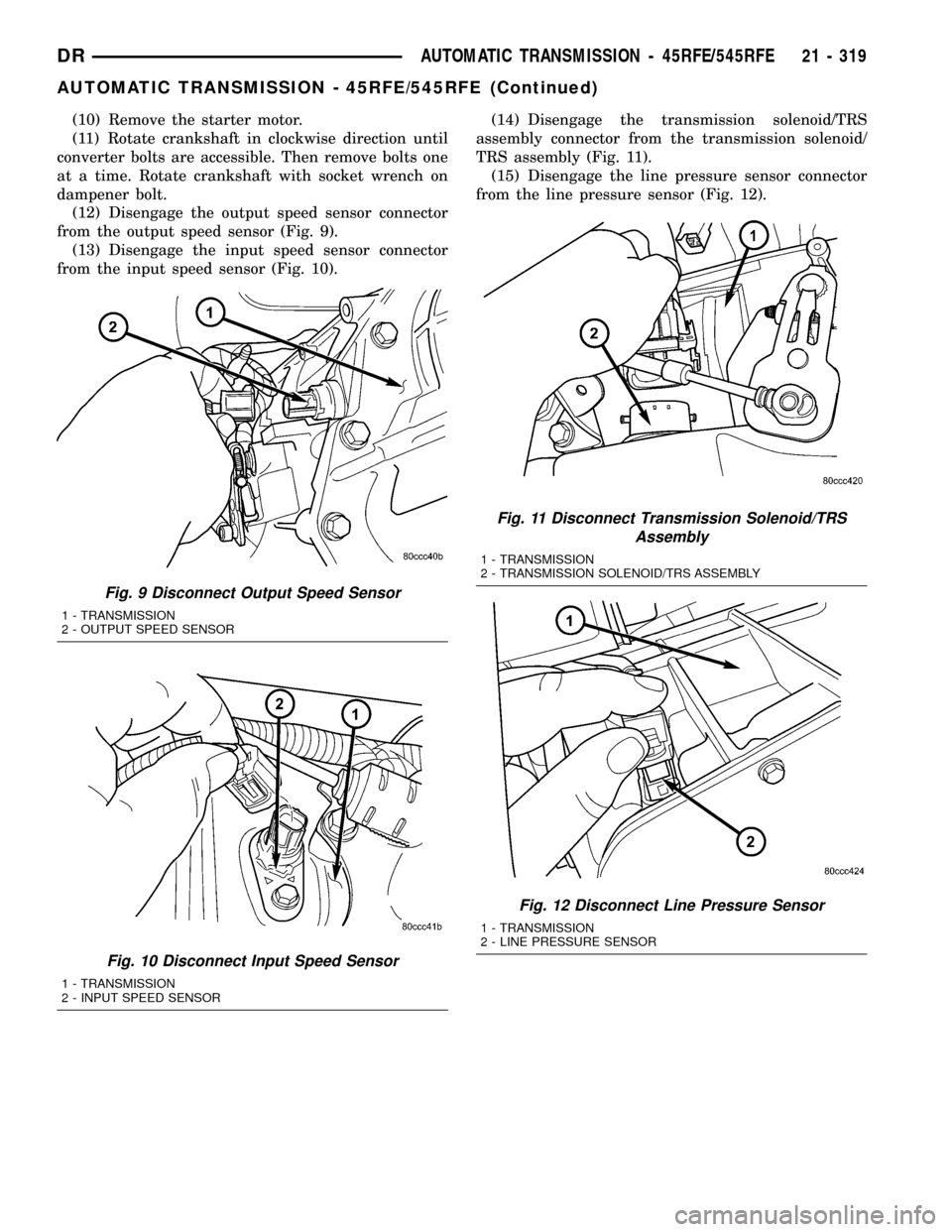
(10) Remove the starter motor.
(11) Rotate crankshaft in clockwise direction until
converter bolts are accessible. Then remove bolts one
at a time. Rotate crankshaft with socket wrench on
dampener bolt.
(12) Disengage the output speed sensor connector
from the output speed sensor (Fig. 9).
(13) Disengage the input speed sensor connector
from the input speed sensor (Fig. 10).(14) Disengage the transmission solenoid/TRS
assembly connector from the transmission solenoid/
TRS assembly (Fig. 11).
(15) Disengage the line pressure sensor connector
from the line pressure sensor (Fig. 12).
Fig. 9 Disconnect Output Speed Sensor
1 - TRANSMISSION
2 - OUTPUT SPEED SENSOR
Fig. 10 Disconnect Input Speed Sensor
1 - TRANSMISSION
2 - INPUT SPEED SENSOR
Fig. 11 Disconnect Transmission Solenoid/TRS
Assembly
1 - TRANSMISSION
2 - TRANSMISSION SOLENOID/TRS ASSEMBLY
Fig. 12 Disconnect Line Pressure Sensor
1 - TRANSMISSION
2 - LINE PRESSURE SENSOR
DRAUTOMATIC TRANSMISSION - 45RFE/545RFE 21 - 319
AUTOMATIC TRANSMISSION - 45RFE/545RFE (Continued)
Page 2023 of 2627
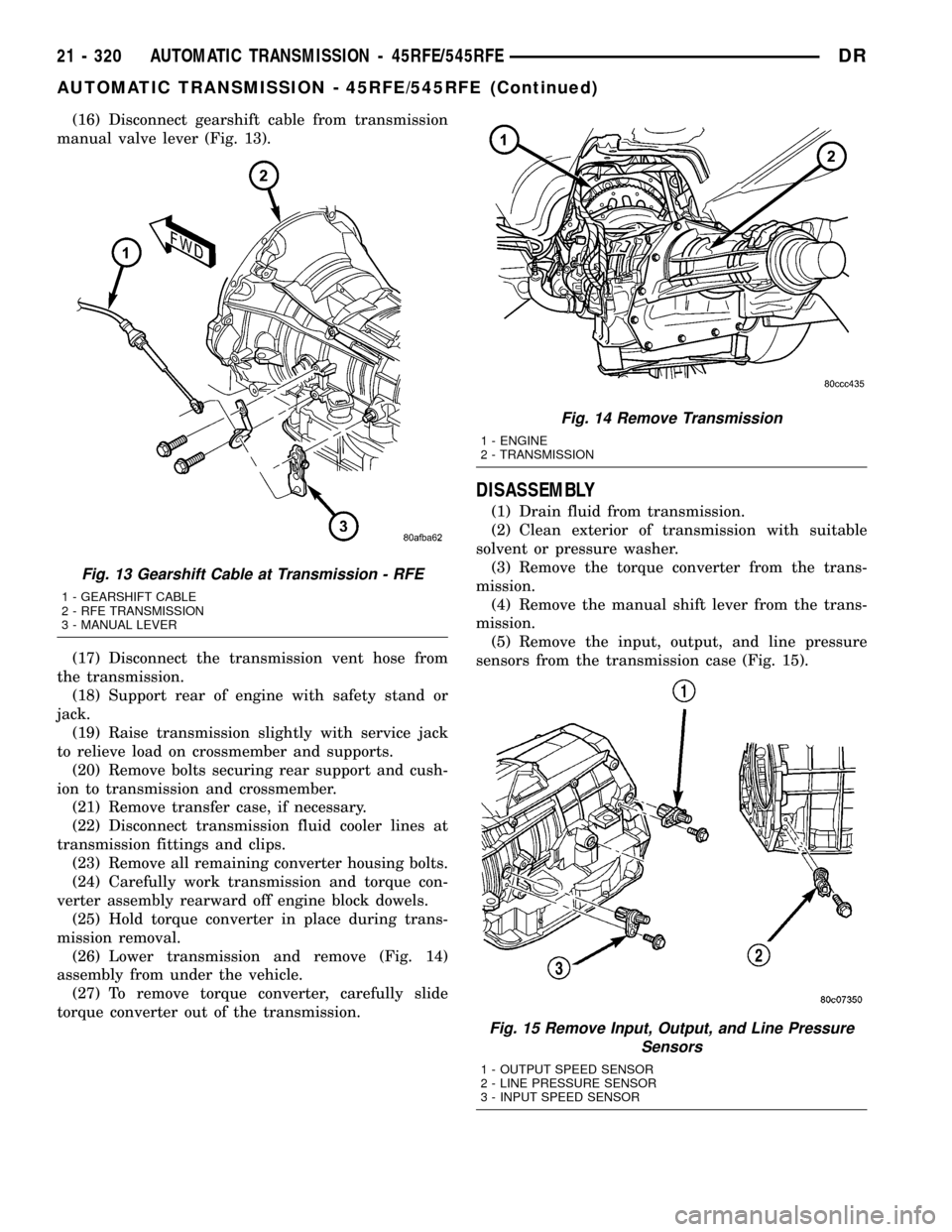
(16) Disconnect gearshift cable from transmission
manual valve lever (Fig. 13).
(17) Disconnect the transmission vent hose from
the transmission.
(18) Support rear of engine with safety stand or
jack.
(19) Raise transmission slightly with service jack
to relieve load on crossmember and supports.
(20) Remove bolts securing rear support and cush-
ion to transmission and crossmember.
(21) Remove transfer case, if necessary.
(22) Disconnect transmission fluid cooler lines at
transmission fittings and clips.
(23) Remove all remaining converter housing bolts.
(24) Carefully work transmission and torque con-
verter assembly rearward off engine block dowels.
(25) Hold torque converter in place during trans-
mission removal.
(26) Lower transmission and remove (Fig. 14)
assembly from under the vehicle.
(27) To remove torque converter, carefully slide
torque converter out of the transmission.
DISASSEMBLY
(1) Drain fluid from transmission.
(2) Clean exterior of transmission with suitable
solvent or pressure washer.
(3) Remove the torque converter from the trans-
mission.
(4) Remove the manual shift lever from the trans-
mission.
(5) Remove the input, output, and line pressure
sensors from the transmission case (Fig. 15).
Fig. 13 Gearshift Cable at Transmission - RFE
1 - GEARSHIFT CABLE
2 - RFE TRANSMISSION
3 - MANUAL LEVER
Fig. 14 Remove Transmission
1 - ENGINE
2 - TRANSMISSION
Fig. 15 Remove Input, Output, and Line Pressure
Sensors
1 - OUTPUT SPEED SENSOR
2 - LINE PRESSURE SENSOR
3 - INPUT SPEED SENSOR
21 - 320 AUTOMATIC TRANSMISSION - 45RFE/545RFEDR
AUTOMATIC TRANSMISSION - 45RFE/545RFE (Continued)
Page 2024 of 2627
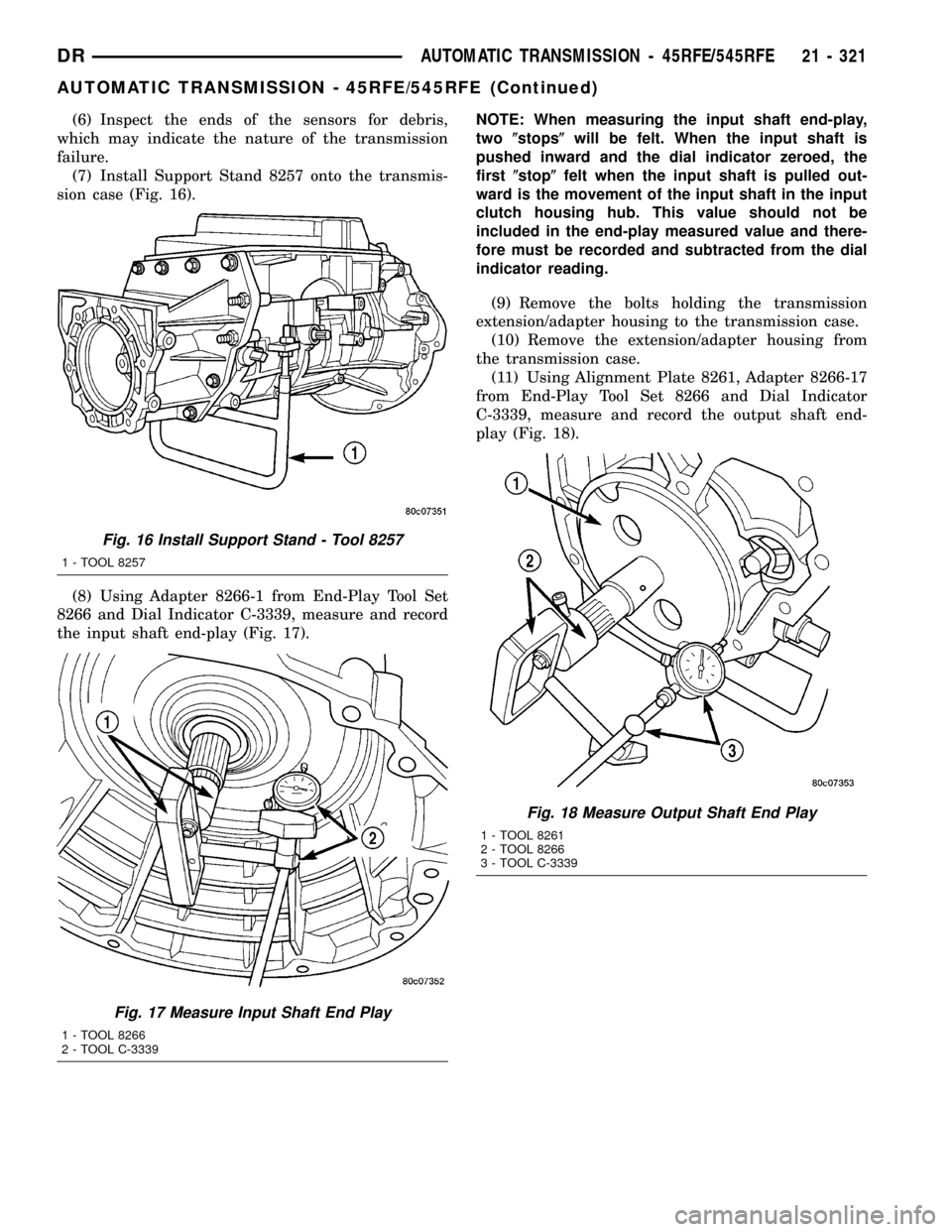
(6) Inspect the ends of the sensors for debris,
which may indicate the nature of the transmission
failure.
(7) Install Support Stand 8257 onto the transmis-
sion case (Fig. 16).
(8) Using Adapter 8266-1 from End-Play Tool Set
8266 and Dial Indicator C-3339, measure and record
the input shaft end-play (Fig. 17).NOTE: When measuring the input shaft end-play,
two(stops(will be felt. When the input shaft is
pushed inward and the dial indicator zeroed, the
first(stop(felt when the input shaft is pulled out-
ward is the movement of the input shaft in the input
clutch housing hub. This value should not be
included in the end-play measured value and there-
fore must be recorded and subtracted from the dial
indicator reading.
(9) Remove the bolts holding the transmission
extension/adapter housing to the transmission case.
(10) Remove the extension/adapter housing from
the transmission case.
(11) Using Alignment Plate 8261, Adapter 8266-17
from End-Play Tool Set 8266 and Dial Indicator
C-3339, measure and record the output shaft end-
play (Fig. 18).
Fig. 16 Install Support Stand - Tool 8257
1 - TOOL 8257
Fig. 17 Measure Input Shaft End Play
1 - TOOL 8266
2 - TOOL C-3339
Fig. 18 Measure Output Shaft End Play
1 - TOOL 8261
2 - TOOL 8266
3 - TOOL C-3339
DRAUTOMATIC TRANSMISSION - 45RFE/545RFE 21 - 321
AUTOMATIC TRANSMISSION - 45RFE/545RFE (Continued)