Page 65 of 2627
DESCRIPTION N´m Ft. Lbs. In. Lbs.
Stabilizer Bar
Frame Bolt61 45 Ð
Stabilizer Link
Lower Control Arm Nut102 75 Ð
Stabilizer Link
Axle Bracket71 52 Ð
Stabilizer Link
Stabilizer Bar Nut38 27 Ð
Hub/Bearing
Bolts202 149 Ð
Axle Nut 179 Beginning Torque,
Then Rotate 5 to 10
Times With a Final Torque
of 356132 Beginning Torque,
Then Rotate 5 to 10
Times With a Final Torque
of 263Ð
Tie Rod End
Nut75 55 Ð
NOTE: Suspension components with rubber/urethane bushings should be tightened with the vehicle at nor-
mal ride height. It is important to have the springs supporting the weight of the vehicle when the fasteners
are torqued. If springs are not at their normal ride position, vehicle ride comfort could be affected and pre-
mature bushing wear may occur.
SPECIAL TOOLS
9 1/4 AA
Puller C-3894±A
Remover, Wheel Stud C-4150A
BALL JOINT PRESS - C-4212F
REMOVER / INSTALLER BALLJOINT - 8445
2 - 30 FRONT - LINK/COILDR
FRONT - LINK/COIL (Continued)
Page 66 of 2627
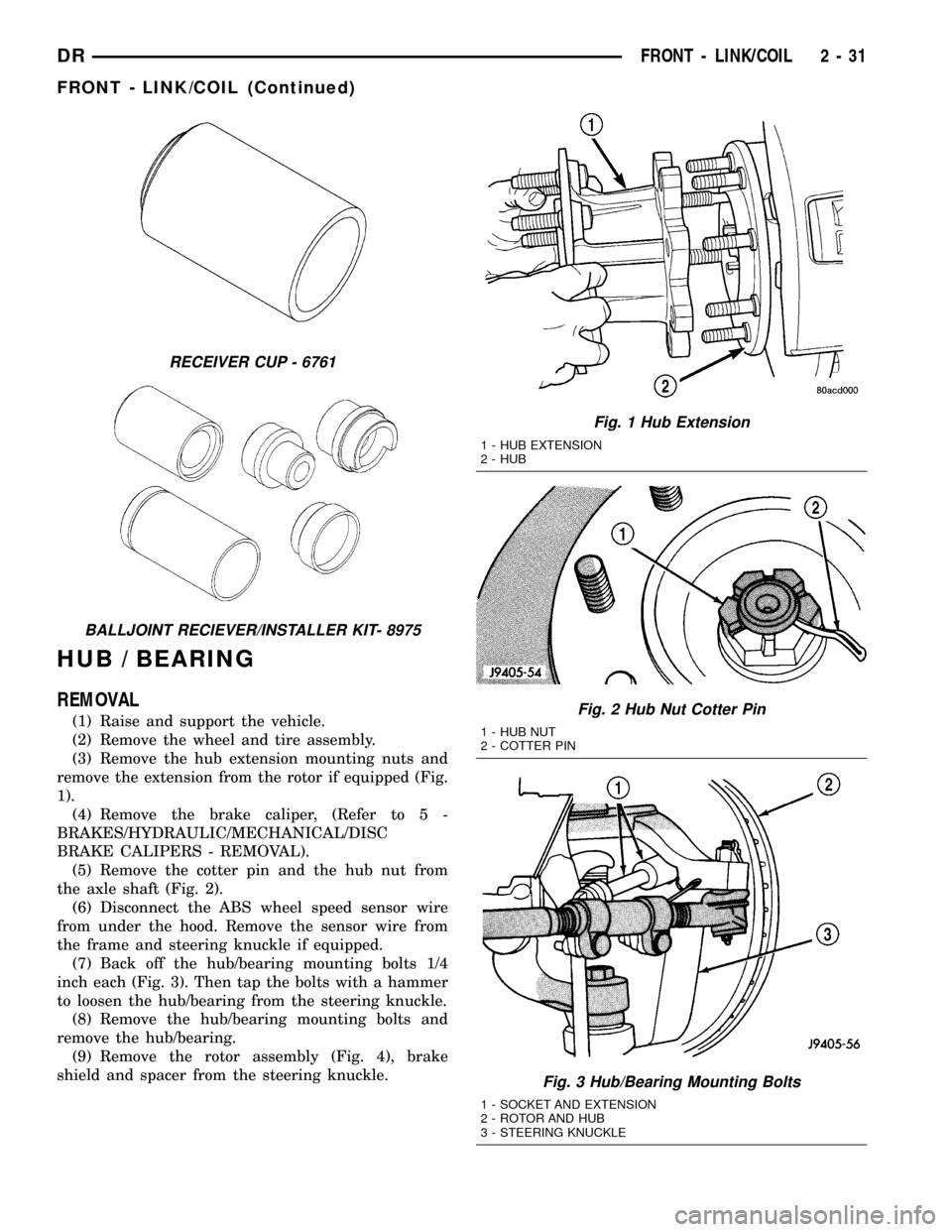
HUB / BEARING
REMOVAL
(1) Raise and support the vehicle.
(2) Remove the wheel and tire assembly.
(3) Remove the hub extension mounting nuts and
remove the extension from the rotor if equipped (Fig.
1).
(4) Remove the brake caliper, (Refer to 5 -
BRAKES/HYDRAULIC/MECHANICAL/DISC
BRAKE CALIPERS - REMOVAL).
(5) Remove the cotter pin and the hub nut from
the axle shaft (Fig. 2).
(6) Disconnect the ABS wheel speed sensor wire
from under the hood. Remove the sensor wire from
the frame and steering knuckle if equipped.
(7) Back off the hub/bearing mounting bolts 1/4
inch each (Fig. 3). Then tap the bolts with a hammer
to loosen the hub/bearing from the steering knuckle.
(8) Remove the hub/bearing mounting bolts and
remove the hub/bearing.
(9) Remove the rotor assembly (Fig. 4), brake
shield and spacer from the steering knuckle.
RECEIVER CUP - 6761
BALLJOINT RECIEVER/INSTALLER KIT- 8975
Fig. 1 Hub Extension
1 - HUB EXTENSION
2 - HUB
Fig. 2 Hub Nut Cotter Pin
1 - HUB NUT
2 - COTTER PIN
Fig. 3 Hub/Bearing Mounting Bolts
1 - SOCKET AND EXTENSION
2 - ROTOR AND HUB
3 - STEERING KNUCKLE
DRFRONT - LINK/COIL 2 - 31
FRONT - LINK/COIL (Continued)
Page 67 of 2627
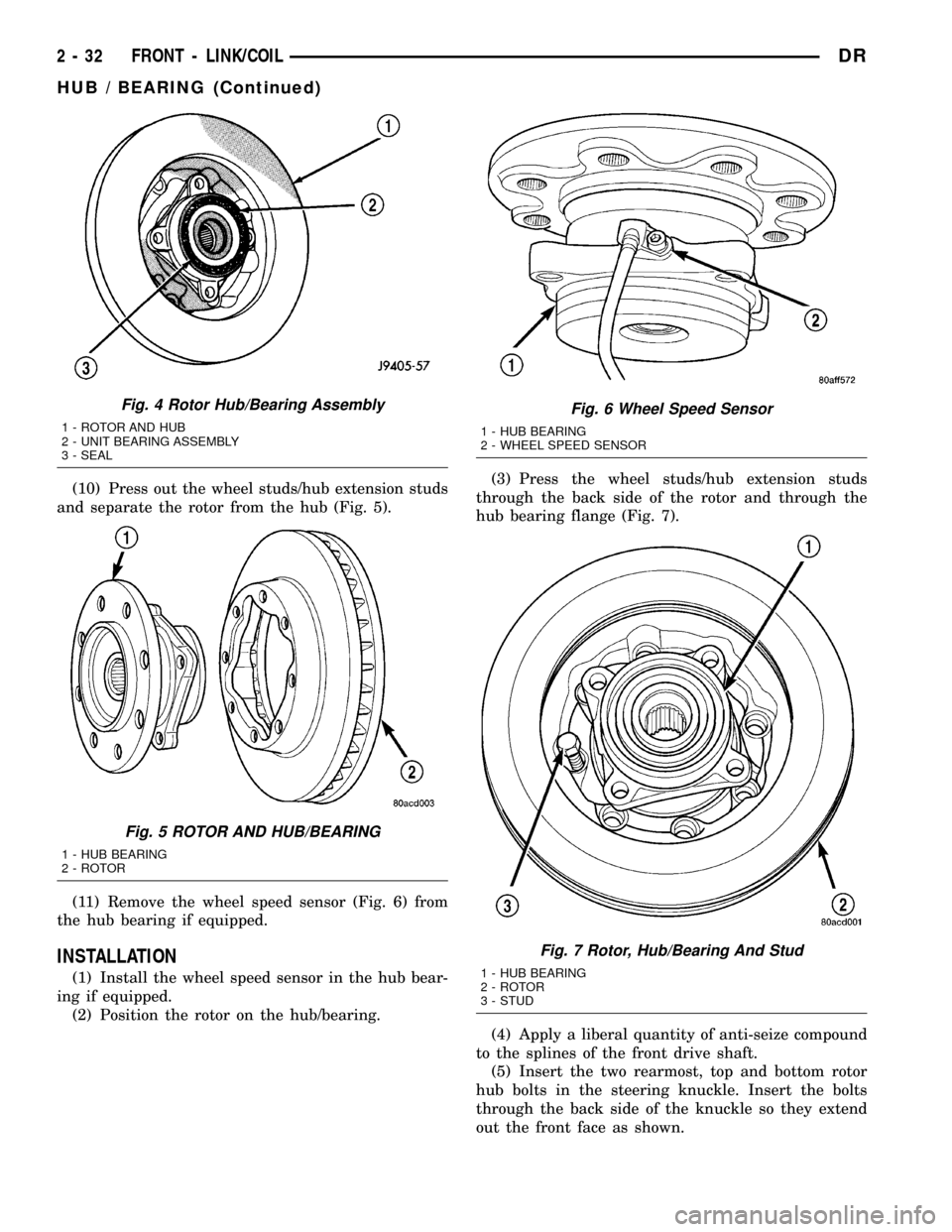
(10) Press out the wheel studs/hub extension studs
and separate the rotor from the hub (Fig. 5).
(11) Remove the wheel speed sensor (Fig. 6) from
the hub bearing if equipped.
INSTALLATION
(1) Install the wheel speed sensor in the hub bear-
ing if equipped.
(2) Position the rotor on the hub/bearing.(3) Press the wheel studs/hub extension studs
through the back side of the rotor and through the
hub bearing flange (Fig. 7).
(4) Apply a liberal quantity of anti-seize compound
to the splines of the front drive shaft.
(5) Insert the two rearmost, top and bottom rotor
hub bolts in the steering knuckle. Insert the bolts
through the back side of the knuckle so they extend
out the front face as shown.
Fig. 4 Rotor Hub/Bearing Assembly
1 - ROTOR AND HUB
2 - UNIT BEARING ASSEMBLY
3 - SEAL
Fig. 5 ROTOR AND HUB/BEARING
1 - HUB BEARING
2 - ROTOR
Fig. 6 Wheel Speed Sensor
1 - HUB BEARING
2 - WHEEL SPEED SENSOR
Fig. 7 Rotor, Hub/Bearing And Stud
1 - HUB BEARING
2 - ROTOR
3 - STUD
2 - 32 FRONT - LINK/COILDR
HUB / BEARING (Continued)
Page 68 of 2627
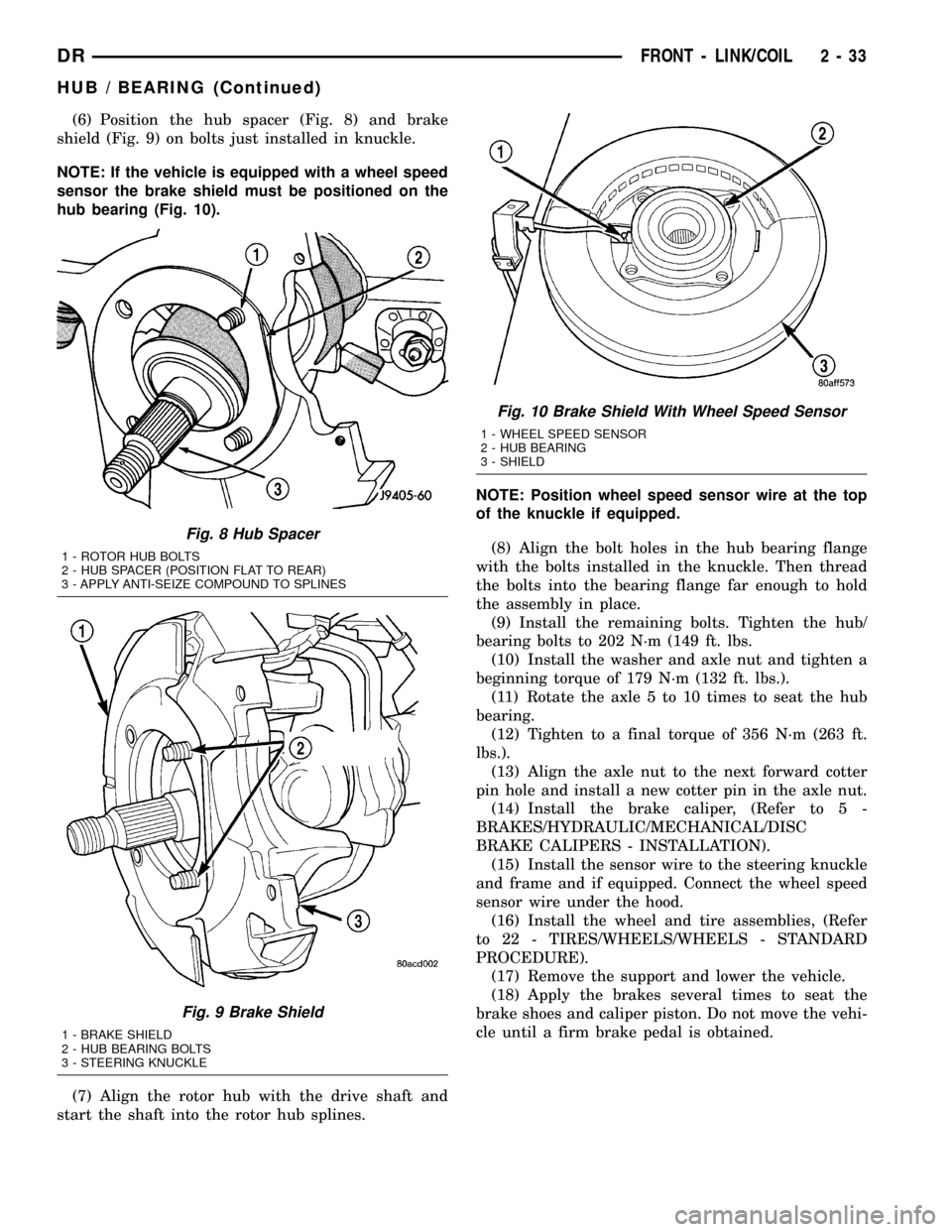
(6) Position the hub spacer (Fig. 8) and brake
shield (Fig. 9) on bolts just installed in knuckle.
NOTE: If the vehicle is equipped with a wheel speed
sensor the brake shield must be positioned on the
hub bearing (Fig. 10).
(7) Align the rotor hub with the drive shaft and
start the shaft into the rotor hub splines.NOTE: Position wheel speed sensor wire at the top
of the knuckle if equipped.
(8) Align the bolt holes in the hub bearing flange
with the bolts installed in the knuckle. Then thread
the bolts into the bearing flange far enough to hold
the assembly in place.
(9) Install the remaining bolts. Tighten the hub/
bearing bolts to 202 N´m (149 ft. lbs.
(10) Install the washer and axle nut and tighten a
beginning torque of 179 N´m (132 ft. lbs.).
(11) Rotate the axle 5 to 10 times to seat the hub
bearing.
(12) Tighten to a final torque of 356 N´m (263 ft.
lbs.).
(13) Align the axle nut to the next forward cotter
pin hole and install a new cotter pin in the axle nut.
(14) Install the brake caliper, (Refer to 5 -
BRAKES/HYDRAULIC/MECHANICAL/DISC
BRAKE CALIPERS - INSTALLATION).
(15) Install the sensor wire to the steering knuckle
and frame and if equipped. Connect the wheel speed
sensor wire under the hood.
(16) Install the wheel and tire assemblies, (Refer
to 22 - TIRES/WHEELS/WHEELS - STANDARD
PROCEDURE).
(17) Remove the support and lower the vehicle.
(18) Apply the brakes several times to seat the
brake shoes and caliper piston. Do not move the vehi-
cle until a firm brake pedal is obtained.
Fig. 8 Hub Spacer
1 - ROTOR HUB BOLTS
2 - HUB SPACER (POSITION FLAT TO REAR)
3 - APPLY ANTI-SEIZE COMPOUND TO SPLINES
Fig. 9 Brake Shield
1 - BRAKE SHIELD
2 - HUB BEARING BOLTS
3 - STEERING KNUCKLE
Fig. 10 Brake Shield With Wheel Speed Sensor
1 - WHEEL SPEED SENSOR
2 - HUB BEARING
3 - SHIELD
DRFRONT - LINK/COIL 2 - 33
HUB / BEARING (Continued)
Page 69 of 2627
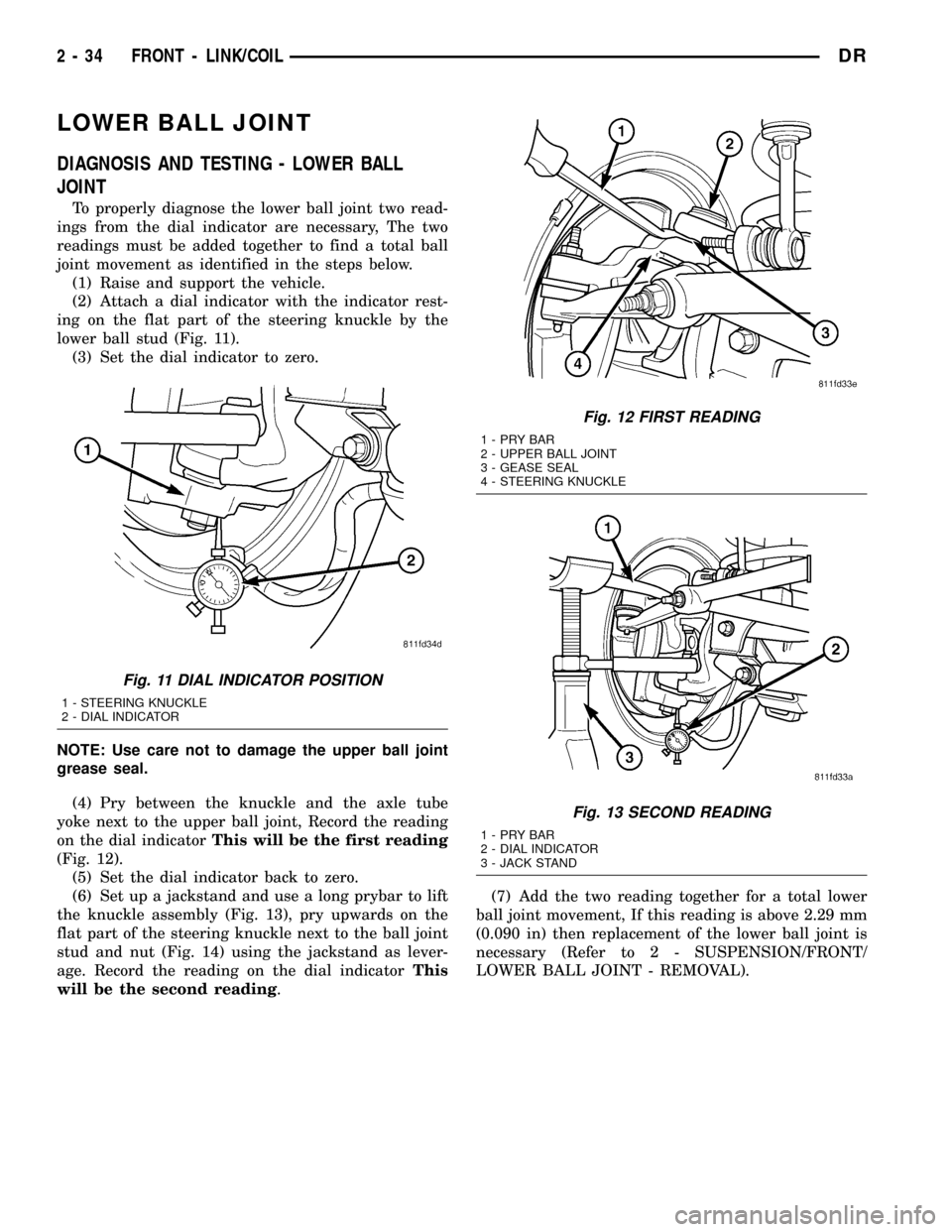
LOWER BALL JOINT
DIAGNOSIS AND TESTING - LOWER BALL
JOINT
To properly diagnose the lower ball joint two read-
ings from the dial indicator are necessary, The two
readings must be added together to find a total ball
joint movement as identified in the steps below.
(1) Raise and support the vehicle.
(2) Attach a dial indicator with the indicator rest-
ing on the flat part of the steering knuckle by the
lower ball stud (Fig. 11).
(3) Set the dial indicator to zero.
NOTE: Use care not to damage the upper ball joint
grease seal.
(4) Pry between the knuckle and the axle tube
yoke next to the upper ball joint, Record the reading
on the dial indicatorThis will be the first reading
(Fig. 12).
(5) Set the dial indicator back to zero.
(6) Set up a jackstand and use a long prybar to lift
the knuckle assembly (Fig. 13), pry upwards on the
flat part of the steering knuckle next to the ball joint
stud and nut (Fig. 14) using the jackstand as lever-
age. Record the reading on the dial indicatorThis
will be the second reading.(7) Add the two reading together for a total lower
ball joint movement, If this reading is above 2.29 mm
(0.090 in) then replacement of the lower ball joint is
necessary (Refer to 2 - SUSPENSION/FRONT/
LOWER BALL JOINT - REMOVAL).
Fig. 11 DIAL INDICATOR POSITION
1 - STEERING KNUCKLE
2 - DIAL INDICATOR
Fig. 12 FIRST READING
1-PRYBAR
2 - UPPER BALL JOINT
3 - GEASE SEAL
4 - STEERING KNUCKLE
Fig. 13 SECOND READING
1-PRYBAR
2 - DIAL INDICATOR
3 - JACK STAND
2 - 34 FRONT - LINK/COILDR
Page 70 of 2627
REMOVAL
(1) Remove lower snap ring from the lower ball
joint (Fig. 15).
(2) Position special tool 8975±2 (RECEIVER) and
8975±4 (DRIVER) with tool C4212±F as shown to
remove lower ball stud (Fig. 16).
INSTALLATION
(1) Position special tool 8975±1 (DRIVER) and
8975±3 (RECEIVER) with C4212±F as shown to
install lower ball stud (Fig. 17).
Fig. 14 PRYING LOCATION
1-PRYBAR
2 - UPPER BALL JOINT
3 - AXLE YOKE
4 - GRESE SEAL
5 - STEERING KNUCKLE
Fig. 15 LOWER SNAP RING
Fig. 16 LOWER BALL JOINT REMOVAL
1 - SPECIAL TOOL
C4212-F
2 - SPECIAL TOOL
8975-2
3 - KNUCKLE
4 - SPECIAL TOOL
8975-4
Fig. 17 LOWER BALL JOINT INSTALLATION
1 - SPECIAL TOOL
C4212-F
2 - SPECIAL TOOL
8975-1
3 - BALL JOINT
4 - KNUCKLE
5 - SPECIAL TOOL
8975-3
DRFRONT - LINK/COIL 2 - 35
LOWER BALL JOINT (Continued)
Page 71 of 2627
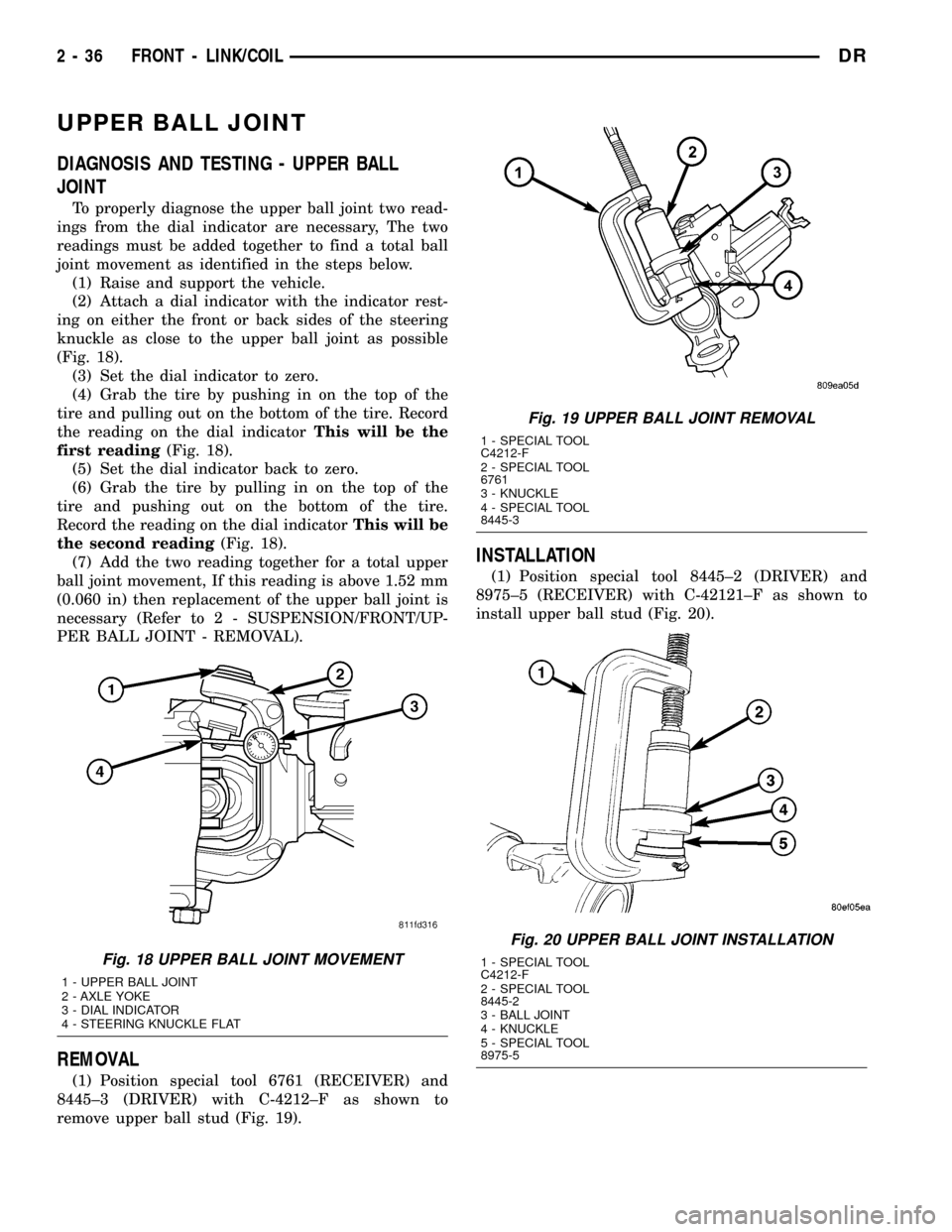
UPPER BALL JOINT
DIAGNOSIS AND TESTING - UPPER BALL
JOINT
To properly diagnose the upper ball joint two read-
ings from the dial indicator are necessary, The two
readings must be added together to find a total ball
joint movement as identified in the steps below.
(1) Raise and support the vehicle.
(2) Attach a dial indicator with the indicator rest-
ing on either the front or back sides of the steering
knuckle as close to the upper ball joint as possible
(Fig. 18).
(3) Set the dial indicator to zero.
(4) Grab the tire by pushing in on the top of the
tire and pulling out on the bottom of the tire. Record
the reading on the dial indicatorThis will be the
first reading(Fig. 18).
(5) Set the dial indicator back to zero.
(6) Grab the tire by pulling in on the top of the
tire and pushing out on the bottom of the tire.
Record the reading on the dial indicatorThis will be
the second reading(Fig. 18).
(7) Add the two reading together for a total upper
ball joint movement, If this reading is above 1.52 mm
(0.060 in) then replacement of the upper ball joint is
necessary (Refer to 2 - SUSPENSION/FRONT/UP-
PER BALL JOINT - REMOVAL).
REMOVAL
(1) Position special tool 6761 (RECEIVER) and
8445±3 (DRIVER) with C-4212±F as shown to
remove upper ball stud (Fig. 19).
INSTALLATION
(1) Position special tool 8445±2 (DRIVER) and
8975±5 (RECEIVER) with C-42121±F as shown to
install upper ball stud (Fig. 20).
Fig. 18 UPPER BALL JOINT MOVEMENT
1 - UPPER BALL JOINT
2 - AXLE YOKE
3 - DIAL INDICATOR
4 - STEERING KNUCKLE FLAT
Fig. 19 UPPER BALL JOINT REMOVAL
1 - SPECIAL TOOL
C4212-F
2 - SPECIAL TOOL
6761
3 - KNUCKLE
4 - SPECIAL TOOL
8445-3
Fig. 20 UPPER BALL JOINT INSTALLATION
1 - SPECIAL TOOL
C4212-F
2 - SPECIAL TOOL
8445-2
3 - BALL JOINT
4 - KNUCKLE
5 - SPECIAL TOOL
8975-5
2 - 36 FRONT - LINK/COILDR
Page 72 of 2627
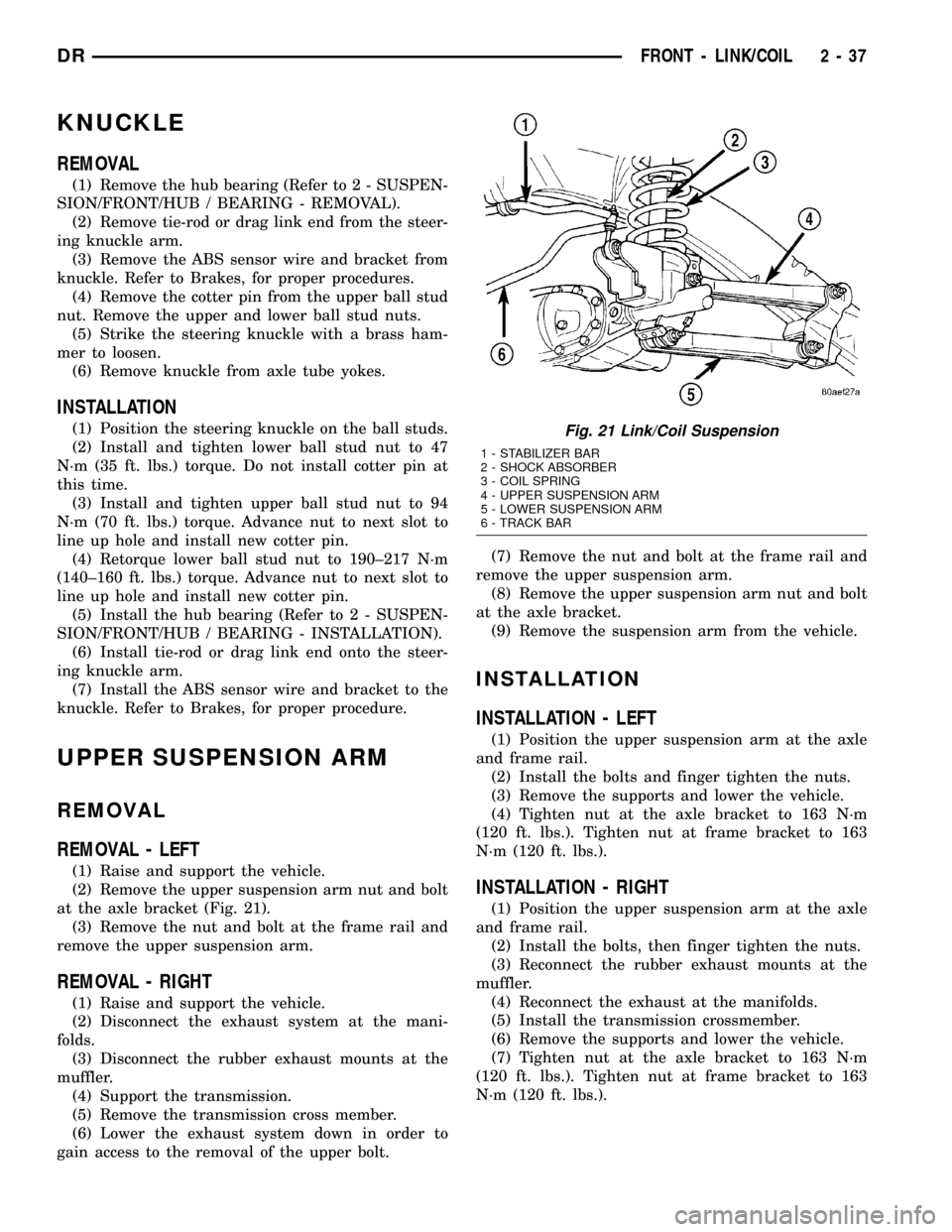
KNUCKLE
REMOVAL
(1) Remove the hub bearing (Refer to 2 - SUSPEN-
SION/FRONT/HUB / BEARING - REMOVAL).
(2) Remove tie-rod or drag link end from the steer-
ing knuckle arm.
(3) Remove the ABS sensor wire and bracket from
knuckle. Refer to Brakes, for proper procedures.
(4) Remove the cotter pin from the upper ball stud
nut. Remove the upper and lower ball stud nuts.
(5) Strike the steering knuckle with a brass ham-
mer to loosen.
(6) Remove knuckle from axle tube yokes.
INSTALLATION
(1) Position the steering knuckle on the ball studs.
(2) Install and tighten lower ball stud nut to 47
N´m (35 ft. lbs.) torque. Do not install cotter pin at
this time.
(3) Install and tighten upper ball stud nut to 94
N´m (70 ft. lbs.) torque. Advance nut to next slot to
line up hole and install new cotter pin.
(4) Retorque lower ball stud nut to 190±217 N´m
(140±160 ft. lbs.) torque. Advance nut to next slot to
line up hole and install new cotter pin.
(5) Install the hub bearing (Refer to 2 - SUSPEN-
SION/FRONT/HUB / BEARING - INSTALLATION).
(6) Install tie-rod or drag link end onto the steer-
ing knuckle arm.
(7) Install the ABS sensor wire and bracket to the
knuckle. Refer to Brakes, for proper procedure.
UPPER SUSPENSION ARM
REMOVAL
REMOVAL - LEFT
(1) Raise and support the vehicle.
(2) Remove the upper suspension arm nut and bolt
at the axle bracket (Fig. 21).
(3) Remove the nut and bolt at the frame rail and
remove the upper suspension arm.
REMOVAL - RIGHT
(1) Raise and support the vehicle.
(2) Disconnect the exhaust system at the mani-
folds.
(3) Disconnect the rubber exhaust mounts at the
muffler.
(4) Support the transmission.
(5) Remove the transmission cross member.
(6) Lower the exhaust system down in order to
gain access to the removal of the upper bolt.(7) Remove the nut and bolt at the frame rail and
remove the upper suspension arm.
(8) Remove the upper suspension arm nut and bolt
at the axle bracket.
(9) Remove the suspension arm from the vehicle.
INSTALLATION
INSTALLATION - LEFT
(1) Position the upper suspension arm at the axle
and frame rail.
(2) Install the bolts and finger tighten the nuts.
(3) Remove the supports and lower the vehicle.
(4) Tighten nut at the axle bracket to 163 N´m
(120 ft. lbs.). Tighten nut at frame bracket to 163
N´m (120 ft. lbs.).
INSTALLATION - RIGHT
(1) Position the upper suspension arm at the axle
and frame rail.
(2) Install the bolts, then finger tighten the nuts.
(3) Reconnect the rubber exhaust mounts at the
muffler.
(4) Reconnect the exhaust at the manifolds.
(5) Install the transmission crossmember.
(6) Remove the supports and lower the vehicle.
(7) Tighten nut at the axle bracket to 163 N´m
(120 ft. lbs.). Tighten nut at frame bracket to 163
N´m (120 ft. lbs.).
Fig. 21 Link/Coil Suspension
1 - STABILIZER BAR
2 - SHOCK ABSORBER
3 - COIL SPRING
4 - UPPER SUSPENSION ARM
5 - LOWER SUSPENSION ARM
6 - TRACK BAR
DRFRONT - LINK/COIL 2 - 37