Page 1937 of 2627
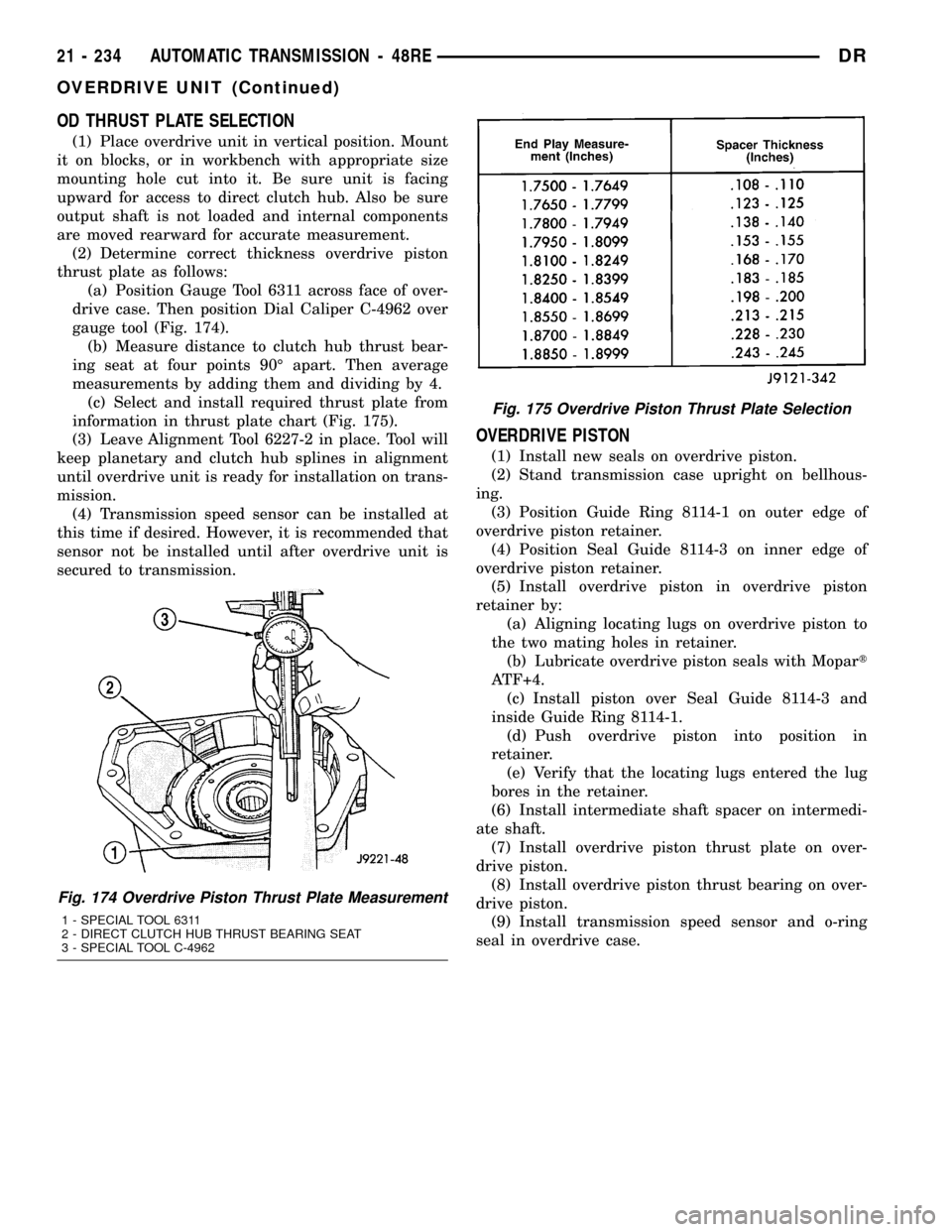
OD THRUST PLATE SELECTION
(1) Place overdrive unit in vertical position. Mount
it on blocks, or in workbench with appropriate size
mounting hole cut into it. Be sure unit is facing
upward for access to direct clutch hub. Also be sure
output shaft is not loaded and internal components
are moved rearward for accurate measurement.
(2) Determine correct thickness overdrive piston
thrust plate as follows:
(a) Position Gauge Tool 6311 across face of over-
drive case. Then position Dial Caliper C-4962 over
gauge tool (Fig. 174).
(b) Measure distance to clutch hub thrust bear-
ing seat at four points 90É apart. Then average
measurements by adding them and dividing by 4.
(c) Select and install required thrust plate from
information in thrust plate chart (Fig. 175).
(3) Leave Alignment Tool 6227-2 in place. Tool will
keep planetary and clutch hub splines in alignment
until overdrive unit is ready for installation on trans-
mission.
(4) Transmission speed sensor can be installed at
this time if desired. However, it is recommended that
sensor not be installed until after overdrive unit is
secured to transmission.
OVERDRIVE PISTON
(1) Install new seals on overdrive piston.
(2) Stand transmission case upright on bellhous-
ing.
(3) Position Guide Ring 8114-1 on outer edge of
overdrive piston retainer.
(4) Position Seal Guide 8114-3 on inner edge of
overdrive piston retainer.
(5) Install overdrive piston in overdrive piston
retainer by:
(a) Aligning locating lugs on overdrive piston to
the two mating holes in retainer.
(b) Lubricate overdrive piston seals with Mopart
ATF+4.
(c) Install piston over Seal Guide 8114-3 and
inside Guide Ring 8114-1.
(d) Push overdrive piston into position in
retainer.
(e) Verify that the locating lugs entered the lug
bores in the retainer.
(6) Install intermediate shaft spacer on intermedi-
ate shaft.
(7) Install overdrive piston thrust plate on over-
drive piston.
(8) Install overdrive piston thrust bearing on over-
drive piston.
(9) Install transmission speed sensor and o-ring
seal in overdrive case.
Fig. 174 Overdrive Piston Thrust Plate Measurement
1 - SPECIAL TOOL 6311
2 - DIRECT CLUTCH HUB THRUST BEARING SEAT
3 - SPECIAL TOOL C-4962
Fig. 175 Overdrive Piston Thrust Plate Selection
21 - 234 AUTOMATIC TRANSMISSION - 48REDR
OVERDRIVE UNIT (Continued)
Page 1938 of 2627

INSTALLATION
(1) Be sure overdrive unit Alignment Tool 6227-2
is fully seated before moving unit. If tool is not
seated and gear splines rotate out of alignment, over-
drive unit will have to be disassembled in order to
realign splines.
(2) If overdrive piston retainer was not removed
during service and original case gasket is no longer
reusable, prepare new gasket by trimming it.
(3) Cut out old case gasket around piston retainer
with razor knife (Fig. 176).
(4) Use old gasket as template and trim new gas-
ket to fit.
(5) Position new gasket over piston retainer and
on transmission case. Use petroleum jelly to hold
gasket in place if necessary. Do not use any type of
sealer to secure gasket. Use petroleum jelly only.
(6) Install selective spacer on intermediate shaft, if
removed. Spacer goes in groove just rearward of
shaft rear splines (Fig. 177).
(7) Install thrust bearing in overdrive unit sliding
hub. Use petroleum jelly to hold bearing in position.
CAUTION: Be sure the shoulder on the inside diam-
eter of the bearing is facing forward.(8) Verify that splines in overdrive planetary gear
and overrunning clutch hub are aligned with Align-
ment Tool 6227-2. Overdrive unit cannot be installed
if splines are not aligned. If splines have rotated out
of alignment, unit will have to be disassembled to
realign splines.
(9) Carefully slide Alignment Tool 6227-2 out of
overdrive planetary gear and overrunning clutch
splines.
(10) Raise overdrive unit and carefully slide it
straight onto intermediate shaft. Insert park rod into
park lock reaction plug at same time. Avoid tilting
overdrive during installation as this could cause
planetary gear and overrunning clutch splines to
rotate out of alignment. If this occurs, it will be nec-
essary to remove and disassemble overdrive unit to
realign splines.
(11) Work overdrive unit forward on intermediate
shaft until seated against transmission case.
(12) Install bolts attaching overdrive unit to trans-
mission unit. Tighten bolts in diagonal pattern to 34
N´m (25 ft-lbs).
(13) Connect the transmission speed sensor and
overdrive wiring connectors.
(14) Install the transfer case, if equipped.
(15) Align and install rear propeller shaft, if nec-
essary. (Refer to 3 - DIFFERENTIAL & DRIVELINE/
PROPELLER SHAFT/PROPELLER SHAFT -
INSTALLATION)
Fig. 176 Trimming Overdrive Case Gasket
1 - GASKET
2 - SHARP KNIFE
Fig. 177 Intermediate Shaft Selective Spacer
Location
1 - SELECTIVE SPACER
2 - SPACER GROOVE
3 - INTERMEDIATE SHAFT
DRAUTOMATIC TRANSMISSION - 48RE 21 - 235
OVERDRIVE UNIT (Continued)
Page 1939 of 2627
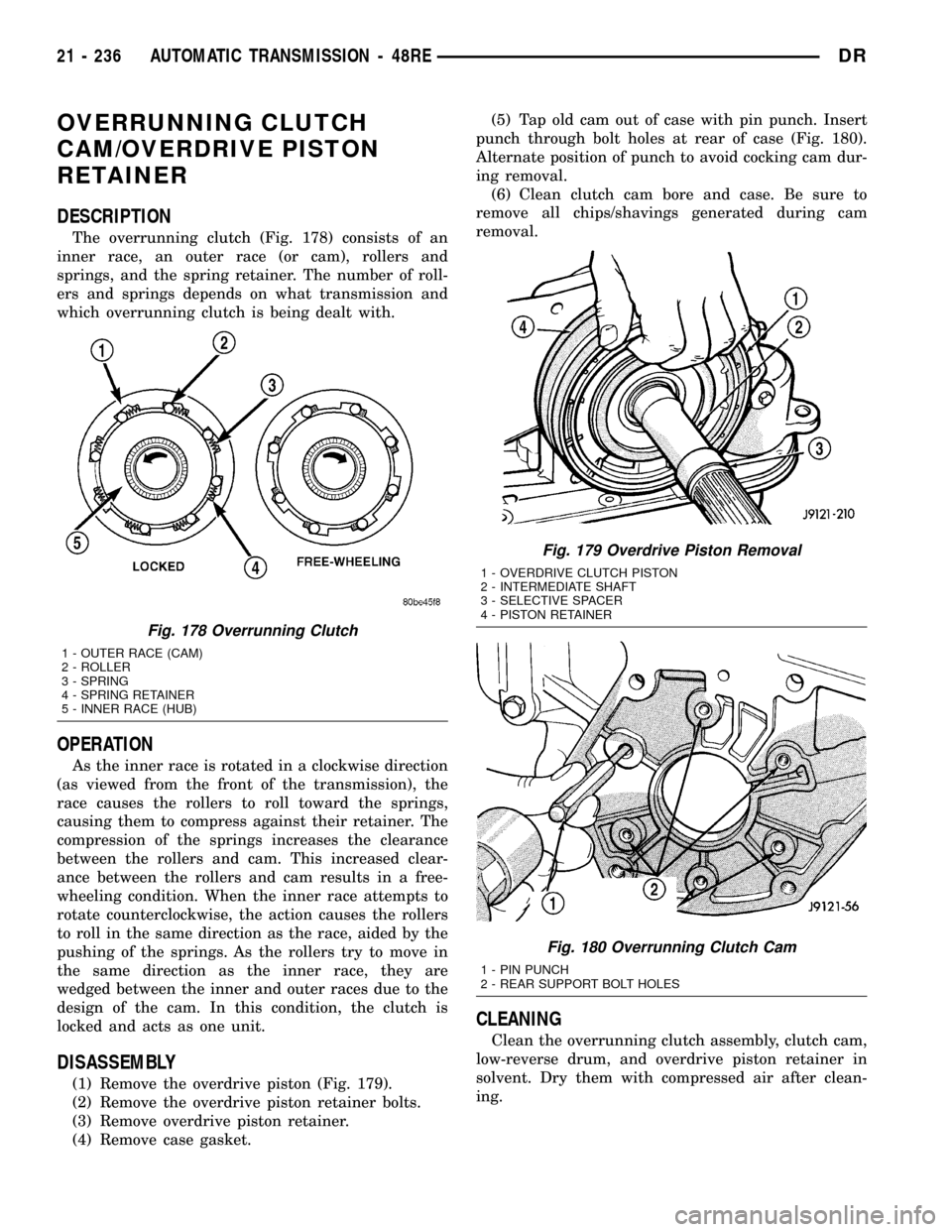
OVERRUNNING CLUTCH
CAM/OVERDRIVE PISTON
RETAINER
DESCRIPTION
The overrunning clutch (Fig. 178) consists of an
inner race, an outer race (or cam), rollers and
springs, and the spring retainer. The number of roll-
ers and springs depends on what transmission and
which overrunning clutch is being dealt with.
OPERATION
As the inner race is rotated in a clockwise direction
(as viewed from the front of the transmission), the
race causes the rollers to roll toward the springs,
causing them to compress against their retainer. The
compression of the springs increases the clearance
between the rollers and cam. This increased clear-
ance between the rollers and cam results in a free-
wheeling condition. When the inner race attempts to
rotate counterclockwise, the action causes the rollers
to roll in the same direction as the race, aided by the
pushing of the springs. As the rollers try to move in
the same direction as the inner race, they are
wedged between the inner and outer races due to the
design of the cam. In this condition, the clutch is
locked and acts as one unit.
DISASSEMBLY
(1) Remove the overdrive piston (Fig. 179).
(2) Remove the overdrive piston retainer bolts.
(3) Remove overdrive piston retainer.
(4) Remove case gasket.(5) Tap old cam out of case with pin punch. Insert
punch through bolt holes at rear of case (Fig. 180).
Alternate position of punch to avoid cocking cam dur-
ing removal.
(6) Clean clutch cam bore and case. Be sure to
remove all chips/shavings generated during cam
removal.
CLEANING
Clean the overrunning clutch assembly, clutch cam,
low-reverse drum, and overdrive piston retainer in
solvent. Dry them with compressed air after clean-
ing.
Fig. 178 Overrunning Clutch
1 - OUTER RACE (CAM)
2 - ROLLER
3 - SPRING
4 - SPRING RETAINER
5 - INNER RACE (HUB)
Fig. 179 Overdrive Piston Removal
1 - OVERDRIVE CLUTCH PISTON
2 - INTERMEDIATE SHAFT
3 - SELECTIVE SPACER
4 - PISTON RETAINER
Fig. 180 Overrunning Clutch Cam
1 - PIN PUNCH
2 - REAR SUPPORT BOLT HOLES
21 - 236 AUTOMATIC TRANSMISSION - 48REDR
Page 1940 of 2627
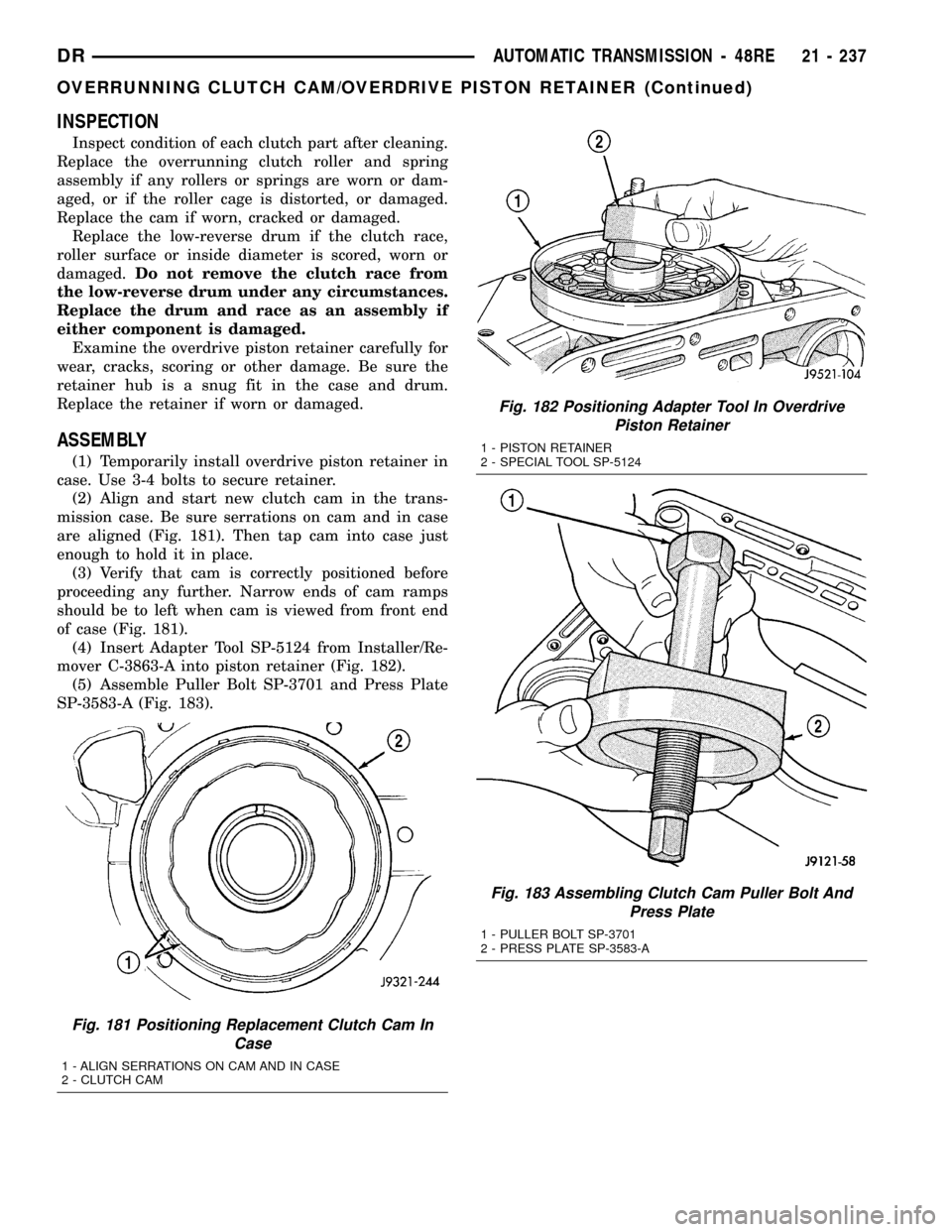
INSPECTION
Inspect condition of each clutch part after cleaning.
Replace the overrunning clutch roller and spring
assembly if any rollers or springs are worn or dam-
aged, or if the roller cage is distorted, or damaged.
Replace the cam if worn, cracked or damaged.
Replace the low-reverse drum if the clutch race,
roller surface or inside diameter is scored, worn or
damaged.Do not remove the clutch race from
the low-reverse drum under any circumstances.
Replace the drum and race as an assembly if
either component is damaged.
Examine the overdrive piston retainer carefully for
wear, cracks, scoring or other damage. Be sure the
retainer hub is a snug fit in the case and drum.
Replace the retainer if worn or damaged.
ASSEMBLY
(1) Temporarily install overdrive piston retainer in
case. Use 3-4 bolts to secure retainer.
(2) Align and start new clutch cam in the trans-
mission case. Be sure serrations on cam and in case
are aligned (Fig. 181). Then tap cam into case just
enough to hold it in place.
(3) Verify that cam is correctly positioned before
proceeding any further. Narrow ends of cam ramps
should be to left when cam is viewed from front end
of case (Fig. 181).
(4) Insert Adapter Tool SP-5124 from Installer/Re-
mover C-3863-A into piston retainer (Fig. 182).
(5) Assemble Puller Bolt SP-3701 and Press Plate
SP-3583-A (Fig. 183).
Fig. 181 Positioning Replacement Clutch Cam In
Case
1 - ALIGN SERRATIONS ON CAM AND IN CASE
2 - CLUTCH CAM
Fig. 182 Positioning Adapter Tool In Overdrive
Piston Retainer
1 - PISTON RETAINER
2 - SPECIAL TOOL SP-5124
Fig. 183 Assembling Clutch Cam Puller Bolt And
Press Plate
1 - PULLER BOLT SP-3701
2 - PRESS PLATE SP-3583-A
DRAUTOMATIC TRANSMISSION - 48RE 21 - 237
OVERRUNNING CLUTCH CAM/OVERDRIVE PISTON RETAINER (Continued)
Page 1941 of 2627
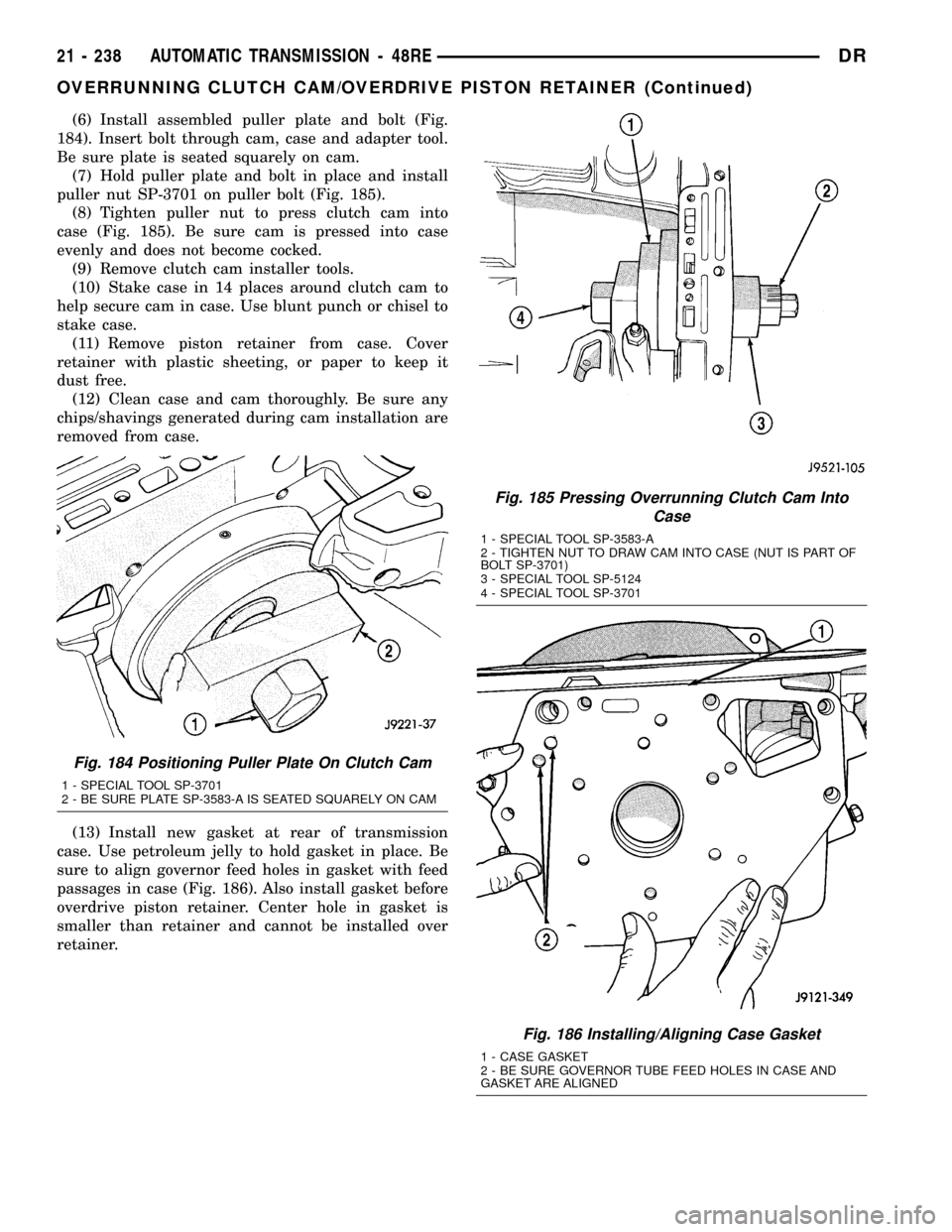
(6) Install assembled puller plate and bolt (Fig.
184). Insert bolt through cam, case and adapter tool.
Be sure plate is seated squarely on cam.
(7) Hold puller plate and bolt in place and install
puller nut SP-3701 on puller bolt (Fig. 185).
(8) Tighten puller nut to press clutch cam into
case (Fig. 185). Be sure cam is pressed into case
evenly and does not become cocked.
(9) Remove clutch cam installer tools.
(10) Stake case in 14 places around clutch cam to
help secure cam in case. Use blunt punch or chisel to
stake case.
(11) Remove piston retainer from case. Cover
retainer with plastic sheeting, or paper to keep it
dust free.
(12) Clean case and cam thoroughly. Be sure any
chips/shavings generated during cam installation are
removed from case.
(13) Install new gasket at rear of transmission
case. Use petroleum jelly to hold gasket in place. Be
sure to align governor feed holes in gasket with feed
passages in case (Fig. 186). Also install gasket before
overdrive piston retainer. Center hole in gasket is
smaller than retainer and cannot be installed over
retainer.
Fig. 186 Installing/Aligning Case Gasket
1 - CASE GASKET
2 - BE SURE GOVERNOR TUBE FEED HOLES IN CASE AND
GASKET ARE ALIGNED
Fig. 184 Positioning Puller Plate On Clutch Cam
1 - SPECIAL TOOL SP-3701
2 - BE SURE PLATE SP-3583-A IS SEATED SQUARELY ON CAM
Fig. 185 Pressing Overrunning Clutch Cam Into
Case
1 - SPECIAL TOOL SP-3583-A
2 - TIGHTEN NUT TO DRAW CAM INTO CASE (NUT IS PART OF
BOLT SP-3701)
3 - SPECIAL TOOL SP-5124
4 - SPECIAL TOOL SP-3701
21 - 238 AUTOMATIC TRANSMISSION - 48REDR
OVERRUNNING CLUTCH CAM/OVERDRIVE PISTON RETAINER (Continued)
Page 1942 of 2627
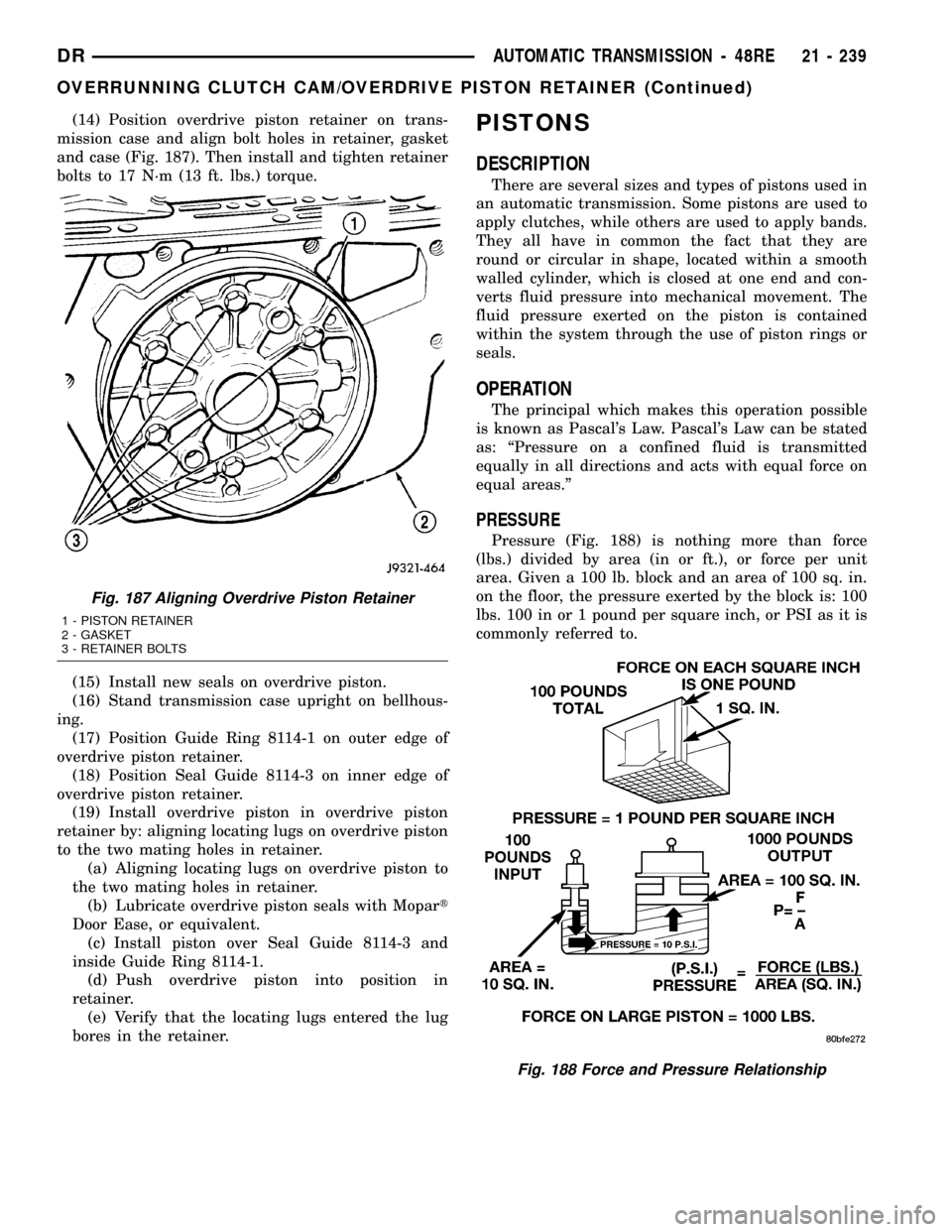
(14) Position overdrive piston retainer on trans-
mission case and align bolt holes in retainer, gasket
and case (Fig. 187). Then install and tighten retainer
bolts to 17 N´m (13 ft. lbs.) torque.
(15) Install new seals on overdrive piston.
(16) Stand transmission case upright on bellhous-
ing.
(17) Position Guide Ring 8114-1 on outer edge of
overdrive piston retainer.
(18) Position Seal Guide 8114-3 on inner edge of
overdrive piston retainer.
(19) Install overdrive piston in overdrive piston
retainer by: aligning locating lugs on overdrive piston
to the two mating holes in retainer.
(a) Aligning locating lugs on overdrive piston to
the two mating holes in retainer.
(b) Lubricate overdrive piston seals with Mopart
Door Ease, or equivalent.
(c) Install piston over Seal Guide 8114-3 and
inside Guide Ring 8114-1.
(d) Push overdrive piston into position in
retainer.
(e) Verify that the locating lugs entered the lug
bores in the retainer.PISTONS
DESCRIPTION
There are several sizes and types of pistons used in
an automatic transmission. Some pistons are used to
apply clutches, while others are used to apply bands.
They all have in common the fact that they are
round or circular in shape, located within a smooth
walled cylinder, which is closed at one end and con-
verts fluid pressure into mechanical movement. The
fluid pressure exerted on the piston is contained
within the system through the use of piston rings or
seals.
OPERATION
The principal which makes this operation possible
is known as Pascal's Law. Pascal's Law can be stated
as: ªPressure on a confined fluid is transmitted
equally in all directions and acts with equal force on
equal areas.º
PRESSURE
Pressure (Fig. 188) is nothing more than force
(lbs.) divided by area (in or ft.), or force per unit
area. Given a 100 lb. block and an area of 100 sq. in.
on the floor, the pressure exerted by the block is: 100
lbs. 100 in or 1 pound per square inch, or PSI as it is
commonly referred to.
Fig. 187 Aligning Overdrive Piston Retainer
1 - PISTON RETAINER
2 - GASKET
3 - RETAINER BOLTS
Fig. 188 Force and Pressure Relationship
DRAUTOMATIC TRANSMISSION - 48RE 21 - 239
OVERRUNNING CLUTCH CAM/OVERDRIVE PISTON RETAINER (Continued)
Page 1943 of 2627
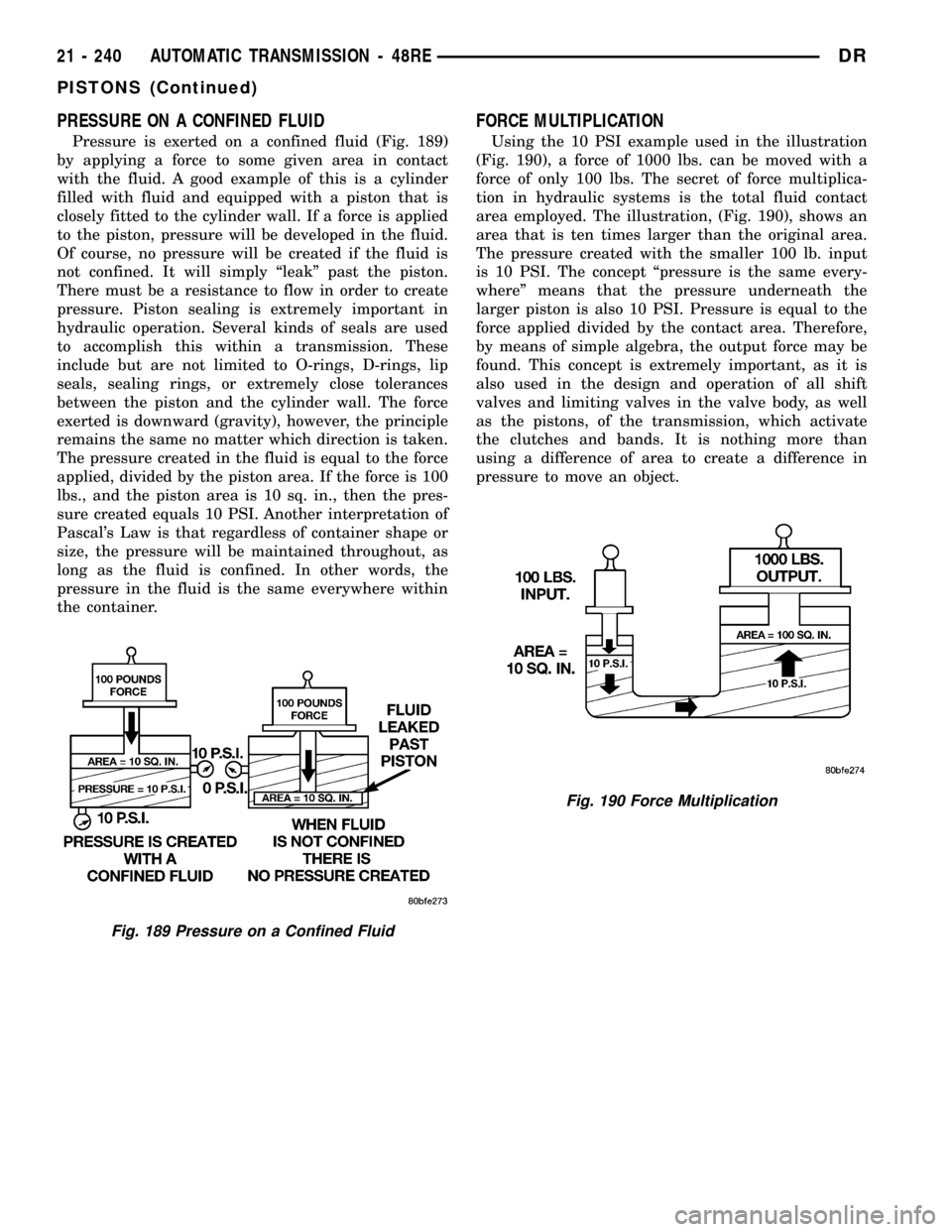
PRESSURE ON A CONFINED FLUID
Pressure is exerted on a confined fluid (Fig. 189)
by applying a force to some given area in contact
with the fluid. A good example of this is a cylinder
filled with fluid and equipped with a piston that is
closely fitted to the cylinder wall. If a force is applied
to the piston, pressure will be developed in the fluid.
Of course, no pressure will be created if the fluid is
not confined. It will simply ªleakº past the piston.
There must be a resistance to flow in order to create
pressure. Piston sealing is extremely important in
hydraulic operation. Several kinds of seals are used
to accomplish this within a transmission. These
include but are not limited to O-rings, D-rings, lip
seals, sealing rings, or extremely close tolerances
between the piston and the cylinder wall. The force
exerted is downward (gravity), however, the principle
remains the same no matter which direction is taken.
The pressure created in the fluid is equal to the force
applied, divided by the piston area. If the force is 100
lbs., and the piston area is 10 sq. in., then the pres-
sure created equals 10 PSI. Another interpretation of
Pascal's Law is that regardless of container shape or
size, the pressure will be maintained throughout, as
long as the fluid is confined. In other words, the
pressure in the fluid is the same everywhere within
the container.
FORCE MULTIPLICATION
Using the 10 PSI example used in the illustration
(Fig. 190), a force of 1000 lbs. can be moved with a
force of only 100 lbs. The secret of force multiplica-
tion in hydraulic systems is the total fluid contact
area employed. The illustration, (Fig. 190), shows an
area that is ten times larger than the original area.
The pressure created with the smaller 100 lb. input
is 10 PSI. The concept ªpressure is the same every-
whereº means that the pressure underneath the
larger piston is also 10 PSI. Pressure is equal to the
force applied divided by the contact area. Therefore,
by means of simple algebra, the output force may be
found. This concept is extremely important, as it is
also used in the design and operation of all shift
valves and limiting valves in the valve body, as well
as the pistons, of the transmission, which activate
the clutches and bands. It is nothing more than
using a difference of area to create a difference in
pressure to move an object.
Fig. 189 Pressure on a Confined Fluid
Fig. 190 Force Multiplication
21 - 240 AUTOMATIC TRANSMISSION - 48REDR
PISTONS (Continued)
Page 1944 of 2627
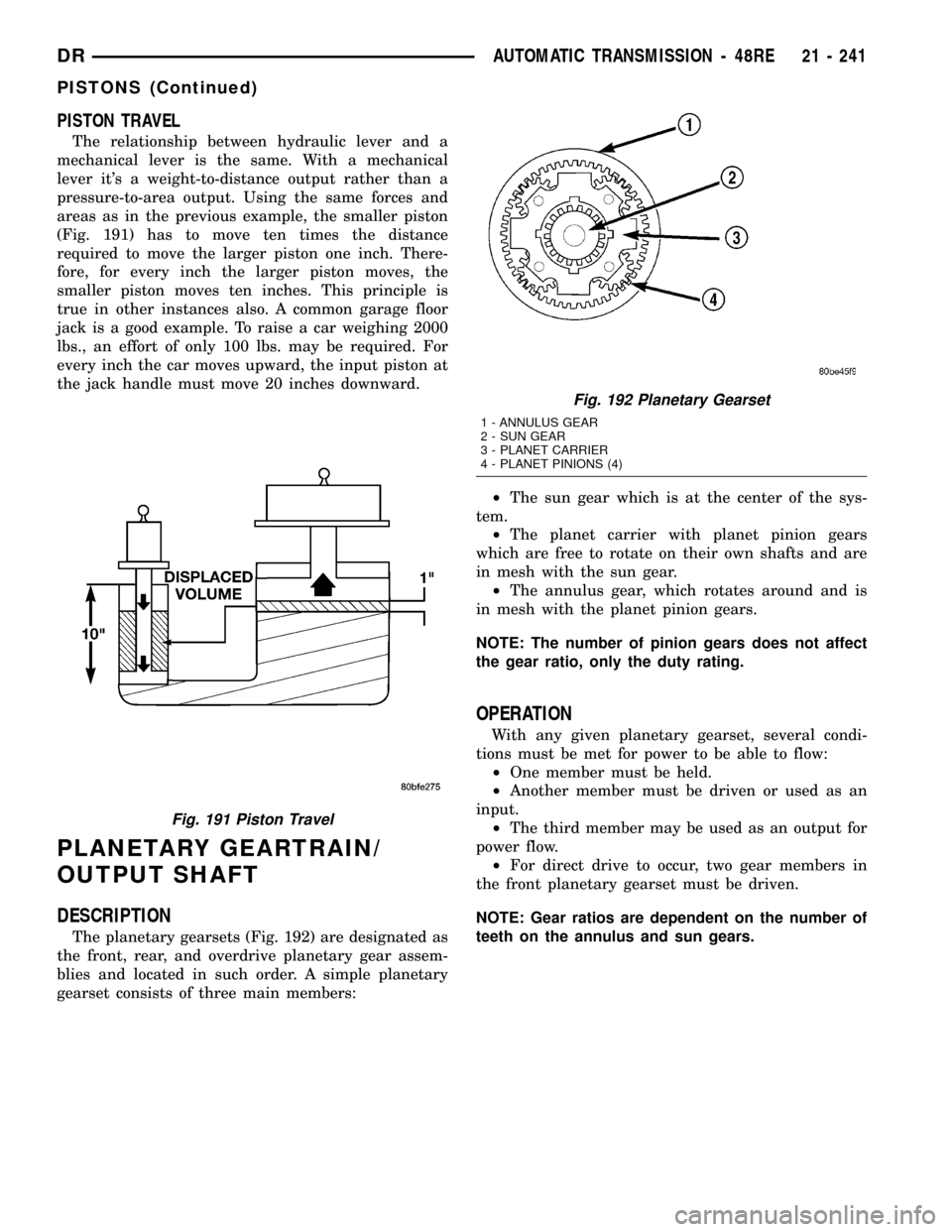
PISTON TRAVEL
The relationship between hydraulic lever and a
mechanical lever is the same. With a mechanical
lever it's a weight-to-distance output rather than a
pressure-to-area output. Using the same forces and
areas as in the previous example, the smaller piston
(Fig. 191) has to move ten times the distance
required to move the larger piston one inch. There-
fore, for every inch the larger piston moves, the
smaller piston moves ten inches. This principle is
true in other instances also. A common garage floor
jack is a good example. To raise a car weighing 2000
lbs., an effort of only 100 lbs. may be required. For
every inch the car moves upward, the input piston at
the jack handle must move 20 inches downward.
PLANETARY GEARTRAIN/
OUTPUT SHAFT
DESCRIPTION
The planetary gearsets (Fig. 192) are designated as
the front, rear, and overdrive planetary gear assem-
blies and located in such order. A simple planetary
gearset consists of three main members:²The sun gear which is at the center of the sys-
tem.
²The planet carrier with planet pinion gears
which are free to rotate on their own shafts and are
in mesh with the sun gear.
²The annulus gear, which rotates around and is
in mesh with the planet pinion gears.
NOTE: The number of pinion gears does not affect
the gear ratio, only the duty rating.
OPERATION
With any given planetary gearset, several condi-
tions must be met for power to be able to flow:
²One member must be held.
²Another member must be driven or used as an
input.
²The third member may be used as an output for
power flow.
²For direct drive to occur, two gear members in
the front planetary gearset must be driven.
NOTE: Gear ratios are dependent on the number of
teeth on the annulus and sun gears.
Fig. 191 Piston Travel
Fig. 192 Planetary Gearset
1 - ANNULUS GEAR
2 - SUN GEAR
3 - PLANET CARRIER
4 - PLANET PINIONS (4)
DRAUTOMATIC TRANSMISSION - 48RE 21 - 241
PISTONS (Continued)