Page 185 of 2627
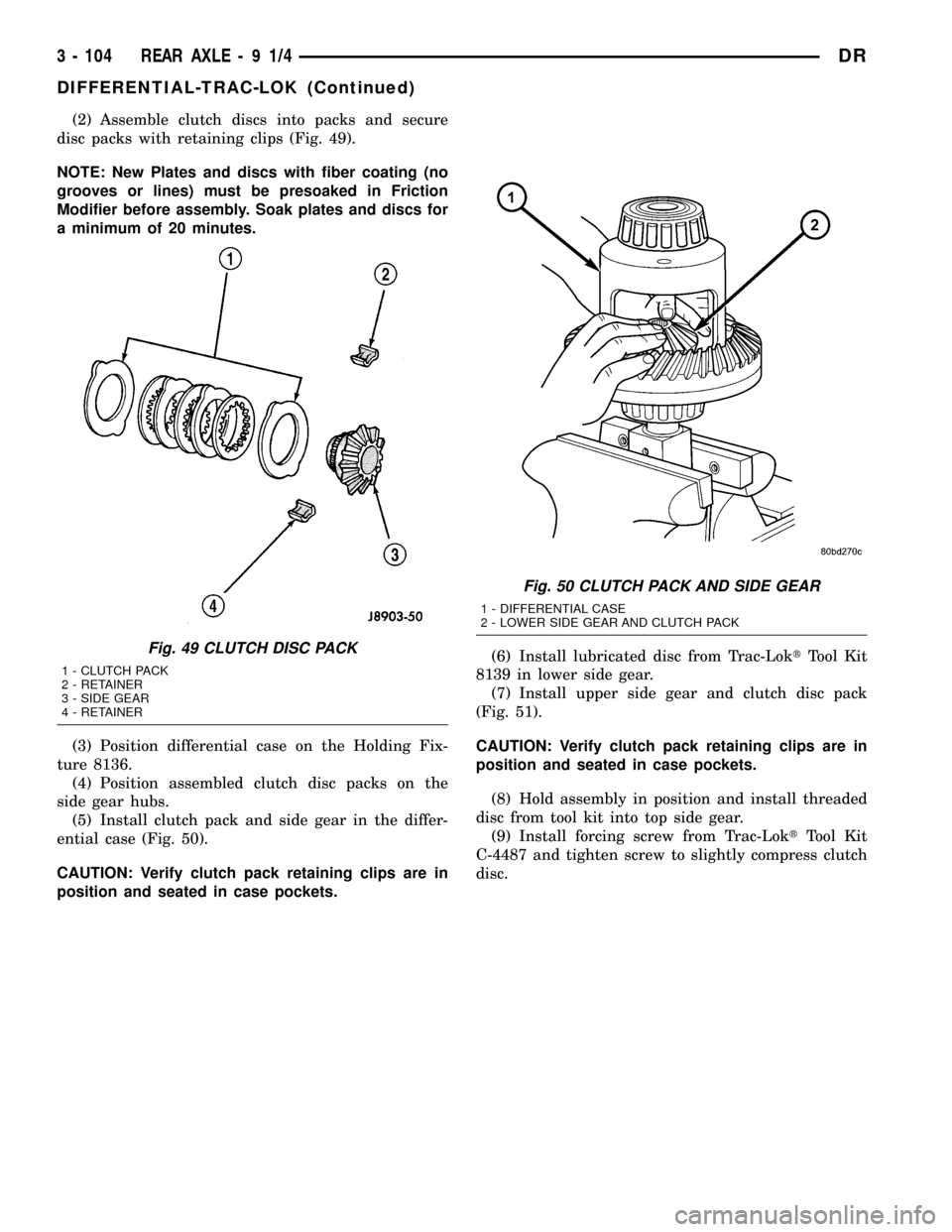
(2) Assemble clutch discs into packs and secure
disc packs with retaining clips (Fig. 49).
NOTE: New Plates and discs with fiber coating (no
grooves or lines) must be presoaked in Friction
Modifier before assembly. Soak plates and discs for
a minimum of 20 minutes.
(3) Position differential case on the Holding Fix-
ture 8136.
(4) Position assembled clutch disc packs on the
side gear hubs.
(5) Install clutch pack and side gear in the differ-
ential case (Fig. 50).
CAUTION: Verify clutch pack retaining clips are in
position and seated in case pockets.(6) Install lubricated disc from Trac-LoktTool Kit
8139 in lower side gear.
(7) Install upper side gear and clutch disc pack
(Fig. 51).
CAUTION: Verify clutch pack retaining clips are in
position and seated in case pockets.
(8) Hold assembly in position and install threaded
disc from tool kit into top side gear.
(9) Install forcing screw from Trac-LoktTool Kit
C-4487 and tighten screw to slightly compress clutch
disc.
Fig. 49 CLUTCH DISC PACK
1 - CLUTCH PACK
2 - RETAINER
3 - SIDE GEAR
4 - RETAINER
Fig. 50 CLUTCH PACK AND SIDE GEAR
1 - DIFFERENTIAL CASE
2 - LOWER SIDE GEAR AND CLUTCH PACK
3 - 104 REAR AXLE-91/4DR
DIFFERENTIAL-TRAC-LOK (Continued)
Page 186 of 2627
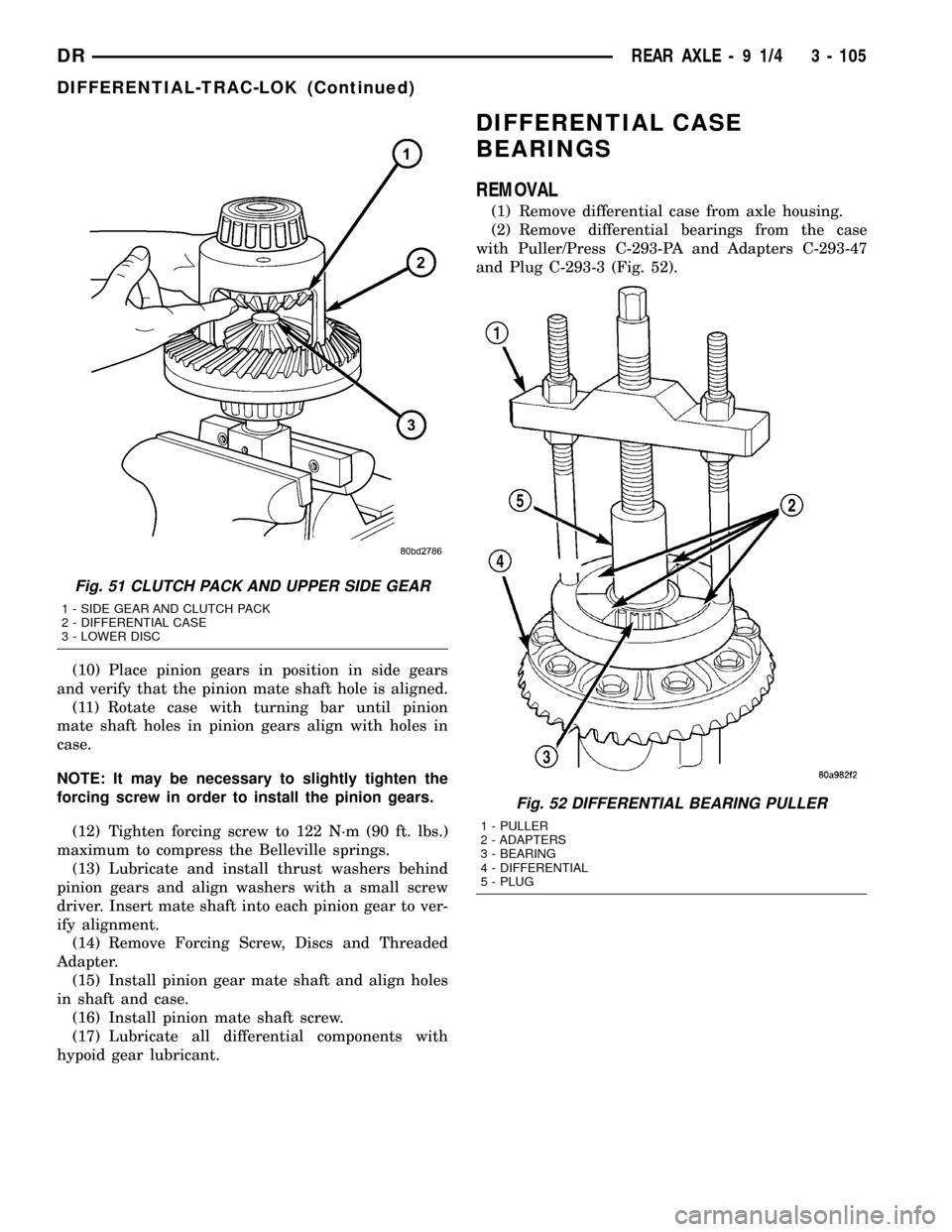
(10) Place pinion gears in position in side gears
and verify that the pinion mate shaft hole is aligned.
(11) Rotate case with turning bar until pinion
mate shaft holes in pinion gears align with holes in
case.
NOTE: It may be necessary to slightly tighten the
forcing screw in order to install the pinion gears.
(12) Tighten forcing screw to 122 N´m (90 ft. lbs.)
maximum to compress the Belleville springs.
(13) Lubricate and install thrust washers behind
pinion gears and align washers with a small screw
driver. Insert mate shaft into each pinion gear to ver-
ify alignment.
(14) Remove Forcing Screw, Discs and Threaded
Adapter.
(15) Install pinion gear mate shaft and align holes
in shaft and case.
(16) Install pinion mate shaft screw.
(17) Lubricate all differential components with
hypoid gear lubricant.
DIFFERENTIAL CASE
BEARINGS
REMOVAL
(1) Remove differential case from axle housing.
(2) Remove differential bearings from the case
with Puller/Press C-293-PA and Adapters C-293-47
and Plug C-293-3 (Fig. 52).
Fig. 51 CLUTCH PACK AND UPPER SIDE GEAR
1 - SIDE GEAR AND CLUTCH PACK
2 - DIFFERENTIAL CASE
3 - LOWER DISC
Fig. 52 DIFFERENTIAL BEARING PULLER
1 - PULLER
2 - ADAPTERS
3 - BEARING
4 - DIFFERENTIAL
5 - PLUG
DRREAR AXLE - 9 1/4 3 - 105
DIFFERENTIAL-TRAC-LOK (Continued)
Page 187 of 2627
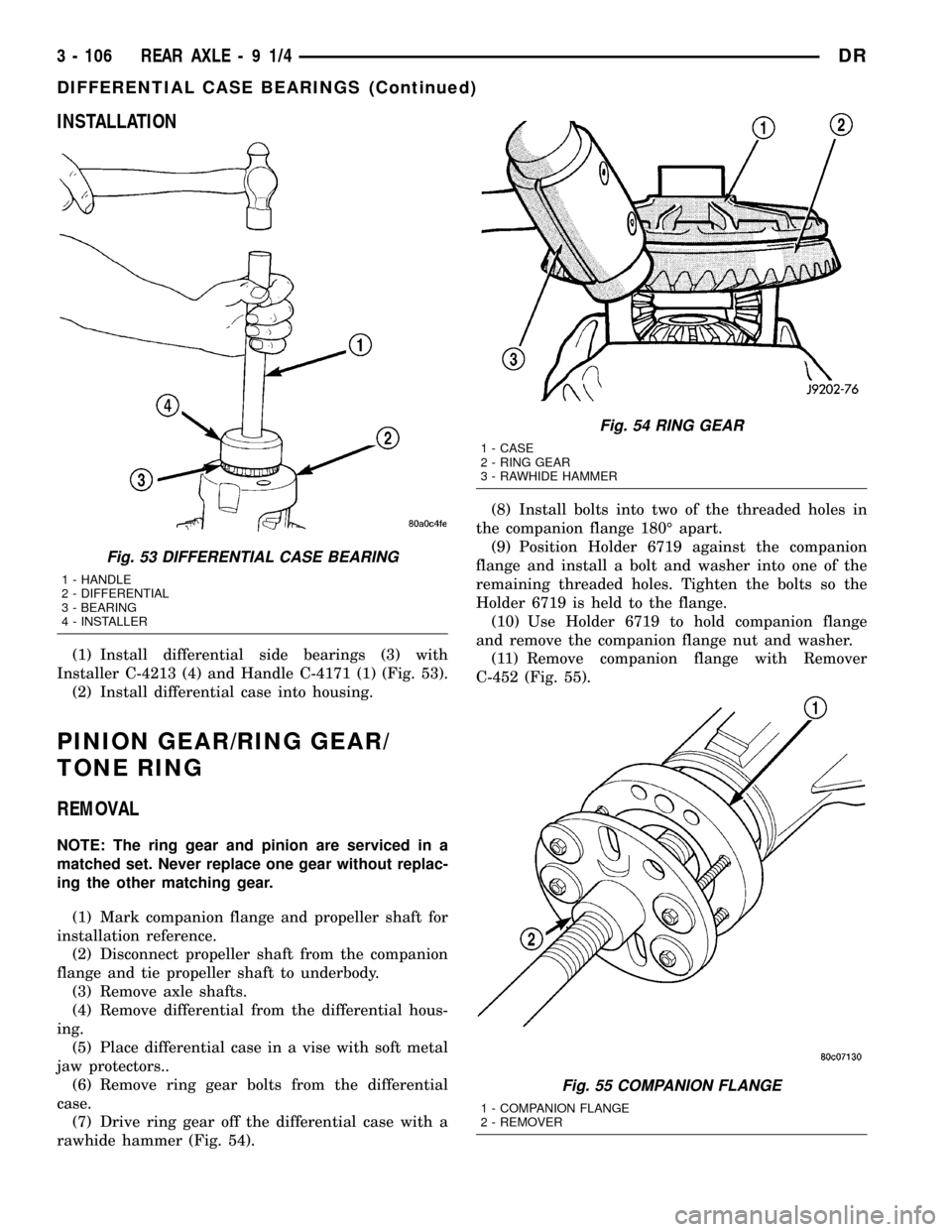
INSTALLATION
(1) Install differential side bearings (3) with
Installer C-4213 (4) and Handle C-4171 (1) (Fig. 53).
(2) Install differential case into housing.
PINION GEAR/RING GEAR/
TONE RING
REMOVAL
NOTE: The ring gear and pinion are serviced in a
matched set. Never replace one gear without replac-
ing the other matching gear.
(1) Mark companion flange and propeller shaft for
installation reference.
(2) Disconnect propeller shaft from the companion
flange and tie propeller shaft to underbody.
(3) Remove axle shafts.
(4) Remove differential from the differential hous-
ing.
(5) Place differential case in a vise with soft metal
jaw protectors..
(6) Remove ring gear bolts from the differential
case.
(7) Drive ring gear off the differential case with a
rawhide hammer (Fig. 54).(8) Install bolts into two of the threaded holes in
the companion flange 180É apart.
(9) Position Holder 6719 against the companion
flange and install a bolt and washer into one of the
remaining threaded holes. Tighten the bolts so the
Holder 6719 is held to the flange.
(10) Use Holder 6719 to hold companion flange
and remove the companion flange nut and washer.
(11) Remove companion flange with Remover
C-452 (Fig. 55).
Fig. 53 DIFFERENTIAL CASE BEARING
1 - HANDLE
2 - DIFFERENTIAL
3 - BEARING
4 - INSTALLER
Fig. 54 RING GEAR
1 - CASE
2 - RING GEAR
3 - RAWHIDE HAMMER
Fig. 55 COMPANION FLANGE
1 - COMPANION FLANGE
2 - REMOVER
3 - 106 REAR AXLE-91/4DR
DIFFERENTIAL CASE BEARINGS (Continued)
Page 188 of 2627
(12)Remove pinion gear from the housing (Fig. 56).
(13) Remove pinion seal with a pry tool or slide-
hammer mounted screw.
(14) Remove front pinion bearing and oil slinger if
equipped.
(15) Remove front pinion bearing cup with
Remover C-4345 and Handle C-4171 (Fig. 57).(16) Remove rear pinion bearing cup from housing
(Fig. 58) with Remover C-4307 and Handle C-4171.
(17) Remove collapsible spacer from the pinion
shaft (Fig. 59).
Fig. 56 PINION GEAR
1 - RAWHIDE HAMMER
Fig. 57 FRONT PINION BEARING CUP
1 - REMOVER
2 - HANDLE
Fig. 58 REAR PINION BEARING CUP
1 - DRIVER
2 - HANDLE
Fig. 59 COLLAPSIBLE SPACER
1 - COLLAPSIBLE SPACER
2 - REAR PINION BEARING
3 - PINION DEPTH SHIM
DRREAR AXLE - 9 1/4 3 - 107
PINION GEAR/RING GEAR/TONE RING (Continued)
Page 189 of 2627
(18) Remove rear pinion bearing (Fig. 60) from the
pinion shaft with Puller C-293-PA and Adapters
C-293-37.
(19) Remove pinion depth shim (Fig. 61) from the
pinion shaft and record shim thickness.
INSTALLATION
NOTE: The ring gear and pinion are serviced in a
matched set. Do not replace one gear without
replacing the other matching gear. If ring and pinion
gears or bearings are replaced, Refer to Adjust-
ments for Pinion Gear Depth Setting.
(1) Apply Mopar Door Ease or equivalent stick
lubricant to outside surface of the pinion bearing
cups.
(2) Install rear pinion bearing cup (Fig. 62) with
Installer C-4308 and Driver Handle C-4171 and ver-
ify cup is seated.
Fig. 60 REAR PINION BEARING
1 - PULLER
2 - VISE
3 - ADAPTERS
4 - PINION SHAFT
Fig. 61 PINION DEPTH SHIM
1 - PINION DEPTH SHIM
2 - PINION GEAR
Fig. 62 REAR PINION BEARING CUP
1 - INSTALLER
2 - HANDLE
3 - 108 REAR AXLE-91/4DR
PINION GEAR/RING GEAR/TONE RING (Continued)
Page 190 of 2627
(3) Install front pinion bearing cup (Fig. 63) with
Installer D-129 and Handle C-4171 and verify cup is
seated.
(4) Lubricate and install front pinion bearing into
the housing.
(5) Apply a light coating of gear lubricant on the
lip of pinion seal. Install seal with Installer C-4076-B
and Handle C-4735-1 (Fig. 64).
(6) Install pinion depth shim (Fig. 65) on the pin-
ion gear shaft.
(7) Install rear bearing on the pinion (Fig. 66) with
Installer C-3095-A and a press.
Fig. 63 FRONT PINION BEARING CUP
1 - INSTALLER
2 - HANDLE
Fig. 64 PINION SEAL INSTALLER
1 - HANDLE
2 - INSTALLER
3 - HOUSING
Fig. 65 PINION DEPTH SHIM
1 - PINION DEPTH SHIM
2 - PINION GEAR
Fig. 66 REAR PINION BEARING
1 - PRESS
2 - INSTALLER
3 - PINION GEAR
4 - REAR PINION BEARING
DRREAR AXLE - 9 1/4 3 - 109
PINION GEAR/RING GEAR/TONE RING (Continued)
Page 191 of 2627
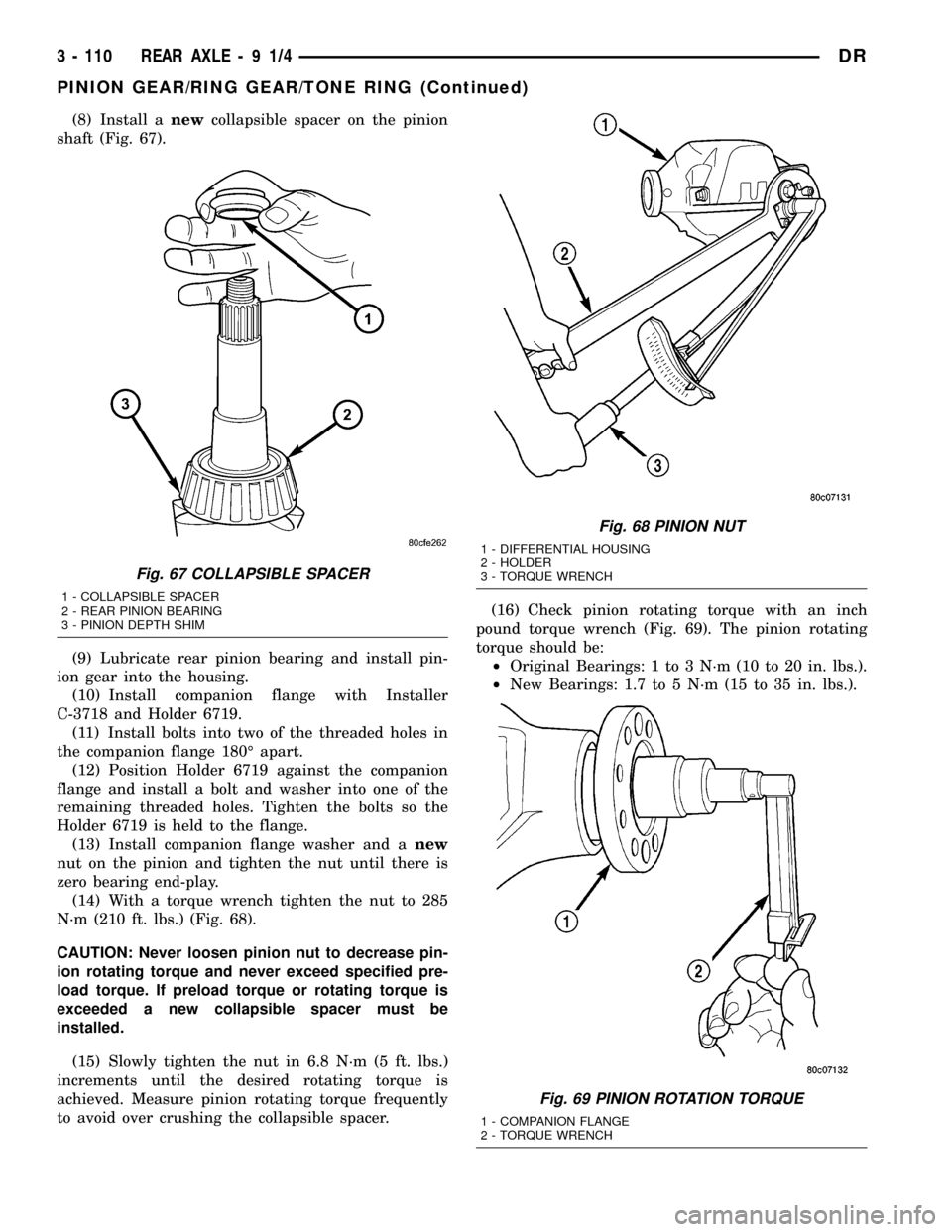
(8) Install anewcollapsible spacer on the pinion
shaft (Fig. 67).
(9) Lubricate rear pinion bearing and install pin-
ion gear into the housing.
(10) Install companion flange with Installer
C-3718 and Holder 6719.
(11) Install bolts into two of the threaded holes in
the companion flange 180É apart.
(12) Position Holder 6719 against the companion
flange and install a bolt and washer into one of the
remaining threaded holes. Tighten the bolts so the
Holder 6719 is held to the flange.
(13) Install companion flange washer and anew
nut on the pinion and tighten the nut until there is
zero bearing end-play.
(14) With a torque wrench tighten the nut to 285
N´m (210 ft. lbs.) (Fig. 68).
CAUTION: Never loosen pinion nut to decrease pin-
ion rotating torque and never exceed specified pre-
load torque. If preload torque or rotating torque is
exceeded a new collapsible spacer must be
installed.
(15) Slowly tighten the nut in 6.8 N´m (5 ft. lbs.)
increments until the desired rotating torque is
achieved. Measure pinion rotating torque frequently
to avoid over crushing the collapsible spacer.(16) Check pinion rotating torque with an inch
pound torque wrench (Fig. 69). The pinion rotating
torque should be:
²Original Bearings: 1 to 3 N´m (10 to 20 in. lbs.).
²New Bearings: 1.7 to 5 N´m (15 to 35 in. lbs.).
Fig. 67 COLLAPSIBLE SPACER
1 - COLLAPSIBLE SPACER
2 - REAR PINION BEARING
3 - PINION DEPTH SHIM
Fig. 68 PINION NUT
1 - DIFFERENTIAL HOUSING
2 - HOLDER
3 - TORQUE WRENCH
Fig. 69 PINION ROTATION TORQUE
1 - COMPANION FLANGE
2 - TORQUE WRENCH
3 - 110 REAR AXLE-91/4DR
PINION GEAR/RING GEAR/TONE RING (Continued)
Page 192 of 2627
(17) Position exciter ring on differential case. With
a brass drift, slowly and evenly tap the exciter ring
into position.
(18) Position ring gear on the differential case and
start two ring gear bolts. This will provide case-to-
ring gear bolt hole alignment.
(19) Invert the differential case in the vise.
(20) Installnewring gear bolts and alternately
tighten to 156 N´m (115 ft. lbs.) (Fig. 70).
CAUTION: Never reuse the ring gear bolts. The
bolts can fracture causing extensive damage.
(21) Install differential in housing and verify gear
mesh, backlash and contact pattern.
(22) Install axle shafts.
(23) Install differential cover and fill with gear
lubricant.
(24) Install propeller shaft with reference marks
aligned.
Fig. 70 RING GEAR BOLTS
1 - TORQUE WRENCH
2 - RING GEAR BOLTS
3 - RING GEAR
4 - DIFFERENTIAL CASE
DRREAR AXLE - 9 1/4 3 - 111
PINION GEAR/RING GEAR/TONE RING (Continued)