Page 2097 of 2627
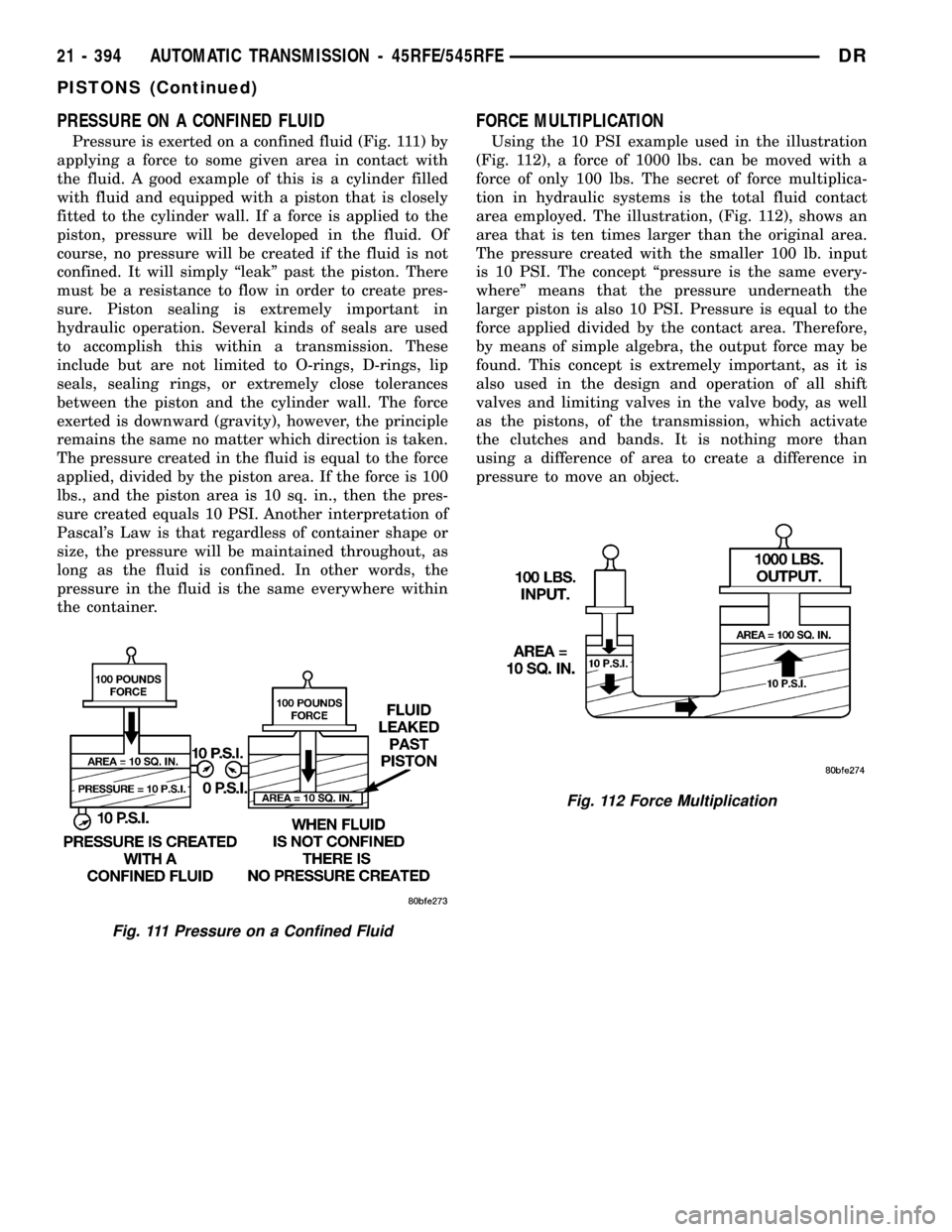
PRESSURE ON A CONFINED FLUID
Pressure is exerted on a confined fluid (Fig. 111) by
applying a force to some given area in contact with
the fluid. A good example of this is a cylinder filled
with fluid and equipped with a piston that is closely
fitted to the cylinder wall. If a force is applied to the
piston, pressure will be developed in the fluid. Of
course, no pressure will be created if the fluid is not
confined. It will simply ªleakº past the piston. There
must be a resistance to flow in order to create pres-
sure. Piston sealing is extremely important in
hydraulic operation. Several kinds of seals are used
to accomplish this within a transmission. These
include but are not limited to O-rings, D-rings, lip
seals, sealing rings, or extremely close tolerances
between the piston and the cylinder wall. The force
exerted is downward (gravity), however, the principle
remains the same no matter which direction is taken.
The pressure created in the fluid is equal to the force
applied, divided by the piston area. If the force is 100
lbs., and the piston area is 10 sq. in., then the pres-
sure created equals 10 PSI. Another interpretation of
Pascal's Law is that regardless of container shape or
size, the pressure will be maintained throughout, as
long as the fluid is confined. In other words, the
pressure in the fluid is the same everywhere within
the container.
FORCE MULTIPLICATION
Using the 10 PSI example used in the illustration
(Fig. 112), a force of 1000 lbs. can be moved with a
force of only 100 lbs. The secret of force multiplica-
tion in hydraulic systems is the total fluid contact
area employed. The illustration, (Fig. 112), shows an
area that is ten times larger than the original area.
The pressure created with the smaller 100 lb. input
is 10 PSI. The concept ªpressure is the same every-
whereº means that the pressure underneath the
larger piston is also 10 PSI. Pressure is equal to the
force applied divided by the contact area. Therefore,
by means of simple algebra, the output force may be
found. This concept is extremely important, as it is
also used in the design and operation of all shift
valves and limiting valves in the valve body, as well
as the pistons, of the transmission, which activate
the clutches and bands. It is nothing more than
using a difference of area to create a difference in
pressure to move an object.
Fig. 111 Pressure on a Confined Fluid
Fig. 112 Force Multiplication
21 - 394 AUTOMATIC TRANSMISSION - 45RFE/545RFEDR
PISTONS (Continued)
Page 2098 of 2627
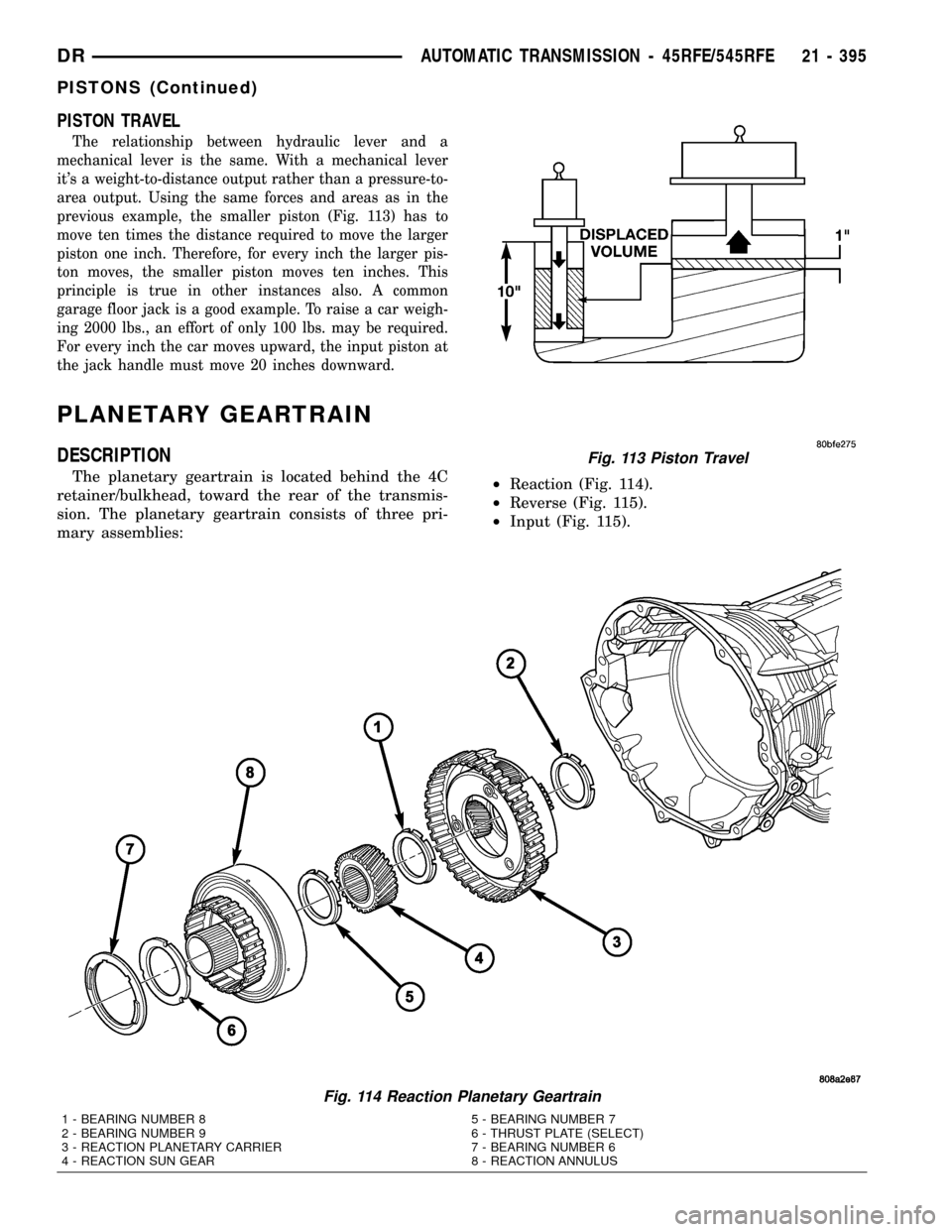
PISTON TRAVEL
The relationship between hydraulic lever and a
mechanical lever is the same. With a mechanical lever
it's a weight-to-distance output rather than a pressure-to-
area output. Using the same forces and areas as in the
previous example, the smaller piston (Fig. 113) has to
move ten times the distance required to move the larger
piston one inch. Therefore, for every inch the larger pis-
ton moves, the smaller piston moves ten inches. This
principle is true in other instances also. A common
garage floor jack is a good example. To raise a car weigh-
ing 2000 lbs., an effort of only 100 lbs. may be required.
For every inch the car moves upward, the input piston at
the jack handle must move 20 inches downward.
PLANETARY GEARTRAIN
DESCRIPTION
The planetary geartrain is located behind the 4C
retainer/bulkhead, toward the rear of the transmis-
sion. The planetary geartrain consists of three pri-
mary assemblies:²Reaction (Fig. 114).
²Reverse (Fig. 115).
²Input (Fig. 115).
Fig. 113 Piston Travel
Fig. 114 Reaction Planetary Geartrain
1 - BEARING NUMBER 8 5 - BEARING NUMBER 7
2 - BEARING NUMBER 9 6 - THRUST PLATE (SELECT)
3 - REACTION PLANETARY CARRIER 7 - BEARING NUMBER 6
4 - REACTION SUN GEAR 8 - REACTION ANNULUS
DRAUTOMATIC TRANSMISSION - 45RFE/545RFE 21 - 395
PISTONS (Continued)
Page 2099 of 2627
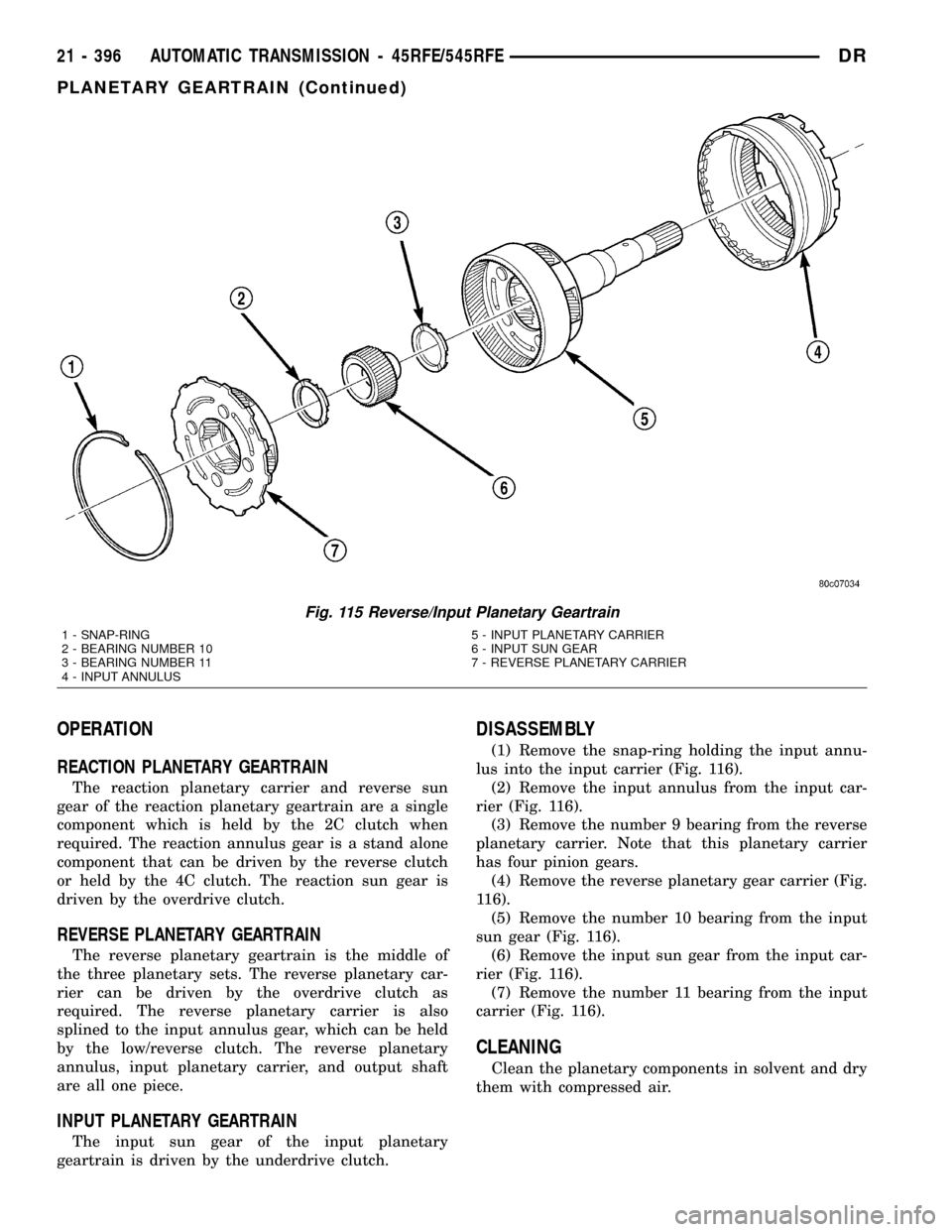
OPERATION
REACTION PLANETARY GEARTRAIN
The reaction planetary carrier and reverse sun
gear of the reaction planetary geartrain are a single
component which is held by the 2C clutch when
required. The reaction annulus gear is a stand alone
component that can be driven by the reverse clutch
or held by the 4C clutch. The reaction sun gear is
driven by the overdrive clutch.
REVERSE PLANETARY GEARTRAIN
The reverse planetary geartrain is the middle of
the three planetary sets. The reverse planetary car-
rier can be driven by the overdrive clutch as
required. The reverse planetary carrier is also
splined to the input annulus gear, which can be held
by the low/reverse clutch. The reverse planetary
annulus, input planetary carrier, and output shaft
are all one piece.
INPUT PLANETARY GEARTRAIN
The input sun gear of the input planetary
geartrain is driven by the underdrive clutch.
DISASSEMBLY
(1) Remove the snap-ring holding the input annu-
lus into the input carrier (Fig. 116).
(2) Remove the input annulus from the input car-
rier (Fig. 116).
(3) Remove the number 9 bearing from the reverse
planetary carrier. Note that this planetary carrier
has four pinion gears.
(4) Remove the reverse planetary gear carrier (Fig.
116).
(5) Remove the number 10 bearing from the input
sun gear (Fig. 116).
(6) Remove the input sun gear from the input car-
rier (Fig. 116).
(7) Remove the number 11 bearing from the input
carrier (Fig. 116).
CLEANING
Clean the planetary components in solvent and dry
them with compressed air.
Fig. 115 Reverse/Input Planetary Geartrain
1 - SNAP-RING 5 - INPUT PLANETARY CARRIER
2 - BEARING NUMBER 10 6 - INPUT SUN GEAR
3 - BEARING NUMBER 11 7 - REVERSE PLANETARY CARRIER
4 - INPUT ANNULUS
21 - 396 AUTOMATIC TRANSMISSION - 45RFE/545RFEDR
PLANETARY GEARTRAIN (Continued)
Page 2100 of 2627
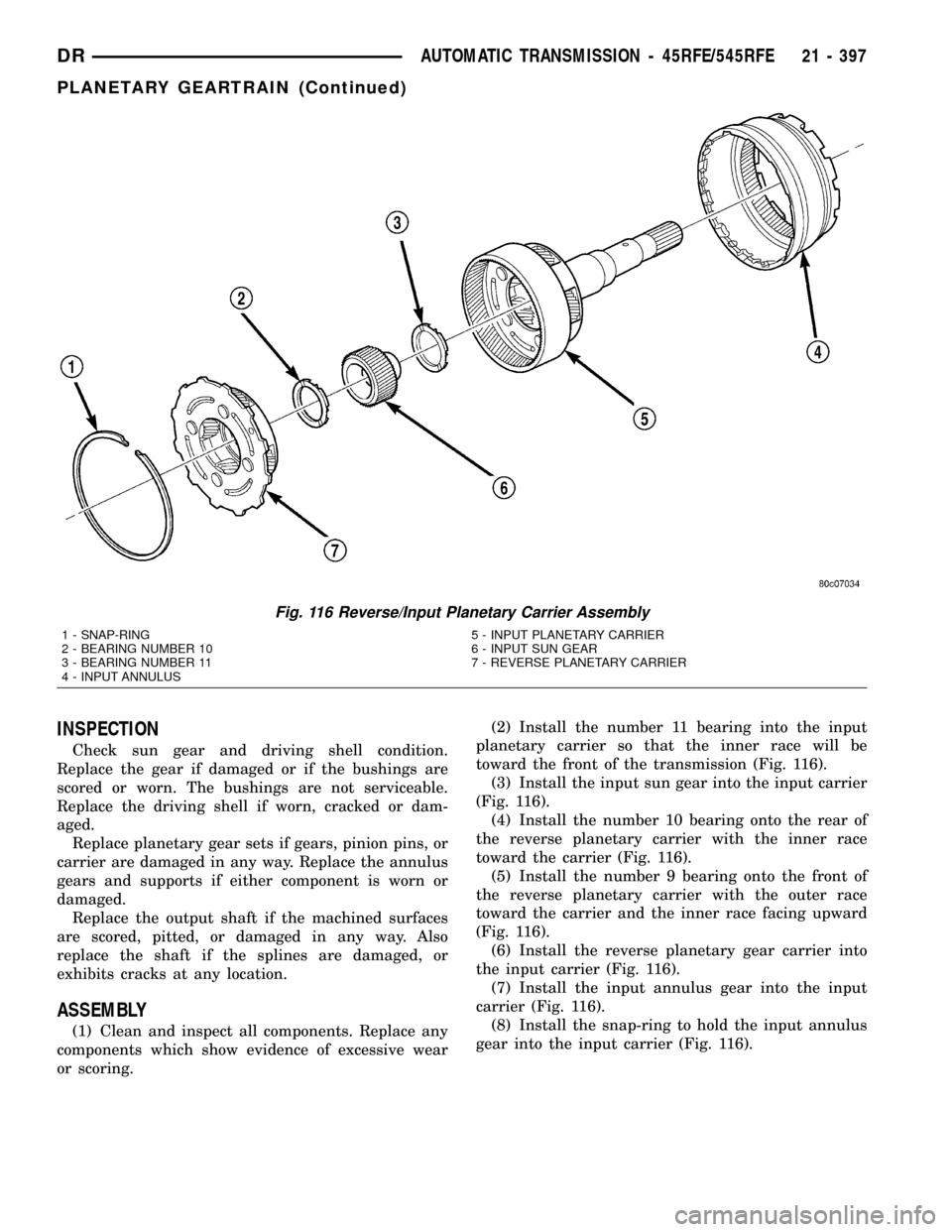
INSPECTION
Check sun gear and driving shell condition.
Replace the gear if damaged or if the bushings are
scored or worn. The bushings are not serviceable.
Replace the driving shell if worn, cracked or dam-
aged.
Replace planetary gear sets if gears, pinion pins, or
carrier are damaged in any way. Replace the annulus
gears and supports if either component is worn or
damaged.
Replace the output shaft if the machined surfaces
are scored, pitted, or damaged in any way. Also
replace the shaft if the splines are damaged, or
exhibits cracks at any location.
ASSEMBLY
(1) Clean and inspect all components. Replace any
components which show evidence of excessive wear
or scoring.(2) Install the number 11 bearing into the input
planetary carrier so that the inner race will be
toward the front of the transmission (Fig. 116).
(3) Install the input sun gear into the input carrier
(Fig. 116).
(4) Install the number 10 bearing onto the rear of
the reverse planetary carrier with the inner race
toward the carrier (Fig. 116).
(5) Install the number 9 bearing onto the front of
the reverse planetary carrier with the outer race
toward the carrier and the inner race facing upward
(Fig. 116).
(6) Install the reverse planetary gear carrier into
the input carrier (Fig. 116).
(7) Install the input annulus gear into the input
carrier (Fig. 116).
(8) Install the snap-ring to hold the input annulus
gear into the input carrier (Fig. 116).
Fig. 116 Reverse/Input Planetary Carrier Assembly
1 - SNAP-RING 5 - INPUT PLANETARY CARRIER
2 - BEARING NUMBER 10 6 - INPUT SUN GEAR
3 - BEARING NUMBER 11 7 - REVERSE PLANETARY CARRIER
4 - INPUT ANNULUS
DRAUTOMATIC TRANSMISSION - 45RFE/545RFE 21 - 397
PLANETARY GEARTRAIN (Continued)
Page 2101 of 2627
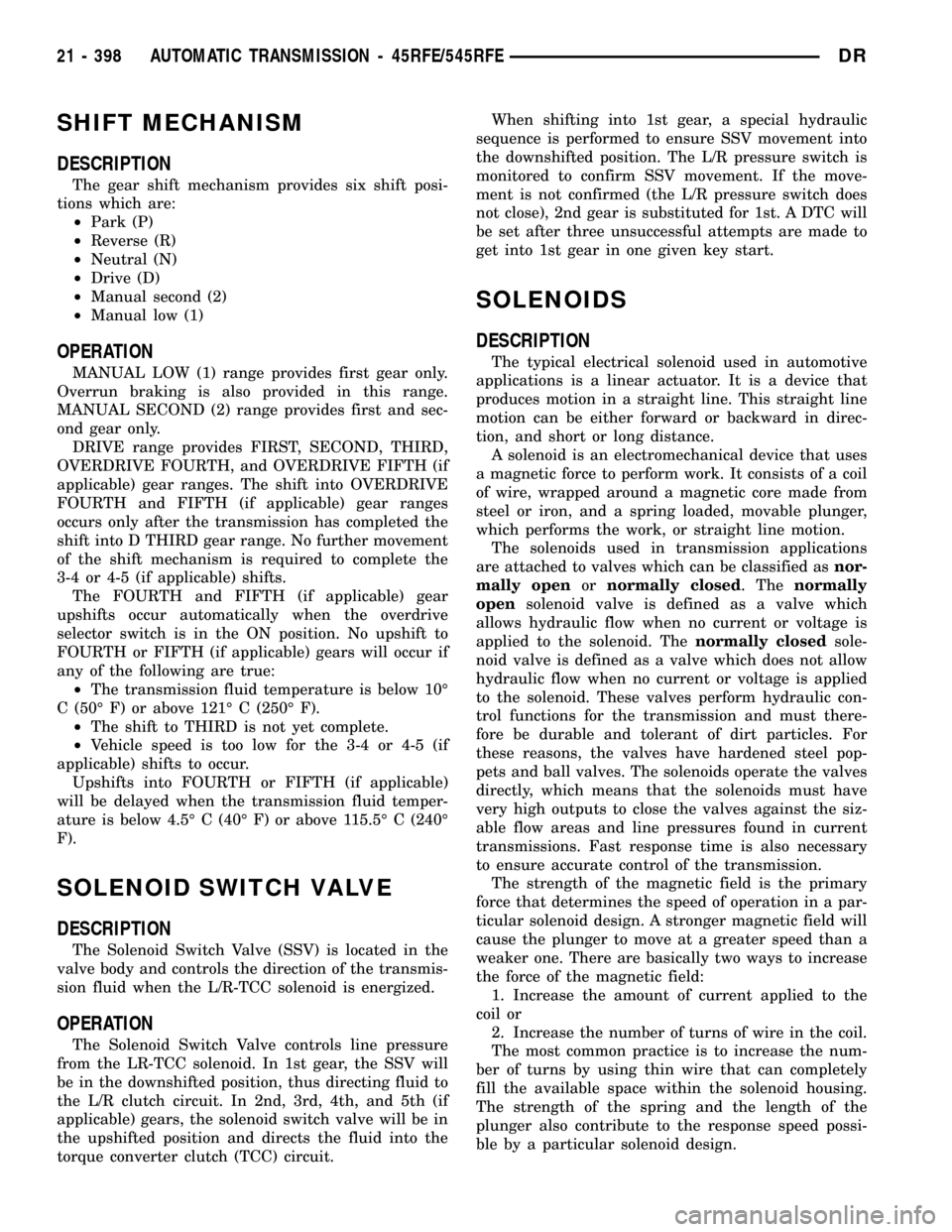
SHIFT MECHANISM
DESCRIPTION
The gear shift mechanism provides six shift posi-
tions which are:
²Park (P)
²Reverse (R)
²Neutral (N)
²Drive (D)
²Manual second (2)
²Manual low (1)
OPERATION
MANUAL LOW (1) range provides first gear only.
Overrun braking is also provided in this range.
MANUAL SECOND (2) range provides first and sec-
ond gear only.
DRIVE range provides FIRST, SECOND, THIRD,
OVERDRIVE FOURTH, and OVERDRIVE FIFTH (if
applicable) gear ranges. The shift into OVERDRIVE
FOURTH and FIFTH (if applicable) gear ranges
occurs only after the transmission has completed the
shift into D THIRD gear range. No further movement
of the shift mechanism is required to complete the
3-4 or 4-5 (if applicable) shifts.
The FOURTH and FIFTH (if applicable) gear
upshifts occur automatically when the overdrive
selector switch is in the ON position. No upshift to
FOURTH or FIFTH (if applicable) gears will occur if
any of the following are true:
²The transmission fluid temperature is below 10É
C (50É F) or above 121É C (250É F).
²The shift to THIRD is not yet complete.
²Vehicle speed is too low for the 3-4 or 4-5 (if
applicable) shifts to occur.
Upshifts into FOURTH or FIFTH (if applicable)
will be delayed when the transmission fluid temper-
ature is below 4.5É C (40É F) or above 115.5É C (240É
F).
SOLENOID SWITCH VALVE
DESCRIPTION
The Solenoid Switch Valve (SSV) is located in the
valve body and controls the direction of the transmis-
sion fluid when the L/R-TCC solenoid is energized.
OPERATION
The Solenoid Switch Valve controls line pressure
from the LR-TCC solenoid. In 1st gear, the SSV will
be in the downshifted position, thus directing fluid to
the L/R clutch circuit. In 2nd, 3rd, 4th, and 5th (if
applicable) gears, the solenoid switch valve will be in
the upshifted position and directs the fluid into the
torque converter clutch (TCC) circuit.When shifting into 1st gear, a special hydraulic
sequence is performed to ensure SSV movement into
the downshifted position. The L/R pressure switch is
monitored to confirm SSV movement. If the move-
ment is not confirmed (the L/R pressure switch does
not close), 2nd gear is substituted for 1st. A DTC will
be set after three unsuccessful attempts are made to
get into 1st gear in one given key start.
SOLENOIDS
DESCRIPTION
The typical electrical solenoid used in automotive
applications is a linear actuator. It is a device that
produces motion in a straight line. This straight line
motion can be either forward or backward in direc-
tion, and short or long distance.
A solenoid is an electromechanical device that uses
a magnetic force to perform work. It consists of a coil
of wire, wrapped around a magnetic core made from
steel or iron, and a spring loaded, movable plunger,
which performs the work, or straight line motion.
The solenoids used in transmission applications
are attached to valves which can be classified asnor-
mally openornormally closed. Thenormally
opensolenoid valve is defined as a valve which
allows hydraulic flow when no current or voltage is
applied to the solenoid. Thenormally closedsole-
noid valve is defined as a valve which does not allow
hydraulic flow when no current or voltage is applied
to the solenoid. These valves perform hydraulic con-
trol functions for the transmission and must there-
fore be durable and tolerant of dirt particles. For
these reasons, the valves have hardened steel pop-
pets and ball valves. The solenoids operate the valves
directly, which means that the solenoids must have
very high outputs to close the valves against the siz-
able flow areas and line pressures found in current
transmissions. Fast response time is also necessary
to ensure accurate control of the transmission.
The strength of the magnetic field is the primary
force that determines the speed of operation in a par-
ticular solenoid design. A stronger magnetic field will
cause the plunger to move at a greater speed than a
weaker one. There are basically two ways to increase
the force of the magnetic field:
1. Increase the amount of current applied to the
coil or
2. Increase the number of turns of wire in the coil.
The most common practice is to increase the num-
ber of turns by using thin wire that can completely
fill the available space within the solenoid housing.
The strength of the spring and the length of the
plunger also contribute to the response speed possi-
ble by a particular solenoid design.
21 - 398 AUTOMATIC TRANSMISSION - 45RFE/545RFEDR
Page 2102 of 2627
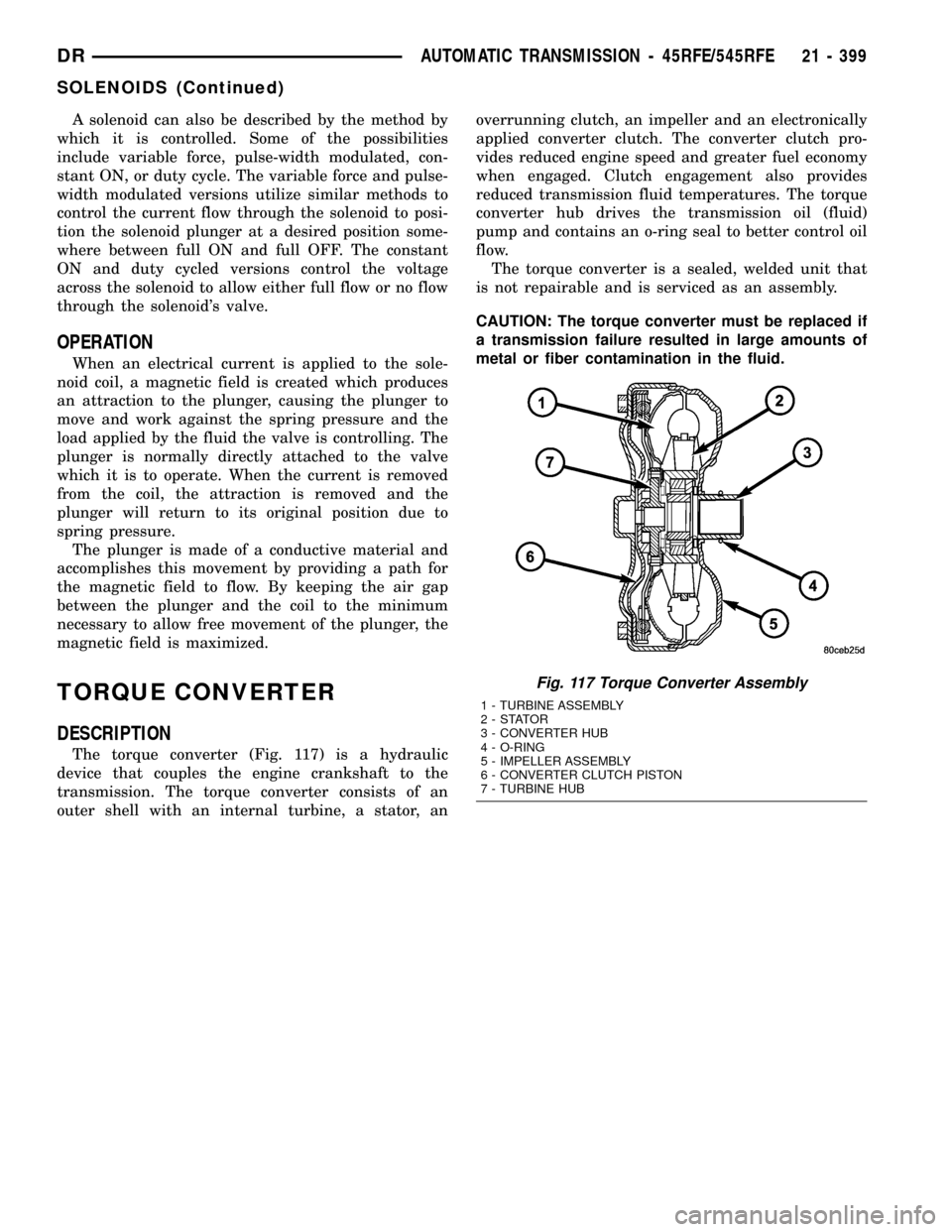
A solenoid can also be described by the method by
which it is controlled. Some of the possibilities
include variable force, pulse-width modulated, con-
stant ON, or duty cycle. The variable force and pulse-
width modulated versions utilize similar methods to
control the current flow through the solenoid to posi-
tion the solenoid plunger at a desired position some-
where between full ON and full OFF. The constant
ON and duty cycled versions control the voltage
across the solenoid to allow either full flow or no flow
through the solenoid's valve.
OPERATION
When an electrical current is applied to the sole-
noid coil, a magnetic field is created which produces
an attraction to the plunger, causing the plunger to
move and work against the spring pressure and the
load applied by the fluid the valve is controlling. The
plunger is normally directly attached to the valve
which it is to operate. When the current is removed
from the coil, the attraction is removed and the
plunger will return to its original position due to
spring pressure.
The plunger is made of a conductive material and
accomplishes this movement by providing a path for
the magnetic field to flow. By keeping the air gap
between the plunger and the coil to the minimum
necessary to allow free movement of the plunger, the
magnetic field is maximized.
TORQUE CONVERTER
DESCRIPTION
The torque converter (Fig. 117) is a hydraulic
device that couples the engine crankshaft to the
transmission. The torque converter consists of an
outer shell with an internal turbine, a stator, anoverrunning clutch, an impeller and an electronically
applied converter clutch. The converter clutch pro-
vides reduced engine speed and greater fuel economy
when engaged. Clutch engagement also provides
reduced transmission fluid temperatures. The torque
converter hub drives the transmission oil (fluid)
pump and contains an o-ring seal to better control oil
flow.
The torque converter is a sealed, welded unit that
is not repairable and is serviced as an assembly.
CAUTION: The torque converter must be replaced if
a transmission failure resulted in large amounts of
metal or fiber contamination in the fluid.
Fig. 117 Torque Converter Assembly
1 - TURBINE ASSEMBLY
2-STATOR
3 - CONVERTER HUB
4 - O-RING
5 - IMPELLER ASSEMBLY
6 - CONVERTER CLUTCH PISTON
7 - TURBINE HUB
DRAUTOMATIC TRANSMISSION - 45RFE/545RFE 21 - 399
SOLENOIDS (Continued)
Page 2103 of 2627
IMPELLER
The impeller (Fig. 118) is an integral part of the
converter housing. The impeller consists of curved
blades placed radially along the inside of the housing
on the transmission side of the converter. As the con-
verter housing is rotated by the engine, so is the
impeller, because they are one and the same and are
the driving members of the system.
Fig. 118 Impeller
1 - ENGINE FLEXPLATE 4 - ENGINE ROTATION
2 - OIL FLOW FROM IMPELLER SECTION INTO TURBINE
SECTION5 - ENGINE ROTATION
3 - IMPELLER VANES AND COVER ARE INTEGRAL
21 - 400 AUTOMATIC TRANSMISSION - 45RFE/545RFEDR
TORQUE CONVERTER (Continued)
Page 2104 of 2627
TURBINE
The turbine (Fig. 119) is the output, or driven,
member of the converter. The turbine is mounted
within the housing opposite the impeller, but is not
attached to the housing. The input shaft is inserted
through the center of the impeller and splined into
the turbine. The design of the turbine is similar to
the impeller, except the blades of the turbine are
curved in the opposite direction.
Fig. 119 Turbine
1 - TURBINE VANE 4 - PORTION OF TORQUE CONVERTER COVER
2 - ENGINE ROTATION 5 - ENGINE ROTATION
3 - INPUT SHAFT 6 - OIL FLOW WITHIN TURBINE SECTION
DRAUTOMATIC TRANSMISSION - 45RFE/545RFE 21 - 401
TORQUE CONVERTER (Continued)