Page 41 of 1007
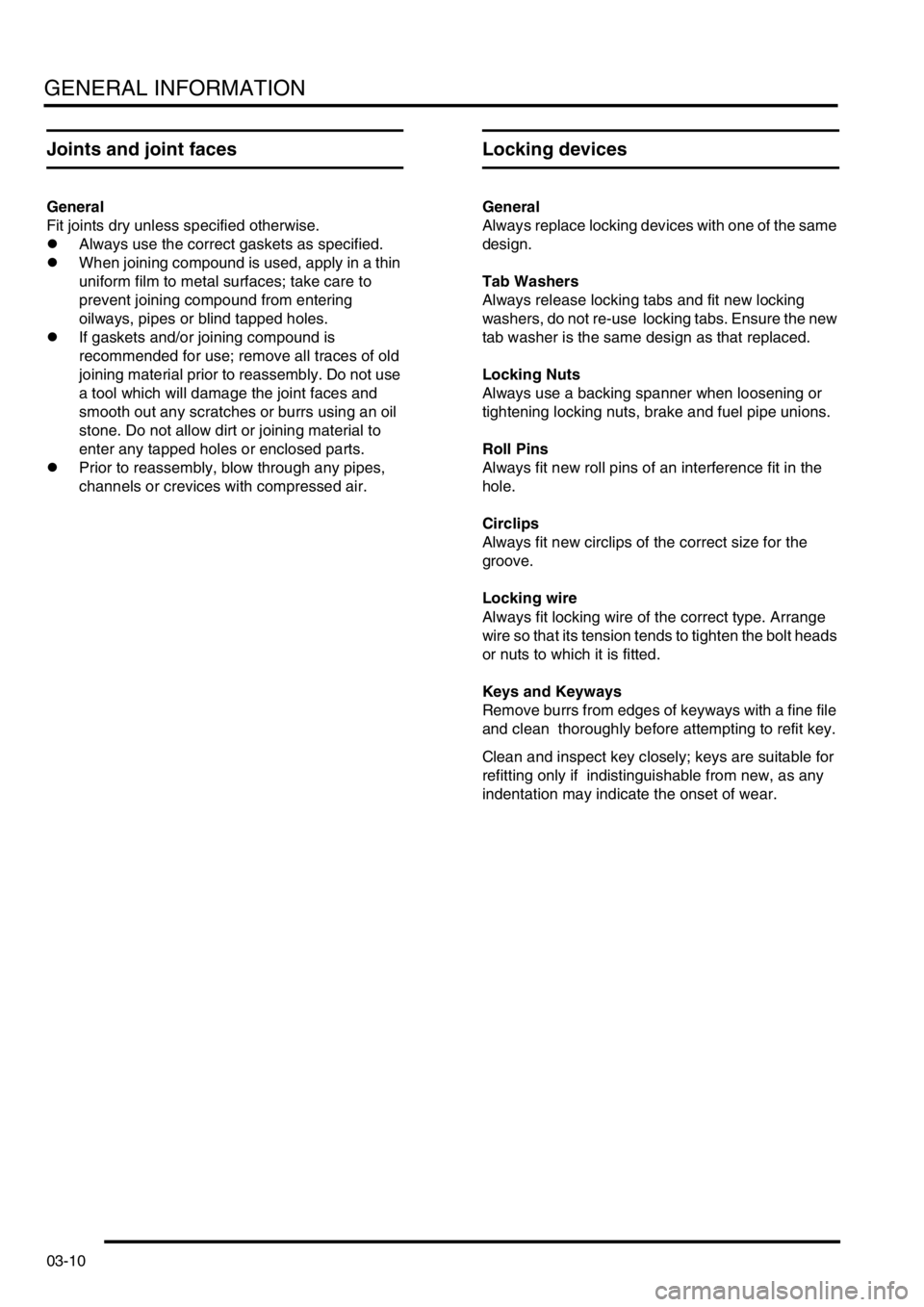
GENERAL INFORMATION
03-10
Joints and joint faces
General
Fit joints dry unless specified otherwise.
lAlways use the correct gaskets as specified.
lWhen joining compound is used, apply in a thin
uniform film to metal surfaces; take care to
prevent joining compound from entering
oilways, pipes or blind tapped holes.
lIf gaskets and/or joining compound is
recommended for use; remove all traces of old
joining material prior to reassembly. Do not use
a tool which will damage the joint faces and
smooth out any scratches or burrs using an oil
stone. Do not allow dirt or joining material to
enter any tapped holes or enclosed parts.
lPrior to reassembly, blow through any pipes,
channels or crevices with compressed air.
Locking devices
General
Always replace locking devices with one of the same
design.
Tab Washers
Always release locking tabs and fit new locking
washers, do not re-use locking tabs. Ensure the new
tab washer is the same design as that replaced.
Locking Nuts
Always use a backing spanner when loosening or
tightening locking nuts, brake and fuel pipe unions.
Roll Pins
Always fit new roll pins of an interference fit in the
hole.
Circlips
Always fit new circlips of the correct size for the
groove.
Locking wire
Always fit locking wire of the correct type. Arrange
wire so that its tension tends to tighten the bolt heads
or nuts to which it is fitted.
Keys and Keyways
Remove burrs from edges of keyways with a fine file
and clean thoroughly before attempting to refit key.
Clean and inspect key closely; keys are suitable for
refitting only if indistinguishable from new, as any
indentation may indicate the onset of wear.
Page 42 of 1007
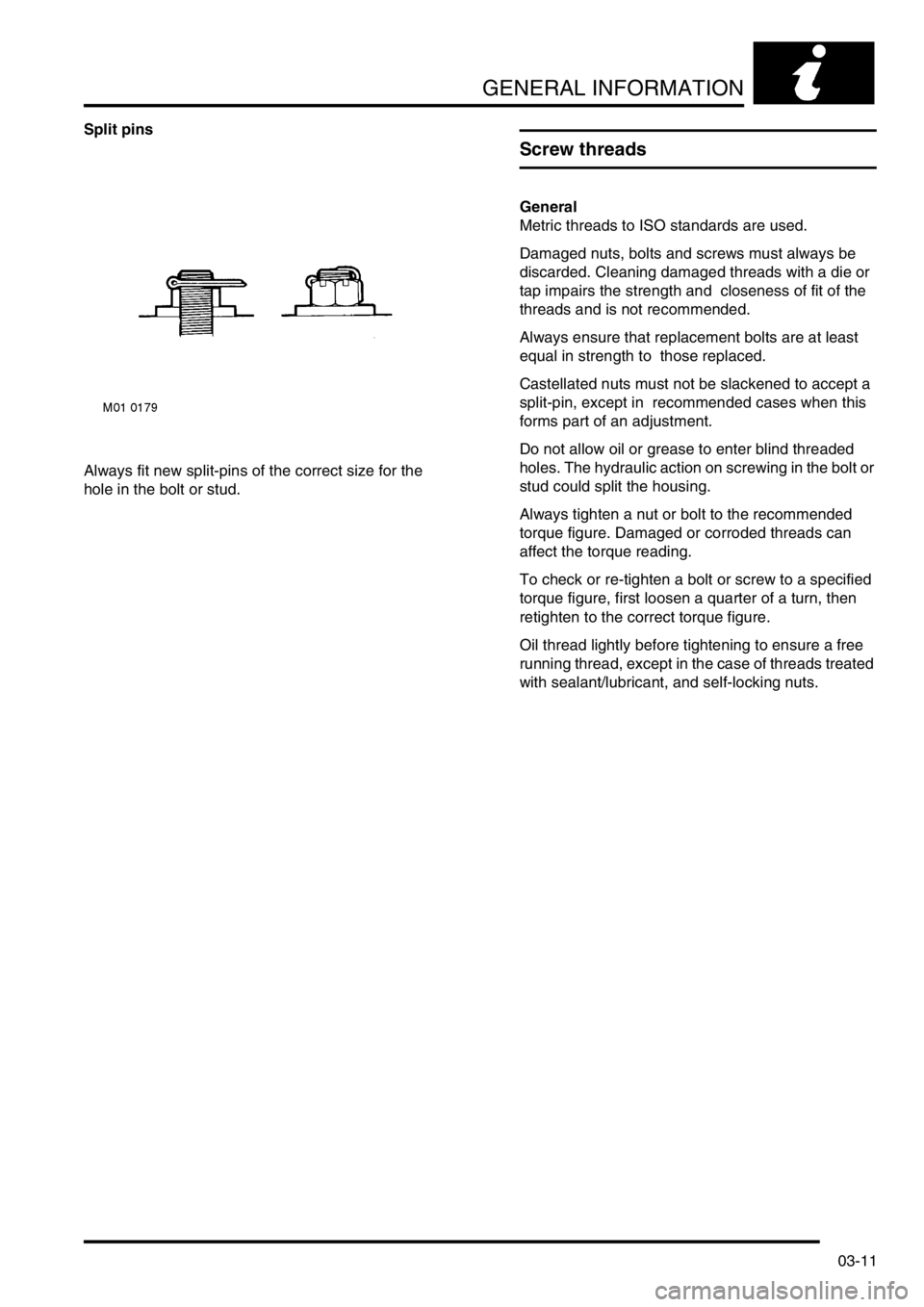
GENERAL INFORMATION
03-11
Split pins
Always fit new split-pins of the correct size for the
hole in the bolt or stud.
Screw threads
General
Metric threads to ISO standards are used.
Damaged nuts, bolts and screws must always be
discarded. Cleaning damaged threads with a die or
tap impairs the strength and closeness of fit of the
threads and is not recommended.
Always ensure that replacement bolts are at least
equal in strength to those replaced.
Castellated nuts must not be slackened to accept a
split-pin, except in recommended cases when this
forms part of an adjustment.
Do not allow oil or grease to enter blind threaded
holes. The hydraulic action on screwing in the bolt or
stud could split the housing.
Always tighten a nut or bolt to the recommended
torque figure. Damaged or corroded threads can
affect the torque reading.
To check or re-tighten a bolt or screw to a specified
torque figure, first loosen a quarter of a turn, then
retighten to the correct torque figure.
Oil thread lightly before tightening to ensure a free
running thread, except in the case of threads treated
with sealant/lubricant, and self-locking nuts.
Page 43 of 1007
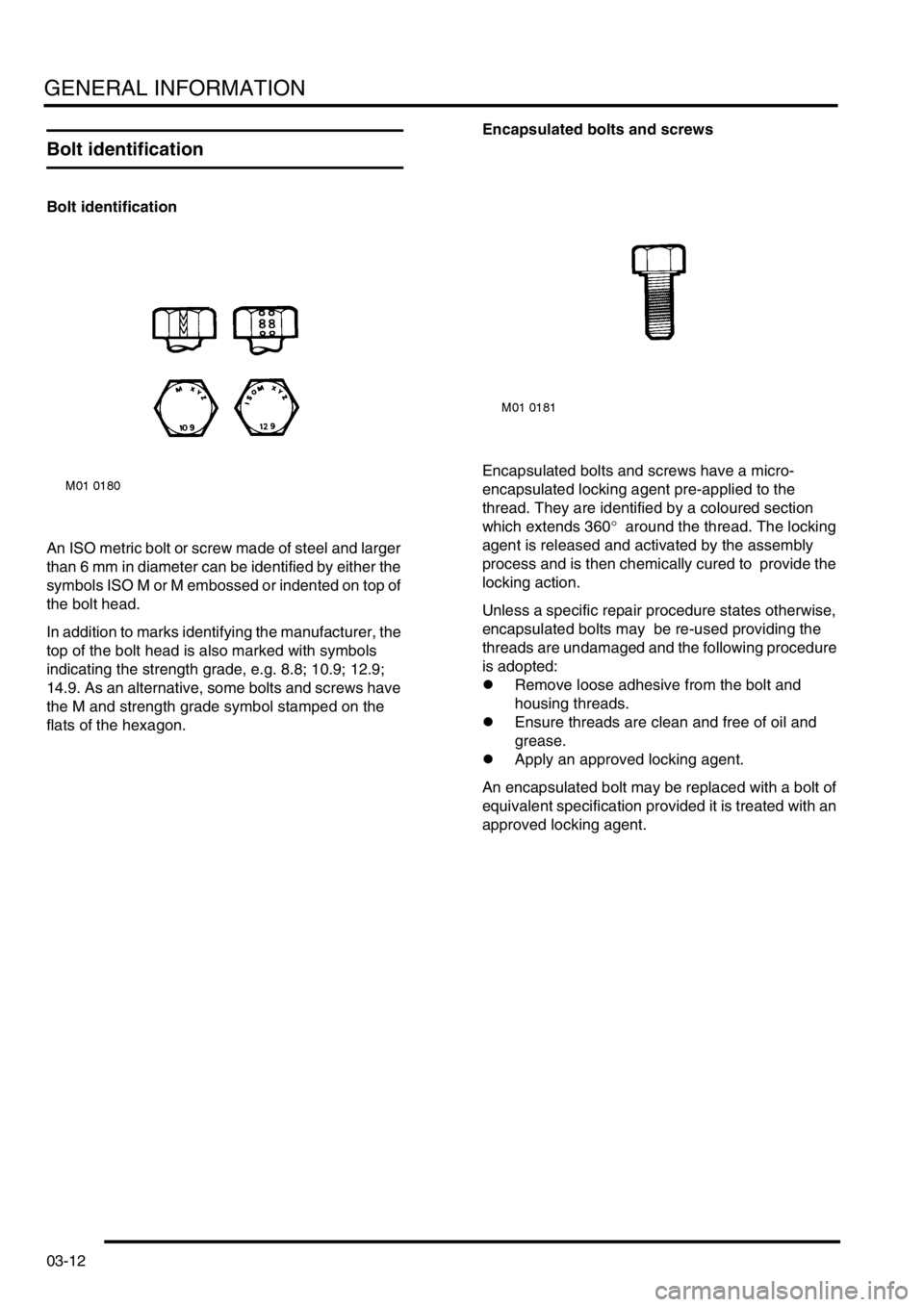
GENERAL INFORMATION
03-12
Bolt identification
Bolt identification
An ISO metric bolt or screw made of steel and larger
than 6 mm in diameter can be identified by either the
symbols ISO M or M embossed or indented on top of
the bolt head.
In addition to marks identifying the manufacturer, the
top of the bolt head is also marked with symbols
indicating the strength grade, e.g. 8.8; 10.9; 12.9;
14.9. As an alternative, some bolts and screws have
the M and strength grade symbol stamped on the
flats of the hexagon.Encapsulated bolts and screws
Encapsulated bolts and screws have a micro-
encapsulated locking agent pre-applied to the
thread. They are identified by a coloured section
which extends 360° around the thread. The locking
agent is released and activated by the assembly
process and is then chemically cured to provide the
locking action.
Unless a specific repair procedure states otherwise,
encapsulated bolts may be re-used providing the
threads are undamaged and the following procedure
is adopted:
lRemove loose adhesive from the bolt and
housing threads.
lEnsure threads are clean and free of oil and
grease.
lApply an approved locking agent.
An encapsulated bolt may be replaced with a bolt of
equivalent specification provided it is treated with an
approved locking agent.
Page 44 of 1007
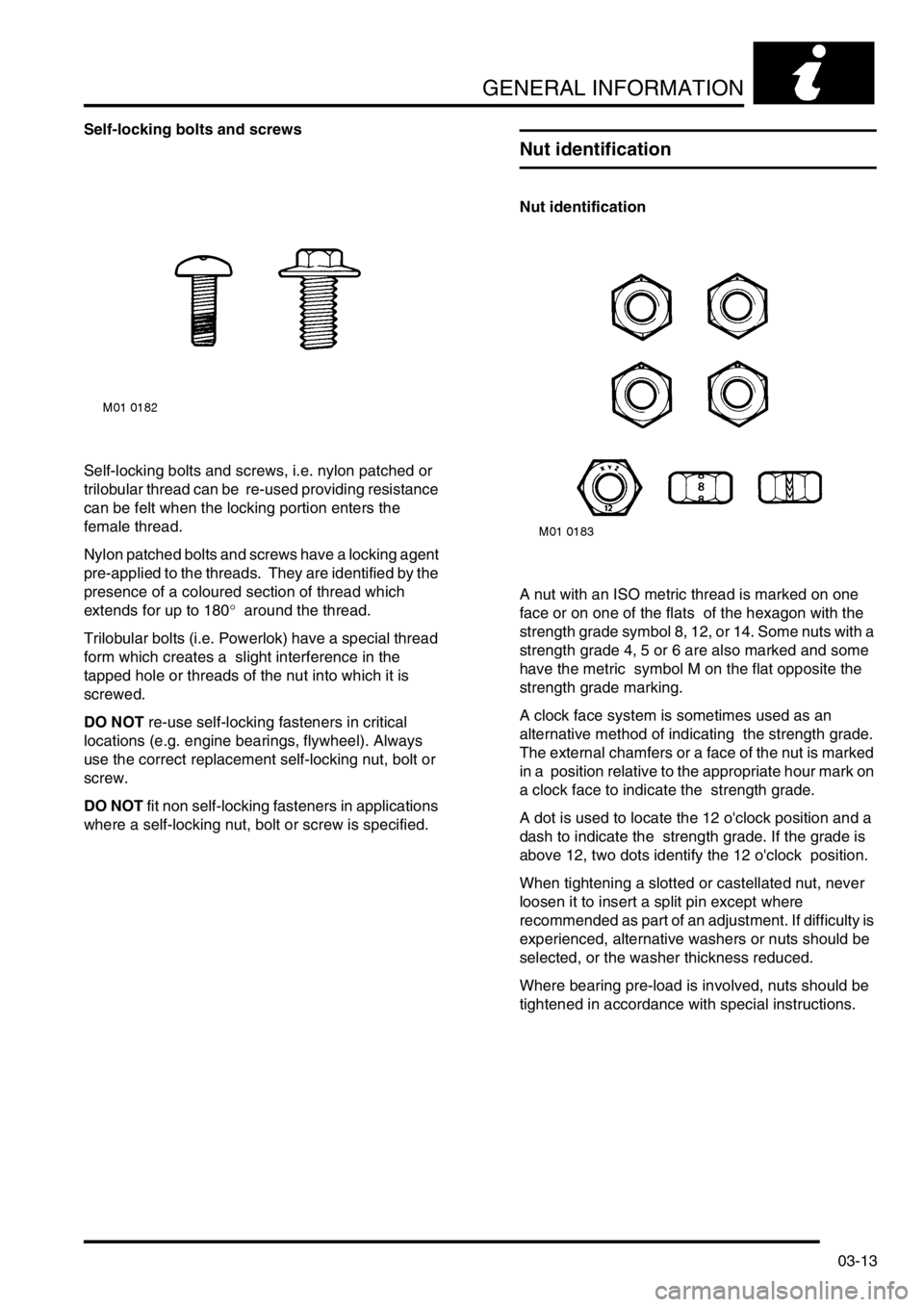
GENERAL INFORMATION
03-13
Self-locking bolts and screws
Self-locking bolts and screws, i.e. nylon patched or
trilobular thread can be re-used providing resistance
can be felt when the locking portion enters the
female thread.
Nylon patched bolts and screws have a locking agent
pre-applied to the threads. They are identified by the
presence of a coloured section of thread which
extends for up to 180° around the thread.
Trilobular bolts (i.e. Powerlok) have a special thread
form which creates a slight interference in the
tapped hole or threads of the nut into which it is
screwed.
DO NOT re-use self-locking fasteners in critical
locations (e.g. engine bearings, flywheel). Always
use the correct replacement self-locking nut, bolt or
screw.
DO NOT fit non self-locking fasteners in applications
where a self-locking nut, bolt or screw is specified.
Nut identification
Nut identification
A nut with an ISO metric thread is marked on one
face or on one of the flats of the hexagon with the
strength grade symbol 8, 12, or 14. Some nuts with a
strength grade 4, 5 or 6 are also marked and some
have the metric symbol M on the flat opposite the
strength grade marking.
A clock face system is sometimes used as an
alternative method of indicating the strength grade.
The external chamfers or a face of the nut is marked
in a position relative to the appropriate hour mark on
a clock face to indicate the strength grade.
A dot is used to locate the 12 o'clock position and a
dash to indicate the strength grade. If the grade is
above 12, two dots identify the 12 o'clock position.
When tightening a slotted or castellated nut, never
loosen it to insert a split pin except where
recommended as part of an adjustment. If difficulty is
experienced, alternative washers or nuts should be
selected, or the washer thickness reduced.
Where bearing pre-load is involved, nuts should be
tightened in accordance with special instructions.
Page 45 of 1007
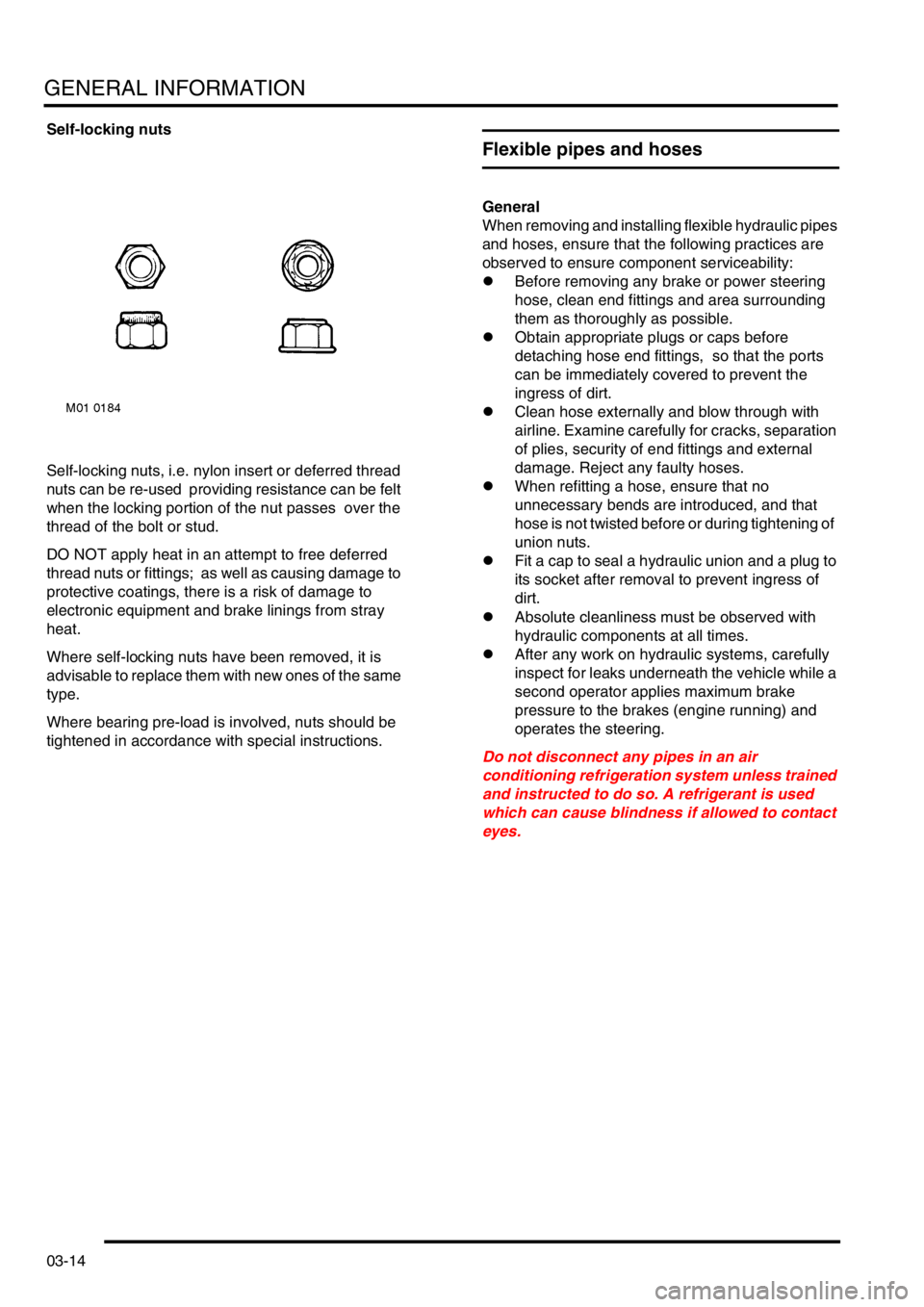
GENERAL INFORMATION
03-14
Self-locking nuts
Self-locking nuts, i.e. nylon insert or deferred thread
nuts can be re-used providing resistance can be felt
when the locking portion of the nut passes over the
thread of the bolt or stud.
DO NOT apply heat in an attempt to free deferred
thread nuts or fittings; as well as causing damage to
protective coatings, there is a risk of damage to
electronic equipment and brake linings from stray
heat.
Where self-locking nuts have been removed, it is
advisable to replace them with new ones of the same
type.
Where bearing pre-load is involved, nuts should be
tightened in accordance with special instructions.
Flexible pipes and hoses
General
When removing and installing flexible hydraulic pipes
and hoses, ensure that the following practices are
observed to ensure component serviceability:
lBefore removing any brake or power steering
hose, clean end fittings and area surrounding
them as thoroughly as possible.
lObtain appropriate plugs or caps before
detaching hose end fittings, so that the ports
can be immediately covered to prevent the
ingress of dirt.
lClean hose externally and blow through with
airline. Examine carefully for cracks, separation
of plies, security of end fittings and external
damage. Reject any faulty hoses.
lWhen refitting a hose, ensure that no
unnecessary bends are introduced, and that
hose is not twisted before or during tightening of
union nuts.
lFit a cap to seal a hydraulic union and a plug to
its socket after removal to prevent ingress of
dirt.
lAbsolute cleanliness must be observed with
hydraulic components at all times.
lAfter any work on hydraulic systems, carefully
inspect for leaks underneath the vehicle while a
second operator applies maximum brake
pressure to the brakes (engine running) and
operates the steering.
Do not disconnect any pipes in an air
conditioning refrigeration system unless trained
and instructed to do so. A refrigerant is used
which can cause blindness if allowed to contact
eyes.
Page 46 of 1007
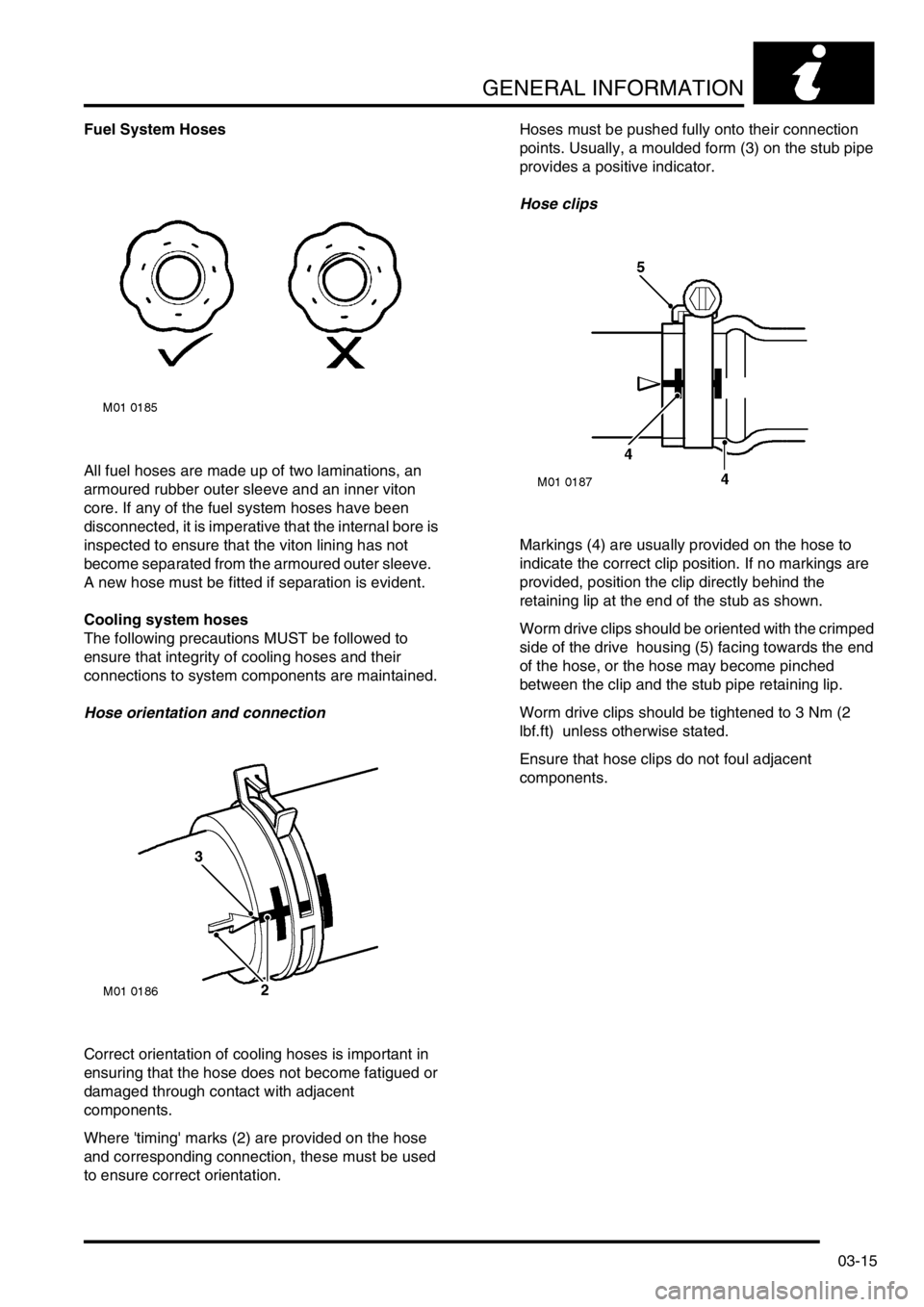
GENERAL INFORMATION
03-15
Fuel System Hoses
All fuel hoses are made up of two laminations, an
armoured rubber outer sleeve and an inner viton
core. If any of the fuel system hoses have been
disconnected, it is imperative that the internal bore is
inspected to ensure that the viton lining has not
become separated from the armoured outer sleeve.
A new hose must be fitted if separation is evident.
Cooling system hoses
The following precautions MUST be followed to
ensure that integrity of cooling hoses and their
connections to system components are maintained.
Hose orientation and connection
Correct orientation of cooling hoses is important in
ensuring that the hose does not become fatigued or
damaged through contact with adjacent
components.
Where 'timing' marks (2) are provided on the hose
and corresponding connection, these must be used
to ensure correct orientation.Hoses must be pushed fully onto their connection
points. Usually, a moulded form (3) on the stub pipe
provides a positive indicator.
Hose clips
Markings (4) are usually provided on the hose to
indicate the correct clip position. If no markings are
provided, position the clip directly behind the
retaining lip at the end of the stub as shown.
Worm drive clips should be oriented with the crimped
side of the drive housing (5) facing towards the end
of the hose, or the hose may become pinched
between the clip and the stub pipe retaining lip.
Worm drive clips should be tightened to 3 Nm (2
lbf.ft) unless otherwise stated.
Ensure that hose clips do not foul adjacent
components.
Page 47 of 1007
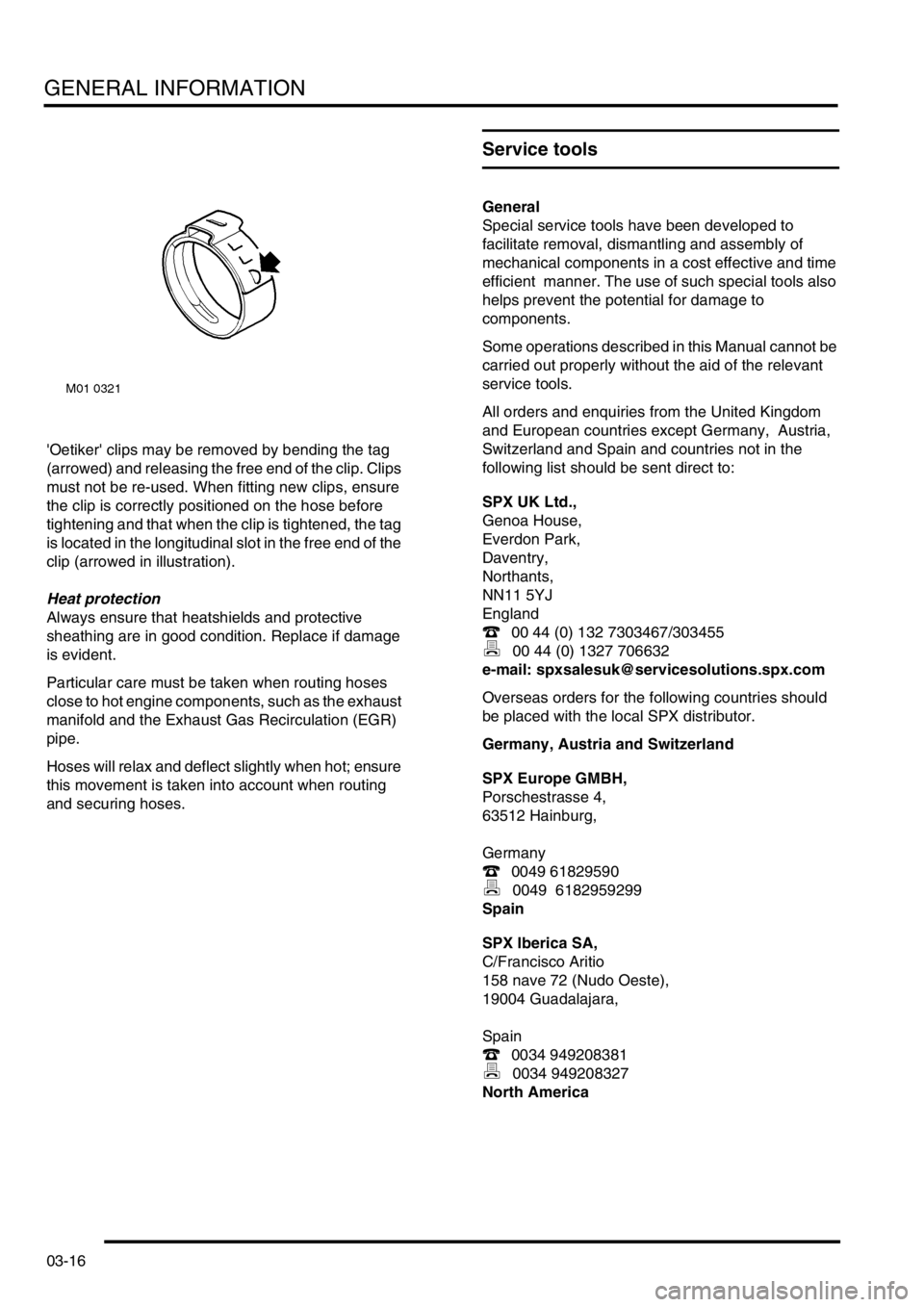
GENERAL INFORMATION
03-16
'Oetiker' clips may be removed by bending the tag
(arrowed) and releasing the free end of the clip. Clips
must not be re-used. When fitting new clips, ensure
the clip is correctly positioned on the hose before
tightening and that when the clip is tightened, the tag
is located in the longitudinal slot in the free end of the
clip (arrowed in illustration).
Heat protection
Always ensure that heatshields and protective
sheathing are in good condition. Replace if damage
is evident.
Particular care must be taken when routing hoses
close to hot engine components, such as the exhaust
manifold and the Exhaust Gas Recirculation (EGR)
pipe.
Hoses will relax and deflect slightly when hot; ensure
this movement is taken into account when routing
and securing hoses.
Service tools
General
Special service tools have been developed to
facilitate removal, dismantling and assembly of
mechanical components in a cost effective and time
efficient manner. The use of such special tools also
helps prevent the potential for damage to
components.
Some operations described in this Manual cannot be
carried out properly without the aid of the relevant
service tools.
All orders and enquiries from the United Kingdom
and European countries except Germany, Austria,
Switzerland and Spain and countries not in the
following list should be sent direct to:
SPX UK Ltd.,
Genoa House,
Everdon Park,
Daventry,
Northants,
NN11 5YJ
England
( 00 44 (0) 132 7303467/303455
) 00 44 (0) 1327 706632
e-mail: [email protected]
Overseas orders for the following countries should
be placed with the local SPX distributor.
Germany, Austria and Switzerland
SPX Europe GMBH,
Porschestrasse 4,
63512 Hainburg,
Germany
( 0049 61829590
) 0049 6182959299
Spain
SPX Iberica SA,
C/Francisco Aritio
158 nave 72 (Nudo Oeste),
19004 Guadalajara,
Spain
( 0034 949208381
) 0034 949208327
North America
Page 48 of 1007
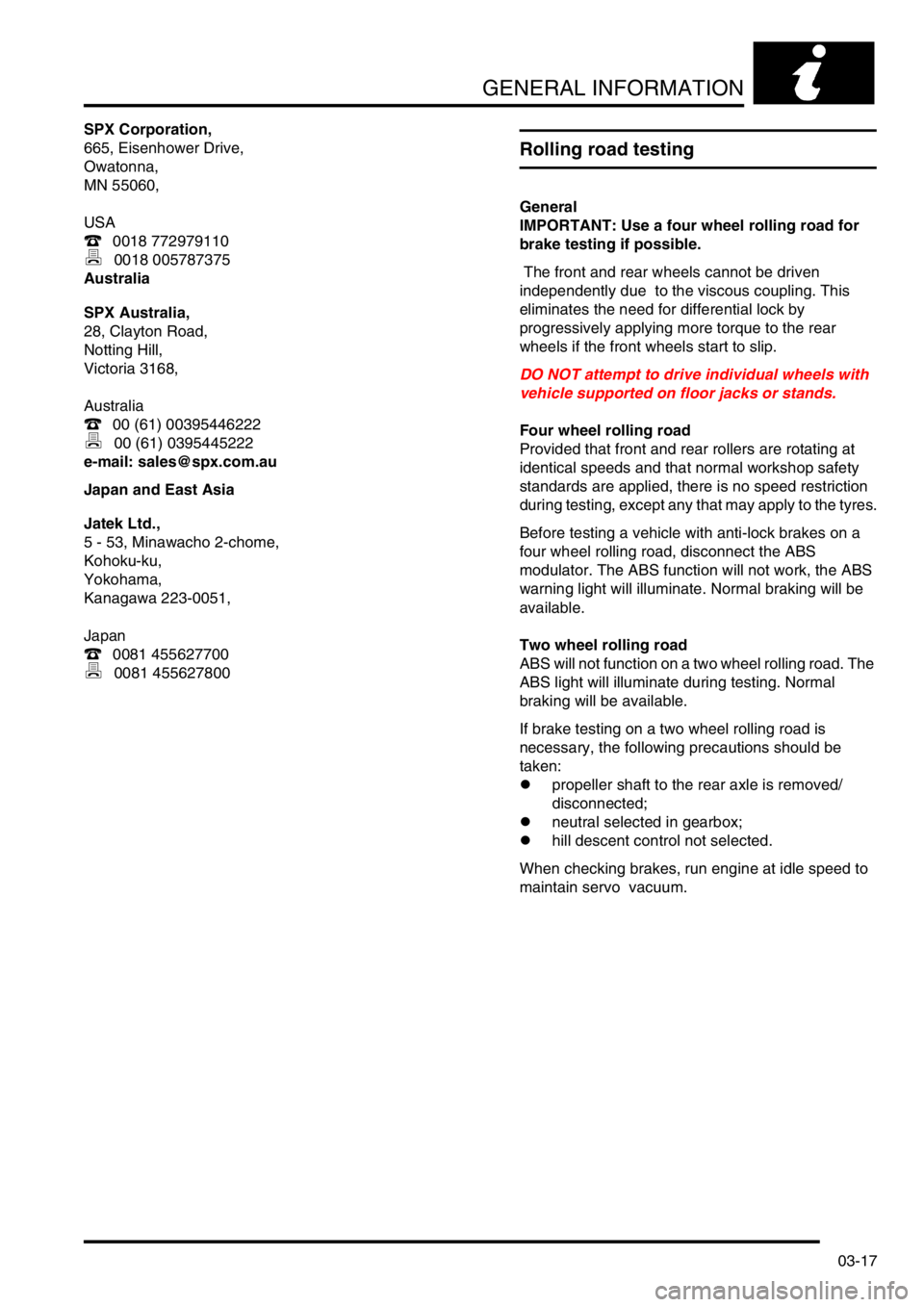
GENERAL INFORMATION
03-17
SPX Corporation,
665, Eisenhower Drive,
Owatonna,
MN 55060,
USA
( 0018 772979110
) 0018 005787375
Australia
SPX Australia,
28, Clayton Road,
Notting Hill,
Victoria 3168,
Australia
( 00 (61) 00395446222
) 00 (61) 0395445222
e-mail: [email protected]
Japan and East Asia
Jatek Ltd.,
5 - 53, Minawacho 2-chome,
Kohoku-ku,
Yokohama,
Kanagawa 223-0051,
Japan
( 0081 455627700
) 0081 455627800
Rolling road testing
General
IMPORTANT: Use a four wheel rolling road for
brake testing if possible.
The front and rear wheels cannot be driven
independently due to the viscous coupling. This
eliminates the need for differential lock by
progressively applying more torque to the rear
wheels if the front wheels start to slip.
DO NOT attempt to drive individual wheels with
vehicle supported on floor jacks or stands.
Four wheel rolling road
Provided that front and rear rollers are rotating at
identical speeds and that normal workshop safety
standards are applied, there is no speed restriction
during testing, except any that may apply to the tyres.
Before testing a vehicle with anti-lock brakes on a
four wheel rolling road, disconnect the ABS
modulator. The ABS function will not work, the ABS
warning light will illuminate. Normal braking will be
available.
Two wheel rolling road
ABS will not function on a two wheel rolling road. The
ABS light will illuminate during testing. Normal
braking will be available.
If brake testing on a two wheel rolling road is
necessary, the following precautions should be
taken:
lpropeller shaft to the rear axle is removed/
disconnected;
lneutral selected in gearbox;
lhill descent control not selected.
When checking brakes, run engine at idle speed to
maintain servo vacuum.