Page 729 of 1007
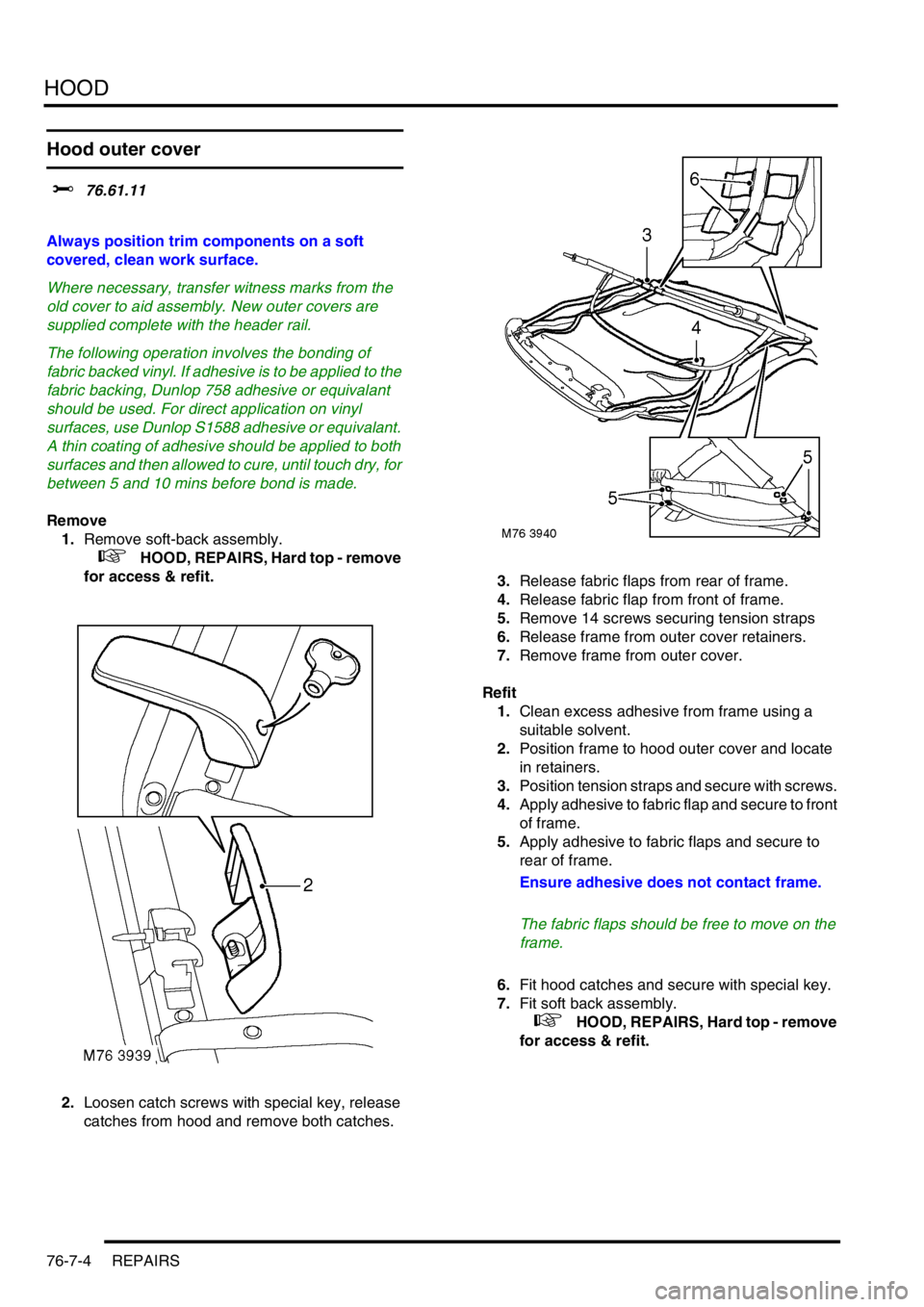
HOOD
76-7-4 REPAIRS
Hood outer cover
$% 76.61.11
Always position trim components on a soft
covered, clean work surface.
Where necessary, transfer witness marks from the
old cover to aid assembly. New outer covers are
supplied complete with the header rail.
The following operation involves the bonding of
fabric backed vinyl. If adhesive is to be applied to the
fabric backing, Dunlop 758 adhesive or equivalant
should be used. For direct application on vinyl
surfaces, use Dunlop S1588 adhesive or equivalant.
A thin coating of adhesive should be applied to both
surfaces and then allowed to cure, until touch dry, for
between 5 and 10 mins before bond is made.
Remove
1.Remove soft-back assembly.
+ HOOD, REPAIRS, Hard top - remove
for access & refit.
2.Loosen catch screws with special key, release
catches from hood and remove both catches. 3.Release fabric flaps from rear of frame.
4.Release fabric flap from front of frame.
5.Remove 14 screws securing tension straps
6.Release frame from outer cover retainers.
7.Remove frame from outer cover.
Refit
1.Clean excess adhesive from frame using a
suitable solvent.
2.Position frame to hood outer cover and locate
in retainers.
3.Position tension straps and secure with screws.
4.Apply adhesive to fabric flap and secure to front
of frame.
5.Apply adhesive to fabric flaps and secure to
rear of frame.
Ensure adhesive does not contact frame.
The fabric flaps should be free to move on the
frame.
6.Fit hood catches and secure with special key.
7.Fit soft back assembly.
+ HOOD, REPAIRS, Hard top - remove
for access & refit.
Page 730 of 1007
HOOD
REPAIRS 76-7-5
Glass - body side - hard back
$% 76.61.29
Always position trim components on a soft
covered, clean work surface.
Wear protective gloves when handling glass,
solvents and primers.
Wear suitable eye protection when removing and
refitting glass.
The following equipment is required: ```Cutting wire
and handles ```Sharp knife ```Windscreen repair kit
```Sealer applicator gun ```Suction cups
Remove
1.Remove hard-back.
+ HOOD, REPAIRS, Frame & hood
cover - assembly - remove for access & refit.
2.Remove 2 screws securing 'E' post finisher,
release finisher from clips and remove finisher.3.Remove 4 Torx screws securing hard-back
catches, slide catches from position and
remove catches.
4.Remove 3 Torx screws securing headlining
release headlining from hard-back seal and
remove headlining.
5.Cover interior of hard-back with protective
sheet.
6.Apply masking tape to protect paintwork.
Page 731 of 1007
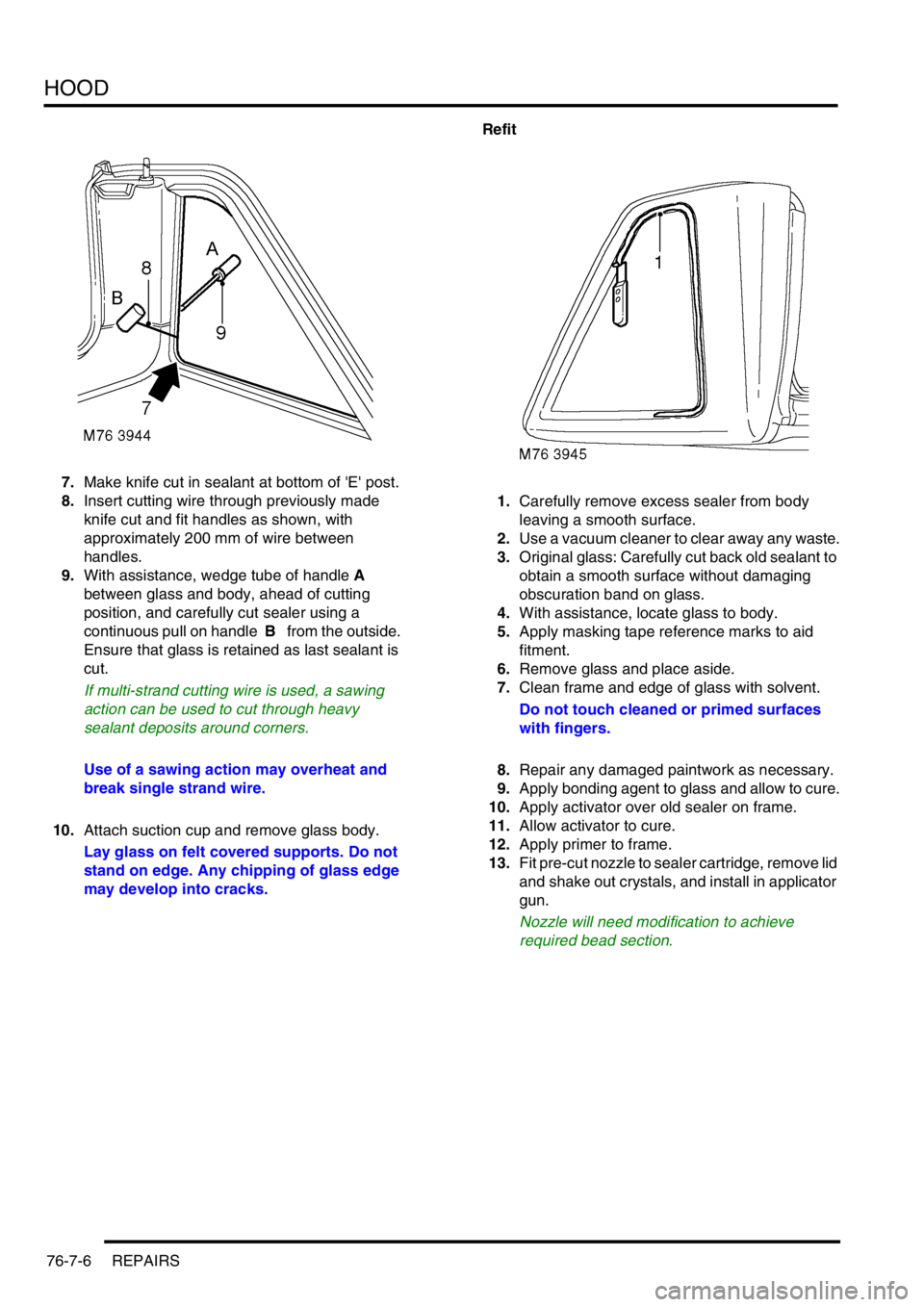
HOOD
76-7-6 REPAIRS
7.Make knife cut in sealant at bottom of 'E' post.
8.Insert cutting wire through previously made
knife cut and fit handles as shown, with
approximately 200 mm of wire between
handles.
9.With assistance, wedge tube of handle A
between glass and body, ahead of cutting
position, and carefully cut sealer using a
continuous pull on handle B from the outside.
Ensure that glass is retained as last sealant is
cut.
If multi-strand cutting wire is used, a sawing
action can be used to cut through heavy
sealant deposits around corners.
Use of a sawing action may overheat and
break single strand wire.
10.Attach suction cup and remove glass body.
Lay glass on felt covered supports. Do not
stand on edge. Any chipping of glass edge
may develop into cracks. Refit
1.Carefully remove excess sealer from body
leaving a smooth surface.
2.Use a vacuum cleaner to clear away any waste.
3.Original glass: Carefully cut back old sealant to
obtain a smooth surface without damaging
obscuration band on glass.
4.With assistance, locate glass to body.
5.Apply masking tape reference marks to aid
fitment.
6.Remove glass and place aside.
7.Clean frame and edge of glass with solvent.
Do not touch cleaned or primed surfaces
with fingers.
8.Repair any damaged paintwork as necessary.
9.Apply bonding agent to glass and allow to cure.
10.Apply activator over old sealer on frame.
11.Allow activator to cure.
12.Apply primer to frame.
13.Fit pre-cut nozzle to sealer cartridge, remove lid
and shake out crystals, and install in applicator
gun.
Nozzle will need modification to achieve
required bead section.
Page 732 of 1007
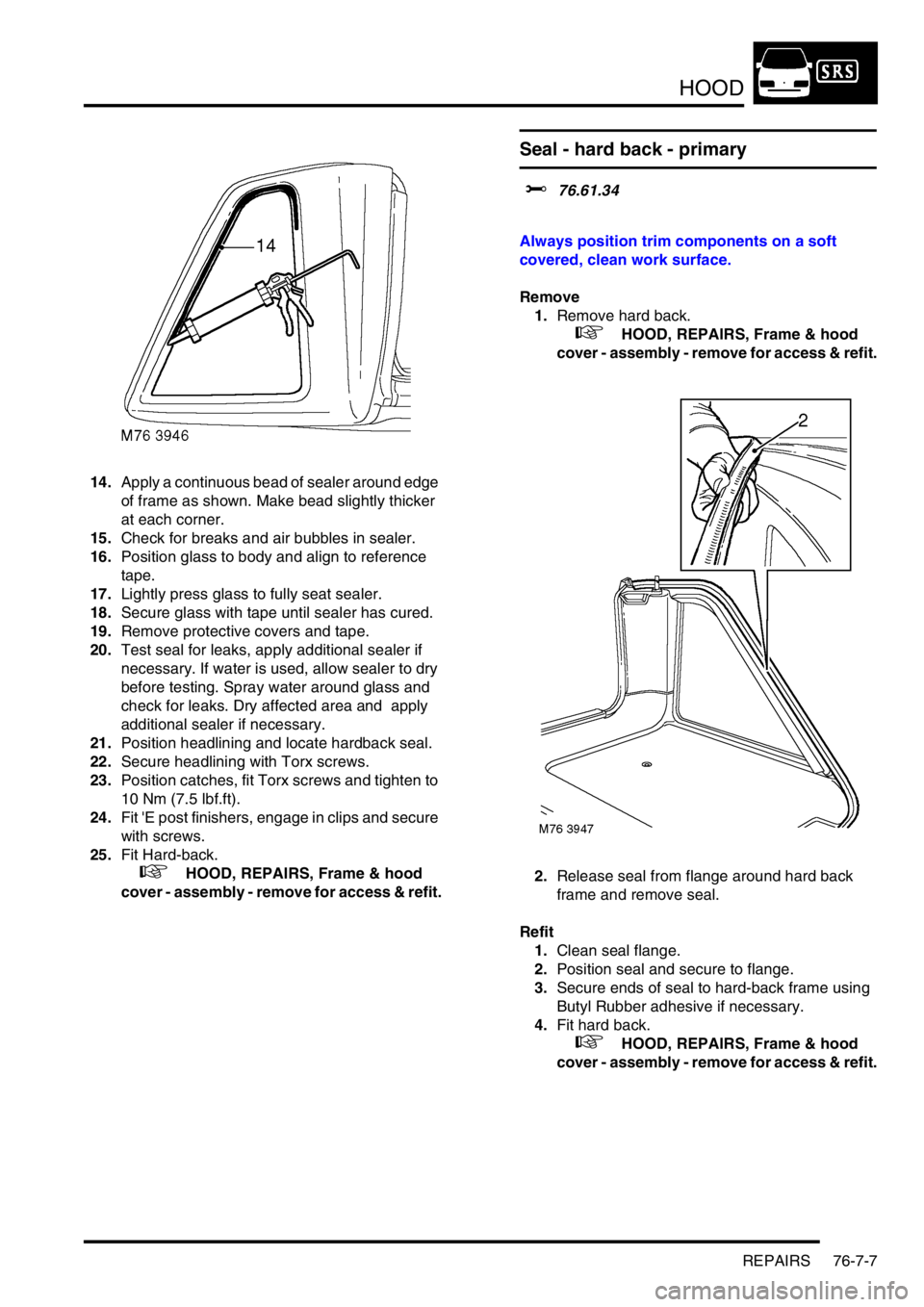
HOOD
REPAIRS 76-7-7
14.Apply a continuous bead of sealer around edge
of frame as shown. Make bead slightly thicker
at each corner.
15.Check for breaks and air bubbles in sealer.
16.Position glass to body and align to reference
tape.
17.Lightly press glass to fully seat sealer.
18.Secure glass with tape until sealer has cured.
19.Remove protective covers and tape.
20.Test seal for leaks, apply additional sealer if
necessary. If water is used, allow sealer to dry
before testing. Spray water around glass and
check for leaks. Dry affected area and apply
additional sealer if necessary.
21.Position headlining and locate hardback seal.
22.Secure headlining with Torx screws.
23.Position catches, fit Torx screws and tighten to
10 Nm (7.5 lbf.ft).
24.Fit 'E post finishers, engage in clips and secure
with screws.
25.Fit Hard-back.
+ HOOD, REPAIRS, Frame & hood
cover - assembly - remove for access & refit.
Seal - hard back - primary
$% 76.61.34
Always position trim components on a soft
covered, clean work surface.
Remove
1.Remove hard back.
+ HOOD, REPAIRS, Frame & hood
cover - assembly - remove for access & refit.
2.Release seal from flange around hard back
frame and remove seal.
Refit
1.Clean seal flange.
2.Position seal and secure to flange.
3.Secure ends of seal to hard-back frame using
Butyl Rubber adhesive if necessary.
4.Fit hard back.
+ HOOD, REPAIRS, Frame & hood
cover - assembly - remove for access & refit.
Page 733 of 1007
HOOD
76-7-8 REPAIRS
Catch and retainer - hard-back - front
$% 76.61.94
Remove
1.Remove hard-back.
+ HOOD, REPAIRS, Frame & hood
cover - assembly - remove for access & refit.
2.Remove 2 Torx screws securing catch, slide
catch from position and remove catch. 3.Remove Torx screw securing roof finisher to
hard-back retainer.
4.Remove 3 Torx screws securing hard-back
retainer and remove retainer.
Refit
1.Position hard-back retainer, fit Torx screws
and tighten to 10Nm (7.5 lbf.ft).
2.Fit Torx screw securing roof finisher.
3.Position catch, fit Torx screws and tighten to 10
Nm (7.5 lbf.ft).
Ensure formed washer is correctly located
in catch recess.
4.Fit hard-back.
+ HOOD, REPAIRS, Frame & hood
cover - assembly - remove for access & refit.
Page 734 of 1007
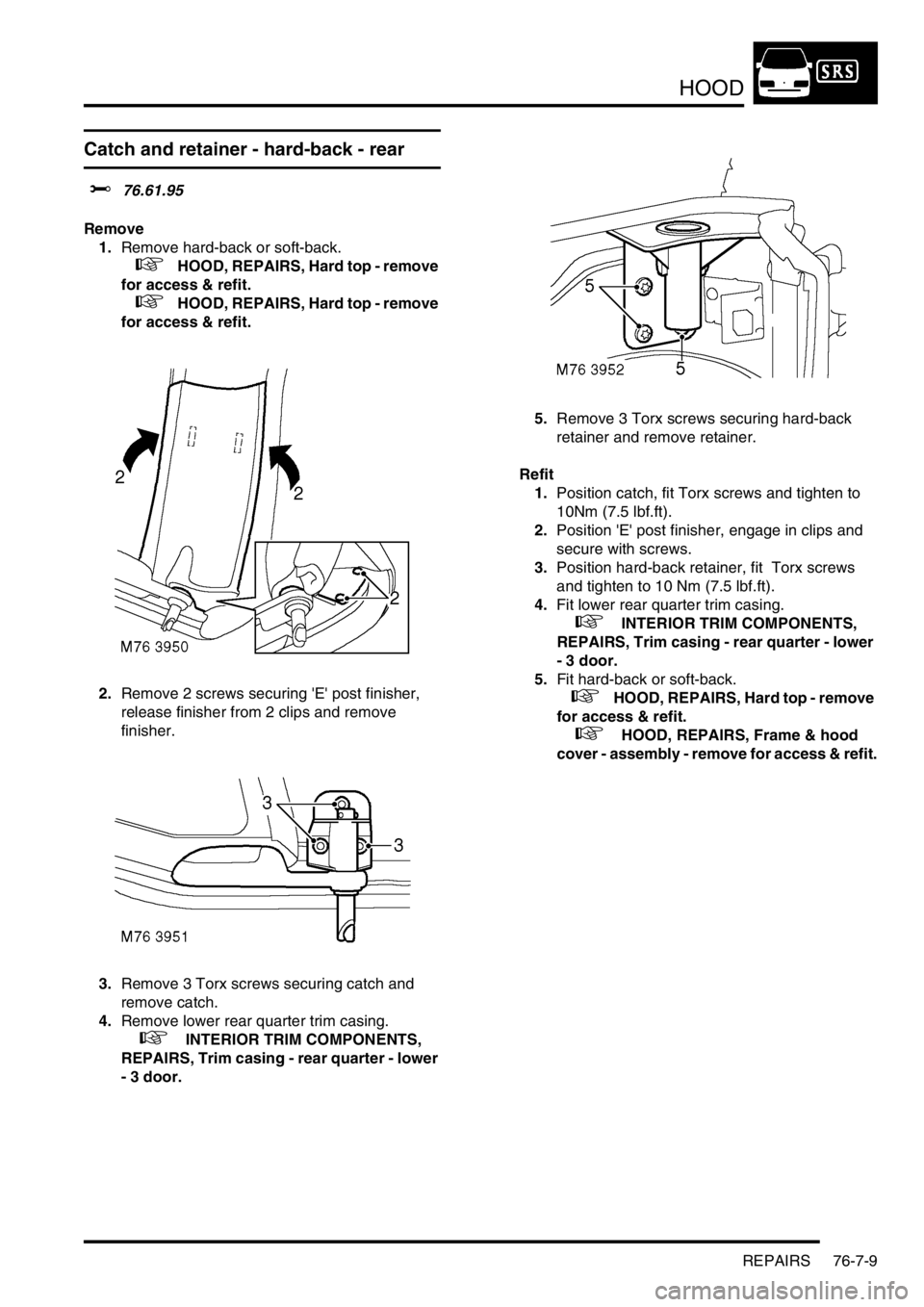
HOOD
REPAIRS 76-7-9
Catch and retainer - hard-back - rear
$% 76.61.95
Remove
1.Remove hard-back or soft-back.
+ HOOD, REPAIRS, Hard top - remove
for access & refit.
+ HOOD, REPAIRS, Hard top - remove
for access & refit.
2.Remove 2 screws securing 'E' post finisher,
release finisher from 2 clips and remove
finisher.
3.Remove 3 Torx screws securing catch and
remove catch.
4.Remove lower rear quarter trim casing.
+ INTERIOR TRIM COMPONENTS,
REPAIRS, Trim casing - rear quarter - lower
- 3 door.5.Remove 3 Torx screws securing hard-back
retainer and remove retainer.
Refit
1.Position catch, fit Torx screws and tighten to
10Nm (7.5 lbf.ft).
2.Position 'E' post finisher, engage in clips and
secure with screws.
3.Position hard-back retainer, fit Torx screws
and tighten to 10 Nm (7.5 lbf.ft).
4.Fit lower rear quarter trim casing.
+ INTERIOR TRIM COMPONENTS,
REPAIRS, Trim casing - rear quarter - lower
- 3 door.
5.Fit hard-back or soft-back.
+ HOOD, REPAIRS, Hard top - remove
for access & refit.
+ HOOD, REPAIRS, Frame & hood
cover - assembly - remove for access & refit.
Page 735 of 1007
Page 736 of 1007
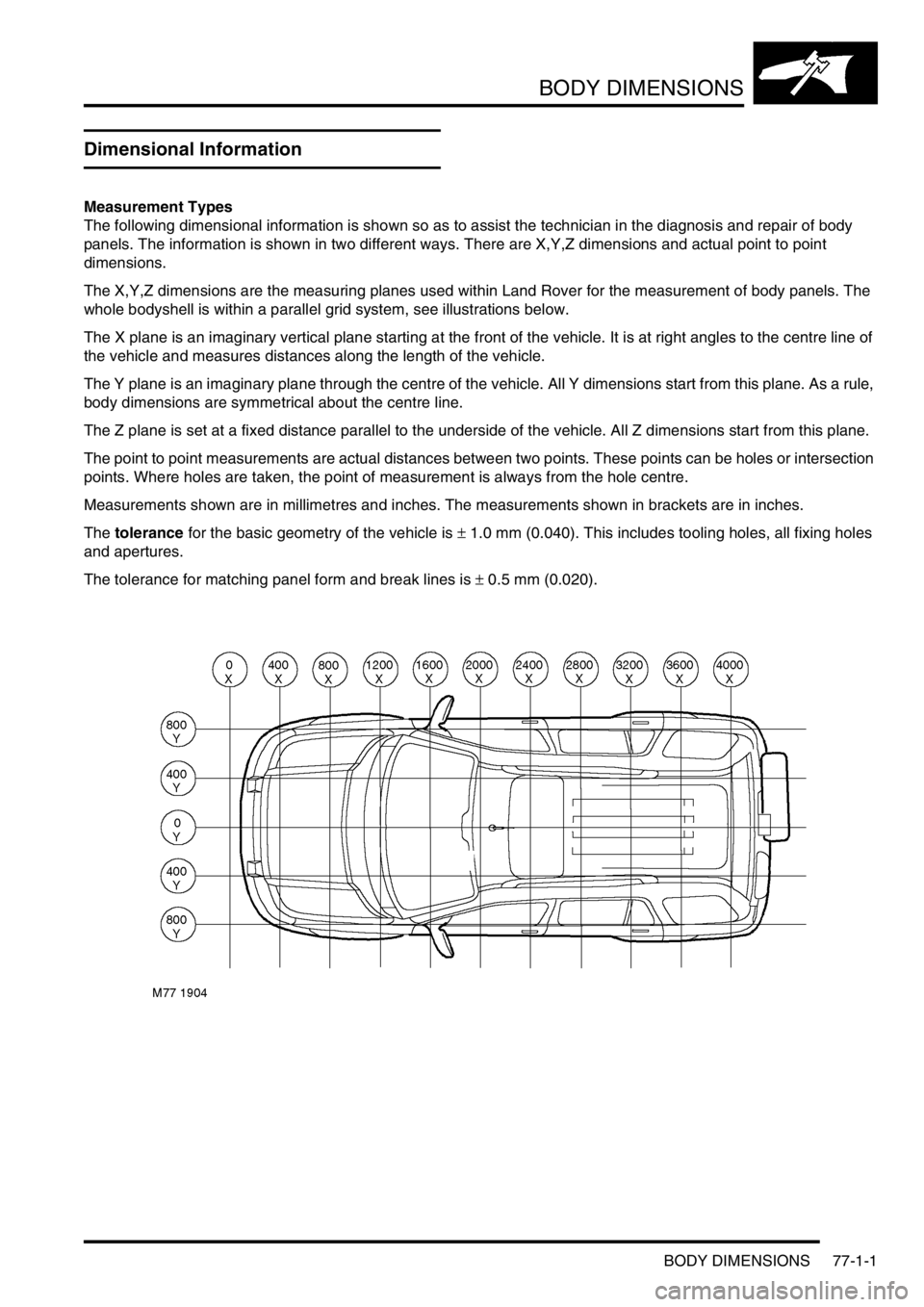
BODY DIMENSIONS
BODY DIMENSIONS 77-1-1
BODY DIMENSIONS BODY DIMENSIONS
Dimensional Information
Measurement Types
The following dimensional information is shown so as to assist the technician in the diagnosis and repair of body
panels. The information is shown in two different ways. There are X,Y,Z dimensions and actual point to point
dimensions.
The X,Y,Z dimensions are the measuring planes used within Land Rover for the measurement of body panels. The
whole bodyshell is within a parallel grid system, see illustrations below.
The X plane is an imaginary vertical plane starting at the front of the vehicle. It is at right angles to the centre line of
the vehicle and measures distances along the length of the vehicle.
The Y plane is an imaginary plane through the centre of the vehicle. All Y dimensions start from this plane. As a rule,
body dimensions are symmetrical about the centre line.
The Z plane is set at a fixed distance parallel to the underside of the vehicle. All Z dimensions start from this plane.
The point to point measurements are actual distances between two points. These points can be holes or intersection
points. Where holes are taken, the point of measurement is always from the hole centre.
Measurements shown are in millimetres and inches. The measurements shown in brackets are in inches.
The tolerance for the basic geometry of the vehicle is ± 1.0 mm (0.040). This includes tooling holes, all fixing holes
and apertures.
The tolerance for matching panel form and break lines is ± 0.5 mm (0.020).