Page 57 of 1007
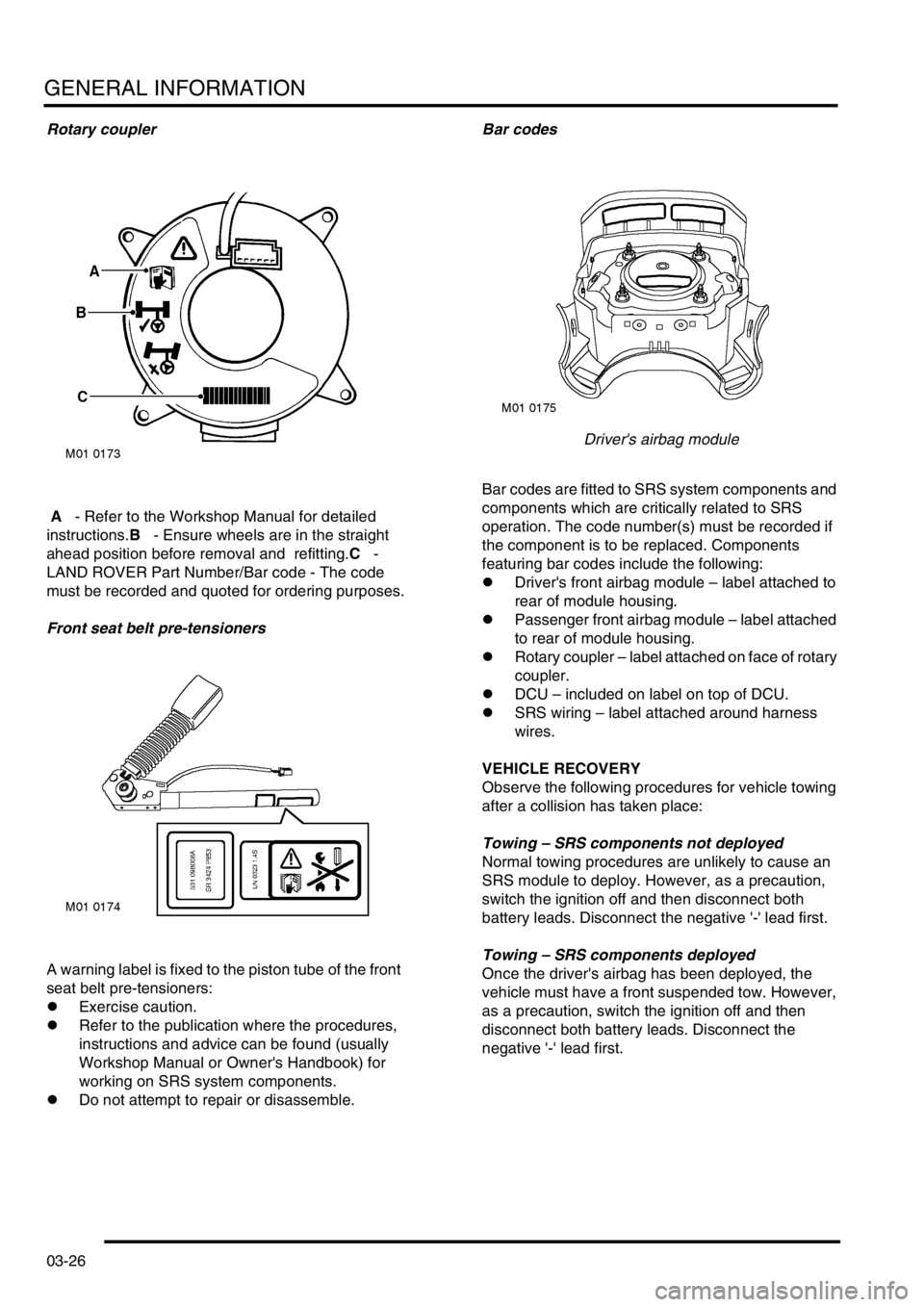
GENERAL INFORMATION
03-26
Rotary coupler
A - Refer to the Workshop Manual for detailed
instructions.B - Ensure wheels are in the straight
ahead position before removal and refitting.C -
LAND ROVER Part Number/Bar code - The code
must be recorded and quoted for ordering purposes.
Front seat belt pre-tensioners
A warning label is fixed to the piston tube of the front
seat belt pre-tensioners:
lExercise caution.
lRefer to the publication where the procedures,
instructions and advice can be found (usually
Workshop Manual or Owner's Handbook) for
working on SRS system components.
lDo not attempt to repair or disassemble.Bar codes
Driver's airbag module
Bar codes are fitted to SRS system components and
components which are critically related to SRS
operation. The code number(s) must be recorded if
the component is to be replaced. Components
featuring bar codes include the following:
lDriver's front airbag module – label attached to
rear of module housing.
lPassenger front airbag module – label attached
to rear of module housing.
lRotary coupler – label attached on face of rotary
coupler.
lDCU – included on label on top of DCU.
lSRS wiring – label attached around harness
wires.
VEHICLE RECOVERY
Observe the following procedures for vehicle towing
after a collision has taken place:
Towing – SRS components not deployed
Normal towing procedures are unlikely to cause an
SRS module to deploy. However, as a precaution,
switch the ignition off and then disconnect both
battery leads. Disconnect the negative '-' lead first.
Towing – SRS components deployed
Once the driver's airbag has been deployed, the
vehicle must have a front suspended tow. However,
as a precaution, switch the ignition off and then
disconnect both battery leads. Disconnect the
negative '-' lead first.
Page 58 of 1007
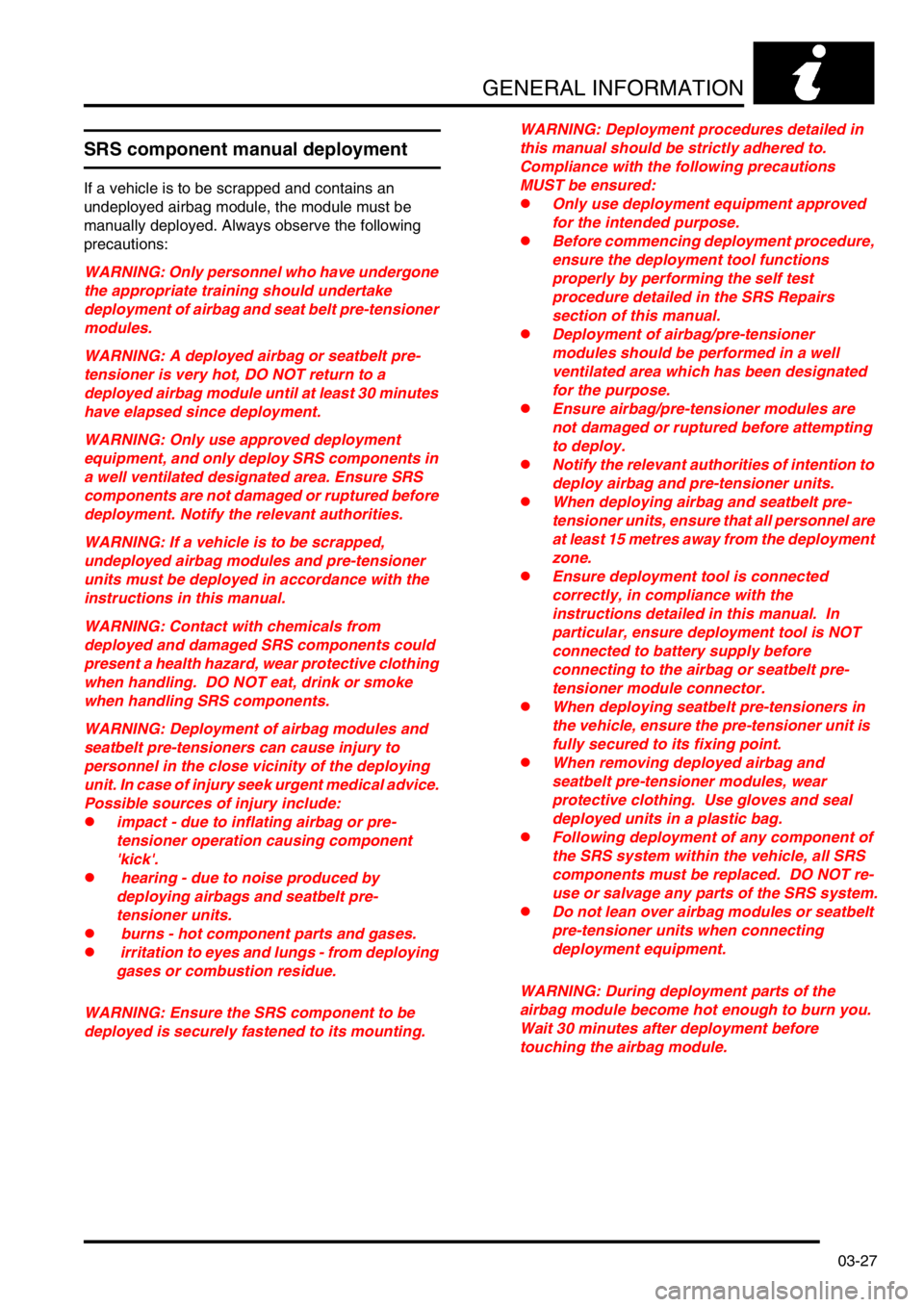
GENERAL INFORMATION
03-27
SRS component manual deployment
If a vehicle is to be scrapped and contains an
undeployed airbag module, the module must be
manually deployed. Always observe the following
precautions:
WARNING: Only personnel who have undergone
the appropriate training should undertake
deployment of airbag and seat belt pre-tensioner
modules.
WARNING: A deployed airbag or seatbelt pre-
tensioner is very hot, DO NOT return to a
deployed airbag module until at least 30 minutes
have elapsed since deployment.
WARNING: Only use approved deployment
equipment, and only deploy SRS components in
a well ventilated designated area. Ensure SRS
components are not damaged or ruptured before
deployment. Notify the relevant authorities.
WARNING: If a vehicle is to be scrapped,
undeployed airbag modules and pre-tensioner
units must be deployed in accordance with the
instructions in this manual.
WARNING: Contact with chemicals from
deployed and damaged SRS components could
present a health hazard, wear protective clothing
when handling. DO NOT eat, drink or smoke
when handling SRS components.
WARNING: Deployment of airbag modules and
seatbelt pre-tensioners can cause injury to
personnel in the close vicinity of the deploying
unit. In case of injury seek urgent medical advice.
Possible sources of injury include:
limpact - due to inflating airbag or pre-
tensioner operation causing component
'kick'.
l hearing - due to noise produced by
deploying airbags and seatbelt pre-
tensioner units.
l burns - hot component parts and gases.
l irritation to eyes and lungs - from deploying
gases or combustion residue.
WARNING: Ensure the SRS component to be
deployed is securely fastened to its mounting.WARNING: Deployment procedures detailed in
this manual should be strictly adhered to.
Compliance with the following precautions
MUST be ensured:
lOnly use deployment equipment approved
for the intended purpose.
lBefore commencing deployment procedure,
ensure the deployment tool functions
properly by performing the self test
procedure detailed in the SRS Repairs
section of this manual.
lDeployment of airbag/pre-tensioner
modules should be performed in a well
ventilated area which has been designated
for the purpose.
lEnsure airbag/pre-tensioner modules are
not damaged or ruptured before attempting
to deploy.
lNotify the relevant authorities of intention to
deploy airbag and pre-tensioner units.
lWhen deploying airbag and seatbelt pre-
tensioner units, ensure that all personnel are
at least 15 metres away from the deployment
zone.
lEnsure deployment tool is connected
correctly, in compliance with the
instructions detailed in this manual. In
particular, ensure deployment tool is NOT
connected to battery supply before
connecting to the airbag or seatbelt pre-
tensioner module connector.
lWhen deploying seatbelt pre-tensioners in
the vehicle, ensure the pre-tensioner unit is
fully secured to its fixing point.
lWhen removing deployed airbag and
seatbelt pre-tensioner modules, wear
protective clothing. Use gloves and seal
deployed units in a plastic bag.
lFollowing deployment of any component of
the SRS system within the vehicle, all SRS
components must be replaced. DO NOT re-
use or salvage any parts of the SRS system.
lDo not lean over airbag modules or seatbelt
pre-tensioner units when connecting
deployment equipment.
WARNING: During deployment parts of the
airbag module become hot enough to burn you.
Wait 30 minutes after deployment before
touching the airbag module.
Page 59 of 1007
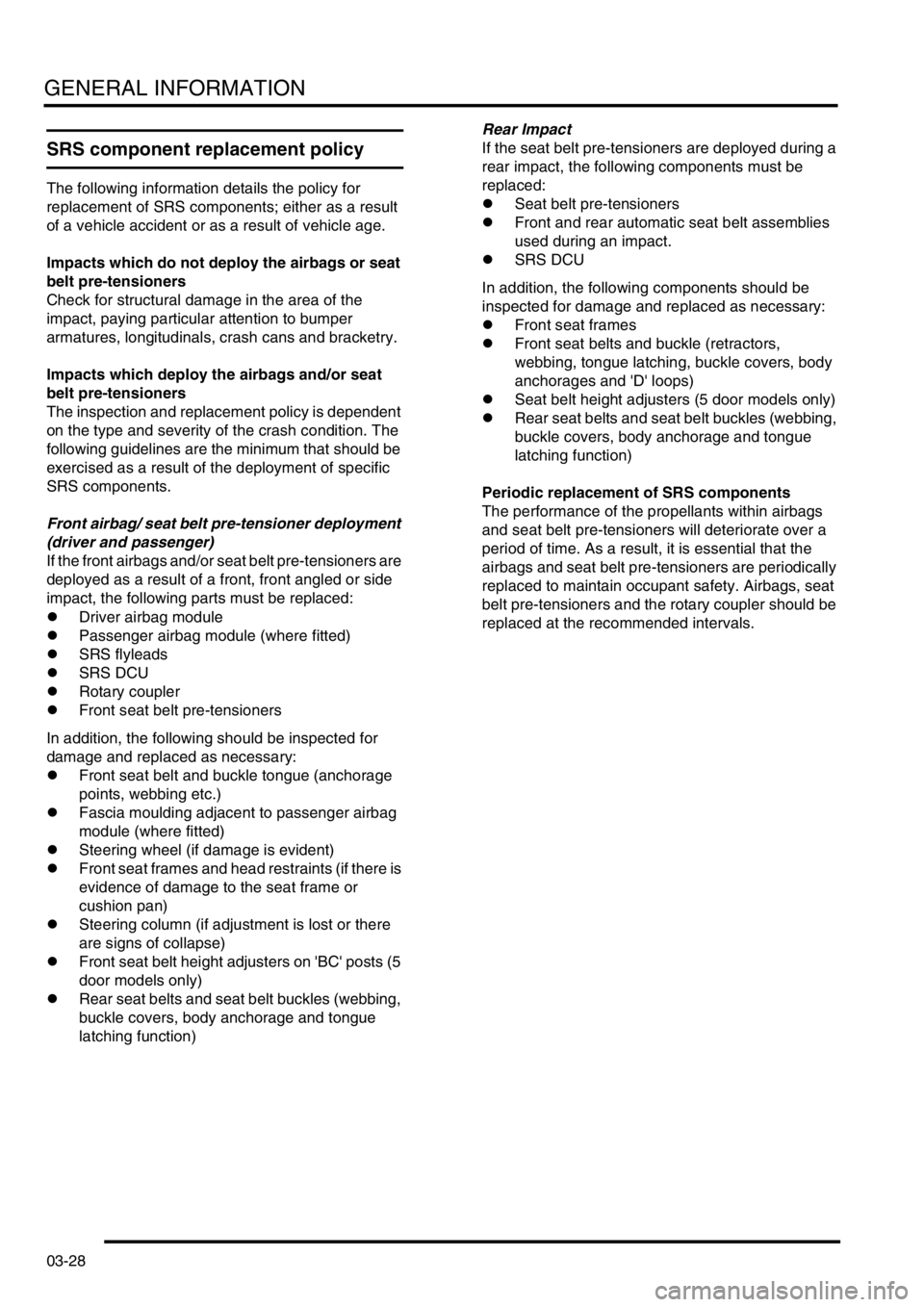
GENERAL INFORMATION
03-28
SRS component replacement policy
The following information details the policy for
replacement of SRS components; either as a result
of a vehicle accident or as a result of vehicle age.
Impacts which do not deploy the airbags or seat
belt pre-tensioners
Check for structural damage in the area of the
impact, paying particular attention to bumper
armatures, longitudinals, crash cans and bracketry.
Impacts which deploy the airbags and/or seat
belt pre-tensioners
The inspection and replacement policy is dependent
on the type and severity of the crash condition. The
following guidelines are the minimum that should be
exercised as a result of the deployment of specific
SRS components.
Front airbag/ seat belt pre-tensioner deployment
(driver and passenger)
If the front airbags and/or seat belt pre-tensioners are
deployed as a result of a front, front angled or side
impact, the following parts must be replaced:
lDriver airbag module
lPassenger airbag module (where fitted)
lSRS flyleads
lSRS DCU
lRotary coupler
lFront seat belt pre-tensioners
In addition, the following should be inspected for
damage and replaced as necessary:
lFront seat belt and buckle tongue (anchorage
points, webbing etc.)
lFascia moulding adjacent to passenger airbag
module (where fitted)
lSteering wheel (if damage is evident)
lFront seat frames and head restraints (if there is
evidence of damage to the seat frame or
cushion pan)
lSteering column (if adjustment is lost or there
are signs of collapse)
lFront seat belt height adjusters on 'BC' posts (5
door models only)
lRear seat belts and seat belt buckles (webbing,
buckle covers, body anchorage and tongue
latching function)Rear Impact
If the seat belt pre-tensioners are deployed during a
rear impact, the following components must be
replaced:
lSeat belt pre-tensioners
lFront and rear automatic seat belt assemblies
used during an impact.
lSRS DCU
In addition, the following components should be
inspected for damage and replaced as necessary:
lFront seat frames
lFront seat belts and buckle (retractors,
webbing, tongue latching, buckle covers, body
anchorages and 'D' loops)
lSeat belt height adjusters (5 door models only)
lRear seat belts and seat belt buckles (webbing,
buckle covers, body anchorage and tongue
latching function)
Periodic replacement of SRS components
The performance of the propellants within airbags
and seat belt pre-tensioners will deteriorate over a
period of time. As a result, it is essential that the
airbags and seat belt pre-tensioners are periodically
replaced to maintain occupant safety. Airbags, seat
belt pre-tensioners and the rotary coupler should be
replaced at the recommended intervals.
Page 60 of 1007
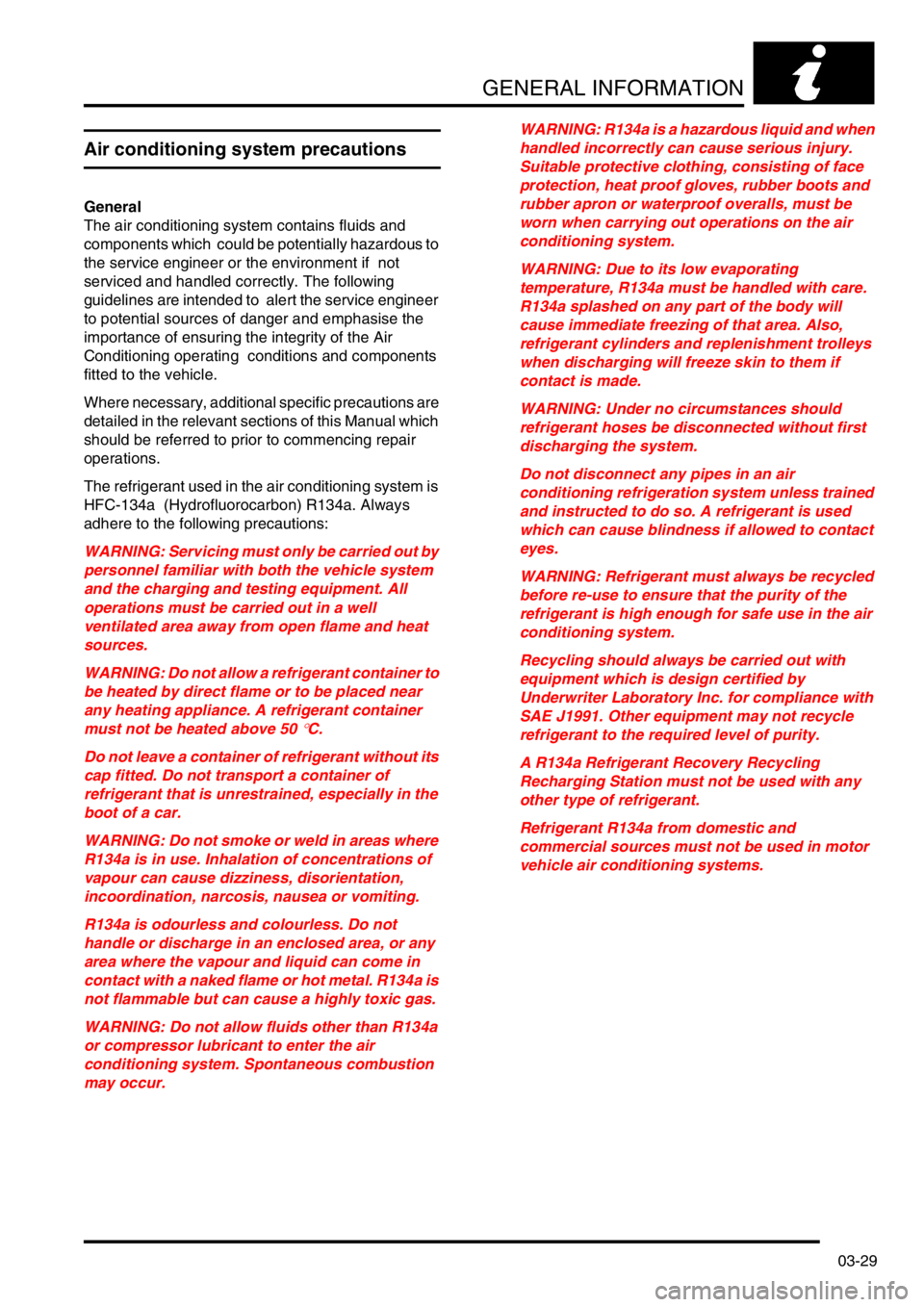
GENERAL INFORMATION
03-29
Air conditioning system precautions
General
The air conditioning system contains fluids and
components which could be potentially hazardous to
the service engineer or the environment if not
serviced and handled correctly. The following
guidelines are intended to alert the service engineer
to potential sources of danger and emphasise the
importance of ensuring the integrity of the Air
Conditioning operating conditions and components
fitted to the vehicle.
Where necessary, additional specific precautions are
detailed in the relevant sections of this Manual which
should be referred to prior to commencing repair
operations.
The refrigerant used in the air conditioning system is
HFC-134a (Hydrofluorocarbon) R134a. Always
adhere to the following precautions:
WARNING: Servicing must only be carried out by
personnel familiar with both the vehicle system
and the charging and testing equipment. All
operations must be carried out in a well
ventilated area away from open flame and heat
sources.
WARNING: Do not allow a refrigerant container to
be heated by direct flame or to be placed near
any heating appliance. A refrigerant container
must not be heated above 50
°C.
Do not leave a container of refrigerant without its
cap fitted. Do not transport a container of
refrigerant that is unrestrained, especially in the
boot of a car.
WARNING: Do not smoke or weld in areas where
R134a is in use. Inhalation of concentrations of
vapour can cause dizziness, disorientation,
incoordination, narcosis, nausea or vomiting.
R134a is odourless and colourless. Do not
handle or discharge in an enclosed area, or any
area where the vapour and liquid can come in
contact with a naked flame or hot metal. R134a is
not flammable but can cause a highly toxic gas.
WARNING: Do not allow fluids other than R134a
or compressor lubricant to enter the air
conditioning system. Spontaneous combustion
may occur.WARNING: R134a is a hazardous liquid and when
handled incorrectly can cause serious injury.
Suitable protective clothing, consisting of face
protection, heat proof gloves, rubber boots and
rubber apron or waterproof overalls, must be
worn when carrying out operations on the air
conditioning system.
WARNING: Due to its low evaporating
temperature, R134a must be handled with care.
R134a splashed on any part of the body will
cause immediate freezing of that area. Also,
refrigerant cylinders and replenishment trolleys
when discharging will freeze skin to them if
contact is made.
WARNING: Under no circumstances should
refrigerant hoses be disconnected without first
discharging the system.
Do not disconnect any pipes in an air
conditioning refrigeration system unless trained
and instructed to do so. A refrigerant is used
which can cause blindness if allowed to contact
eyes.
WARNING: Refrigerant must always be recycled
before re-use to ensure that the purity of the
refrigerant is high enough for safe use in the air
conditioning system.
Recycling should always be carried out with
equipment which is design certified by
Underwriter Laboratory Inc. for compliance with
SAE J1991. Other equipment may not recycle
refrigerant to the required level of purity.
A R134a Refrigerant Recovery Recycling
Recharging Station must not be used with any
other type of refrigerant.
Refrigerant R134a from domestic and
commercial sources must not be used in motor
vehicle air conditioning systems.
Page 61 of 1007
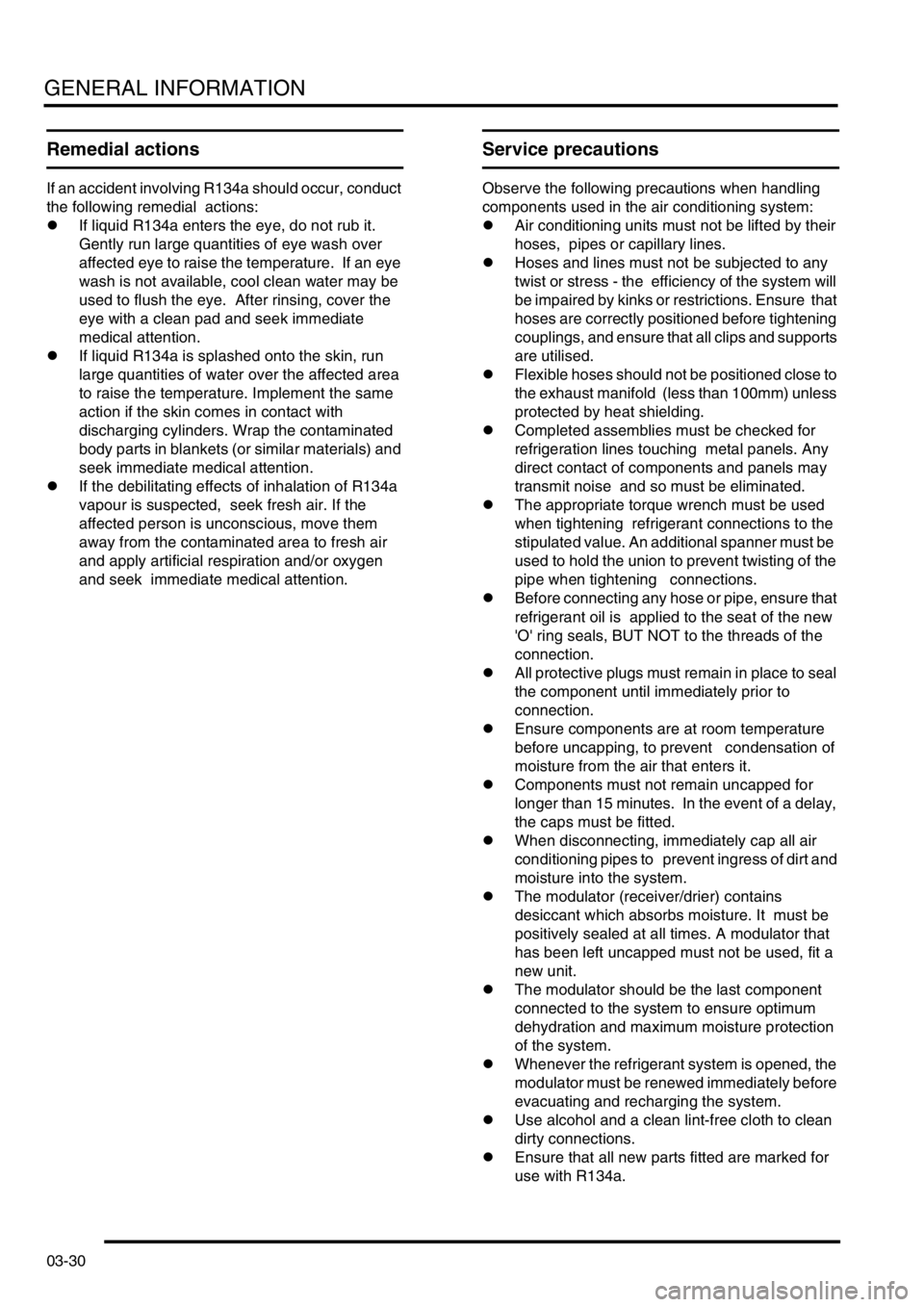
GENERAL INFORMATION
03-30
Remedial actions
If an accident involving R134a should occur, conduct
the following remedial actions:
lIf liquid R134a enters the eye, do not rub it.
Gently run large quantities of eye wash over
affected eye to raise the temperature. If an eye
wash is not available, cool clean water may be
used to flush the eye. After rinsing, cover the
eye with a clean pad and seek immediate
medical attention.
lIf liquid R134a is splashed onto the skin, run
large quantities of water over the affected area
to raise the temperature. Implement the same
action if the skin comes in contact with
discharging cylinders. Wrap the contaminated
body parts in blankets (or similar materials) and
seek immediate medical attention.
lIf the debilitating effects of inhalation of R134a
vapour is suspected, seek fresh air. If the
affected person is unconscious, move them
away from the contaminated area to fresh air
and apply artificial respiration and/or oxygen
and seek immediate medical attention.
Service precautions
Observe the following precautions when handling
components used in the air conditioning system:
lAir conditioning units must not be lifted by their
hoses, pipes or capillary lines.
lHoses and lines must not be subjected to any
twist or stress - the efficiency of the system will
be impaired by kinks or restrictions. Ensure that
hoses are correctly positioned before tightening
couplings, and ensure that all clips and supports
are utilised.
lFlexible hoses should not be positioned close to
the exhaust manifold (less than 100mm) unless
protected by heat shielding.
lCompleted assemblies must be checked for
refrigeration lines touching metal panels. Any
direct contact of components and panels may
transmit noise and so must be eliminated.
lThe appropriate torque wrench must be used
when tightening refrigerant connections to the
stipulated value. An additional spanner must be
used to hold the union to prevent twisting of the
pipe when tightening connections.
lBefore connecting any hose or pipe, ensure that
refrigerant oil is applied to the seat of the new
'O' ring seals, BUT NOT to the threads of the
connection.
lAll protective plugs must remain in place to seal
the component until immediately prior to
connection.
lEnsure components are at room temperature
before uncapping, to prevent condensation of
moisture from the air that enters it.
lComponents must not remain uncapped for
longer than 15 minutes. In the event of a delay,
the caps must be fitted.
lWhen disconnecting, immediately cap all air
conditioning pipes to prevent ingress of dirt and
moisture into the system.
lThe modulator (receiver/drier) contains
desiccant which absorbs moisture. It must be
positively sealed at all times. A modulator that
has been left uncapped must not be used, fit a
new unit.
lThe modulator should be the last component
connected to the system to ensure optimum
dehydration and maximum moisture protection
of the system.
lWhenever the refrigerant system is opened, the
modulator must be renewed immediately before
evacuating and recharging the system.
lUse alcohol and a clean lint-free cloth to clean
dirty connections.
lEnsure that all new parts fitted are marked for
use with R134a.
Page 62 of 1007
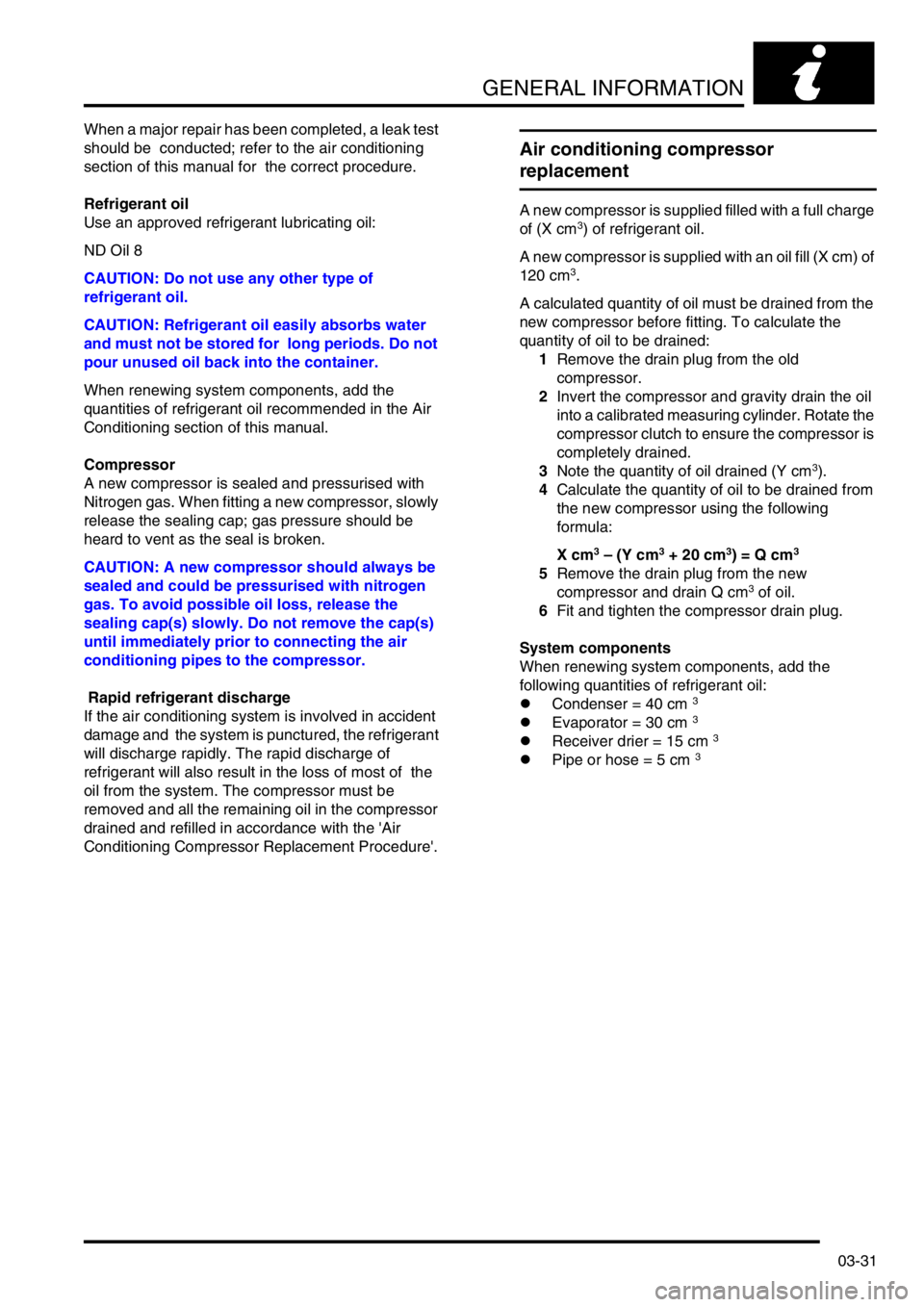
GENERAL INFORMATION
03-31
When a major repair has been completed, a leak test
should be conducted; refer to the air conditioning
section of this manual for the correct procedure.
Refrigerant oil
Use an approved refrigerant lubricating oil:
ND Oil 8
CAUTION: Do not use any other type of
refrigerant oil.
CAUTION: Refrigerant oil easily absorbs water
and must not be stored for long periods. Do not
pour unused oil back into the container.
When renewing system components, add the
quantities of refrigerant oil recommended in the Air
Conditioning section of this manual.
Compressor
A new compressor is sealed and pressurised with
Nitrogen gas. When fitting a new compressor, slowly
release the sealing cap; gas pressure should be
heard to vent as the seal is broken.
CAUTION: A new compressor should always be
sealed and could be pressurised with nitrogen
gas. To avoid possible oil loss, release the
sealing cap(s) slowly. Do not remove the cap(s)
until immediately prior to connecting the air
conditioning pipes to the compressor.
Rapid refrigerant discharge
If the air conditioning system is involved in accident
damage and the system is punctured, the refrigerant
will discharge rapidly. The rapid discharge of
refrigerant will also result in the loss of most of the
oil from the system. The compressor must be
removed and all the remaining oil in the compressor
drained and refilled in accordance with the 'Air
Conditioning Compressor Replacement Procedure'.
Air conditioning compressor
replacement
A new compressor is supplied filled with a full charge
of (X cm3) of refrigerant oil.
A new compressor is supplied with an oil fill (X cm) of
120 cm
3.
A calculated quantity of oil must be drained from the
new compressor before fitting. To calculate the
quantity of oil to be drained:
1Remove the drain plug from the old
compressor.
2Invert the compressor and gravity drain the oil
into a calibrated measuring cylinder. Rotate the
compressor clutch to ensure the compressor is
completely drained.
3Note the quantity of oil drained (Y cm
3).
4Calculate the quantity of oil to be drained from
the new compressor using the following
formula:
X cm
3 – (Y cm3 + 20 cm3) = Q cm3
5Remove the drain plug from the new
compressor and drain Q cm3 of oil.
6Fit and tighten the compressor drain plug.
System components
When renewing system components, add the
following quantities of refrigerant oil:
lCondenser = 40 cm
3
lEvaporator = 30 cm 3
lReceiver drier = 15 cm 3
lPipe or hose = 5 cm 3
Page 63 of 1007
Page 64 of 1007

GENERAL DATA
04-1
GENERAL DATA
Engine - Td4 Diesel
General
Type 2.0 litre in-line direct injection diesel, 16-valve, DOHC, turbocharged
and intercooled
Cylinder arrangement 4 in-line, transverse, No.1 cylinder at front of engine
Bore 84.00 mm (3.307 in.)
Stroke 88.00 mm (3.465 in.)
Capacity 1951 cm
3 (119.05 in3)
Firing order 1-3-4-2
Compression ratio 18:1 ± 0.5:1
Direction of rotation Clockwise, viewed from the front of the engine
Maximum power:
⇒ Up to 03 Model Year - Manual and automatic
gearbox
⇒ 03 Model Year onwards - Manual gearbox
⇒ 03 Model Year onwards - Automatic gearbox82 kW (112 bhp) @ 4000 rev/min.
82 kW (112 bhp) @ 4000 rev/min
80 kW (107 bhp) @ 4000 rev/min
Maximum torque 260 Nm (192 lbf.ft) @ 1750 rev/min.
Maximum governed speed 4800 rev/min.
Maximum overrun speed 5250 rev/min
Idle speed 780 ± 30 rev/min
Dimensions:
⇒ Length
⇒ Width
⇒ Height482 mm (19.0 in)
634 mm (25.0 in)
697 mm (27.4 in)
Glow plugs: 4 off, one per cylinder arranged centrally on inlet side between inlet
valves
Turbocharger Garrett GT2
Fuel injection system: Common rail, direct injection fed by Bosch high pressure delivery
pump
Injection timing Controlled by ECM
Emissions standard ECD3
Valve timing
Inlet valves:
⇒ Opens
⇒ Closes8° BTDC
28° ABDC
Exhaust valves:
⇒ Opens
⇒ Closes38° BBDC
4° ATDC