Page 857 of 1007
CORROSION PREVENTION AND SEALING
77-4-26 SEALING
Seam sealer on vehicle interior and rear quarter - 5 door
Seams symmetrically opposite to those shown are also treated. Sealant to be wiped to a smooth finish over length 'A'
(rear load floor to rear heelboard underframe).
Page 858 of 1007
CORROSION PREVENTION AND SEALING
INTERNAL SEALING 77-4-27
INT ERNAL SEALING
Expanding foam acoustic seals
3 Door shown
M77 2056
Page 859 of 1007
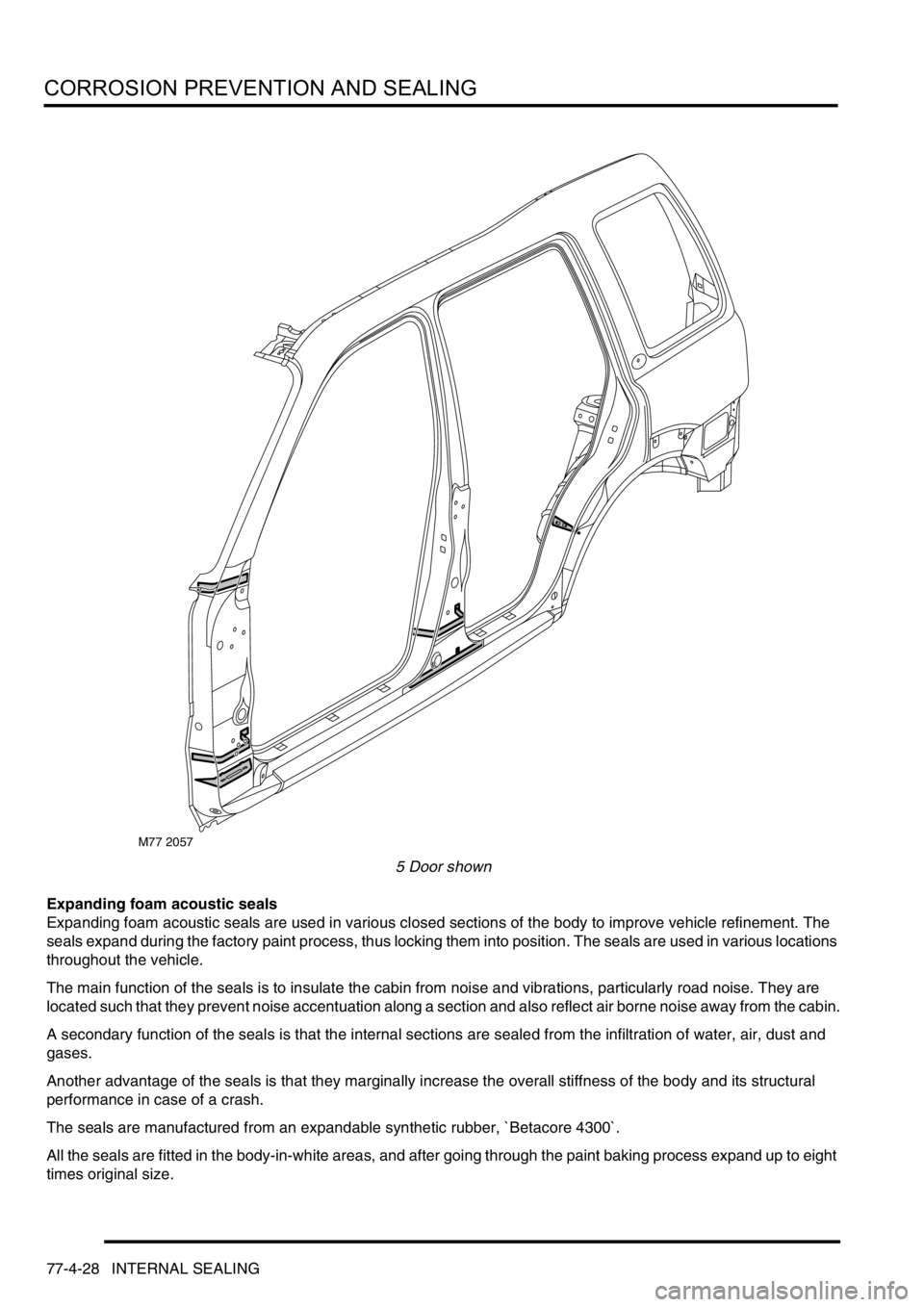
CORROSION PREVENTION AND SEALING
77-4-28 INTERNAL SEALING
5 Door shown
Expanding foam acoustic seals
Expanding foam acoustic seals are used in various closed sections of the body to improve vehicle refinement. The
seals expand during the factory paint process, thus locking them into position. The seals are used in various locations
throughout the vehicle.
The main function of the seals is to insulate the cabin from noise and vibrations, particularly road noise. They are
located such that they prevent noise accentuation along a section and also reflect air borne noise away from the cabin.
A secondary function of the seals is that the internal sections are sealed from the infiltration of water, air, dust and
gases.
Another advantage of the seals is that they marginally increase the overall stiffness of the body and its structural
performance in case of a crash.
The seals are manufactured from an expandable synthetic rubber, `Betacore 4300`.
All the seals are fitted in the body-in-white areas, and after going through the paint baking process expand up to eight
times original size.
M77 2057
Page 860 of 1007
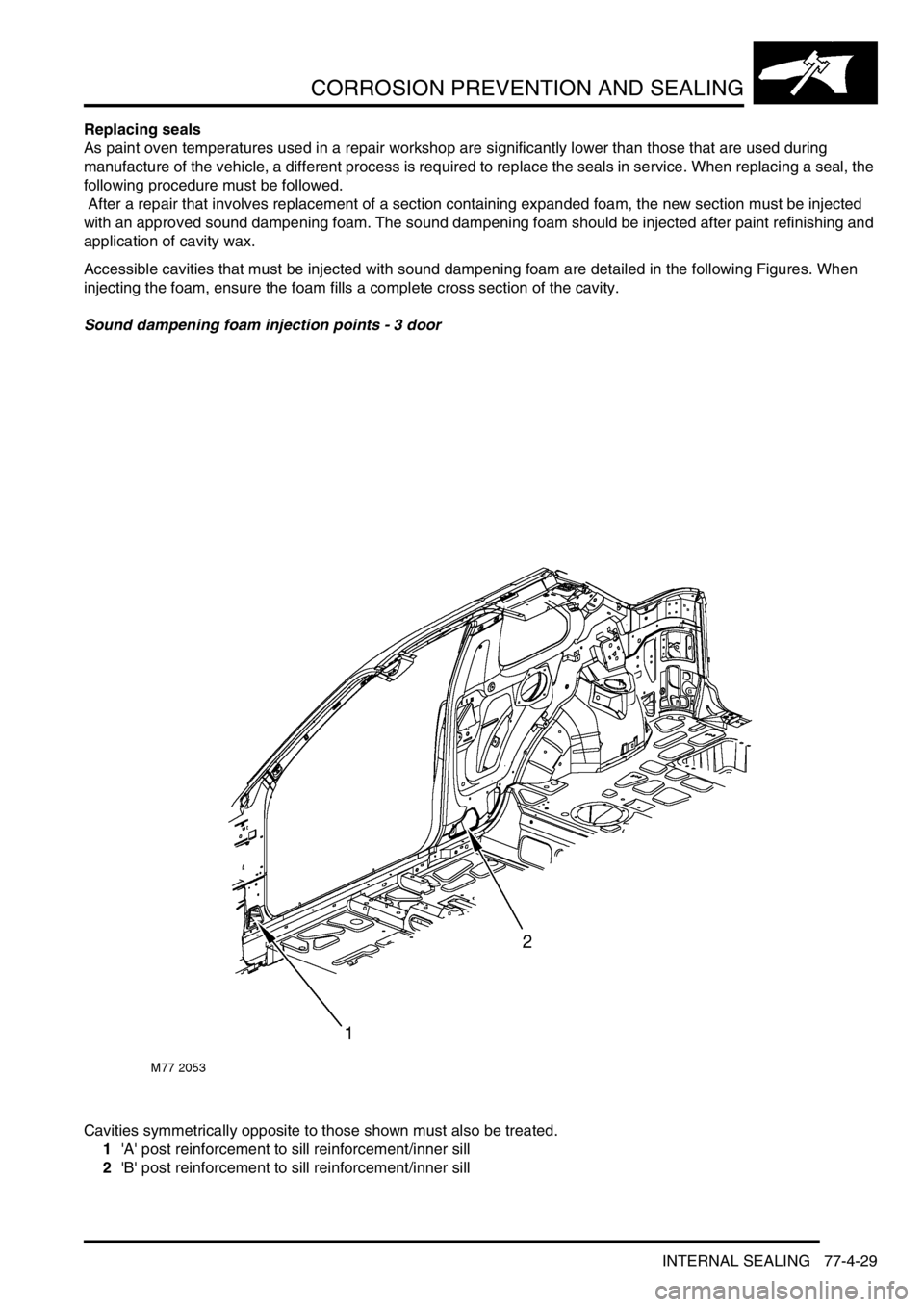
CORROSION PREVENTION AND SEALING
INTERNAL SEALING 77-4-29
Replacing seals
As paint oven temperatures used in a repair workshop are significantly lower than those that are used during
manufacture of the vehicle, a different process is required to replace the seals in service. When replacing a seal, the
following procedure must be followed.
After a repair that involves replacement of a section containing expanded foam, the new section must be injected
with an approved sound dampening foam. The sound dampening foam should be injected after paint refinishing and
application of cavity wax.
Accessible cavities that must be injected with sound dampening foam are detailed in the following Figures. When
injecting the foam, ensure the foam fills a complete cross section of the cavity.
Sound dampening foam injection points - 3 door
Cavities symmetrically opposite to those shown must also be treated.
1'A' post reinforcement to sill reinforcement/inner sill
2'B' post reinforcement to sill reinforcement/inner sill
Page 861 of 1007
CORROSION PREVENTION AND SEALING
77-4-30 INTERNAL SEALING
Sound dampening foam injection points - 5 door
Cavities symmetrically opposite to those shown must also be treated.
1'A' post reinforcement to sill reinforcement/inner sill
2'B/C' post reinforcement to sill reinforcement/inner sill
3Outer wheelarch to outer body side
Page 862 of 1007
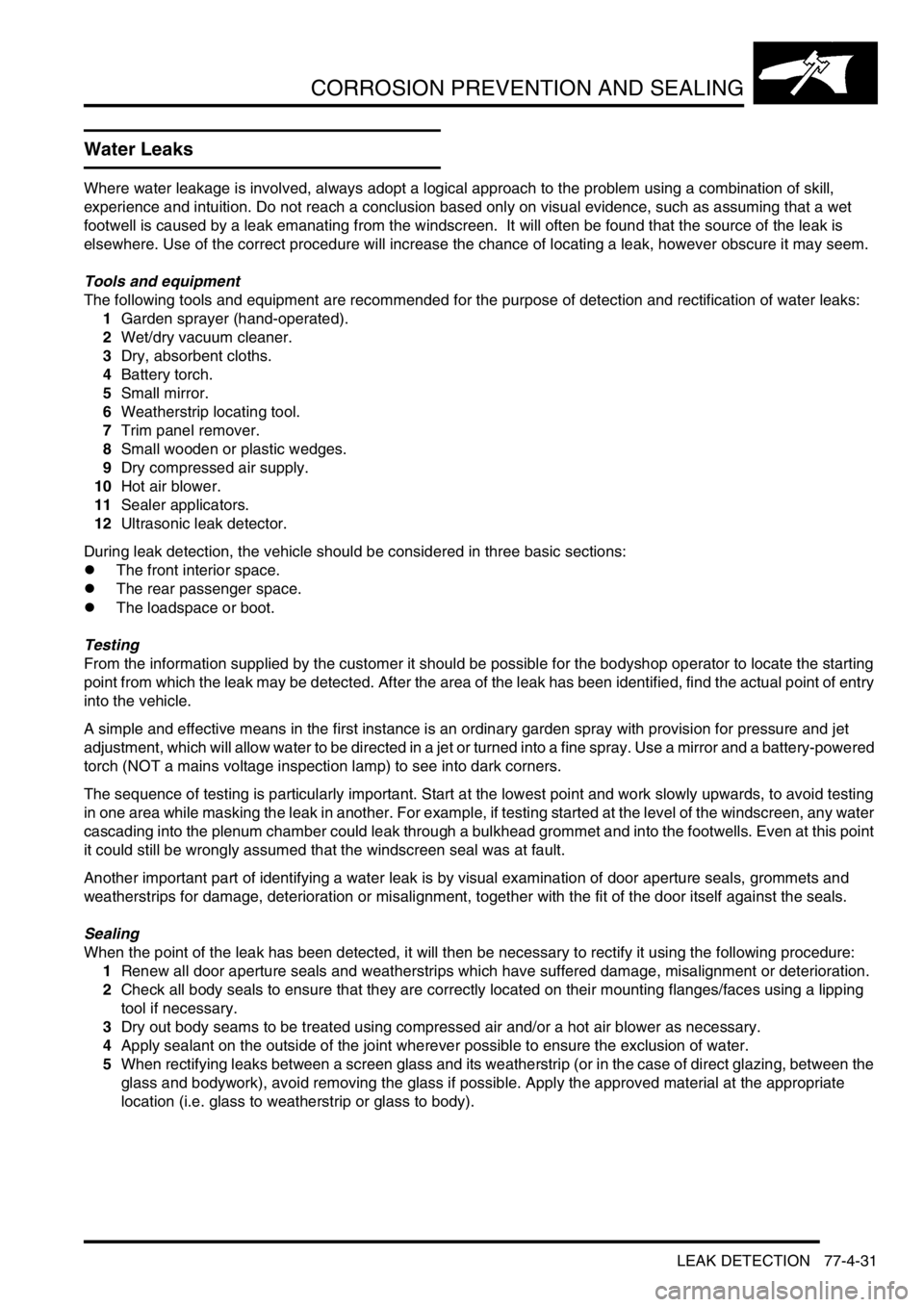
CORROSION PREVENTION AND SEALING
LEAK DETECTION 77-4-31
LEAK DETECT ION
Water Leaks
Where water leakage is involved, always adopt a logical approach to the problem using a combination of skill,
experience and intuition. Do not reach a conclusion based only on visual evidence, such as assuming that a wet
footwell is caused by a leak emanating from the windscreen. It will often be found that the source of the leak is
elsewhere. Use of the correct procedure will increase the chance of locating a leak, however obscure it may seem.
Tools and equipment
The following tools and equipment are recommended for the purpose of detection and rectification of water leaks:
1Garden sprayer (hand-operated).
2Wet/dry vacuum cleaner.
3Dry, absorbent cloths.
4Battery torch.
5Small mirror.
6Weatherstrip locating tool.
7Trim panel remover.
8Small wooden or plastic wedges.
9Dry compressed air supply.
10Hot air blower.
11Sealer applicators.
12Ultrasonic leak detector.
During leak detection, the vehicle should be considered in three basic sections:
lThe front interior space.
lThe rear passenger space.
lThe loadspace or boot.
Testing
From the information supplied by the customer it should be possible for the bodyshop operator to locate the starting
point from which the leak may be detected. After the area of the leak has been identified, find the actual point of entry
into the vehicle.
A simple and effective means in the first instance is an ordinary garden spray with provision for pressure and jet
adjustment, which will allow water to be directed in a jet or turned into a fine spray. Use a mirror and a battery-powered
torch (NOT a mains voltage inspection lamp) to see into dark corners.
The sequence of testing is particularly important. Start at the lowest point and work slowly upwards, to avoid testing
in one area while masking the leak in another. For example, if testing started at the level of the windscreen, any water
cascading into the plenum chamber could leak through a bulkhead grommet and into the footwells. Even at this point
it could still be wrongly assumed that the windscreen seal was at fault.
Another important part of identifying a water leak is by visual examination of door aperture seals, grommets and
weatherstrips for damage, deterioration or misalignment, together with the fit of the door itself against the seals.
Sealing
When the point of the leak has been detected, it will then be necessary to rectify it using the following procedure:
1Renew all door aperture seals and weatherstrips which have suffered damage, misalignment or deterioration.
2Check all body seals to ensure that they are correctly located on their mounting flanges/faces using a lipping
tool if necessary.
3Dry out body seams to be treated using compressed air and/or a hot air blower as necessary.
4Apply sealant on the outside of the joint wherever possible to ensure the exclusion of water.
5When rectifying leaks between a screen glass and its weatherstrip (or in the case of direct glazing, between the
glass and bodywork), avoid removing the glass if possible. Apply the approved material at the appropriate
location (i.e. glass to weatherstrip or glass to body).
Page 863 of 1007
Page 864 of 1007
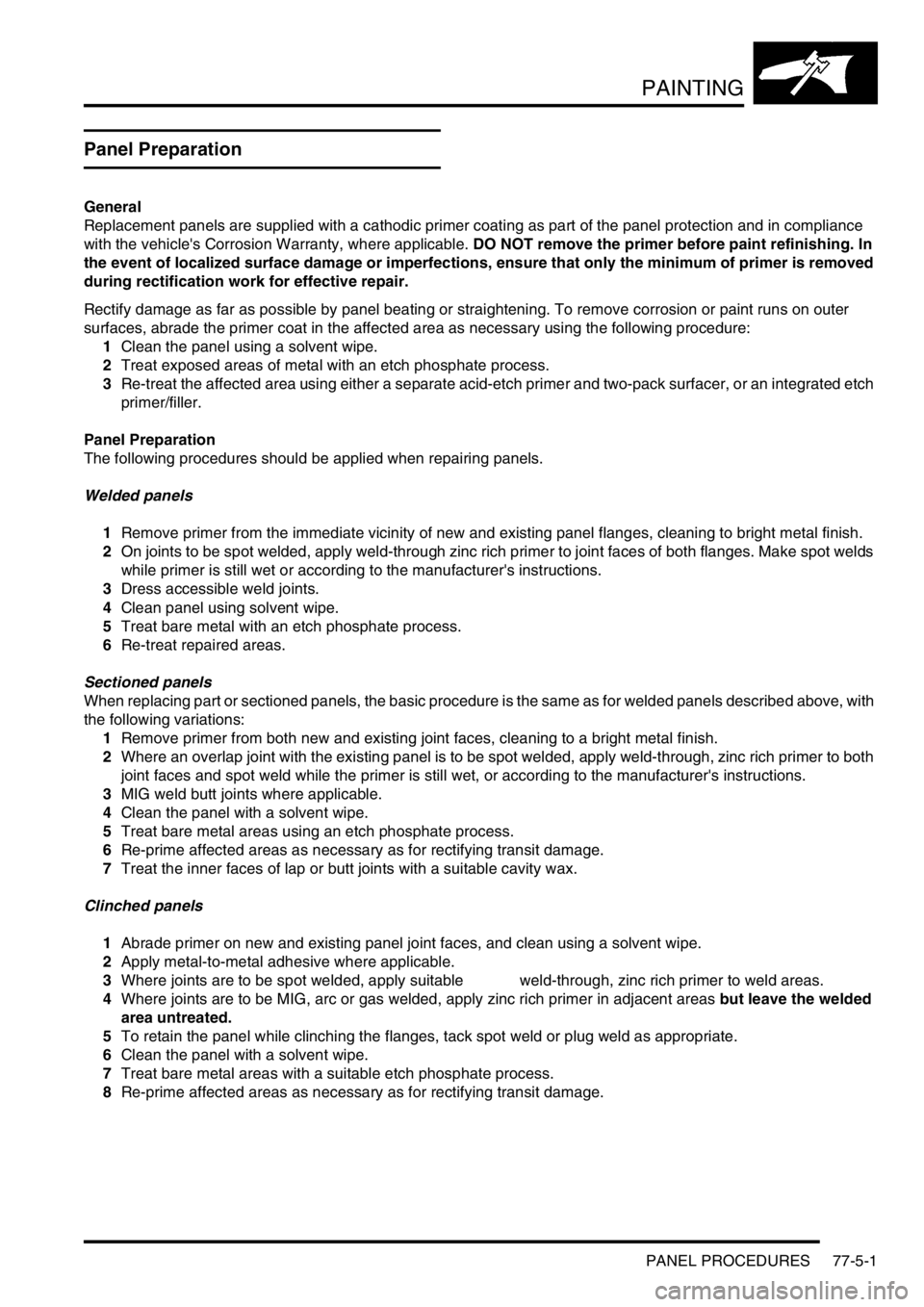
PAINTING
PANEL PROCEDURES 77-5-1
PAINTING PANEL PROCEDURES
Panel Preparation
General
Replacement panels are supplied with a cathodic primer coating as part of the panel protection and in compliance
with the vehicle's Corrosion Warranty, where applicable. DO NOT remove the primer before paint refinishing. In
the event of localized surface damage or imperfections, ensure that only the minimum of primer is removed
during rectification work for effective repair.
Rectify damage as far as possible by panel beating or straightening. To remove corrosion or paint runs on outer
surfaces, abrade the primer coat in the affected area as necessary using the following procedure:
1Clean the panel using a solvent wipe.
2Treat exposed areas of metal with an etch phosphate process.
3Re-treat the affected area using either a separate acid-etch primer and two-pack surfacer, or an integrated etch
primer/filler.
Panel Preparation
The following procedures should be applied when repairing panels.
Welded panels
1Remove primer from the immediate vicinity of new and existing panel flanges, cleaning to bright metal finish.
2On joints to be spot welded, apply weld-through zinc rich primer to joint faces of both flanges. Make spot welds
while primer is still wet or according to the manufacturer's instructions.
3Dress accessible weld joints.
4Clean panel using solvent wipe.
5Treat bare metal with an etch phosphate process.
6Re-treat repaired areas.
Sectioned panels
When replacing part or sectioned panels, the basic procedure is the same as for welded panels described above, with
the following variations:
1Remove primer from both new and existing joint faces, cleaning to a bright metal finish.
2Where an overlap joint with the existing panel is to be spot welded, apply weld-through, zinc rich primer to both
joint faces and spot weld while the primer is still wet, or according to the manufacturer's instructions.
3MIG weld butt joints where applicable.
4Clean the panel with a solvent wipe.
5Treat bare metal areas using an etch phosphate process.
6Re-prime affected areas as necessary as for rectifying transit damage.
7Treat the inner faces of lap or butt joints with a suitable cavity wax.
Clinched panels
1Abrade primer on new and existing panel joint faces, and clean using a solvent wipe.
2Apply metal-to-metal adhesive where applicable.
3Where joints are to be spot welded, apply suitable weld-through, zinc rich primer to weld areas.
4Where joints are to be MIG, arc or gas welded, apply zinc rich primer in adjacent areas but leave the welded
area untreated.
5To retain the panel while clinching the flanges, tack spot weld or plug weld as appropriate.
6Clean the panel with a solvent wipe.
7Treat bare metal areas with a suitable etch phosphate process.
8Re-prime affected areas as necessary as for rectifying transit damage.
PAINT P ROCEDURES