Page 753 of 1007
BODY DIMENSIONS
77-1-18 BODY GAPS AND PROFILES
Section Gap Description Dimension
D-D d Headlamp to wing 3.0 (0.118)
E-E e Bonnet to wing 6.0 (0.236)
F-F f Rear edge bonnet to wing 6.0 (0.236)
G-G g Wing to front door 5.0 (0.196)
H-H, J-J h Front door frame to body 5.0 (0.196)
K-K, L-L k Front door to rear door 5.0 (0.196)
M-M m Bottom of door to sill 6.0 (0.236)
N-N, P-P n Rear door to body 5.0 (0.196)
Page 754 of 1007
BODY DIMENSIONS
BODY GAPS AND PROFILES 77-1-19
The tolerance for sections E-E and F-F is ± 1.0 mm (0.040). The other dimensions all have a tolerance of ± 0.5 mm
(0.020).
Section D-D, if the wing has been exposed to oven curing set gap to 4.4 mm (0.173) to enable subsequent expansion.
Section G-G, profile of wing to front door is 0.0 nominal, tolerance +1.0 (0.040) / -0.0.
Section H-H and J-J, profile of front door frame to body is -2.5 mm (0.098) nominal, tolerance +0.0 / -1.0 mm (0.040).
Section K-K and L-L, profile of front door to rear door is 0.0 nominal, tolerance +0.0 / -1.0 mm (0.040).
Section N-N and P-P, profile of rear door to body is 0.0 nominal, tolerance +1.0 (0.040) / -0.0.
The tolerance for sections P-P and Q-Q is ± 0.5 mm (0.020).
Section Gap Description Dimension
P-P p Taildoor to rear lamp 5.0 (0.196)
Q-Q q Taildoor to rear bumper 6.0 (0.236)
Page 755 of 1007
Page 756 of 1007
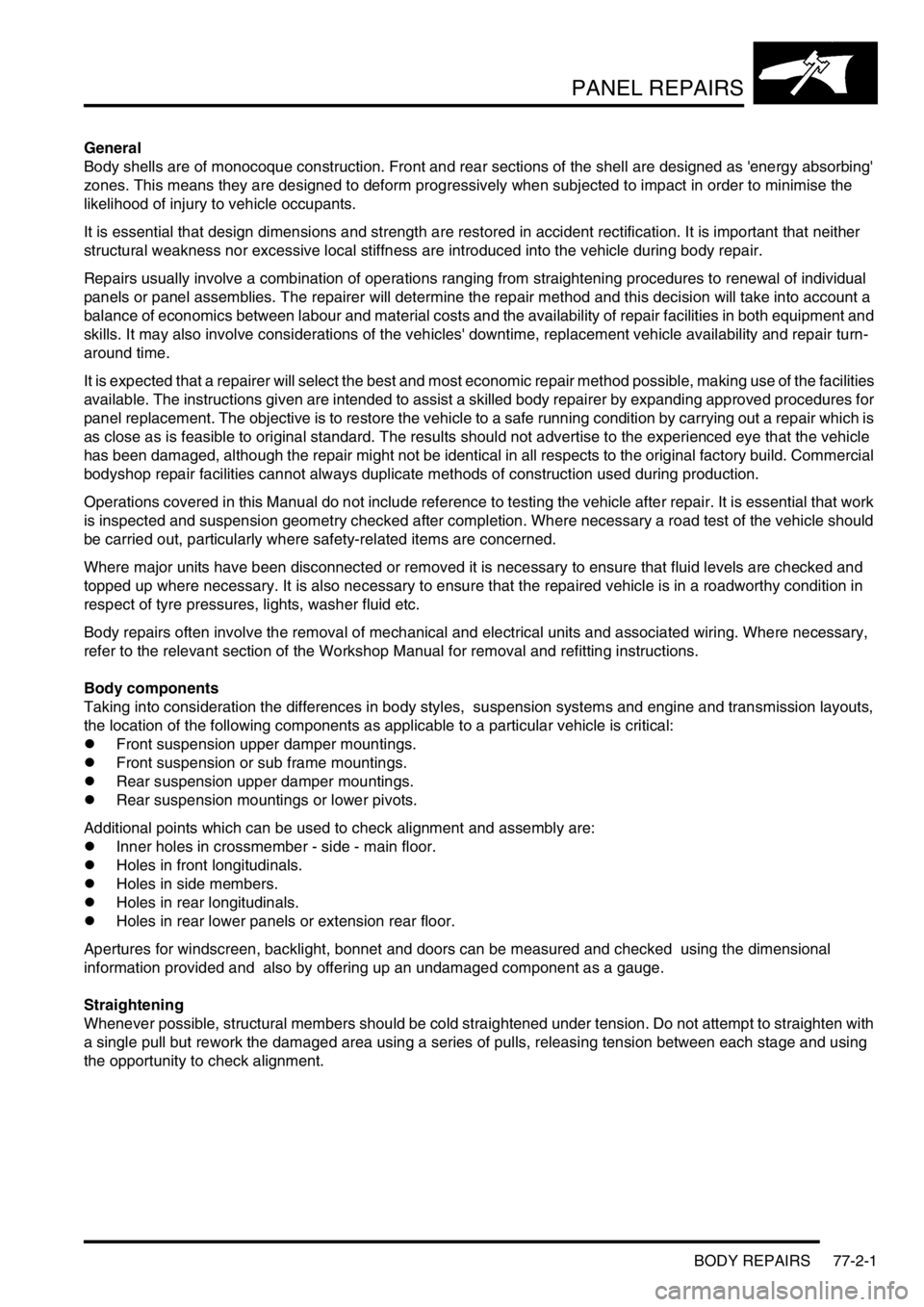
PANEL REPAIRS
BODY REPAIRS 77-2-1
PANEL REPAIRS
General
Body shells are of monocoque construction. Front and rear sections of the shell are designed as 'energy absorbing'
zones. This means they are designed to deform progressively when subjected to impact in order to minimise the
likelihood of injury to vehicle occupants.
It is essential that design dimensions and strength are restored in accident rectification. It is important that neither
structural weakness nor excessive local stiffness are introduced into the vehicle during body repair.
Repairs usually involve a combination of operations ranging from straightening procedures to renewal of individual
panels or panel assemblies. The repairer will determine the repair method and this decision will take into account a
balance of economics between labour and material costs and the availability of repair facilities in both equipment and
skills. It may also involve considerations of the vehicles' downtime, replacement vehicle availability and repair turn-
around time.
It is expected that a repairer will select the best and most economic repair method possible, making use of the facilities
available. The instructions given are intended to assist a skilled body repairer by expanding approved procedures for
panel replacement. The objective is to restore the vehicle to a safe running condition by carrying out a repair which is
as close as is feasible to original standard. The results should not advertise to the experienced eye that the vehicle
has been damaged, although the repair might not be identical in all respects to the original factory build. Commercial
bodyshop repair facilities cannot always duplicate methods of construction used during production.
Operations covered in this Manual do not include reference to testing the vehicle after repair. It is essential that work
is inspected and suspension geometry checked after completion. Where necessary a road test of the vehicle should
be carried out, particularly where safety-related items are concerned.
Where major units have been disconnected or removed it is necessary to ensure that fluid levels are checked and
topped up where necessary. It is also necessary to ensure that the repaired vehicle is in a roadworthy condition in
respect of tyre pressures, lights, washer fluid etc.
Body repairs often involve the removal of mechanical and electrical units and associated wiring. Where necessary,
refer to the relevant section of the Workshop Manual for removal and refitting instructions.
Body components
Taking into consideration the differences in body styles, suspension systems and engine and transmission layouts,
the location of the following components as applicable to a particular vehicle is critical:
lFront suspension upper damper mountings.
lFront suspension or sub frame mountings.
lRear suspension upper damper mountings.
lRear suspension mountings or lower pivots.
Additional points which can be used to check alignment and assembly are:
lInner holes in crossmember - side - main floor.
lHoles in front longitudinals.
lHoles in side members.
lHoles in rear longitudinals.
lHoles in rear lower panels or extension rear floor.
Apertures for windscreen, backlight, bonnet and doors can be measured and checked using the dimensional
information provided and also by offering up an undamaged component as a gauge.
Straightening
Whenever possible, structural members should be cold straightened under tension. Do not attempt to straighten with
a single pull but rework the damaged area using a series of pulls, releasing tension between each stage and using
the opportunity to check alignment.
Page 757 of 1007
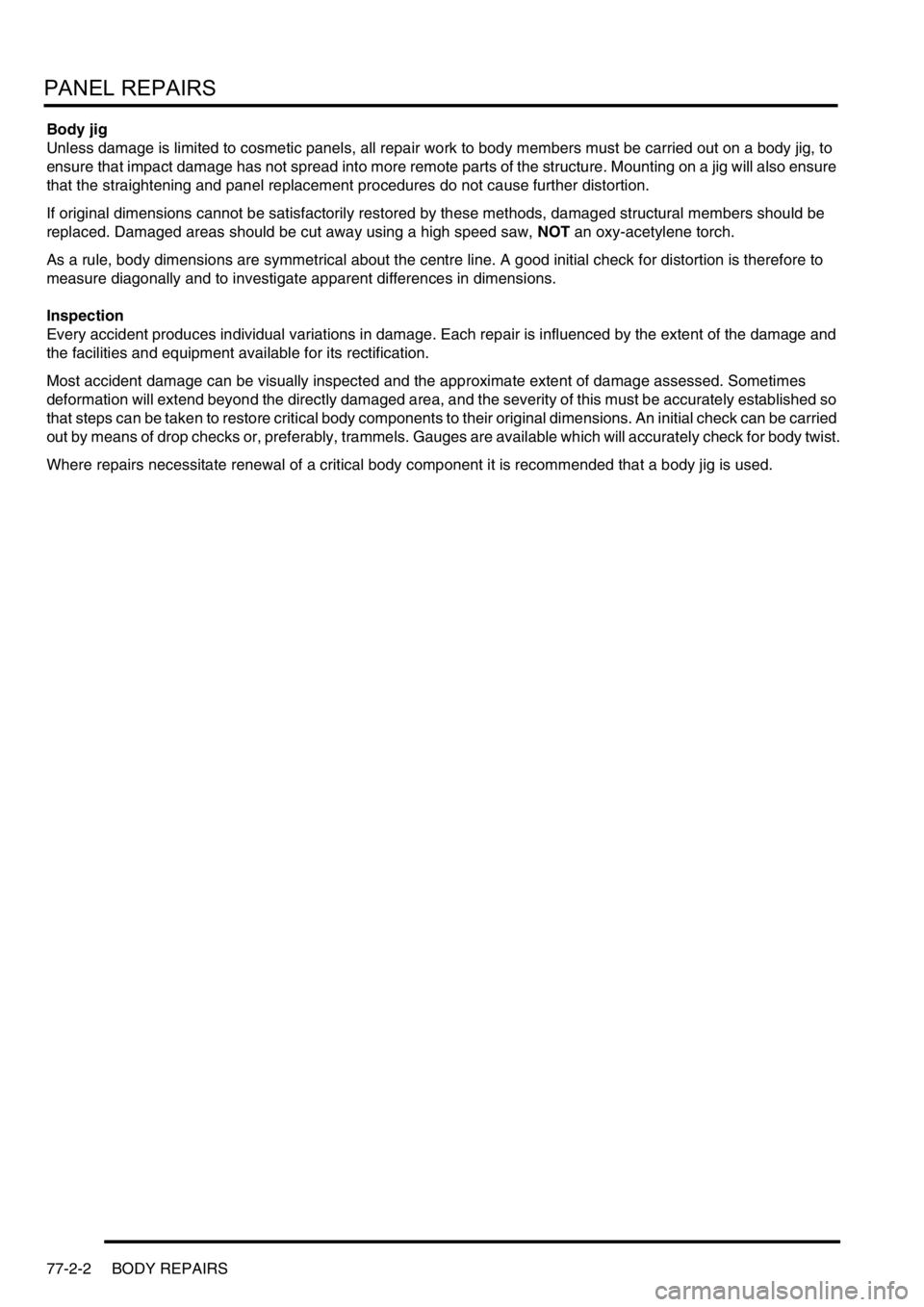
PANEL REPAIRS
77-2-2 BODY REPAIRS
Body jig
Unless damage is limited to cosmetic panels, all repair work to body members must be carried out on a body jig, to
ensure that impact damage has not spread into more remote parts of the structure. Mounting on a jig will also ensure
that the straightening and panel replacement procedures do not cause further distortion.
If original dimensions cannot be satisfactorily restored by these methods, damaged structural members should be
replaced. Damaged areas should be cut away using a high speed saw, NOT an oxy-acetylene torch.
As a rule, body dimensions are symmetrical about the centre line. A good initial check for distortion is therefore to
measure diagonally and to investigate apparent differences in dimensions.
Inspection
Every accident produces individual variations in damage. Each repair is influenced by the extent of the damage and
the facilities and equipment available for its rectification.
Most accident damage can be visually inspected and the approximate extent of damage assessed. Sometimes
deformation will extend beyond the directly damaged area, and the severity of this must be accurately established so
that steps can be taken to restore critical body components to their original dimensions. An initial check can be carried
out by means of drop checks or, preferably, trammels. Gauges are available which will accurately check for body twist.
Where repairs necessitate renewal of a critical body component it is recommended that a body jig is used.
Page 758 of 1007
PANEL REPAIRS
REPLACEMENT PANELS 77-2-3
REPLACE ME NT PA NELS
Serviceable Panels
Front end panels
1Bonnet locking platform
2LH headlamp mounting panel
3Front lower crossmember assembly
4LH crossmember gusset plate
5RH crossmember gusset plate
6Front bulkhead assembly
7RH headlamp mounting panel
8Bonnet locking platform reinforcement
Page 759 of 1007
PANEL REPAIRS
77-2-4 REPLACEMENT PANELS
Inner front end panels
1Valance outer reinforcement assembly
2Valance upper front assembly
3Front valance assembly
4Valance front assembly
5Front sidemember closing panel
6Front sidemember assembly
Page 760 of 1007
PANEL REPAIRS
REPLACEMENT PANELS 77-2-5
Outer body side panels - 3 door
1Outer body side assembly
2Rear outer body side panel
3Lower outer body side panel
4Front outer body side panel