Page 321 of 659
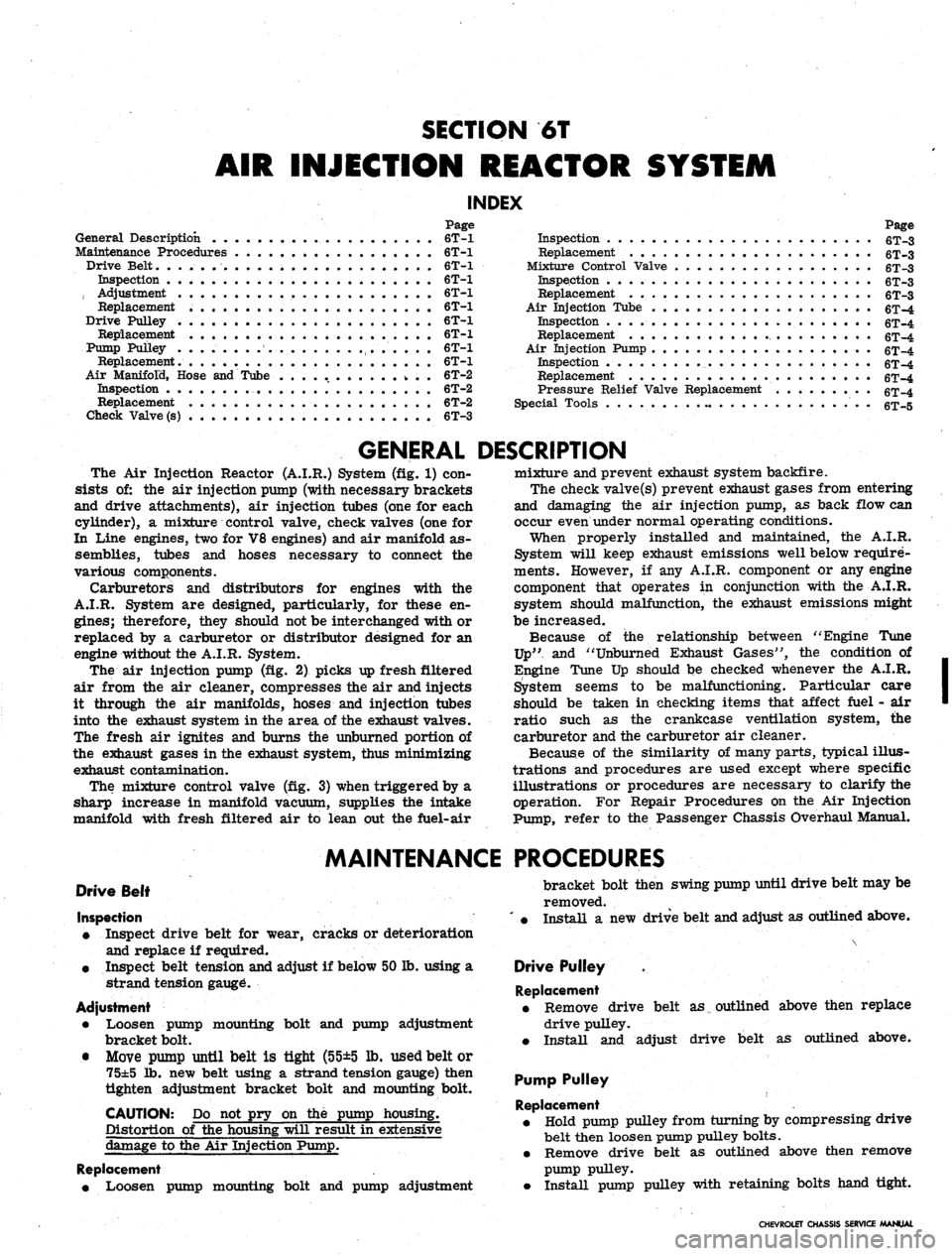
SECTION 6T
AIR INJECTION REACTOR SYSTEM
INDEX
Page
General Description 6T-1
Maintenance Procedures 6T>1
Drive Belt. ...-..' 6T-1
Inspection 6T-1
, Adjustment . . 6T-1
Replacement 6T-1
Drive Pulley . . . . 6T-1
Replacement 6T-1
Pump Pulley ....................... 6T-1
Replacement. 6T-1
Air Manifold, Hose and Tube
...........>*.
6T-2
Inspection . . 6T-2
Replacement 6T-2
Check Valve (s) 6T-3
Page
Inspection 6T-3
Replacement . . 6T-3
Mixture Control Valve 6T-3
Inspection 6T-3
Replacement 6T-3
Air Injection Tube 6T-4
Inspection . . . ... . . . .... 6T-4
Replacement 6T-4
Air Injection Pump 6T-4
Inspection 6T-4
Replacement . 6T-4
Pressure Relief Valve Replacement 6T-4
Special Tools 6T-5
GENERAL
The Air Injection Reactor (A.I.R.) System (fig. 1) con-
sists of: the air injection pump (with necessary brackets
and drive attachments), air injection tubes (one for each
cylinder), a mixture control valve, check valves (one for
In Line engines, two for V8 engines) and air manifold as-
semblies, tubes and hoses necessary to connect the
various components.
Carburetors and distributors for engines with the
A.I.R. System are designed, particularly, for these en-
gines;
therefore, they should not be interchanged with or
replaced by a carburetor or distributor designed for an
engine without the A.I.R. System.
The air injection pump (fig. 2) picks up fresh filtered
air from the air cleaner, compresses the air and injects
it through the air manifolds, hoses and injection tubes
into the exhaust system in the area of the exhaust valves.
The fresh air ignites and burns the unburned portion of
the exhaust gases in the exhaust system, thus minimizing
exhaust contamination.
The mixture control valve (fig. 3) when triggered by a
sharp increase in manifold vacuum, supplies the intake
manifold with fresh filtered air to lean out the fuel-air
DESCRIPTION
mixture and prevent exhaust system backfire.
The check valve(s) prevent exhaust gases from entering
and damaging the air injection pump, as back flow can
occur even under normal operating conditions.
When properly installed and maintained, the A.I.R.
System will keep exhaust emissions well below require-
ments. However, if any A.I.R. component or any engine
component that operates in conjunction with the A.I.R.
system should malfunction, the exhaust emissions might
be increased.
Because of the relationship between "Engine Tune
Up"
and "Unburned Exhaust Gases", the condition of
Engine Tune Up should be checked whenever the A.I.R.
System seems to be malfunctioning. Particular care
should be taken in checking items that affect fuel - air
ratio such as the crankcase ventilation system, the
carburetor and the carburetor air cleaner.
Because of the similarity of many parts, typical illus-
trations and procedures are used except where specific
illustrations or procedures are necessary to clarify the
operation. For Repair Procedures on the Air Injection
Pump,
refer to the Passenger Chassis Overhaul Manual.
MAINTENANCE PROCEDURES
Drive Belt
Inspection
• Inspect drive belt for wear, cracks or deterioration
and replace if required.
• Inspect belt tension and adjust if below 50 lb. using a
strand tension gauge.
Adjustment
• Loosen pump mounting bolt and pump adjustment
bracket bolt.
• Move pump until belt is tight (55±5 lb. used belt or
75±5 lb. new belt using a strand tension gauge) then
tighten adjustment bracket bolt and mounting bolt.
CAUTION: Do not pry on the pump housing.
Distortion of the housing will result in extensive
damage to the Air Injection Pump.
Replacement
• Loosen pump mounting bolt and pump adjustment
bracket bolt then swing pump until drive belt may be
removed.
• Install a new drive belt and adjust as outlined above.
Drive Pulley .
Replacement
• Remove drive belt as outlined above then replace
drive pulley.
• Install and adjust drive belt as outlined above.
Pump Pulley
Replacement
• Hold pump pulley from turning by compressing drive
belt then loosen pump pulley bolts.
• Remove drive belt as outlined above then remove
pump pulley.
• Install pump pulley with retaining bolts hand tight.
CHEVROLET CHASSIS SERVICE MANUAL
Page 322 of 659

AIR INJECTOR REACTOR SYSTEM
6T-2
AIR
MANIFOLD
MIXTURE
CONTROL
VALVE
AIR
INJECTION
PUMP
IN LINE
MIXTURE
CONTROL
VALVE
AIR INJECTION
PUMP
CHECK
VALVE
V8
Fig.
I—Air
Injection Reactor System (Typical)
• Install
and
adjust drive belt
as
outlined above.
• Hold pump pulley from turning
by
compressing drive
belt then torque pump pulley bolts
to 25 ft. lbs.
• Recheck drive belt tension
and
adjust
if
required.
Air Manifold, Hose and Tube
Inspection (Fig. 4)
• Inspect
all
hoses
for
deterioration
or
holes.
• Inspect
all
tubes
for
cracks
or
holes.
PUMP
HOUSING
91
DRIVE V
HUB
PRESSURE
RELIEF VALVE
•H
PUMP
'
Mm ^
COVER
A.
J^HTEXHAUST
wBBE
TUBES
SB
^1 INTAKE
JH TUBE
• Check
all
hose and tube connections.
• Check
all
tube
and
hose routing. Interference
may
cause wear.
•
If a
leak
is
suspected
on the
pressure side
of the
system
or any
tubes and/or hoses have been discon-
nected
on the
pressure side,
the
connections should
be checked
for
leaks with
a
soapy water solution.
With
the
pump running, bubbles will form
if
aleak
exists.
Replacement
•
To
replace
any
hose and/or tube, note routing then
remove hose(s) and/or tube(s)
as
required.
CAUTION:
The 1/4"
pipe threads
at the
cylin-
der head
(In
Line)
or
exhaust manifold
(V8) are
VALVE
IN
OPEN
POSITION
INLET
VALVE
IN
CLOSED
POSITION
DIAPHRAGM
POSITIONS
SIGNAL
LINE
CONNECTION
ALVE
Fig.
2—Air Injection Pump
Fig.
3—Mixture Control Valve
CHEVROLET CHASSIS SERVICE MANUAL
Page 323 of 659
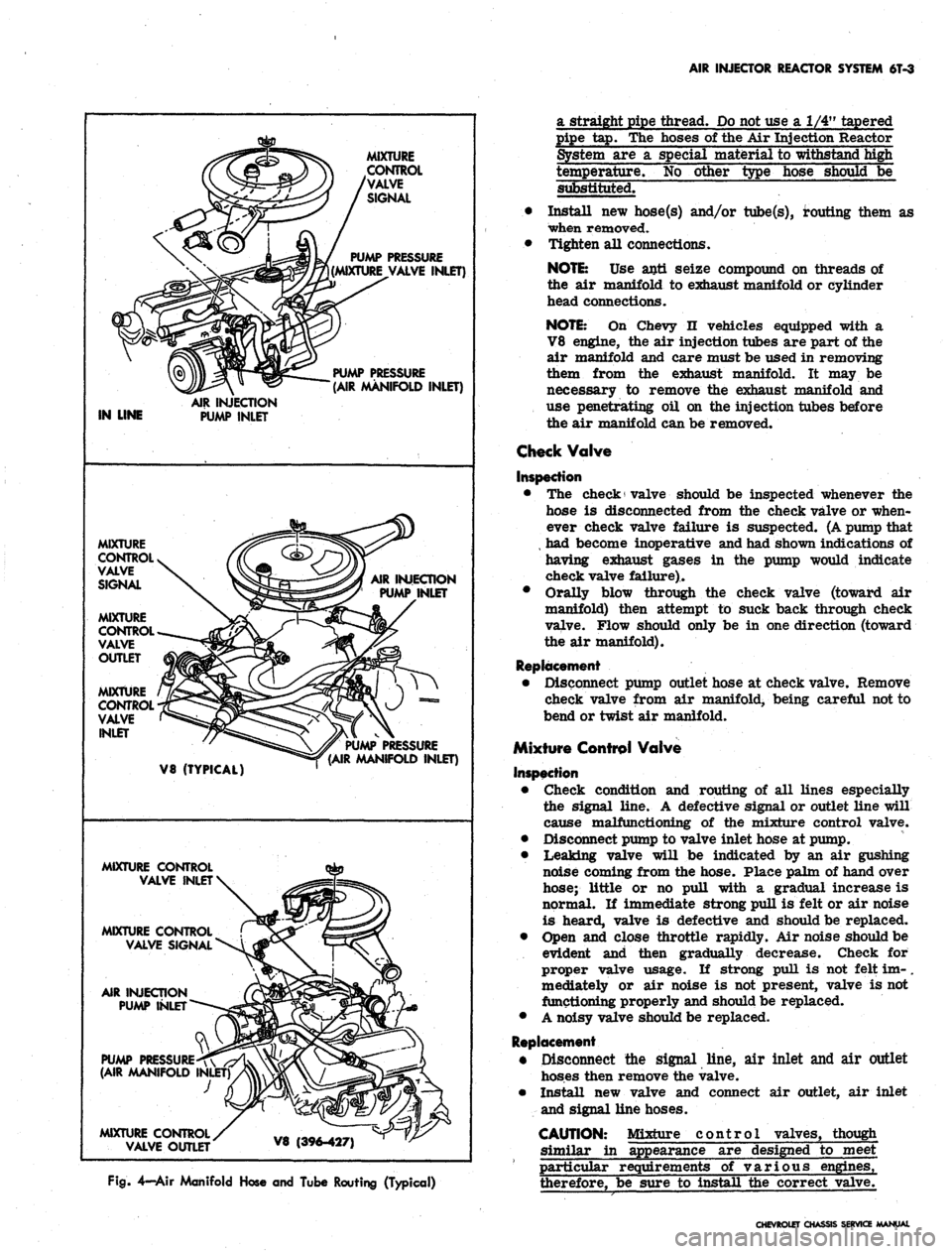
AIR INJECTOR REACTOR SYSTEM
6T-3
MIXTURE
CONTROL
VALVE
SIGNAL
PUMP PRESSURE
(MIXTURE VALVE INLET)
PUMP PRESSURE
(AIR MANIFOLD INLET)
IN LINE
AIR INJECTION
PUMP INLET
MIXTURE
CONTROL
VALVE
SIGNAL
MIXTURE
CONTROL
VALVE
OUTLET
MIXTURE
CONTROL
VALVE
INLET
AIR INJECTION
PUMP INLET
V8 (TYPICAL)
PUMP PRESSURE
(AIR MANIFOLD INLET)
MIXTURE CONTROL
VALVE INLET
MIXTURE CONTROL
VALVE SIGNAL
AIR INJECTION
PUMP INLET
PUMP PRESSURE^
(AIR MANIFOLD
J
MIXTURE CONTROL
VALVE OUTLET
V8 (396-427)
Fig.
4—Air Manifold Hose and Tube Routing (Typical)
a straight pipe thread.
Do
not use
a 1/4"
tapered
pipe
tap. The
hoses
of
the
Air
Injection Reactor
System
are a
special material
to
withstand high
temperature.
No
other type hose should
be
substituted.
• Install
new
hose(s) and/or tube(s), routing them
as
when removed.
• Tighten
all
connections.
NOTE:
Use
anti seize compound
on
threads
of
the
air
manifold
to
exhaust manifold
or
cylinder
head connections.
NOTE:
On
Chevy
n
vehicles equipped with
a
V8 engine,
the air
injection tubes
are
part
of the
air manifold
and
care must
be
used
in
removing
them from
the
exhaust manifold.
It may be
necessary
to
remove
the
exhaust manifold
and
use penetrating
oil on the
injection tubes before
the
air
manifold can
be
removed.
Check Valve
Inspection
•
The
check valve should
be
inspected whenever
the
hose
is
disconnected from
the
check valve
or
when-
ever check valve failure
is
suspected. (A pump that
,
had
become inoperative and had shown indications
of
having exhaust gases
in the
pump would indicate
check valve failure)..
• Orally blow through
the
check valve (toward
air
manifold) then attempt
to
suck back through check
valve. Flow should only
be in one
direction (toward
the
air
manifold).
Replacement
• Disconnect pump outlet hose
at
check valve. Remove
check valve from
air
manifold, being careful not
to
bend
or
twist
air
manifold.
Mixture Control Valve
Inspection
• Check condition
and
routing
of all
lines especially
the signal line.
A
defective signal
or
outlet line will
cause malfunctioning
of the
mixture control valve.
• Disconnect pump
to
valve inlet hose
at
pump.
• Leaking valve will
be
indicated
by an air
gushing
noise coming from
the
hose. Place palm
of
hand over
hose; little
or no
pull with
a
gradual increase
is
normal.
If
immediate strong pull
is
felt
or air
noise
is heard, valve
is
defective
and
should
be
replaced.
• Open
and
close throttle rapidly.
Air
noise should
be
evident
and
then gradually decrease. Check
for
proper valve usage.
If
strong pull
is not
felt
im-.
mediately
or air
noise
is not
present, valve
is not
functioning properly and should be replaced.
•
A
noisy valve should be replaced.
Replacement
• Disconnect
the
signal line,
air
inlet
and air
outlet
hoses then remove
the
valve.
• Install
new
valve
and
connect
air
outlet,
air
inlet
and signal line hoses.
CAUTION: Mixture control valves, though
similar
in
appearance
are
designed
to
meet
particular requirements
of
various engines,
therefore,
be
sure
to
install
the
correct valve.
CHEVROLET CHASSIS SERVICE MANUAL
Page 324 of 659
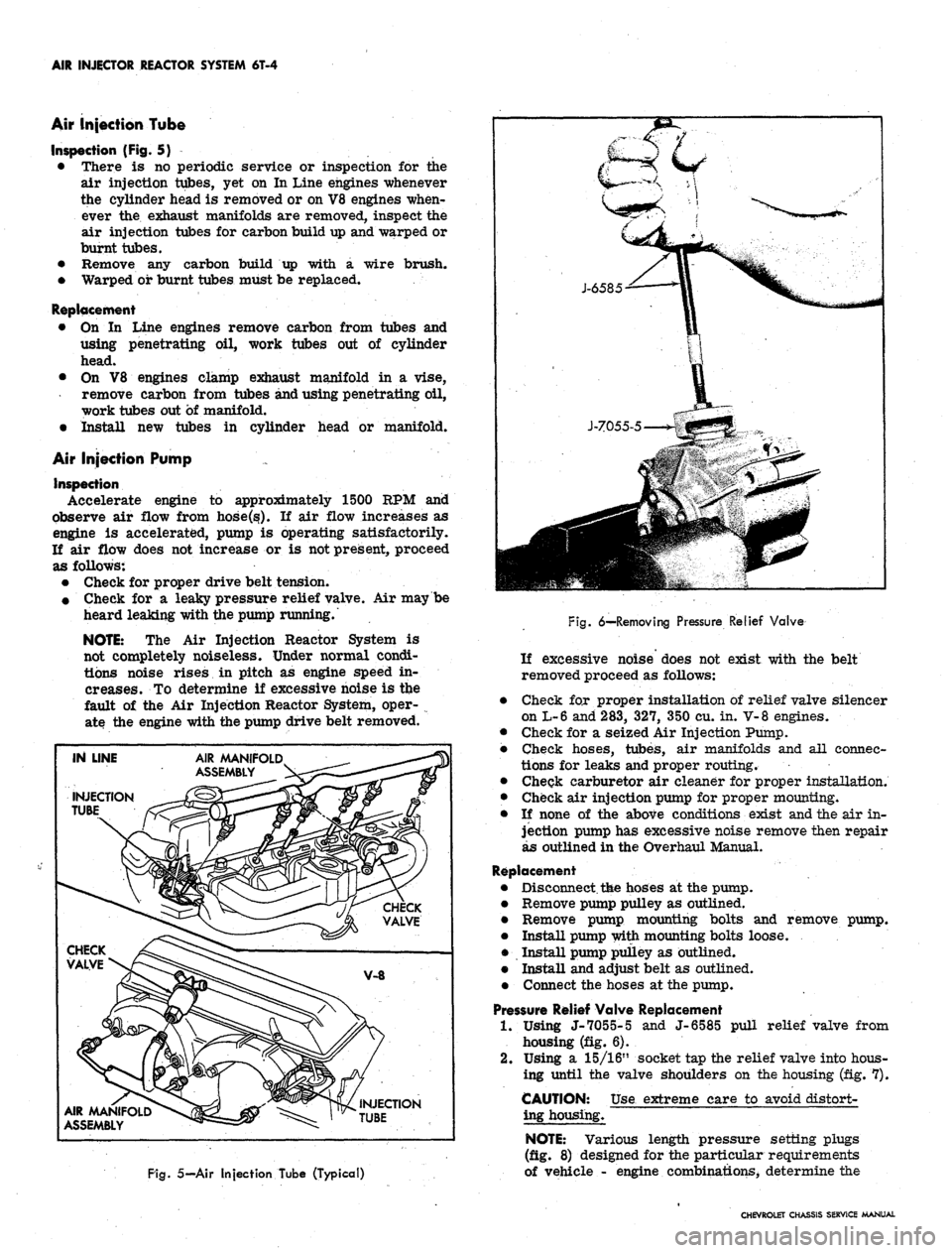
AIR INJECTOR REACTOR SYSTEM 6T-4
Air injection Tube
Inspection (Fig. 5)
• There is no periodic service or inspection for the
air injection tubes, yet on In Line engines whenever
the cylinder head is removed or on V8 engines when-
ever the exhaust manifolds are removed, inspect the
air injection tubes for carbon build up and warped or
burnt tubes.
• Remove any carbon build up with a wire brush.
• Warped or burnt tubes must be replaced.
Replacement
• On In Line engines remove carbon from tubes and
using penetrating oil, work tubes out of cylinder
head.
• On V8 engines clamp exhaust manifold in a vise,
remove carbon from tubes and using penetrating oil,
work tubes out of manifold.
• Install new tubes in cylinder head or manifold.
Air Injection Pump
Inspection
Accelerate engine to approximately 1500 KPM and
observe air flow from hose.Osf). If air flow increases as
engine is accelerated, pump is operating satisfactorily.
If air flow does not increase or is not present, proceed
as follows:
• Check for proper drive belt tension.
• Check for a leaky pressure relief valve. Air maybe
heard leaking with the pump running.
NOTE:
The Air Injection Reactor System is
not completely noiseless. Under normal condi-
tions noise rises in pitch as engine speed in-
creases. To determine if excessive noise is the
fault of the Air Injection Reactor System, oper-
ate the engine with the pump drive belt removed.
IN LINE
INJECTION
si
AIR AAANIFOLD^
ASSEMBLY
AIR MANIFOLD
ASSEMBLY ^S
~jk
VALVE
V-8
ff
>yi
INJECTION
» TUBE
' ,•
Fig.
5—Air Injection Tube (Typical)
Fig.
6-HRemoving Pressure Relief Valve
If excessive noise does not exist with the belt
removed proceed as follows:
Check for proper installation of relief valve silencer
on L-6 and 283, 327, 350 cu. in. V-8 engines.
Check for a seized Air Injection Pump.
Check hoses, tubes, air manifolds and all connec-
tions for leaks and proper routing.
Cheqk carburetor air cleaner for proper installation.
Check air injection pump for proper mounting.
If none of the above conditions exist and the air in-
jection pump has excessive noise remove then repair
as outlined in the Overhaul Manual.
Replacement
Disconnect,
t&e
hoses at the pump.
Remove pump pulley as outlined.
Remove pump mounting bolts and remove pump.
Install pump with mounting bolts loose.
Install pump pulley as outlined.
Install and adjust belt as outlined.
Connect the hoses at the pump.
Pressure Relief Valve Replacement
1.
Using J-7055-5 and J-6585 pull relief valve from
housing (fig. 6).
2.
Using a 15/16" socket tap the relief valve into hous-
ing until the valve shoulders on the housing (fig. 7).
CAUTION: Use extreme care to avoid distort-
ing housing.
NOTE:
Various length pressure setting plugs
(fig. 8) designed for the particular requirements
of vehicle - engine combinations, determine the
CHEVROLET CHASSIS SERVICE MANUAL
Page 325 of 659
AIR INJECTOR REACTOR SYSTEM 6T-5
LEGS LOCK
ON
INSIDE SURFACE
/
BLUE-194,
230
SILVER-250
GREEN-283
BLACK-327,
350, 396 & 427
PRESSURE
RELIEF VALVE
Fig.
7—Installing Pressure Relief Valve
Fig.
8—Pressure Setting Plug
pressure required to open the relief valve. For
identification, the pressure setting plugs are
color coded. To remove the pressure setting
plug, carefully unlock legs from inside surface
of relief valve with a small screw, driver. To
install the pressure setting plug, carefully push
into relief valve until legs lock. If a pressure
setting plug is to be reused be sure leg angles
are sufficient for the pressure setting plug to
lock in place.
SPECIAL TOOLS
J-7055-5
J-6585
J-21844
J-21058
Fig.
9-Special Tools
CHEVROLET CHASSIS SERVICE MANUAL
Page 326 of 659
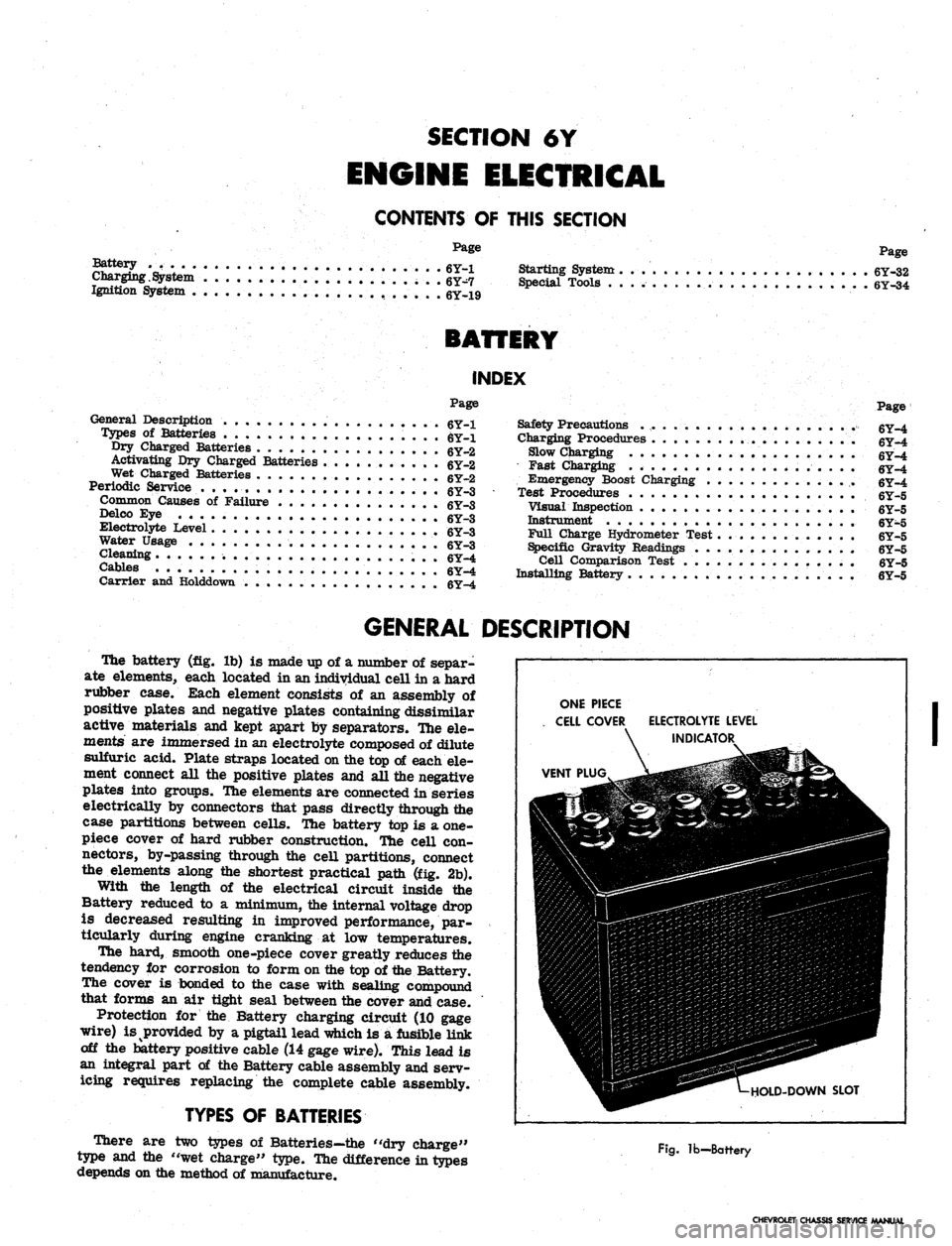
SECTION 6Y
ENGINE ELECTRICAL
CONTENTS
OF
THIS SECTION
Page
System
6Y-19
6Y-32
6Y-34
BATTERY
INDEX
Page
General Description 6Y_i
Types of Batteries 6Y-1
Dry Charged Batteries 6Y-2
Activating Dry Charged Batteries 6Y-2
Wet Charged Batteries 6Y 2
Periodic Service 6Y-3
Common Causes of Failure 6Y-3
Delco Eye 6Y_3
Electrolyte Level
AY
3
Water Usage ] \ 6Y_3
Cleaning 6Y_4
Cables 6Y_4
Carrier and Holddown 6Y-4
Page
Safety Precautions 6Y-4
Charging Procedures . . gY_4
Slow Charging gY-4
Fast Charging . * 6Y-4
Emergency Boost Charging 6Y-4
Test Procedures QY-S
Visual Inspection 6Y-5
Instrument 6Y-5
Full Charge Hydrometer Test. 6Y-5
Specific Gravity Readings 6Y-5
Cell Comparison Test . 6Y-5
Installing Battery 6Y-5
GENERAL DESCRIPTION
The battery (fig. lb) is made up of a number of separ-
ate elements, each located in an individual cell in a hard
rubber case. Each element consists of an assembly of
positive plates and negative plates containing dissimilar
active materials and kept apart by separators. Hie ele-
ments are immersed in an electrolyte composed of dilute
sulfuric acid. Plate straps located on the top of each ele-
ment connect all the positive plates and all the negative
plates into groups. The elements are connected in series
electrically by connectors that pass directly through the
case partitions between cells. The battery top is a one-
piece cover of hard rubber construction. Tfte cell con-
nectors, by-passing through the cell partitions, connect
the elements along the shortest practical path (fig. 2b).
With the length of the electrical circuit inside the
Battery reduced to a minimum, the internal voltage drop
is decreased resulting in improved performance, par-
ticularly during engine cranking at low temperatures.
The hard, smooth one-piece cover greatly reduces the
tendency for corrosion to form on the top of the Battery.
The cover is bonded to the case with sealing compound
that forms an air tight seal between the cover and case.
Protection for the Battery charging circuit (10 gage
wire) is provided by a pigtail lead which is a fusible Hnk
off the battery positive cable (14 gage wire). This lead is
an integral part of the Battery cable assembly and serv-
icing requires replacing the complete cable assembly.
TYPES
OF
BATTERIES
There are two types of Batteries—the "dry charge"
type and the "wet charge" type. The difference in types
depends on the method of manufacture.
ONE PIECE
CELL COVER
VENT PLUG
ELECTROLYTE LEVEL
INDICATOR
HOLD-DOWN SLOT
Fig.
lb—Battery
CHEVROLET CHASSIS SERVICE MANUAL
Page 327 of 659
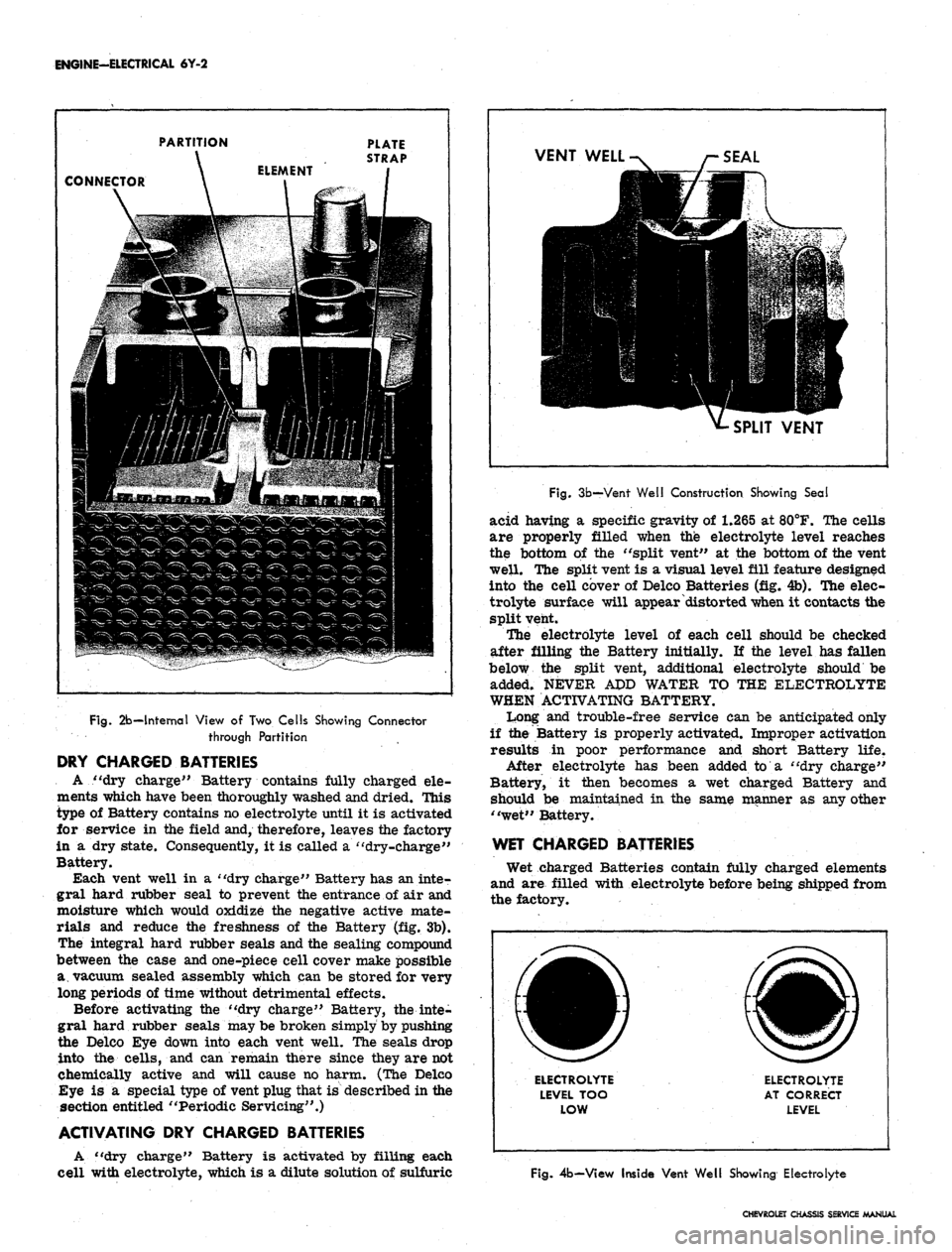
ENGINE-ELECTRICAL 6Y-2
PARTITION
PLATE
STRAP
CONNECTOR
Fig.
2b—Internal View of Two Cells Showing Connector
through Partition
DRY CHARGED BATTERIES
A "dry charge" Battery contains fully charged ele-
ments which have been thoroughly washed and dried. Hiis
type of Battery contains no electrolyte until it is activated
for service in the field and, therefore, leaves the factory
in a dry state. Consequently, it is called a "dry-charge"
Battery.
Each vent well in a "dry charge" Battery has an inte-
gral hard rubber seal to prevent the entrance of air and
moisture which would oxidize the negative active mate-
rials and reduce the freshness of the Battery (fig. 3b).
The integral hard rubber seals and the sealing compound
between the case and one-piece cell cover make possible
a. vacuum sealed assembly which can be stored for very
long periods of time without detrimental effects.
Before activating the "dry charge" Battery, the inte-
gral hard rubber seals may be broken simply by pushing
the Delco Eye down into each vent well. The seals drop
into the cells, and can remain there since they are not
chemically active and will cause no harm. (The Delco
Eye is a special type of vent plug that is described in the
section entitled "Periodic Servicing".)
ACTIVATING DRY CHARGED BATTERIES
A "dry charge" Battery is activated by filling each
cell with electrolyte, which is a dilute solution of sulfuric
VENT WELL
SEAL
SPLIT VENT
Fig. 3b—Vent Well Construction Showing Seal
acid having a specific gravity of 1.265 at 80°F. The cells
are properly filled when the electrolyte level reaches
the bottom of the "split vent" at the bottom of the vent
well. The split vent is a visual level fill feature designed
into the cell cover of Delco Batteries (fig. 4b). The elec-
trolyte surface will appear distorted when it contacts the
split vent.
The electrolyte level of each cell should be checked
after filling the Battery initially. If the level has fallen
below the split vent, additional electrolyte should be
added. NEVER APD WATER TO THE ELECTROLYTE
WHEN ACTIVATING BATTERY.
Ir?ong and trouble-free service can be anticipated only
if the Battery is properly activated. Improper activation
results in poor performance and short Battery life.
After electrolyte has been added to a "dry charge"
Battery, it then becomes a wet charged Battery and
should be maintained in the same manner as any other
"wet" Battery.
WET CHARGED BATTERIES
Wet charged Batteries contain fully charged elements
and are filled with electrolyte before being shipped from
the factory.
ELECTROLYTE
LEVEL TOO
LOW
ELECTROLYTE
AT CORRECT
LEVEL
Fig. 4b-View Inside Vent Well Showing Electrolyte
CHEVROLET CHASSIS SERVICE MANUAL
Page 328 of 659
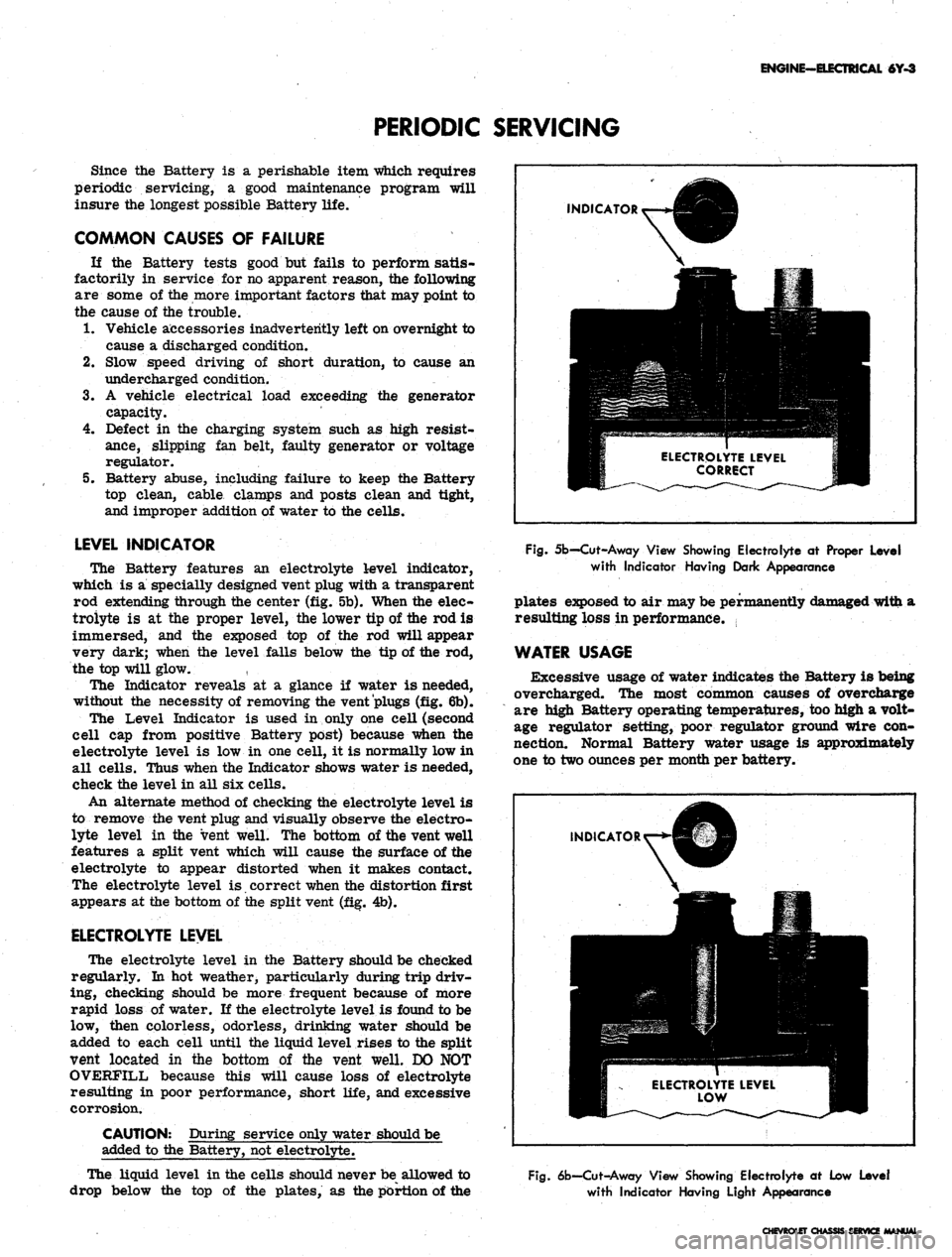
ENGINE-EIECTRICAI 6Y-3
PERIODIC SERVICING
Since the Battery is a perishable item which requires
periodic servicing, a good maintenance program will
insure the longest possible Battery life.
COMMON CAUSES OF FAILURE
If the Battery tests good but fails to perform satis-
factorily in service for no apparent reason, the following
are some of the more important factors that may point to
the cause of the trouble.
1.
Vehicle accessories inadvertently left on overnight to
cause a discharged condition.
2.
Slow speed driving of short duration, to cause an
3.
undercharged condition.
A vehicle
capacity.
electrical load exceeding the generator
4.
Defect in the charging system such as high resist-
ance, slipping fan belt, faulty generator or voltage
regulator.
5. Battery abuse, including failure to keep the Battery
top clean, cable clamps and posts clean and tight,
and improper addition of water to the cells.
LEVEL INDICATOR
The Battery features an electrolyte level indicator,
which is a specially designed vent plug with a transparent
rod extending through the center (fig. 5b). When the elec-
trolyte is at the proper level, the lower tip of the rod is
immersed, and the exposed top of the rod will appear
very dark; when the level falls below the tip of the rod,
the top will glow. ,
The Indicator reveals at a glance if water is needed,
without the necessity of removing the vent plugs (fig. 6b).
The Level Indicator is used in only one cell (second
cell cap from positive Battery post) because when the
electrolyte level is low in one cell, it is normally low in
all cells. Thus when the Indicator shows water is needed,
check the level in all six cells.
An alternate method of checking the electrolyte level is
to remove the vent plug and visually observe the electro-
lyte level in the vent well. The bottom of the vent well
features a split vent which will cause the surface of the
electrolyte to appear distorted when it makes contact.
The electrolyte level is. correct when the distortion first
appears at the bottom of the split vent (fig. 4b).
ELECTROLYTE LEVEL
The electrolyte level in the Battery should be checked
regularly. In hot weather, particularly during trip driv-
ing, checking should be more frequent because of more
rapid loss of water. If the electrolyte level is found to be
low, then colorless, odorless, drinking water should be
added to each cell until the liquid level rises to the split
vent located in the bottom of the vent well. DO NOT
OVERFILL because this will cause loss of electrolyte
resulting in poor performance, short life, and excessive
corrosion.
CAUTION: During service only water should be
added to the Battery, not electrolyte.
The liquid level in the cells should never be allowed to
drop below the top of the plates, as the portion of the
INDICATOR
ELECTROLYTE LEVEL
CORRECT
Fig.
5b—Cut-Away View Showing Electrolyte at Proper Level
with Indicator Having Dark Appearance
plates exposed to air may be permanently damaged with a
resulting loss in performance.
WATER USAGE
Excessive usage of water indicates the Battery is being
overcharged. The most common causes of overcharge
are high Battery operating temperatures, too high a volt-
age regulator setting, poor regulator ground wire con-
nection. Normal Battery water usage is approximately
one to two ounces per month per battery.
INDICATOR
Fig.
6b—Cut-Away View Showing Electrolyte at Low Level
with Indicator Having Light Appearance
CHASSIS SBtVKZ MANUAL