Page 385 of 659
CLUTCH
AND
TRANSMISSIONS
7-26
TUBE
&
LEVER
ASM (B)
SELECTOR
PLATE
TRANSMISSION
LEVER
(A)
TUBE
B
LEVER
(B)
VIEW B
BRACKET
ROD
(C)
VIEW A
Fig.
3PG - Chevelle Shift Linkage Adjustments
BUSHING
VIEW
A
NUT{D)
ROD{C)
VIEWD
1.00MIN.
NOTE:
DIMENSION MUST
BE
MAINTAINED
WITH
TRANS.
IN"NEUTRAL" POSITION.
TUBE
&
LEVER ASM (&}
VIEWB
Fig.
4PG - Chevy II Shift Linkage Adjustments
CHEVROLET CHASSIS SERVICE MANUAL
Page 386 of 659
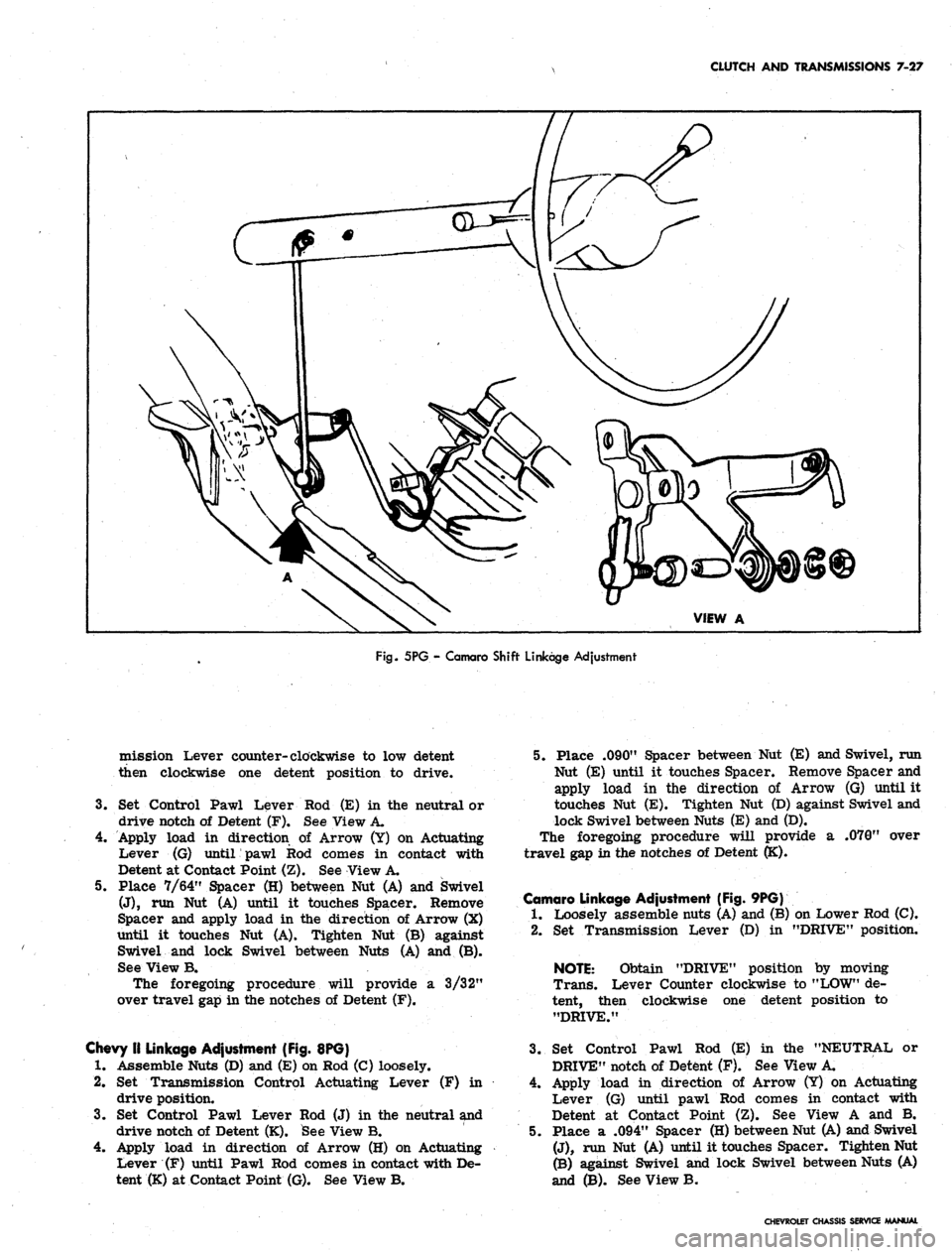
CLUTCH AND TRANSMISSIONS 7-27
Fig.
5PG - Camaro Shift Linkage Adjustment
mission Lever counter-clockwise to low detent
then clockwise one detent position to drive.
3.
Set Control Pawl Lever
drive notch of Detent (F).
Rod (E) in the neutral or
See View A.
4.
Apply load in direction of Arrow (Y) on Actuating
Lever (G) until pawl Rod comes in contact with
Detent at Contact Point (Z). See View A.
5. Place 7/64" Spacer (H) between Nut (A) and Swivel
(J),
run Nut (A) until it touches Spacer. Remove
Spacer and apply load in the direction of Arrow (X)
until it touches Nut (A). Tighten Nut (B) against
Swivel and lock Swivel between Nuts (A) and (B).
See View B.
The foregoing procedure will provide a 3/32"
over travel gap in the notches of Detent (F).
Chevy II Linkage Adjustment (Fig. 8PG)
1.
Assemble Nuts (D) and (E) on Rod (C) loosely.
2.
Set Transmission Control Actuating Lever (F) in
drive position.
3.
Set Control Pawl Lever Rod (J) in the neutral and
drive notch of Detent (K). See View B.
4.
Apply load in direction of Arrow (H) on Actuating
Lever (F) until Pawl Rod comes in contact with De-
tent (K) at Contact Point (G). See View B.
5. Place .090" Spacer between Nut (E) and Swivel, run
Nut (E) until it touches Spacer. Remove Spacer and
apply load in the direction of Arrow (G) until it
touches Nut (E). Tighten Nut (D) against Swivel and
lock Swivel between Nuts (E) and (D).
The foregoing procedure will provide a .070" over
travel gap in the notches of Detent (K).
Camaro Linkage Adjustment (Fig. 9PG)
1.
Loosely assemble nuts (A) and (B) on Lower Rod (C).
2.
Set Transmission Lever (D) in "DRIVE" position.
NOTE:
Obtain "DRIVE" position by moving
Trans. Lever Counter clockwise to "LOW" de-
tent, then clockwise one detent position to
"DRIVE."
3.
Set Control Pawl Rod (E) in the "NEUTRAL or
DRIVE" notch of Detent (F). See View A.
4.
Apply load in direction of Arrow (Y) on Actuating
Lever (G) until pawl Rod comes in contact with
Detent at Contact Point (Z). See View A and B.
5. Place a .094" Spacer (H) between Nut (A) and Swivel
(J),
run Nut (A) until it touches Spacer. Tighten Nut
(B) against Swivel and lock Swivel between Nuts (A)
and (B). See View B.
CHEVROLET CHASSIS SERVICE MANUAL
Page 387 of 659
CLUTCH AND TRANSMISSIONS
7-28
.PAWL
ROD (E)
DETENT
(F)
LOAD(Y)
NUT (A)
Fig.
6PG
-
Chevrolet Floor Shift Linkage Adjustment
DRIVE
POSITION
// CONTACT
POINT
Z
v ACTUATING
4./
VIEW
A
\ LEVER
G
ACTUATING LEVER (F)
LOAD{G)
1
ROD
(QSyYi-LOAD
(H)
NUT (D)
/tl—SPACER
/Hh-09
SWIVEL'
VIEW
A
#^
POINT
OF
V
CONTACT
(G)\\
A
DETENT (K)H^
¥
VUULPAWL
VIEW
B
y DETENT (K)
Fig.
7PG
-
Chevelle Floor Shift Linkage Adjustment
Fig.
SPG
-
Chevy
II
Floor Shift Linkage Adjustment
CHEVROLET CHASSIS SERVICE MANUAL
Page 388 of 659
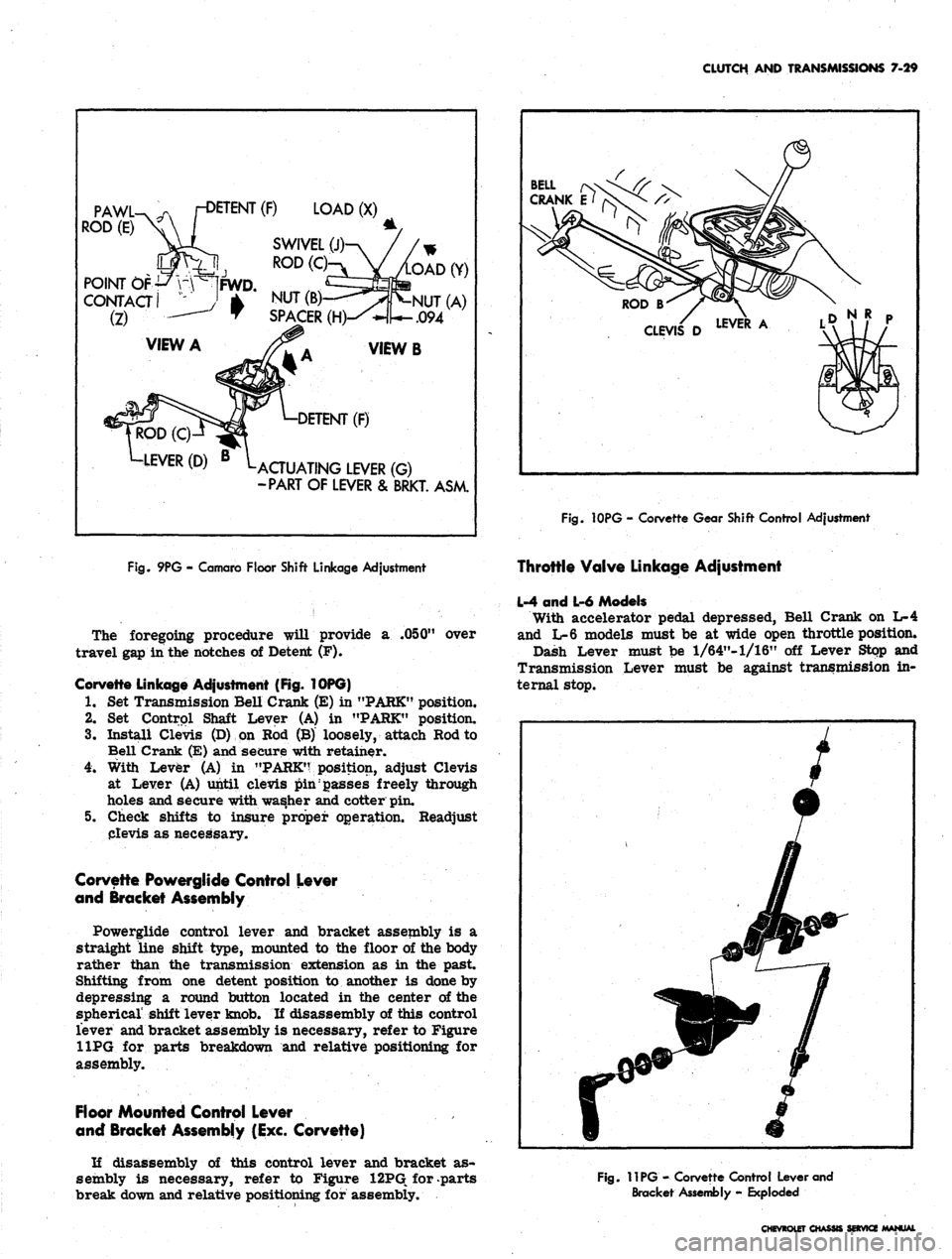
CLUTCH AND TRANSMISSIONS 7-29
ROD
(E)~X\
or
POINT OF-i-7V
CONTACT
i
(2)
-
VIEW
^ROD
(C
LLEVER
r-D
I
j
.——j
A
{
(D)
ETENT
FWD.
B
\_
(?) LOAD (X)
SWIVEL (J)-\
ROD(CK V
NUT (B)-—-^
SPACER
(H)-^
K
/ / n
/LOAD (Y)
I^-NUT
(A)
k-.O94
/^A
VIEWB
L-DETENT
(F)
AQUATING LEVER
-PART
OF
LEVER
&
(G)
BRKT. ASM.
Fig.
10PG - Corvette Gear Shift Control Adjustment
Fig.
9PG - Comoro Floor Shift Linkage Adjustment
The foregoing procedure will provide a .050" over
travel gap in the notches of Detent (F).
Corvette Linkage Adjustment (Fig. 10PG)
1.
Set Transmission Bell Crank (E) in "PARK" position.
2.
Set Control Shaft Lever (A) in "PARK" position.
3.
Install Clevis (D) on Rod (B) loosely, attach Rod to
Bell Crank (E) and secure with retainer.
4.
With Lever (A) in "PARK'? position, adjust Clevis
at Lever (A) until clevis pin passes freely through
holes and secure with washer and cotter pin.
5. Check shifts to insure proper operation. Readjust
Clevis as necessary.
Corvette Powerglide Control Lever
and Bracket Assembly
Powerglide control lever and bracket assembly is a
straight line shift type, mounted to the floor of the body
rather than the transmission extension as in the past.
Shifting from one detent position to another is done by
depressing a round button located in the center of the
spherical' shift lever knob. If disassembly of this control
lever and bracket assembly is necessary, refer to Figure
11PG for parts breakdown and relative positioning for
assembly.
Floor Mounted Control Lever
and Bracket Assembly (Exc. Corvette)
If disassembly of this control lever and bracket as-
sembly is necessary, refer to Figure 12PG for parts
break down and relative positioning for assembly.
Throttle Valve Linkage Adjustment
L-4 and L-6 Models
With accelerator pedal depressed, Bell Crank on L-4
and L-6 models must be at wide open throttle position.
Dash Lever must be 1/64"-1/16" off Lever Stop and
Transmission Lever must be against transmission in-
ternal stop.
Fig.
11PG - Corvette Control Lever and
Bracket Assembly - Exploded
CHEVtOLET CHASSIS SERVICE
Page 389 of 659
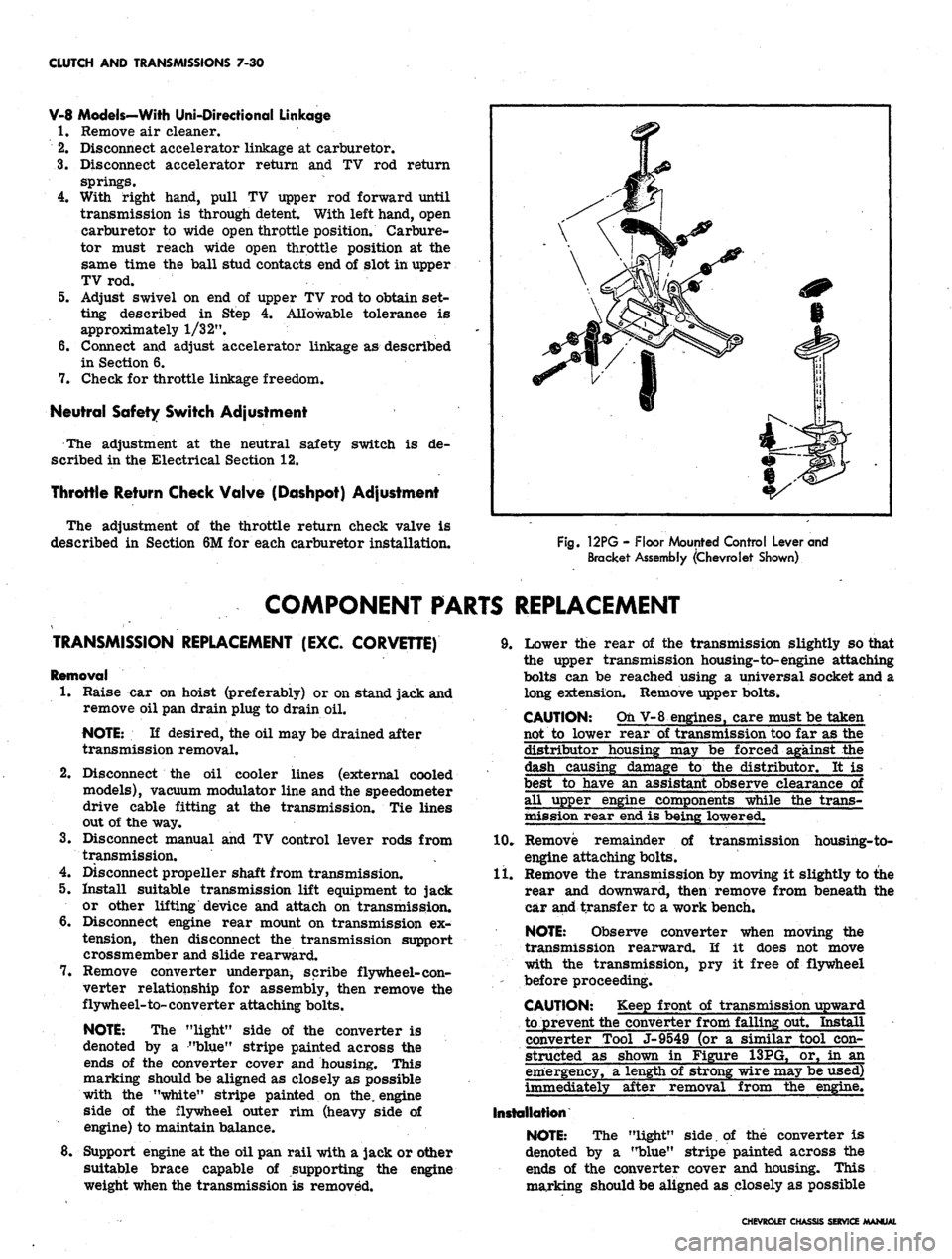
CLUTCH AND TRANSMISSIONS
7*30
V-8 Models-With Uni-Directional Linkage
1.
Remove air cleaner.
2.
Disconnect accelerator linkage at carburetor.
3.
Disconnect accelerator return and TV rod return
springs.
4.
With right hand, pull TV upper rod forward until
transmission is through detent. With left hand, open
carburetor to wide open throttle position. Carbure-
tor must reach wide open throttle position at the
same time the ball stud contacts end of slot in upper
TV rod.
5. Adjust swivel on end of upper TV rod to obtain set-
ting described in Step 4. Allowable tolerance is
approximately 1/32".
6. Connect and adjust accelerator linkage as described
in Section 6.
7. Check for throttle linkage freedom.
Neutral Safety Switch Adjustment
The adjustment at the neutral safety switch is de-
scribed in the Electrical Section 12.
Throttle Return Check Valve (Dashpot) Adjustment
The adjustment of the throttle return check valve is
described in Section 6M for each carburetor installation.
Fig.
12PG - Floor Mounted Control Lever and
Bracket Assembly (Chevrolet Shown)
COMPONENT PARTS REPLACEMENT
TRANSMISSION REPLACEMENT (EXC. CORVETTE)
Removal
1.
Raise car on hoist (preferably) or on stand jack and
remove oil pan drain plug to drain oil.
NOTE:
If desired, the oil may be drained after
transmission removal.
2.
Disconnect the oil cooler lines (external cooled
models), vacuum modulator line and the speedometer
drive cable fitting at the transmission. Tie lines
out of the way.
3.
Disconnect manual and TV control lever rods from
transmission.
4.
Disconnect propeller shaft from transmission.
5. Install suitable transmission lift equipment to jack
or other lifting device and attach on transmission.
6. Disconnect engine rear mount on transmission ex-
tension, then disconnect the transmission support
crossmember and slide rearward.
7. Remove converter underpan, scribe flywheel-con-
verter relationship for assembly, then remove the
flywheel-to-converter attaching bolts.
NOTE:
The "light" side of the converter is
denoted by a "blue" stripe painted across the
ends of the converter cover and housing. This
marking should be aligned as closely as possible
with the "white" stripe painted on the. engine
side of the flywheel outer rim (heavy side of
engine) to maintain balance.
8. Support engine at the oil pan rail with a jack or other
suitable brace capable of supporting the engine
weight when the transmission is removed.
9. Lower the rear of the transmission slightly so that
the upper transmission housing-to-engine attaching
bolts can be reached using a universal socket and a
long extension. Remove upper bolts.
CAUTION: Oh V-8 engines, care must be taken
not to lower rear of transmission too far as the
distributor housing may be forced against the
dash causing damage to the distributor. It is
best to have an assistant observe clearance of
all upper engine components while the trans-
mission rear end is being lowered.
10.
Remove remainder of transmission housing-to-
engine attaching bolts.
11.
Remove the transmission by moving it slightly to the
rear and downward, then remove from beneath the
car and transfer to a work bench.
NOTE:
Observe converter when moving the
transmission rearward. If it does not move
with the transmission, pry it free of flywheel
before proceeding.
CAUTION: Keep front of transmission upward
to prevent the converter from falling out. Install
converter Tool J-9549 (or a similar tool con-
structed as shown in Figure 13PG, or, in an
emergency, a length of strong wire may be used)
immediately after removal from the engine.
Installation
NOTE:
The "light" side, of the converter is
denoted by a "blue" stripe painted across the
ends of the converter cover and housing. This
marking should be aligned as closely as possible
CHEVROLET CHASSIS SERVICE MANUAL
Page 390 of 659
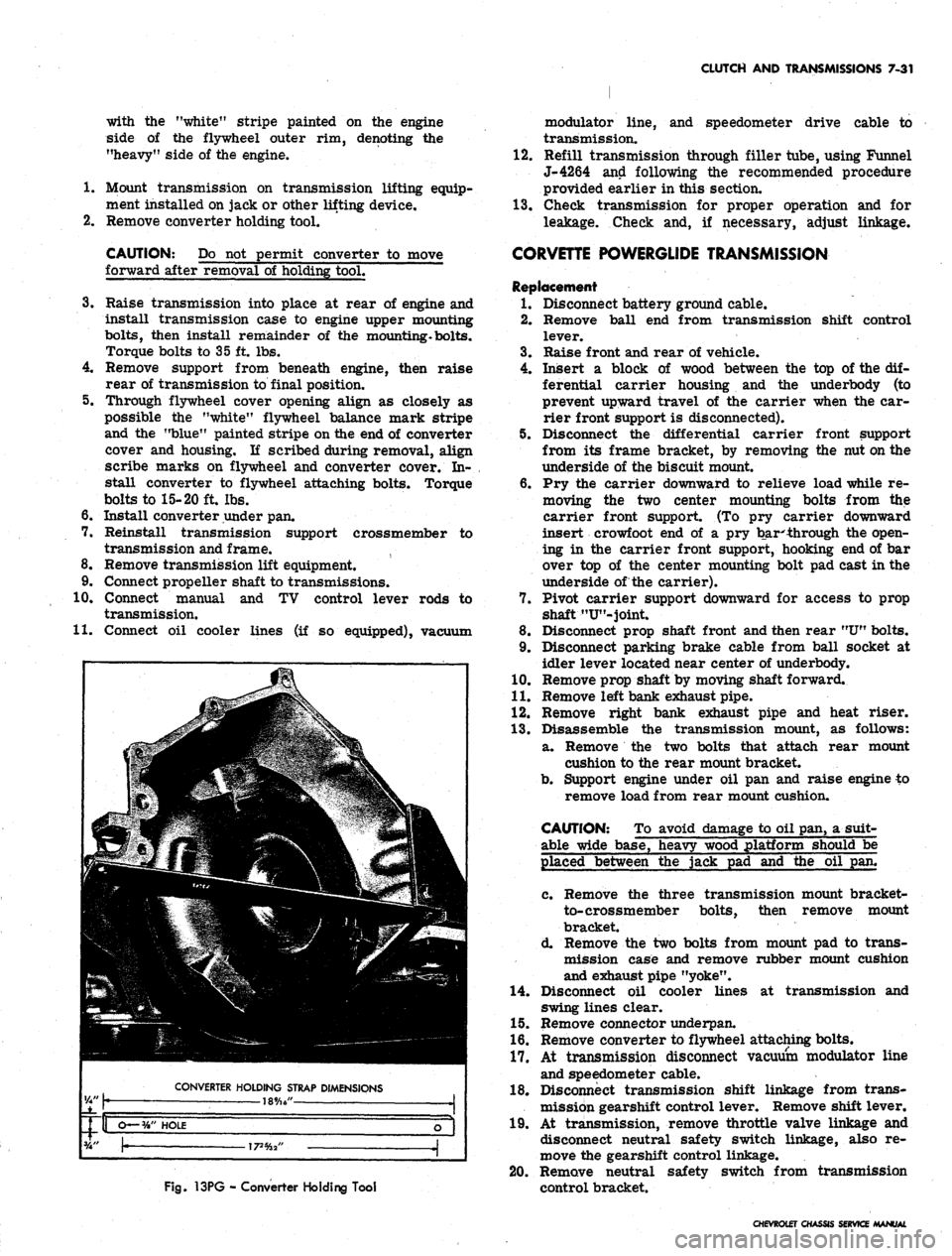
CLUTCH AND TRANSMISSIONS 7-31
with the "white" stripe painted on the engine
side of the flywheel outer rim, denoting the
"heavy" side of the engine.
1.
Mount transmission on transmission lifting equip-
ment installed on jack or other lifting device.
2.
Remove converter holding tool.
CAUTION: Do not permit converter to move
forward after removal of holding tool.
3.
Raise transmission into place at rear of engine and
install transmission case to engine upper mounting
bolts,
then install remainder of the mounting*bolts.
Torque bolts to 35 ft. lbs.
4.
Remove support from beneath engine, then raise
rear of transmission to final position.
5. Through flywheel cover opening align as closely as
possible the "white" flywheel balance mark stripe
and the "blue" painted stripe on the end of converter
cover and housing. If scribed during removal, align
scribe marks on flywheel and converter cover. In-
stall converter to flywheel attaching bolts. Torque
bolts to 15-20 ft. lbs.
6. Install converter under pan.
7. Reinstall transmission support crossmember to
transmission and frame.
8. Remove transmission lift equipment.
9. Connect propeller shaft to transmissions.
10.
Connect manual and TV control lever rods to
transmission.
11.
Connect oil cooler lines (if so equipped), vacuum
Fig.
13PG - Converter Holding Tool
modulato:* line, and speedometer drive cable to
transmission.
12.
Refill transmission through filler tube, using Funnel
J-4264 and following the recommended procedure
provided earlier in this section.
13.
Check transmission for proper operation and for
leakage. Check and, if necessary, adjust linkage.
CORVETTE POWERGLIDE TRANSMISSION
Replacement
1.
Disconnect battery ground cable.
2.
Remove ball end from transmission shift control
lever.
3.
Raise front and rear of vehicle.
4.
Insert a block of wood between the top of the dif-
ferential carrier housing and the underbody (to
prevent upward travel of the carrier when the car-
rier front support is disconnected).
5. Disconnect the differential carrier front support
from its frame bracket, by removing the nut on the
underside of the biscuit mount.
6. Pry the carrier downward to relieve load while re-
moving the two center mounting bolts from the
carrier front support. (To pry carrier downward
insert crowfoot end of a pry bar**hrough the open-
ing in the carrier front support, hooking end of bar
over top of the center mounting bolt pad cast in the
underside of the carrier).
7. Pivot carrier support downward for access to prop
shaft "U"-joint.
8. Disconnect prop shaft front and then rear
"U"
bolts.
9. Disconnect parking brake cable from ball socket at
idler lever located near center of underbody.
10.
Remove prop shaft by moving shaft forward.
11.
Remove left bank exhaust pipe.
12.
Remove right bank exhaust pipe and heat riser.
13.
Disassemble the transmission mount, as follows:
a. Remove the two bolts that attach rear mount
cushion to the rear mount bracket.
b.
Support engine under oil pan and raise engine to
remove load from rear mount cushion.
CAUTION: To avoid damage to oil pan, a suit-
able wide base, heavy wood platform should be
placed between the jack pad and the oil pan.
c. Remove the three transmission mount bracket-
to-crossmember bolts, then remove mount
bracket.
d. Remove the two bolts from mount pad to trans-
mission case and remove rubber mount cushion
and exhaust pipe "yoke".
14.
Disconnect oil cooler lines at transmission and
swing lines clear.
15.
Remove connector underpan.
16.
Remove converter to flywheel attaching bolts.
17.
At transmission disconnect vacuum modulator line
and speedometer cable.
18.
Disconnect transmission shift linkage from trans-
mission gearshift control lever. Remove shift lever.
19.
At transmission, remove throttle valve linkage and
disconnect neutral safety switch linkage, also re-
move the gearshift control linkage.
20.
Remove neutral safety switch from transmission
control bracket.
CHEVROLET CHASSIS SERVICE
Page 391 of 659
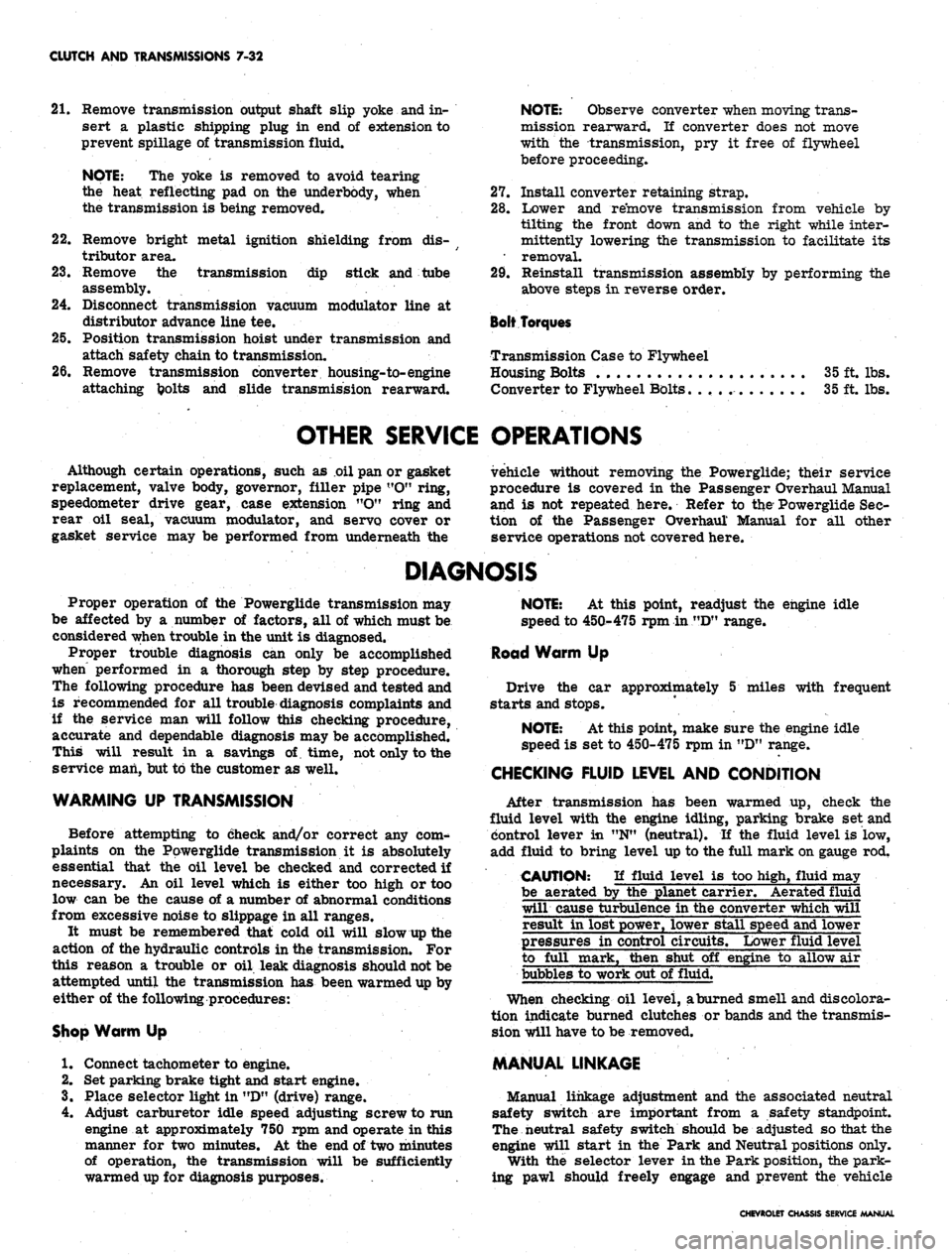
CLUTCH AND TRANSMISSIONS 7-32
21.
Remove transmission output shaft slip yoke and in-
sert a plastic shipping plug in end of extension to
prevent spillage of transmission fluid.
NOTE:
The yoke is removed to avoid tearing
the heat reflecting pad on the underbbdy, when
the transmission is being removed.
22.
Remove bright metal ignition shielding from dis-
tributor area.
23.
Remove the transmission dip stick and tube
assembly.
24.
Disconnect transmission vacuum modulator line at
distributor advance line tee.
25.
Position transmission hoist under transmission and
attach safety chain to transmission.
26.
Remove transmission converter housing-to-engine
attaching foolts and slide transmission rearward.
NOTE:
Observe converter when moving trans-
mission rearward. If converter does not move
with the transmission, pry it free of flywheel
before proceeding.
27.
Install converter retaining strap.
28.
Lower and remove transmission from vehicle by
tilting the front down and to the right while inter-
mittently lowering the transmission to facilitate its
• removal.
29.
Reinstall transmission assembly by performing the
above steps in reverse order.
Bolt Torques
Transmission Case to Flywheel
Housing Bolts 35 ft. lbs.
Converter to Flywheel Bolts. . , . . 35 ft. lbs.
OTHER SERVICE OPERATIONS
Although certain operations, such as oil pan or gasket
replacement, valve body, governor, filler pipe "O" ring,
speedometer drive gear, case extension "0" ring and
rear oil seal, vacuum modulator, and servo cover or
gasket service may be performed from underneath the
vehicle without removing the Powerglide; their service
procedure is covered in the Passenger Overhaul Manual
and is not repeated here. Refer to the- Powerglide Sec-
tion of the Passenger Overhaul Manual for all other
service operations not covered here.
DIAGNOSIS
Proper operation of the Powerglide transmission may
be affected by a number of factors, all of which must be
considered when trouble in the unit is diagnosed.
Proper trouble diagnosis can only be accomplished
when performed in a thorough step by step procedure.
The following procedure has been devised and tested and
is recommended for all trouble diagnosis complaints and
if the service man will follow this checking procedure,
accurate and dependable diagnosis may be accomplished.
This will result in a savings of time, not only to the
service man, but to the customer as well.
WARMING UP TRANSMISSION
Before attempting to check and/or correct any com-
plaints on the Powerglide transmission it is absolutely
essential that the oil level be checked and corrected if
necessary. An oil level which is either too high or too
low can be the cause of a number of abnormal conditions
from excessive noise to slippage in all ranges.
It must be remembered that cold oil will slow up the
action of the hydraulic controls in the transmission. For
this reason a trouble or oil leak diagnosis should not be
attempted until the transmission has been warmed up by
either of the following procedures:
Shop Warm Up
1.
Connect tachometer to engine.
2.
Set parking brake tight and start engine.
3.
Place selector light in
"D"
(drive) range.
4.
Adjust carburetor idle speed adjusting screw to run
engine at approximately 750 rpm and operate in this
manner for two minutes. At the end of two minutes
of operation, the transmission will be sufficiently
warmed up for diagnosis purposes.
NOTE:
At this point, readjust the engine idle
speed to 450-475 rpm in
"D"
range.
Road Warm Up
Drive the car approximately 5 miles with frequent
starts and stops.
NOTE:
At this point, make sure the engine idle
speed is set to 450-475 rpm in
"D"
range.
CHECKING FLUID LEVEL AND CONDITION
After transmission has been warmed up, check the
fluid level with the engine idling, parking brake set and
control lever in "N" (neutral). If the fluid level is low,
add fluid to bring level up to the full mark on gauge rod,
CAUTION: If fluid level is too high, fluid may
be aerated by the planet carrier. Aerated fluid
will cause turbulence in the converter which will
result in lost power, lower stall speed and lower
pressures in control circuits. Lower fluid level
to full mark, then shut off engine to allow air
bubbles to work out of fluid.
When checking oil level, aburned smell and discolora-
tion indicate burned clutches or bands and the transmis-
sion will have to be removed.
MANUAL LINKAGE
Manual linkage adjustment and the associated neutral
safety switch are important from a safety standpoint.
The neutral safety switch should be adjusted so that the
engine will start in the Park and Neutral positions only.
With the selector lever in the Park position, the park-
ing pawl should freely engage and prevent the vehicle
CHEVROLET CHASSIS SERVICE MANUAL
Page 392 of 659

CLUTCH AND TRANSMISSIONS 7-33
from rolling. The pointer on the indicator quadrant
should line up properly with the range indicators in all
ranges.
OIL LEAKS
Before attempting to correct an oil leak, the actual
source of the leak must be determined. In many cases
the source of the leak can be deceiving due to "wind flow1 f
around the engine and transmission.
The suspected area should be wiped clean of all oil
before inspecting for the source of the leak. Red dye is
used in the transmission oil at the assembly plant and
will indicate if the oil leak is from the transmission.
The use of a "black light"* to identify the oil at the
source of leak is also helpful. Comparing the oil from
the leak to that on the engine or transmission dip stick
(when viewed by black light) will determine the source
of the leak.
Oil leaks around the engine and transmission are gen-
erally carried toward the rear of the car by the air
stream. For example, a transmission "oil filter tube
to case leak" will sometimes appear as a leak at the
rear of the transmission. In determining the source of
an oil leak it is most helpful to keep the engine running.
The mating surfaces of servo cover, converter housing,
transmission case and transmission case extension
should be carefully examined for signs of leakage. The
vacuum modulator must also be checked to insure that
the diaphragm has not ruptured as this would allow trans-
mission oil to be drawn into the intake manifold. Us-
ually, the exhaust will be excessively smoky if the
diaphragm ruptures due to the transmission oil added to
the combustion. The transmission case extension rear
oil seal should also be checked. All test plugs should be
checked to make sure that they are tight and that there
is no sign of leakage at these points. The converter
underpan should also be removed. Any appreciable quan-
tity of oil in this area would indicate leakage at the pump
square seal ring, pump seal assembly, or pump bolt
sealing washers.
BASIC PRESSURE CHECKS
Four basic pressure checks are used for diagnosis and
operational checks for the Aluminum Powerglide trans-
mission. All checks should be made only after thoroughly
warming up the transmission.
• Wide Open Throttle Upshift Pressure.
• Idle Pressure in "Drive" Range.
• Manual "Low" Range Pressure.
• "Drive" Range Overrun (Coast) Pressure.
It is not recommended that stall tests be conducted
which would result in engine vacuum falling below 10" Hg.
Pressure gauge hose connections should be made at
the low servo apply (main line) test point (fig. 14PG).
Run the gauge line into the driving compartment by
pushing aside the mast jacket seal. The line out of the
way of the drivers feet and connect to pressure gauge
J-21867.
• Wide Open Throttle Upshift Pressure Check
Refer to the pressure check chart for upshift pressure
SERVO APPLY
PRESSURE
Fig.
14PG - Pressure Test Plug
points as indicated on the lower servo apply (main line)
gauge.
• Idle Pressure in "Drive" Range
In addition tp the oil pressure gauges, a vacuum gauge
is needed for this check.
With the parking brake applied and the shift selector
lever in "Drive", low servo apply (main line) pressure
should be as shown on the pressure check chart.
If pressures are not within these ranges, the following
items should be checked for oil circuit leakage:
1.
Pressure regulator valve stuck.
2.
Vacuum modulator valve stuck.
3.
Hydraulic modulator valve stuck.
4.
Leak at low servo piston ring (between ring and
bore).
5.
Leak at low servo piston rod (between rod and bore).
6. Leak at valve body to case gasket.
7.
Leak at valve body gaskets.
8. Front pump clearances.
9. Check passages in transmission case for porosity.
• Manual "Low" Range Pressure Check
Connect a tachometer, apply the parking brake, place
the selector lever in "Low" range, and adjust the engine
speed to 1000 rpm with the car stationary.
Low servo apply (main line) pressure should be as
shown on the pressure check chart.
Pressures not within this range can indicate the fol-
lowing possibilities:
1.
Partially plugged oil suction screen.
2.
Broken or damaged ring low servo.
CHEVROLET CHASSIS SERVICE MANUAL