Page 617 of 659
ACCESSORIES
15-8
BROWN
BRAKE
SWITCH
+12V *
BLACK
CONNECTOR
AT FUSE BLOCK
CRUISE POSITION
BUTTON RELEASED
ENGAGE POSITION
BUTTON PARTIALLY DEPRESSED^ N. ENOAOi SWITCH
TRIM POSITION N. N. I
BUHON FULLY DEPRESSED. \ ^
BROWN
BLUE
ENGAGE SWITCH
CONFIGURATION
BLACK
BLUE
REGULATOR
- SOLENOID COIL
(5 a RESISTANCE)
9 BLACK
BLUE
REGULATOR
Fig.
10 - Wiring Diagram
Replacement
1.
Insert the switch into the turn signal knob, push the
retaining ring firmly against the switch, and push the
operating button onto the switch plunger. " .
SERVO
Service
—
H the Servo unit is found to be defective, re-
placement is required. Note the condition of the hoses
and replace any which are cracked or deteriorated.
CHEVROLET CHASSIS SERVICE MANUAL
Page 618 of 659
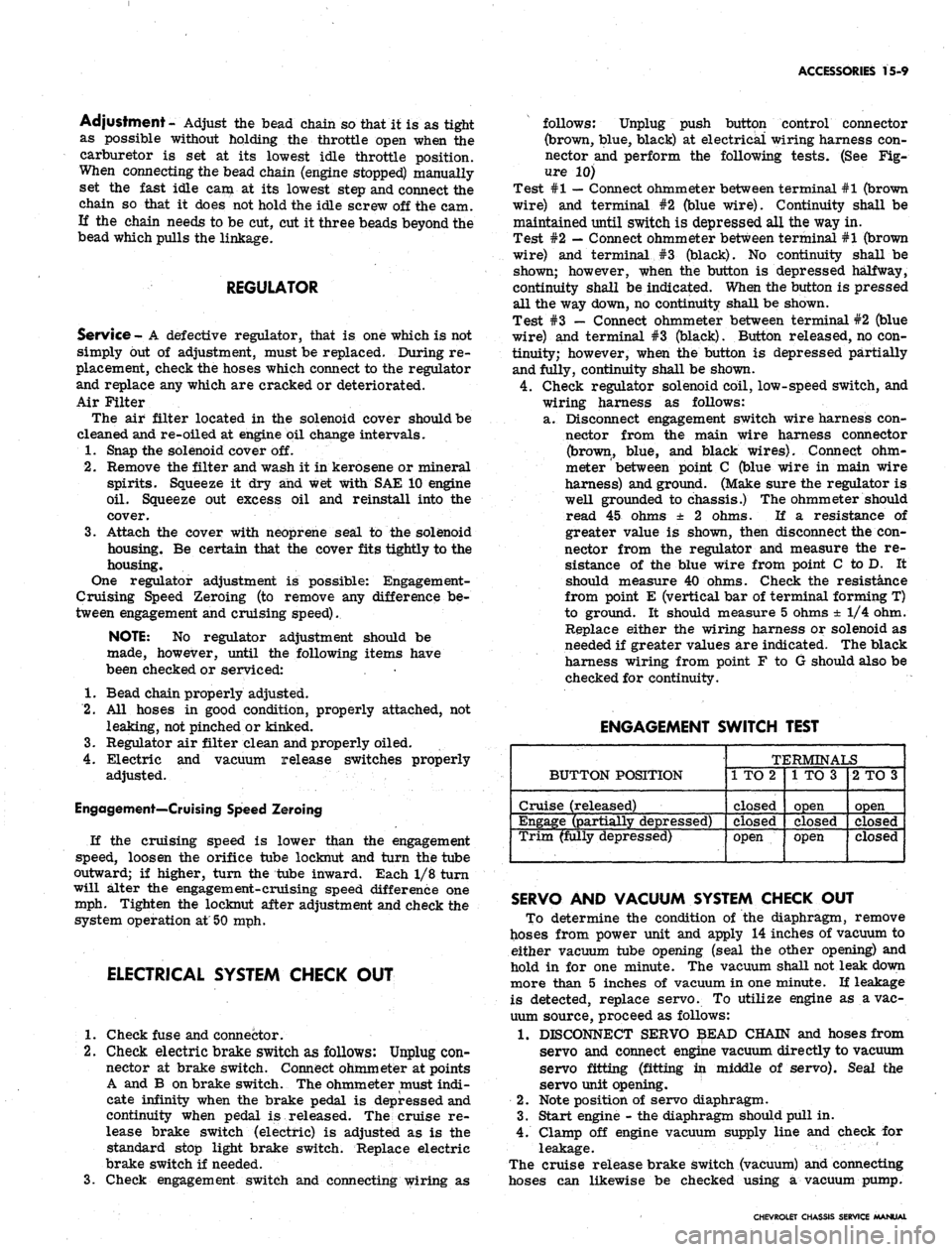
ACCESSORIES 15-9
Adjustment- Adjust the bead chain so that it is as tight
as possible without holding the throttle open when the
carburetor is set at its lowest idle throttle position.
When connecting the bead chain (engine stopped) manually
set the fast idle cam at its lowest step and connect the
chain so that it does not hold the idle screw off the cam.
If the chain needs to be cut, cut it three beads beyond the
bead which pulls the linkage.
REGULATOR
Service - A defective regulator, that is one which is not
simply out of adjustment, must be replaced. During re-
placement, check the hoses which connect to the regulator
and replace any which are cracked or deteriorated.
Air Filter
The air filter located in the solenoid cover should be
cleaned and re-oiled at engine oil change intervals.
1.
Snap the solenoid cover off.
2.
Remove the filter and wash it in kerosene or mineral
spirits. Squeeze it dry and wet with SAE 10 engine
oil.
Squeeze out excess oil and reinstall into the
cover.
3.
Attach the cover with neoprene seal to the solenoid
housing. Be certain that the cover fits tightly to the
housing.
One regulator adjustment is possible: Engagement-
Cruising Speed Zeroing (to remove any difference be-
tween engagement and cruising speed).
NOTE:
No regulator adjustment should be
made, however, until the following items have
been checked or serviced:
1.
Bead chain properly adjusted.
2.
All hoses in good condition, properly attached, not
leaking, not pinched or kinked.
3.
Regulator air filter clean and properly oiled.
4.
Electric and vacuum release switches properly
adjusted.
Engagement—Cruising Speed Zeroing
If the cruising speed is lower than the engagement
speed, loosen the orifice tube locknut and turn the tube
outward; if higher, turn the tube inward. Each 1/8 turn
will alter the engagement-cruising speed difference one
mph. Tighten the locknut after adjustment and check the
system operation at 50 mph.
ELECTRICAL SYSTEM CHECK OUT
1.
Check fuse and connector.
2.
Check electric brake switch as follows: Unplug con-
nector at brake switch. Connect ohmmeter at points
A and B on brake switch. The ohmmeter must indi-
cate infinity when the brake pedal is depressed and
continuity when pedal is released. The cruise re-
lease brake switch (electric) is adjusted as is the
standard stop light brake switch. Replace electric
brake switch if needed.
3.
Check engagement switch and connecting wiring as
follows: Unplug push button control connector
(brown, blue, black) at electrical wiring harness con-
nector and perform the following tests. (See Fig-
ure 10)
Test #1
—
Connect ohmmeter between terminal #1 (brown
wire) and terminal #2 (blue wire). Continuity shall be
maintained until switch is depressed all the way in.
Test #2
—
Connect ohmmeter between terminal #1 (brown
wire) and terminal #3 (black). No continuity shall be
shown; however, when the button is depressed halfway,
continuity shall be indicated. When the button is pressed
all the way down, no continuity shall be shown.
Test #3 — Connect ohmmeter between terminal #2 (blue
wire) and terminal #3 (black). Button released, no con-
tinuity; however, when the button is depressed partially
and fully, continuity shall be shown.
4.
Check regulator solenoid coil, low-speed switch, and
wiring harness as follows:
a. Disconnect engagement switch wire harness con-
nector from the main wire harness connector
(brown, blue, and black wires). Connect ohm-
meter
'
between point C (blue wire in main wire
harness) and ground. (Make sure the regulator is
well grounded to chassis.) The ohmmeter should
read 45 ohms ± 2 ohms. If a resistance of
greater value is shown, then disconnect the con-
nector from the regulator and measure the re-
sistance of the blue wire from point C to D. It
should measure 40 ohms. Check the resistance
from point E (vertical bar of terminal forming T)
to ground. It should measure 5 ohms ± 1/4 ohm.
Replace either the wiring harness or solenoid as
needed if greater values are indicated. The black
harness wiring from point F to G should also be
checked for continuity.
ENGAGEMENT SWITCH TEST
BUTTON POSITION
Cruise (released)
Engage (partially depressed)
Trim (fully depressed)
TERMINALS
1 TO 2
closed
Closed
open
1 TO 3
open
closed
open
2 TO 3
open
closed
closed
SERVO AND VACUUM SYSTEM CHECK OUT
To determine the condition of the diaphragm, remove
hoses from power unit and apply 14 inches of vacuum to
either vacuum tube opening (seal the other opening) and
hold in for one minute. The vacuum shall not leak down
more than 5 inches of vacuum in one minute. If leakage
is detected, replace servo. To utilize engine as a vac-
uum source, proceed as follows:
1.
DISCONNECT SERVO $EAD CHAIN and hoses from
servo and connect engine vacuum directly to vacuum
servo fitting (fitting in middle of servo). Seal the
servo unit opening.
2.
Note position of servo diaphragm.
3.
Start engine - the diaphragm should pull in.
4.
Clamp off engine vacuum supply line and check for
leakage. '
The cruise release brake switch (vacuum) and connecting
hoses can likewise be checked using a vacuum pump.
CHEVROLET CHASSIS SERVICE MANUAL
Page 619 of 659
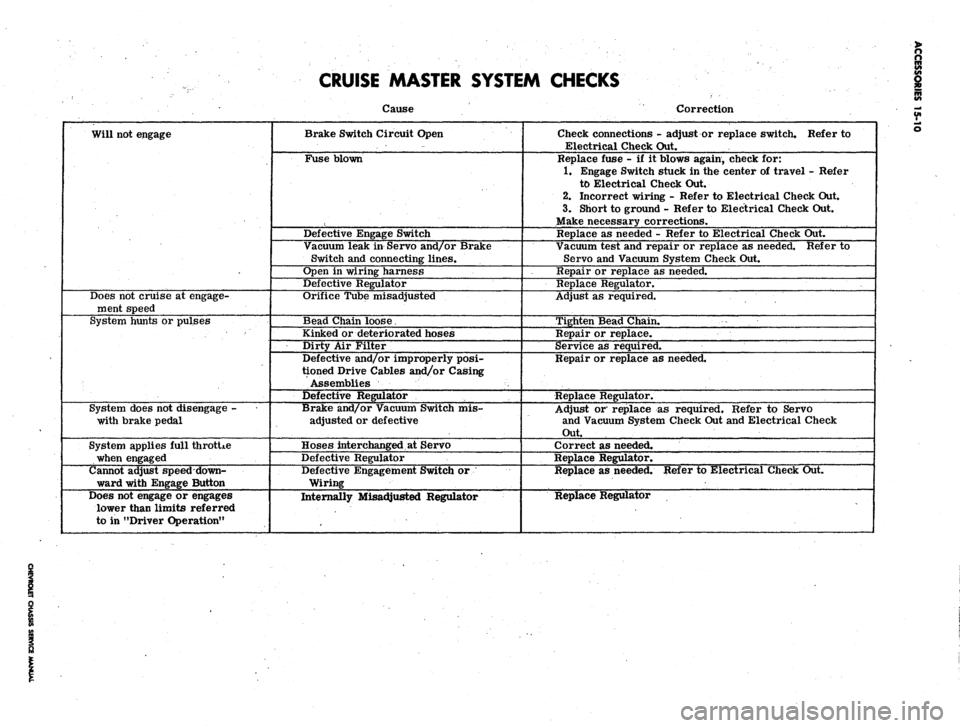
CRUISE MASTER SYSTEM CHECKS
Will not engage
Does not cruise at engage-
ment speed
System hunts or pulses
System does not disengage -
with brake pedal
System applies full throtUe
when engaged
Cannot adjust speed down-
ward with Engage Button
Does not engage or engages
lower than limits referred
to in "Driver Operation"
Cause
Brake Switch Circuit Open
Fuse blown
Defective Engage Switch
Vacuum leak in Servo and/or Brake
Switch and connecting lines.
Open in wiring harness
Defective Regulator
Orifice Tube misadjusted
Bead Chain loose.
Kinked or deteriorated hoses
Dirty Air Filter
Defective and/or improperly posi-
tioned Drive Cables and/or Casing
Assemblies
Defective Regulator
Brake and/or Vacuum Switch mis-
adjusted or defective
Hoses interchanged at Servo
Defective Regulator
Defective Engagement Switch or
Wiring
Internally Misadjusted Regulator
Correction
Check connections - adjust or replace switch. Refer to
Electrical Check Out.
Replace fuse - if it blows again, check for:
1.
Engage Switch stuck in the center of travel - Refer
to Electrical Check Out.
2.
Incorrect wiring - Refer to Electrical Check Out.
3.
Short to ground - Refer to Electrical Check Out.
Make necessary corrections.
Replace as needed - Refer to Electrical Check Out.
Vacuum test and repair or replace as needed. Refer to
Servo and Vacuum System Check Out.
Repair or replace as needed.
Replace Regulator.
Adjust as required.
Tighten Bead Chain.
Repair or replace.
Service as required.
Repair or replace as needed.
Replace Regulator.
Adjust or replace as required. Refer to Servo
and Vacuum System Check Out and Electrical Check
Out.
Correct as needed.
Replace Regulator.
Replace as needed. Refer to Electrical Check Out.
Replace Regulator
Page 620 of 659
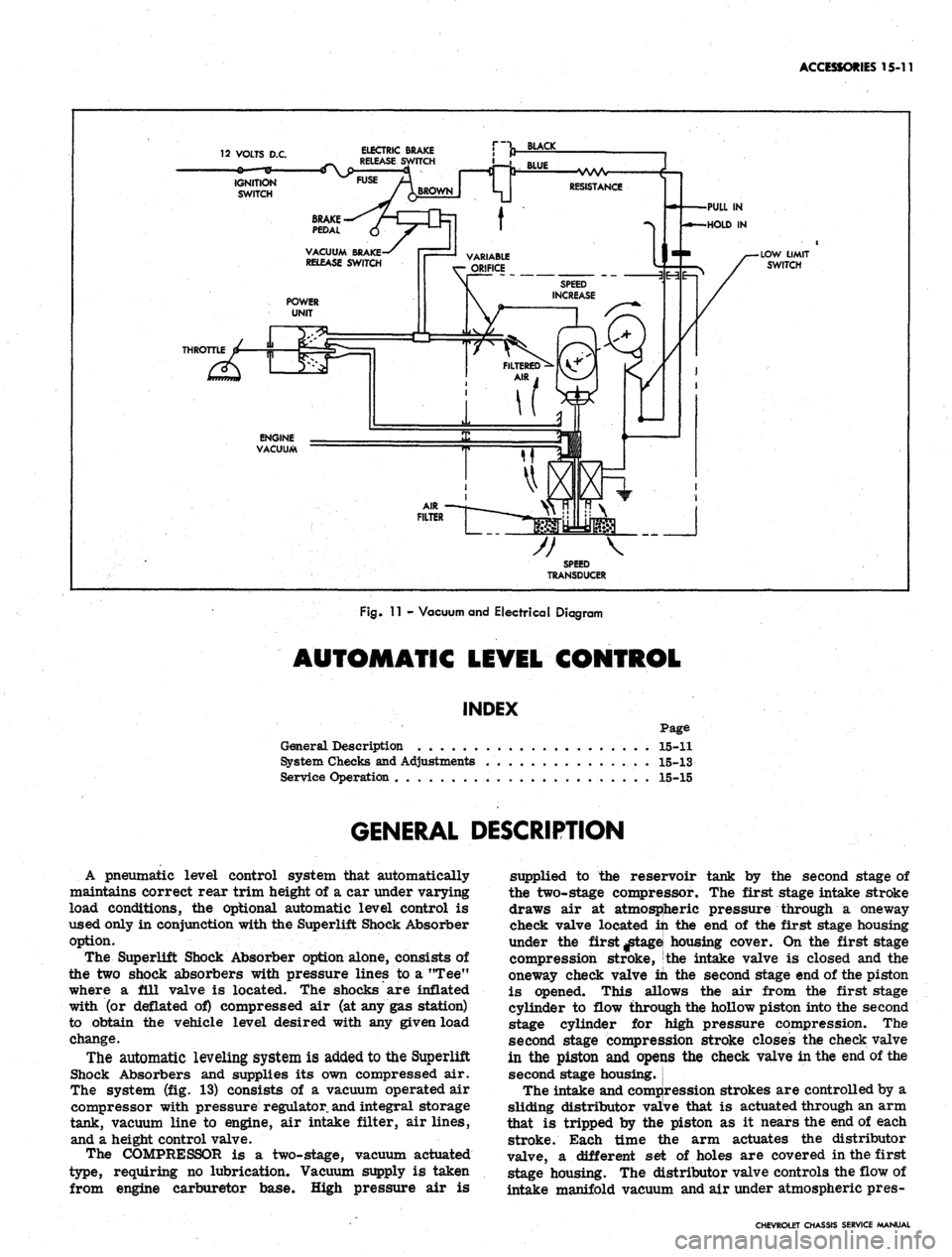
ACCESSORIES 15-11
12 VOLTS D.C.
ELECTRIC BRAKE
RELEASE
IGNITION
SWITCH
ENGINE
VACUUM
TRANSDUCER
Fig.
11 - Vacuum and Electrical Diagram
AUTOMATIC LEVEL CONTROL
INDEX
Page
General Description . . 15-11
System Checks and Adjustments 15-13
Service Operation . 15-15
GENERAL DESCRIPTION
A pneumatic level control system that automatically
maintains correct rear trim height of a car under varying
load conditions, the optional automatic level control is
used only in conjunction with the Superlift Shock Absorber
option.
The Superlift Shock Absorber option alone, consists of
the two shock absorbers with pressure lines to a "Tee"
where a ill valve is located, the shocks are inflated
with (or deflated of) compressed air (at any gas station)
to obtain the vehicle level desired with any given load
change.
The automatic leveling system is added to the Superlift
Shock Absorbers and supplies its own compressed air.
The system (fig. 13) consists of a vacuum operated air
compressor with pressure regulator,
and
integral storage
tank, vacuum line to engine, air intake filter, air lines,
and a height control valve.
The COMPRESSOR is a two-stage, vacuum actuated
type, requiring no lubrication. Vacuum supply is taken
from engine carburetor base. High pressure air is
supplied to the reservoir tank by the second stage of
the two-stage compressor. The first stage intake stroke
draws air at atmospheric pressure through a oneway
check valve located in the end of the first stage housing
under the first ^tagei housing cover. On the first stage
compression stroke, the intake valve is closed and the
oneway check valve in the second stage end of the piston
is opened. This allows the air from the first stage
cylinder to flow through the hollow piston into the second
stage cylinder for jhigh pressure compression. The
second stage compression stroke closes the check valve
in the piston and opeijis the check valve in the end of the
second stage housing.
The intake and compression strokes are controlled by a
sliding distributor valive that is actuated through an arm
that is tripped by the piston as it nears the end of each
stroke. Each time the arm actuates the distributor
valve, a different set of holes are covered in the first
stage housing. The distributor valve controls the flow of
intake manifold vacuum and air under atmospheric pres-
CHEVROLET CHASSIS SERVICE MANUAL
Page 621 of 659
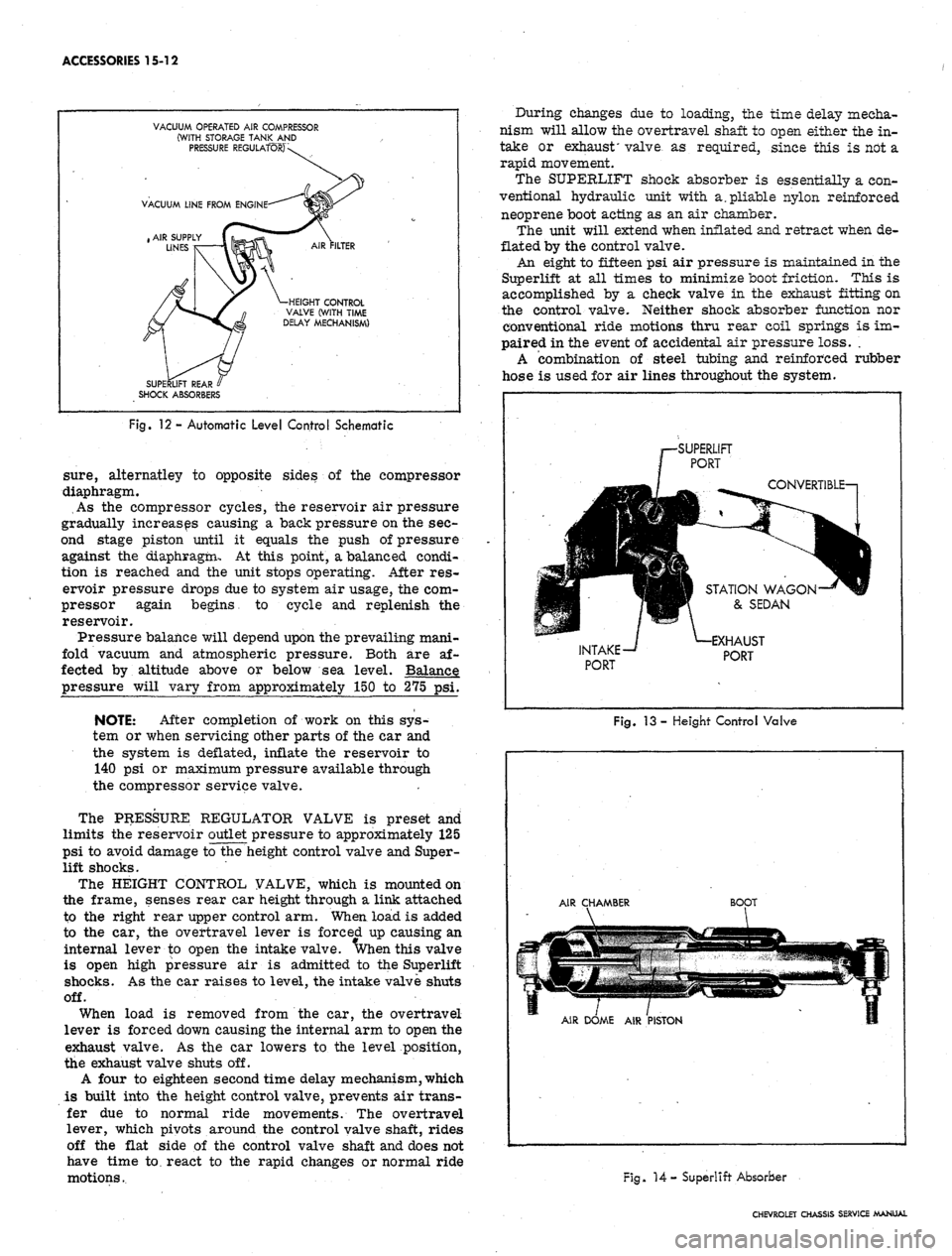
ACCESSORIES 15-12
VACUUM
(WIT
P
VACUUM Llh
, AIR SUPPt
LINES
t
SUPERLIFT F
SHOCK ABSO
OPERATED AIR COMPRESSOR
H STORAGE TANK AND
RESSURE REGULATORJV
\A
4E FROM ENG«NE^"^
/ \-HEIGHT CONTROL
•^-Z n VALVE (WITH TIME
^*
DELAY MECHANISM)
EAR II
RBERS
Fig.
12 - Automatic Level Control Schematic
sure,
alternatley to opposite sides of the compressor
diaphragm.
As the compressor cycles, the reservoir air pressure
gradually increases causing a back pressure on the sec-
ond stage piston until it equals the push of pressure
against the diaphragm- At this point, a balanced condi-
tion is reached and the unit stops operating. After res-
ervoir pressure drops due to system air usage, the com-
pressor again begins to cycle and replenish the
reservoir.
Pressure balance will depend upon the prevailing mani-
fold vacuum and atmospheric pressure. Both are af-
fected by altitude above or below sea level. Balance
pressure will vary from approximately 150 to 275 psi.
NOTE: After completion of work on this sys-
tem or when servicing other parts of the car and
the system is deflated, inflate the reservoir to
140 psi or maximum pressure available through
the compressor service valve.
The PRESSURE REGULATOR VALVE is preset and
limits the reservoir outlet pressure to approximately 125
psi to avoid damage to the height control valve and Super-
lift shocks.
The HEIGHT CONTROL VALVE, which is mounted on
the frame, senses rear car height through a link attached
to the right rear upper control arm. When load is added
to the car, the overtravel lever is forced up causing an
internal lever to open the intake valve, when this valve
is open high pressure air is admitted to the Superlift
shocks. As the car raises to level, the intake valve shuts
off.
When load is removed from the car, the overtravel
lever is forced down causing the internal arm to open the
exhaust valve. As the car lowers to the level position,
the exhaust valve shuts off.
A four to eighteen second time delay mechanism, which
is built into the height control valve, prevents air trans-
fer due to normal ride movements. The overtravel
lever, which pivots around the control valve shaft, rides
off the flat side of the control valve shaft and does not
have time to. react to the rapid changes or normal ride
motions.
During changes due to loading, the time delay mecha-
nism will allow the overtravel shaft to open either the in-
take or exhaust' valve as required, since this is not a
rapid movement.
The SUPERLIFT shock absorber is essentially a con-
ventional hydraulic unit with a. pliable nylon reinforced
neoprene boot acting as an air chamber.
The unit will extend when inflated and retract when de-
flated by the control valve.
An eight to fifteen psi air pressure is maintained in the
Superlift at all times to minimize boot friction- This is
accomplished by a check valve in the exhaust fitting on
the control valve. Neither shock absorber function nor
conventional ride motions thru rear coil springs is im-
paired in the event of accidental air pressure loss. .
A combination of steel tubing and reinforced rubber
hose is used for air lines throughout the system.
-SUPERLIFT
PORT
STATION WAGON
& SEDAN
INTAKE
PORT
HAUST
PORT
Fig. 13 - Height Control Valve
AIR CHAMBER
BOOT
AIR DOME AIR PISTON
Fig. 14- Superlift Absorber
CHEVROLET CHASSIS SERVICE MANUAL
Page 622 of 659
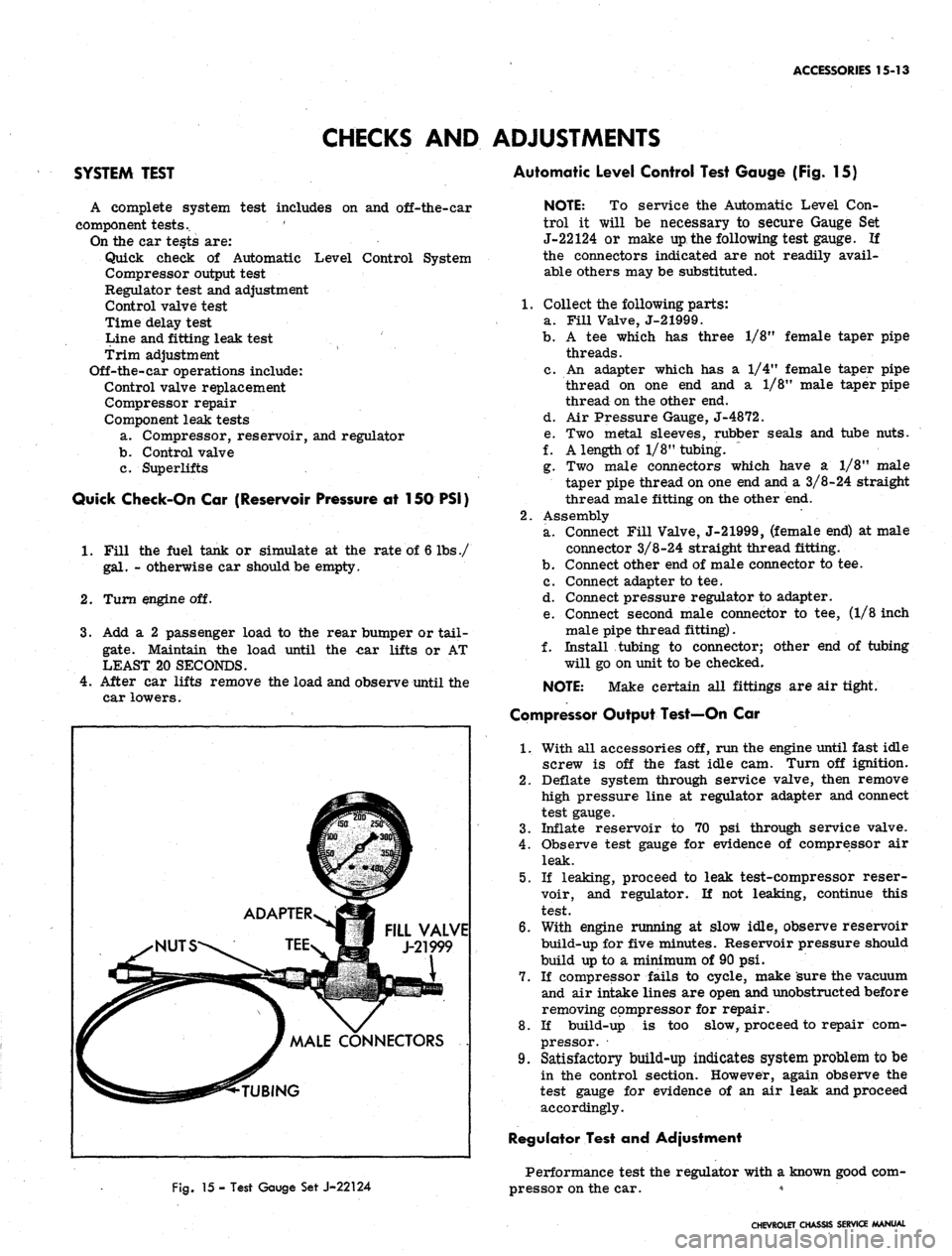
ACCESSORIES 15-13
SYSTEM TEST
CHECKS AND ADJUSTMENTS
Automatic Level Control Test Gauge (Fig. 15)
A complete system test includes on and off-the-car
component tests.. '
On the car tests are:
Quick check of Automatic Level Control System
Compressor output test
Regulator test and adjustment
Control valve test
Time delay test
Line and fitting leak test
Trim adjustment
Off-the-car operations include:
Control valve replacement
Compressor repair
Component leak tests
a. Compressor, reservoir, and regulator
b.
Control valve
c. Superlifts
Quick Check-On Car (Reservoir Pressure at 150 PSI)
1.
Fill the fuel tank or simulate at the rate of 6 lbs./
gal.
- otherwise car should be empty.
2.
Turn engine off.
3.
Add a 2 passenger load to the rear bumper or tail-
gate.
Maintain the load until the -car lifts or AT
LEAST 20 SECONDS.
4.
After car lifts remove the load and observe until the
car lowers.
FILL VALVE
J-21999
CONNECTORS
Fig.
15 - Test Gauge Set J-22124
NOTE: To service the Automatic Level Con-
trol it will be necessary to secure Gauge Set
J-22124 or make up the following test gauge. If
the connectors indicated are not readily avail-
able others may be substituted.
1.
Collect the following parts:
a. Fill Valve, J-21999.
b.
A tee which has three 1/8M female taper pipe
threads.
c. An adapter which has a 1/4" female taper pipe
thread on one end and a 1/8" male taper pipe
thread on the other end.
d. Air Pressure Gauge, J-4872.
e. Two metal sleeves, rubber seals and tube nuts.
f. A length of 1/8" tubing. ~
g. Two male connectors which have a 1/8" male
taper pipe thread on one end and a 3/8-24 straight
thread male fitting on the other end.
2.
Assembly
a. Connect Fill Valve, J-21999, (female end) at male
connector 3/8-24 straight thread fitting.
b.
Connect other end of male connector to tee.
c. Connect adapter to tee.
d. Connect pressure regulator to adapter.
e. Connect second male connector to tee, (1/8 inch
male pipe thread fitting).
f. Install tubing to connector; other end of tubing
will go on unit to be checked.
NOTE:
Make certain all fittings are air tight.
Compressor Output Test—On Car
1.
With all accessories off, run the engine until fast idle
screw is off the fast idle cam. Turn off ignition.
2.
Deflate system through service valve, then remove
high pressure line at regulator adapter and connect
test gauge.
3.
Inflate reservoir to 70 psi through service valve.
4.
Observe test gauge for evidence of compressor air
leak.
5.
If leaking, proceed to leak test-compressor reser-
voir, and regulator. If not leaking, continue this
test.
6. With engine running at slow idle, observe reservoir
build-up for five minutes. Reservoir pressure should
build up to a minimum of 90 psi.
7.
If compressor fails to cycle, make sure the vacuum
and air intake lines are open and unobstructed before
removing compressor for repair.
8. If build-up is too slow, proceed to repair com-
pressor.
9. Satisfactory build-up indicates system problem to be
in the control section. However, again observe the
test gauge for evidence of an air leak and proceed
accordingly.
Regulator Test and Adjustment
Performance test the regulator with a known good com-
pressor on the car. *
CHEVROLET CHASSIS SERVICE MANUAL
Page 623 of 659
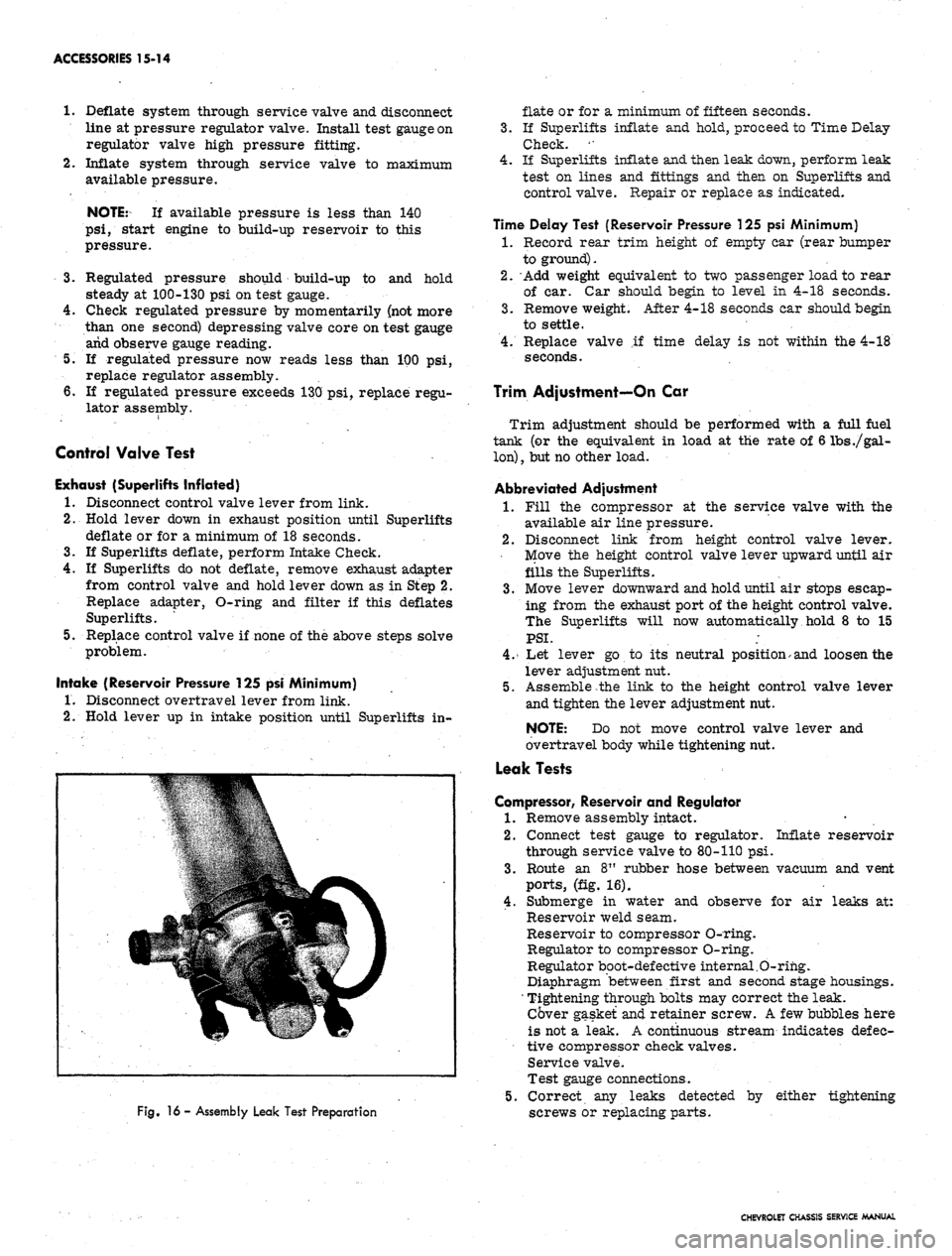
ACCESSORIES 15-14
Deflate system through service valve and disconnect
line at pressure regulator valve. Install test gauge on
regulator valve high pressure fitting.
Inflate system through service valve to maximum
available pressure.
NOTE: If available pressure is less than 140
psi,
start engine to build-up reservoir to this
pressure.
Regulated pressure should build-up to and hold
steady at 100-130 psi on test gauge.
Check regulated pressure by momentarily (not more
than one second) depressing valve core on test gauge
arid observe gauge reading.
If regulated pressure now reads less than 100 psi,
replace regulator assembly.
If regulated pressure exceeds 130 psi, replace regu-
lator assembly.
Control Valve Test
Exhaust (Superlifts Inflated)
1.
Disconnect control valve lever from link.
2.
Hold lever down in exhaust position until Superlifts
deflate or for a minimum of 18 seconds.
3.
If Superlifts deflate, perform Intake Check.
4.
If Superlifts do not deflate, remove exhaust adapter
from control valve and hold lever down as in Step 2.
Replace adapter, O-ring and filter if this deflates
Superlifts.
5.
Replace control valve if none of the above steps solve
problem.
Intake (Reservoir Pressure 125 psi Minimum)
1.
Disconnect overtravel lever from link.
2.
Hold lever up in intake position until Superlifts in-
Fig.
16 - Assembly Leak Test Preparation
flate or for a minimum of fifteen seconds.
3.
If Superlifts inflate and hold, proceed to Time Delay
Check. '•
4.
If Superlifts inflate and then leak down, perform leak
test on lines and fittings and then on Superlifts and
control valve. Repair or replace as indicated.
Time Delay Test (Reservoir Pressure 125 psi Minimum)
1.
Record rear trim height of empty car (rear bumper
to ground).
2.
Add weight equivalent to two passenger load to rear
of car. Car should begin to level in 4-18 seconds.
3.
Remove weight. After 4-18 seconds car should begin
to settle.
4.
Replace valve if time delay is not within the 4-18
seconds.
Trim Adjustment—On Car
Trim adjustment should be performed with a full fuel
tank (or the equivalent in load at the rate of 6 lbs
./gal-
lon)
,
but no other load.
Abbreviated Adjustment
1.
Fill the compressor at the service valve with the
available air line pressure.
2.
Disconnect link from height control valve lever.
Move the height control valve lever upward until air
fills the Superlifts.
3.
Move lever downward and hold until air stops escap-
ing from the exhaust port of the height control valve.
The Superlifts will now automatically hold 8 to 15
PSI.
;
4.
Let lever go to its neutral position> and loosen the
lever adjustment nut.
5.
Assemble the link to the height control valve lever
and tighten the lever adjustment nut.
NOTE: Do not move control valve lever and
overtravel body while tightening nut.
Leak Tests
Compressor, Reservoir and Regulator
1.
Remove assembly intact.
2.
Connect test gauge to regulator. Inflate reservoir
through service valve to 80-110 psi.
3.
Route an 8" rubber hose between vacuum and vent
ports,
(fig. 16).
4.
Submerge in water and observe for air leaks at:
Reservoir weld seam.
Reservoir to compressor O-ring.
Regulator to compressor O-ring.
Regulator boot-defective internal.O-rihg.
Diaphragm between first and second stage housings.
' Tightening through bolts may correct the leak.
Cover gasket and retainer screw. A few bubbles here
is not a leak. A continuous stream indicates defec-
tive compressor check valves.
Service valve.
Test gauge connections.
5.
Correct any leaks detected by either tightening
screws or replacing parts.
CHEVROLET CHASSIS SERVICE MANUAL
Page 624 of 659
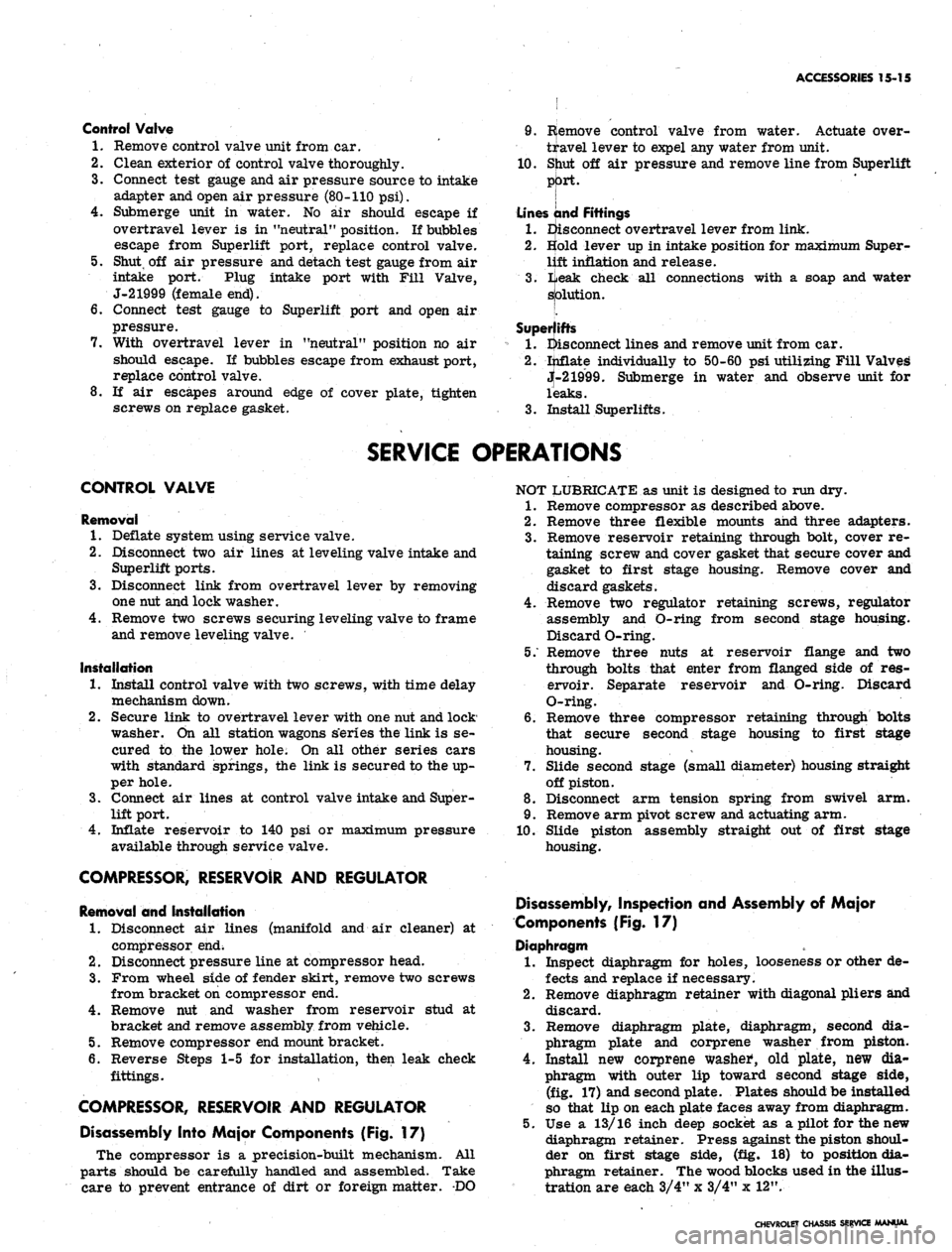
ACCESSORIES 15-15
Control Valve
1.
Remove control valve unit from car.
2.
Clean exterior of control valve thoroughly.
3.
Connect test gauge and air pressure source to intake
adapter and open air pressure (80-110 psi).
4.
Submerge unit in water. No air should escape if
overtravel lever is in "neutral" position. If bubbles
escape from Superlift port, replace control valve.
5. Shut, off air pressure and detach test gauge from air
intake port. Plug intake port with Fill Valve,
J-21999 (female end).
6. Connect test gauge to Superlift port and open air
pressure.
7. With overtravel lever in "neutral" position no air
should escape. If bubbles escape from exhaust port,
replace control valve.
8. If air escapes around edge of cover plate, tighten
screws on replace gasket.
9. R(emove control valve from water. Actuate over-
travel lever to expel any water from unit.
10.
Sjiut off air pressure and remove line from Superlift
[
Lines and Fittings
1.
Eisconnect overtravel lever from link.
2.
Bold lever up in intake position for maximum Super-
lift inflation and release.
3.
iieak check all connections with a soap and water
splution.
[.
Superlifts
1.
disconnect lines and remove unit from car.
2.
ijiflate individually to 50-60 psi utilizing Fill Valves
jt-21999. Submerge in water and observe unit for
leaks.
3.
Install Superlifts.
SERVICE OPERATIONS
CONTROL VALVE
Removal
1.
Deflate system using service valve.
2.
Disconnect two air lines at leveling valve intake and
Superlift ports.
3.
Disconnect link from overtravel lever by removing
one nut and lock washer.
4.
Remove two screws securing leveling valve to frame
and remove leveling valve.
Installation
1.
Install control valve with two screws, with time delay
mechanism down.
2.
Secure link to overtravel lever with one nut and lock
washer. On all station wagons s'eries the link is se-
cured to the lower hole. On all other series cars
with standard springs, the link is secured to the up-
per hole.
3.
Connect air lines at control valve intake and Super-
lift port.
4.
Inflate reservoir to 140 psi or maximum pressure
available through service valve.
COMPRESSOR, RESERVOIR AND REGULATOR
Removal and Installation
1.
Disconnect air lines (manifold and air cleaner) at
compressor end;
2.
Disconnect pressure line at compressor head.
3.
From wheel side of fender skirt, remove two screws
from bracket on compressor end.
4.
Remove nut and washer from reservoir stud at
bracket and remove assembly from vehicle.
5. Remove compressor end mount bracket.
6. Reverse Steps 1-5 for installation, then leak check
fittings.
COMPRESSOR, RESERVOIR AND REGULATOR
Disassembly Into Major Components (Fig. 17)
The compressor is a precision-built mechanism. All
parts should be carefully handled and assembled. Take
care to prevent entrance of dirt or foreign matter. DO
NOT LUBRICATE as unit is designed to run dry.
1.
Remove compressor as described above.
2.
Remove three flexible mounts and three adapters.
3.
Remove reservoir retaining through bolt, cover re-
taining screw and cover gasket that secure cover and
gasket to first stage housing. Remove cover and
discard gaskets.
4.
Remove two regulator retaining screws, regulator
assembly and O-ring from second stage housing.
Discard O-ring.
5/ Remove three nuts at reservoir flange and two
through bolts that enter from flanged side of res-
ervoir. Separate reservoir and O-ring. Discard
O-ring.
6. Remove three compressor retaining through bolts
that secure second stage housing to first stage
housing.
7. Slide second stage (small diameter) housing straight
off piston.
8. Disconnect arm tension spring from swivel arm.
9. Remove arm pivot screw and actuating arm.
10.
Slide piston assembly straight out of first stage
housing.
Disassembly, Inspection and Assembly of Major
Components (Fig. 17)
Diaphragm
1.
Inspect diaphragm for holes, looseness or other de-
fects and replace if necessary.
2.
Remove diaphragm retainer with diagonal pliers and
discard.
3.
Remove diaphragm plate, diaphragm, second dia-
phragm plate and corprene washer from piston.
4.
Install new corprene washed, old plate, new dia-
phragm with outer lip toward second stage side,
(fig. 17) and second plate. Plates should be installed
so that lip on each plate faces away from diaphragm.
5. Use a 13/16 inch deep socket as a pilot for the new
diaphragm retainer. Press against the piston shoul-
der on first stage side, (fig. 18) to position dia-
phragm retainer. The wood blocks used in the illus-
tration are each 3/4" x 3/4" x 12".
CHEVROLET CHASSIS SERVICE MANUAL