Page 913 of 1574
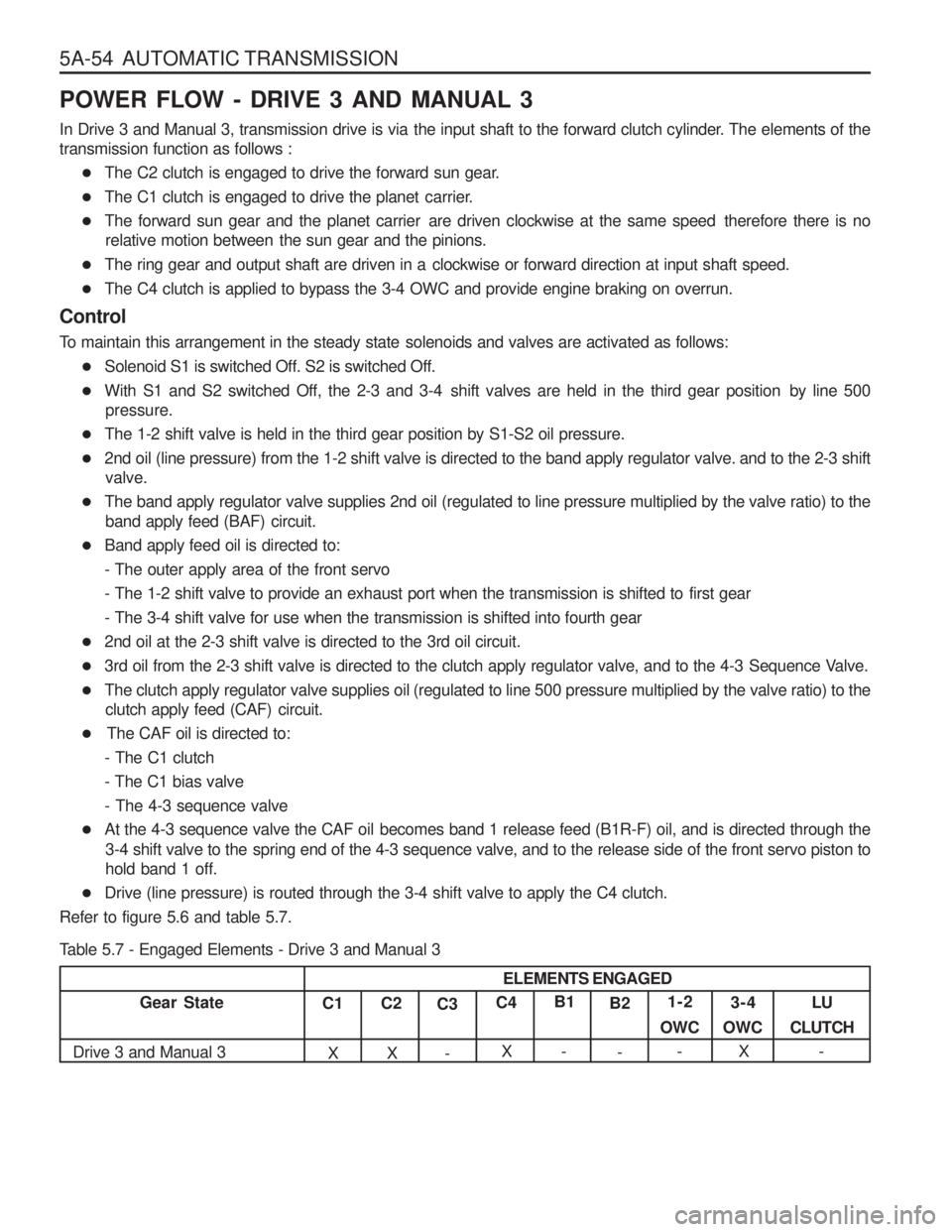
5A-54 AUTOMATIC TRANSMISSION POWER FLOW - DRIVE 3 AND MANUAL 3
In Drive 3 and Manual 3, transmission drive is via the input shaft to the forward clutch cylinder. The elements of the transmission function as follows : The C2 clutch is engaged to drive the forward sun gear.
The C1 clutch is engaged to drive the planet carrier.
The forward sun gear and the planet carrier are driven clockwise at the same speed therefore there is no
relative motion between the sun gear and the pinions.
The ring gear and output shaft are driven in a clockwise or forward direction at input shaft speed.
The C4 clutch is applied to bypass the 3-4 OWC and provide engine braking on overrun.
Control
To maintain this arrangement in the steady state solenoids and valves are activated as follows: Solenoid S1 is switched Off. S2 is switched Off.
With S1 and S2 switched Off, the 2-3 and 3-4 shift valves are held in the third gear position by line 500
pressure.
The 1-2 shift valve is held in the third gear position by S1-S2 oil pressure.
2nd oil (line pressure) from the 1-2 shift valve is directed to the band apply regulator valve. and to the 2-3 shift
valve.
The band apply regulator valve supplies 2nd oil (regulated to line pressure multiplied by the valve ratio) to the
band apply feed (BAF) circuit.
Band apply feed oil is directed to:
- The outer apply area of the front servo
- The 1-2 shift valve to provide an exhaust port when the transmission is shifted to first gear
- The 3-4 shift valve for use when the transmission is shifted into fourth gear
2nd oil at the 2-3 shift valve is directed to the 3rd oil circuit.
3rd oil from the 2-3 shift valve is directed to the clutch apply regulator valve, and to the 4-3 Sequence Valve.
The clutch apply regulator valve supplies oil (regulated to line 500 pressure multiplied by the valve ratio) to the
clutch apply feed (CAF) circuit.
The CAF oil is directed to:
- The C1 clutch- The C1 bias valve- The 4-3 sequence valve
At the 4-3 sequence valve the CAF oil becomes band 1 release feed (B1R-F) oil, and is directed through the
3-4 shift valve to the spring end of the 4-3 sequence valve, and to the release side of the front servo piston to hold band 1 off.
Drive (line pressure) is routed through the 3-4 shift valve to apply the C4 clutch.
Refer to figure 5.6 and table 5.7.
Table 5.7 - Engaged Elements - Drive 3 and Manual 3
Gear State
Drive 3 and Manual 3 C1
X C2
X C3
- C4
X B1
- B2
- 1-2
OWC - 3-4
OWC X LU
CLUTCH -
ELEMENTS ENGAGED
Page 914 of 1574
AUTOMATIC TRANSMISSION 5A-55
Page 915 of 1574
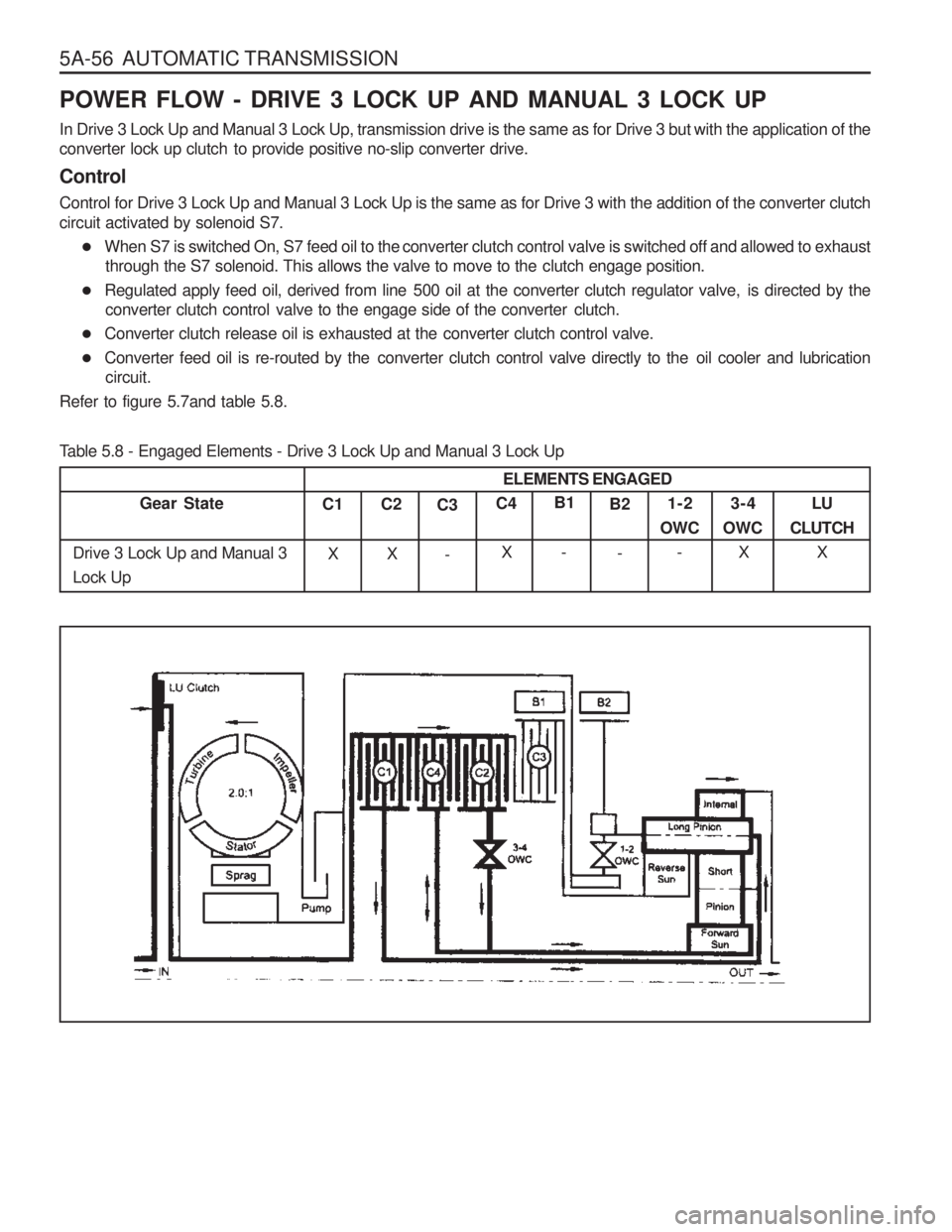
5A-56 AUTOMATIC TRANSMISSION POWER FLOW - DRIVE 3 LOCK UP AND MANUAL 3 LOCK UP
In Drive 3 Lock Up and Manual 3 Lock Up, transmission drive is the same as for Drive 3 but with the application of the
converter lock up clutch to provide positive no-slip converter drive. Control
Control for Drive 3 Lock Up and Manual 3 Lock Up is the same as for Drive 3 with the addition of the converter clutch circuit activated by solenoid S7. When S7 is switched On, S7 feed oil to the converter clutch control valve is switched off and allowed to exhaust
through the S7 solenoid. This allows the valve to move to the clutch engage position.
Regulated apply feed oil, derived from line 500 oil at the converter clutch regulator valve, is directed by the
converter clutch control valve to the engage side of the converter clutch.
Converter clutch release oil is exhausted at the converter clutch control valve.
Converter feed oil is re-routed by the converter clutch control valve directly to the oil cooler and lubrication
circuit.
Refer to figure 5.7and table 5.8.
Table 5.8 - Engaged Elements - Drive 3 Lock Up and Manual 3 Lock Up
Gear State
Drive 3 Lock Up and Manual 3 Lock Up C1
X C2
X C3
- C4
X B1
- B2
- 1-2
OWC - 3-4
OWC X LU
CLUTCH X
ELEMENTS ENGAGED
Page 916 of 1574
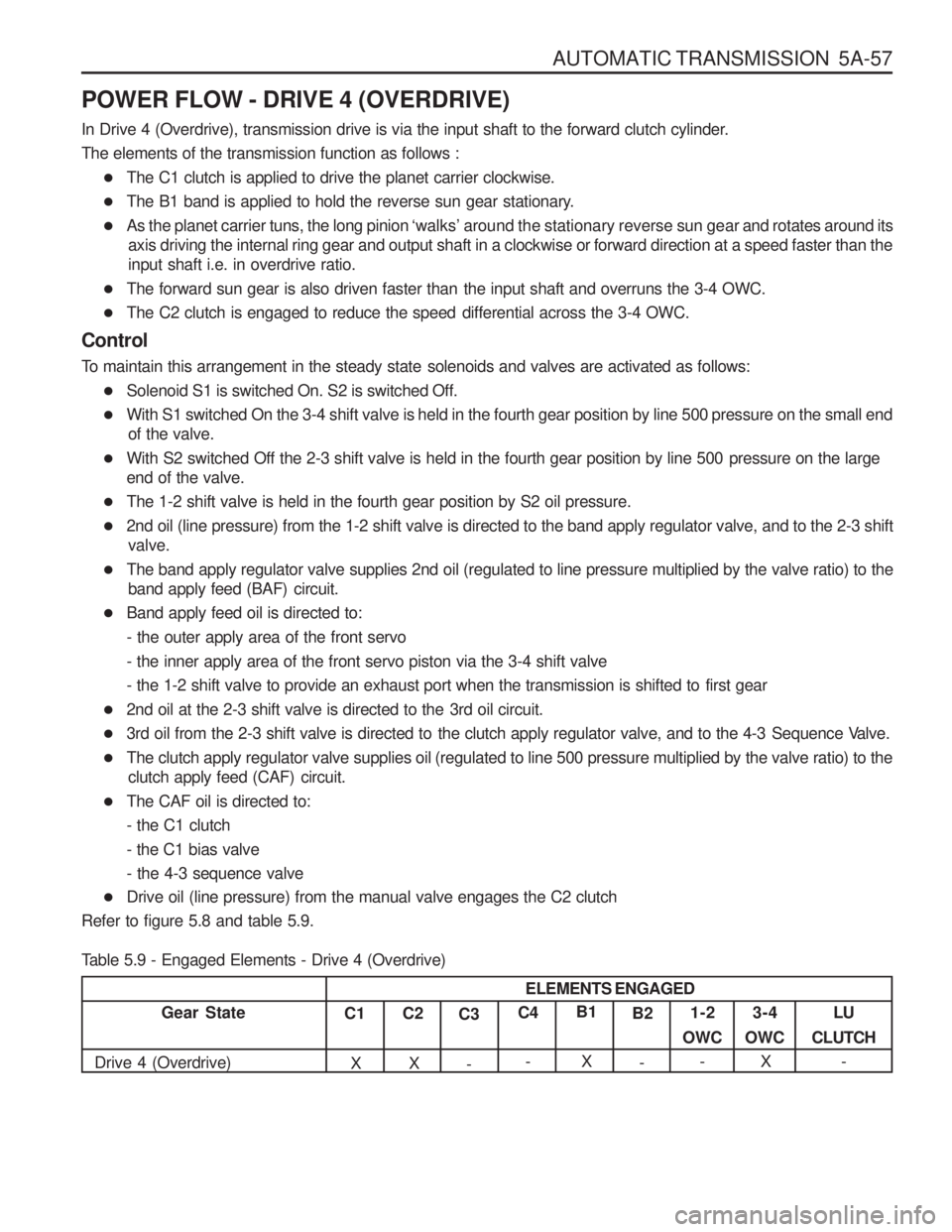
AUTOMATIC TRANSMISSION 5A-57
POWER FLOW - DRIVE 4 (OVERDRIVE)
In Drive 4 (Overdrive), transmission drive is via the input shaft to the forward clutch cylinder. The elements of the transmission function as follows :
The C1 clutch is applied to drive the planet carrier clockwise.
The B1 band is applied to hold the reverse sun gear stationary.
As the planet carrier tuns, the long pinion ‘walks ’ around the stationary reverse sun gear and rotates around its
axis driving the internal ring gear and output shaft in a clockwise or forward direction at a speed faster than the input shaft i.e. in overdrive ratio.
The forward sun gear is also driven faster than the input shaft and overruns the 3-4 OWC.
The C2 clutch is engaged to reduce the speed differential across the 3-4 OWC.
Control
To maintain this arrangement in the steady state solenoids and valves are activated as follows: Solenoid S1 is switched On. S2 is switched Off.
With S1 switched On the 3-4 shift valve is held in the fourth gear position by line 500 pressure on the small end
of the valve.
With S2 switched Off the 2-3 shift valve is held in the fourth gear position by line 500 pressure on the large end of the valve.
The 1-2 shift valve is held in the fourth gear position by S2 oil pressure.
2nd oil (line pressure) from the 1-2 shift valve is directed to the band apply regulator valve, and to the 2-3 shift
valve.
The band apply regulator valve supplies 2nd oil (regulated to line pressure multiplied by the valve ratio) to the
band apply feed (BAF) circuit.
Band apply feed oil is directed to: - the outer apply area of the front servo- the inner apply area of the front servo piston via the 3-4 shift valve
- the 1-2 shift valve to provide an exhaust port when the transmission is shifted to first gear
2nd oil at the 2-3 shift valve is directed to the 3rd oil circuit.
3rd oil from the 2-3 shift valve is directed to the clutch apply regulator valve, and to the 4-3 Sequence Valve.
The clutch apply regulator valve supplies oil (regulated to line 500 pressure multiplied by the valve ratio) to the
clutch apply feed (CAF) circuit.
The CAF oil is directed to:- the C1 clutch- the C1 bias valve- the 4-3 sequence valve
Drive oil (line pressure) from the manual valve engages the C2 clutch
Refer to figure 5.8 and table 5.9.
Table 5.9 - Engaged Elements - Drive 4 (Overdrive)
Gear State
Drive 4 (Overdrive) C1
X C2
X C3
- C4
- B1
X B2
- 1-2
OWC - 3-4
OWC X LU
CLUTCH -
ELEMENTS ENGAGED
Page 917 of 1574
5A-58 AUTOMATIC TRANSMISSION
Page 918 of 1574
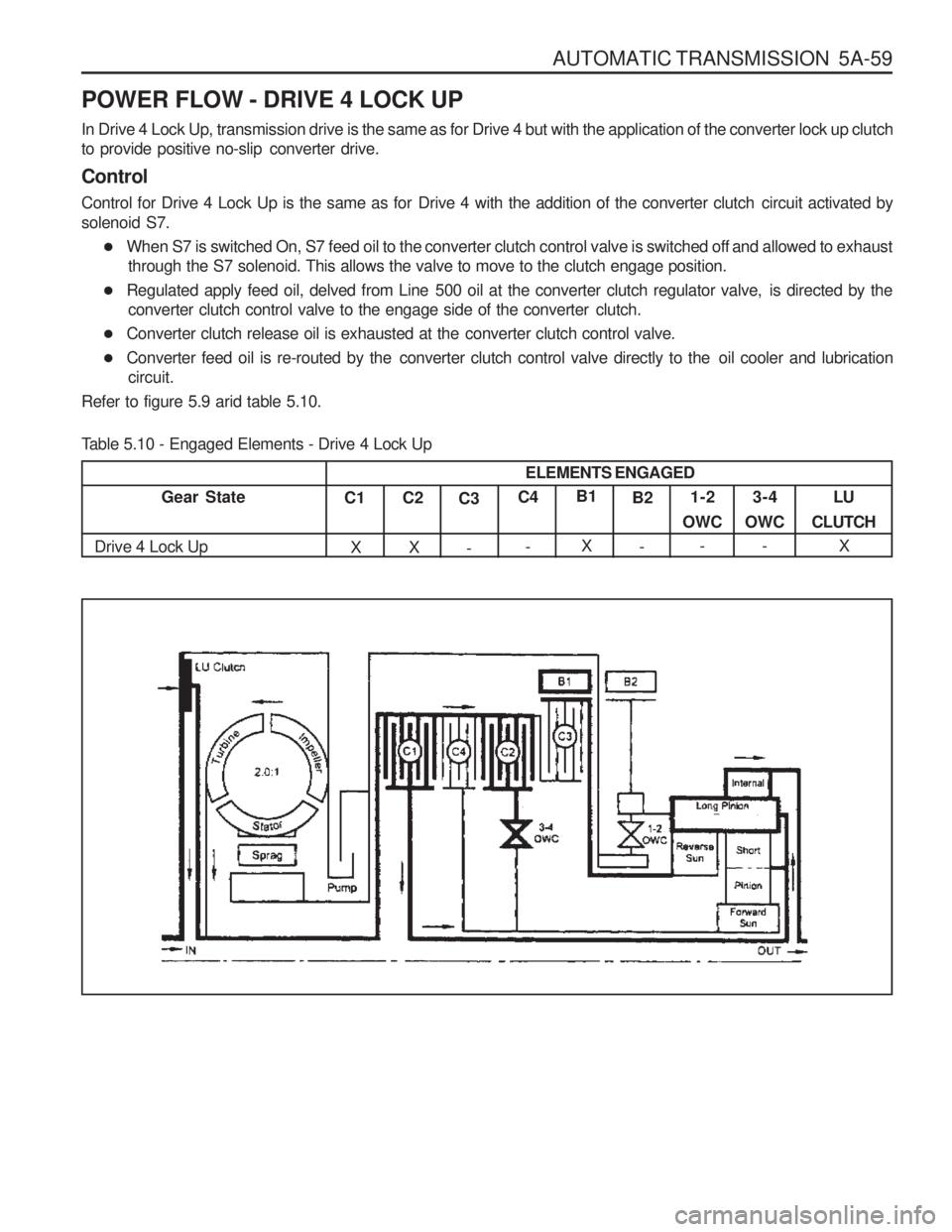
AUTOMATIC TRANSMISSION 5A-59
POWER FLOW - DRIVE 4 LOCK UP
In Drive 4 Lock Up, transmission drive is the same as for Drive 4 but with the application of the converter lock up clutch
to provide positive no-slip converter drive. Control
Control for Drive 4 Lock Up is the same as for Drive 4 with the addition of the converter clutch circuit activated by solenoid S7. When S7 is switched On, S7 feed oil to the converter clutch control valve is switched off and allowed to exhaust
through the S7 solenoid. This allows the valve to move to the clutch engage position.
Regulated apply feed oil, delved from Line 500 oil at the converter clutch regulator valve, is directed by the
converter clutch control valve to the engage side of the converter clutch.
Converter clutch release oil is exhausted at the converter clutch control valve.
Converter feed oil is re-routed by the converter clutch control valve directly to the oil cooler and lubrication
circuit.
Refer to figure 5.9 arid table 5.10.
Table 5.10 - Engaged Elements - Drive 4 Lock Up
Gear State
Drive 4 Lock Up C1
X C2
X C3
- C4
- B1
X B2
- 1-2
OWC - 3-4
OWC - LU
CLUTCH X
ELEMENTS ENGAGED
Page 919 of 1574
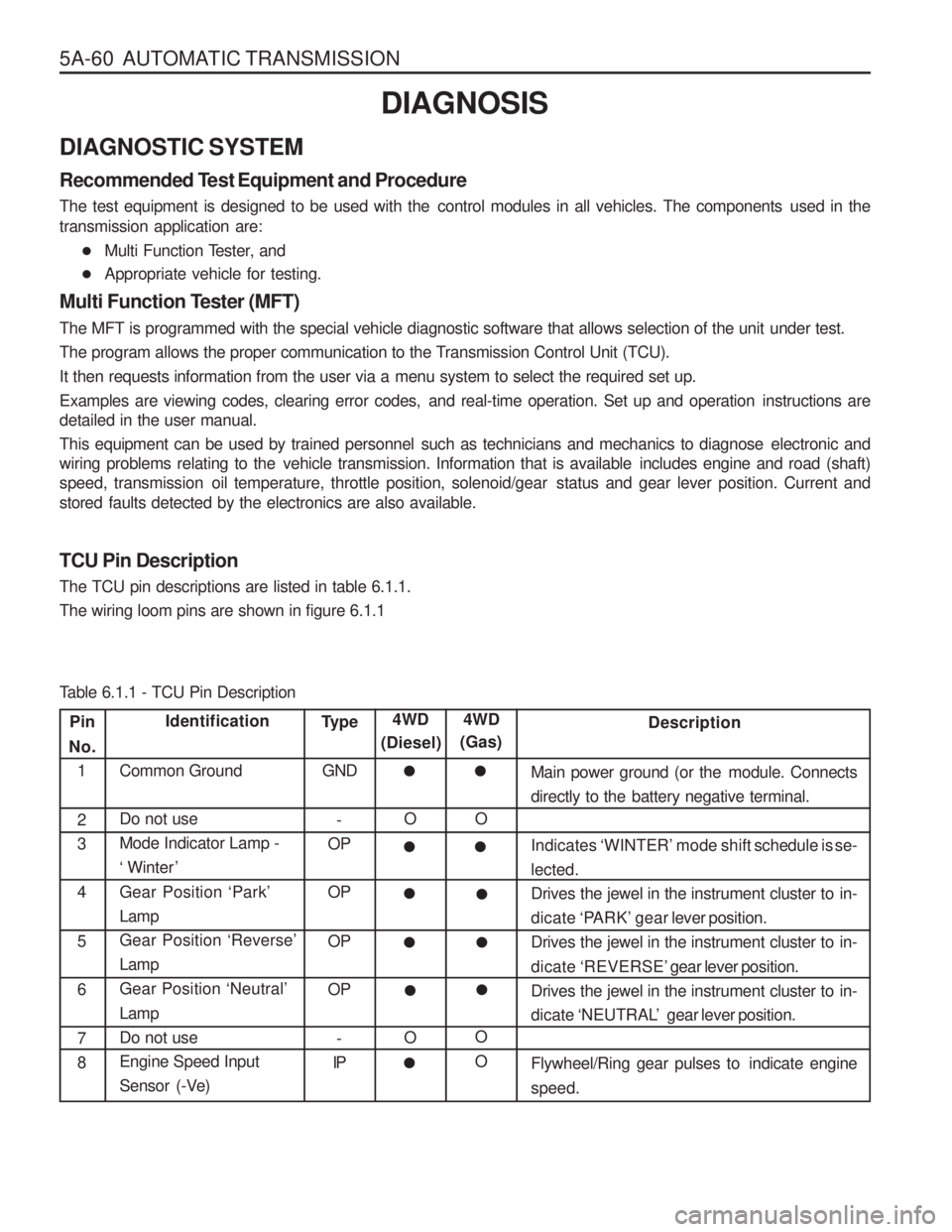
5A-60 AUTOMATIC TRANSMISSIONDIAGNOSIS
DIAGNOSTIC SYSTEM Recommended T est Equipment and Procedure
The test equipment is designed to be used with the control modules in all vehicles. The components used in the transmission application are: Multi Function Tester, and
Appropriate vehicle for testing.
Multi Function Tester (MFT)
The MFT is programmed with the special vehicle diagnostic software that allows selection of the unit under test.
The program allows the proper communication to the Transmission Control Unit (TCU).
It then requests information from the user via a menu system to select the required set up.
Examples are viewing codes, clearing error codes, and real-time operation. Set up and operation instructions are detailed in the user manual.
This equipment can be used by trained personnel such as technicians and mechanics to diagnose electronic and
wiring problems relating to the vehicle transmission. Information that is available includes engine and road (shaft)
speed, transmission oil temperature, throttle position, solenoid/gear status and gear lever position. Current andstored faults detected by the electronics are also available.
TCU Pin Description The TCU pin descriptions are listed in table 6.1.1. The wiring loom pins are shown in figure 6.1.1
Pin
No. 1 2 3 4 5 6 7 8Identification
Common Ground Do not use Mode Indicator Lamp -‘ Winter ’
Gear Position ‘Park ’
LampGear Position ‘Reverse ’
LampGear Position ‘Neutral ’
LampDo not useEngine Speed Input
Sensor (-Ve) Type
GND -
OP OP OP OP
-
IP Description
Main power ground (or the module. Connects
directly to the battery negative terminal. Indicates ‘WINTER ’ mode shift schedule is se-
lected.
Drives the jewel in the instrument cluster to in-dicate ‘PARK ’ gear lever position.
Drives the jewel in the instrument cluster to in- dicate ‘REVERSE ’ gear lever position.
Drives the jewel in the instrument cluster to in- dicate ‘NEUTRAL ’ gear lever position.
Flywheel/Ring gear pulses to indicate engine speed.
4WD
(Diesel)
O O
4WD
(Gas)
O O O
Table 6.1.1 - TCU Pin Description
Page 920 of 1574
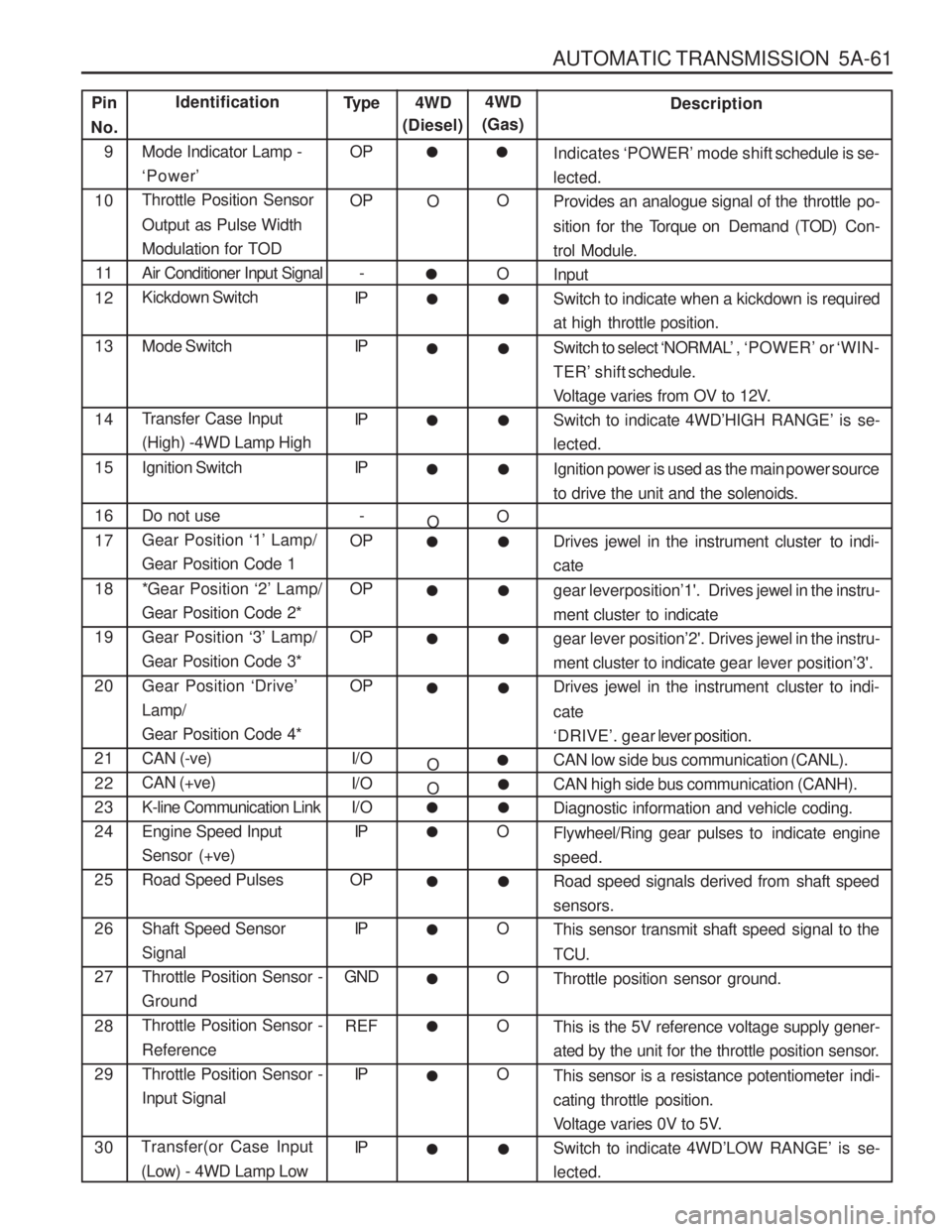
AUTOMATIC TRANSMISSION 5A-61
Pin
No. 9 10
11
12 13 14 1516 17 1819 20 21 22 2324 25 26 27 28 29 30Identification
Mode Indicator Lamp - ‘ Power ’
Throttle Position Sensor Output as Pulse Width Modulation for TODAir Conditioner Input SignalKickdown Switch Mode Switch
Transfer Case Input (High) -4WD Lamp High Ignition Switch Do not use Gear Position ‘1’ Lamp/
Gear Position Code 1
*Gear Position ‘2’ Lamp/
Gear Position Code 2* Gear Position ‘3’ Lamp/
Gear Position Code 3* Gear Position ‘Drive ’
Lamp/ Gear Position Code 4*CAN (-ve)CAN (+ve) K-line Communication Link Engine Speed InputSensor (+ve)Road Speed Pulses Shaft Speed Sensor SignalThrottle Position Sensor -GroundThrottle Position Sensor - Reference Throttle Position Sensor -Input Signal
Transfer(or Case Input
(Low) - 4WD Lamp Low Type
OP OP
-
IP IP IP IP
-
OPOPOP OP
I/O
I/O
I/O IP
OP
IP
GND
REF IP IP Description
Indicates ‘POWER ’ mode shift schedule is se-
lected.
Provides an analogue signal of the throttle po- sition for the T orque on Demand (T OD) Con-
trol Module. Input
Switch to indicate when a kickdown is required
at high throttle position. Switch to select ‘NORMAL ’, ‘POWER ’ or ‘WIN-
TER ’ shift schedule.
Voltage varies from OV to 12V. Switch to indicate 4WD ’HIGH RANGE ’ is se-
lected.
Ignition power is used as the main power source
to drive the unit and the solenoids.
Drives jewel in the instrument cluster to indi- cate gear leverposition ’1'. Drives jewel in the instru-
ment cluster to indicate gear lever position ’2'. Drives jewel in the instru-
ment cluster to indicate gear lever position’3'.
Drives jewel in the instrument cluster to indi- cate ‘ DRIVE ’. gear lever position.
CAN low side bus communication (CANL).
CAN high side bus communication (CANH).
Diagnostic information and vehicle coding.
Flywheel/Ring gear pulses to indicate engine speed.
Road speed signals derived from shaft speedsensors.
This sensor transmit shaft speed signal to the TCU. Throttle position sensor ground. This is the 5V reference voltage supply gener-
ated by the unit for the throttle position sensor.
This sensor is a resistance potentiometer indi-
cating throttle position.
Voltage varies 0V to 5V.Switch to indicate 4WD ’LOW RANGE ’ is se-
lected.
4WD
(Diesel)
O O O O
4WD
(Gas)
O O O O O O OO