Page 889 of 1574
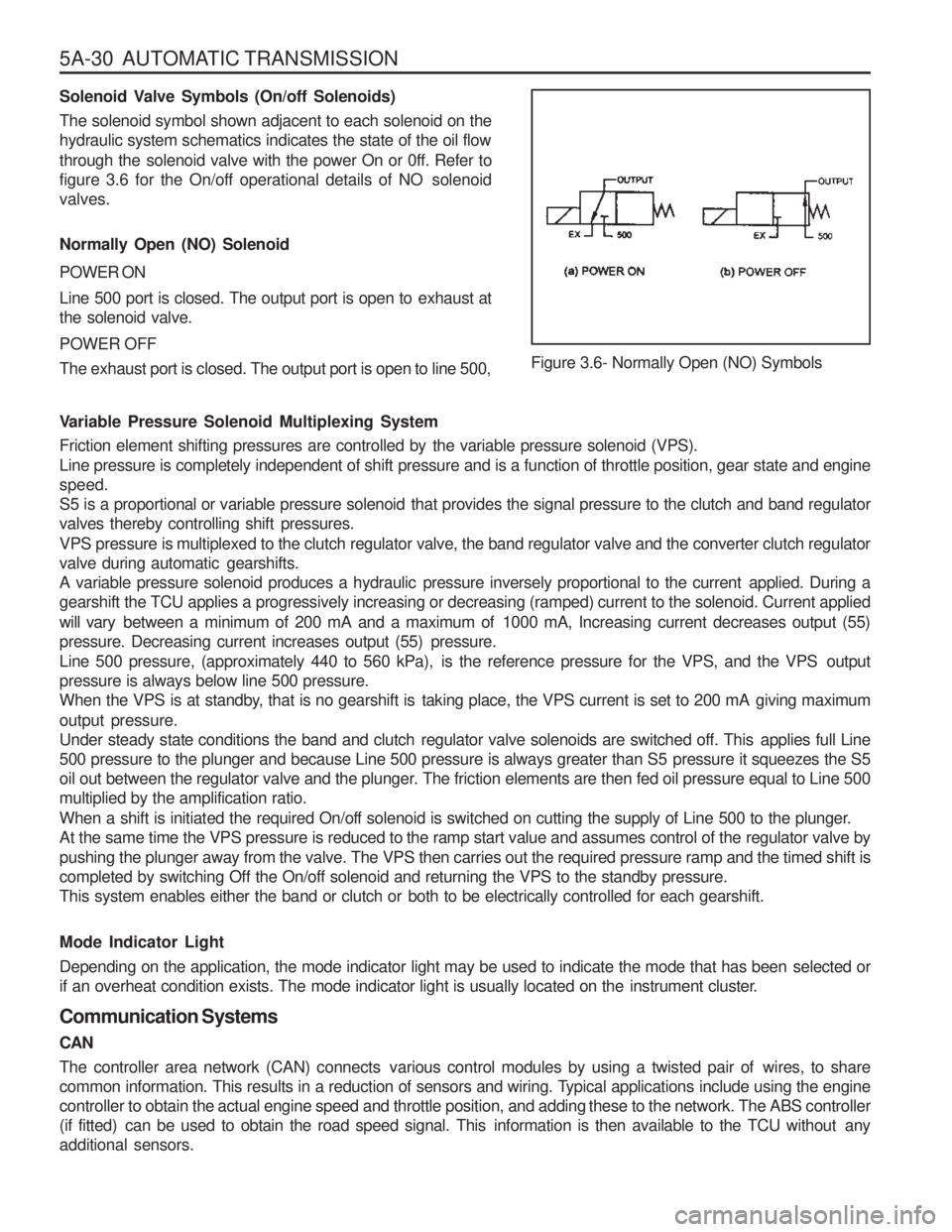
5A-30 AUTOMATIC TRANSMISSION
Solenoid Valve Symbols (On/off Solenoids)
The solenoid symbol shown adjacent to each solenoid on the
hydraulic system schematics indicates the state of the oil flow
through the solenoid valve with the power On or 0ff. Refer to
figure 3.6 for the On/off operational details of NO solenoidvalves. Normally Open (NO) Solenoid POWER ON
Line 500 port is closed. The output port is open to exhaust at the solenoid valve. POWER OFF
The exhaust port is closed. The output port is open to line 500,Figure 3.6- Normally Open (NO) Symbols
Variable Pressure Solenoid Multiplexing System
Friction element shifting pressures are controlled by the variable pressure solenoid (VPS).
Line pressure is completely independent of shift pressure and is a function of throttle position, gear state and enginespeed.
S5 is a proportional or variable pressure solenoid that provides the signal pressure to the clutch and band regulator
valves thereby controlling shift pressures.
VPS pressure is multiplexed to the clutch regulator valve, the band regulator valve and the converter clutch regulator
valve during automatic gearshifts.
A variable pressure solenoid produces a hydraulic pressure inversely proportional to the current applied. During a
gearshift the TCU applies a progressively increasing or decreasing (ramped) current to the solenoid. Current applied will vary between a minimum of 200 mA and a maximum of 1000 mA, Increasing current decreases output (55)
pressure. Decreasing current increases output (55) pressure.
Line 500 pressure, (approximately 440 to 560 kPa), is the reference pressure for the VPS, and the VPS outputpressure is always below line 500 pressure.
When the VPS is at standby, that is no gearshift is taking place, the VPS current is set to 200 mA giving maximum output pressure.
Under steady state conditions the band and clutch regulator valve solenoids are switched off. This applies full Line
500 pressure to the plunger and because Line 500 pressure is always greater than S5 pressure it squeezes the S5
oil out between the regulator valve and the plunger. The friction elements are then fed oil pressure equal to Line 500multiplied by the amplification ratio.
When a shift is initiated the required On/off solenoid is switched on cutting the supply of Line 500 to the plunger.
At the same time the VPS pressure is reduced to the ramp start value and assumes control of the regulator valve by
pushing the plunger away from the valve. The VPS then carries out the required pressure ramp and the timed shift is
completed by switching Off the On/off solenoid and returning the VPS to the standby pressure.
This system enables either the band or clutch or both to be electrically controlled for each gearshift. Mode Indicator Light
Depending on the application, the mode indicator light may be used to indicate the mode that has been selected or
if an overheat condition exists. The mode indicator light is usually located on the instrument cluster. Communication Systems CAN
The controller area network (CAN) connects various control modules by using a twisted pair of wires, to share
common information. This results in a reduction of sensors and wiring. Typical applications include using the engine
controller to obtain the actual engine speed and throttle position, and adding these to the network. The ABS controller
(if fitted) can be used to obtain the road speed signal. This information is then available to the TCU without anyadditional sensors.
Page 890 of 1574
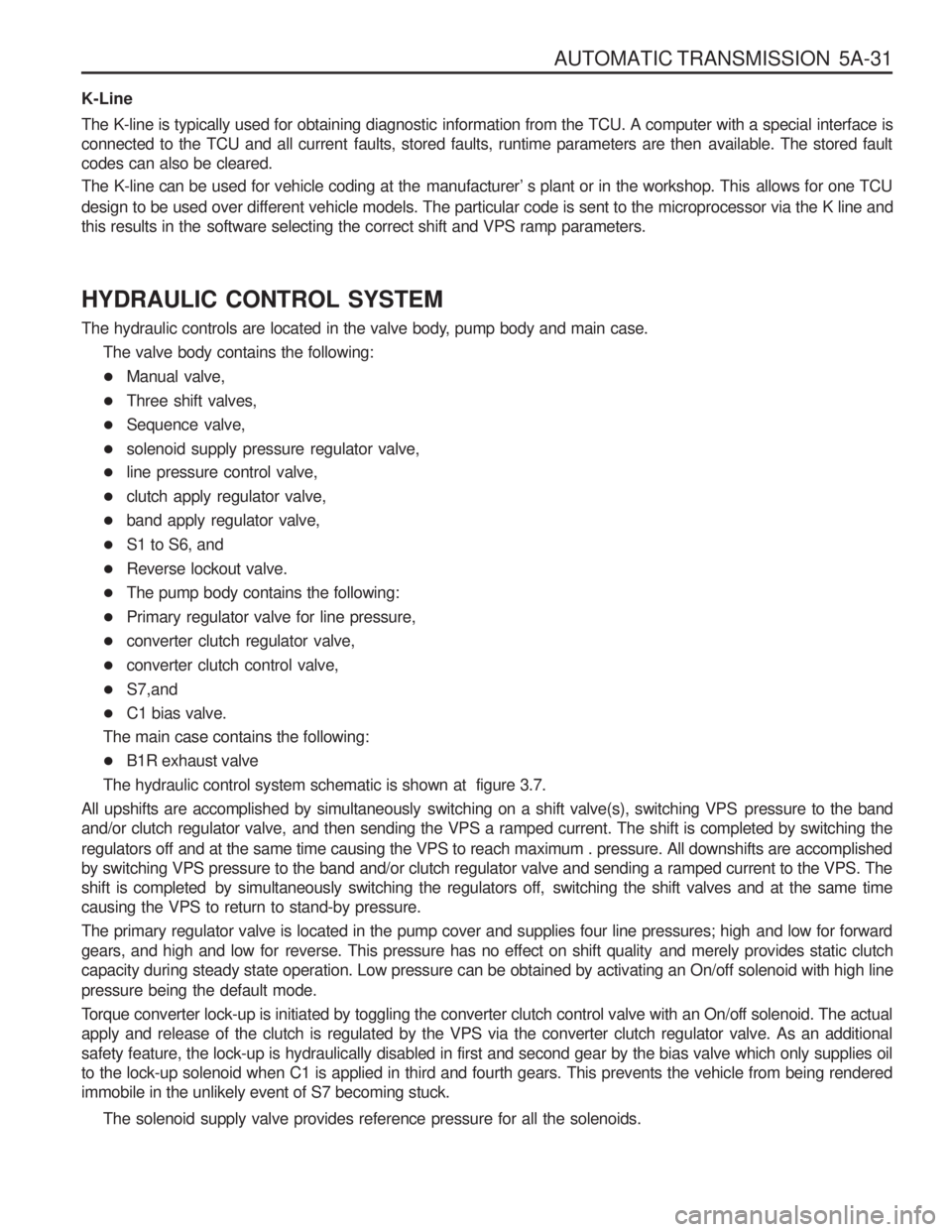
AUTOMATIC TRANSMISSION 5A-31
K-Line
The K-line is typically used for obtaining diagnostic information from the TCU. A computer with a special interface is
connected to the TCU and all current faults, stored faults, runtime parameters are then available. The stored faultcodes can also be cleared.
The K-line can be used for vehicle coding at the manufacturer’ s plant or in the workshop. This allows for one TCU
design to be used over different vehicle models. The particular code is sent to the microprocessor via the K line and
this results in the software selecting the correct shift and VPS ramp parameters. HYDRAULIC CONTROL SYSTEM
The hydraulic controls are located in the valve body, pump body and main case.The valve body contains the following:
Manual valve,
Three shift valves,
Sequence valve,
solenoid supply pressure regulator valve,
line pressure control valve,
clutch apply regulator valve,
band apply regulator valve,
S1 to S6, and
Reverse lockout valve.
The pump body contains the following:
Primary regulator valve for line pressure,
converter clutch regulator valve,
converter clutch control valve,
S7,and
C1 bias valve.
The main case contains the following:
B1R exhaust valve
The hydraulic control system schematic is shown at figure 3.7.
All upshifts are accomplished by simultaneously switching on a shift valve(s), switching VPS pressure to the band
and/or clutch regulator valve, and then sending the VPS a ramped current. The shift is completed by switching the
regulators off and at the same time causing the VPS to reach maximum . pressure. All downshifts are accomplished
by switching VPS pressure to the band and/or clutch regulator valve and sending a ramped current to the VPS. The
shift is completed by simultaneously switching the regulators off, switching the shift valves and at the same timecausing the VPS to return to stand-by pressure.
The primary regulator valve is located in the pump cover and supplies four line pressures; high and low for forward
gears, and high and low for reverse. This pressure has no effect on shift quality and merely provides static clutch
capacity during steady state operation. Low pressure can be obtained by activating an On/off solenoid with high line pressure being the default mode.
Torque converter lock-up is initiated by toggling the converter clutch control valve with an On/off solenoid. The actual apply and release of the clutch is regulated by the VPS via the converter clutch regulator valve. As an additionalsafety feature, the lock-up is hydraulically disabled in first and second gear by the bias valve which only supplies oilto the lock-up solenoid when C1 is applied in third and fourth gears. This prevents the vehicle from being renderedimmobile in the unlikely event of S7 becoming stuck.
The solenoid supply valve provides reference pressure for all the solenoids.
Page 891 of 1574
5A-32 AUTOMATIC TRANSMISSION Figure 3.7 - Hydraulic Control Circuit
Page 892 of 1574
AUTOMATIC TRANSMISSION 5A-33
Figure 3.8 - Valve Body
Figure 3.9 - Pump Cover
Valve Body Figure 3.8 depicts the valve body as a unit as viewed from the
transmission sump. Figure 3.9 depicts the pump cover.
Page 893 of 1574
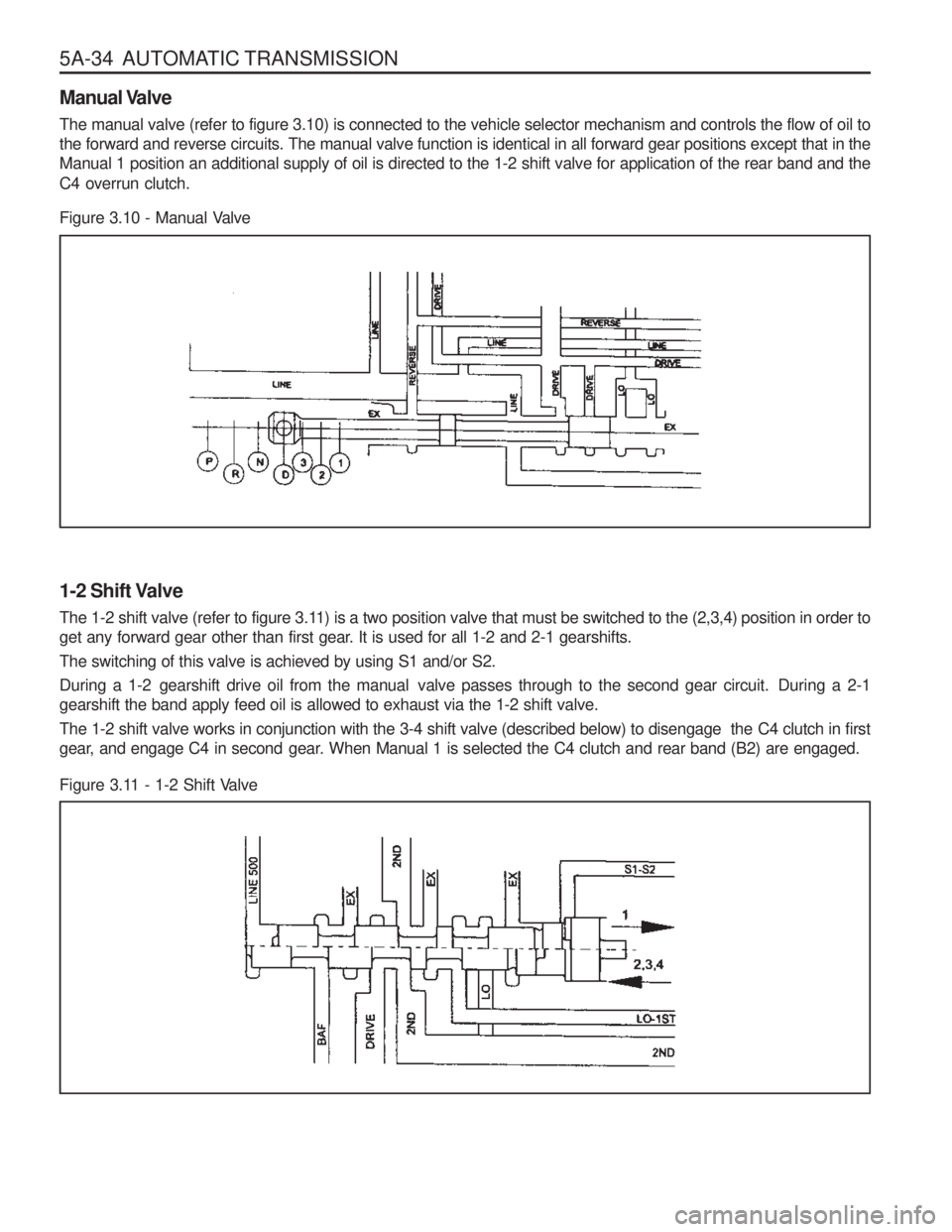
5A-34 AUTOMATIC TRANSMISSION
Figure 3.10 - Manual Valve
1-2 Shift Valve
The 1-2 shift valve (refer to figure 3.11) is a two position valve that must be switched to the (2,3,4) position in order to
get any forward gear other than first gear. It is used for all 1-2 and 2-1 gearshifts.
The switching of this valve is achieved by using S1 and/or S2.
During a 1-2 gearshift drive oil from the manual valve passes through to the second gear circuit. During a 2-1
gearshift the band apply feed oil is allowed to exhaust via the 1-2 shift valve.
The 1-2 shift valve works in conjunction with the 3-4 shift valve (described below) to disengage the C4 clutch in first
gear, and engage C4 in second gear. When Manual 1 is selected the C4 clutch and rear band (B2) are engaged.
Figure 3.11 - 1-2 Shift Valve
Manual Valve The manual valve (refer to figure 3.10) is connected to the vehicle selector mechanism and controls the flow of oil to the forward and reverse circuits. The manual valve function is identical in all forward gear positions except that in theManual 1 position an additional supply of oil is directed to the 1-2 shift valve for application of the rear band and the C4 overrun clutch.
Page 894 of 1574
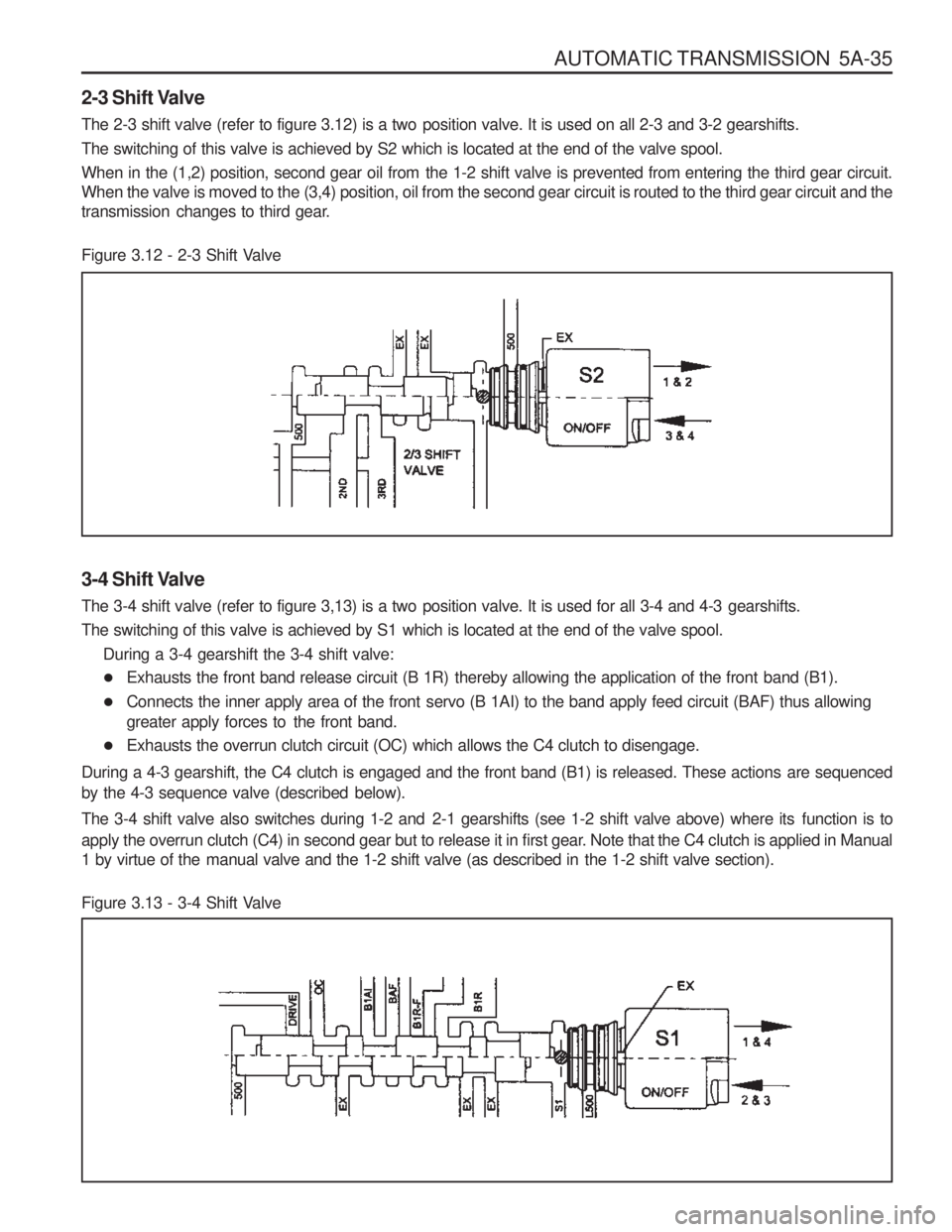
AUTOMATIC TRANSMISSION 5A-35
2-3 Shift Valve
The 2-3 shift valve (refer to figure 3.12) is a two position valve. It is used on all 2-3 and 3-2 gearshifts.
The switching of this valve is achieved by S2 which is located at the end of the valve spool.
When in the (1,2) position, second gear oil from the 1-2 shift valve is prevented from entering the third gear circuit.
When the valve is moved to the (3,4) position, oil from the second gear circuit is routed to the third gear circuit and the
transmission changes to third gear.
Figure 3.12 - 2-3 Shift Valve
3-4 Shift Valve
The 3-4 shift valve (refer to figure 3,13) is a two position valve. It is used for all 3-4 and 4-3 gearshifts.
The switching of this valve is achieved by S1 which is located at the end of the valve spool.During a 3-4 gearshift the 3-4 shift valve:
Exhausts the front band release circuit (B 1R) thereby allowing the application of the front band (B1).
Connects the inner apply area of the front servo (B 1AI) to the band apply feed circuit (BAF) thus allowing
greater apply forces to the front band.
Exhausts the overrun clutch circuit (OC) which allows the C4 clutch to disengage.
During a 4-3 gearshift, the C4 clutch is engaged and the front band (B1) is released. These actions are sequenced
by the 4-3 sequence valve (described below).
The 3-4 shift valve also switches during 1-2 and 2-1 gearshifts (see 1-2 shift valve above) where its function is to
apply the overrun clutch (C4) in second gear but to release it in first gear. Note that the C4 clutch is applied in Manual
1 by virtue of the manual valve and the 1-2 shift valve (as described in the 1-2 shift valve section).
Figure 3.13 - 3-4 Shift Valve
Page 895 of 1574
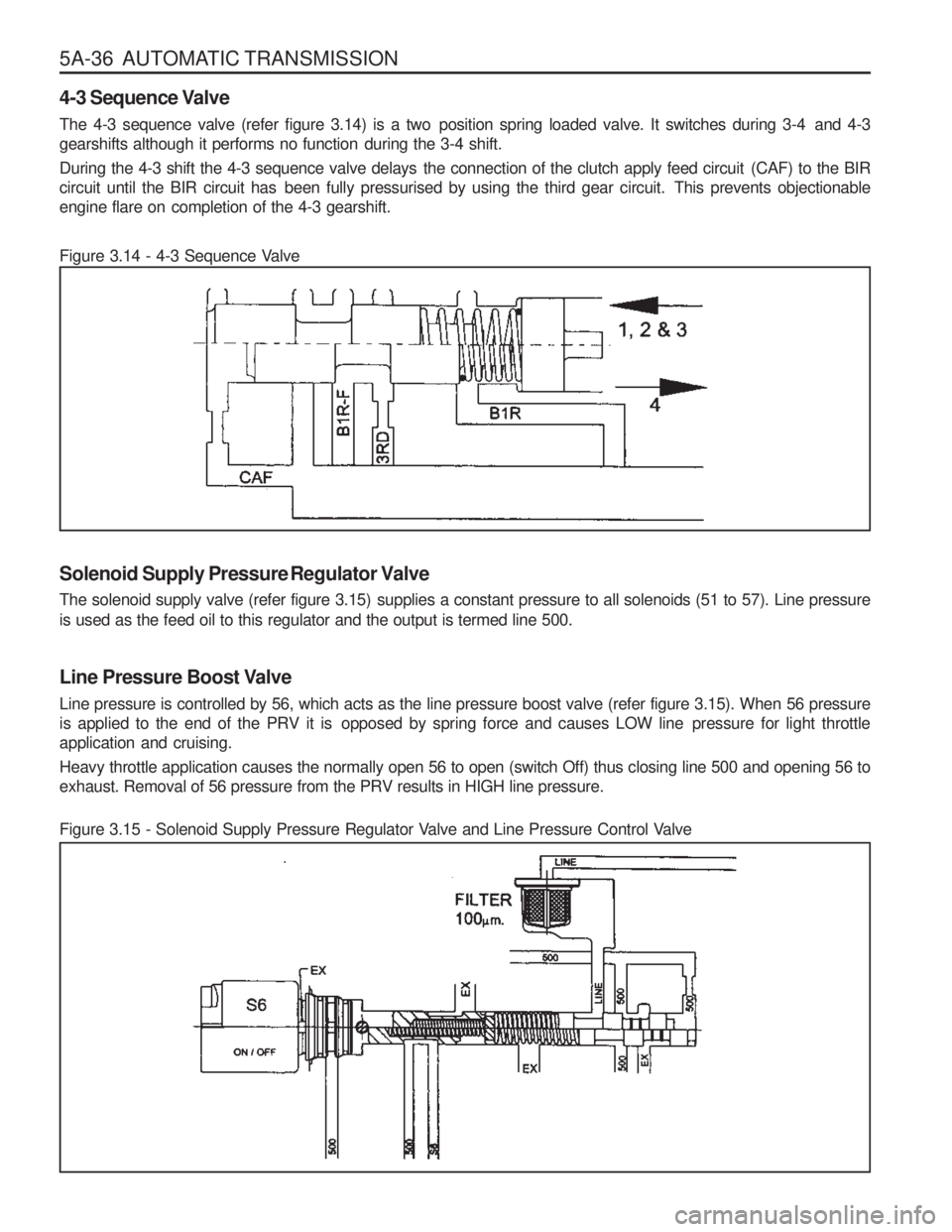
5A-36 AUTOMATIC TRANSMISSION
4-3 Sequence Valve
The 4-3 sequence valve (refer figure 3.14) is a two position spring loaded valve. It switches during 3-4 and 4-3
gearshifts although it performs no function during the 3-4 shift.
During the 4-3 shift the 4-3 sequence valve delays the connection of the clutch apply feed circuit (CAF) to the BIR
circuit until the BIR circuit has been fully pressurised by using the third gear circuit. This prevents objectionable
engine flare on completion of the 4-3 gearshift.
Figure 3.14 - 4-3 Sequence Valve
Figure 3.15 - Solenoid Supply Pressure Regulator Valve and Line Pressure Control Valve
Solenoid Supply Pressure Regulator Valve
The solenoid supply valve (refer figure 3.15) supplies a constant pressure to all solenoids (51 to 57). Line pressure
is used as the feed oil to this regulator and the output is termed line 500.
Line Pressure Boost Valve
Line pressure is controlled by 56, which acts as the line pressure boost valve (refer figure 3.15). When 56 pressure
is applied to the end of the PRV it is opposed by spring force and causes LOW line pressure for light throttleapplication and cruising.
Heavy throttle application causes the normally open 56 to open (switch Off) thus closing line 500 and opening 56 to
exhaust. Removal of 56 pressure from the PRV results in HIGH line pressure.
Page 896 of 1574
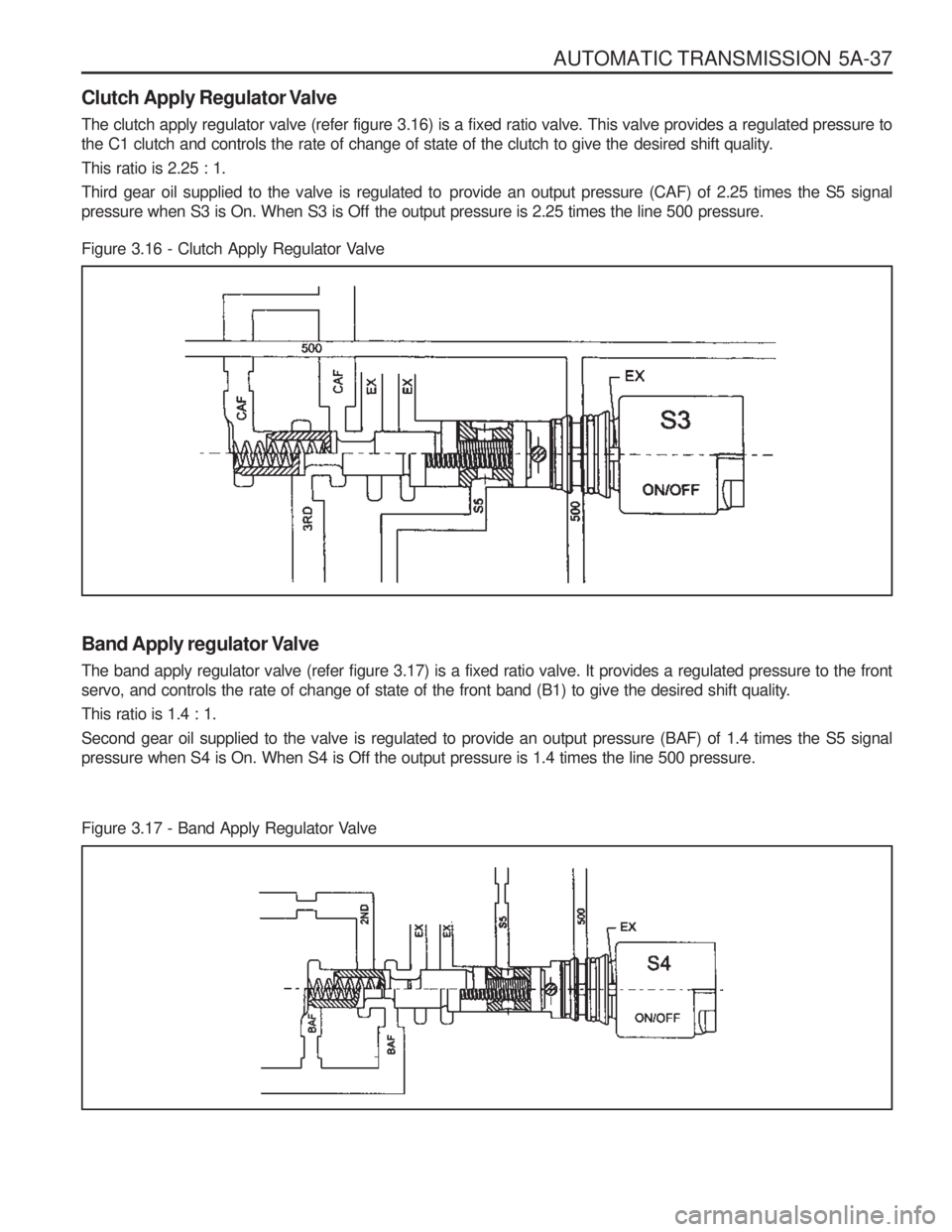
AUTOMATIC TRANSMISSION 5A-37
Figure 3.16 - Clutch Apply Regulator Valve
Clutch Apply Regulator Valve
The clutch apply regulator valve (refer figure 3.16) is a fixed ratio valve. This valve provides a regulated pressure to
the C1 clutch and controls the rate of change of state of the clutch to give the desired shift quality. This ratio is 2.25 : 1.
Third gear oil supplied to the valve is regulated to provide an output pressure (CAF) of 2.25 times the S5 signal
pressure when S3 is On. When S3 is Off the output pressure is 2.25 times the line 500 pressure.
Band Apply regulator Valve The band apply regulator valve (refer figure 3.17) is a fixed ratio valve. It provides a regulated pressure to the front
servo, and controls the rate of change of state of the front band (B1) to give the desired shift quality. This ratio is 1.4 : 1.
Second gear oil supplied to the valve is regulated to provide an output pressure (BAF) of 1.4 times the S5 signal pressure when S4 is On. When S4 is Off the output pressure is 1.4 times the line 500 pressure.
Figure 3.17 - Band Apply Regulator Valve