Page 393 of 1216
ENGINE <2.0L DOHC Engine> - Camshaft and Rocker Arm9-l 09
CAMSHAFT AND ROCKER ARMNo9LE-B
- DISASSEMBLY AND REASSEMBLY3
19-21 Nm8,14-15 ftlbs.,9 IQ&”
80-100 Nm
58-72 ftlbs.
,11IO-13 Nm7-9 ftlbs.
6EN0467
Disassembly steps
r)+ 1. Crank angle sensor+* l +2. Camshaft sprocketl +3. Bearing cap rear*4 4. Bearing cap frontl 45. Camshaft oil seall *6. Bearing cap No. 5
++ 7. Bearing cap No. 2+a 8. Bearing cap No. 4~~ 9. Beanng cap No. 3l * 1;: kz$&;;m12. Lash adjuster
13. Oil delivery body
NOTE(I) Reverse the disassembly procedures to reassemble.(2) 4e : Refer to “Service Points of Disassembly”.(3) l a : Refer to “Service Points of Reassembly”.(4) m : Non-reusable parts
SERVICE POINTS OF DISASSEMBLYNOSLBDD2. REMOVAL OF CAMSHAFT SPROCKET
(1) Using a wrench, hold the camshaft at its hexagon
(between the
No.2 and No.3 journals) and remove the
camshaft sprocket bolt.
Caution
Locking the camshaft sprocket with a tool damages
the sprocket.
(2) Remove the camshaft sprockets.
Page 394 of 1216
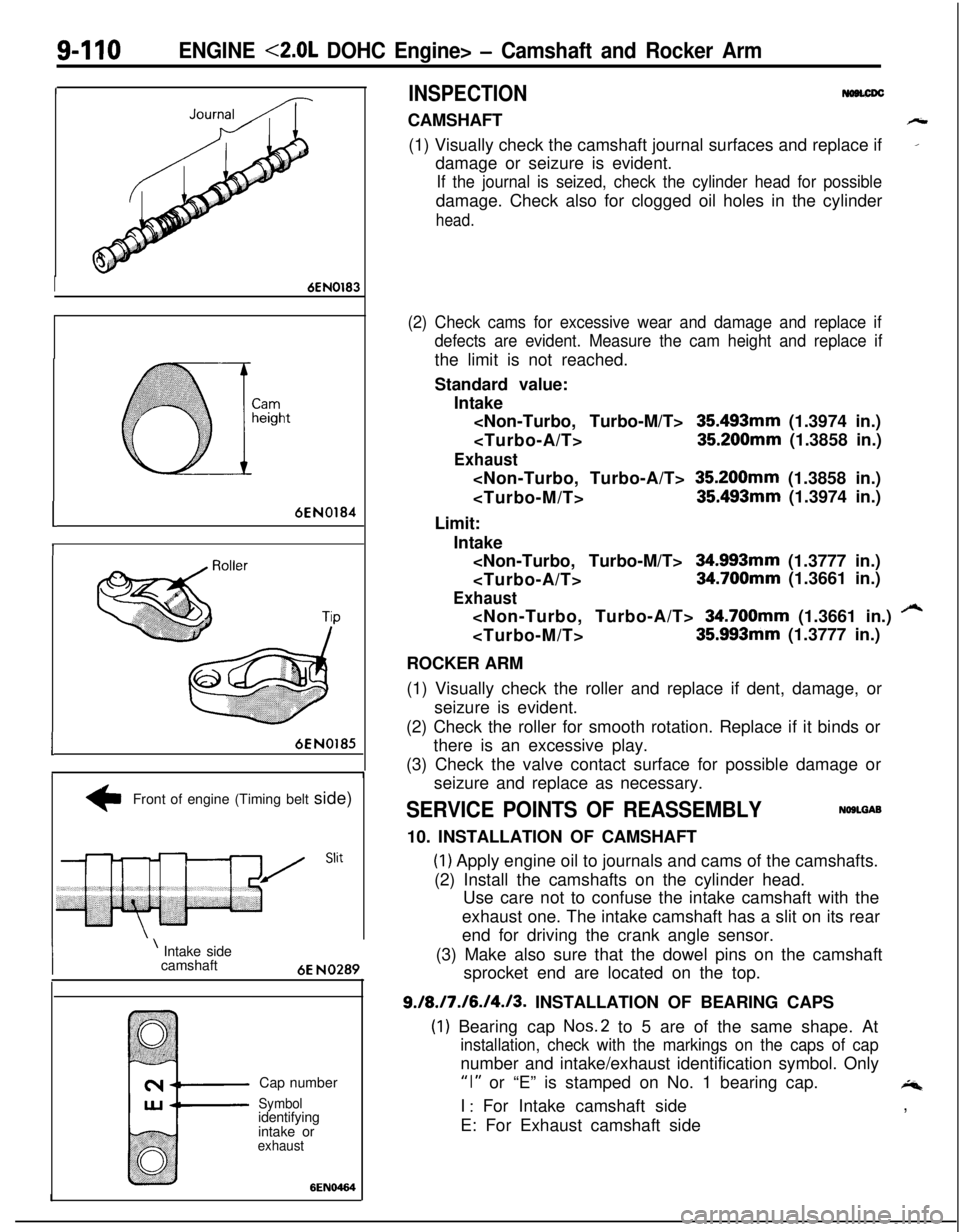
9-110ENGINE <2.0L DOHC Engine> - Camshaft and Rocker Arm
I
I6EN0183
I6EN0184
I
I6EN0185
,I
+Front of engine (Timing belt side)
WIB’ S’it
’ Intake side
camshaft
6E NO289Cap number
Symbolidentifying
intake or
exhaust6EN6464
I
INSPECTIONCAMSHAFT
h(1) Visually check the camshaft journal surfaces and replace if
_damage or seizure is evident.
If the journal is seized, check the cylinder head for possibledamage. Check also for clogged oil holes in the cylinder
head.
(2) Check cams for excessive wear and damage and replace if
defects are evident. Measure the cam height and replace ifthe limit is not reached.
Standard value:
Intake
35493mm (1.3974 in.)
35.200mm (1.3858 in.)
Exhaust 35.200mm (1.3858 in.)
35.493mm (1.3974 in.)
Limit:
Intake
34.993mm (1.3777 in.)
34.700mm (1.3661 in.)
Exhaust 34.700mm (1.3661 in.)
/“435.993mm (1.3777 in.)
ROCKER ARM
(1) Visually check the roller and replace if dent, damage, or
seizure is evident.
(2) Check the roller for smooth rotation. Replace if it binds or
there is an excessive play.
(3) Check the valve contact surface for possible damage or
seizure and replace as necessary.
SERVICE POINTS OF REASSEMBLYNOSLGAB10. INSTALLATION OF CAMSHAFT
(1) Apply engine oil to journals and cams of the camshafts.
(2) Install the camshafts on the cylinder head.
Use care not to confuse the intake camshaft with the
exhaust one. The intake camshaft has a slit on its rear
end for driving the crank angle sensor.
(3) Make also sure that the dowel pins on the camshaft
sprocket end are located on the top.
9./8./7./6./4./3. INSTALLATION OF BEARING CAPS
(1) Bearing cap Nos.2 to 5 are of the same shape. At
installation, check with the markings on the caps of capnumber and intake/exhaust identification symbol. Only
“I” or “E” is stamped on No. 1 bearing cap.4I
: For Intake camshaft side
E: For Exhaust camshaft side,
Page 395 of 1216
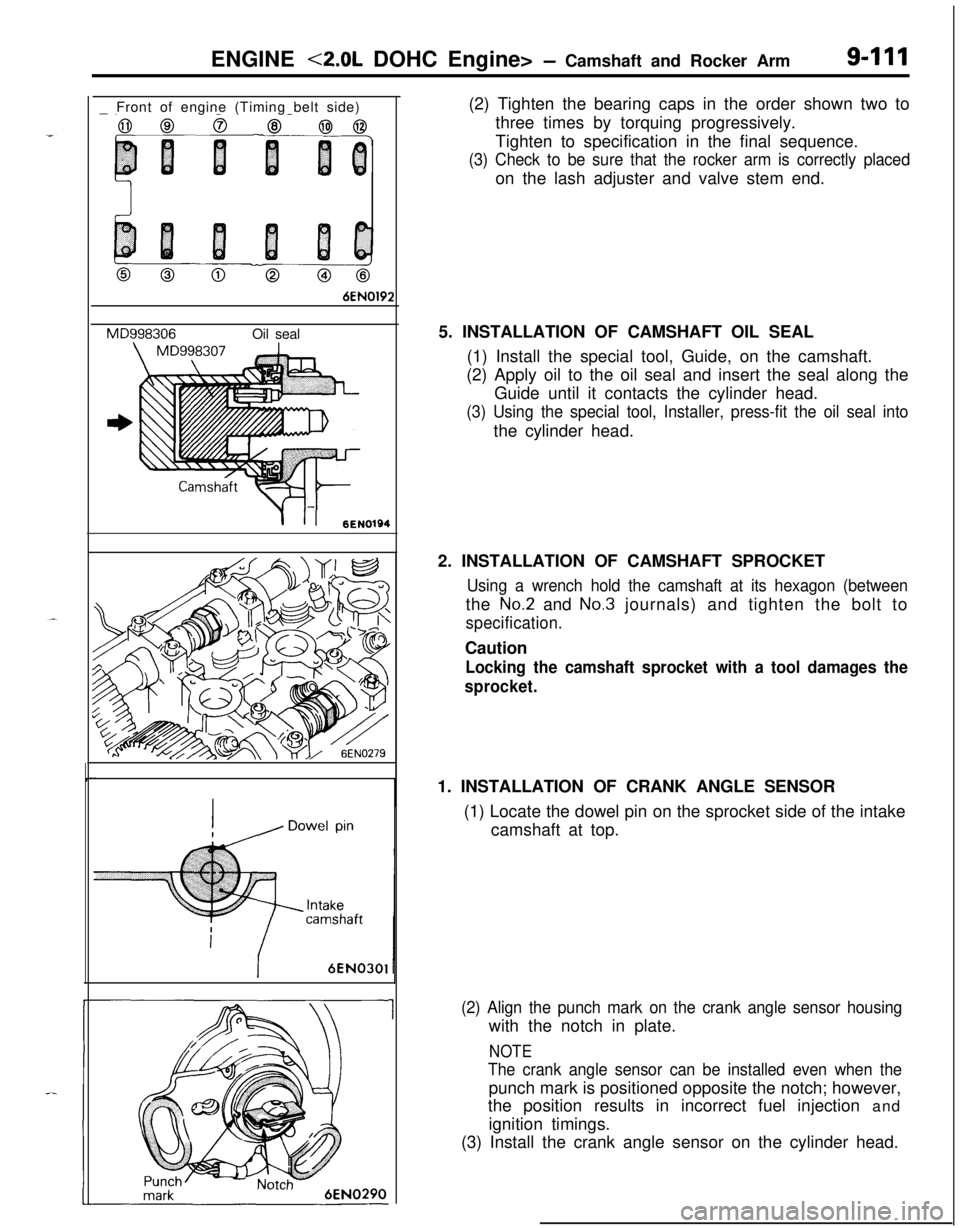
ENGINE <2.0L DOHC Engine> - Camshaft and Rocker Arm9-111_ Front of engine (Timing belt side)
0 Co@
6EN0192
MD998306Oil seal
-
Y-II6ENI01946EN030’
1(2) Tighten the bearing caps in the order shown two to
three times by torquing progressively.
Tighten to specification in the final sequence.
(3) Check to be sure that the rocker arm is correctly placedon the lash adjuster and valve stem end.
5. INSTALLATION OF CAMSHAFT OIL SEAL
(1) Install the special tool, Guide, on the camshaft.
(2) Apply oil to the oil seal and insert the seal along the
Guide until it contacts the cylinder head.
(3) Using the special tool, Installer, press-fit the oil seal intothe cylinder head.
2. INSTALLATION OF CAMSHAFT SPROCKET
Using a wrench hold the camshaft at its hexagon (betweenthe
No.2 and No.3 journals) and tighten the bolt to
specification.Caution
Locking the camshaft sprocket with a tool damages the
sprocket.1. INSTALLATION OF CRANK ANGLE SENSOR
(1) Locate the dowel pin on the sprocket side of the intake
camshaft at top.
(2) Align the punch mark on the crank angle sensor housingwith the notch in plate.
NOTE
The crank angle sensor can be installed even when thepunch mark is positioned opposite the notch; however,
the position results in incorrect fuel injection and
ignition timings.
(3) Install the crank angle sensor on the cylinder head.
Page 396 of 1216
9-112ENGINE <2.0L DOHC Engine> - Cylinder Head and ValveCYLINDER HEAD AND VALVE
DISASSEMBLY ANDREASSEMBLYNewlie6
Disassembly steps
Cylinder head boltWasher
r$!$zr head
Retainer lock
Valve spring retainer
Valve spring
Intake valve
Retainer lock
Valve spring retainer
Valve spring
Exhaust valve
Valve stem seal
Valve spring seat
Valve stem seal
Valve spring seat
Intake valve guide
Exhaust valve guide
Intake valve seat
Exhaust valve seat
.
6E NO196
!??everse the disassembly procedures to reassemble.(2) +e : Refer to “Service Points of Disassembly”.(3) H : Refer to “Service Points of Reassembly”.(4) m : Non-reusable parts
Page 397 of 1216
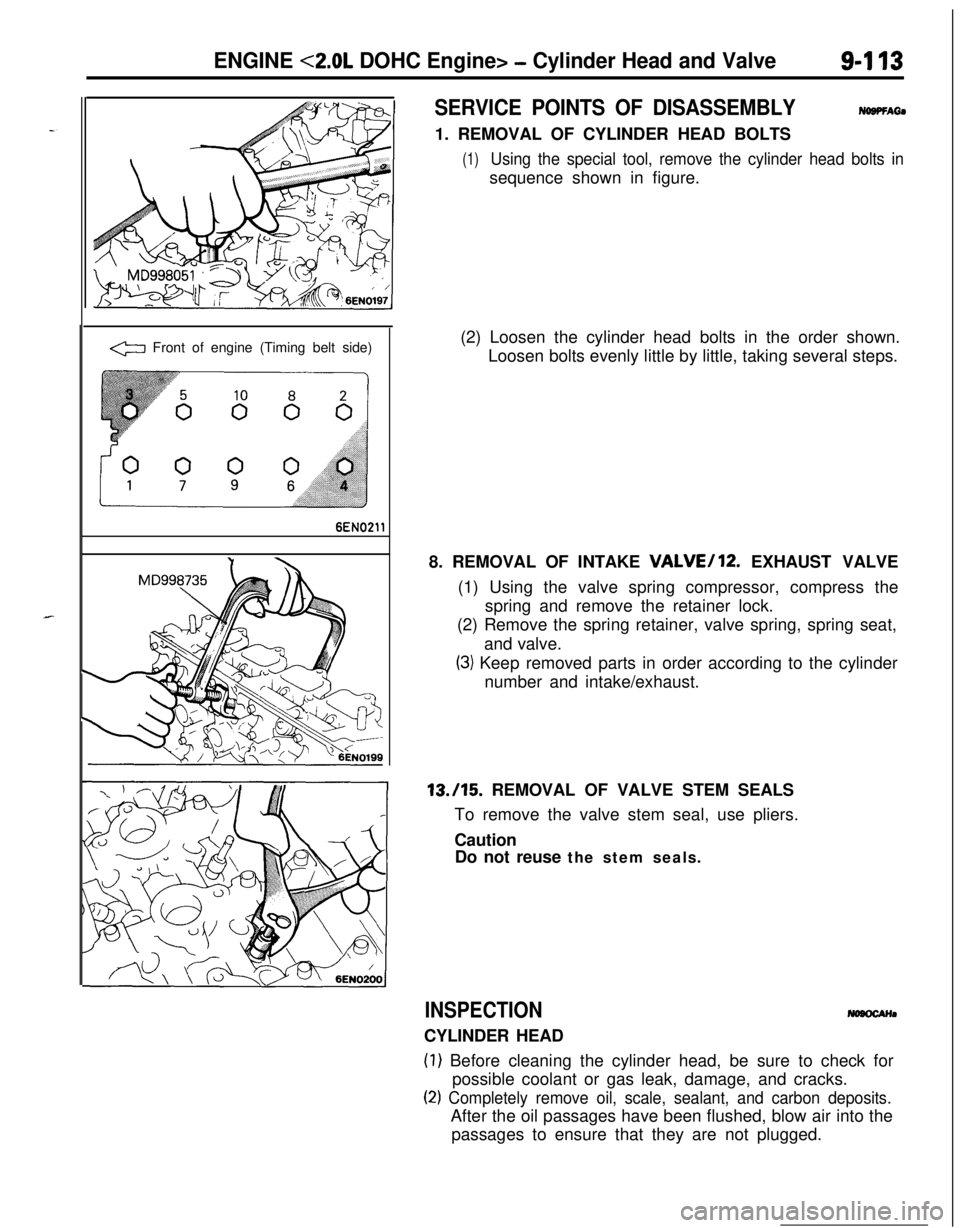
ENGINE <2.0L DOHC Engine> - Cylinder Head and Valve9-l 13
.
.
a Front of engine (Timing belt side)
6EN0211
SERVICE POINTS OF DISASSEMBLYNOBPFAti1. REMOVAL OF CYLINDER HEAD BOLTS
(1)Using the special tool, remove the cylinder head bolts insequence shown in figure.
(2) Loosen the cylinder head bolts in the order shown.
Loosen bolts evenly little by little, taking several steps.
8. REMOVAL OF INTAKE
VALVE/12. EXHAUST VALVE
(1) Using the valve spring compressor, compress the
spring and remove the retainer lock.
(2) Remove the spring retainer, valve spring, spring seat,
and valve.
(3) Keep removed parts in order according to the cylinder
number and intake/exhaust.13./15. REMOVAL OF VALVE STEM SEALS
To remove the valve stem seal, use pliers.
Caution
Do not reuse the stem seals.
INSPECTIONCYLINDER HEAD
(1) Before cleaning the cylinder head, be sure to check for
possible coolant or gas leak, damage, and cracks.
(2) Completely remove oil, scale, sealant, and carbon deposits.After the oil passages have been flushed, blow air into the
passages to ensure that they are not plugged.
Page 398 of 1216
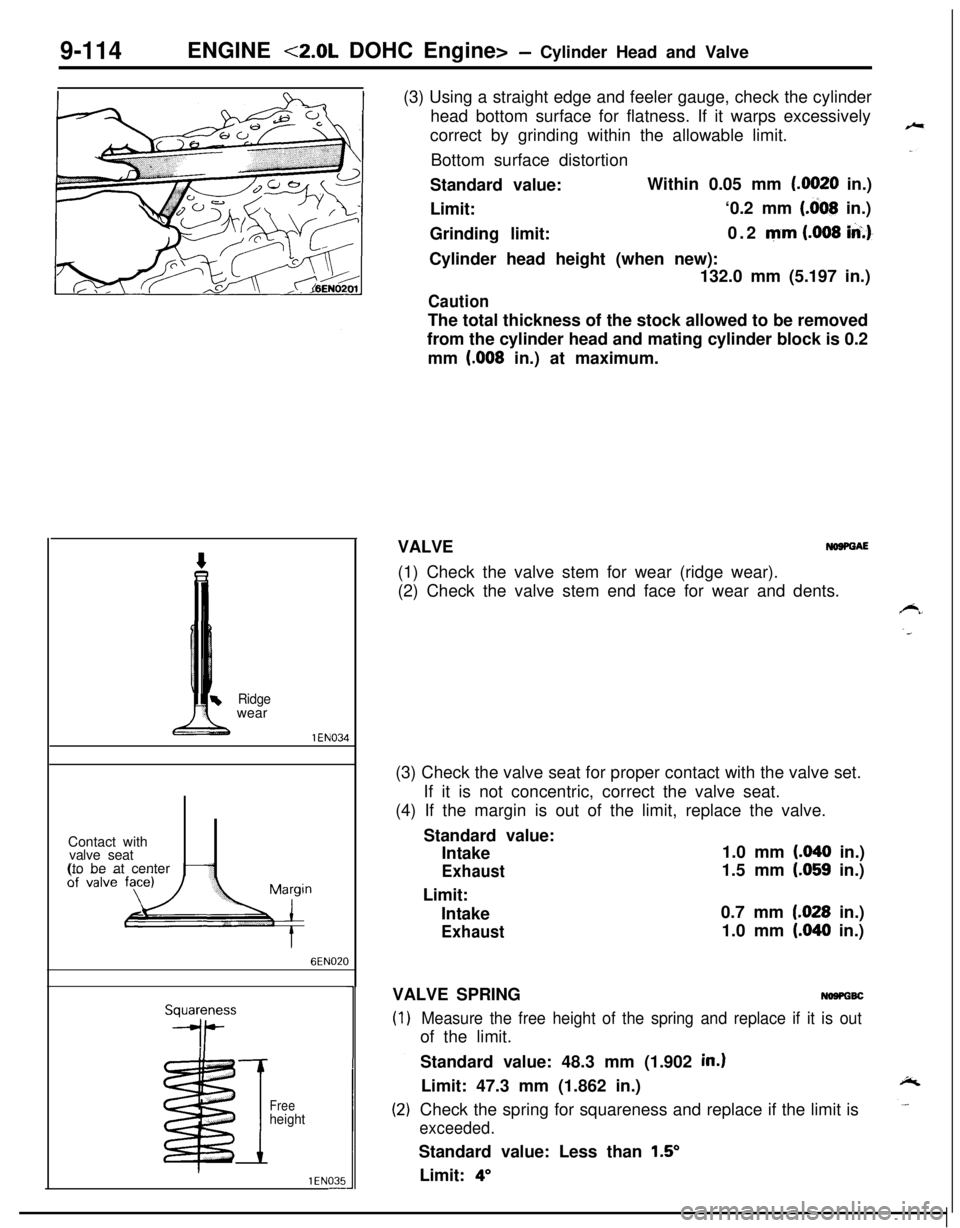
9-114ENGINE <2.0L DOHC Engine> - Cylinder Head and Valve
Ridgewear
1 EN034Contact with
valve seat
(to be at center
6EN020
I
Freeheight
1 EN035-(3) Using a straight edge and feeler gauge, check the cylinder
head bottom surface for flatness. If it warps excessively
correct by grinding within the allowable limit.
Bottom surface distortion
Standard value:Within 0.05 mm
(.0020 in.)
Limit:‘0.2 mm
(.dO8 in.)
Grinding limit:0.2 mm
(.008 iA.)-Cylinder head height (when new):
132.0 mm (5.197 in.)
CautionThe total thickness of the stock allowed to be removed
from the cylinder head and mating cylinder block is 0.2
mm
(.008 in.) at maximum.
VALVE
NOSPGAE(1) Check the valve stem for wear (ridge wear).
(2) Check the valve stem end face for wear and dents.
(3) Check the valve seat for proper contact with the valve set.
If it is not concentric, correct the valve seat.
(4) If the margin is out of the limit, replace the valve.
Standard value:
Intake1.0 mm
(.040 in.)
Exhaust1.5 mm (.059 in.)
Limit:
Intake0.7 mm
1.028 in.)
Exhaust1.0 mm (.040 in.)
VALVE SPRING
NOSPGBC
Measure the free height of the spring and replace if it is outof the limit.
Standard value: 48.3 mm (1.902
in.)Limit: 47.3 mm (1.862 in.)
Check the spring for squareness and replace if the limit is
exceeded.Standard value: Less than
1.5’Limit:
4”
Page 399 of 1216
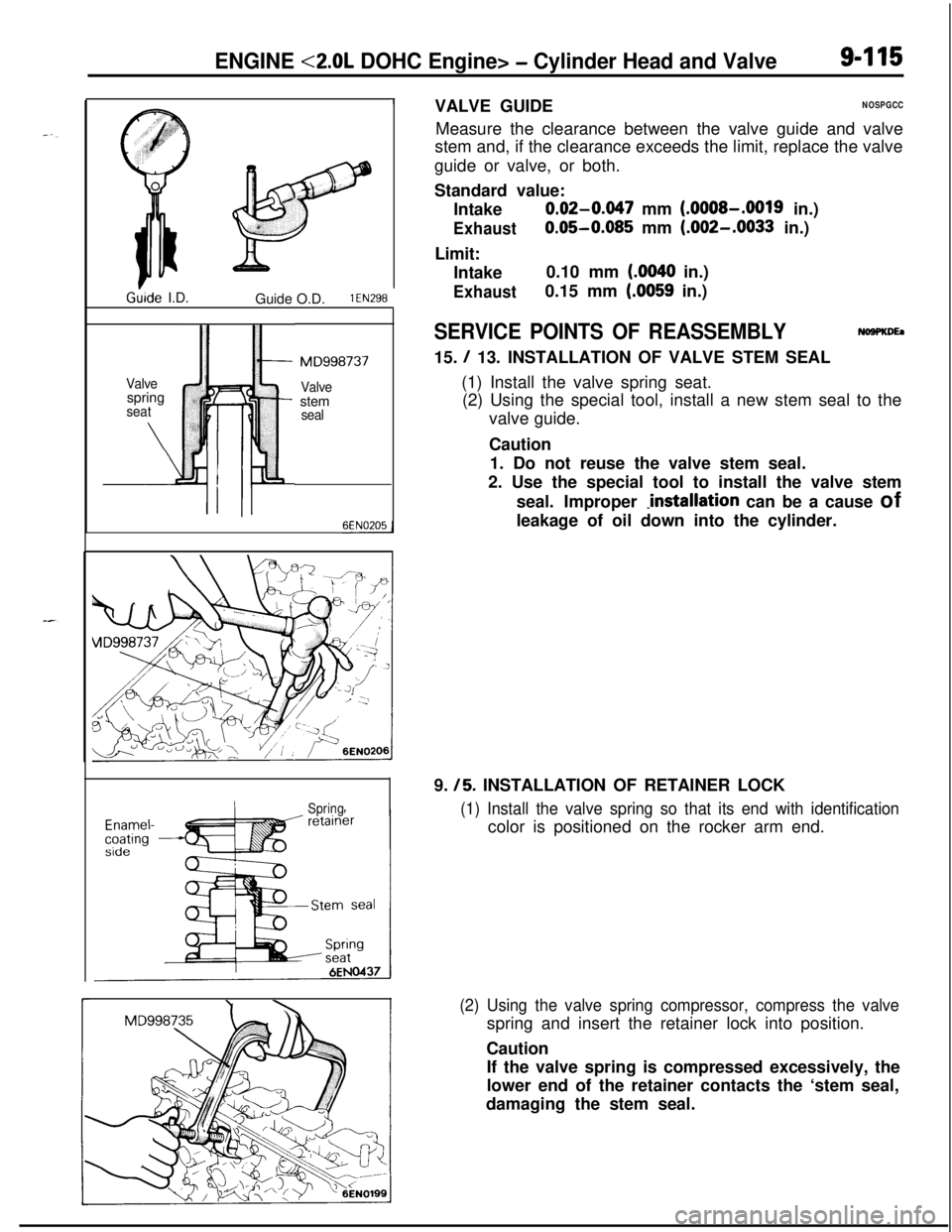
ENGINE <2.0L DOHC Engine> - Cylinder Head and Valve9-115
1Ghde I.D.
Guide O.D.
1 EN298
Valve
ispring
*seat
\ Iril
: :
MD998737
Valvestem
seal
SpringVALVE GUIDE
NOSPGCCMeasure the clearance between the valve guide and valve
stem and, if the clearance exceeds the limit, replace the valve
guide or valve, or both.
Standard value:
Intake
0.02-0.047 mm (.OOOS-.0019 in.)
Exhaust0.05-0.085 mm (.002-.0033 in.)
Limit:
Intake0.10 mm
(.0040 in.)
Exhaust0.15 mm (.0059 in.)
SERVICE POINTS OF REASSEMBLYNoaPKDEa15.
/ 13. INSTALLATION OF VALVE STEM SEAL
(1) Install the valve spring seat.
(2) Using the special tool, install a new stem seal to the
valve guide.
Caution
1. Do not reuse the valve stem seal.
2. Use the special tool to install the valve stem
seal. Improper
Jnstallation can be a cause of
leakage of oil down into the cylinder.
9.
/5. INSTALLATION OF RETAINER LOCK
(1) Install the valve spring so that its end with identificationcolor is positioned on the rocker arm end.
(2) Using the valve spring compressor, compress the valvespring and insert the retainer lock into position.
Caution
If the valve spring is compressed excessively, the
lower end of the retainer contacts the ‘stem seal,
damaging the stem seal.
Page 400 of 1216
9416
I
ENGINE <2.0L DOHC Engine> - Cylinder Head and Valve
I1. INSTALLATION OF CYLINDER HEAD BOLTS
(1) Using the special tool, tighten the cylinder head bolts.
G Front of engine (Timing belt side)(2) Tighten the cylinder head bolts in the sequence shown.
Each bolt should be tightened in two to three steps,
torquing progressively. Tighten to specified torque in
the final sequence.