Page 345 of 1216
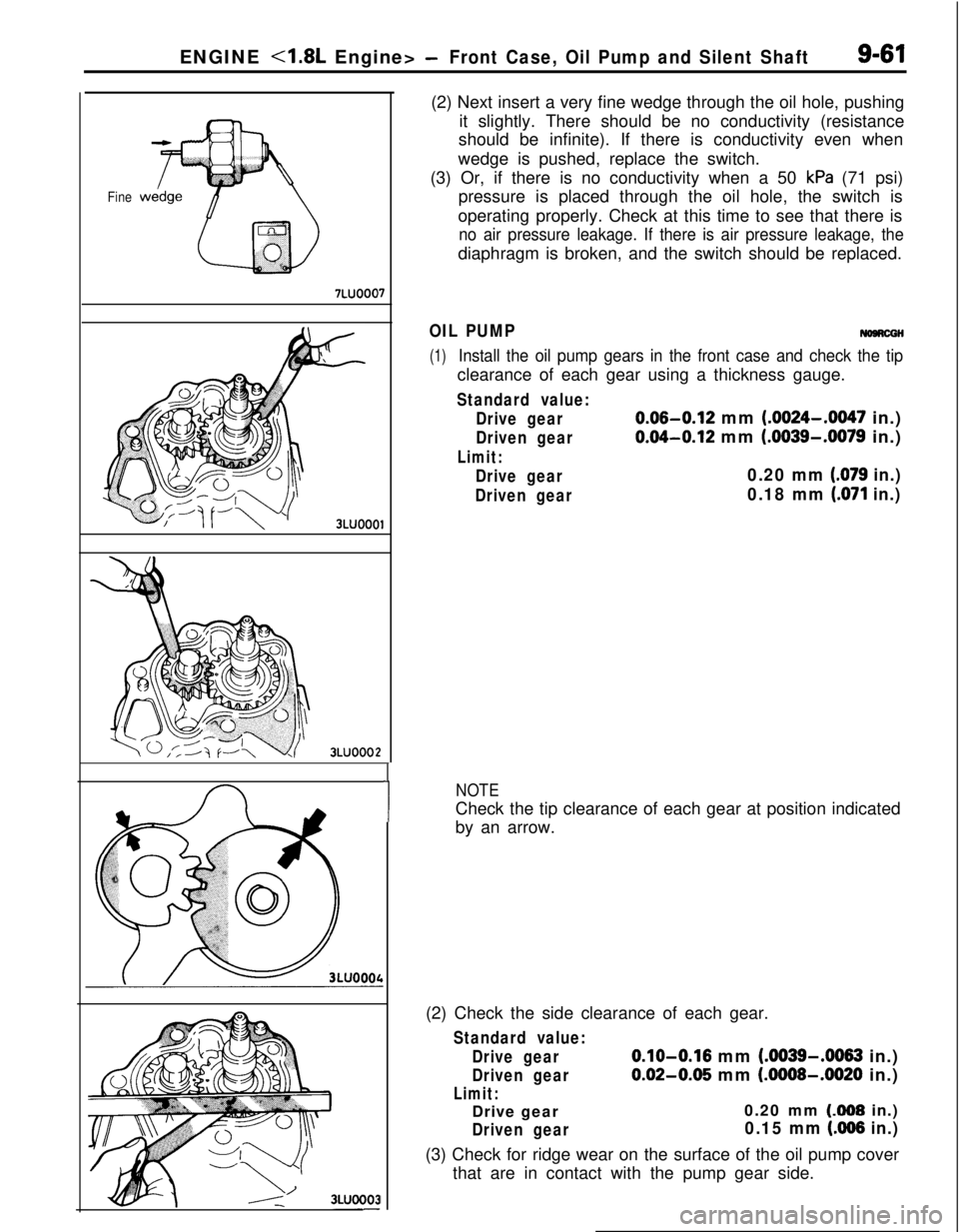
ENGINE <1.8L Engine> -Front Case, Oil Pump and Silent Shaft9-61
Fine
7LUOOO7
3LUOOOl
3LUOOO2
I
1(2) Next insert a very fine wedge through the oil hole, pushing
it slightly. There should be no conductivity (resistance
should be infinite). If there is conductivity even when
wedge is pushed, replace the switch.
(3) Or, if there is no conductivity when a 50
kPa (71 psi)
pressure is placed through the oil hole, the switch is
operating properly. Check at this time to see that there is
no air pressure leakage. If there is air pressure leakage, thediaphragm is broken, and the switch should be replaced.
OIL PUMPNomcGH
(1)Install the oil pump gears in the front case and check the tipclearance of each gear using a thickness gauge.
Standard value:
Drive gear
0.06-0.12 mm (.0024-.0047 in.)
Driven gear0.04-0.12 mm (.0039-.0079 in.)
Limit:
Drive gear0.20 mm (.079 in.)
Driven gear0.18 mm (.071 in.)
NOTECheck the tip clearance of each gear at position indicated
by an arrow.
(2) Check the side clearance of each gear.
Standard value:
Drive gear
0.10-0.16 mm (.0039-.0063 in.)
Driven gear0.02-0.05 mm (.0008-.0020 in.)
Limit:Drive gear0.20 mm (308 in.)
Driven gear0.15 mm (AI66 in.)(3) Check for ridge wear on the surface of the oil pump cover
that are in contact with the pump gear side.
Page 346 of 1216
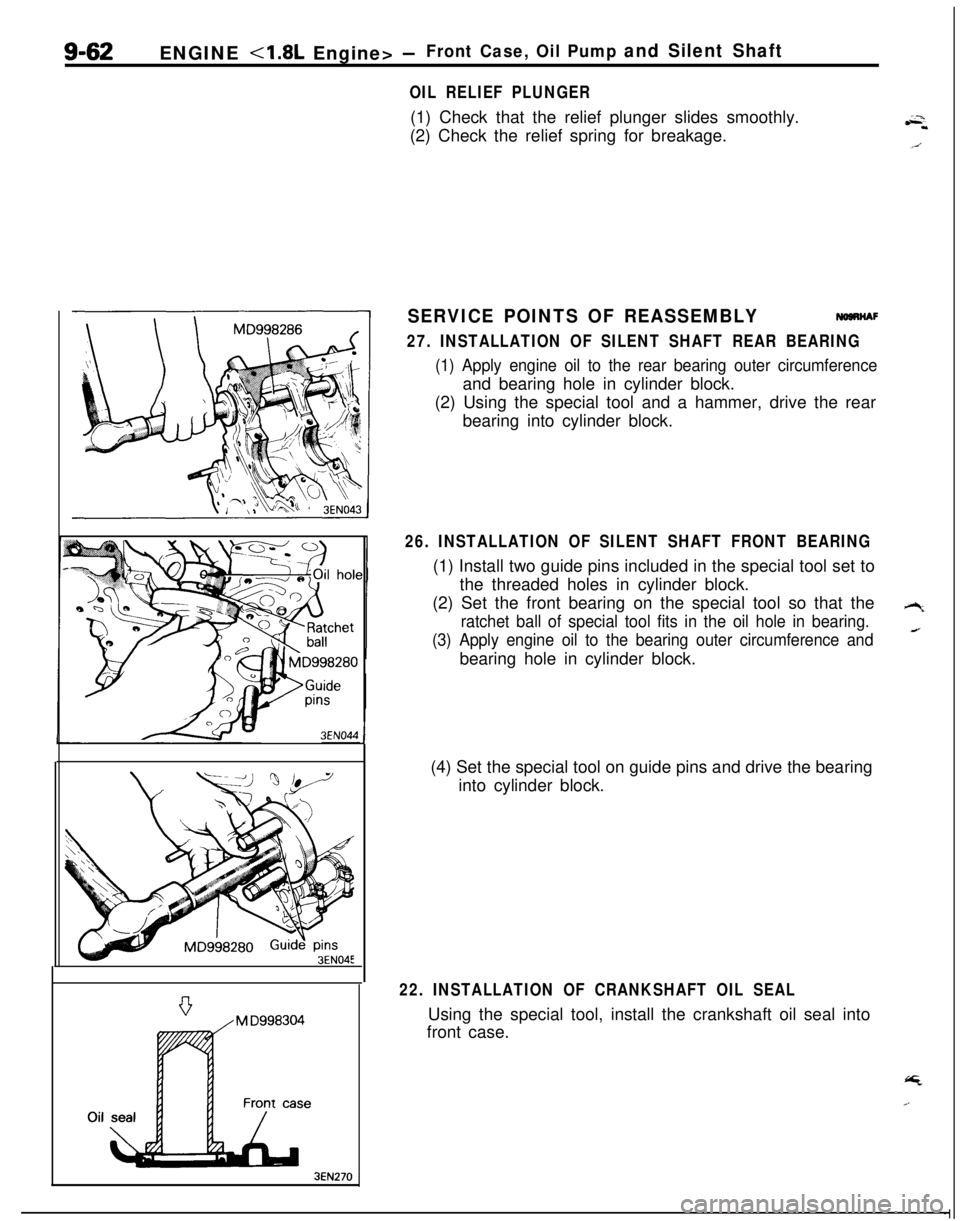
9-62ENGINE -4.8L Engine> -Front Case, Oil Pump and Silent Shaft
OIL RELIEF PLUNGER(1) Check that the relief plunger slides smoothly.
(2) Check the relief spring for breakage.
3EN044J
MD998280
3EN270
0M D998304
SERVICE POINTS OF REASSEMBLYNOBRHAF
27. INSTALLATION OF SILENT SHAFT REAR BEARING
(1) Apply engine oil to the rear bearing outer circumferenceand bearing hole in cylinder block.
(2) Using the special tool and a hammer, drive the rear
bearing into cylinder block.
26. INSTALLATION OF SILENT SHAFT FRONT BEARING(1) Install two guide pins included in the special tool set to
the threaded holes in cylinder block.
(2) Set the front bearing on the special tool so that the
ratchet ball of special tool fits in the oil hole in bearing.
(3) Apply engine oil to the bearing outer circumference andbearing hole in cylinder block.
(4) Set the special tool on guide pins and drive the bearing
into cylinder block.
22. INSTALLATION OF CRANKSHAFT OIL SEALUsing the special tool, install the crankshaft oil seal into
front case.
Page 347 of 1216
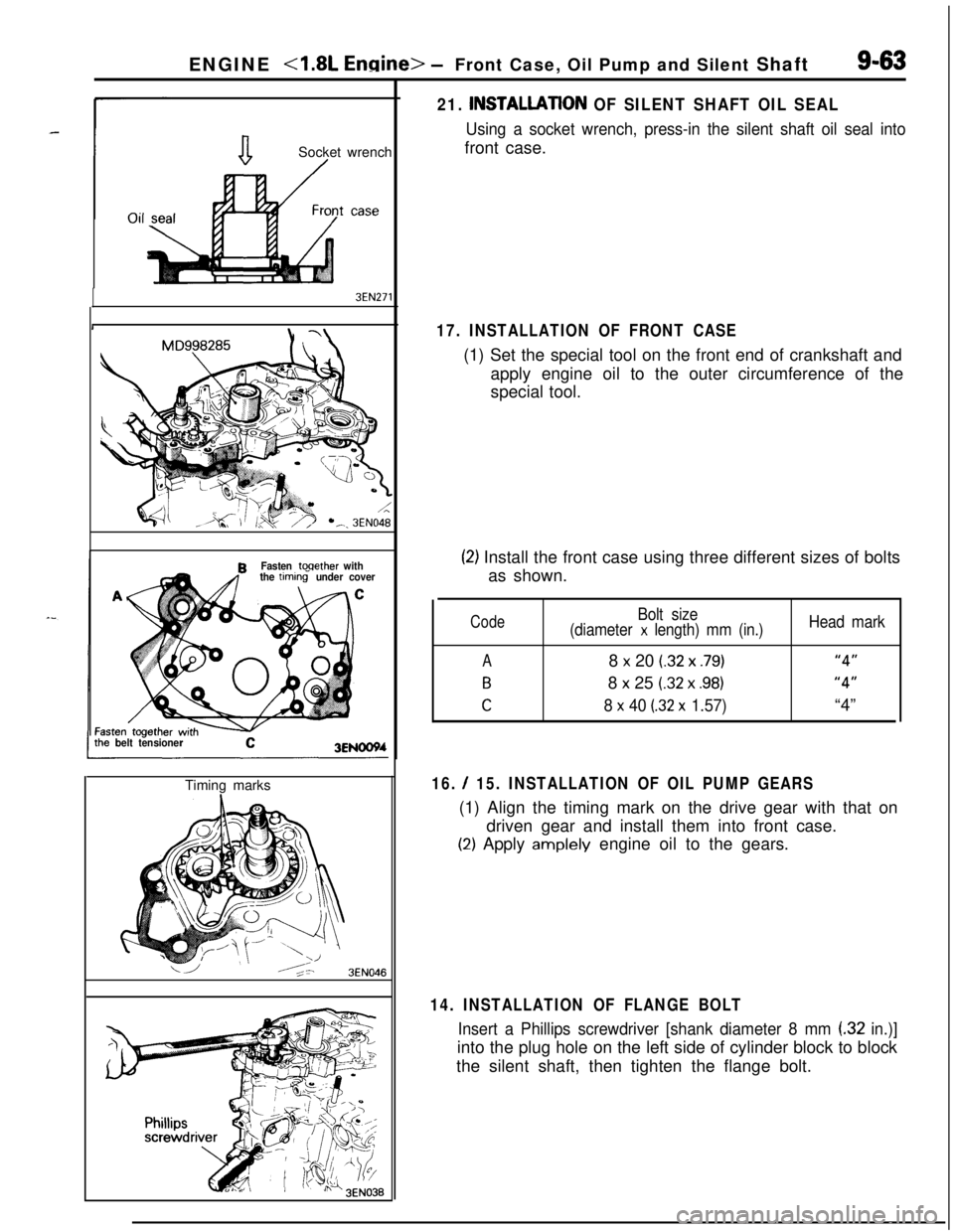
ENGINE <1.8L Engine> -Front Case, Oil Pump and Silent Shaft9-63
aSocket wrench/
3EN271
MD998285R
Fasten toqether with
the timtins under cover
C
belt tensioner3ENOOWTiming marks
16. / 15. INSTALLATION OF OIL PUMP GEARS(1) Align the timing mark on the drive gear with that on
driven gear and install them into front case.
(2) Apply amplely engine oil to the gears.
3EN046
21. INSTALLATlON OF SILENT SHAFT OIL SEAL
Using a socket wrench, press-in the silent shaft oil seal intofront case.
17. INSTALLATION OF FRONT CASE(1) Set the special tool on the front end of crankshaft and
apply engine oil to the outer circumference of the
special tool.
(2) Install the front case using three different sizes of bolts
as shown.
Code
A
B
C
Bolt size
(diameter x length) mm (in.)8
x 20 (.32 x .79)8
x 25 (.32 x .98)
8 x 40 (32 x 1.57)
Head mark
“4”
“4”“4”
14. INSTALLATION OF FLANGE BOLT
Insert a Phillips screwdriver [shank diameter 8 mm (32 in.)]into the plug hole on the left side of cylinder block to block
the silent shaft, then tighten the flange bolt.
Page 348 of 1216
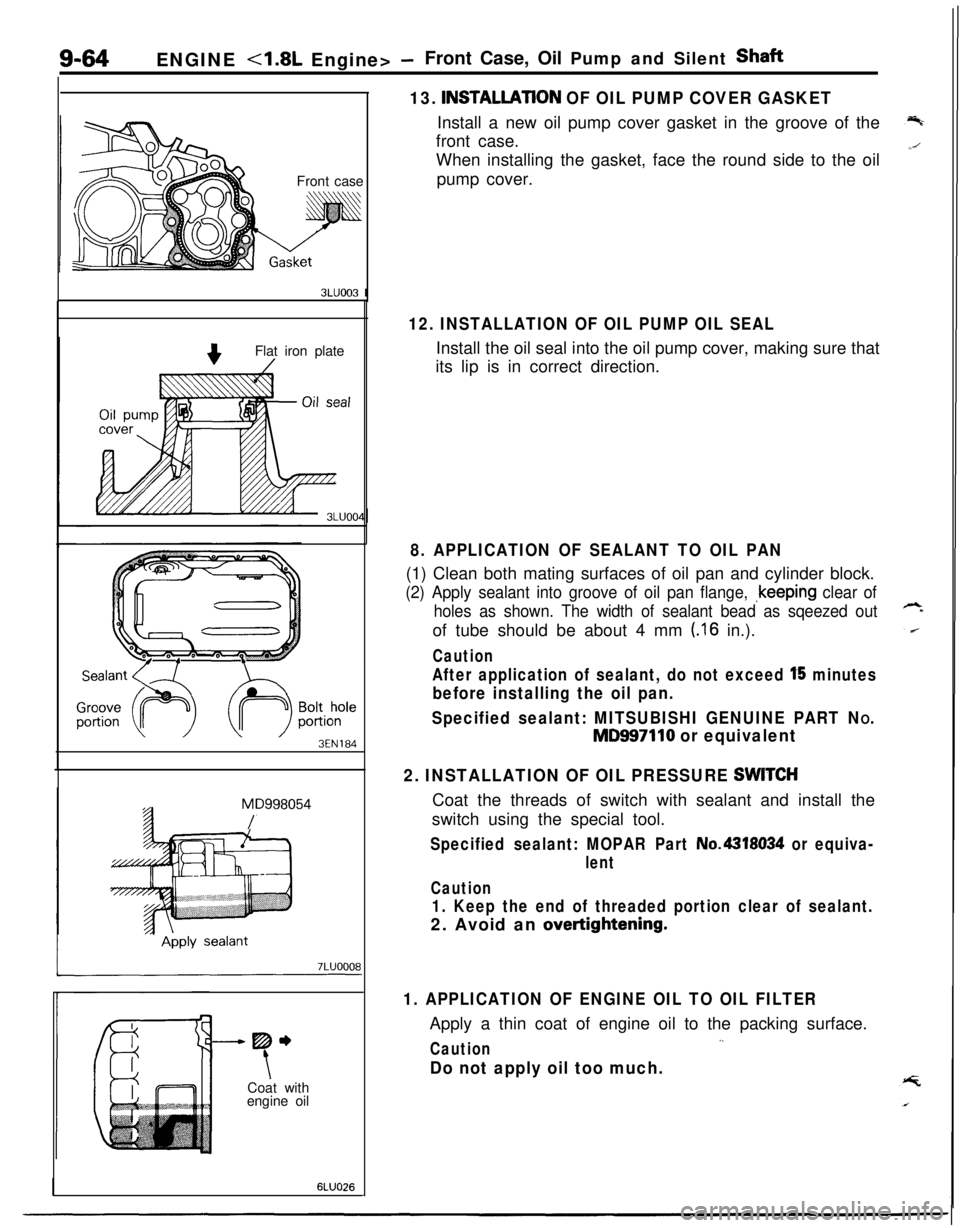
9-64ENGINE 4.8L Engine> -Front Case, Oil Pump and Silent Shaft
13.
INSTALLATlON OF OIL PUMP COVER GASKETInstall a new oil pump cover gasket in the groove of the
front case.
Front caseWhen installing the gasket, face the round side to the oil
pump cover.
3LUOO3 I
Flat iron plate
3EN184
MD998054
/
-----me
tCoat with
engine oil
6LUO26
12. INSTALLATION OF OIL PUMP OIL SEALInstall the oil seal into the oil pump cover, making sure that
its lip is in correct direction.
8. APPLICATION OF SEALANT TO OIL PAN(1) Clean both mating surfaces of oil pan and cylinder block.
(2) Apply sealant into groove of oil pan flange, ~keeping clear of
holes as shown. The width of sealant bead as sqeezed outof tube should be about 4 mm
(.I6 in.).
Caution
After application of sealant, do not exceed l’5 minutes
before installing the oil pan.
Specified sealant: MITSUBISHI GENUINE PART N
O.
MD997110 or equivalent
2. INSTALLATION OF OIL PRESSURE
SWlTCHCoat the threads of switch with sealant and install the
switch using the special tool.
Specified sealant: MOPAR Part No.4318034 or equiva-
lent
Caution
1. Keep the end of threaded portion clear of sealant.2. Avoid an
overtightening.
1. APPLICATION OF ENGINE OIL TO OIL FILTERApply a thin coat of engine oil to the packing surface.
,.Caution
Do not apply oil too much.
Page 349 of 1216
ENGINE <1.8L Engine> - Piston and Connecting Rod9-65
PISTON AND CONNECTING ROD
S--DISASSEMBLY AND REASSEMBLYMaTEA
Disassembly steps
l 4Inspection of connecting rod big end side
clearance1. Nut
+e I)+ 2. Connecting rod cap
3. Cpnnecting rod bearing11. Piston12. Connecting rod
l *4. Piston and connecting rod assembly5. Connecting rod bearing6. Bolt
++I)+ 7. No. 1 piston ring+e l +8. No. 2 piston ringl * 9. Oil ring10. Piston pin
NOTE(1) Reverse the disassembly procedures to reassemble.
(2) 4e : Refer to “Service Points of Disassembly”.
(3) l + : Refer to “Service Points of Reassembly”.
3EN275
Page 350 of 1216
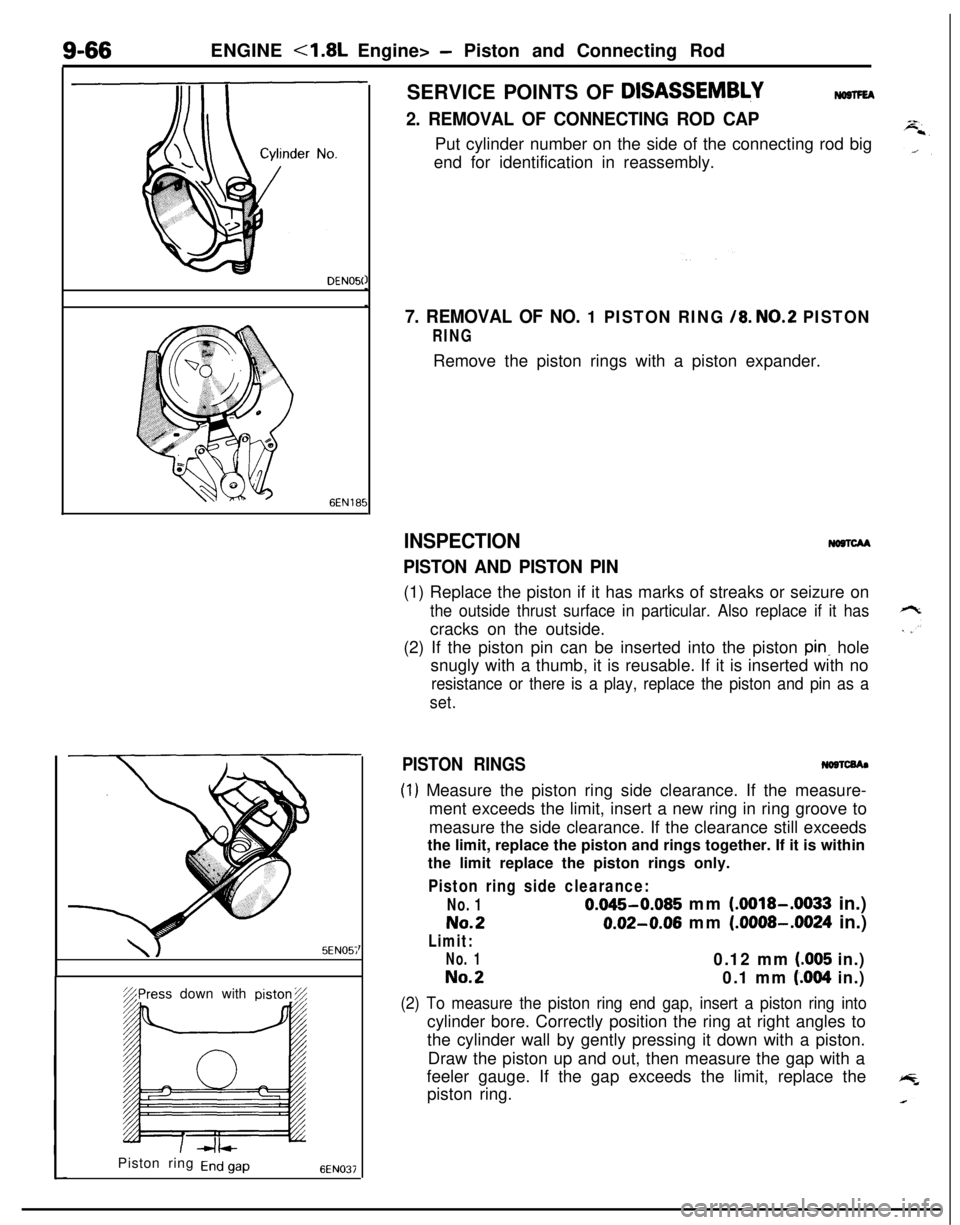
9-66ENGINE <1.8L Engine> - Piston and Connecting Rod
DENOSC
\J5EN05;%Press down withpiston%
Piston ring
End gap6EN037SERVICE POINTS OF
DlSASSEMB&Y
2. REMOVAL OF CONNECTING ROD CAPPut cylinder number on the side of the connecting rod big
end for identification in reassembly.
7. REMOVAL OF NO. 1 PISTON RING /8. NO.2 PISTON
RINGRemove the piston rings with a piston expander.
INSPECTION
PISTON AND PISTON PIN
NoncM(1) Replace the piston if it has marks of streaks or seizure on
the outside thrust surface in particular. Also replace if it hascracks on the outside.
(2) If the piston pin can be inserted into the piston
pink hole
snugly with a thumb, it is reusable. If it is inserted with no
resistance or there is a play, replace the piston and pin as a
set.
PISTON RINGS
(1) Measure the piston ring side clearance. If the measure-
ment exceeds the limit, insert a new ring in ring groove to
measure the side clearance. If the clearance still exceeds
the limit, replace the piston and rings together. If it is within
the limit replace the piston rings only.
Piston ring side clearance:
No. 10.045-0.085 mm (.0018-.0033 in.)
No.20.02-0.06 mm (.0008-.0024 in.)
Limit:
No. 10.12 mm (.005 in.)
No.20.1 mm (.004 in.)
(2) To measure the piston ring end gap, insert a piston ring intocylinder bore. Correctly position the ring at right angles to
the cylinder wall by gently pressing it down with a piston.
Draw the piston up and out, then measure the gap with a
feeler gauge. If the gap exceeds the limit, replace the
piston ring.
Page 351 of 1216
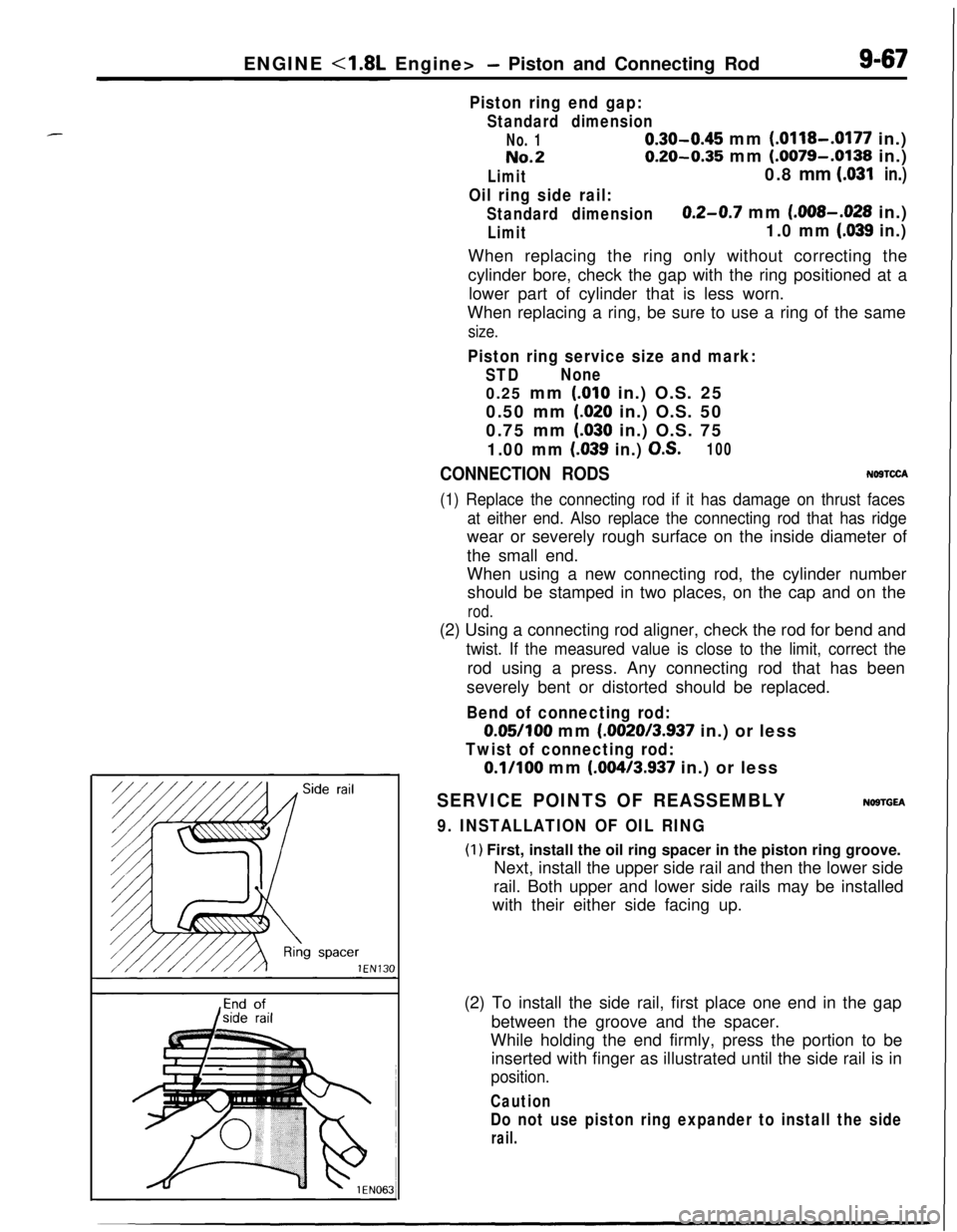
ENGINE <1.8L Engine>- Piston and Connecting Rod9-67
Piston ring end gap:
Standard dimension
No. 10.30-0.45 mm (.0118-.0177 in.)
No.20.20-0.35 mm (.0079-.0138 in.)
Limit0.8 mm LO31in.)
Oil ring side rail:
Standard dimension0.2-0.7 mm (.008-.028 in.)
Limit1.0 mm (.039 in.)When replacing the ring only without correcting the
cylinder bore, check the gap with the ring positioned at a
lower part of cylinder that is less worn.
When replacing a ring, be sure to use a ring of the same
size.
Piston ring service size and mark:
STDNone0.25 mm
(.OlO in.) O.S. 25
0.50 mm
(020 in.) O.S. 50
0.75 mm
(030 in.) O.S. 75
1.00 mm (039 in.) B.S.100
CONNECTION RODSNOSTCCA
(1) Replace the connecting rod if it has damage on thrust faces
at either end. Also replace the connecting rod that has ridgewear or severely rough surface on the inside diameter of
the small end.
When using a new connecting rod, the cylinder number
should be stamped in two places, on the cap and on the
rod.(2) Using a connecting rod aligner, check the rod for bend and
twist. If the measured value is close to the limit, correct therod using a press. Any connecting rod that has been
severely bent or distorted should be replaced.
Bend of connecting rod:
0.05/100 mm (.0020/3.937 in.) or less
Twist of connecting rod:
O.l/lOO mm (.004/3.937 in.) or less
SERVICE POINTS OF REASSEMBLYNOSTGEA
9. INSTALLATION OF OIL RING
(1) First, install the oil ring spacer in the piston ring groove.
Next, install the upper side rail and then the lower side
rail. Both upper and lower side rails may be installed
with their either side facing up.
(2) To install the side rail, first place one end in the gap
between the groove and the spacer.
While holding the end firmly, press the portion to be
inserted with finger as illustrated until the side rail is in
position.
Caution
Do not use piston ring expander to install the side
rail.
Page 352 of 1216
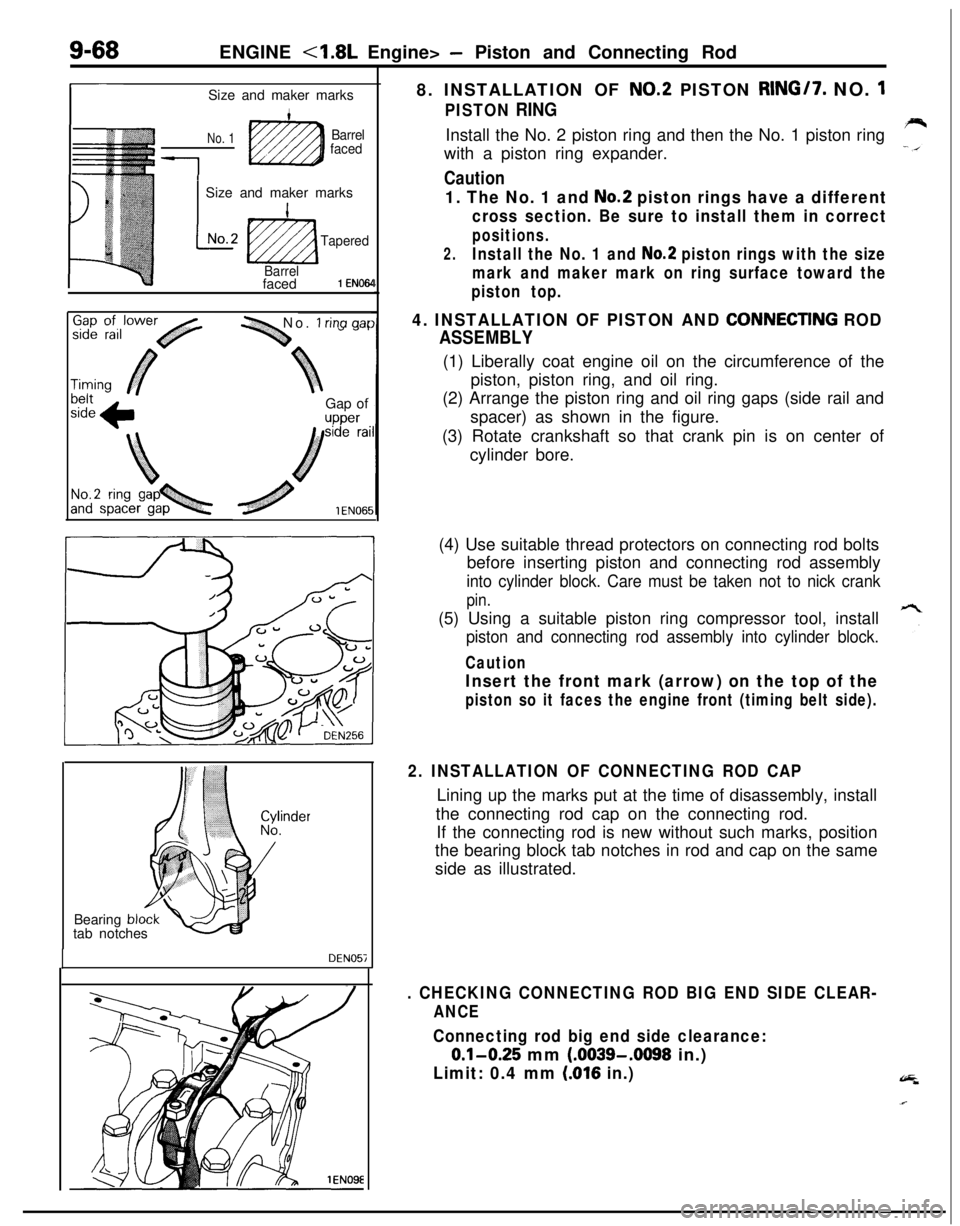
9-68ENGINE <1.8L Engine> - Piston and Connecting Rod
r-Size and maker marks
No. 1Barrel
faced
1
1 Size and maker marks
L
INo.2
ti2zza
Tapered
Barrelfaced
1 EN064
-1 No. 1 rina aarGap of
upper8. INSTALLATION OF
NO.2 PISTON RING/7. NO. 1
PISTON RINGInstall the No. 2 piston ring and then the No. 1 piston ring
with a piston ring expander.
Caution
1. The No. 1 and No.2 piston rings have a different
cross section. Be sure to install them in correct
positions.
2.Install the No. 1 and No.2 piston rings with the size
mark and maker mark on ring surface toward the
piston top.
4. INSTALLATION OF PISTON AND CONNECTlNG ROD
ASSEMBLY(1) Liberally coat engine oil on the circumference of the
piston, piston ring, and oil ring.
(2) Arrange the piston ring and oil ring gaps (side rail and
spacer) as shown in the figure.
(3) Rotate crankshaft so that crank pin is on center of
cylinder bore.
Bearing
bltab notches
DEN057(4) Use suitable thread protectors on connecting rod bolts
before inserting piston and connecting rod assembly
into cylinder block. Care must be taken not to nick crank
pin.(5) Using a suitable piston ring compressor tool, install
piston and connecting rod assembly into cylinder block.
Caution
Insert the front mark (arrow) on the top of the
piston so it faces the engine front (timing belt side).
2. INSTALLATION OF CONNECTING ROD CAPLining up the marks put at the time of disassembly, install
the connecting rod cap on the connecting rod.
If the connecting rod is new without such marks, position
the bearing block tab notches in rod and cap on the same
side as illustrated.
. CHECKING CONNECTING ROD BIG END SIDE CLEAR-
ANCE
Connecting rod big end side clearance:
0.1-0.25 mm (.0039-.0098 in.)
Limit: 0.4 mm (016 in.)