Page 545 of 1216
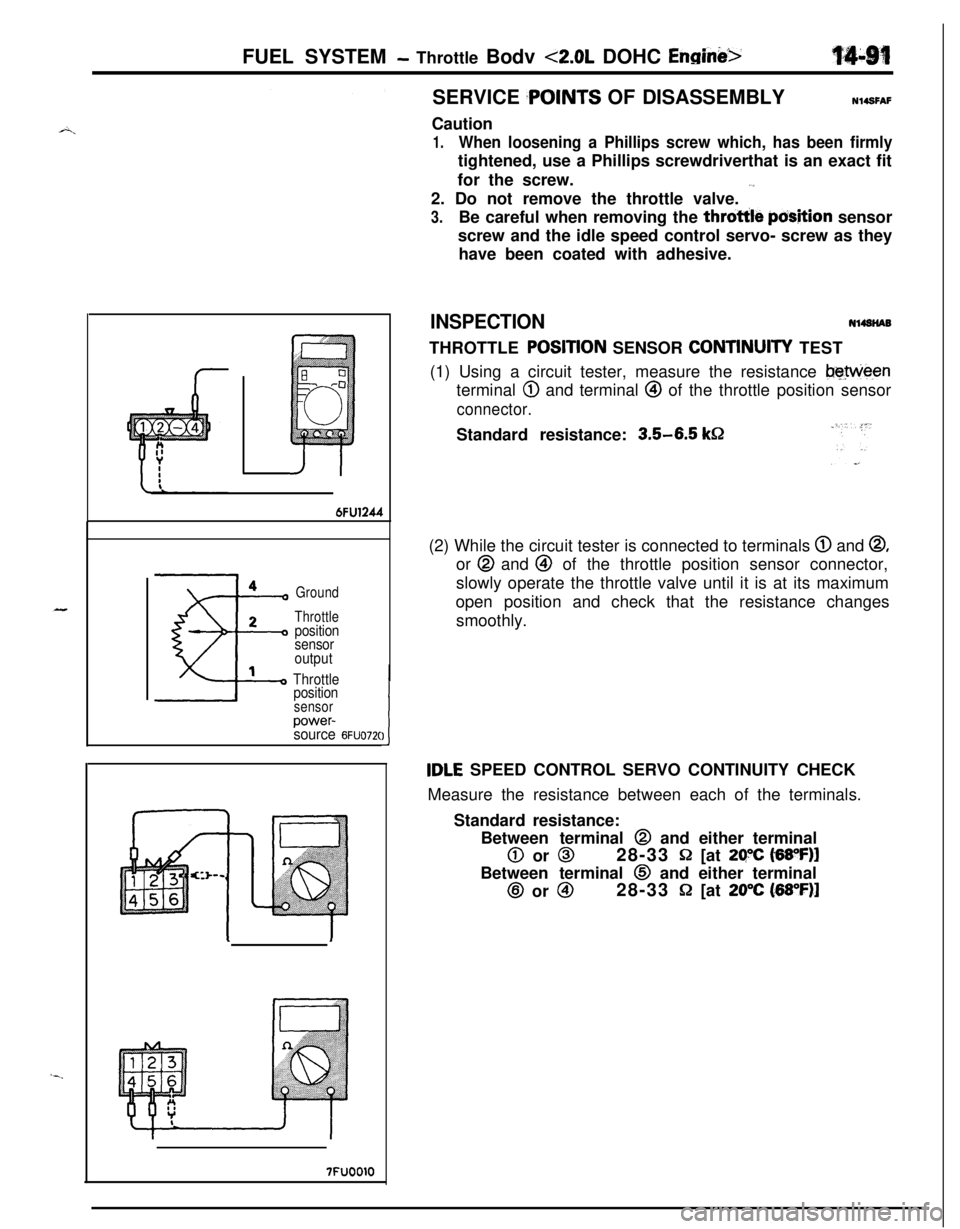
FUEL SYSTEM - Throttle Bodv <2.0L DOHC Erwini+
i
6FU1244
Ground
Throttle
position
sensor
output
Throttle
position
sensorpower-source 6FUO7X
7FUOOlO
ISERVICE
~POINTS OF DISASSEMBLYNl4SFAF
Caution
1.When loosening a Phillips screw which, has been firmlytightened, use a Phillips screwdriverthat is an exact fit
for the screw.
2. Do not remove the throttle valve.
”
3.Be careful when removing the throtite pos?ion sensor
screw and the idle speed control servo- screw as they
have been coated with adhesive.
INSPECTIONNl4SNABTHROTTLE
POStTlON SENSOR CONTtNUlTY TEST
(1) Using a circuit tester, measure the resistance
beweenterminal
@ and terminal @ of the throttle position sensor
connector.Standard resistance:
3.5-6.5 k&2(2) While the circuit tester is connected to terminals
@ and @,or @ and @ of the throttle position sensor connector,
slowly operate the throttle valve until it is at its maximum
open position and check that the resistance changes
smoothly.
tDLE SPEED CONTROL SERVO CONTINUITY CHECK
Measure the resistance between each of the terminals.
Standard resistance:
Between terminal @ and either terminal
0 or 028-33 Q [at 29X t6WF)lBetween terminal
0 and either terminal@ or
@I28-33 P [at 20°C (68”F)l
Page 546 of 1216
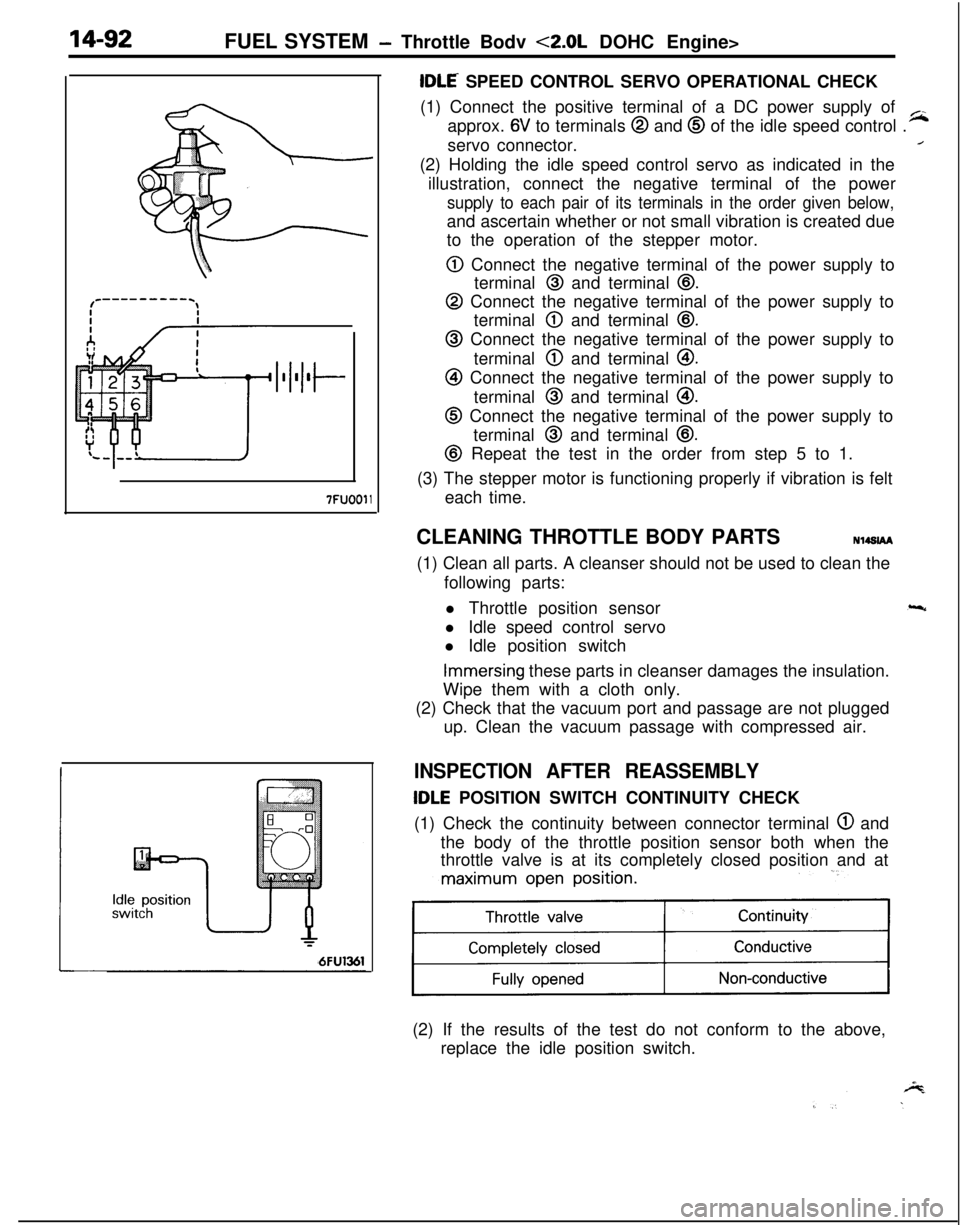
14-92FUEL SYSTEM- Throttle Bodv <2.0L DOHC Engine>
Iw--
7FUOOl I
tDLE SPEED CONTROL SERVO OPERATIONAL CHECK
(1) Connect the positive terminal of a DC power supply of
approx.
6V to terminals @ and @ of the idle speed control .
~servo connector.
/(2) Holding the idle speed control servo as indicated in the
illustration, connect the negative terminal of the power
supply to each pair of its terminals in the order given below,and ascertain whether or not small vibration is created due
to the operation of the stepper motor.
0 Connect the negative terminal of the power supply to
terminal
@ and terminal @.
@ Connect the negative terminal of the power supply to
terminal
@ and terminal @I.
@ Connect the negative terminal of the power supply to
terminal
@ and terminal @I.
@I Connect the negative terminal of the power supply to
terminal
@ and terminal @I.
@ Connect the negative terminal of the power supply to
terminal
@ and terminal @.
@ Repeat the test in the order from step 5 to 1.
(3) The stepper motor is functioning properly if vibration is felt
each time.
CLEANING THROTTLE BODY PARTSN14SlAA
(1) Clean all parts. A cleanser should not be used to clean the
following parts:
l Throttle position sensor
l Idle speed control servo
l Idle position switch
Immersing these parts in cleanser damages the insulation.
Wipe them with a cloth only.
(2) Check that the vacuum port and passage are not plugged
up. Clean the vacuum passage with compressed air.
INSPECTION AFTER REASSEMBLY
tDLE POSITION SWITCH CONTINUITY CHECK
(1) Check the continuity between connector terminal
@ and
the body of the throttle position sensor both when the
throttle valve is at its completely closed position and at
maximum open position.
11(2) If the results of the test do not conform to the above,
replace the idle position switch.
Page 547 of 1216
FUEL SYSTEM - Fuel Tank
FUEL TANK cFWD>
,*. REMOVAL AND INSTALLATION
q?&g
NlMA-30-40 Nm
2-3 Nm22-29 ft.lbs.
---15-20 Nm
11-14 ft.lbs.
15-22 ft.lbs.Removal steps
l + 1. Return hosel +2. Vapor hose
3. Clamp
4. Fuel gauge unit connector
5. Electrical fuel pump connector
l + l q6. High pressure fuel hose
l + 7. Filler hose
l + 8. Vapor hose
~~ 9. Self-locking nut10. Tank band11. Fuel tank
l + 12. Vapor hosel + 13. Overfill limiter (Two-way valve)I)+ 14. Fuel gauge unitl + 15. Electrical fuel pump16. Drain plug
17. Fuel tank cap
18. Packing
19. Fuel filler neck$TEeverse the removal procedures to reinstall,(2) +e : Refer to “Service Points of Removal”:,,
(3) *+ : Refer to “Service Points of lnstallatlon .(4) m : Non-reusable parts
Page 548 of 1216

14-94FUEL SYSTEM - Fuel Tank
Outlet side_ Inlet side01
W838
Positioning projection
03A0220SERVICE POINTS OF REMOVALtilirro8AH
6. DISCONNECTION OF HIGH PRESSURE FUEL
H;OSECaution
Cover the hose connection with rags to prevent splash
of fuel that could be caused by some residual pressure
in the fuel pipe line.
INSPECTIONN14GCAll Check the hoses and the pipes for crack or damage.
l Check the fuel tank cap for malfunction.
l Check the fuel tank for deformation, corrosion or crack.
0,. Check the fuel tank for dust or foreign material.
NOTE
If the inside of the fuel tank is to be cleaned, use any one ofthe following:
(1) Kerosene
(2)
Trichloroethylene-(3) A neutral emulsion type detergent
OVERFILL LIMITER (TWO-WAY VALVE)
Set a hand vacuum pump at inlet side or outlet side; the valve
is good if, when a negative pressure (vacuum) is applied, air
flows after a slight negative pressure is initially maintained.
SERVICE POINTS OF INSTALLATION.
Nl4DDAL15. INSTALLATION OF ELECTRICAL FUEL PUMP
(1) Align the three positioning projections of the packing
with the holes in the fuel pump.
(2) When the fuel pump is installed, the holding bolt at the
lower side of the fuel tank should be installed first.
Care should be taken at this time that the O-ring is not
pinched.14. INSTALLATION OF FUEL GAUGE UNIT
Align the two positioning projections of the packing with
the holes in the fuel gauge unit.
Caution
When mounting the fuel gauge unit, incline the float at
the end leftward, and insert it into the fuel tank. Since
the reserver cap is provided in the fuel tank, the fuel
gauge unit will contact the reserver cap if the fuel
gauge unit is inclined rightward during insertion.
-
4
-,
Page 549 of 1216
FUEL SYSTEM - Fuel Tank
W304I I
I03FDO7 1
Tank band
03AO229
I I\ \\u\ I \I-
03AO189
?4-.03FOO7A
13’. INSTALLATION OF OVERFILL LIMITER (TWO-WAY
VALVE)
Install so that the overfill limiter is facing in the direction
shown in the figure.
12. CONNECTION OF VAPOR
HOSE/l. RETURN HOSE
When attaching the fuel hose to the pipe, be sure that the
hose is attached as shown in the illustration.
Standard value:
25-30 mm (l&1.2 t@.).”. .9. INSTALLATION OF SELF-LOCKING NUT
Tighten the self-locking nuts until the rear end of the tank
band contacts the body.
6. CONNECTION OF VAPOR
HOSE/7. FILLER HOSE
(1) The vapor hose should be connected all the way at the
tank, and approximately 40 mm (1.6 in.) at the filler
neck.(2) The end of the filler hose with the shorter straight pipe
part should be connected at the tank side.
Page 550 of 1216
FUEL SYSTEM- Fuel Tank
Flare nut
Se&e side 03~043
03FOO76. CONNECTION OF HIGH PRESSURE FUEL HOSE TO
FUEL PUMP
Temporarily tighten the flare nut by hand, and then tighten
;Jtit to the specified torque, being careful that the high
’pressure fuel hose does not become twisted.
Caution
When tightening flare nut, be careful not to bend or
twist line to prevent damage to fuel pump low
connection.2. CONNECTION OF VAPOR HOSE/l. RETURN HOSE
When attaching the fuel hose to the pipe, be sure that the
hose is attached as shown in the illustration.
Standard value:
25-30 mm (1 .O-1.2 in.)
Page 551 of 1216
FUEL SYSTEM - Fuel Tank
FUEL TANK
i. REMOVAL AND INSTALLATION
N140A-A
_-Pre-removal Operation
eDraining of the fuel.@Release of Residual Pressure from High
Pressure Fuel Hose(Refer to
P.14-44.)Post-installation Operation
*Measurement of Fuel Pressure(Refer to P.14-44, 52.)l .Supplving of the Fuel.
1-2 Nm825-35 Nm
‘*-*: ft-‘bs*
9-14 Nm- 7-10 ft.lbs.-9
-7
03AO262
15-20 Nm
11-14 ftlbs.Removal steps
1. Fuel tankcap2. Packing
3. Drain plug4. Return hose
5. Vapor hose
4*6. High pressure fuel hose
7. Fuel filler hose
8. Cable band9. Protector
10. Vapor pipe11. Vapor hose
l 4 12. Hole cover13. Self-locking nut
14. Fuel tank
15. Overfill limiter (Two-way valve)
l + 16. Fuel pump and fuel gauge unit assembly
17. Fuel filler neck
FyTEeverse the removal procedures to reinstall.(2) ~~ : Refer to “Service Points of RemoveI”.(3) l + : Refer to “Service Points of Installation”.(4) m : Non-reusable parts
Page 552 of 1216
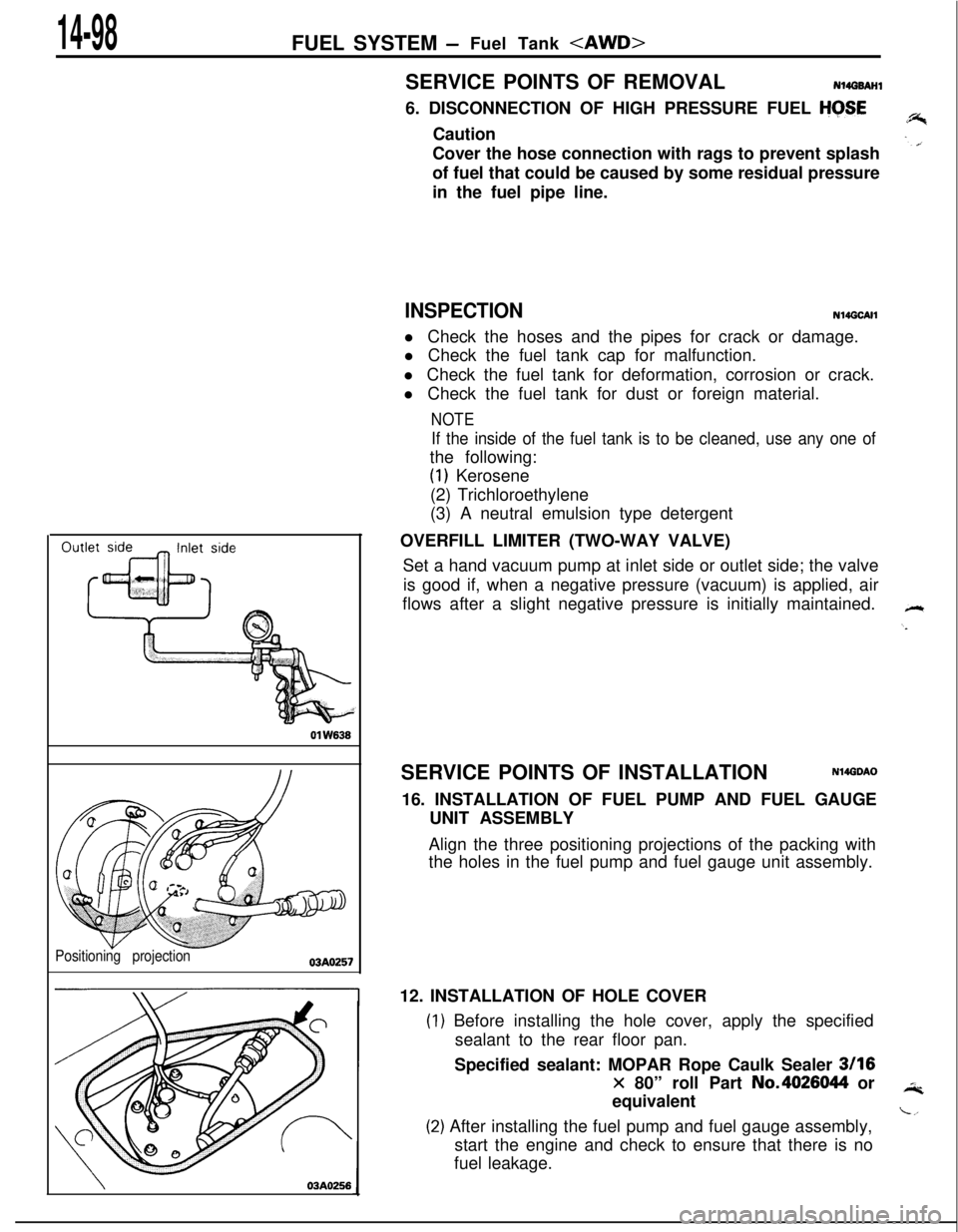
14-98FUEL SYSTEM -Fuel Tank 01
W636
Positioning projection03AO257
\03A0256SERVICE POINTS OF REMOVAL
N14G6AHl6. DISCONNECTION OF HIGH PRESSURE FUEL
HGSECaution
Cover the hose connection with rags to prevent splash
of fuel that could be caused by some residual pressure
in the fuel pipe line.
INSPECTIONN14GCAHl Check the hoses and the pipes for crack or damage.
l Check the fuel tank cap for malfunction.
l Check the fuel tank for deformation, corrosion or crack.
l Check the fuel tank for dust or foreign material.
NOTE
If the inside of the fuel tank is to be cleaned, use any one ofthe following:
(1) Kerosene
(2) Trichloroethylene
(3) A neutral emulsion type detergent
OVERFILL LIMITER (TWO-WAY VALVE)
Set a hand vacuum pump at inlet side or outlet side; the valve
is good if, when a negative pressure (vacuum) is applied, air
flows after a slight negative pressure is initially maintained.
SERVICE POINTS OF INSTALLATION
N14GDAO16. INSTALLATION OF FUEL PUMP AND FUEL GAUGE
UNIT ASSEMBLY
Align the three positioning projections of the packing with
the holes in the fuel pump and fuel gauge unit assembly.
12. INSTALLATION OF HOLE COVER
) Before installing the hole cover, apply the specified
sealant to the rear floor pan.
Specified sealant: MOPAR Rope Caulk Sealer
3116
x 80” roll Part No.4026044 or
equivalent
!) After installing the fuel pump and fuel gauge assembly,
start the engine and check to ensure that there is no
fuel leakage.