Page 1025 of 1216
AUTOMATIC TRANSAXLE - Center Differential 21-331
3. INSTALLATION OF TAPER ROLLER BEARING
Using the special tool, install the taper roller bearing on thecenter differential flange.
2. INSTALLATION OF TAPER ROLLER BEARING
Using the special tool, install the taper roller bearing on thetransfer driven gear.
Page 1026 of 1216
21-332AUTOMATIC TRANSAXLE - Front Output Shaft
FRONT OUTPUT SHAFT 2
DISASSEMBLY AND REASSEMBLY
II
NZlLXAA
Disassembly steps
*I) l 1. Taper roller bearing+e l 42. Taper roller bearing
3. Front output shaft
NOTE(I) Reverse the disassembly procedures to reassemble.(2) +I) : Refer to “Service Points of Disassembly”.
(3) l 4 : Refer to “Service Points of Reassembly”.
SERVICE POINTS OF DISASSEMBLY1./2. REMOVAL
OF TAPER ROLLER BEARINGSUsing the special tool, remove the taper roller bearings on
both ends of the front output shaft.
MD998822
SERVICE POINTS OF REASSEMBLY
2./l. INSTALLATION OF TAPER ROLLER BEARINGSUsing the special tool, press-fit the taper roller bearings on
both ends of the front output shaft.
Page 1027 of 1216
AUTOMATIC TRANSAXLE - Transfer Assembly
TRANSFER ASSEMBLY
- DISASSEMBLY AND REASSEMBLY
21-333
NElVE-35-42
Nm26-30 ft.lbs.
TFAO601
Disassembly steps
1. Cover
2. Cover gasket
3. Extension housing assembly
4. Oil guide
l I5. Transfer case sub assemblyl 6. Spacer7. O-ring
l +8. Transfer case adapter sub assembly
$?everse the disassembly procedures to reassemble.(2) l 4 : Refer to “Service Points of Reassembly”.
(3) m : Non-reusable parts
Page 1028 of 1216
21-334AUTOMATIC TRANSAXLE - Transfer Assemblv
2210050
-TifAO315
SERVICE POINTS OF REASSEMBLYWmnAE
8. INSTALLATION OF TRANSFER CASE ADAPTER SUB +=GASSEMBLY
-Using a brush, apply a thin even coat of machine blue orminium to both tooth surfaces of the driven bevel gear.
6. INSTALLATION OF SPACERInstall the spacer which has been used so far.
5. INSTALLATION OF TRANSFER CASE SUB ASSEMBLY
(1) Tighten the transfer case adapter sub assembly on the
transfer case sub assembly to the specified torque.
\
-;--.(2) Using the special tool, turn the drive bevel gear shaft
one turn each in the direction of normal and reverse
rotation.Caution
Do not rotate the drive bevel gear shaft more thanone turn
as it cause a blurred tooth contact pattern.
MB991144(3) Make sure that the contact pattern of the driven bevel
gear teeth is correct.
NOTE
See Tooth Contact Adjustment Procedure on next pagefor the standard tooth contact pattern.
4
-am--
Page 1029 of 1216
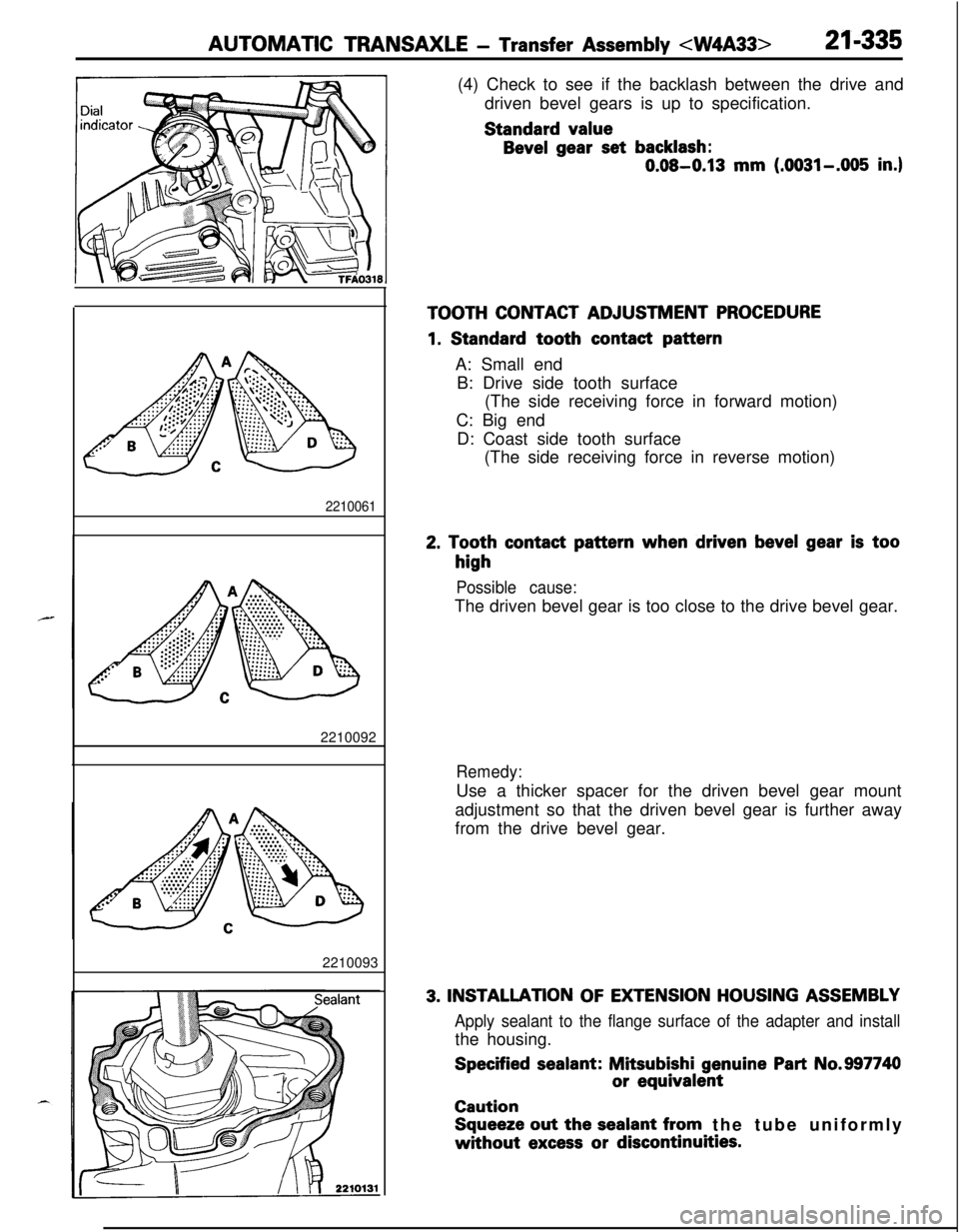
AUTOMATIC TRANSAXLE - Transfer Assembly 21-335(4) Check to see if the backlash between the drive and
driven bevel gears is up to specification.Standard value
Bevel gear set backlash:
0.08-0.13 mm (.0031-.005 in.)
22100612210092
2210093
TOOTH CONTACT ADJUSTMENT PROCEDURE
1. Standard tooth contact pattern
A: Small end
B: Drive side tooth surface
(The side receiving force in forward motion)
C: Big end
D: Coast side tooth surface
(The side receiving force in reverse motion)
2. Tooth contact pattern when driven bevel gear is too
high
Possible cause:The driven bevel gear is too close to the drive bevel gear.
Remedy:Use a thicker spacer for the driven bevel gear mount
adjustment so that the driven bevel gear is further away
from the drive bevel gear.
3. INSTALLATlON OF EXTENSION HOUSING ASSEMBLY
Apply sealant to the flange surface of the adapter and installthe housing.
Specified sealant: Mitsubishi genuine Part No.997740Caution
or equivalentSqueeze out
the sealant from the tube uniformly
without excess or discontinuities.
Page 1030 of 1216
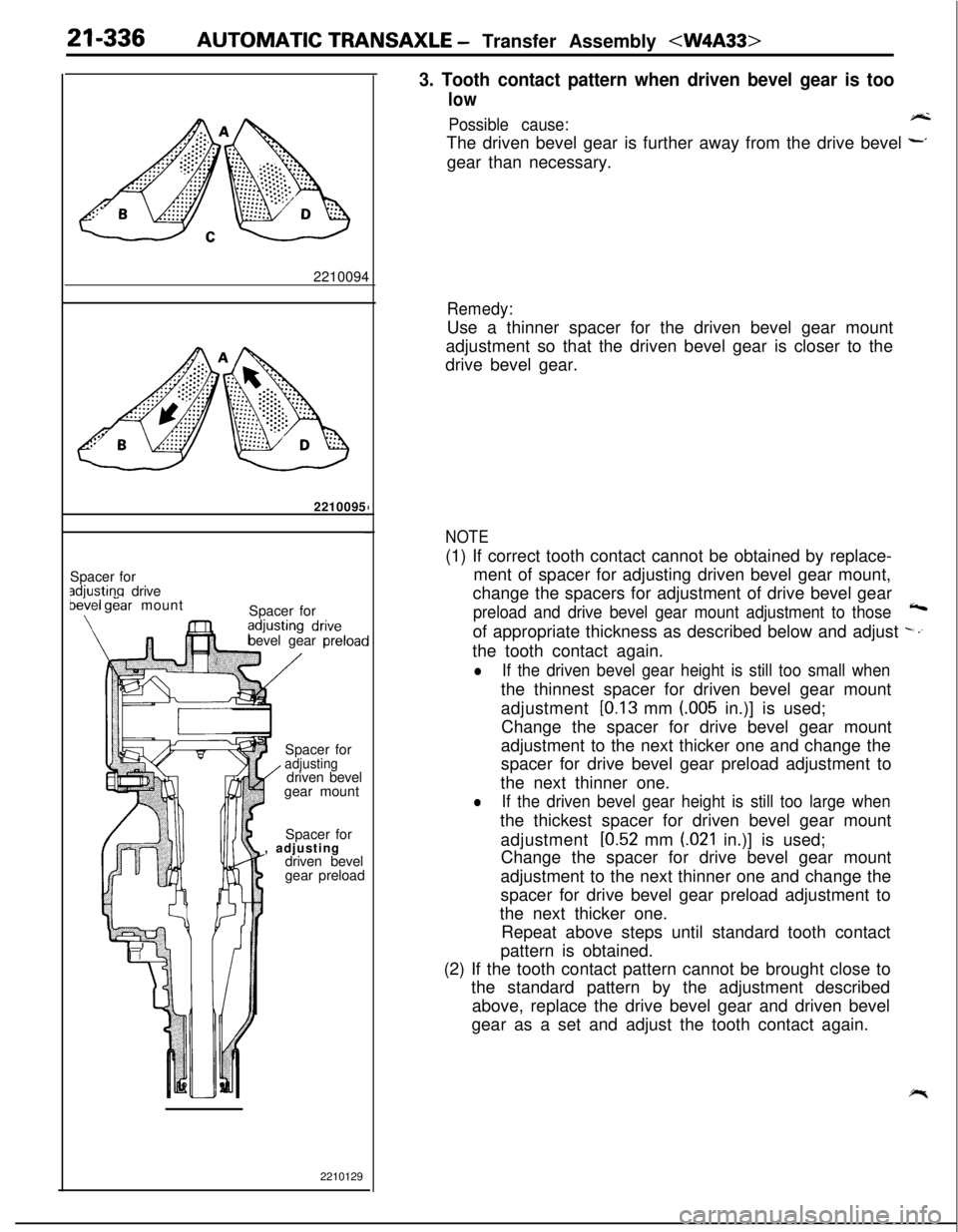
21-336AUTOMATIC TRANSAXLE - Transfer Assembly 2210094
2210095
Spacer for
adiustina drivebekel gear mount
\Spacer for
bevel gear preloacSpacer for
adjusting/ driven bevel
gear mount
Spacer for
, adjusting
driven bevel
gear preload
2210129
3. Tooth contact pattern when driven bevel gear is too
low
Possible cause:A-kThe driven bevel gear is further away from the drive bevel
~gear than necessary.
Remedy:Use a thinner spacer for the driven bevel gear mount
adjustment so that the driven bevel gear is closer to the
drive bevel gear.
NOTE(1) If correct tooth contact cannot be obtained by replace-
ment of spacer for adjusting driven bevel gear mount,
change the spacers for adjustment of drive bevel gear
preload and drive bevel gear mount adjustment to those4of appropriate thickness as described below and adjust
-.’the tooth contact again.
lIf the driven bevel gear height is still too small whenthe thinnest spacer for driven bevel gear mount
adjustment
[0.13 mm (.005 in.)] is used;
Change the spacer for drive bevel gear mount
adjustment to the next thicker one and change the
spacer for drive bevel gear preload adjustment to
the next thinner one.
lIf the driven bevel gear height is still too large whenthe thickest spacer for driven bevel gear mount
adjustment
[0.52 mm (021 in.)] is used;
Change the spacer for drive bevel gear mount
adjustment to the next thinner one and change the
spacer for drive bevel gear preload adjustment to
the next thicker one.
Repeat above steps until standard tooth contact
pattern is obtained.
(2) If the tooth contact pattern cannot be brought close to
the standard pattern by the adjustment described
above, replace the drive bevel gear and driven bevel
gear as a set and adjust the tooth contact again.
Page 1031 of 1216
AUTOMATIC TRANSAXLE- Extension Housing Assembly 211337
EXTENSION HOUSING ASSEMBLY
- DISASSEMBLY AND REASSEMBLY
NZlVGAA
>-
Disassembly steps
l +1. Air breather2. Dust seal guardl * 3. Oil seal4. Extension housing
NOTE(I) Reverse the disassembly procedures to reassemble.(2) W : Refer to “Service Points of Reassembly”.(3) q : Non-reusable parts
R3
MD99881 2MD998822
TFA03192010043
SERVICE POINTS OF REASSEMBLY
3. INSTALLATION OF OIL SEALUsing the special tool, install the oil seal.
1. INSTALLATION OF AIR BREATHER
Apply sealant to the air breather port and fit the air breatherin position.
Specified sealant: MOPAR Part No.4318025 or equiva-lent
Page 1032 of 1216
21-338AUTOMATIC TRANSAXLE- Transfer Case Adapter Sub Assembly 4W4A33>
TRANSFER CASE ADAPTER SUB ASSEMBLY N21VlAADISASSEMBLY
AND REASSEMBLY
Disassembly steps
4**+1.Locknut
4*2. Driven bevel gear
I)4 3. Taper roller bearing
*4 ;. ;z;;r
6:Outer race
7.Outer race
8. Transfer case adapter
4e W 9. Taper roller bearing
NOTE(I) Reverse the disassembly procedures to reassemble.(2) 4e : Refer to ::Service Points of Disassembly:‘.[j &@ j Refer to Service Points of Reassembly
Non-reusable parts
140-150 Nm102-115 ft.lbs.
TEA0 604
SERVICE POINTS OF DISASSEMBLY
1. REMOVAL OF LOCK NUT
(1) Unstake the lock nut.
I IMB991013
TFAO289(2) Remove the driven bevel gear’s lock nut by using the
special tool.