Page 361 of 1216
ENGINE <2.0L DOHC Engine> - Engine Mounting
ENGINE MOUNTING
- REMOVAL AND INSTALLATION
9-77
NOBGA-B
*Raise and Suspend the Engine to theExtent Force is not applied to the Engine
Post-installation Operation@Lower the Engine50-65 Nm36-47 ftlbs.
Removal steps
50-65 Nm36-47 ftlbs.
OlAO559I1. Pressure hose (power steering)2. Bracket
3. Engine mount bracket and body
connection bolt4. Engine mount bracket
l + 5. Mounting stopper
NOTE(1) Reverse the removal procedures to reinstall.(2) *+ : Refer to “Service Points of Installatron”.
Engine side
CI
Mounting stopper
AnowOlA0004
INSPECTIONNOSGCAHJl Check each insulator for cracks or damage.
l Check each bracket for deformation or damage.
SERVICE POINTS OF INSTALLATIONNOSGDAKl5. INSTALLATION OF MOUNTING STOPPER
Install the mounting stopper of the engine mount bracket
so that the arrow faces the center part of the engine.
Page 362 of 1216
Page 363 of 1216
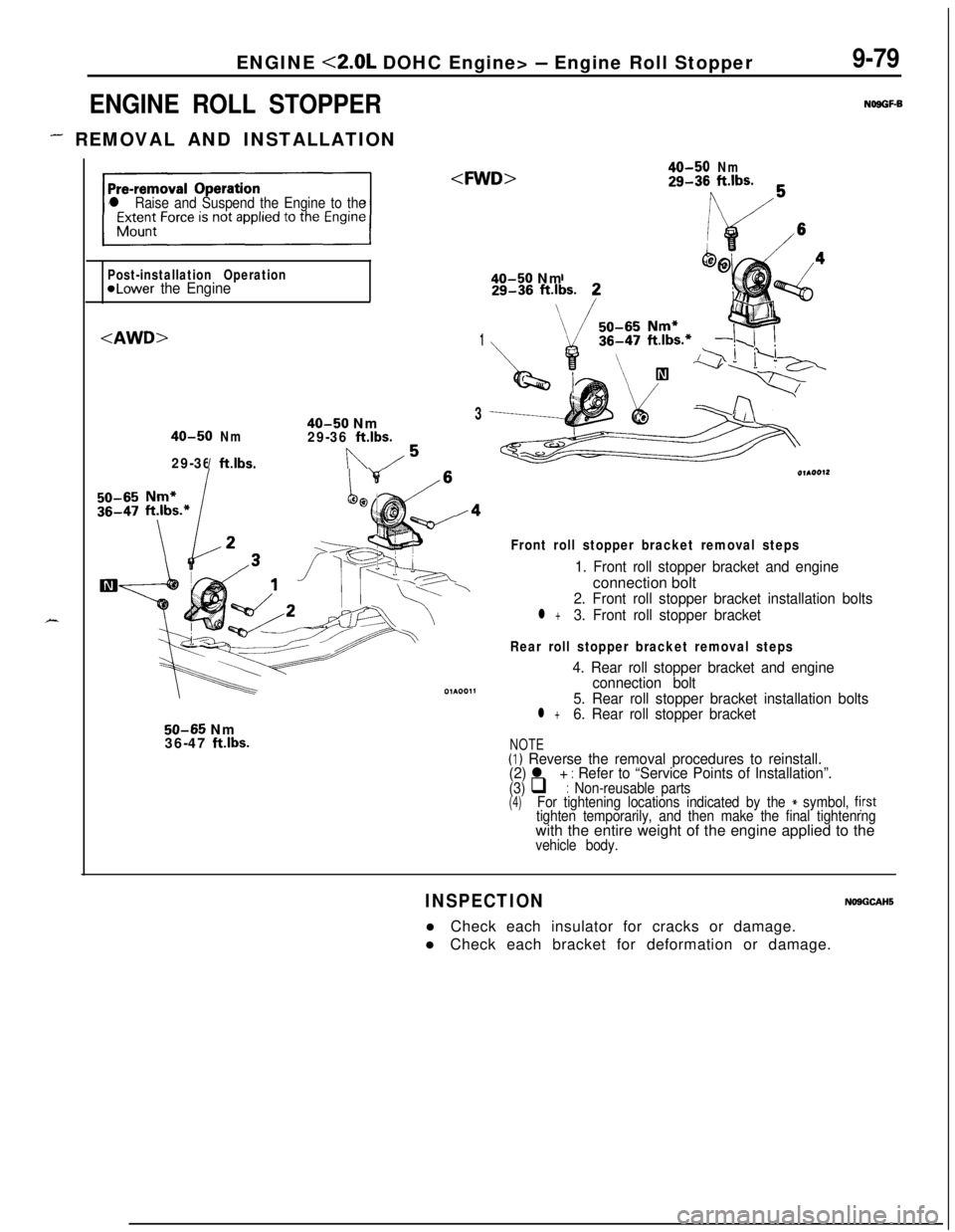
ENGINE <2.0L DOHC Engine> - Engine Roll Stopper
ENGINE ROLL STOPPER
- REMOVAL AND INSTALLATION
9-79
NOSGF-B
X
l Raise and Suspend the Engine to the
40-50Nm29-36ft.lbs.
Post-installation Operation
@Lower the Engine40-50 Nm
1
40-50 Nm3
40-50Nm29-36ft.lbs.
29-36ft.lbs.In/5
/4
\
50-65 Nm
36-47 ftlbs.
Front roll stopper bracket removal steps
1. Front roll stopper bracket and engineconnection bolt
2. Front roll stopper bracket installation bolts
l +3. Front roll stopper bracket
Rear roll stopper bracket removal steps
4. Rear roll stopper bracket and engine
connection bolt
5. Rear roll stopper bracket installation bolts
l +6. Rear roll stopper bracket
NOTE(I) Reverse the removal procedures to reinstall.
(2) l + : Refer to “Service Points of Installation”.(3) q : Non-reusable parts(4)For tightening locations indicated by the * symbol, fjrsttighten temporarily, and then make the final tightenrngwith the entire weight of the engine applied to the
vehicle body.
INSPECTIONNOSGCAHSl Check each insulator for cracks or damage.
l Check each bracket for deformation or damage.
Page 364 of 1216
9-80ENGINE <2.0L DOHC Engine> - Engine Roll Stopper
Rear roll
-92
.7 mm-3.6in.)12A0638
Forward
0
:fYVD>Front roll
stopper bracket
/
jl.7-57.7 mm2.0-2.3 in.)olR003t
44-50 mm(1.7-2.0 in.)Front rollOlAO610
J
ISERVICE POINTS OF INSTALLATION
N-$?y
6. INSTALLATION OF REAR ROLL STOPPER BMFKE?
AWD-A/T>, (1;r.After temporarily tightening the rear roll stopper bracket,
tighten so that, in the unladen vehicle condition, the
distance from the center hole of the insulator to
th:e lower
edge of the bracket is the specified distance.
3. INSTALLATION OF FRONT ROLL STOPPER BRACKET(1) Install the front roll stopper bracket so that the part
where the round hole is made is facing the front of the
vehicle.(2) After temporarily tightening the front roll stopper
bracket, tighten so that, in the unladen vehicle condi-
tion, the distance from the center hole of the
insul&torto the lower edge of the bracket is the specified
-
distance.
Page 365 of 1216
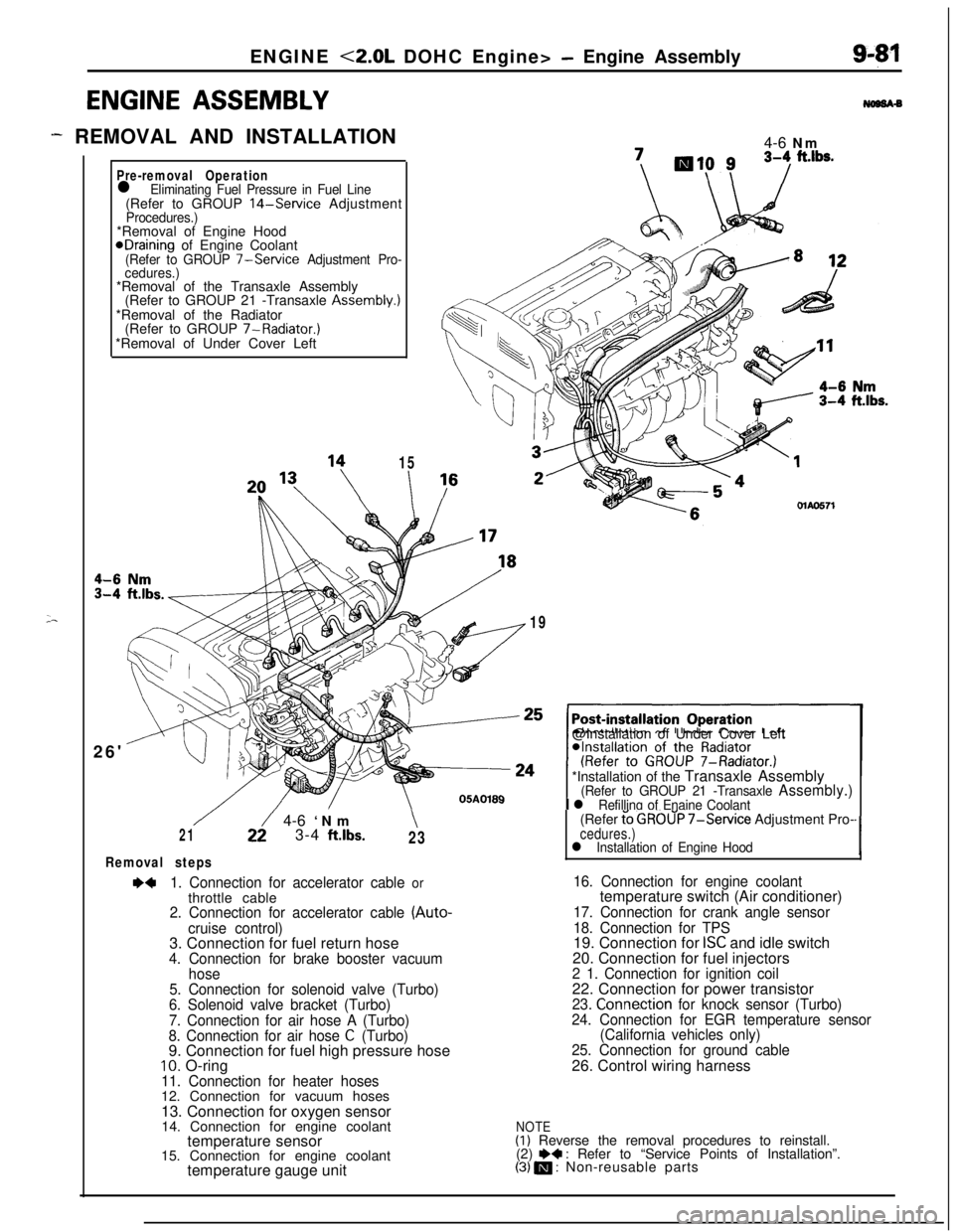
ENGINE <2.0L DOHC Engine> - Engine Assembly
ENGINE ASSEMBLY
- REMOVAL AND INSTALLATION
;-
Pre-removal Operationl Eliminating Fuel Pressure in Fuel Line(Refer to GROUP 14-Service AdjustmentProcedures.)*Removal of Engine Hood
@Draining of Engine Coolant(Refer to GROUP 7-Service Adjustment Pro-
cedures.)*Removal of the Transaxle Assembly
(Refer to GROUP 21 -Transaxle Assembly.)
*Removal of the Radiator
(Refer to GROUP 7-Radiator.)
*Removal of Under Cover Left
26'
15
I4-6 Nm\I /MAO571
19@Installation of Under Cover Left
*Installation of the Transaxle Assembly
(Refer to GROUP 21 -Transaxle Assembly.)
I l Refilling of Enaine Coolant
/22/ 4-6 ‘Nm\213-4 ftlbs.23
Removal steps
~~1. Connection for accelerator cable orthrottle cable
2. Connection for accelerator cable (Auto-
cruise control)3. Connection for fuel return hose
4. Connection for brake booster vacuum
hose
5. Connection for solenoid valve (Turbo)
6. Solenoid valve bracket (Turbo)
7. Connection for air hose A (Turbo)
8. Connection for air hose
C (Turbo)9. Connection for fuel high pressure hose
10. O-ring11. Connection for heater hoses12. Connection for vacuum hoses
13. Connection for oxygen sensor
14. Connection for engine coolant
temperature sensor
15. Connection for engine coolant
temperature gauge unit(Refer
t’o GROUP 7-Service Adjustment Pro-cedures.)l Installation of Engine Hood‘I
16. Connection for engine coolanttemperature switch (Air conditioner)
17. Connection for crank angle sensor
18. Connection for TPS19. Connection for
ISC and idle switch
20. Connection for fuel injectors
2 1. Connection for ignition coil22. Connection for power transistor
23. Connection for knock sensor (Turbo)
24. Connection for EGR temperature sensor
(California vehicles only)
25. Connection for ground cable26. Control wiring harness
NOTE(I) Reverse the removal procedures to reinstall.
(2) e+ : Refer to “Service Points of Installation”.(3) m : Non-reusable parts
Page 366 of 1216
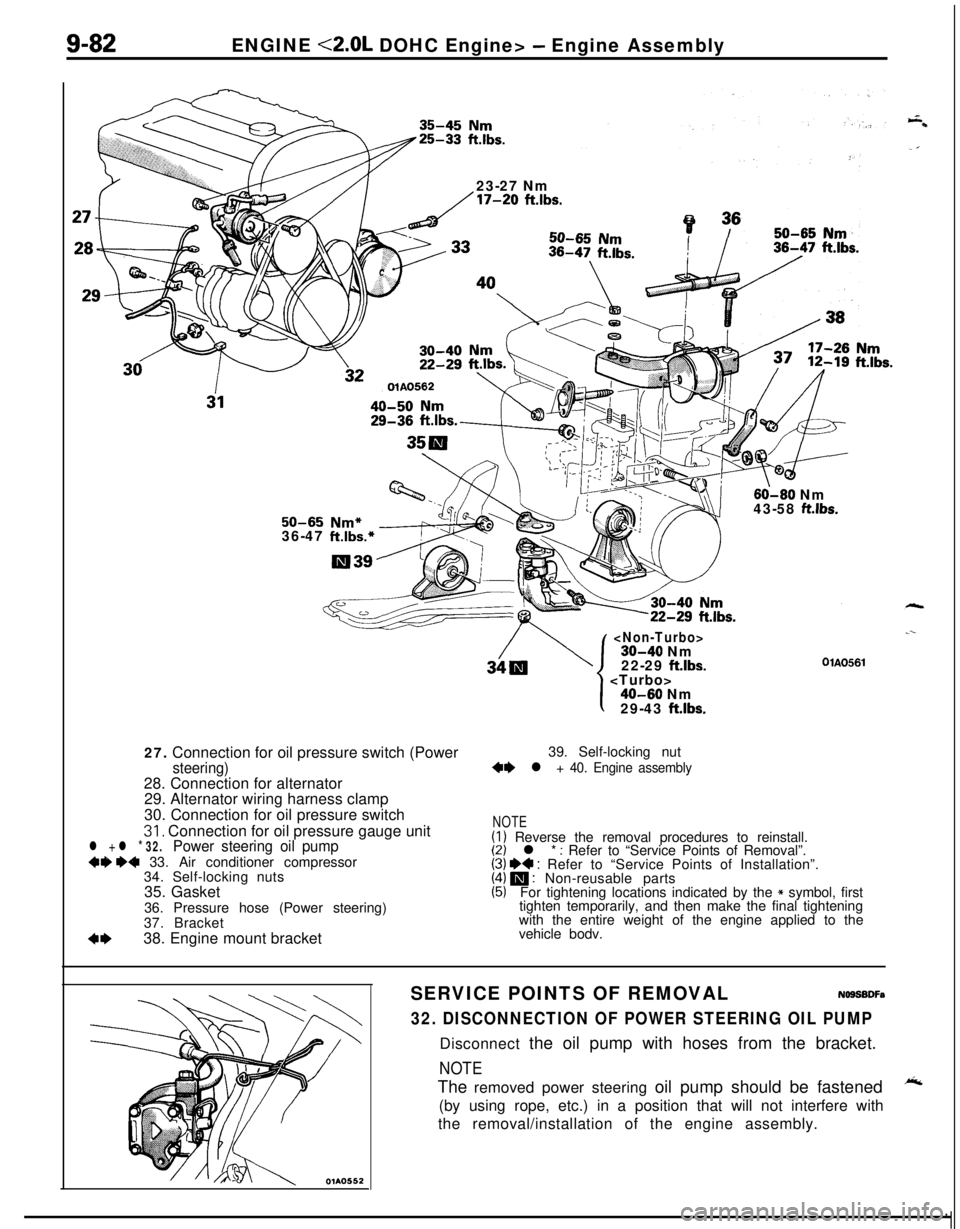
9-82ENGINE <2.0L DOHC Engine> - Engine Assembly
23-27 Nm
/17-20 ftlbs.
60-60 Nm
43-58 ft.lbs.50-65 Nm*36-47 ft.lbs.*27. Connection for oil pressure switch (Power
steering)28. Connection for alternator
29. Alternator wiring harness clamp
30. Connection for oil pressure switch
31, Connection for oil pressure gauge unitl + l * 32.Power steering oil pump+9 ~~ 33. Air conditioner compressor
34. Self-locking nuts
35. Gasket
36. Pressure hose (Power steering)
37. Bracket
4*38. Engine mount bracket
30-40 Nm
22-29 ftlbs.
.--
OlAO561
1
I40-60 Nm
29-43 ft.lbs.39. Self-locking nut
+e l + 40. Engine assembly
NOTE(I) Reverse the removal procedures to reinstall.(2) l * : Refer to “Service Points of Removal”.(3) I)+ : Refer to “Service Points of Installation”.(4) m : Non-reusable parts(5)For tightening locations indicated by the * symbol, first
tighten temporarily, and then make the final tightening
with the entire weight of the engine applied to the
vehicle bodv.
SERVICE POINTS OF REMOVALNOSSBDFa
32. DISCONNECTION OF POWER STEERING OIL PUMPDisconnect the oil pump with hoses from the bracket.
NOTEThe removed power steering oil pump should be fastened
A(by using rope, etc.) in a position that will not interfere with
the removal/installation of the engine assembly.
Page 367 of 1216
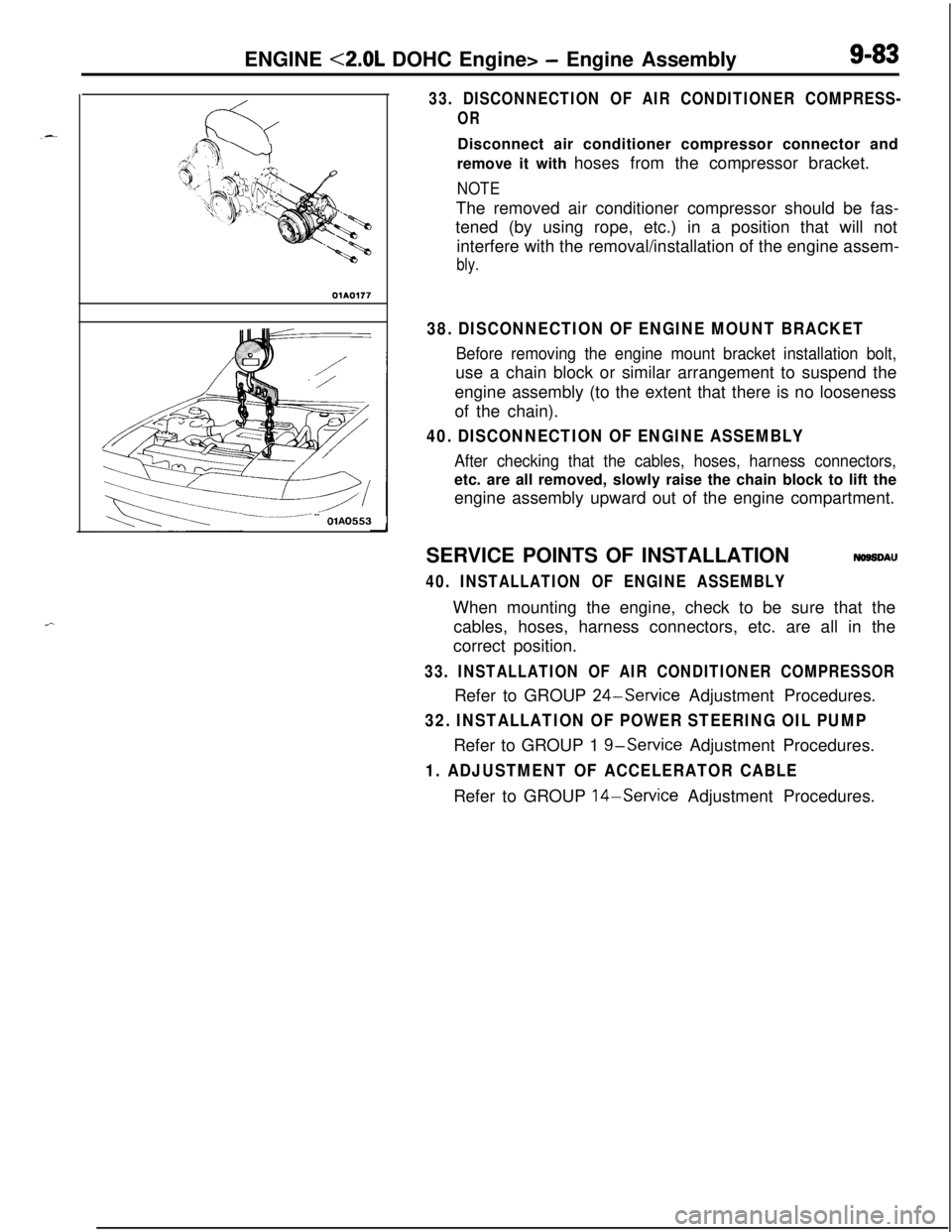
r-.ENGINE <2.0L DOHC Engine>
- Engine AssemblyS-83
OlA0177
-mpp.-/- --OlA0553
33. DISCONNECTION OF AIR CONDITIONER COMPRESS-
ORDisconnect air conditioner compressor connector and
remove it with hoses from the compressor bracket.
NOTEThe removed air conditioner compressor should be fas-
tened (by using rope, etc.) in a position that will not
interfere with the removal/installation of the engine assem-
bly.
38. DISCONNECTION OF ENGINE MOUNT BRACKET
Before removing the engine mount bracket installation bolt,use a chain block or similar arrangement to suspend the
engine assembly (to the extent that there is no looseness
of the chain).
40. DISCONNECTION OF ENGINE ASSEMBLY
After checking that the cables, hoses, harness connectors,etc. are all removed, slowly raise the chain block to lift the
engine assembly upward out of the engine compartment.
SERVICE POINTS OF INSTALLATION
NOSSDAU
40. INSTALLATION OF ENGINE ASSEMBLYWhen mounting the engine, check to be sure that the
cables, hoses, harness connectors, etc. are all in the
correct position.
33. INSTALLATION OF AIR CONDITIONER COMPRESSORRefer to GROUP
24-Service Adjustment Procedures.
32. INSTALLATION OF POWER STEERING OIL PUMPRefer to GROUP 1
g-service Adjustment Procedures.
1. ADJUSTMENT OF ACCELERATOR CABLERefer to GROUP 14-Service Adjustment Procedures.
Page 368 of 1216
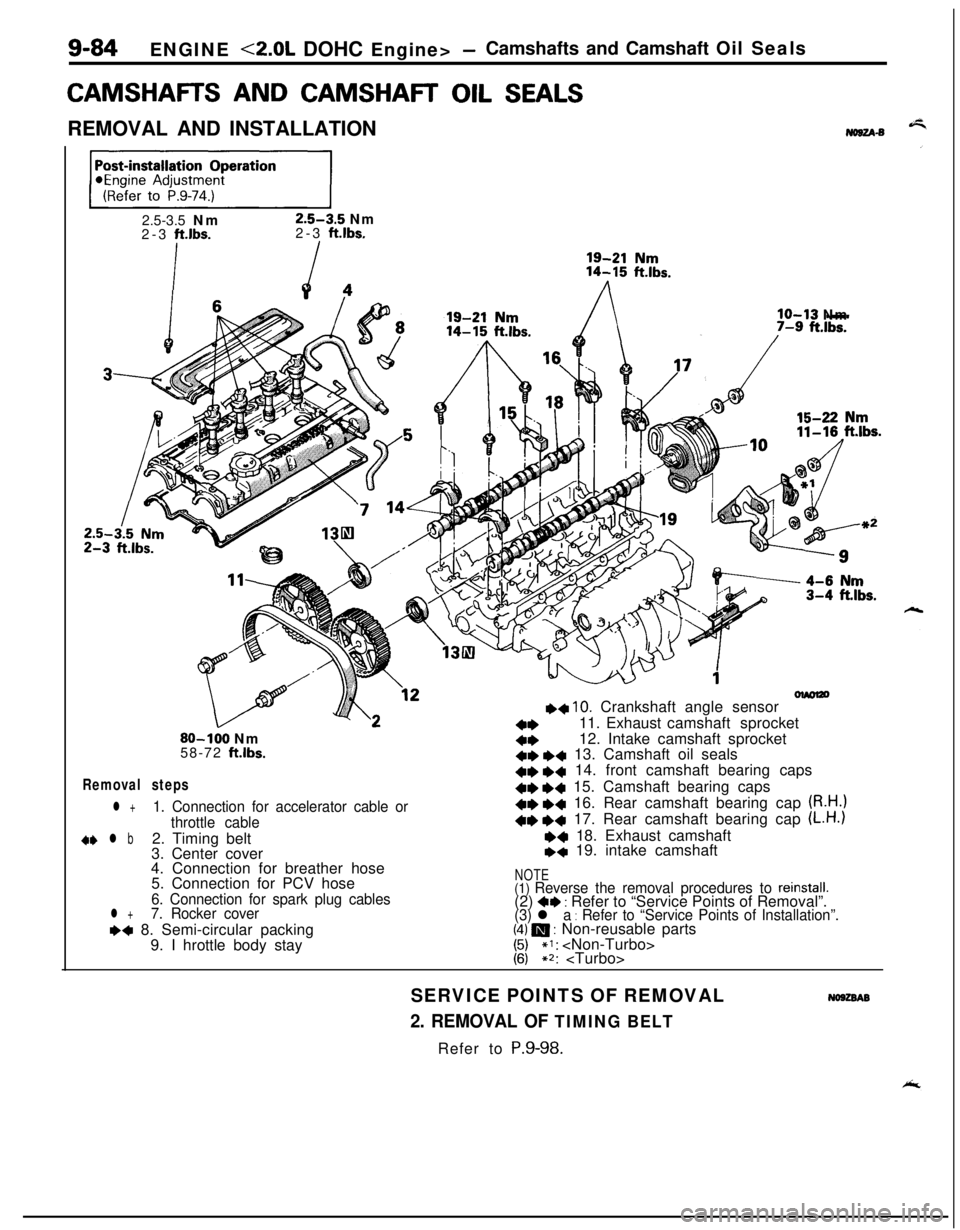
9-84ENGINE <2.0L DOHC Engine> -Camshafts and Camshaft Oil Seals
CAMSHAFR AND CAMSHAR OIL SEALSREMOVAL AND INSTALLATION
No8u-s
ppEJ=-j2.5-3.5 Nm
2.5-3.5 Nm
2-3 ft.lbs.2-3 ft.lbs.
lo-13 Nm
olmlzo++ 10. Crankshaft angle sensor
a*11. Exhaust camshaft sprocket80-100 Nm4*12. Intake camshaft sprocket
58-72 ftlbs.+e *+ 13. Camshaft oil seals
Removal steps+e e+ 14. front camshaft bearing caps41)
+4 15. Camshaft bearing caps
l +1. Connection for accelerator cable or+e +c 16. Rear camshaft bearing cap (R.H.)
throttle cable+e +4 17. Rear camshaft bearing cap (L.H.)
d+ l b2. Timing belt~~ 18. Exhaust camshaft
3. Center cover+q 19. intake camshaft
4. Connection for breather hose
5. Connection for PCV hose
NOTE
6. Connection for spark plug cables(1) Reverse the removal procedures to reinstall.(2) 4* : Refer to “Service Points of Removal”.l +7. Rocker cover
(3) l a : Refer to “Service Points of Installation”.~~ 8. Semi-circular packing(4) m : Non-reusable parts
9. I hrottle body stay
1:;*I: ~2:
SERVICE POINTS OF REMOVAL
No9zsAB
2. REMOVAL OF TIMING BELTRefer to P.9-98.