Page 161 of 1082
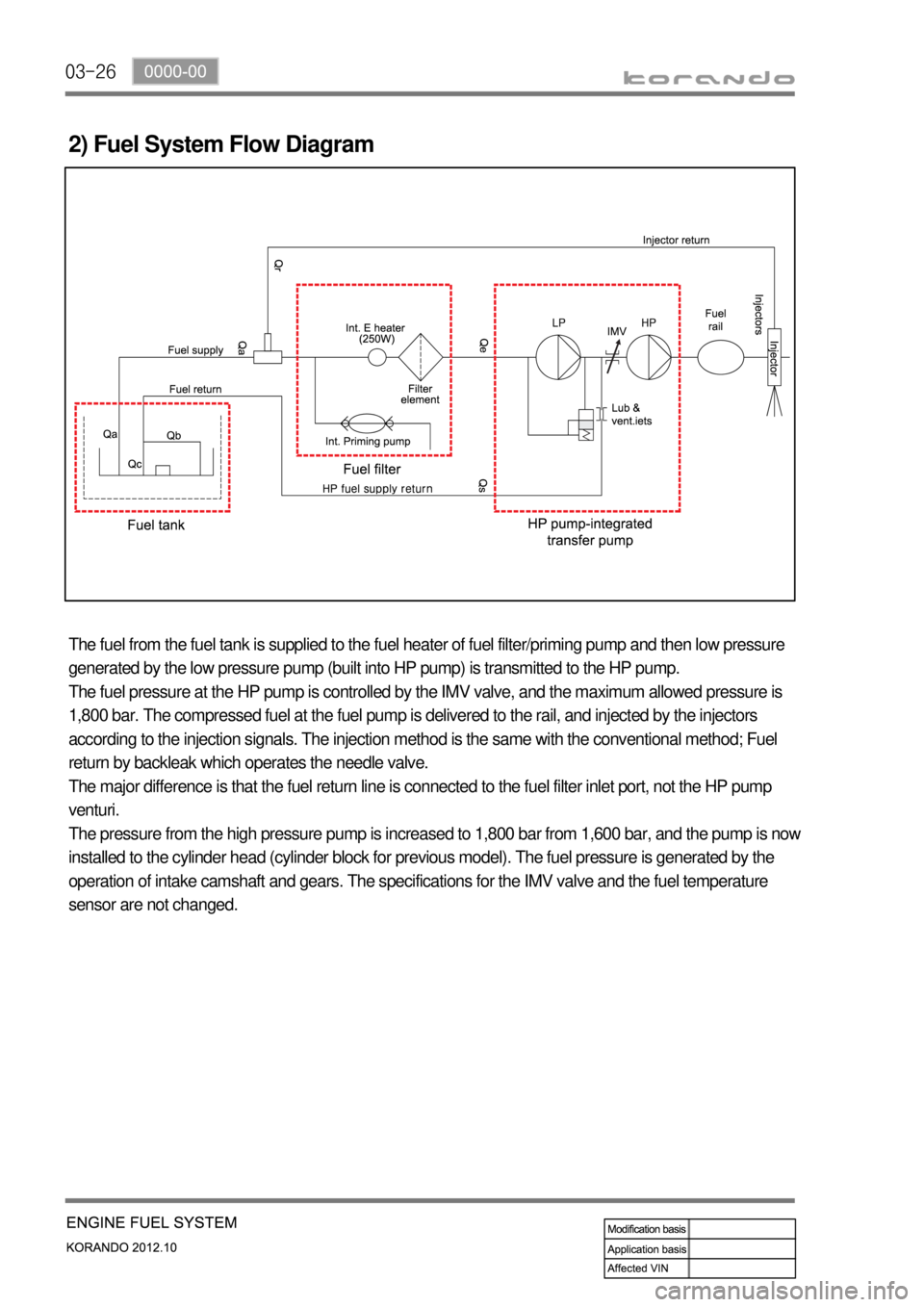
03-26
2) Fuel System Flow Diagram
The fuel from the fuel tank is supplied to the fuel heater of fuel filter/priming pump and then low pressure
generated by the low pressure pump (built into HP pump) is transmitted to the HP pump.
The fuel pressure at the HP pump is controlled by the IMV valve, and the maximum allowed pressure is
1,800 bar. The compressed fuel at the fuel pump is delivered to the rail, and injected by the injectors
according to the injection signals. The injection method is the same with the conventional method; Fuel
return by backleak which operates the needle valve.
The major difference is that the fuel return line is connected to the fuel filter inlet port, not the HP pump
venturi.
The pressure from the high pressure pump is increased to 1,800 bar from 1,600 bar, and the pump is now
installed to the cylinder head (cylinder block for previous model). The fuel pressure is generated by the
operation of intake camshaft and gears. The specifications for the IMV valve and the fuel temperature
sensor are not changed.
Page 162 of 1082
03-270000-00
3) Input/Output devices
Page 163 of 1082
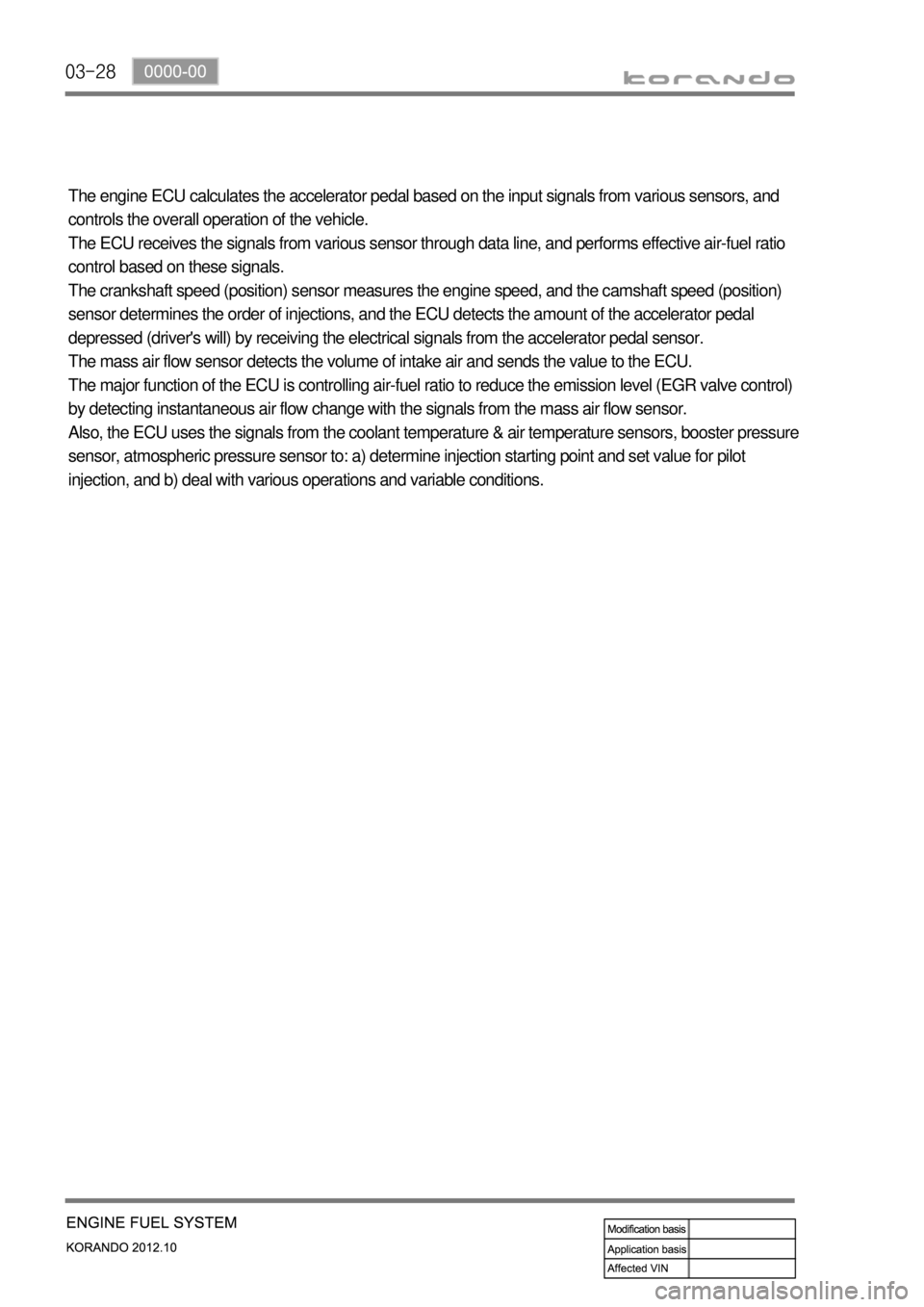
03-28
The engine ECU calculates the accelerator pedal based on the input signals from various sensors, and
controls the overall operation of the vehicle.
The ECU receives the signals from various sensor through data line, and performs effective air-fuel ratio
control based on these signals.
The crankshaft speed (position) sensor measures the engine speed, and the camshaft speed (position)
sensor determines the order of injections, and the ECU detects the amount of the accelerator pedal
depressed (driver's will) by receiving the electrical signals from the accelerator pedal sensor.
The mass air flow sensor detects the volume of intake air and sends the value to the ECU.
The major function of the ECU is controlling air-fuel ratio to reduce the emission level (EGR valve control)
by detecting instantaneous air flow change with the signals from the mass air flow sensor.
Also, the ECU uses the signals from the coolant temperature & air temperature sensors, booster pressure
sensor, atmospheric pressure sensor to: a) determine injection starting point and set value for pilot
injection, and b) deal with various operations and variable conditions.
Page 164 of 1082
03-290000-00
4) Flow Diagram of Fuel Supply System
Page 165 of 1082
Page 166 of 1082
04-30000-00
1. SPECIFICATION
Component Item Specification
Air cleaner elementFilter type Dry, filter element
Filter area0.208 m²
Service intervalEU: Change every 20,000 km (But, shorten the
service interval under severe conditions)
GEN: Change every 15,000 km (But, shorten the
service interval under severe conditions)
Air cleaner assemblyWeight 1.13 kg
Operating temperature
-30 ~ 100℃
Capacity 6.5 L
IntercoolerCore material Aluminum
Size 510 x 110 x 70 (W x H x T)
Core size 510 x 110 x 63 (W x H x T)
Tank material Plastic (Molding)
Efficiency 80%
Shorten the service interval under severe conditions such as driving on a dusty road or off-road. *
Page 167 of 1082
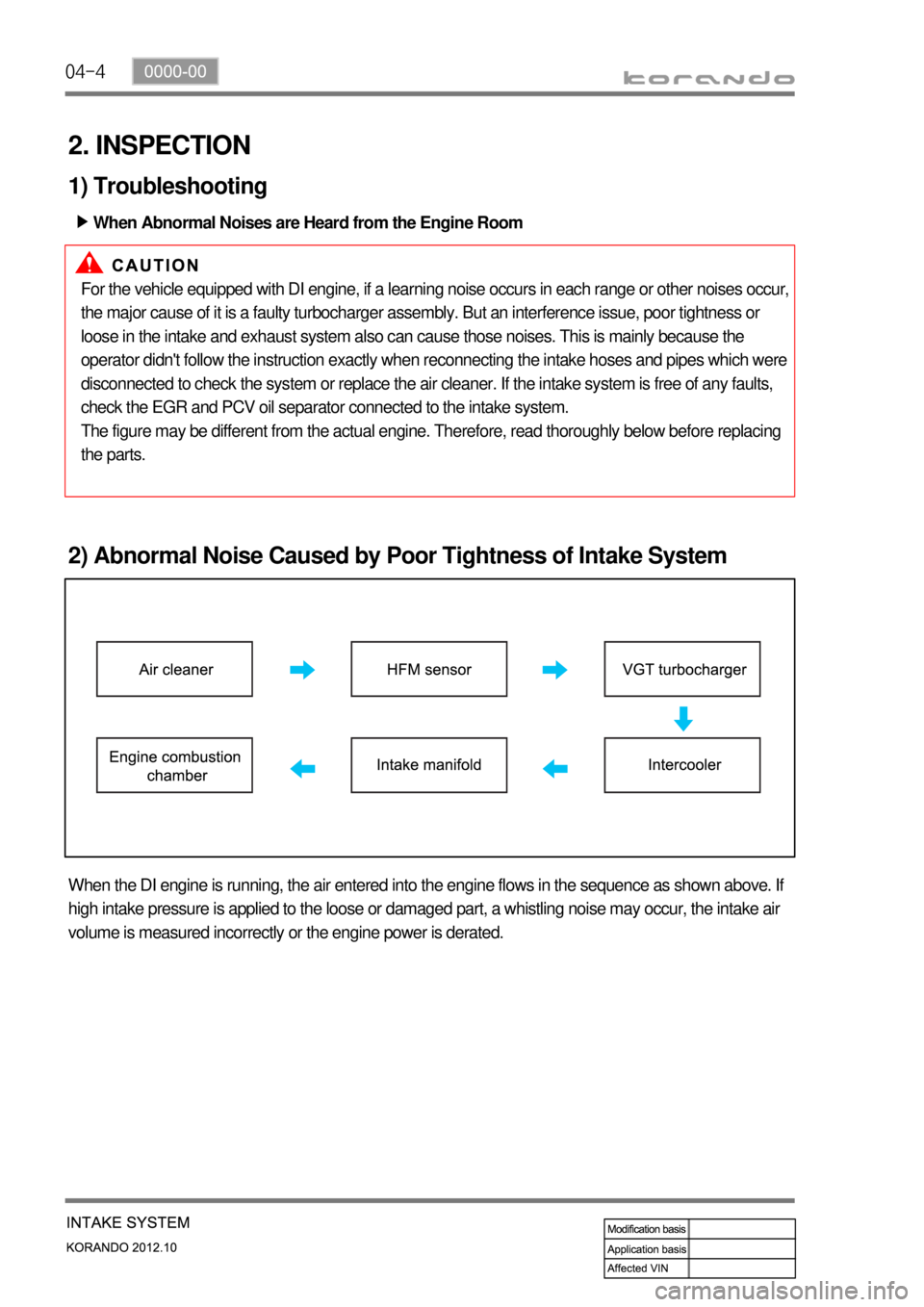
04-4
2. INSPECTION
1) Troubleshooting
When Abnormal Noises are Heard from the Engine Room ▶
For the vehicle equipped with DI engine, if a learning noise occurs in each range or other noises occur,
the major cause of it is a faulty turbocharger assembly. But an interference issue, poor tightness or
loose in the intake and exhaust system also can cause those noises. This is mainly because the
operator didn't follow the instruction exactly when reconnecting the intake hoses and pipes which were
disconnected to check the system or replace the air cleaner. If the intake system is free of any faults,
check the EGR and PCV oil separator connected to the intake system.
The figure may be different from the actual engine. Therefore, read thoroughly below before replacing
the parts.
2) Abnormal Noise Caused by Poor Tightness of Intake System
When the DI engine is running, the air entered into the engine flows in the sequence as shown above. If
high intake pressure is applied to the loose or damaged part, a whistling noise may occur, the intake air
volume is measured incorrectly or the engine power is derated.
Page 168 of 1082
04-50000-00
3) Troubleshooting Sequence
The basic checks for intake system are as follows:
Basic Checks for Intake System ▶
Make sure to replace or clean the air cleaner
element periodically. Otherwise, engine will be
derated or work abnormally because of low
intake air volume.
Unlike the fuel system, which is a closed
circuit, the intake system is an open circuit
system. Therefore any malfunction may occur
due to dust and dirt.
Most of the connections consist of hoses so
the system cannot withstand high temperature
and pressure. Also it can be deformed or
loosened easily because it is a clamp
mounting system. Thus, when checking the
engine, basic inspections, such as tightened
status check and visual inspection for hose,
etc., should be carried out in advance.
Other Checks for Intake System ▶
If the intake system is free of any faults, check
for EGR and PCV oil separator.