Page 1025 of 1082
Page 1026 of 1082
02-10
Driver side air bagSeat Belt Pretensioner
SDM unit assembly
BCM
Driver air bag module Passenger air bag module
1. SYSTEM CONFIGURATION
Page 1027 of 1082
02-118810-00
Inflatable curtain air bag module
Side air bag sensor
assembly
Front impact sensor
assembly
Air bag warning lamp
(IP)
Height adjuster
Page 1028 of 1082
02-12
2. OPERATING CONDITIONS
1) Front Air Bag Operating Conditions When A Frontal Impact
Occurs
2) Side Air Bag Operating Conditions When A Side Impact Occurs
Impact to Left direction Right direction
Seat belt pretensioner - Driver side IGN IGN
Seat belt pretensioner - Passenger side IGN IGN
Side air bag module - Passenger side IGN Not ignite
Side air bag module - Passenger side Not ignite IGN
Inflatable curtain air bag module - Driver side IGN Not ignite
Inflatable curtain air bag module - Passenger side Not ignite IGN
Impact to Front side
Driver air bag IGN
Passenger air bag IGN
Seat belt pretensioner - Driver side IGN
Seat belt pretensioner - Passenger side IGN
Once the ignition starts, the SDM starts to diagnose the air bag system during the ignition process.
If the system is OK, the SDM is armed for a specific impact on the vehicle. The ignition time takes about
6 sec.
Page 1029 of 1082
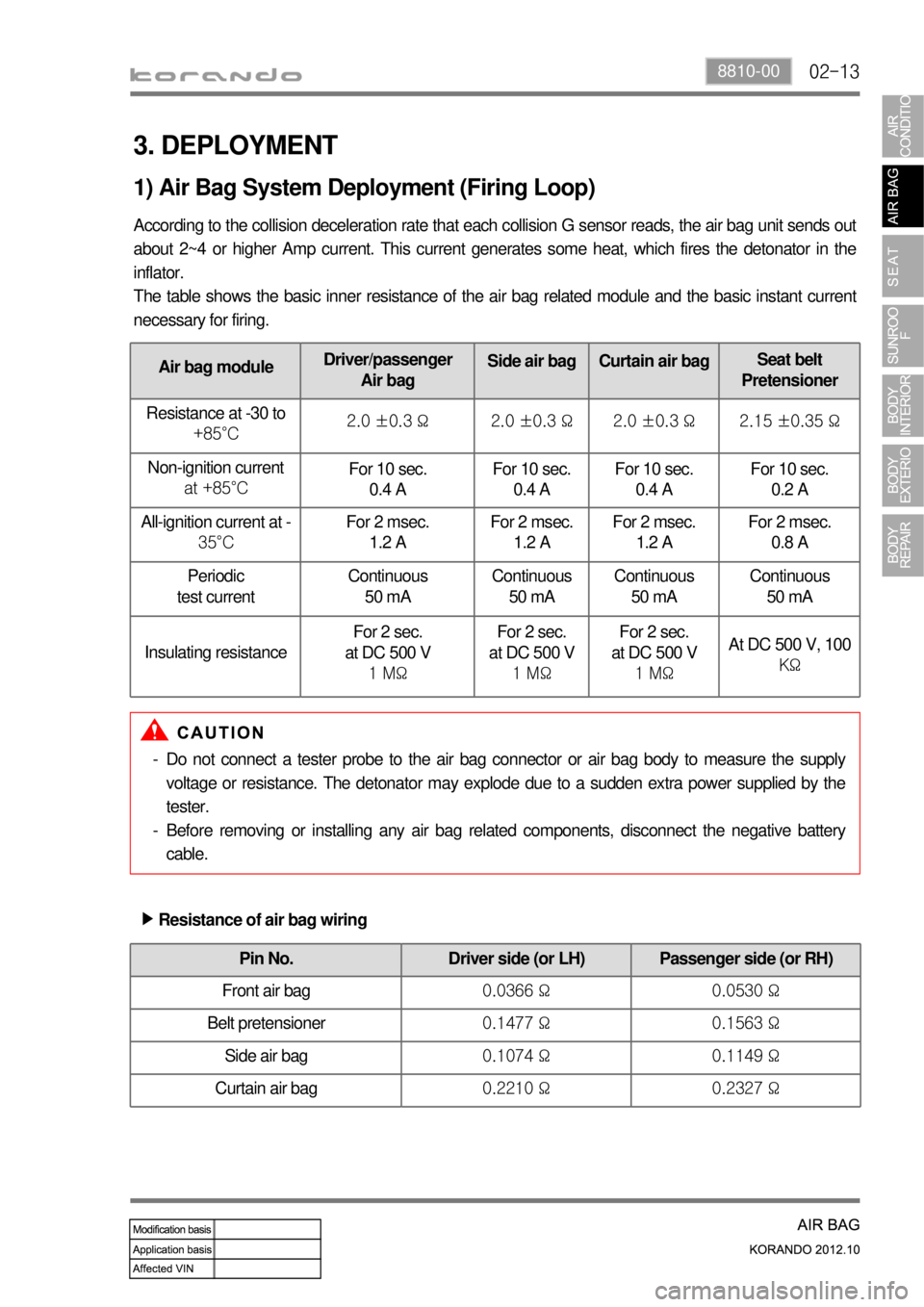
02-138810-00
Air bag moduleDriver/passenger
Air bagSide air bag Curtain air bagSeat belt
Pretensioner
Resistance at -30 to
+85°C2.0 ±0.3 Ω 2.0 ±0.3 Ω 2.0 ±0.3 Ω 2.15 ±0.35 Ω
Non-ignition current
at +85°CFor 10 sec.
0.4 A For 10 sec.
0.4 AFor 10 sec.
0.4 AFor 10 sec.
0.2 A
All-ignition current at -
35°CFor 2 msec.
1.2 AFor 2 msec.
1.2 AFor 2 msec.
1.2 AFor 2 msec.
0.8 A
Periodic
test currentContinuous
50 mAContinuous
50 mAContinuous
50 mAContinuous
50 mA
Insulating resistanceFor 2 sec.
at DC 500 V
1 MΩFor 2 sec.
at DC 500 V
1 MΩFor 2 sec.
at DC 500 V
1 MΩ
At DC 500 V, 100
KΩ
3. DEPLOYMENT
According to the collision deceleration rate that each collision G sensor reads, the air bag unit sends out
about 2~4 or higher Amp current. This current generates some heat, which fires the detonator in the
inflator.
The table shows the basic inner resistance of the air bag related module and the basic instant current
necessary for firing.
1) Air Bag System Deployment (Firing Loop)
Do not connect a tester probe to the air bag connector or air bag body to measure the supply
voltage or resistance. The detonator may explode due to a sudden extra power supplied by the
tester.
Before removing or installing any air bag related components, disconnect the negative battery
cable. -
-
Pin No. Driver side (or LH) Passenger side (or RH)
Front air bag 0.0366 Ω 0.0530 Ω
Belt pretensioner 0.1477 Ω 0.1563 Ω
Side air bag 0.1074 Ω 0.1149 Ω
Curtain air bag 0.2210 Ω 0.2327 Ω
Resistance of air bag wiring ▶
Page 1030 of 1082
02-14
2) Air Bag Deployment Signal Output (Crash Out)
When a situation which requires air bag deployment occurs, they system outputs the air bag deployment
signal (crash out). If another air bag-required situation occurs while the deployment signal is sent, the
second crash out will be delayed until the current 200 ms crash out is completed. (The tolerance at the
time of signaling is ±5%)
The signal repeats increasing for 390 msec. and decreasing for 10 msec. before crash. At the time of
crash, the switch is closed and the signal is kept low condition for 200 msec.
At the time of crash, the crash out signal is changed to the low condition for 200 ms immediately to
indicate the crash moment.
Page 1031 of 1082
02-158810-00
Collision signal interface ▶
The open collector driver raises or lowers the voltage of the pin no. 58 by switching on and off the drive
transistor. The vehicle module can be operated normally only by the logic of open collector interface
and can be maintained in a pull-up state. The followings are the specifications of the electrical interface.
The load resistance of the SDM is 590 ohms or higher. It may not be possible to operate the collision
occurrence circuit normally if the resistance value is not as specified.
Pin No. Minimum Average Maximum Remark
Driving current (current value
when the transistor is turned
on) 12.31 mA 19.6 mA 30 mA Depending on the
battery voltage
Leakage current (current value
when the transistor is turned
off) 147.6 μA 376 μA No crash signal
Load resistance 590 ohms Above than this value
Page 1032 of 1082
02-16
3) CAN Communication Interface (FIS and SIS)
The CAN communication interface uses the PWM for the supply current and the current loop and
communicates with the SDM to transmit the information. The serial communication and power for the
satellite are supplied through the communication line.
Stage FIS SIS
Initial stage Tracking/Check (Self test) Same as FIS
Normal operation Checks the FIS condition and sends the result as
"OK" or "NOK", and also sends the "severity" of the
crash. Same as FIS
Voltage The FIS hardware reset was performed under 5 V,
communication voltage low Same as FIS
Fault The fault is found in the current ignition cycle but the
fault is deactivated in the next ignition cycle. Multiple faults can be found
and deactivated in the same
ignition cycle.
The FIS moves to the initial stage if 'leakage to GND' is occurred in normal operating stage to shut down
the power and prevent abnormal operation.
※ FIS: Front Impact Sensor
SIS: Side Air bag Sensor