Page 105 of 1082
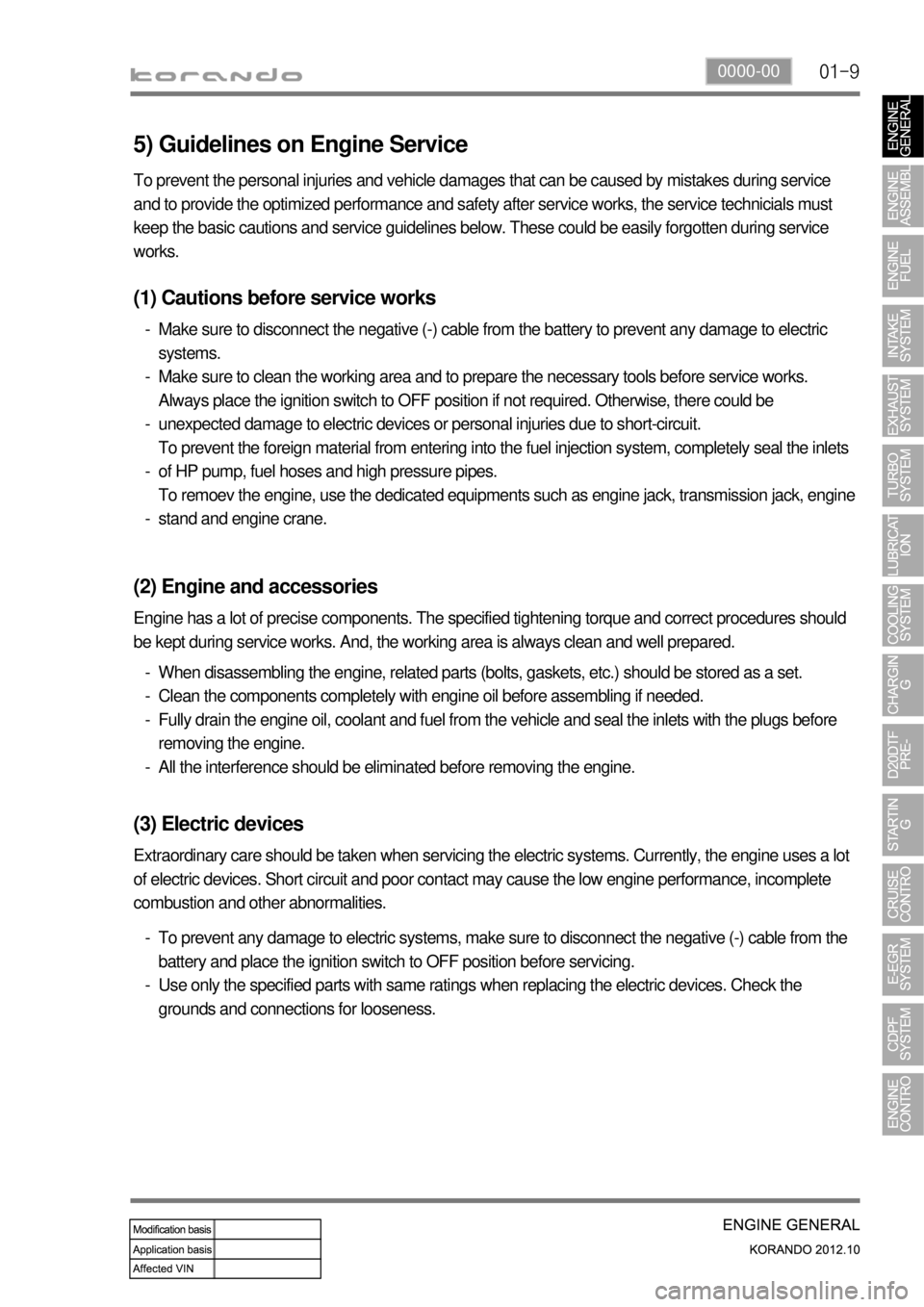
01-90000-00
5) Guidelines on Engine Service
(1) Cautions before service works
Make sure to disconnect the negative (-) cable from the battery to prevent any damage to electric
systems.
Make sure to clean the working area and to prepare the necessary tools before service works.
Always place the ignition switch to OFF position if not required. Otherwise, there could be
unexpected damage to electric devices or personal injuries due to short-circuit.
To prevent the foreign material from entering into the fuel injection system, completely seal the inlets
of HP pump, fuel hoses and high pressure pipes.
To remoev the engine, use the dedicated equipments such as engine jack, transmission jack, engine
stand and engine crane. -
-
-
-
-
(2) Engine and accessories
When disassembling the engine, related parts (bolts, gaskets, etc.) should be stored as a set.
Clean the components completely with engine oil before assembling if needed.
Fully drain the engine oil, coolant and fuel from the vehicle and seal the inlets with the plugs before
removing the engine.
All the interference should be eliminated before removing the engine. -
-
-
-
(3) Electric devices
To prevent any damage to electric systems, make sure to disconnect the negative (-) cable from the
battery and place the ignition switch to OFF position before servicing.
Use only the specified parts with same ratings when replacing the electric devices. Check the
grounds and connections for looseness. -
- To prevent the personal injuries and vehicle damages that can be caused by mistakes during service
and to provide the optimized performance and safety after service works, the service technicials must
keep the basic cautions and service guidelines below. These could be easily forgotten during service
works.
Engine has a lot of precise components. The specified tightening torque and correct procedures should
be kept during service works. And, the working area is always clean and well prepared.
Extraordinary care should be taken when servicing the electric systems. Currently, the engine uses a lot
of electric devices. Short circuit and poor contact may cause the low engine performance, incomplete
combustion and other abnormalities.
Page 106 of 1082
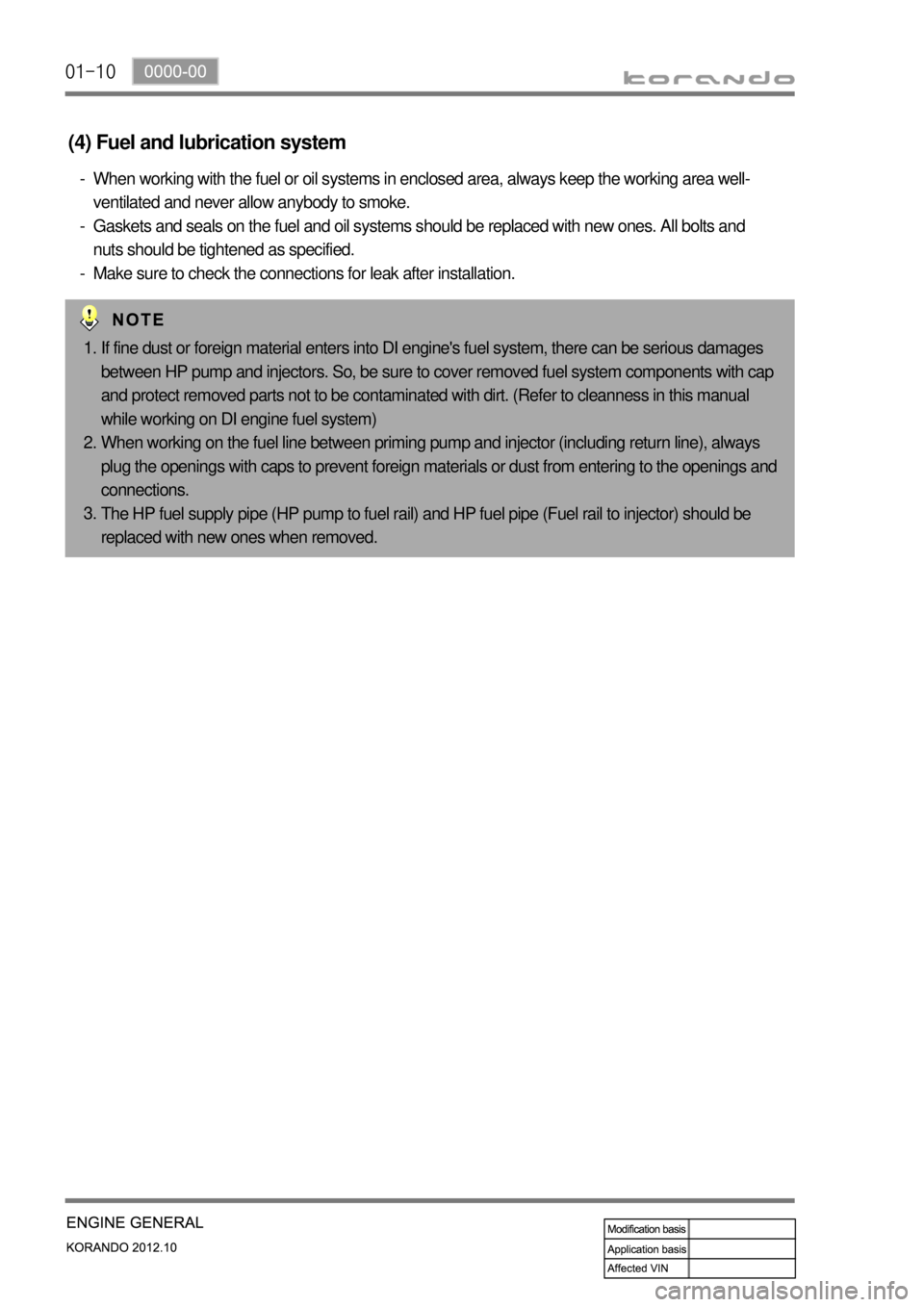
01-10
(4) Fuel and lubrication system
When working with the fuel or oil systems in enclosed area, always keep the working area well-
ventilated and never allow anybody to smoke.
Gaskets and seals on the fuel and oil systems should be replaced with new ones. All bolts and
nuts should be tightened as specified.
Make sure to check the connections for leak after installation. -
-
-
If fine dust or foreign material enters into DI engine's fuel system, there can be serious damages
between HP pump and injectors. So, be sure to cover removed fuel system components with cap
and protect removed parts not to be contaminated with dirt. (Refer to cleanness in this manual
while working on DI engine fuel system)
When working on the fuel line between priming pump and injector (including return line), always
plug the openings with caps to prevent foreign materials or dust from entering to the openings and
connections.
The HP fuel supply pipe (HP pump to fuel rail) and HP fuel pipe (Fuel rail to injector) should be
replaced with new ones when removed. 1.
2.
3.
Page 107 of 1082
01-110000-00
2. JACK-UP POINTS
Stand jack-up points and installation status (front side) ▶
Jack-up points for
2-post liftJack-up points for
2-post liftSupporting
Jack-up points and setup
(rear side)
Supporting
Jack-up points and setup
(front side)
Page 108 of 1082
01-12
3. STANDARD BOLTS SPECIFICATIONS
Metric bolt strength is embossed on the head of each bolt. The strength of bolt can be classified as
4T, 7T, 8.8T, 10.9T, 11T and 12.9T in general.
Observe standard tightening torque during bolt tightening works and can adjust torque to be proper
within 15 % if necessary. Try not to over max. allowable tightening torque if not required to do so.
Determine extra proper tightening torque if tightens with washer or packing.
If tightens bolts on the below materials, be sure to determine the proper torque. 1)
2)
3)
4)
Aluminum alloy: Tighten to 80 % of above torque table.
Plastics: Tighten to 20 % of above torque table. -
-
Page 109 of 1082
01-130000-00
4. CODING AND SETUP
1) Engine Variant Coding
Page 110 of 1082
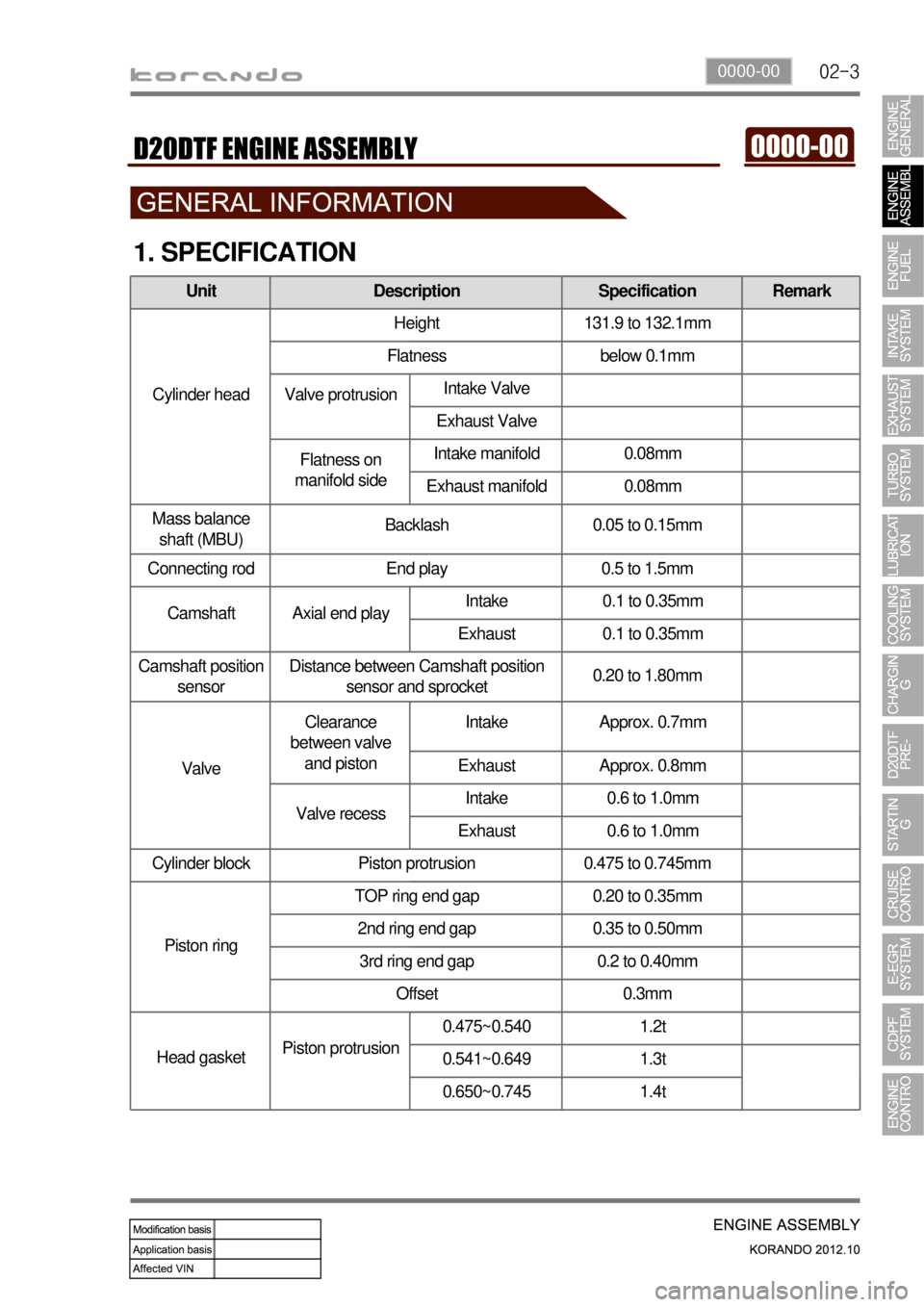
02-30000-00
Unit Description Specification Remark
Cylinder head Height 131.9 to 132.1mm
Flatness below 0.1mm
Valve protrusion Intake Valve 0.1~0.7mm
Exhaust Valve 0.1~0.7mm
Flatness on
manifold sideIntake manifold 0.08mm
Exhaust manifold 0.08mm
Mass balance
shaft (MBU)Backlash
0.05 to 0.15mm
Connecting rod End play 0.5 to 1.5mm
Camshaft Axial end play Intake 0.1~0.35mm
Exhaust 0.1~0.35mm
Camshaft position
sensorDistance between Camshaft position
sensor and sprocket0.20 to 1.80mm
Valve밸브와 피스톤
간극Intake약 0.7mm
Exhaust약 0.8mm
Valve recess Intake 0.1~0.7mm
Exhaust
실린더 블록 피스톤 돌출량0.475 to 0.745mm
피스톤 링 TOP 링 엔드 갭0.20 to 0.35mm
2nd 링 엔드 갭0.35 to 0.50mm
3rd 링 엔드 갭0.2 to 0.40mm
옵셋 (off-set)0.3mm
헤드 가스켓 피스톤 돌출량0.475~0.540 1.2t
0.541~0.649 1.3t
0.650~0.745 1.4t
1. SPECIFICATION
Unit Description
Cylinder headHeight
Flatness
Valve protrusionIntake Valve
Exhaust Valve
Flatness on
manifold sideIntake manifold 0.08mm
Exhaust manifold 0.08mm
Mass balance
shaft (MBU)Backlash
Connecting rod End play
Camshaft Axial end playIntake 0.1 to 0.35mm
Exhaust 0.1 to 0.35mm
Camshaft position
sensorDistance between Camshaft position
sensor and sprocket
ValveClearance
between valve
and pistonIntake Approx. 0.7mm
Exhaust Approx. 0.8mm
Valve recessIntake 0.6 to 1.0mm
Exhaust 0.6 to 1.0mm
Cylinder block Piston protrusion
Piston ringTOP ring end gap
2nd ring end gap
3rd ring end gap
Offset
Head gasketPiston protrusion0.475~0.540 1.2t
0.541~0.649 1.3t
0.650~0.745 1.4t
Page 111 of 1082
02-4
2. TIGHTENING TORQUE
Component Size
QuantityTightening torque
(Nm)Remark
(Total torque)
Main bearing capM12×821055 ± 5Nm,
180˚Not re-usable
Connecting rod capM9×52840 ± 5Nm,
90˚ ± 10˚50~80Nm
Crankshaft rear cover
M6×20610 ± 1Nm-
Oil pumpM8×35325 ± 2.5Nm-
FlywheelM10×22845 ± 5Nm,
90˚ ± 10˚Not re-usable
Isolation damper center
boltM18×501200 ± 20Nm,
180˚ ± 20˚660~720Nm
Not re-usable
Oil panM6×201810 ± 1Nm-
M6×35210 ± 1Nm-
M6×85210 ± 1Nm-
M6×120210 ± 1Nm-
M8×40225 ± 2.5Nm-
HP pump main nutM14×1.5-8-11650 ± 5Nm-
HP pump mounting bolt
M8×553
25 ± 2.5Nm-
Cylinder headM13×1501285Nm
270° ± 10°-
Camshaft capM6×301610 ± 1Nm-
M8×60425 ± 2.5Nm-
Exhaust stud bolt 1015 ± 1.5Nm-
Exhaust sprocket boltM11×40130 ± 3Nm-
Chain tensioner screw
plugM38×1.5125 ± 2.5Nm
-
Coolant temperature
sensor120 ± 2.0Nm-
Belt auto tensionerM8×30(LOW)125 ± 2.5Nm-
M10×75(Upper)155 ± 5.5Nm-
Coolant pumpM6×50710 ± 1.0Nm-
Page 112 of 1082
02-50000-00
품명 규격 볼트
수량규정토오크(Nm) 비고
(총 토오크)
Knock sensorM8×28220 ± 5Nm-
Cam position sensorM8×141 10 ~ 14Nm -
T-MAP pressure sensor
M6×201
10 ± 1Nm-
Exhaust manifold M8 1040 ± 4Nm-
Turbocharger M8 325 ± 2.5Nm-
T/C support bracket bolt
125 ± 2.5Nm-
T/C support bracket bolt
M8 125 ± 2.5Nm-
T/C oil supply pipeM6(block side) 110 ± 1.0Nm-
M6(turbo side) 117 ± 2.0Nm-
T/C oil return pipeM6×16
(turbo side)210 ± 1Nm-
M6×16
(block side)210 ± 1Nm-
EGR valveM8×22325 ± 2.5Nm-
EGR pipe bolt (Intake
side)M6×25210 ± 1Nm-
EGR pipe bolt (EGR
cooler side)M8×16225 ± 2.5Nm-
Component Size
QuantityTightening torque
(Nm)Remark
(Total torque)
Hot water inlet pipeM6×12210 ± 1Nm-
AlternatorM10×90125 ± 2.5NmLower
M10×116146 ± 4.6NmUpper
A/C compressorM8×85425 ± 2.5Nm-
A/C bracketM6×25410 ± 1Nm-
Intake manifoldM8×35225 ± 2.5Nm-
M8×110625 ± 2.5Nm-
Oil filter moduleM8×40625 ± 2.5Nm-
M8×20125 ± 2.5Nm-
M8×140225 ± 2.5Nm-