Page 161 of 1413
3. Measuro the piston pin-to-piston clearance.
NOTE: Check the Diston for distonion or cracks.
It the piston pin clearance is greater than 0.022 mm(0,0009 in), remeasure using an ovorsize piston pin.
Pbton Pin-to-PLton Cloeranco:
StlndErd (Ncwl: 0.010 - 0.022 mm(0.(xto4 - o.(Xxlg inl
4. Check the difference betwsen piston pin diameter
and connecting rod small end diam€ter.
Pbton Pin-to4onnocting Rod Inlcdaranca:
Strndlrd {Ncw}:
Bl8Bl ongino: 0.013 - 0.G12 mm(0.fiX15 - 0.0013 inl
Bl8Cl cngin.: 0.017 - 0.036 mm
IO.ON1 - O.|,o11 int
Connecting Rods
End Play
NOTE: End play should bs insp€cted before removing
the crankshaft.
Connrcting Rod End Pl.y:
Stlndrrd (Nrwl: 0.15 - o.3o mm(0.(xt6 - 0.012 inl
Scrvict Limit o./to mm (0.016 inl
lf out-of-tolerance, install a new connscting rod.
lf still out-of-to16rance, replace the crankshaft
pages 7-10 and 7-22)
a
a
7-21
Page 162 of 1413
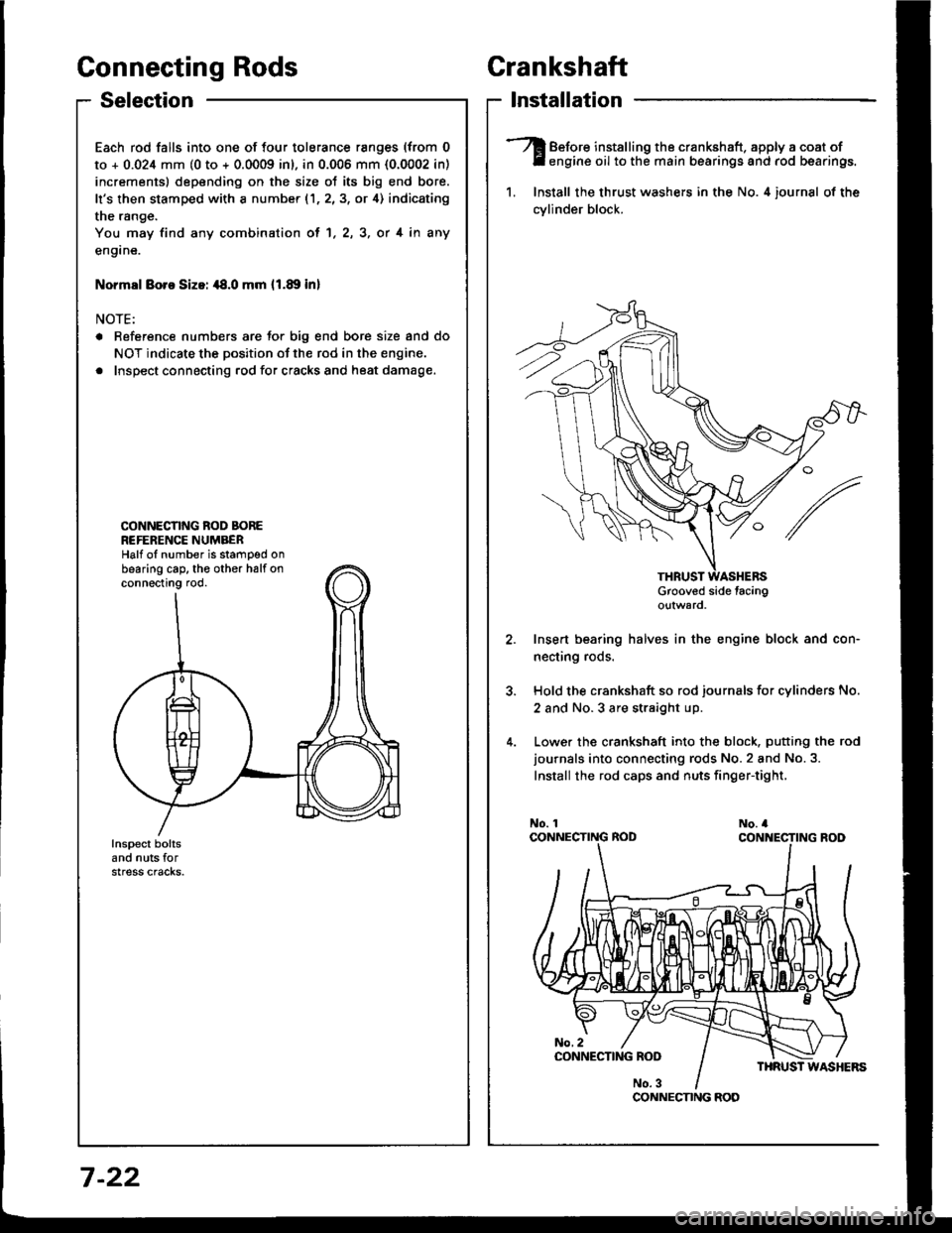
Connecting Rods
Selection
Each rod falls into one of four tolerance ranges (from 0
to + 0.024 mm (0 to + 0.0009 inl, in 0.006 mm {0.0002 in)
increments) depending on the size ot its big end bore.
It's then stamped with a number (1,2,3, or 4) indicating
the range.
You may find any combination ol 1, 2, 3, or 4 in any
engane.
Normsl Boro Sizoi ,18.0 mm 11.89 inl
NOTE:
a Reference numbers are Jor big end bore size and do
NOT indicate the position of the rod in the engine.
. Inspect connecting rod for cracks and heat damage.
CONNECNNG ROD BOREREFERENCE NUMBERHalf oI number is stamped onbearing cap. th€ other halfonconnecting rod.
Crankshaft
lnstallation
Before installing the crankshaft. apply a coat ofengine oil to the main bearings and rod bearings.
1. Install the thrust washers in the No. 4 iournsl of the
cvlinder block.
Grooved side tacingo!tward
Insert bearing halves in the engine block and con-
necting rods.
Hold the crankshaft so rod journals for cylinders No.
2 and No.3 are straight up.
Lower the crankshaft into the block. putting the rod
journals into connecting rods No.2 and No.3.
Install the rod caps and nuts finger-tight,
CONNECNNG ROD
7 -22
Page 163 of 1413
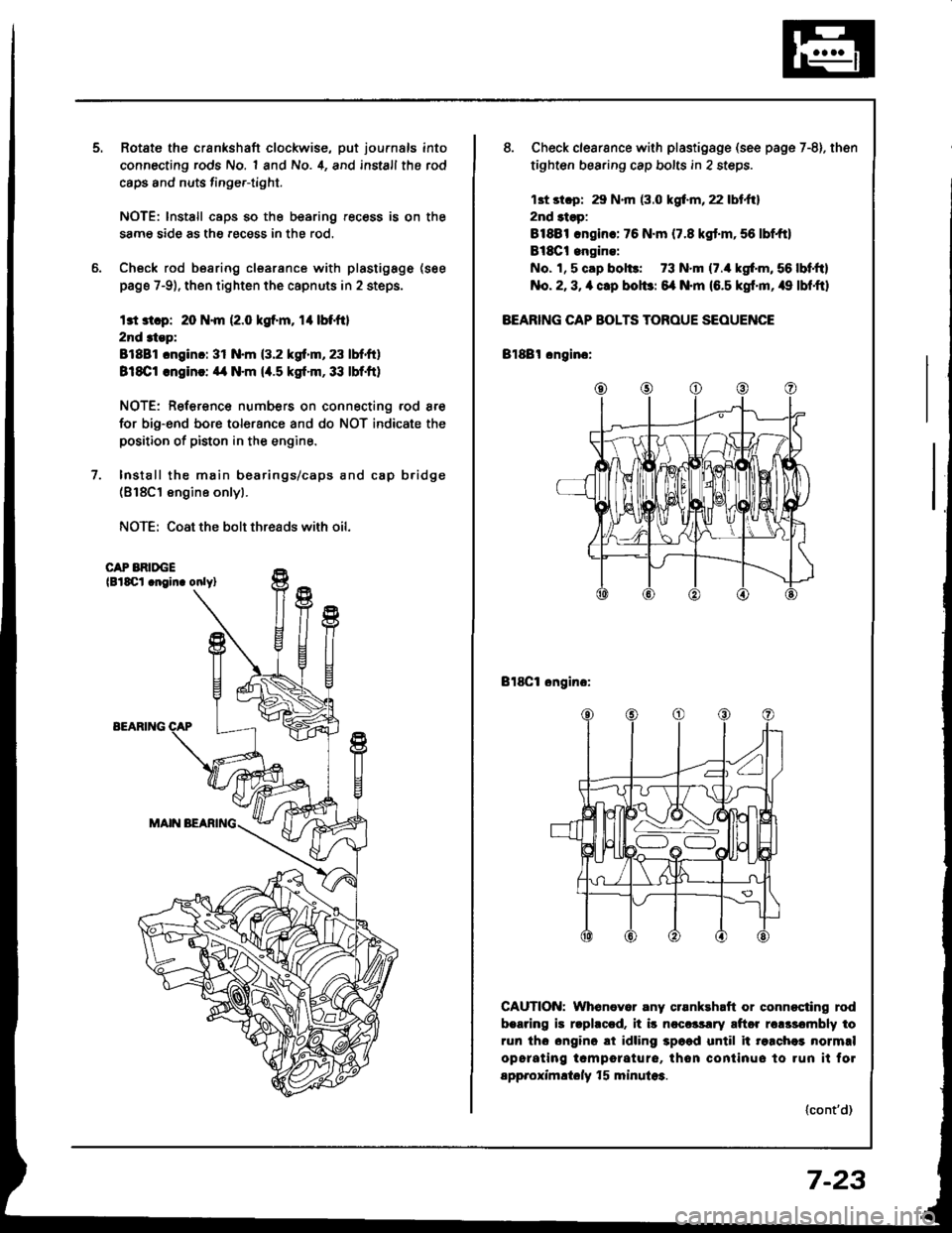
Rotate the crankshaft clockwise, put journals into
connecting rods No. 1 and No. 4, and install the rod
caps and nuts finge.-tight.
NOTE: lnstall caps so the bearing recess is on the
samg side as the .ecess in the rod.
Check rod bearing clsarance with plastigage (see
page 7-9), then tighten the capnuts in 2 steps.
l3t 3t.p: 20 N.m (2.0 kgf.m, rl btfil
2nd 3tep:
81881 cnginc: 31 N.m (3.2 kgf.m, 23 lbf.ft)
818C1 .ngin!: ,14 N.m (4.5 kgt.m,33 lbf.ft)
NOTE: Reference numbers on connecting rod are
for big-end bore tolorance and do NOT indicate the
positioo of piston in the engine.
Install the main bearings/caps and cap b.idge(818C1 engine onlyl.
NOTE: Coat the bolt threads with oil.
CAP BRIDGElBlSCl .noin. onlyl
EEARIlTG
8. Check clearsnce with plastigsge (see page 7-8). then
tighten bearing cap bolts in 2 steps.
13t st.p: 29 N.m (3.0 kgf.m, 22 lbt.ftl
2nd 3tsp:
81881 .ngin.: 76 N.m (7.8 kgt.m,56 lbf,ft)
Bl8Ct engine:
No. 1, 5 cap bol$: 73 N.m (7./r kgf'm, 56 lbf,ftl
No. 2, 3, a clp bolbr 6{ N.m (6.5 kgf'm, /r9 lbf,ftl
BEARING CAP BOLTS TOROUE SEOUENCE
Bl88l cngino:
Bl8Cl ongino:
CAUTION: Whenever any crsnkehaft or connocting rod
b.aring is rlphccd. it i5 ncccrsrry aftor rclssombly to
run tho ongino ai idling 3p6ad until it re.chei normrl
opcrating tcmporature, thon continuo to run it fol
spp.oximltoly f 5 minula3.
(cont'd)
7-23
Page 164 of 1413
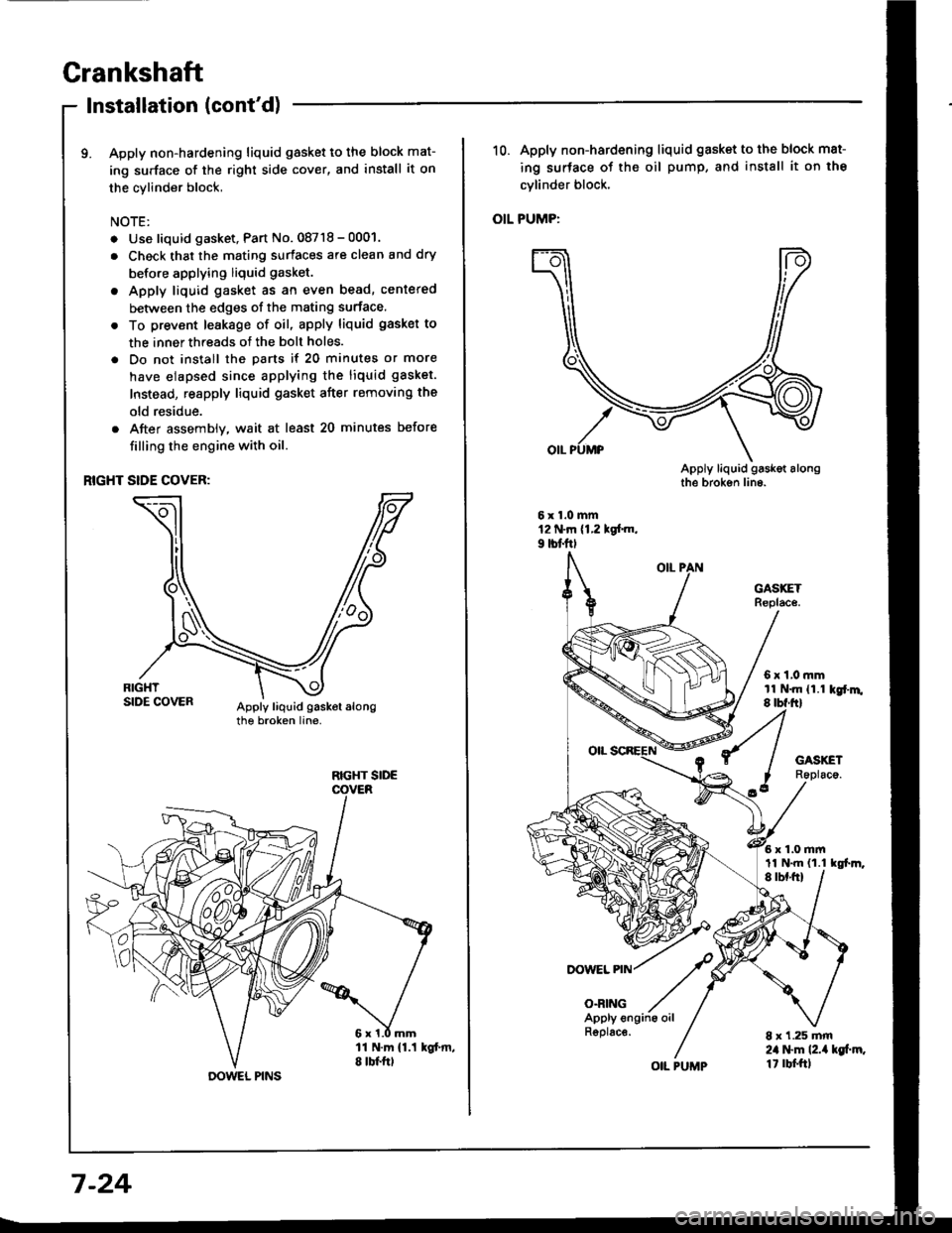
Grankshaft
Installation (cont'd)
9. Apply non-hardening liquid gasket to the block mat-
ing surface of the right side cover, and install it on
the cylinder block,
NOTE:
. Use liquid gasket, Part No. 08718 - 0001.
. Check that the mating surfaces are clean and dry
before applying liquid gasket.
. Apply liquid gasket as an even bead, centered
between the edges of the mating surface.
. To prevent leakage of oil, apply liquid gasket to
the inner threads of the bolt holes.
. Do not install the parts if 20 minutes or more
have elapsed since applying the liquid gasket.
Instead, reapply liquid gasket after removing the
old residue.
. After assembly, wait at least 20 minutes before
filling the engine with oil.
RIGHT SIDE COVER:
RIGHT SIDE
DOWEL PINS
7-24
R6plac€.
OIL PUMP
10. Apply non-hardening liquid gasket to the block mat-
ing surface of the oil pump, and install it on the
cvlinder block.
OIL PUMP:
DOWEL PIN
O.RING
6x1,0mmtl N.m {1.1 kgr'm.8 tbf.ftl
6x1.0mm
8 x 1.25 mm2il l$m l2.ia kg[.m.1t rbf.ftl
11 N.m {1.1 tgl.m,
Page 165 of 1413
11.lnstallthe oil screen.
Installthe oil pan.
NOTE: Clean the oil pan gasket mating surfaces.
Tighten the bolts as shown below.
Torque: 12 N.m {1.2 kgf.m, 9 lbf'ft)
NOTE: Tighten the bolts and nuts in two steps and
toroue the bolts in a crisscross pattern
1' I
Oil Seal
lnstallation
The seal surface on the block should be dry.
Apply a light cost of oil to the crankshaft and to
the liD of the seal.
Drive in flywheel end seal against right side cover.
NOTE: Drive the end seal in squarely.
DRIVER07t,49 - (xll(xtoo
2. Confirm that clearance is equal all the way around
with a fe€ler gauge.
Cler.6nce: 0.5 - 0.8 mm (0.02 - 0.03 inl
RIGHT SIDECOVER
NOTE: Reter to right column and 8-10 lor installa-
tion of the oil pump side oil seal.
lnstall sealwith thepart number sidetacing out.
7-25
Page 166 of 1413
Installation (engine removal not
S€AL DRIVEB07LAD - PRimroAlnstallse6lwith tho
Pan numbertacing out.
Using the special tool, drive in the flywheel-end seal
until the driver bottoms against block.
NOTE: Align the hole in the drivsr attachment withthe Din on the crankshaft.
Oil Seal
required)
The seal surface on the block should b€ dry.Apply a light coat of grease to the crankshaft andto the lio of seal.
Using the special tool, drive in the timing pullsy-
end seal until the driver bottoms against the oilpump.
When the seal is in place, clean any excess grease
off lhe crankshaft and check that the oil seal tiD isnot distoned.
7-26
Page 167 of 1413
Engine Lubrication
Speciaf Tools ........ ........8-2
lllustrated Index ........ ."' 8-3
Engine Oil
Inspection ..........."'...' 8-5
Replacement ................ " ".......'.'. 8-5
Oil Filter
Replacement ...................... "....... 8-6
Oil Pressure
Testing ....' 8-8
Oil Jet
Inspection {818C1 engine only} ..... 8-8
Oil Pump
Overhaul ... 8-9
Removal/lnspection/lnstallation . . ' . . . 8- 1 O
Page 168 of 1413
Special Tools
Rel. No. I Tool NumbelDescrlptionOty I Pago Roferenco
o
@
OTLAD _ PR4Ol OA
o791 2 -61 10001
Seal Driver
Oil Filter Wrench
8-11
8-7
o
8-2