Page 337 of 1413
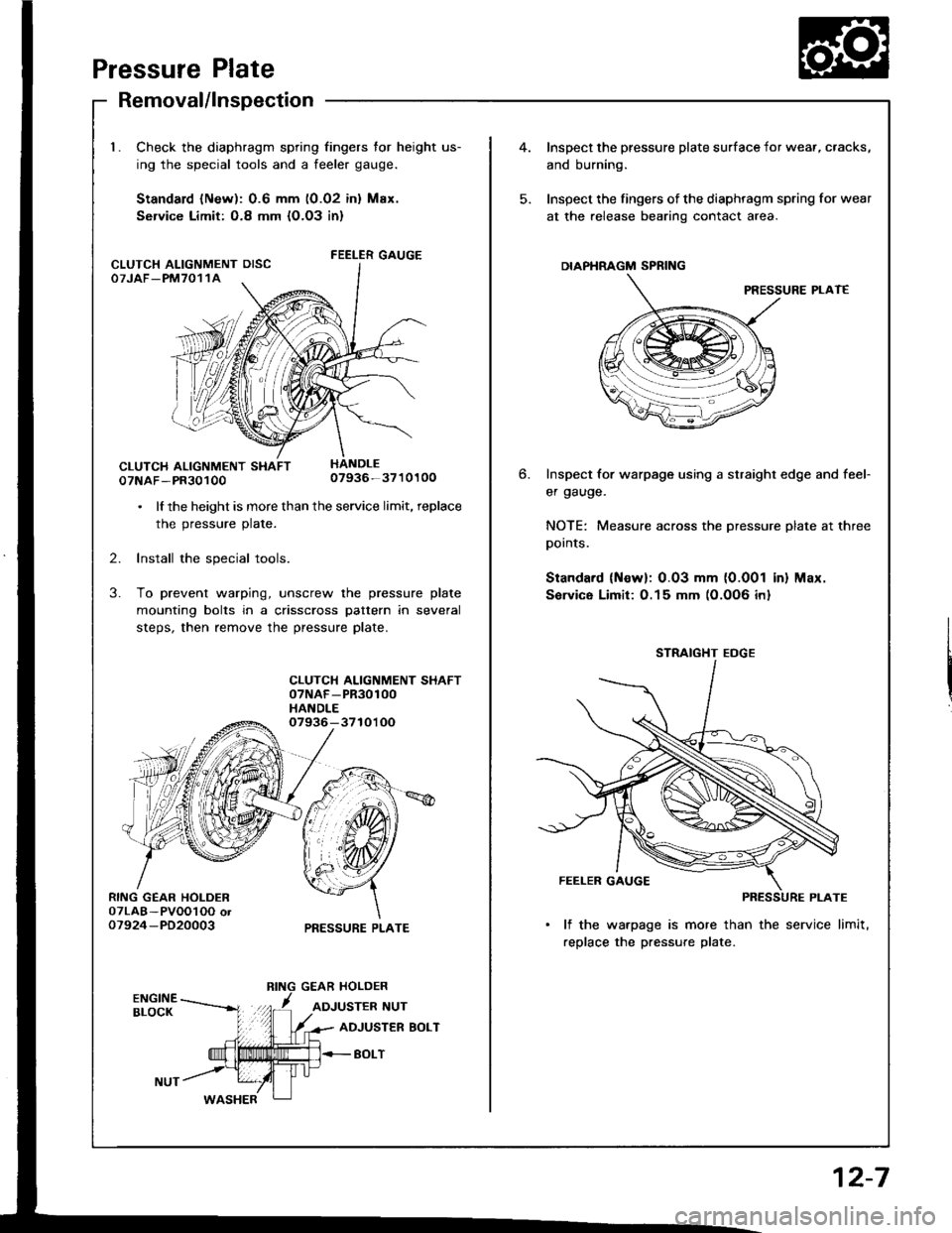
Pressure Plate
RING GEAR HOLDER07LAB-PVOOl OO or07924-PD20003
Removal/lnspection
Check the diaphragm spring fingers for height us-
ing the special tools and a feeler gauge.
Standard lNew): 0.6 mm (0.02 inl Max.
Service Limit: O.8 mm {O.O3 in}
FEELER GAUGE
07NAF-PR3010007936-3710100
. lf the height is more than the service limit, replace
the pressure plate.
2. Install the special tools.
3. To prevent warping, unscrew the pressure plate
mounting bolts in a crisscross pattern in several
steps, then remove the pressure plate.
CLUTCH ALIGNMENT SHAFT07NAF-PR30100HANDLE07936-3710'l OO
PRESSURE PLATE
CLUTCH ALIGNMENT OISCOTJAF_PM7011A
4.Inspect the pressure plate surface
and burning.
Inspect the fingers of the diaphrag
at the release bearing contact ar
DIAPHRAGM SPRING
Inspect for warpage using a stru
er gauge.
NOTE: Measure across the prer
pornls.
Standard (Newl: 0.03 mm (0.0
Sorvice Limit:0.15 mm (0.0O6
STRAIGHT EOGE
FEELER GAUGE
PI
lf the warpage is more than
replace the pressure plate.
6.
I surface for wear, cracks,
diaphragm spring for wear
nracr area.
PRESSURE PLAT€
straight edge and feef
pressure plate at three
0.001 in) Max.
)O6 inl
12-7
Page 338 of 1413
Glutch Disc
'1.Remove the clutch disc and special tools.
Inspect the lining of the clutch disc Jor signs oJ slip-
ping o. oil. lf it is bu.ned black or oil soaked, replace
it.
Measure the depth trom the lining surface to the
rivets, on both sides.
Standard (Now): 1.3 mm (O.05 inl Min.
Se.vice Limit: O.2 mm {O.OO8 inl
CLUTCH ALIGNMEI{T SHAFT07NAF-PR30100HAt{DLE07936-3710 t0O
Measu.e the clutch disc thickness.
Standard {Now}: 8.4-9.1 mm (o.33*0.36 inl
Sarvica Limit: 6.0 mm (O.24 in)
It the rivet deDth is less than the service limit,
reolace the clutch disc.
lf the thickness is less than the service limit,
reolace the clutch disc,
CLUTCH DISCCLUTCH DISC
LINING SURFACE
CLUTCH DISC
Removal/lnspection
ctutch Disc I
'.#fu;;
l''
"LUrcH Drsc |
""-*":'-- {o'oo8 inr
I I
=-.--']! ; i , n-
ll
W@*-l @
slbir":ix:l# Ii!fr..;*'::l;'"o^"
|
'=f
I I
3. Measu.e the clutch disc thic
Page 339 of 1413
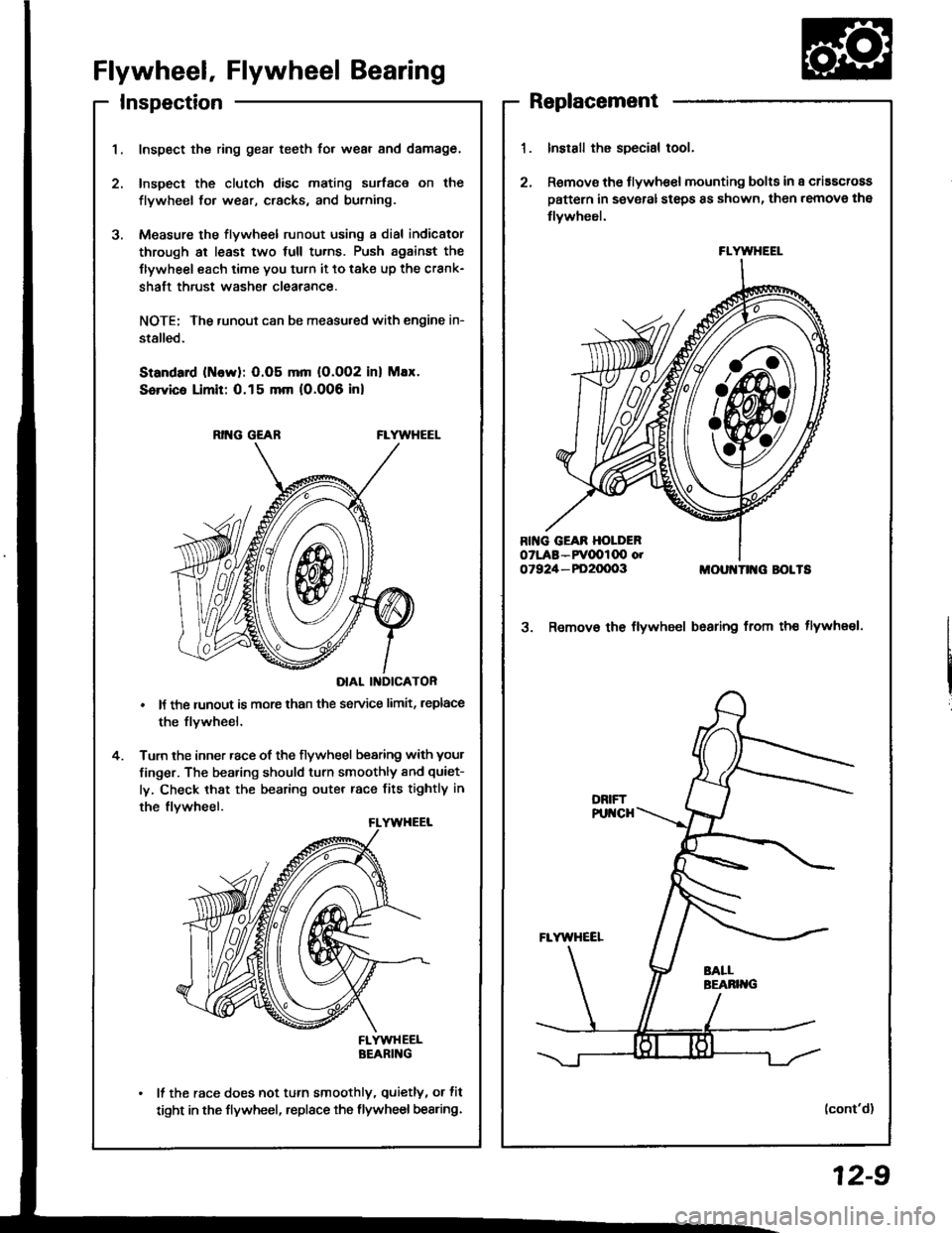
InspectionReplacement
Flywheel, Flywheel Bearing
Inspect the ring gear teeth for wear and damage.
Inspect the clutch disc mating surface on the
flywheel fo. wear, cracks, and burning.
Measure the flywheel runout using a dial indicator
through at least two full tu.ns. Push against the
Ilywheel each time you turn it to take up the crank-
shaft thrust washe. clearance.
NOTE; The runout can be measu.ed with engine in-
stalled.
Standard (ttlervl: O.O5 mm (O.002 inl Max.
Service Limit: 0.15 mm 10.006 inl
RING GEABFLYWHEEL
DIAL II{DICATOR
It the runout is more than the service limit, leplace
the flvwheel.
Turn the inner race of the flywheel bearing with your
finger. The bearing should turn smoothly and quiet-
ly, Check that the bearing outer race fits tightly in
the flvwheel.
FLYWHEELBEARING
It the race does not turn smoothly, quietly, or fit
tight in the flywheel, replace the flywheel bearing.
Install the special tool.
Remov€ the flywhe€l mounting bolts in a criascross
pattern in several steps 8s shown, then remove the
tlywheel.
MOUI{TII{G BOLTS
3. Remov€ the flywheel bsaring from th€ tlywheel.
(cont'd)
FLYWHEEL
12-9
Page 340 of 1413

Clutch Disc,
l.
t
Flywheel, Flywheel BearingPressure Plate
Replacement (cont'd)Installation
Install the ring gear holder.
Apply grease to the spline of the clutch disc, theninstall the clutch disc using the special tools assnown.
NOTE: Use only Super High Temp Urea Grease (P/N
08798-9OO2).
CLUTCH DISC
RING GEAR HOLDEROTLAB-PVOOI O0 ot07924-PD20003
3. Instali the pressure
CLUTCH ALIGNMENT SHAFT07NAF-PR30100HANDLE07936-3710100
plate.
CLUTCH ALIGNMENT SHAFToTNAF-PR30100HANDLE
PRESSURE PLATE
12-10
4. Drive the new flywheel bearing into the flywheel us-
ing rhe special tools as shown.
DRIVER07749-O010000
ATTACHMENT.32x35mm07746-OOlO100
o.
5.
FLYWHEEL
Align the hole in the flywheel with the crankshaft
dowel pin and installthe flywheel. Installthe mount-
ing bolts finger-tight.
Install the special tool as shown, then torque the
flywheel mounting bolts in a crisscross pattern in
several steDs as shown.
MOUNTING BOLTS12 x 1.0 mm103 N.m 110.5 kgf.m,76 tbf.fr)
FLYWHEEL BEARING
FLYWHEEL
07936-3710100
t\_
Page 341 of 1413
spection
release fork boot trom the clutch4. Torque the mounting bolts in a crisscross pattern as
shown. Tighten the bolts in several steps to prevent
warping the diaphragm spring.
8 x 1.25 mm25 N.m 12.6 kgt'm,19 tbt.ftl
2. Remove the release tork trom the clutch housing by
squeezing the release fork set spring with pliers. Re-
move the release bearing.
Check the release bearing for play by spinning it by
hand.
CAUTION: The release boaring i6 packed with
grease. Do not wash it in solvent.
Remove the special tools.
Recheck the diaphragm spring fingers tor height (see
page 12-7]..
Release Bearing
Removal/ln
1. Remove the
housing.
CLUTCH HOUSING
RELEASE FORK
-24/--2,t'.2424?'
IJ
l{ there is excessive plaY, rep)ace the rdease\Ear-
ing with a new one.
,F=:=
Page 342 of 1413
Release Bearing
Installation
1.With the release tork slid between the release bear-
ing pawls, install the release bearing on the main-
shaft while inserting the release fo.k through the hole
in the clutch housing.
Align the detent ot the release fork with the release
tork bolt, then press the release fork over the release
fork bolt.
NOTE; Use only Super High Temp Urea G.ease (P/N
08798- 9002).
2.
-611
lPlN 08798-
-6
{P/N 0879a-9002)
Move the release fork right and left to make sure that
the fork tits properly against the release bearing, and
that the release bearing slides smoothly.
4. lnstall the release fork boot.
12-12
Page 343 of 1413
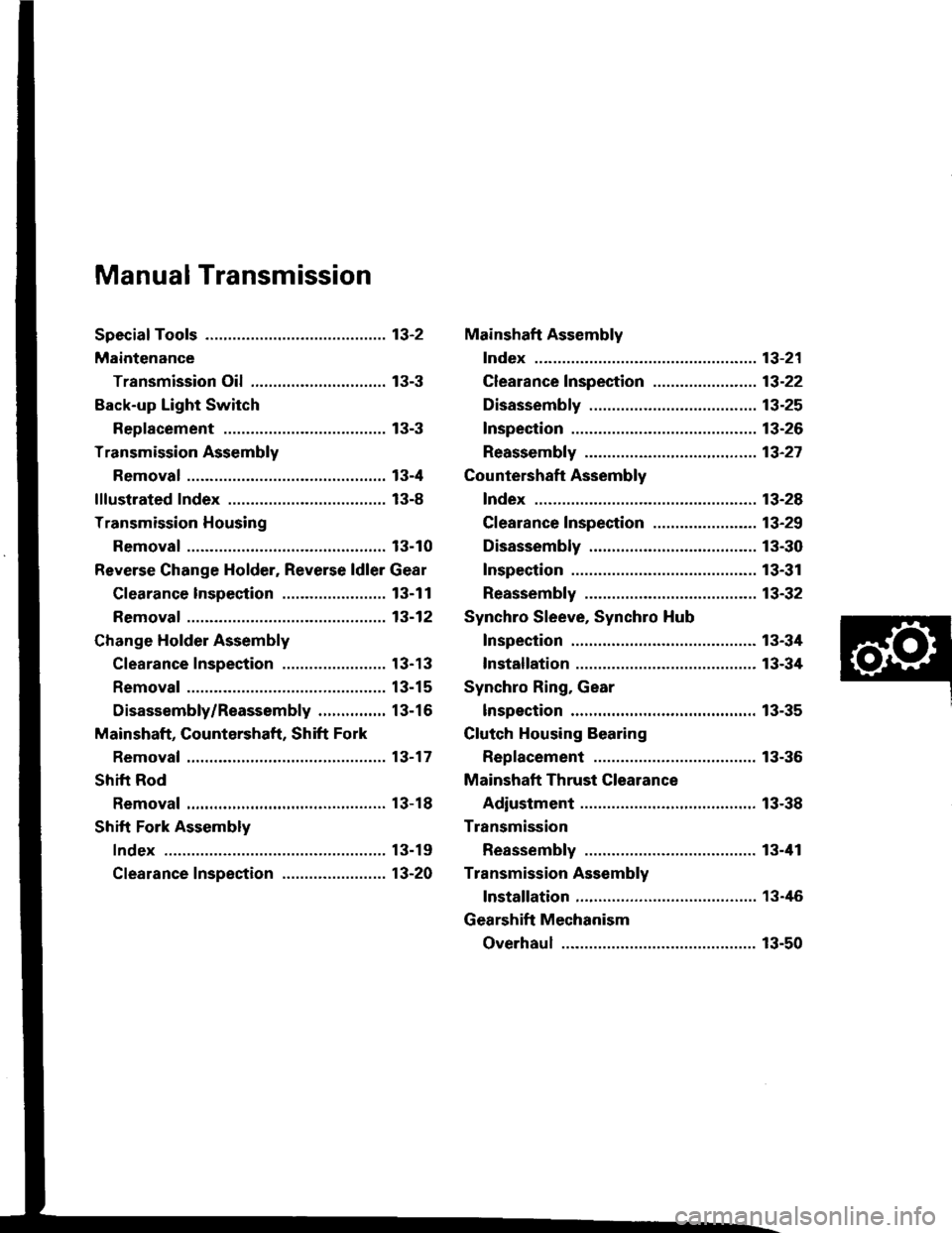
Manual Transmission
Special Toofs ............. 13-2
Maintenance
Transmission Oi1,...,........,........,.,..... 13-3
Back-up Light Switch
Replacement ......... 13-3
Transmission Assembly
Removal ..,.......,...... 13-4
lllustrated Index ................................... 13-8
Transmission Housing
Removal ...........,..... 13-10
Reverse Change Holder, Reverse ldler Gear
Glearance lnspestion ....................... 13-1 1
Removaf ................. 13-12
Change Holder Assembly
Clearance Inspection ....................... 1 3-1 3
Removal ................. 13-15
Disassembly/Reassembly ............... 13-16
Mainshaft, Gountershaft, Shift Fork
Removal ...,............. 13-17
Shift Rod
Removal ................. 13-18
Shift Fork Assembly
Index ................ ...... 13-19
Clearance Inspection ....................... 13-20
Mainshaft Assembly
Index ................ ...... 13-21
Clearance f nspection ....................... 13-22
Disassembly .......... 13-25
Inspection .............. 13-26
Reassembly ........... 13-21
Countershaft Assembly
Index ................ ...... 13-28
Clearance Inspection ....................... 13-29
Disassembly .......... 13-30
Inspection .............. 13-31
Reassembly ........... 13-32
Synchro Sleeve, Synchro Hub
Inspection .............. 13-34
Installation ............. 13-34
Synchro Ring, Gear
lnspection .............. 13-35
Clutch Housing Bearing
Replacement ......... 13-36
Mainshaft Thrust Clearance
Adiustment ............ 13-38
Transmission
Reassembly ........... 13-tl1
Transmission Assembly
lnstallation ............. 13-46
Gearshift Mechanism
Overhaul ................ 13-50
Page 344 of 1413
Special Tools
Rsf. No. I Tool NumbrrD!3criptionOty I Prgc R.{.rcnc.
o
o
o
o
@
@
@
@
@
07GAJ - PG20110
07GAJ - PG20130.07736 - A010004
07746 - 0010300
07746 - 0010400
07746 - 0030r00
07746 - 0030300
07746 - 0030400
07745 - 0041100
07749 - 0010000
Mainshaft Holder
Mainshaft Bas€
Adjustable Bearing Puller, 25 - 40 mm
Attachment, 42 x 47 mm
Attachment, 52 x 55 mm
Oriver, 40 mm l.D.
Attachment, 30 mm l.D.
Attachment, 35 mm l.D,
Pilot, 28 mm
Driver
1
1
1
1
1
1
1
1
1
1
'13 - 40
13-40
13 - 36, 37
13-36
13 - 36, 37
13 - 27,33
13 - 27,33
13 - 27,33
13-36
13 - 36, 37
* Must be used with commerciallv available 3/ 8" - 16 Slide Hammer.
o@
@@@
o@@
ll
13-2