Page 641 of 947
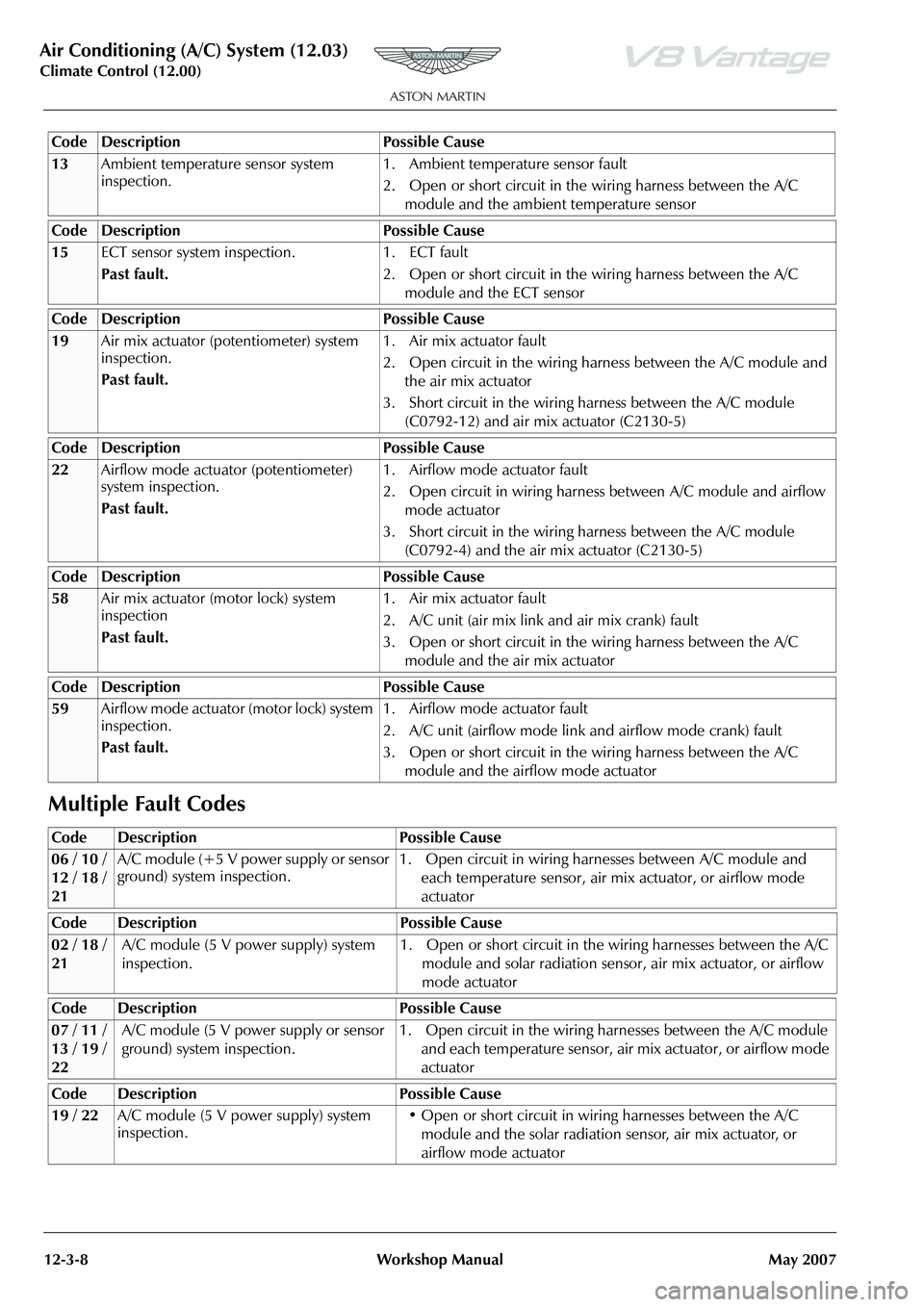
Air Conditioning (A/C) System (12.03)
Climate Control (12.00)
12-3-8 Workshop Manual May 2007
Multiple Fault Codes
Code Description Possible Cause
13 Ambient temperature sensor system
inspection. 1. Ambient temperature sensor fault
2. Open or short circuit in the wiring harness between the A/C
module and the ambient temperature sensor
Code Description Possible Cause
15 ECT sensor system inspection.
Past fault. 1. ECT fault
2. Open or short circuit in the wiring harness between the A/C
module and the ECT sensor
Code Description Possible Cause
19 Air mix actuator (potentiometer) system
inspection.
Past fault. 1. Air mix actuator fault
2. Open circuit in the wiring harness between the A/C module and
the air mix actuator
3. Short circuit in th e wiring harness between the A/C module
(C0792-12) and air mix actuator (C2130-5)
22 Airflow mode actuator (potentiometer)
system inspection.
Past fault. 1. Airflow mode actuator fault
2. Open circuit in wiring harnes
s between A/C module and airflow
mode actuator
3. Short circuit in th e wiring harness between the A/C module
(C0792-4) and the air mix actuator (C2130-5)
Code Description Possible Cause
58 Air mix actuator (motor lock) system
inspection
Past fault. 1. Air mix actuator fault
2. A/C unit (air mix link and air mix crank) fault
3. Open or short circuit in the wiring harness between the A/C
module and the air mix actuator
Code Description Possible Cause
59 Airflow mode actuator (motor lock) system
inspection.
Past fault. 1. Airflow mode actuator fault
2. A/C unit (airflow mode link and airflow mode crank) fault
3. Open or short circuit in the wiring harness between the A/C
module and the airflow mode actuator
Code Description Possible Cause
06 / 10 /
12 / 18 /
21 A/C module (+5 V power supply or sensor
ground) system inspection.
1. Open circuit in wiring harnesses between A/C module and
each temperature sensor, air mix actuator, or airflow mode
actuator
Code Description Possible Cause
02 / 18 /
21 A/C module (5 V power supply) system
inspection. 1. Open or short circuit in the wiring harnesses between the A/C
module and solar radiation sensor, air mix actuator, or airflow
mode actuator
Code Description Possible Cause
07 / 11 /
13 / 19 /
22 A/C module (5 V power supply or sensor
ground) system inspection.
1. Open circuit in the wiring harnesses between the A/C module
and each temperature sensor, air mix actuator, or airflow mode
actuator
Code Description Possible Cause
19 / 22 A/C module (5 V power supply) system
inspection. • Open or short circuit in wiri
ng harnesses between the A/C
module and the solar radiation sensor, air mix actuator, or
airflow mode actuator
Page 642 of 947
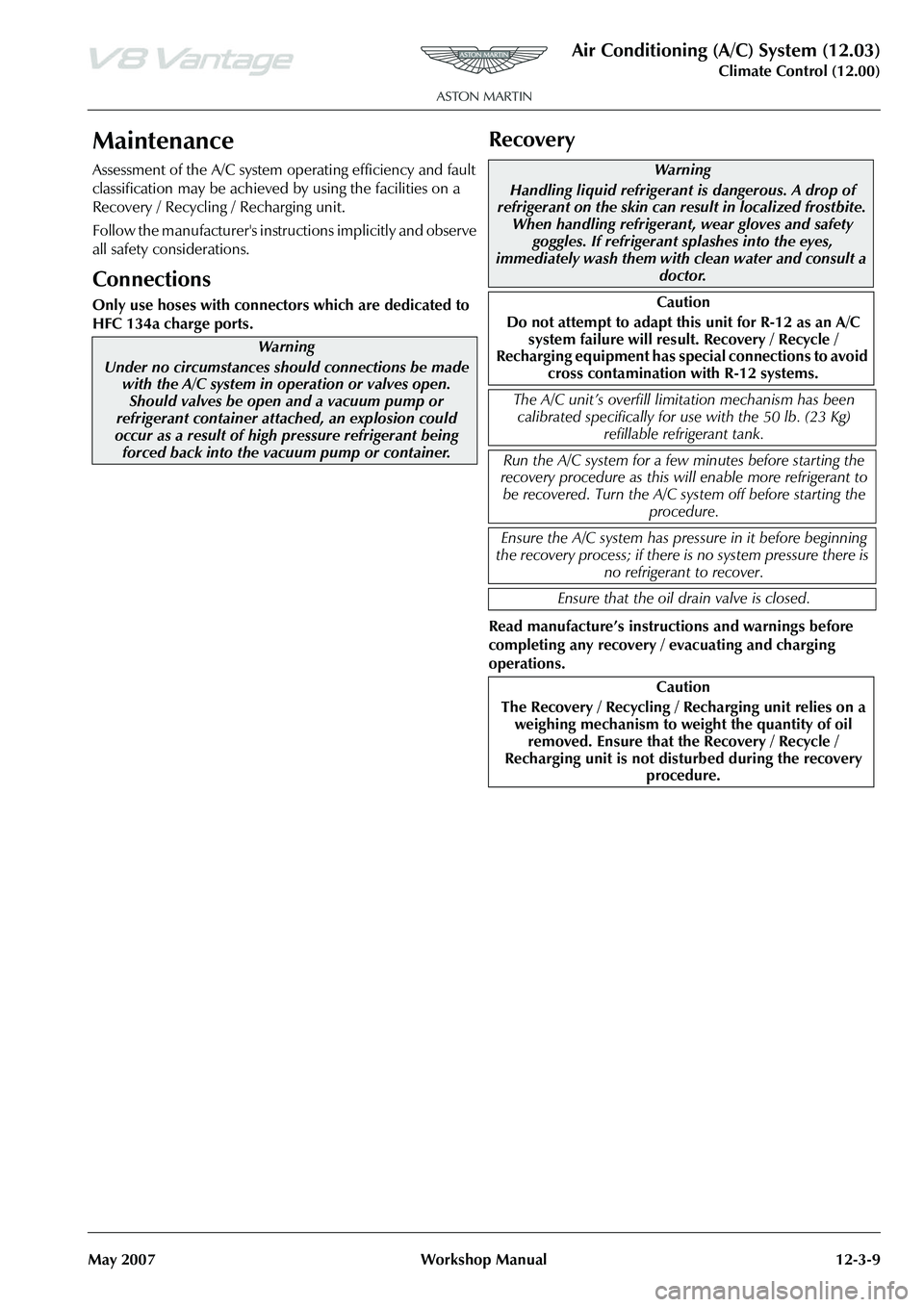
Air Conditioning (A/C) System (12.03)
Climate Control (12.00)
May 2007 Workshop Manual 12-3-9
Maintenance
Assessment of the A/C system operating efficiency and fault
classification may be achieved by using the facilities on a
Recovery / Recycling / Recharging unit.
Follow the manufacturer's instructions implicitly and observe
all safety considerations.
Connections
Only use hoses with connectors which are dedicated to
HFC 134a charge ports.
Recovery
Read manufacture’s instructions and warnings before
completing any recovery / evacuating and charging
operations.
Warning
Under no circumstances should connections be made with the A/C system in operation or valves open. Should valves be open and a vacuum pump or
refrigerant container attached, an explosion could
occur as a result of high pressure refrigerant being forced back into the vacuum pump or container.
Warning
Handling liquid refrigerant is dangerous. A drop of
refrigerant on the skin can result in localized frostbite. When handling refrigerant, wear gloves and safety
goggles. If refrigerant sp lashes into the eyes,
immediately wash them with clean water and consult a doctor.
Caution
Do not attempt to adapt this unit for R-12 as an A/C
system failure will result. Recovery / Recycle /
Recharging equipment has sp ecial connections to avoid
cross contamination wi th R-12 systems.
The A/C unit’s overfill li mitation mechanism has been
calibrated specifically for use with the 50 lb. (23 Kg)
refillable refrigerant tank.
Run the A/C system for a few minutes before starting the
recovery procedure as this wil l enable more refrigerant to
be recovered. Turn the A/C system off before starting the
procedure.
Ensure the A/C system has pre ssure in it before beginning
the recovery process; if there is no system pressure there is
no refrigerant to recover.
Ensure that the oil drain valve is closed.
Caution
The Recovery / Recycling / Re charging unit relies on a
weighing mechanism to weight the quantity of oil
removed. Ensure that the Recovery / Recycle /
Recharging unit is not disturbed during the recovery procedure.
Page 643 of 947
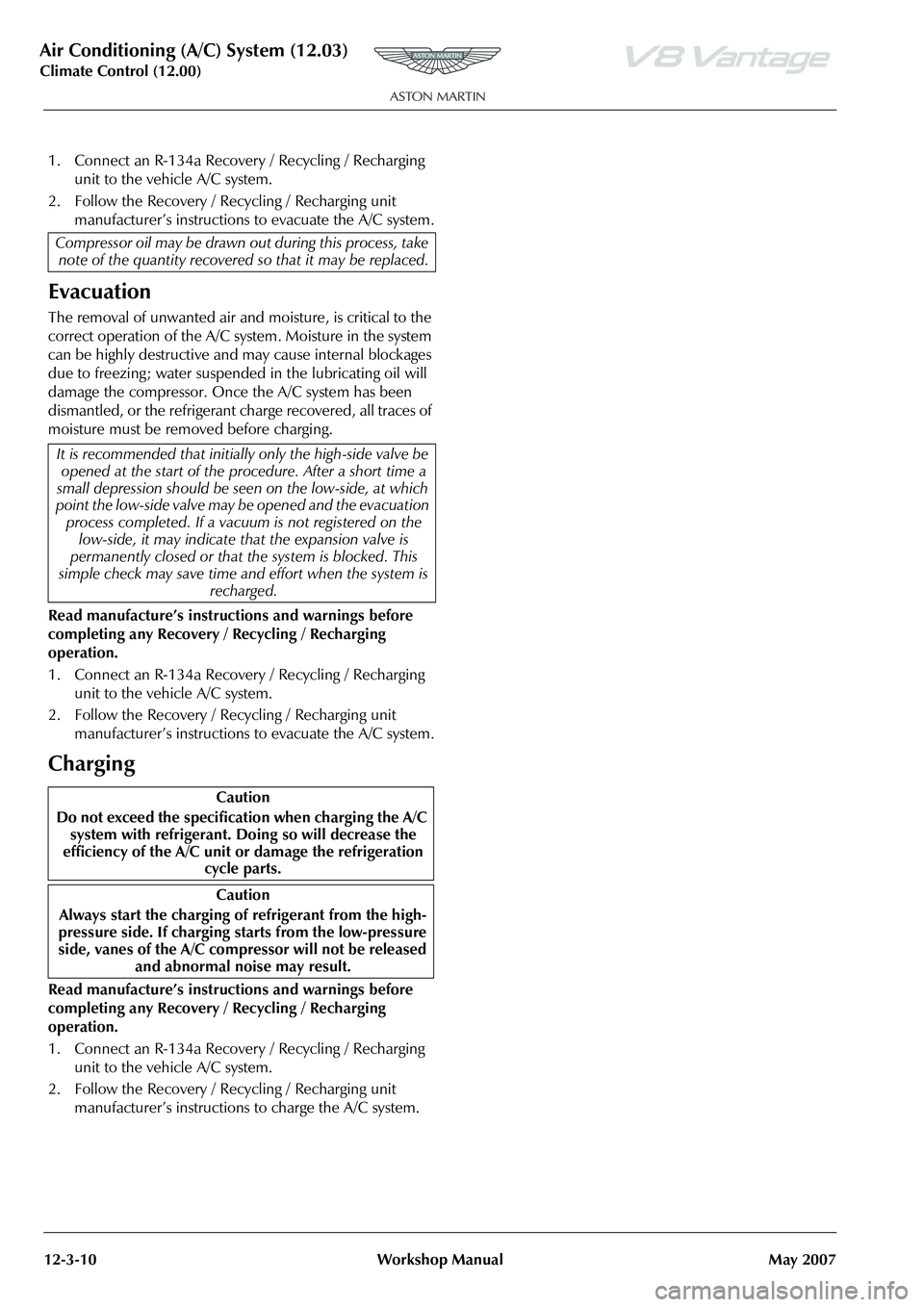
Air Conditioning (A/C) System (12.03)
Climate Control (12.00)
12-3-10 Workshop Manual May 2007
1. Connect an R-134a Recovery / Recycling / Recharging
unit to the vehicle A/C system.
2. Follow the Recovery / Recycling / Recharging unit manufacturer’s instructions to evacuate the A/C system.
Evacuation
The removal of unwanted air and moisture, is critical to the
correct operation of the A/C system. Moisture in the system
can be highly destructive and may cause internal blockages
due to freezing; water suspended in the lubricating oil will
damage the compressor. Once the A/C system has been
dismantled, or the refrigerant charge recovered, all traces of
moisture must be removed before charging.
Read manufacture’s instruct ions and warnings before
completing any Recovery / Recycling / Recharging
operation.
1. Connect an R-134a Recovery / Recycling / Recharging unit to the vehicle A/C system.
2. Follow the Recovery / Recycling / Recharging unit manufacturer’s instructions to evacuate the A/C system.
Charging
Read manufacture’s instruct ions and warnings before
completing any Recovery / Recycling / Recharging
operation.
1. Connect an R-134a Recovery / Recycling / Recharging unit to the vehicle A/C system.
2. Follow the Recovery / Recycling / Recharging unit manufacturer’s instructions to charge the A/C system.
Compressor oil may be drawn ou
t during this process, take
note of the quantity recovered so that it may be replaced.
It is recommended that initiall y only the high-side valve be
opened at the start of the pr ocedure. After a short time a
small depression should be seen on the low-side, at which
point the low-side valve may be opened and the evacuation
process completed. If a vacuum is not registered on the
low-side, it may indicate that the expansion valve is
permanently closed or that th e system is blocked. This
simple check may save time and effort when the system is
recharged.
Caution
Do not exceed the specificat ion when charging the A/C
system with refrigerant. Doing so will decrease the
efficiency of the A/C unit or damage the refrigeration cycle parts.
Caution
Always start the charging of refrigerant from the high-
pressure side. If charging st arts from the low-pressure
side, vanes of the A/C compressor will not be released and abnormal noise may result.
Page 644 of 947
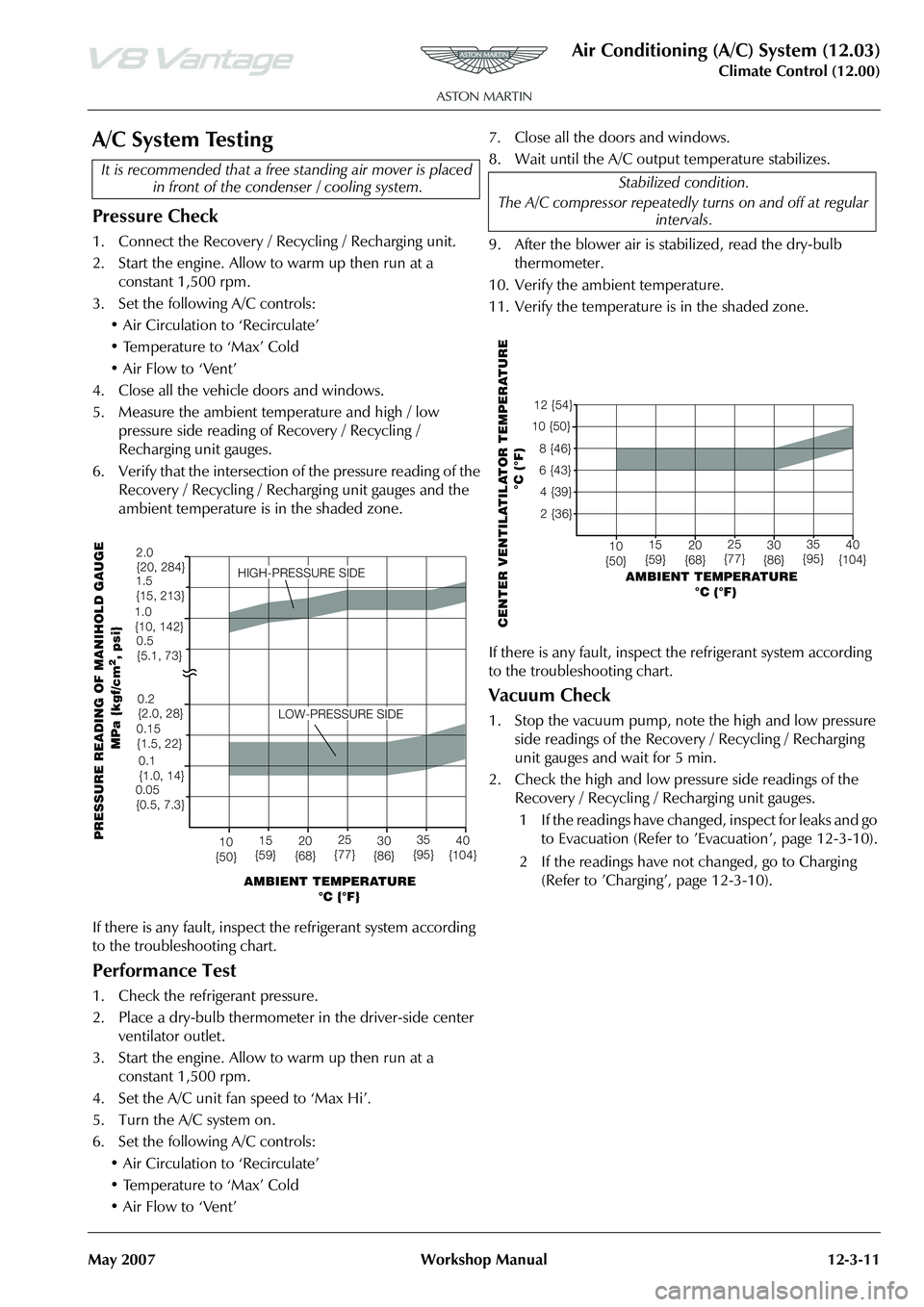
Air Conditioning (A/C) System (12.03)
Climate Control (12.00)
May 2007 Workshop Manual 12-3-11
A/C System Testing
Pressure Check
1. Connect the Recovery / Recycling / Recharging unit.
2. Start the engine. Allow to warm up then run at a constant 1,500 rpm.
3. Set the following A/C controls:
• Air Circulation to ‘Recirculate’
• Temperature to ‘Max’ Cold
• Air Flow to ‘Vent’
4. Close all the vehicle doors and windows.
5. Measure the ambient temperature and high / low pressure side reading of Recovery / Recycling /
Recharging unit gauges.
6. Verify that the intersection of the pressure reading of the Recovery / Recycling / Recharging unit gauges and the
ambient temperature is in the shaded zone.
If there is any fault, inspect the refrigerant system according
to the troubleshooting chart.
Performance Test
1. Check the refrigerant pressure.
2. Place a dry-bulb thermometer in the driver-side center ventilator outlet.
3. Start the engine. Allow to warm up then run at a constant 1,500 rpm.
4. Set the A/C unit fan speed to ‘Max Hi’.
5. Turn the A/C system on.
6. Set the following A/C controls: • Air Circulation to ‘Recirculate’
• Temperature to ‘Max’ Cold
• Air Flow to ‘Vent’ 7. Close all the doors and windows.
8. Wait until the A/C output temperature stabilizes.
9. After the blower air is stabilized, read the dry-bulb
thermometer.
10. Verify the ambient temperature.
11. Verify the temperature is in the shaded zone.
If there is any fault, inspect the refrigerant system according
to the troubleshooting chart.
Vacuum Check
1. Stop the vacuum pump, note the high and low pressure side readings of the Recovery / Recycling / Recharging
unit gauges and wait for 5 min.
2. Check the high and low pressure side readings of the Recovery / Recycling / Recharging unit gauges.
1 If the readings have changed, inspect for leaks and go to Evacuation (Refer to ’E vacuation’, page 12-3-10).
2 If the readings have not changed, go to Charging (Refer to ’Charging’, page 12-3-10).
It is recommended th
at a free standing air mover is placed
in front of the conden ser / cooling system.
AMBIENT TEMPERATURE
°C {°F}
10
{50} 15
{59} 20
{68} 25
{77} 30
{86} 35
{95} 40
{104}
LOW-PRESSURE SIDE
HIGH-PRESSURE SIDE
PRESSURE READING OF MANIHOLD GAUGE
MPa {kgf/cm
2, psi}
2.0
{20, 284}
1.5
{15, 213}
1.0
{10, 142}
0.2
{2.0, 28}0.1
{1.0, 14}
0.15
{1.5, 22}
0.05
{0.5, 7.3} 0.5
{5.1, 73}
Stabilized condition.
The A/C compressor repeatedly turns on and off at regular intervals.
AMBIENT TEMPERATURE
°C (°F)
CENTER VENTILATILATOR TEMPERATURE
°C (°F)
12 {54}
10 {50}
8 {46}
6 {43}4 {39} 2 {36}
10
{50} 15
{59} 20
{68} 25
{77} 30
{86} 35
{95} 40
{104}
Page 645 of 947
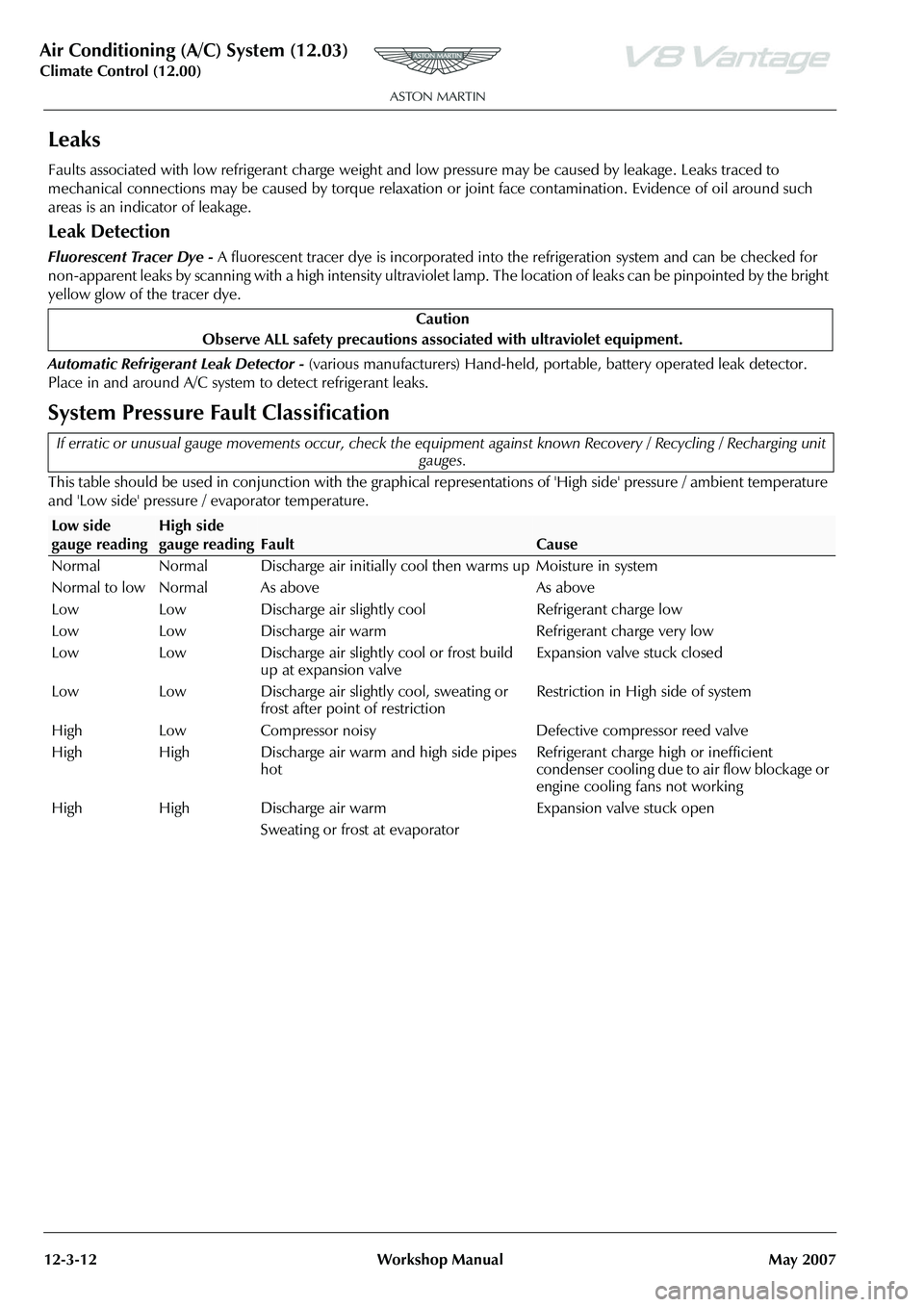
Air Conditioning (A/C) System (12.03)
Climate Control (12.00)
12-3-12 Workshop Manual May 2007
Leaks
Faults associated with low refrigerant charge weight and low pressure may be caused by leakage. Leaks traced to
mechanical connections may be caused by torque relaxation or joint face contamination. Evidence of oil around such
areas is an indicator of leakage.
Leak Detection
Fluorescent Tracer Dye - A fluorescent tracer dye is incorporated into th e refrigeration system and can be checked for
non-apparent leaks by scanning with a high intensity ultraviolet lamp. The location of leaks can be pinpointed by the bright
yellow glow of the tracer dye.
Automatic Refrigerant Leak Detector - (various manufacturers) Hand-held, portable, battery operated leak detector.
Place in and around A/C system to detect refrigerant leaks.
System Pressure Fault Classification
This table should be used in conjunction with the graphical representations of 'High side' pressure / ambient temperature
and 'Low side' pressure / evaporator temperature. Caution
Observe ALL safety precautions associ ated with ultraviolet equipment.
If erratic or unusual gauge movements occur, check the equipment against known Recovery / Recycling / Recharging unit
gauges.
Low side
gauge readingHigh side
gauge reading
Fault
Cause
Normal Normal Discharge air initially c ool then warms up Moisture in system
Normal to low Normal As above As above
Low Low Discharge air slightly cool Refrigerant charge low
Low Low Discharge air warm Refrigerant charge very low
Low Low Discharge air slightly cool or frost build up at expansion valve Expansion valve stuck closed
Low Low Discharge air slightly cool, sweating or frost after point of restriction Restriction in High side of system
High Low Compressor noisy Defective compressor reed valve
High High Discharge air warm and high side pipes hot Refrigerant charge high or inefficient
condenser cooling due to air flow blockage or
engine cooling fans not working
High High Discharge air warm
Sweating or frost at evaporator Expansion valve stuck open
Page 646 of 947
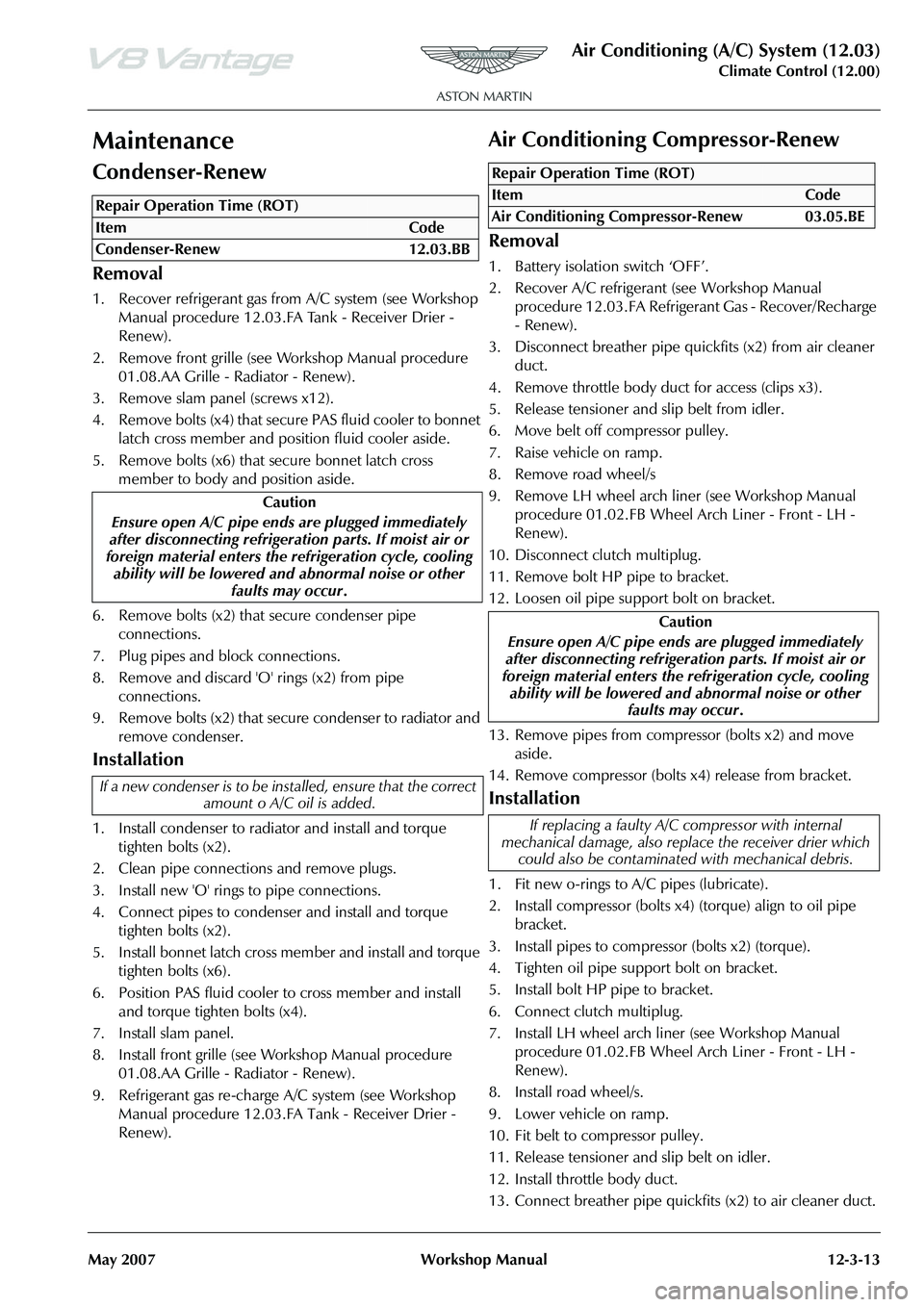
Air Conditioning (A/C) System (12.03)
Climate Control (12.00)
May 2007 Workshop Manual 12-3-13
Maintenance
Condenser-Renew
Removal
1. Recover refrigerant gas from A/C system (see Workshop Manual procedure 12.03.FA Tank - Receiver Drier -
Renew).
2. Remove front grille (see Workshop Manual procedure 01.08.AA Grille - Radiator - Renew).
3. Remove slam panel (screws x12).
4. Remove bolts (x4) that secure PAS fluid cooler to bonnet latch cross member and posi tion fluid cooler aside.
5. Remove bolts (x6) that secure bonnet latch cross member to body and position aside.
6. Remove bolts (x2) that secure condenser pipe connections.
7. Plug pipes and block connections.
8. Remove and discard 'O' rings (x2) from pipe connections.
9. Remove bolts (x2) that secure condenser to radiator and remove condenser.
Installation
1. Install condenser to radiator and install and torque tighten bolts (x2).
2. Clean pipe connections and remove plugs.
3. Install new 'O' rings to pipe connections.
4. Connect pipes to condenser and install and torque tighten bolts (x2).
5. Install bonnet latch cross member and install and torque tighten bolts (x6).
6. Position PAS fluid cooler to cross member and install
and torque tighten bolts (x4).
7. Install slam panel.
8. Install front grille (see Workshop Manual procedure 01.08.AA Grille - Radiator - Renew).
9. Refrigerant gas re-charge A/C system (see Workshop Manual procedure 12.03.FA Tank - Receiver Drier -
Renew).
Air Conditioning Compressor-Renew
Removal
1. Battery isolation switch ‘OFF’.
2. Recover A/C refrigerant (see Workshop Manual procedure 12.03.FA Refriger ant Gas - Recover/Recharge
- Renew).
3. Disconnect breather pipe qu ickfits (x2) from air cleaner
duct.
4. Remove throttle body duct for access (clips x3).
5. Release tensioner and slip belt from idler.
6. Move belt off compressor pulley.
7. Raise vehicle on ramp.
8. Remove road wheel/s
9. Remove LH wheel arch li ner (see Workshop Manual
procedure 01.02.FB Wheel Arch Liner - Front - LH -
Renew).
10. Disconnect clutch multiplug.
11. Remove bolt HP pipe to bracket.
12. Loosen oil pipe support bolt on bracket.
13. Remove pipes from compressor (bolts x2) and move aside.
14. Remove compressor (bolts x4) release from bracket.
Installation
1. Fit new o-rings to A/C pipes (lubricate).
2. Install compressor (bolts x4) (torque) align to oil pipe bracket.
3. Install pipes to compress or (bolts x2) (torque).
4. Tighten oil pipe support bolt on bracket.
5. Install bolt HP pipe to bracket.
6. Connect clutch multiplug.
7. Install LH wheel arch liner (see Workshop Manual procedure 01.02.FB Wheel Arch Liner - Front - LH -
Renew).
8. Install road wheel/s.
9. Lower vehicle on ramp.
10. Fit belt to compressor pulley.
11. Release tensioner an d slip belt on idler.
12. Install throttle body duct.
13. Connect breather pipe quickf its (x2) to air cleaner duct.
Repair Operation Time (ROT)
Repair Operation Time (ROT)
Page 647 of 947
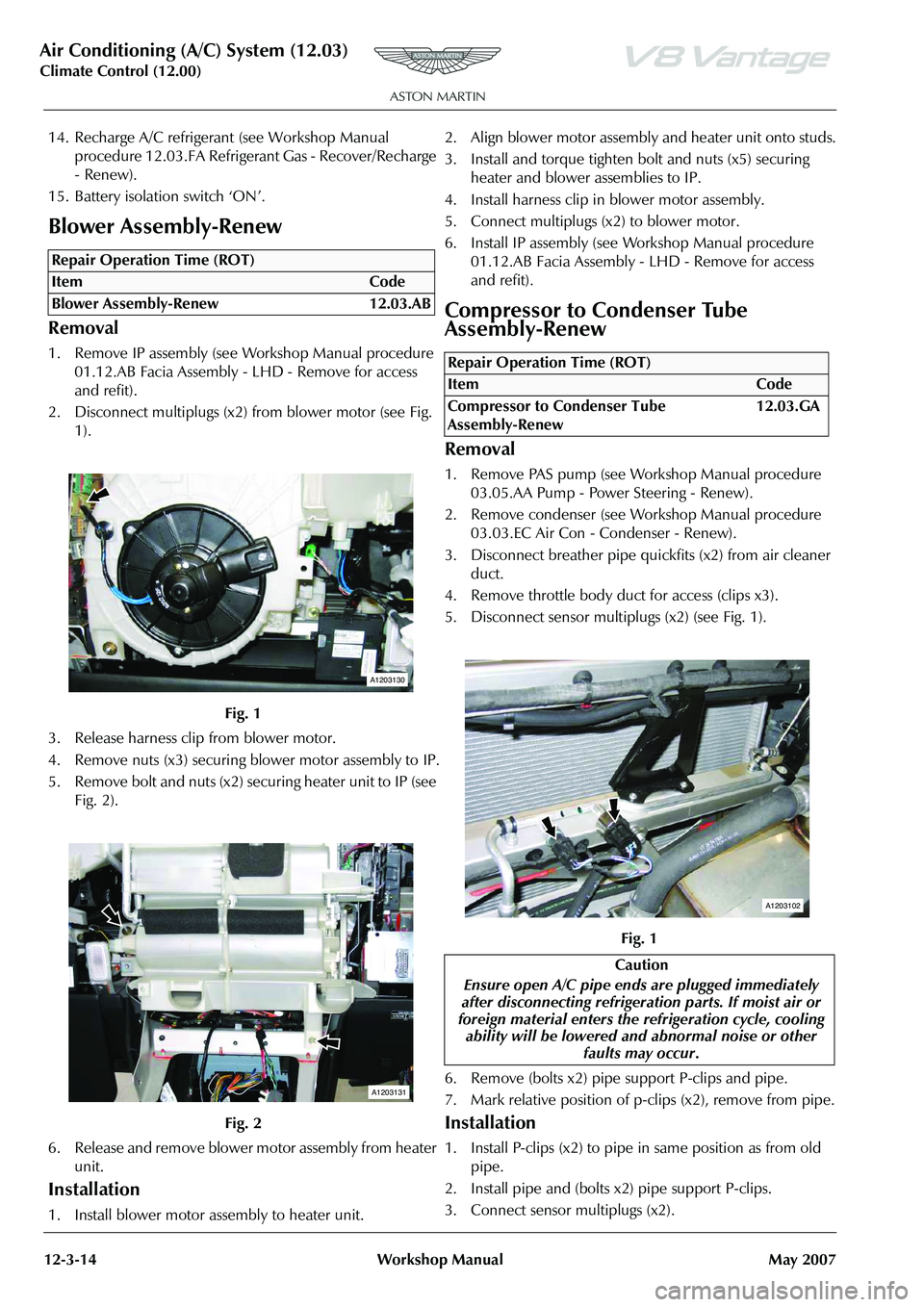
Air Conditioning (A/C) System (12.03)
Climate Control (12.00)
12-3-14 Workshop Manual May 2007
14. Recharge A/C refrigerant (see Workshop Manual
procedure 12.03.FA Refriger ant Gas - Recover/Recharge
- Renew).
15. Battery isolation switch ‘ON’.
Blower Assembly-Renew
Removal
1. Remove IP assembly (see Workshop Manual procedure 01.12.AB Facia Assembly - LHD - Remove for access
and refit).
2. Disconnect multiplugs (x2) from blower motor (see Fig. 1).
3. Release harness clip from blower motor.
4. Remove nuts (x3) securing blower motor assembly to IP.
5 . Remove bolt and nut s (x 2) s ecurin g hea ter u nit to IP (se e Fig. 2).
6. Release and remove blower motor assembly from heater unit.
Installation
1. Install blower motor assembly to heater unit. 2. Align blower motor assembly and heater unit onto studs.
3. Install and torque tighten bolt and nuts (x5) securing
heater and blower assemblies to IP.
4. Install harness clip in blower motor assembly.
5. Connect multiplugs (x2) to blower motor.
6. Install IP assembly (see Workshop Manual procedure
01.12.AB Facia Assembly - LHD - Remove for access
and refit).
Compressor to Condenser Tube
Assembly-Renew
Removal
1. Remove PAS pump (see Workshop Manual procedure 03.05.AA Pump - Power Steering - Renew).
2. Remove condenser (see Workshop Manual procedure 03.03.EC Air Con - Condenser - Renew).
3. Disconnect breather pipe qu ickfits (x2) from air cleaner
duct.
4. Remove throttle body duct for access (clips x3).
5. Disconnect sensor multip lugs (x2) (see Fig. 1).
6. Remove (bolts x2) pipe support P-clips and pipe.
7. Mark relative position of p-clips (x2), remove from pipe.
Installation
1. Install P-clips (x2) to pipe in same position as from old pipe.
2. Install pipe and (bolts x2) pipe support P-clips.
3. Connect sensor multiplugs (x2).
Repair Operation Time (ROT)
$
$
Repair Operation Time (ROT)
ItemCode
Compressor to Condenser Tube
Assembly-Renew 12.03.GA
Fig. 1
Caution
Ensure open A/C pipe ends are plugged immediately
after disconnecting refrigerat ion parts. If moist air or
foreign material enters the refrigeration cycle, cooling ability will be lowered and abnormal noise or other
faults may occur.
$
Page 648 of 947
Air Conditioning (A/C) System (12.03)
Climate Control (12.00)
May 2007 Workshop Manual 12-3-15
4. Install throttle body duct.
5. Connect breather pipe quickf its (x2) to air cleaner duct.
6. Install condenser (see Workshop Manual procedure 03.03.EC Air Con - Condenser - Renew).
7. Install PAS pump (see Workshop Manual procedure 03.05.AA Pump - Powe r Steering - Renew).