Page 873 of 947
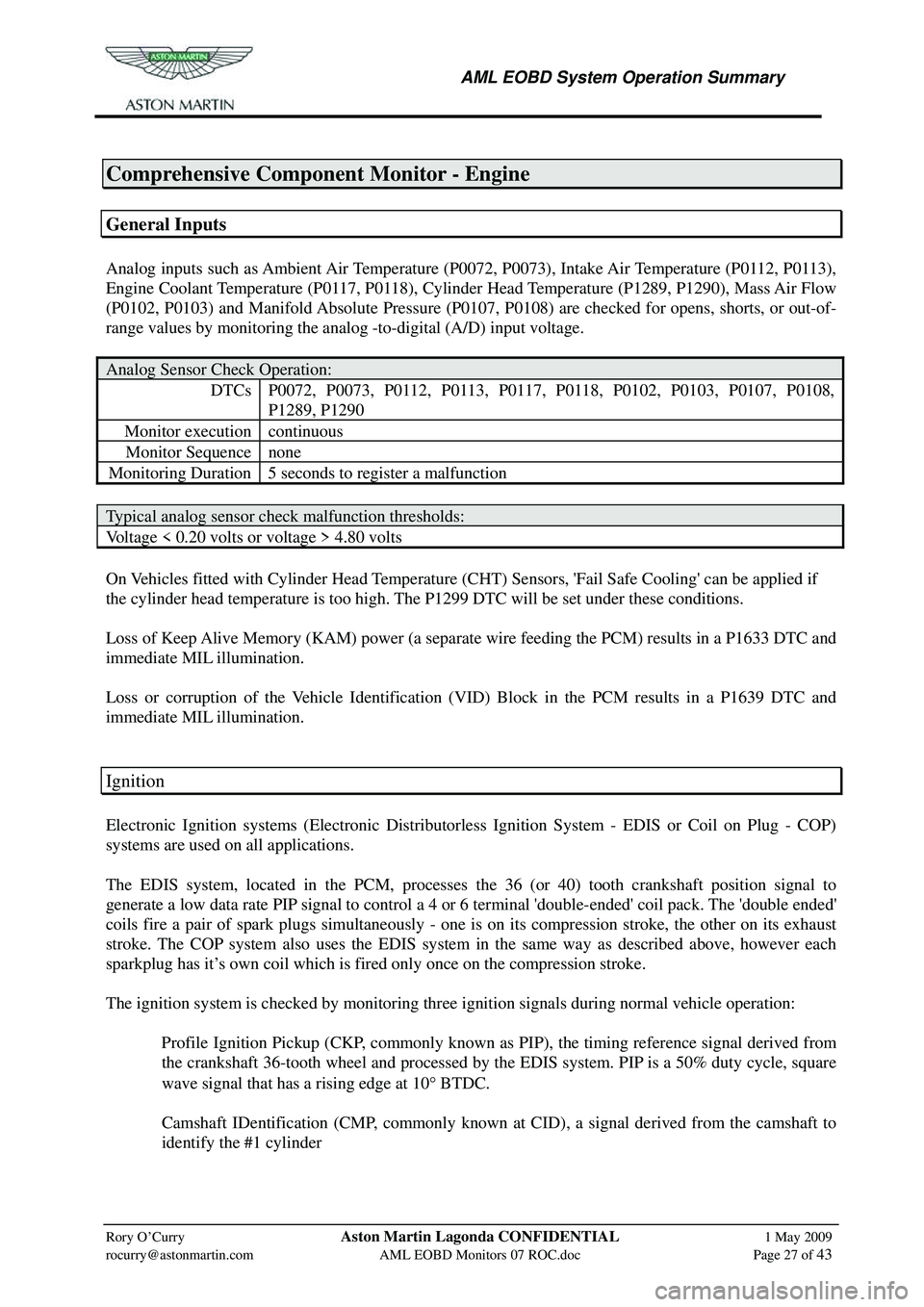
AML EOBD System Operation Summary
Rory O’Curry Aston Martin Lagonda CONFIDENTIAL 1 May 2009
[email protected] AML EOBD Monitors 07 ROC.doc Page 27 of 43
Comprehensive Component Monitor - Engine
General Inputs
Analog inputs such as Ambient Air Temperature (P0072, P0073), Intake Air Temperature (P0112, P0113),
Engine Coolant Temperature (P0117, P0118), Cylinder Head Temperature (P1289, P1290), Mass Air Flow
(P0102, P0103) and Manifold Absolute Pressure (P0107, P0108) are checked for opens, shorts, or out-of-
range values by monitoring the analog -to-digital (A/D) input voltage.
Analog Sensor Check Operation:
DTCs P0072, P0073, P0112, P0113, P0117, P0118, P0102, P0103, P0107, P0108,
P1289, P1290
Monitor execution continuous
Monitor Sequence none
Monitoring Duration 5 seconds to register a malfunction
Typical analog sensor check malfunction thresholds:
Voltage < 0.20 volts or voltage > 4.80 volts
On Vehicles fitted with Cylinder Head Temperature (CHT ) Sensors, 'Fail Safe Cooling' can be applied if
the cylinder head temperature is too high. The P1299 DTC will be set under these conditions.
Loss of Keep Alive Memory (KAM) power (a separate wire feeding the PCM) results in a P1633 DTC and
immediate MIL illumination.
Loss or corruption of the Vehicle Identification (VID) Block in the PCM results in a P1639 DTC and
immediate MIL illumination.
Ignition
Electronic Ignition systems (Electronic Distributorless Ignition System - EDIS or Coil on Plug - COP)
systems are used on all applications.
The EDIS system, located in the PCM, processes the 36 (or 40) tooth crankshaft position signal to
generate a low data rate PIP signal to control a 4 or 6 terminal 'double-ended' coil pack. The 'double ended'
coils fire a pair of spark plugs simultaneously - one is on its compression stroke, the other on its exhaust
stroke. The COP system also uses the EDIS system in the same way as described above, however each
sparkplug has it’s own coil which is fired only once on the compression stroke.
The ignition system is checked by monitoring three ignition signals during normal vehicle operation:
Profile Ignition Pickup (CKP, commonly known as PIP), the timing reference signal derived from the crankshaft 36-tooth wheel and processed by the EDIS system. PIP is a 50% duty cycle, square
wave signal that has a rising edge at 10 ° BTDC.
Camshaft IDentification (CMP, commonly known at CID), a signal derived from the camshaft to identify the #1 cylinder
Page 874 of 947
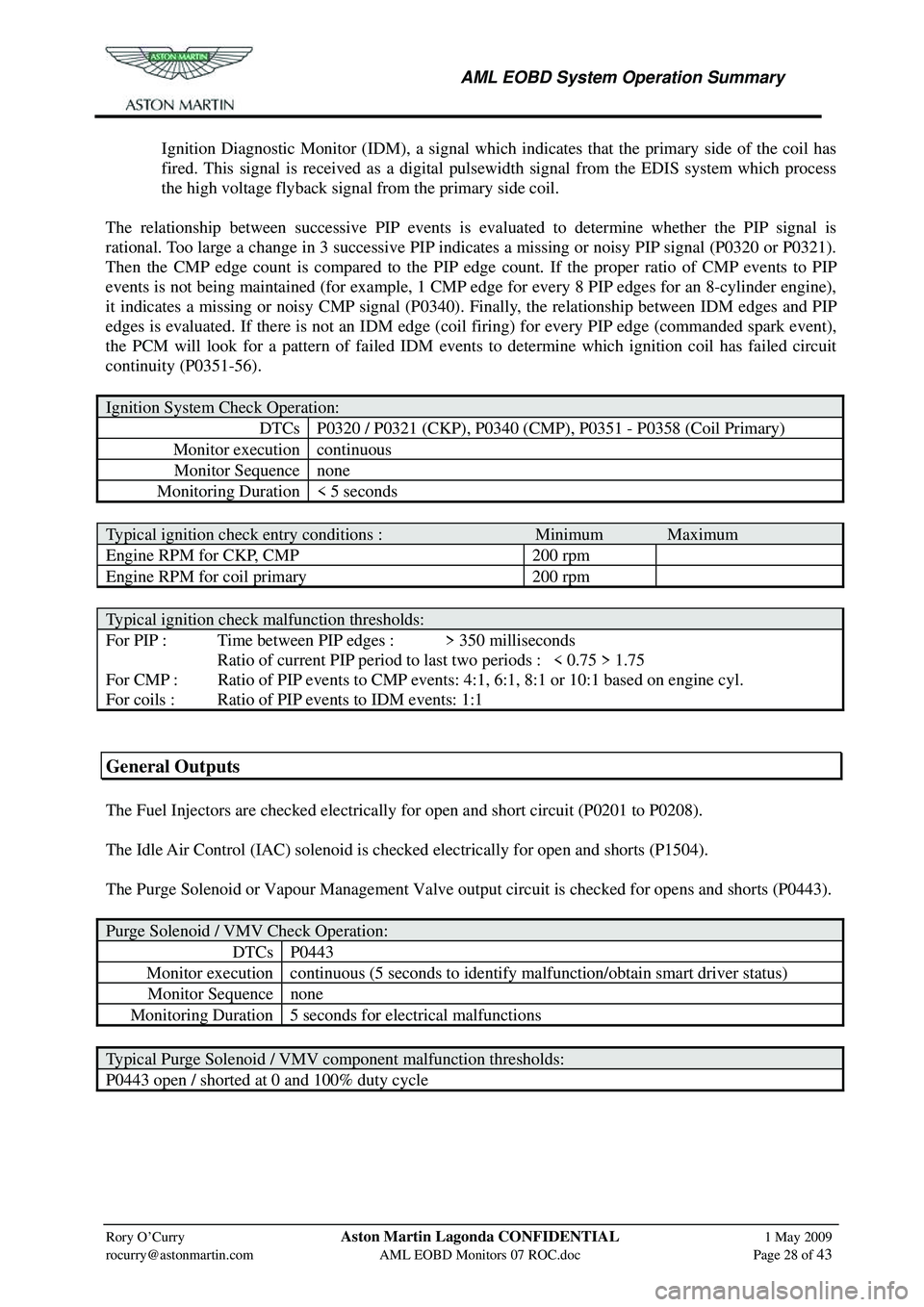
AML EOBD System Operation Summary
Rory O’Curry Aston Martin Lagonda CONFIDENTIAL 1 May 2009
[email protected] AML EOBD Monitors 07 ROC.doc Page 28 of 43
Ignition Diagnostic Monitor (IDM), a signal which indicates that the primary side of the coil has
fired. This signal is received as a digital pulsewidth signal from the EDIS system which process
the high voltage flyback signal from the primary side coil.
The relationship between successive PIP events is ev aluated to determine whether the PIP signal is
rational. Too large a change in 3 successive PIP indicates a missing or noisy PIP signal (P0320 or P0321).
Then the CMP edge count is compared to the PIP e dge count. If the proper ratio of CMP events to PIP
events is not being maintained (for example, 1 CMP e dge for every 8 PIP edges for an 8-cylinder engine),
it indicates a missing or noisy CMP signal (P0340). Finally, the relationship between IDM edges and PIP
edges is evaluated. If there is not an IDM edge (co il firing) for every PIP edge (commanded spark event),
the PCM will look for a pattern of failed IDM events to determine which ignition coil has failed circuit
continuity (P0351-56).
Ignition System Check Operation:
DTCs P0320 / P0321 (CKP), P0340 (CMP), P0351 - P0358 (Coil Primary)
Monitor execution continuous
Monitor Sequence none
Monitoring Duration < 5 seconds
Typical ignition check entry conditions : Minimum Maximum
Engine RPM for CKP, CMP 200 rpm
Engine RPM for coil primary 200 rpm
Typical ignition check malfunction thresholds:
For PIP : Time between PIP edges : > 350 milliseconds
Ratio of current PIP period to last two periods : < 0.75 > 1.75
For CMP : Ratio of PIP events to CMP events: 4:1, 6:1, 8:1 or 10:1 based on engine cyl.
For coils : Ratio of PIP events to IDM events: 1:1
General Outputs
The Fuel Injectors are checked electrically for open and short circuit (P0201 to P0208).
The Idle Air Control (IAC) solenoid is checked electrically for open and shorts (P1504).
The Purge Solenoid or Vapour Management Valve output circuit is checked for opens and shorts (P0443).
Purge Solenoid / VMV Check Operation:
DTCsP0443
Monitor execution continuous (5 seconds to identify malfunction/obtain smart driver status)
Monitor Sequencenone
Monitoring Duration 5 seconds for electrical malfunctions
Typical Purge Solenoid / VMV component malfunction thresholds:
P0443 open / shorted at 0 and 100% duty cycle
Page 875 of 947
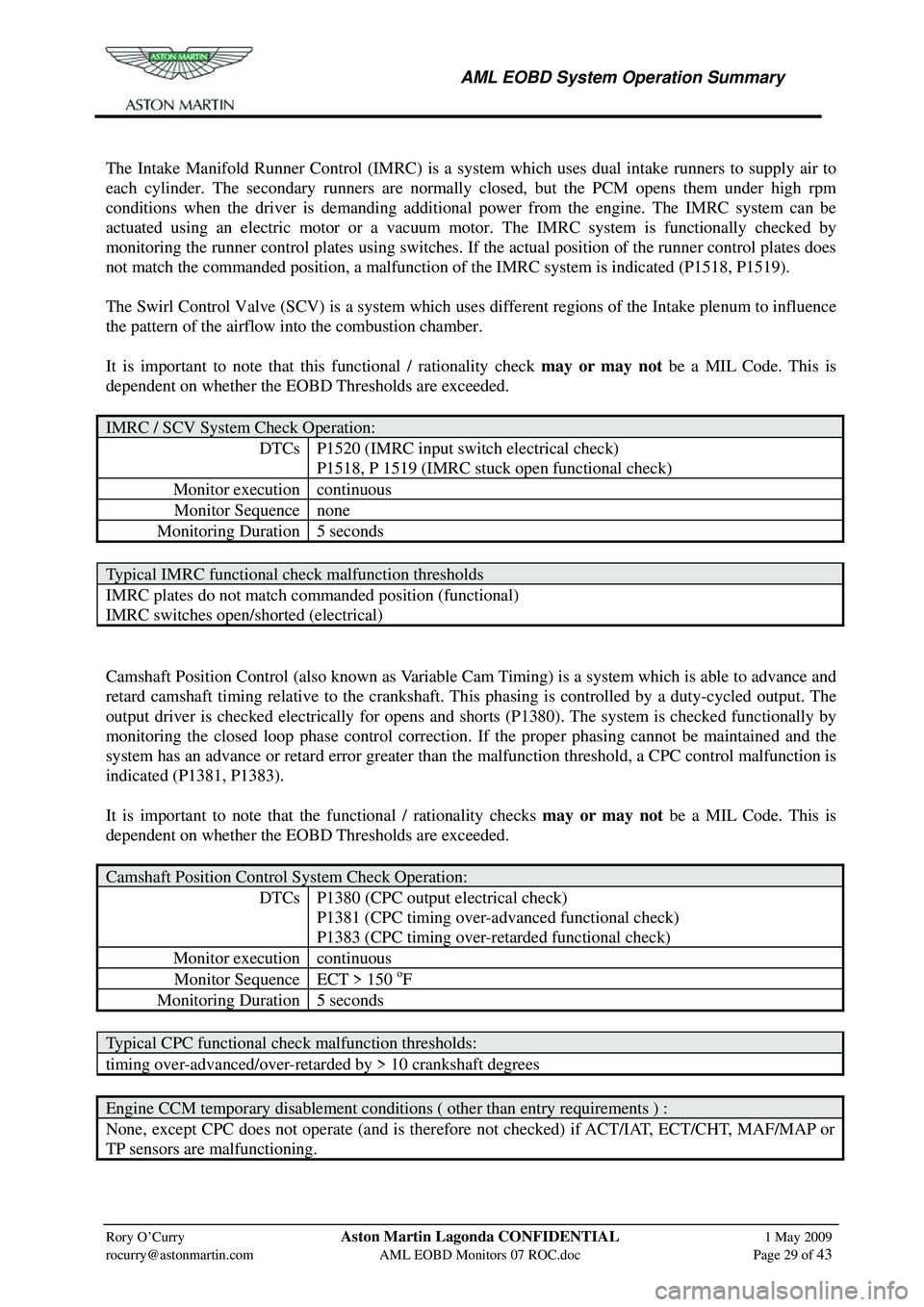
AML EOBD System Operation Summary
Rory O’Curry Aston Martin Lagonda CONFIDENTIAL 1 May 2009
[email protected] AML EOBD Monitors 07 ROC.doc Page 29 of 43
The Intake Manifold Runner Control (IMRC) is a syst em which uses dual intake runners to supply air to
each cylinder. The secondary runners are normally closed, but the PCM opens them under high rpm
conditions when the driver is demanding additiona l power from the engine. The IMRC system can be
actuated using an electric motor or a vacuum moto r. The IMRC system is functionally checked by
monitoring the runner control plates using switches. If the actual position of the runner control plates does
not match the commanded position, a malfunction of the IMRC system is indicated (P1518, P1519).
The Swirl Control Valve (SCV) is a system which uses di fferent regions of the Intake plenum to influence
the pattern of the airflow into the combustion chamber.
It is important to note that this functional / rationality check may or may not be a MIL Code. This is
dependent on whether the EOBD Thresholds are exceeded.
IMRC / SCV System Check Operation:
DTCs P1520 (IMRC input switch electrical check)
P1518, P 1519 (IMRC stuck open functional check)
Monitor execution continuous
Monitor Sequence none
Monitoring Duration 5 seconds
Typical IMRC functional check malfunction thresholds
IMRC plates do not match commanded position (functional)
IMRC switches open/shorted (electrical)
Camshaft Position Control (also known as Variable Cam Ti ming) is a system which is able to advance and
retard camshaft timing relative to the crankshaft. Th is phasing is controlled by a duty-cycled output. The
output driver is checked electrically for opens and s horts (P1380). The system is checked functionally by
monitoring the closed loop phase control correction. If the proper phasing cannot be maintained and the
system has an advance or retard error greater than the malfunction threshold, a CPC control malfunction is
indicated (P1381, P1383).
It is important to note that the functional / rationality checks may or may not be a MIL Code. This is
dependent on whether the EOBD Thresholds are exceeded.
Camshaft Position Control System Check Operation:
DTCs P1380 (CPC output electrical check)
P1381 (CPC timing over-advanced functional check)
P1383 (CPC timing over-retarded functional check)
Monitor execution continuous
Monitor Sequence ECT > 150 oF
Monitoring Duration 5 seconds
Typical CPC functional check malfunction thresholds:
timing over-advanced/over-retard ed by > 10 crankshaft degrees
Engine CCM temporary disablement conditions ( other than entry requirements ) :
None, except CPC does not operate (and is therefore not checked) if ACT/IAT, ECT/CHT, MAF/MAP or
TP sensors are malfunctioning.
Page 876 of 947
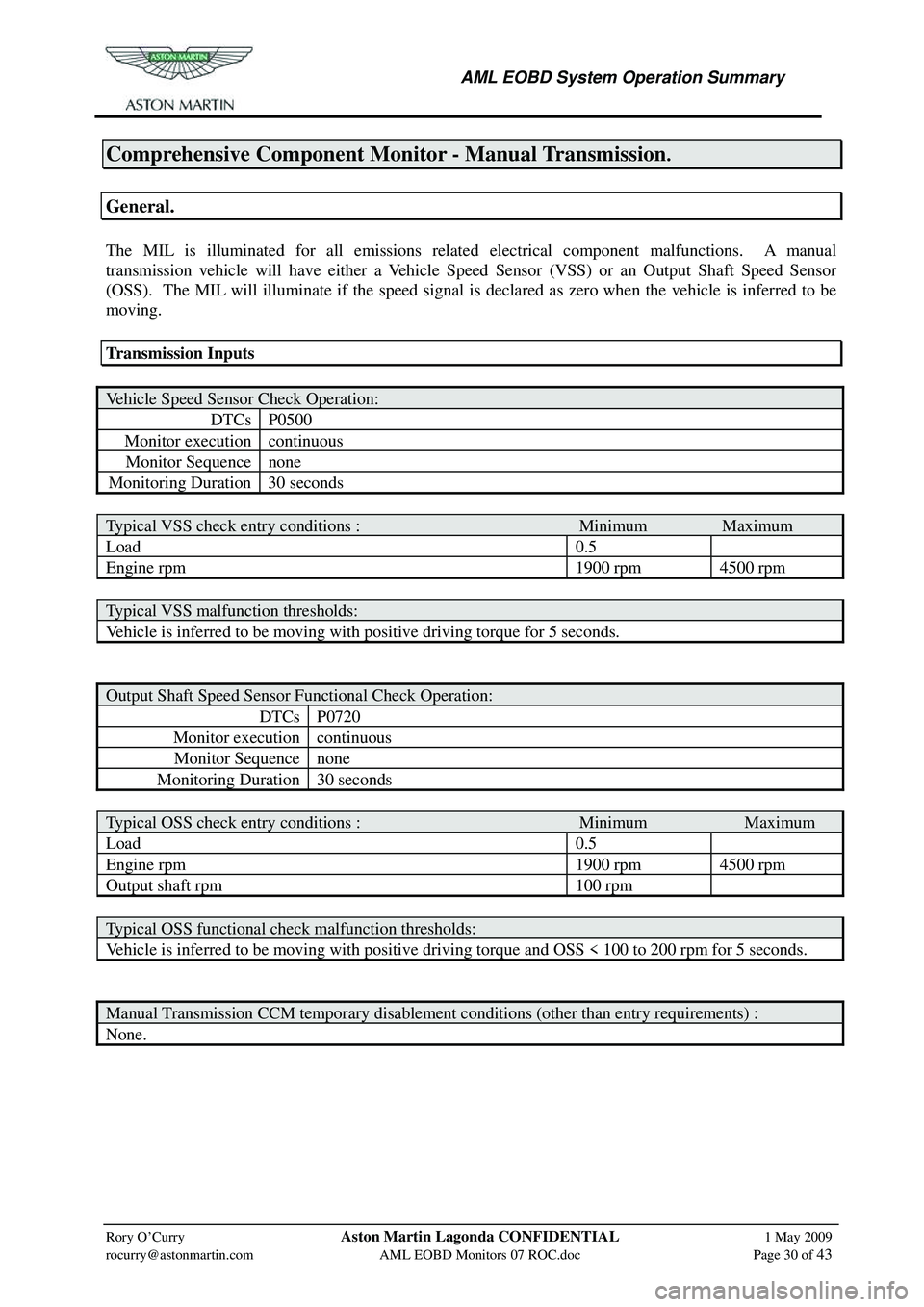
AML EOBD System Operation Summary
Rory O’Curry Aston Martin Lagonda CONFIDENTIAL 1 May 2009
[email protected] AML EOBD Monitors 07 ROC.doc Page 30 of 43
Comprehensive Component Monitor - Manual Transmission.
General.
The MIL is illuminated for all emissions relate d electrical component malfunctions. A manual
transmission vehicle will have either a Vehicle Speed Sensor (VSS) or an Output Shaft Speed Sensor
(OSS). The MIL will illuminate if the speed signal is declared as zero when the vehicle is inferred to be
moving.
Transmission Inputs
Vehicle Speed Sensor Check Operation:
DTCs P0500
Monitor execution continuous
Monitor Sequence none
Monitoring Duration 30 seconds
Typical VSS check entry conditions : Minimum Maximum
Load 0.5
Engine rpm 1900 rpm 4500 rpm
Typical VSS malfunction thresholds:
Vehicle is inferred to be moving with positive driving torque for 5 seconds.
Output Shaft Speed Sensor Functional Check Operation:
DTCs P0720
Monitor execution continuous
Monitor Sequence none
Monitoring Duration 30 seconds
Typical OSS check entry conditions : Minimum Maximum
Load 0.5
Engine rpm 1900 rpm 4500 rpm
Output shaft rpm 100 rpm
Typical OSS functional check malfunction thresholds:
Vehicle is inferred to be moving with positive driving torque and OSS < 100 to 200 rpm for 5 seconds.
Manual Transmission CCM temporary disablement conditions (other than entry requirements) :
None.
Page 877 of 947
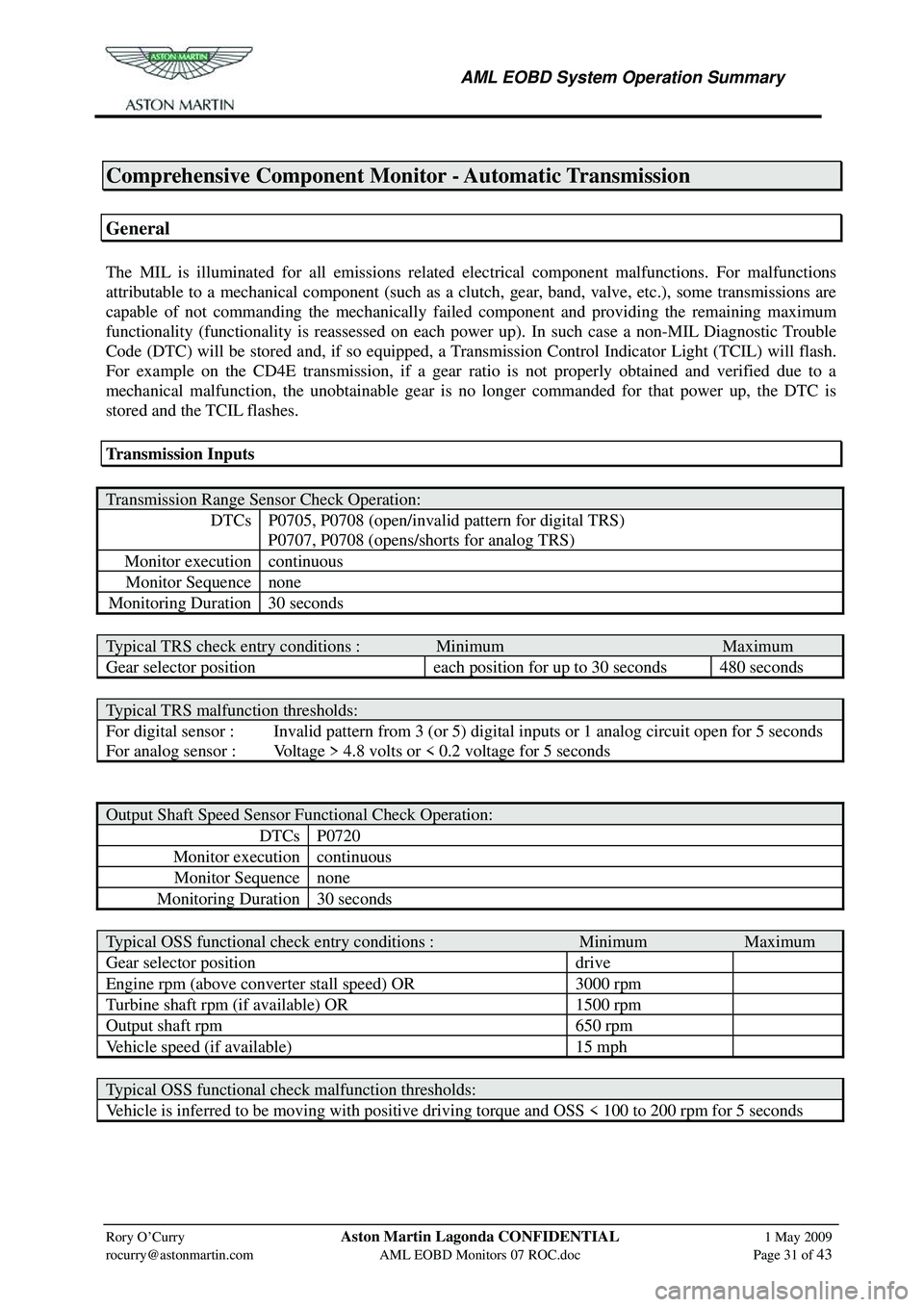
AML EOBD System Operation Summary
Rory O’Curry Aston Martin Lagonda CONFIDENTIAL 1 May 2009
[email protected] AML EOBD Monitors 07 ROC.doc Page 31 of 43
Comprehensive Component Monitor - Automatic Transmission
General
The MIL is illuminated for all emissions related electrical component malfunctions. For malfunctions
attributable to a mechanical component (such as a clutch, gear, band, valve, etc.), some transmissions are
capable of not commanding the mechanically faile d component and providing the remaining maximum
functionality (functionality is reassessed on each power up). In such case a non-MIL Diagnostic Trouble
Code (DTC) will be stored and, if so equipped, a Transmission Control Indicator Light (TCIL) will flash.
For example on the CD4E transmission, if a gear ratio is not properly obtained and verified due to a
mechanical malfunction, the unobtainable gear is no longer commanded for that power up, the DTC is
stored and the TCIL flashes.
Transmission Inputs
Transmission Range Sensor Check Operation:
DTCs P0705, P0708 (open/invalid pattern for digital TRS)
P0707, P0708 (opens/shorts for analog TRS)
Monitor execution continuous
Monitor Sequence none
Monitoring Duration 30 seconds
Typical TRS check entry conditions : Minimum Maximum
Gear selector position each position for up to 30 seconds 480 seconds
Typical TRS malfunction thresholds:
For digital sensor : Invalid pattern from 3 (or 5) digital inputs or 1 analog circuit open for 5 seconds
For analog sensor : Voltage > 4.8 volts or < 0.2 voltage for 5 seconds
Output Shaft Speed Sensor Functional Check Operation:
DTCs P0720
Monitor execution continuous
Monitor Sequence none
Monitoring Duration 30 seconds
Typical OSS functional check entry conditions : Minimum Maximum
Gear selector position drive
Engine rpm (above converter stall speed) OR 3000 rpm
Turbine shaft rpm (if available) OR 1500 rpm
Output shaft rpm 650 rpm
Vehicle speed (if available) 15 mph
Typical OSS functional check malfunction thresholds:
Vehicle is inferred to be moving with positive driving torque and OSS < 100 to 200 rpm for 5 seconds
Page 878 of 947
AML EOBD System Operation Summary
Rory O’Curry Aston Martin Lagonda CONFIDENTIAL 1 May 2009
[email protected] AML EOBD Monitors 07 ROC.doc Page 32 of 43
Turbine Shaft Speed Sensor Functional Check Operation:
DTCs P0715
Monitor execution continuous
Monitor Sequence none
Monitoring Duration 30 seconds
Typical TSS functional check entry conditions: Minimum Maximum
Gear selector position drive
Engine rpm (above converter stall speed) OR 3000 rpm
Turbine shaft rpm (if available) OR 1500 rpm
Output shaft rpm 650 rpm
Vehicle speed (if available) 15 mph
Torque converter lock-up (some applications) 3rd gear only
Typical TSS functional check malfunction thresholds:
Vehicle is inferred to be moving with positiv e driving torque and TSS < 200 rpm for 5 seconds
Page 879 of 947
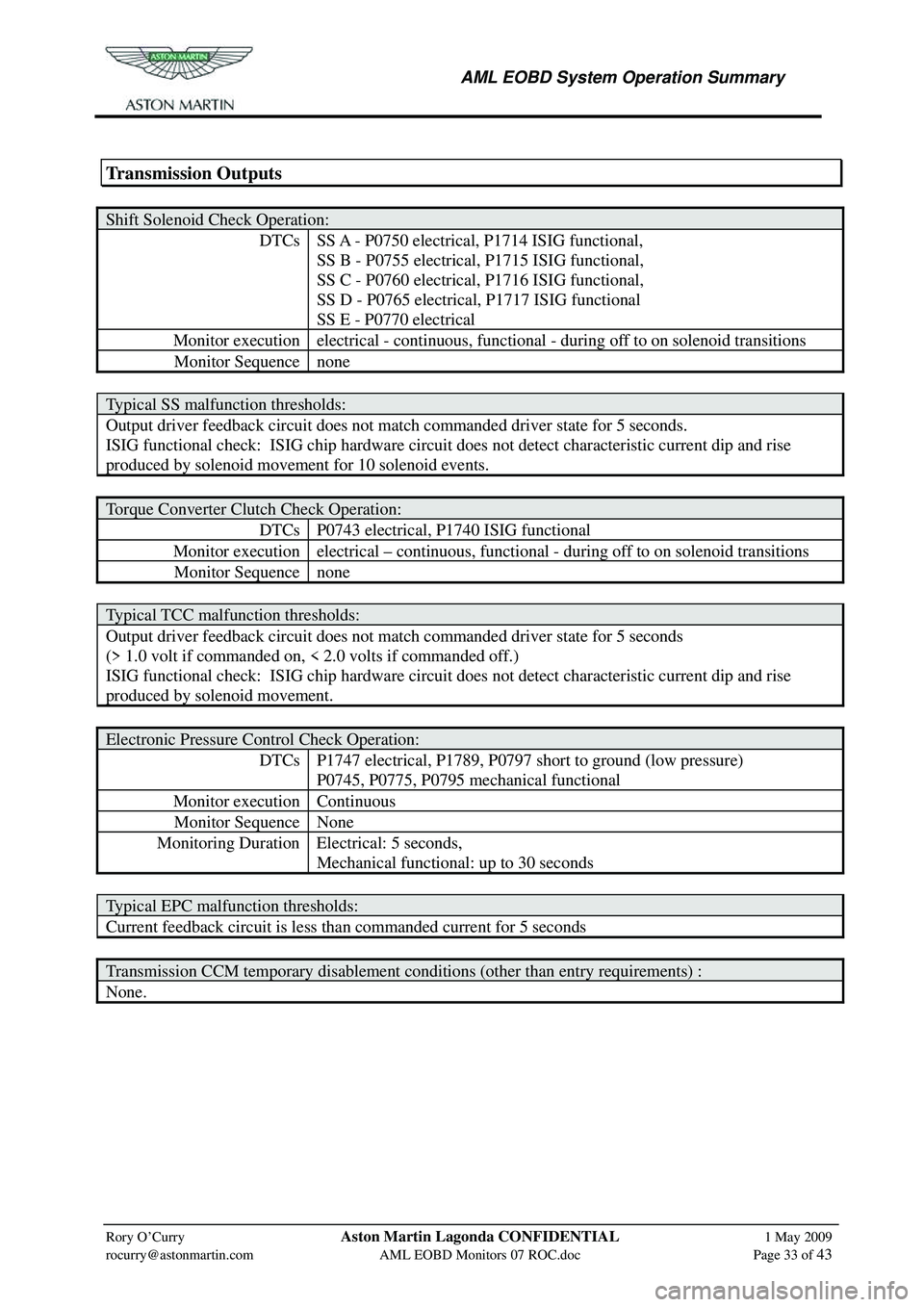
AML EOBD System Operation Summary
Rory O’Curry Aston Martin Lagonda CONFIDENTIAL 1 May 2009
[email protected] AML EOBD Monitors 07 ROC.doc Page 33 of 43
Transmission Outputs
Shift Solenoid Check Operation:
DTCs SS A - P0750 electrical, P1714 ISIG functional,
SS B - P0755 electrical, P1715 ISIG functional,
SS C - P0760 electrical, P1716 ISIG functional,
SS D - P0765 electrical, P1717 ISIG functional
SS E - P0770 electrical
Monitor execution electrical - continuous, functi onal - during off to on solenoid transitions
Monitor Sequence none
Typical SS malfunction thresholds:
Output driver feedback circuit does not match commanded driver state for 5 seconds.
ISIG functional check: ISIG chip hardware circu it does not detect characteristic current dip and rise
produced by solenoid movement for 10 solenoid events.
Torque Converter Clutch Check Operation:
DTCs P0743 electrical, P1740 ISIG functional
Monitor execution electrical – continuous, functi onal - during off to on solenoid transitions
Monitor Sequence none
Typical TCC malfunction thresholds:
Output driver feedback circuit does not match commanded driver state for 5 seconds
(> 1.0 volt if commanded on, < 2.0 volts if commanded off.)
ISIG functional check: ISIG chip hardware circu it does not detect characteristic current dip and rise
produced by solenoid movement.
Electronic Pressure Control Check Operation:
DTCs P1747 electrical, P1789, P0797 short to ground (low pressure)
P0745, P0775, P0795 mechanical functional
Monitor execution Continuous
Monitor Sequence None
Monitoring Duration Electrical: 5 seconds,
Mechanical functional: up to 30 seconds
Typical EPC malfunction thresholds:
Current feedback circuit is less than commanded current for 5 seconds
Transmission CCM temporary disablement conditions (other than entry requirements) :
None.
Page 880 of 947
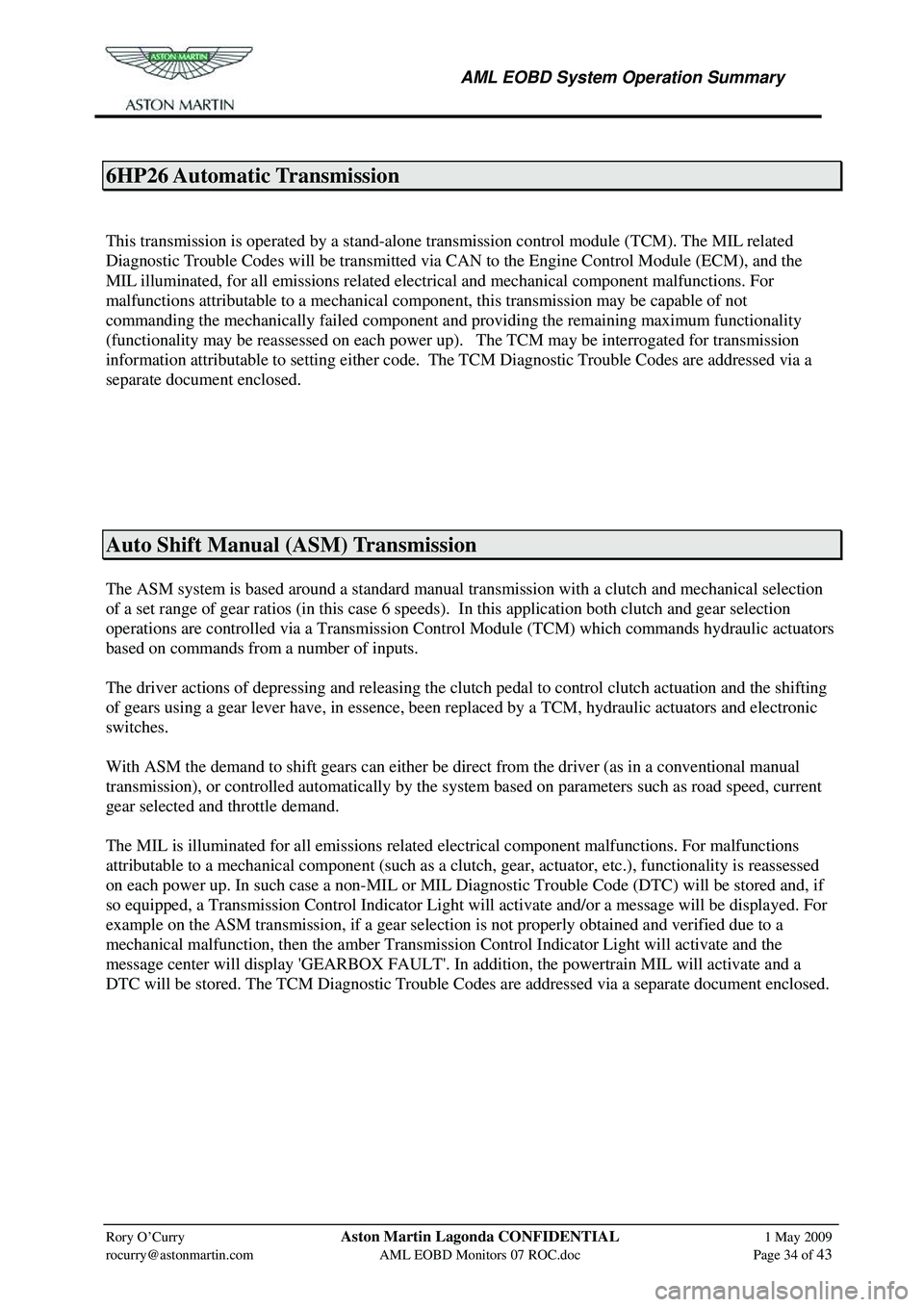
AML EOBD System Operation Summary
Rory O’Curry Aston Martin Lagonda CONFIDENTIAL 1 May 2009
[email protected] AML EOBD Monitors 07 ROC.doc Page 34 of 43
6HP26 Automatic Transmission
This transmission is operated by a stand-alone transmission control module (TCM). The MIL related
Diagnostic Trouble Codes will be transmitted via CAN to the Engine Control Module (ECM), and the
MIL illuminated, for all emissions related electrical and mechanical component malfunctions. For
malfunctions attributable to a mechanical component, this transmission may be capable of not
commanding the mechanically failed component a nd providing the remaining maximum functionality
(functionality may be reassessed on each power up). The TCM may be interrogated for transmission
information attributable to setting either code. The TCM Diagnostic Trouble Codes are addressed via a
separate document enclosed.
Auto Shift Manual (ASM) Transmission
The ASM system is based around a standard manual transmission with a clutch and mechanical selection
of a set range of gear ratios (in this case 6 speeds). In this application both clutch and gear selection
operations are controlled via a Transmission Contro l Module (TCM) which commands hydraulic actuators
based on commands from a number of inputs.
The driver actions of depressing and releasing the clutch pedal to control clutch actuation and the shifting
of gears using a gear lever have, in essence, been re placed by a TCM, hydraulic actuators and electronic
switches.
With ASM the demand to shift gears can either be direct from the driver (as in a conventional manual
transmission), or controlled automatically by the system based on parameters such as road speed, current
gear selected and throttle demand.
The MIL is illuminated for all emissions related electrical component malfunctions. For malfunctions
attributable to a mechanical component (such as a cl utch, gear, actuator, etc.), functionality is reassessed
on each power up. In such case a non-MIL or MIL Diagnos tic Trouble Code (DTC) will be stored and, if
so equipped, a Transmission Control Indicator Light will activate and/or a message will be displayed. For
example on the ASM transmission, if a gear selection is not properly obtained and verified due to a
mechanical malfunction, then the amber Transmission Control Indicator Light will activate and the
message center will display 'GEARBOX FAULT'. In addition, the powertrain MIL will activate and a
DTC will be stored. The TCM Diagnostic Trouble Cod es are addressed via a separate document enclosed.