Page 209 of 796
02-50
The bottom side of water jacket is desgined as sine wave to strengthen the structure of crankcase. The
main flow of coolant starts from outlet port of water pump and goes along the longitudinal direction of
engine. The coolant passage from cylinder head to inlet port of water pump is integrated in cylinder
head.
The engine oil from oil pump is supplied to the main oil gallery through oil channel, oil filter module and
cross bore in cylinder block without using external pipes. This oil is supplied to main bearing, cylinder
head and MBU. And, it is sprayed to the chain through the chain tensioner connected to cross bore.
Crankcase cross bore for oil supply
Water jacket core
Page 210 of 796
03-32210-01
1. SPECIFICATIONS
Description Specification
Fuel Diesel
Fuel filter Type Fuel heater + priming pump + water
separator integrated type
Filter type Changeable filter element type
Change interval EU every 40,000 km
GEN every 45,000 km
Water separation
intervalEU every 20,000 km
GEN every 15,000 km
Water accumulating capacity 200 cc
Heater capacity 250W 13.5V
Injector System pressure 1800 bar
High pressure fuel
pumpType Eccentric cam/Plunger type
Operating type Gear driven type
Normal operating temperature-40 ~ 125˚C
Operating pressure 1800 bar
Operating temperature-30 ~ 120˚C
Low pressure fuel
pumpType Vane type
Gear ratio (pump/engine) 0.5 : 1
Pressure 6 bar
Fuel tank Capacity 80 L
Material Plastic
Fuel sender Single sender type
Page 211 of 796
03-4
Took kit for low pressure lineTool kit for high pressure line
2. MAINTENANCE AND INSPECTION
1) Maintenance Procedures for DI Engine Fuel System
Always keep the workshop and lift clean (especially, from dust).
Always keep the tools clean (from oil or foreign materials).
Wear a clean vinyl apron to prevent the fuzz, dust and foreign materials from getting into fuel
system. Wash your hands and do not wear working gloves. 1.
2.
3.
Follow the below procedures before starting service works for fuel system.
If the problem is from HP pump, fuel supply line or injector, prepare the clean special tools and
sealing caps to perform the diagnosis for DI engine fuel system in this manual. At this point,
thoroughly clean the related area in engine compartment. 4.
Clean the engine compartment before starting service works.
Page 212 of 796
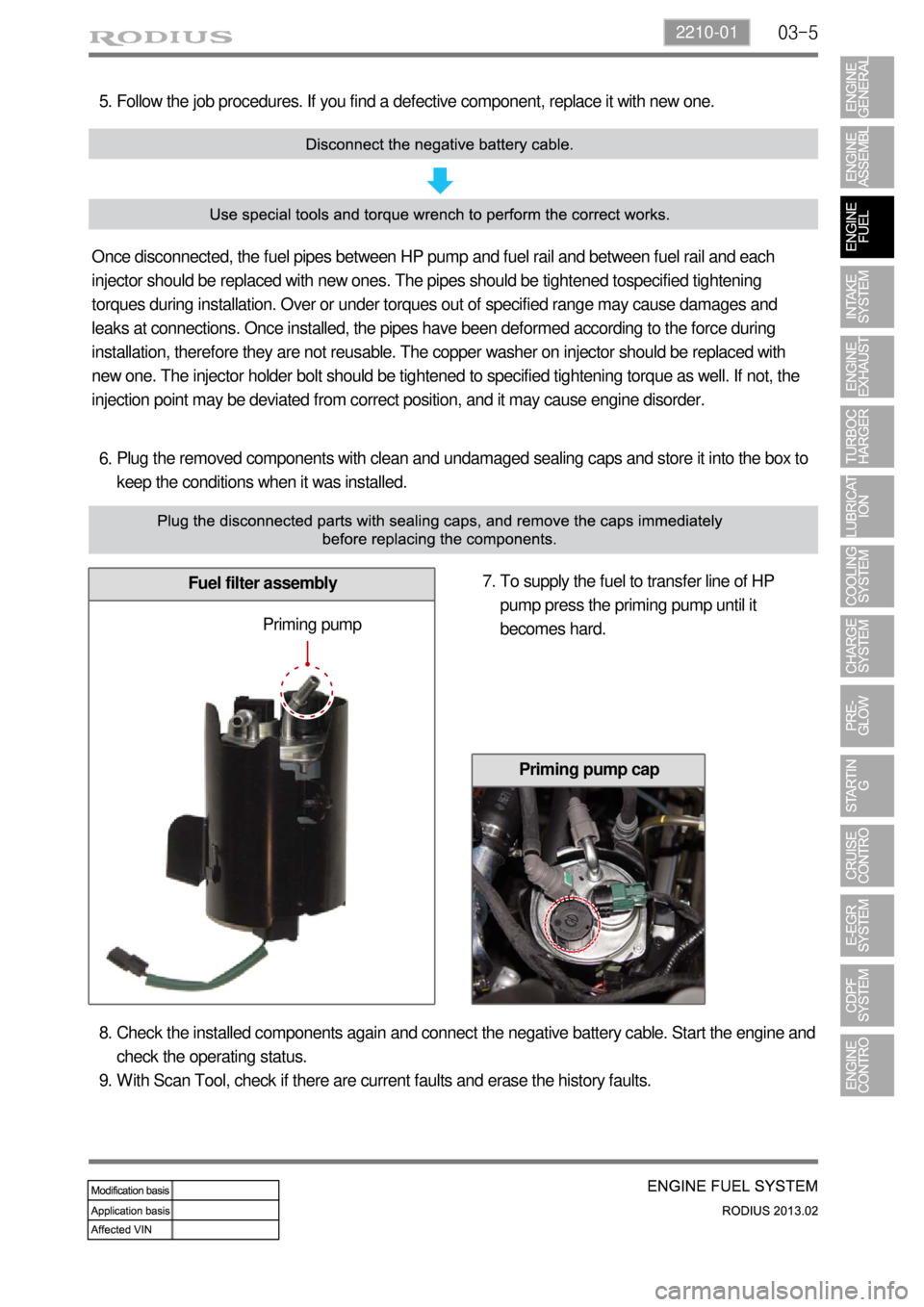
03-52210-01
Plug the removed components with clean and undamaged sealing caps and store it into the box to
keep the conditions when it was installed. 6.
Fuel filter assembly
Follow the job procedures. If you find a defective component, replace it with new one. 5.
Once disconnected, the fuel pipes between HP pump and fuel rail and between fuel rail and each
injector should be replaced with new ones. The pipes should be tightened tospecified tightening
torques during installation. Over or under torques out of specified range may cause damages and
leaks at connections. Once installed, the pipes have been deformed according to the force during
installation, therefore they are not reusable. The copper washer on injector should be replaced with
new one. The injector holder bolt should be tightened to specified tightening torque as well. If not, the
injection point may be deviated from correct position, and it may cause engine disorder.
To supply the fuel to transfer line of HP
pump press the priming pump until it
becomes hard. 7.
Priming pump
Check the installed components again and connect the negative battery cable. Start the engine and
check the operating status.
With Scan Tool, check if there are current faults and erase the history faults. 8.
9.
Priming pump cap
Page 213 of 796
03-6
2) Diagnostic Test for Engine Fuel System
(1) Overview
If a DTC is displayed on the diagnostic device, check the low pressure- and high pressure fuel
systems before removing the components.
To run the system properly, the electric system must be intact but for the DI engine, the fuel pressure
should be measured also when there is a malfunction even after the diagnostic test with a diagnostic
device.
(2) Hydraulic system
Page 214 of 796
03-72210-01
(3) Excessive backleak of injector
Excessive injector backlea ▶
Occurs when the injector control valve is not sealed due to the entry of the foreign materials.
Example: ▶
Entry of foreign materials
Burned out and worn HP pump
Mechanical damage inside the injector -
-
-
Page 215 of 796
03-8
(4) Loss of pump pressure/flow
Loss of HP pump pressure/flow ▶
Faulty fuel supply line, or damaged or worn pump causes the lack of flow pressure and flow volume
Example: ▶
Air in fuel supply line
Excessive load on fuel supply line (←400 mBar)
Burned out and mechanical worn pump
High temperature of fuel supply (> 85℃) -
-
-
-
Page 216 of 796
03-92210-01
Device for high pressure
Device for low pressure
3) DI Engine Fuel System Pressure Test
(1) Test device (Tool kit)
(2) Pre-check
Check-tighten fuel supply line
Check fuel level in fuel tank
Check air in fuel supply line (bubble in fuel supply line or fuel)
Check fuel supply line for leaks (low pressure and high pressure)
Check that specified fuel is used
Check fuel filter for contamination -
-
-
-
-
-