Page 665 of 796
09-194891-01
4) ARP (Active Roll-Over Protection)
The ARP (Active Roll-over Protection) system is a safety assistant device that minimizes, by controlling
brakes and the engine, the physical tendency of the vehicle rollover during sharp lane changes or U-
turns. For the system, software is added to the existing ESP system and no additional device or switch
is needed. One must note that the ARP system, just as general assistant devices including the ABS, is
only a safety assistant device using the ESP system and its function is useless when the situation
overcomes the physical power. Following picture shows how the ARP compensates the vehicle
position by varying each wheel's braking power to overcome the physical tendency of the vehicle
rollover during sharp turns.
The vehicle driving condition is controlled by the internally programmed logic according to the input
signals from wheel speed sensor, steering angle sensor and lateral sensor.
Page 666 of 796
09-20
During the ARP operation, vehicle safety (rollover prevention) takes the first priority and thus,
stronger engine control is in effect. Consequently, the vehicle speed decreases rapidly, so the
driver must take caution for the vehicle may drift away from the lane.
The ARP function is still available even when turning off the ESP system by ESP OFF switch.
However, if the ESP system is shut off due to a system failure, the ARP system is also not
available. -
-
Page 667 of 796
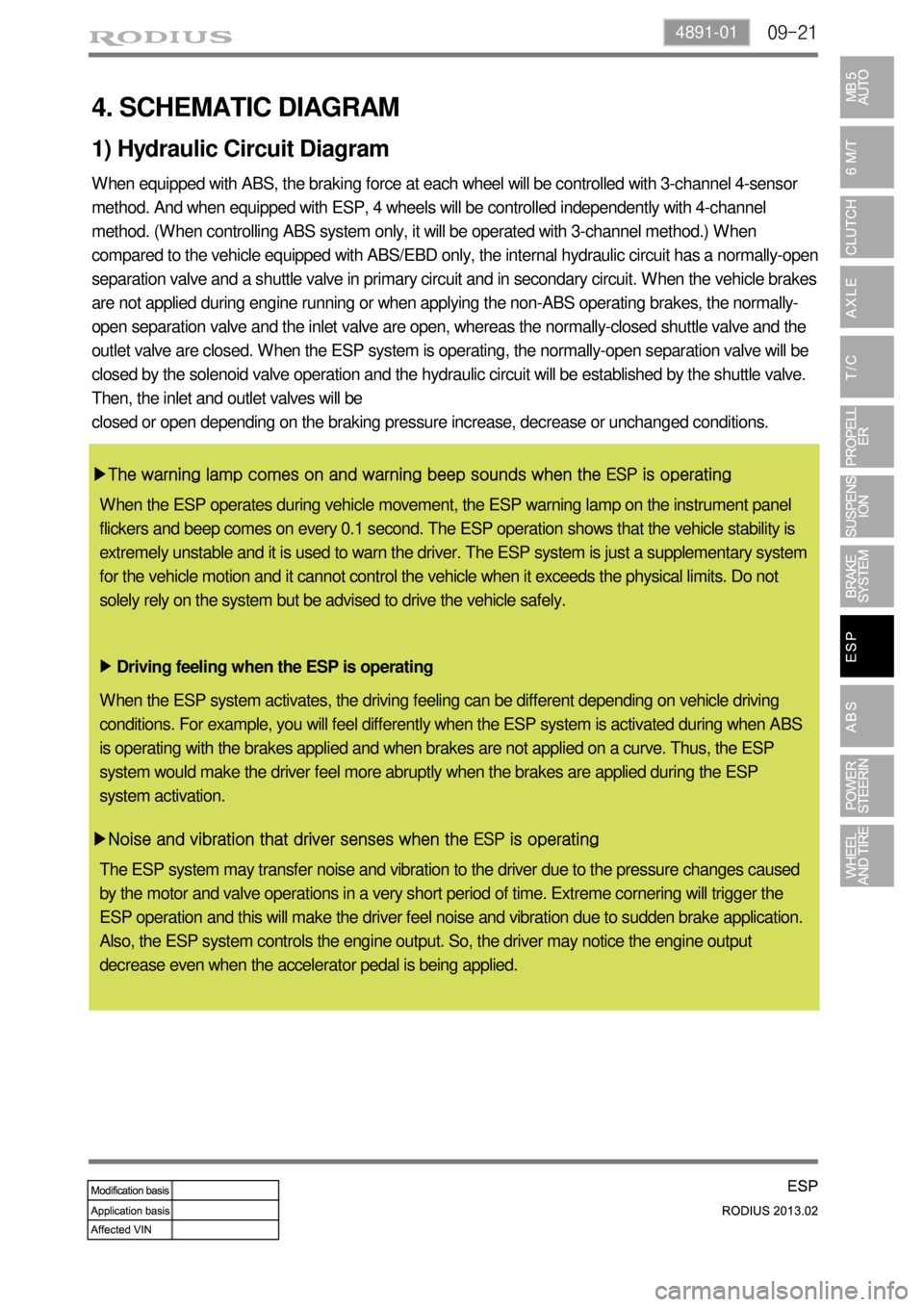
09-214891-01
4. SCHEMATIC DIAGRAM
When equipped with ABS, the braking force at each wheel will be controlled with 3-channel 4-sensor
method. And when equipped with ESP, 4 wheels will be controlled independently with 4-channel
method. (When controlling ABS system only, it will be operated with 3-channel method.) When
compared to the vehicle equipped with ABS/EBD only, the internal hydraulic circuit has a normally-open
separation valve and a shuttle valve in primary circuit and in secondary circuit. When the vehicle brakes
are not applied during engine running or when applying the non-ABS operating brakes, the normally-
open separation valve and the inlet valve are open, whereas the normally-closed shuttle valve and the
outlet valve are closed. When the ESP system is operating, the normally-open separation valve will be
closed by the solenoid valve operation and the hydraulic circuit will be established by the shuttle valve.
Then, the inlet and outlet valves will be
closed or open depending on the braking pressure increase, decrease or unchanged conditions.
▶The warning lamp comes on and warning beep sounds when the ESP is operating
Driving feeling when the ESP is operating ▶
▶Noise and vibration that driver senses when the ESP is operating
1) Hydraulic Circuit Diagram
When the ESP operates during vehicle movement, the ESP warning lamp on the instrument panel
flickers and beep comes on every 0.1 second. The ESP operation shows that the vehicle stability is
extremely unstable and it is used to warn the driver. The ESP system is just a supplementary system
for the vehicle motion and it cannot control the vehicle when it exceeds the physical limits. Do not
solely rely on the system but be advised to drive the vehicle safely.
When the ESP system activates, the driving feeling can be different depending on vehicle driving
conditions. For example, you will feel differently when the ESP system is activated during when ABS
is operating with the brakes applied and when brakes are not applied on a curve. Thus, the ESP
system would make the driver feel more abruptly when the brakes are applied during the ESP
system activation.
The ESP system may transfer noise and vibration to the driver due to the pressure changes caused
by the motor and valve operations in a very short period of time. Extreme cornering will trigger the
ESP operation and this will make the driver feel noise and vibration due to sudden brake application.
Also, the ESP system controls the engine output. So, the driver may notice the engine output
decrease even when the accelerator pedal is being applied.
Page 668 of 796
09-22
(1) Hydraulic Circuit Diagram
When compared to the vehicle equipped with ABS/EBD only, the internal hydraulic circuit has a
normally-open separation valve and a shuttle valve in primary circuit and in secondary circuit.
When the vehicle brakes are not applied during engine running or when applying the non-ABS
operating brakes, the normally-open separation valve and the inlet valve are open, whereas the
normally-closed shuttle valve and the outlet valve are closed.
When the ESP system is operating, the normally-open separation valve will be closed by the solenoid
valve operation and the hydraulic circuit will be established by the shuttle valve. Then, the inlet and
outlet valves will be closed or open depending on the braking pressure RISE, HOLD or DUMP
conditions.
Page 669 of 796
09-234891-01
(2) Hydraulic Circuit of HBA
The above figure shows one front and one rear wheel and the same hydraulic circuit forms as in the
ESP operation. When HECU recognizes that it is an emergency and it is required for hard braking,
depending on the pressure value of the brake pressure sensor and pressure changes caused by the
pressure sensor timing, it operates the pump immediately to apply the brake pressure at the wheels.
Then, the pressure in the pump increases until just before the corresponding wheel gets locked. The
motor still keeps rotating and the outlet valve and the separation valve will stay closed. When the wheel
starts to lock, the HBA function cancels and switches to ABS operation.
Page 670 of 796
09-24
(3) Hydraulic Circuit Diagrams in Conditions
▶Idling and Normal Braking Condition
In this position, the separation valve and the inlet valve are open (normal open), the electrically
operated shuttle valve and the outlet valve are closed.
When the brake is applied under these conditions, the brake fluid will be sent to each wheel via the
separation valve and inlet valve.
Page 671 of 796
09-254891-01
▶DUMP (ESP is working) Mode
The pressure decreases just before the wheel speed drops and the wheels are locked.
The inlet valve closes and the outlet valve opens as in the ESP HECU and the oil is gathered at the
low pressure chamber while no additional oil is being supplied. Then the pump operates to allow fast oil
drainage. The shuttle valve and the separation valve do not operate while decompression.
Page 672 of 796
09-26
▶HOLD (ESP is working) Mode
The Inlet valve and outlet valve will be closed to maintain the pressure in the hydraulic circuit applied at
the wheels. By closing the valves, the hydraulic pressure at the wheels will not be lost or supplied any
more. During ESP operation, the separation valve closes and only the shuttle valve at the pump
opens.