Page 201 of 2199
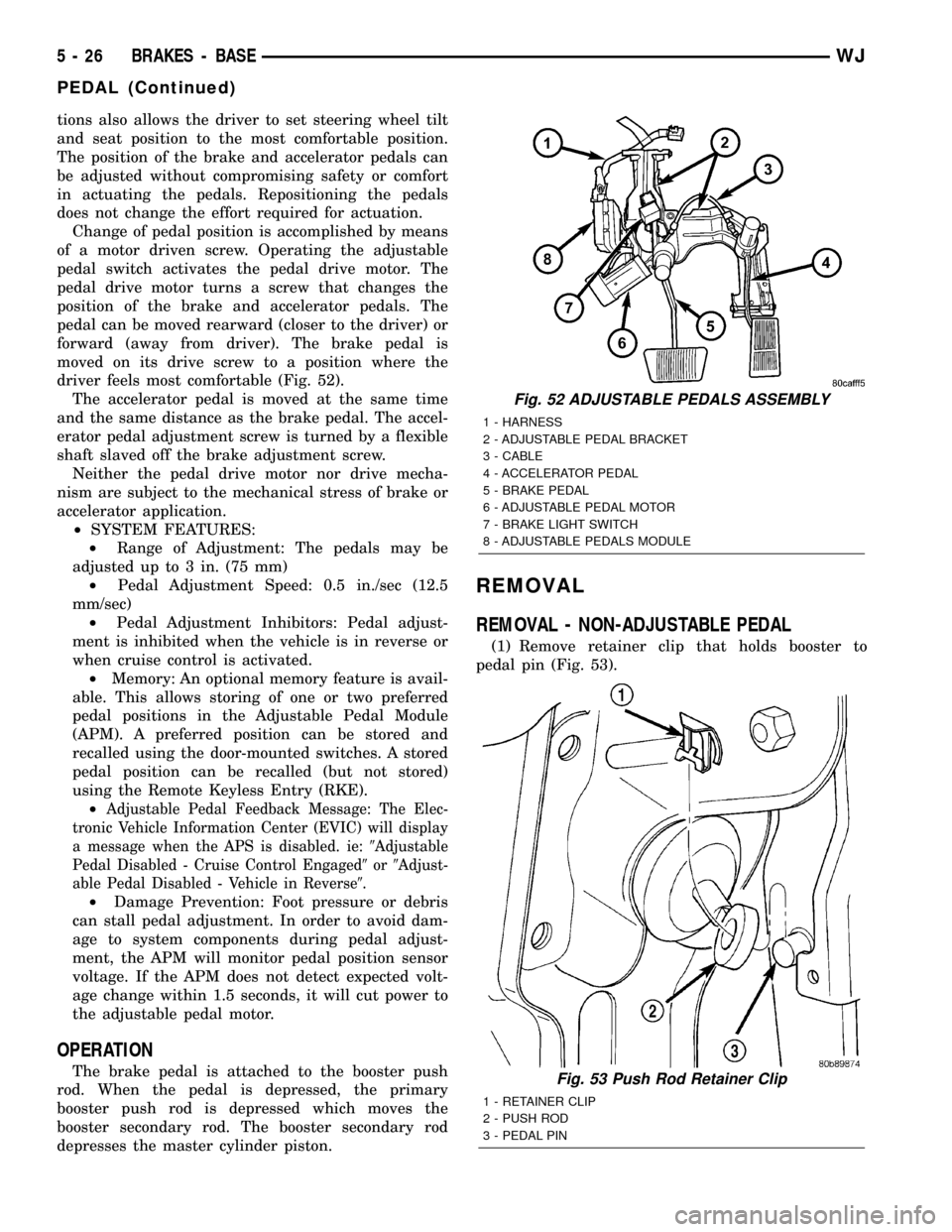
tions also allows the driver to set steering wheel tilt
and seat position to the most comfortable position.
The position of the brake and accelerator pedals can
be adjusted without compromising safety or comfort
in actuating the pedals. Repositioning the pedals
does not change the effort required for actuation.
Change of pedal position is accomplished by means
of a motor driven screw. Operating the adjustable
pedal switch activates the pedal drive motor. The
pedal drive motor turns a screw that changes the
position of the brake and accelerator pedals. The
pedal can be moved rearward (closer to the driver) or
forward (away from driver). The brake pedal is
moved on its drive screw to a position where the
driver feels most comfortable (Fig. 52).
The accelerator pedal is moved at the same time
and the same distance as the brake pedal. The accel-
erator pedal adjustment screw is turned by a flexible
shaft slaved off the brake adjustment screw.
Neither the pedal drive motor nor drive mecha-
nism are subject to the mechanical stress of brake or
accelerator application.
²SYSTEM FEATURES:
²Range of Adjustment: The pedals may be
adjusted up to 3 in. (75 mm)
²Pedal Adjustment Speed: 0.5 in./sec (12.5
mm/sec)
²Pedal Adjustment Inhibitors: Pedal adjust-
ment is inhibited when the vehicle is in reverse or
when cruise control is activated.
²Memory: An optional memory feature is avail-
able. This allows storing of one or two preferred
pedal positions in the Adjustable Pedal Module
(APM). A preferred position can be stored and
recalled using the door-mounted switches. A stored
pedal position can be recalled (but not stored)
using the Remote Keyless Entry (RKE).
²
Adjustable Pedal Feedback Message: The Elec-
tronic Vehicle Information Center (EVIC) will display
a message when the APS is disabled. ie:9Adjustable
Pedal Disabled - Cruise Control Engaged9or9Adjust-
able Pedal Disabled - Vehicle in Reverse9.
²Damage Prevention: Foot pressure or debris
can stall pedal adjustment. In order to avoid dam-
age to system components during pedal adjust-
ment, the APM will monitor pedal position sensor
voltage. If the APM does not detect expected volt-
age change within 1.5 seconds, it will cut power to
the adjustable pedal motor.
OPERATION
The brake pedal is attached to the booster push
rod. When the pedal is depressed, the primary
booster push rod is depressed which moves the
booster secondary rod. The booster secondary rod
depresses the master cylinder piston.
REMOVAL
REMOVAL - NON-ADJUSTABLE PEDAL
(1) Remove retainer clip that holds booster to
pedal pin (Fig. 53).
Fig. 52 ADJUSTABLE PEDALS ASSEMBLY
1 - HARNESS
2 - ADJUSTABLE PEDAL BRACKET
3 - CABLE
4 - ACCELERATOR PEDAL
5 - BRAKE PEDAL
6 - ADJUSTABLE PEDAL MOTOR
7 - BRAKE LIGHT SWITCH
8 - ADJUSTABLE PEDALS MODULE
Fig. 53 Push Rod Retainer Clip
1 - RETAINER CLIP
2 - PUSH ROD
3 - PEDAL PIN
5 - 26 BRAKES - BASEWJ
PEDAL (Continued)
Page 202 of 2199
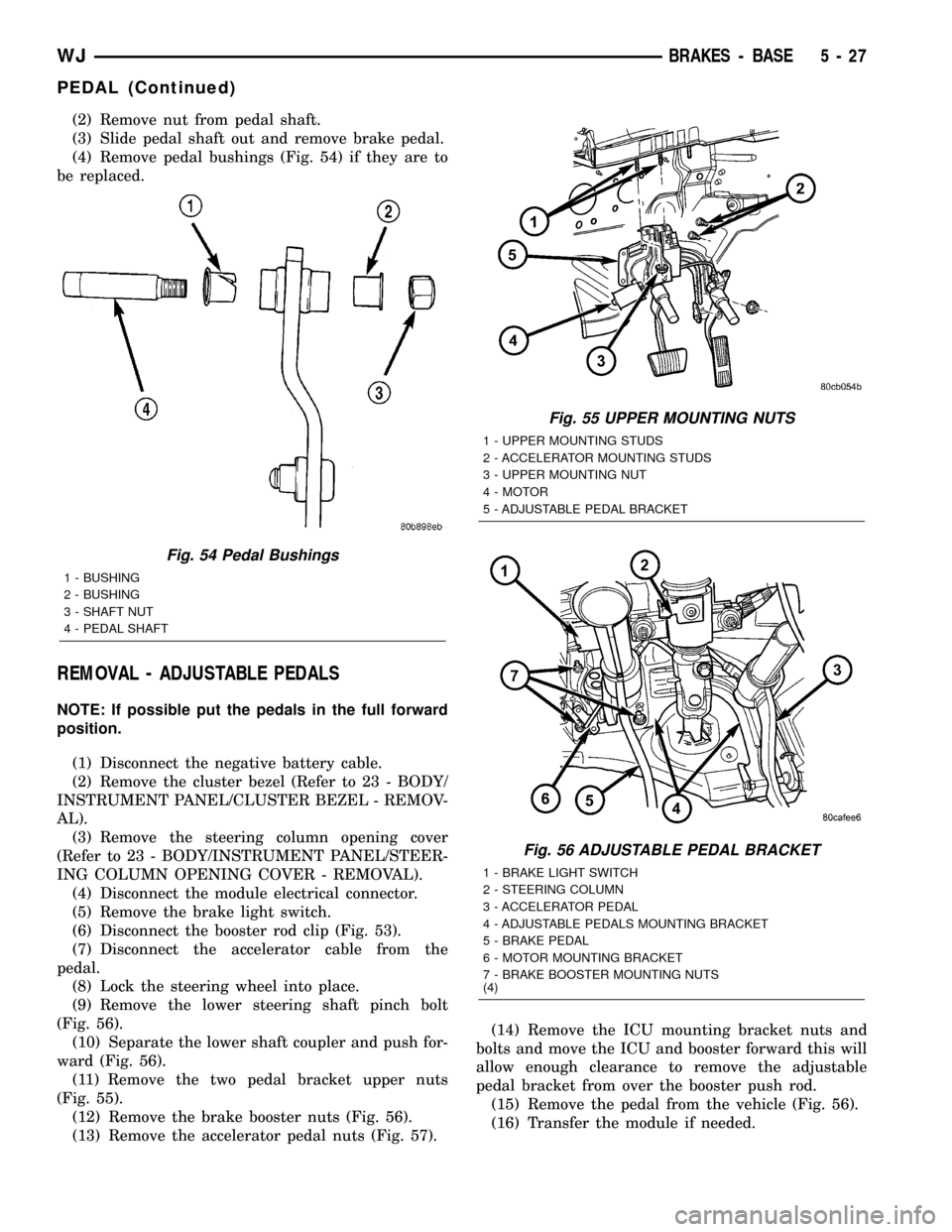
(2) Remove nut from pedal shaft.
(3) Slide pedal shaft out and remove brake pedal.
(4) Remove pedal bushings (Fig. 54) if they are to
be replaced.
REMOVAL - ADJUSTABLE PEDALS
NOTE: If possible put the pedals in the full forward
position.
(1) Disconnect the negative battery cable.
(2) Remove the cluster bezel (Refer to 23 - BODY/
INSTRUMENT PANEL/CLUSTER BEZEL - REMOV-
AL).
(3) Remove the steering column opening cover
(Refer to 23 - BODY/INSTRUMENT PANEL/STEER-
ING COLUMN OPENING COVER - REMOVAL).
(4) Disconnect the module electrical connector.
(5) Remove the brake light switch.
(6) Disconnect the booster rod clip (Fig. 53).
(7) Disconnect the accelerator cable from the
pedal.
(8) Lock the steering wheel into place.
(9) Remove the lower steering shaft pinch bolt
(Fig. 56).
(10) Separate the lower shaft coupler and push for-
ward (Fig. 56).
(11) Remove the two pedal bracket upper nuts
(Fig. 55).
(12) Remove the brake booster nuts (Fig. 56).
(13) Remove the accelerator pedal nuts (Fig. 57).(14) Remove the ICU mounting bracket nuts and
bolts and move the ICU and booster forward this will
allow enough clearance to remove the adjustable
pedal bracket from over the booster push rod.
(15) Remove the pedal from the vehicle (Fig. 56).
(16) Transfer the module if needed.
Fig. 54 Pedal Bushings
1 - BUSHING
2 - BUSHING
3 - SHAFT NUT
4 - PEDAL SHAFT
Fig. 55 UPPER MOUNTING NUTS
1 - UPPER MOUNTING STUDS
2 - ACCELERATOR MOUNTING STUDS
3 - UPPER MOUNTING NUT
4 - MOTOR
5 - ADJUSTABLE PEDAL BRACKET
Fig. 56 ADJUSTABLE PEDAL BRACKET
1 - BRAKE LIGHT SWITCH
2 - STEERING COLUMN
3 - ACCELERATOR PEDAL
4 - ADJUSTABLE PEDALS MOUNTING BRACKET
5 - BRAKE PEDAL
6 - MOTOR MOUNTING BRACKET
7 - BRAKE BOOSTER MOUNTING NUTS
(4)
WJBRAKES - BASE 5 - 27
PEDAL (Continued)
Page 203 of 2199
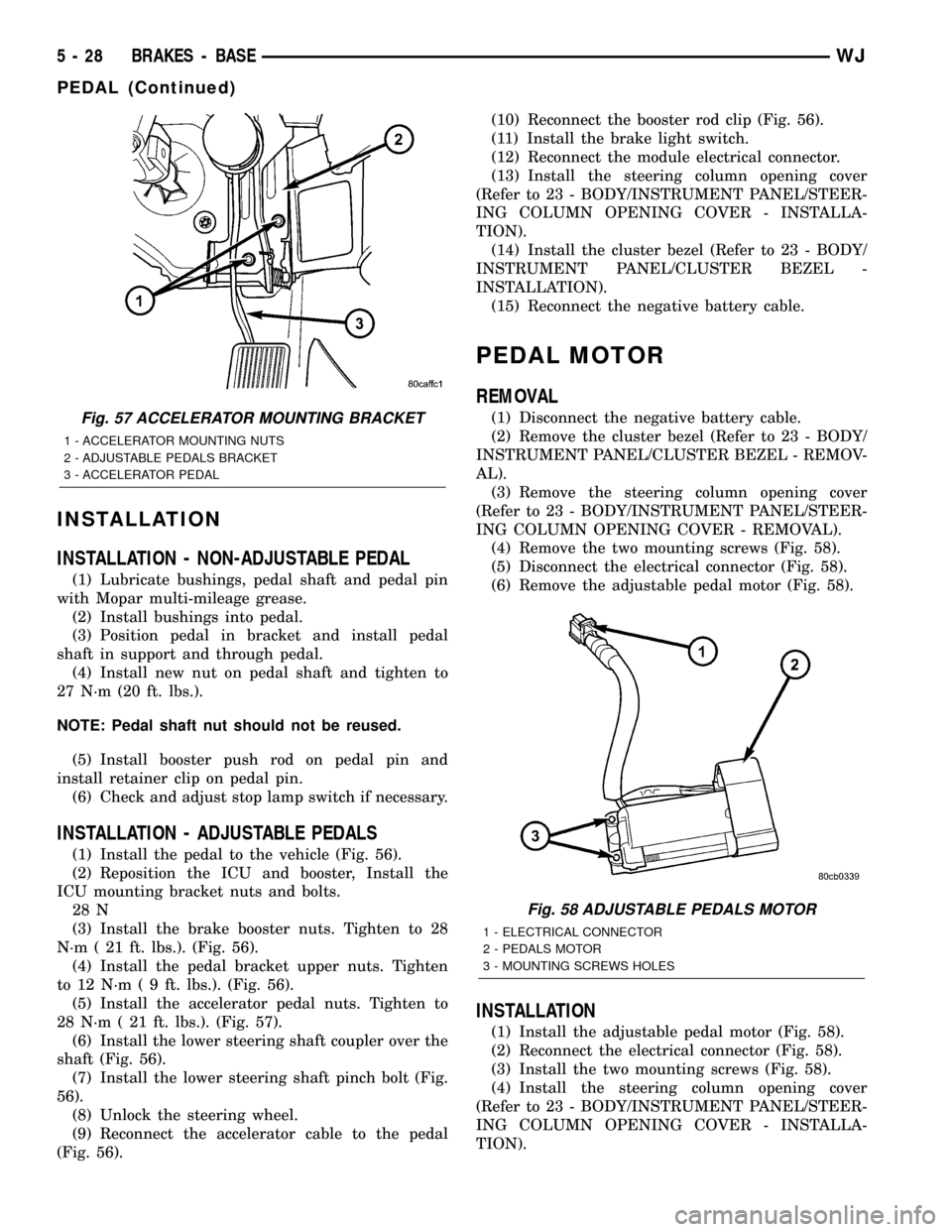
INSTALLATION
INSTALLATION - NON-ADJUSTABLE PEDAL
(1) Lubricate bushings, pedal shaft and pedal pin
with Mopar multi-mileage grease.
(2) Install bushings into pedal.
(3) Position pedal in bracket and install pedal
shaft in support and through pedal.
(4) Install new nut on pedal shaft and tighten to
27 N´m (20 ft. lbs.).
NOTE: Pedal shaft nut should not be reused.
(5) Install booster push rod on pedal pin and
install retainer clip on pedal pin.
(6) Check and adjust stop lamp switch if necessary.
INSTALLATION - ADJUSTABLE PEDALS
(1) Install the pedal to the vehicle (Fig. 56).
(2) Reposition the ICU and booster, Install the
ICU mounting bracket nuts and bolts.
28 N
(3) Install the brake booster nuts. Tighten to 28
N´m ( 21 ft. lbs.). (Fig. 56).
(4) Install the pedal bracket upper nuts. Tighten
to 12 N´m ( 9 ft. lbs.). (Fig. 56).
(5) Install the accelerator pedal nuts. Tighten to
28 N´m ( 21 ft. lbs.). (Fig. 57).
(6) Install the lower steering shaft coupler over the
shaft (Fig. 56).
(7) Install the lower steering shaft pinch bolt (Fig.
56).
(8) Unlock the steering wheel.
(9) Reconnect the accelerator cable to the pedal
(Fig. 56).(10) Reconnect the booster rod clip (Fig. 56).
(11) Install the brake light switch.
(12) Reconnect the module electrical connector.
(13) Install the steering column opening cover
(Refer to 23 - BODY/INSTRUMENT PANEL/STEER-
ING COLUMN OPENING COVER - INSTALLA-
TION).
(14) Install the cluster bezel (Refer to 23 - BODY/
INSTRUMENT PANEL/CLUSTER BEZEL -
INSTALLATION).
(15) Reconnect the negative battery cable.
PEDAL MOTOR
REMOVAL
(1) Disconnect the negative battery cable.
(2) Remove the cluster bezel (Refer to 23 - BODY/
INSTRUMENT PANEL/CLUSTER BEZEL - REMOV-
AL).
(3) Remove the steering column opening cover
(Refer to 23 - BODY/INSTRUMENT PANEL/STEER-
ING COLUMN OPENING COVER - REMOVAL).
(4) Remove the two mounting screws (Fig. 58).
(5) Disconnect the electrical connector (Fig. 58).
(6) Remove the adjustable pedal motor (Fig. 58).
INSTALLATION
(1) Install the adjustable pedal motor (Fig. 58).
(2) Reconnect the electrical connector (Fig. 58).
(3) Install the two mounting screws (Fig. 58).
(4) Install the steering column opening cover
(Refer to 23 - BODY/INSTRUMENT PANEL/STEER-
ING COLUMN OPENING COVER - INSTALLA-
TION).
Fig. 57 ACCELERATOR MOUNTING BRACKET
1 - ACCELERATOR MOUNTING NUTS
2 - ADJUSTABLE PEDALS BRACKET
3 - ACCELERATOR PEDAL
Fig. 58 ADJUSTABLE PEDALS MOTOR
1 - ELECTRICAL CONNECTOR
2 - PEDALS MOTOR
3 - MOUNTING SCREWS HOLES
5 - 28 BRAKES - BASEWJ
PEDAL (Continued)
Page 204 of 2199
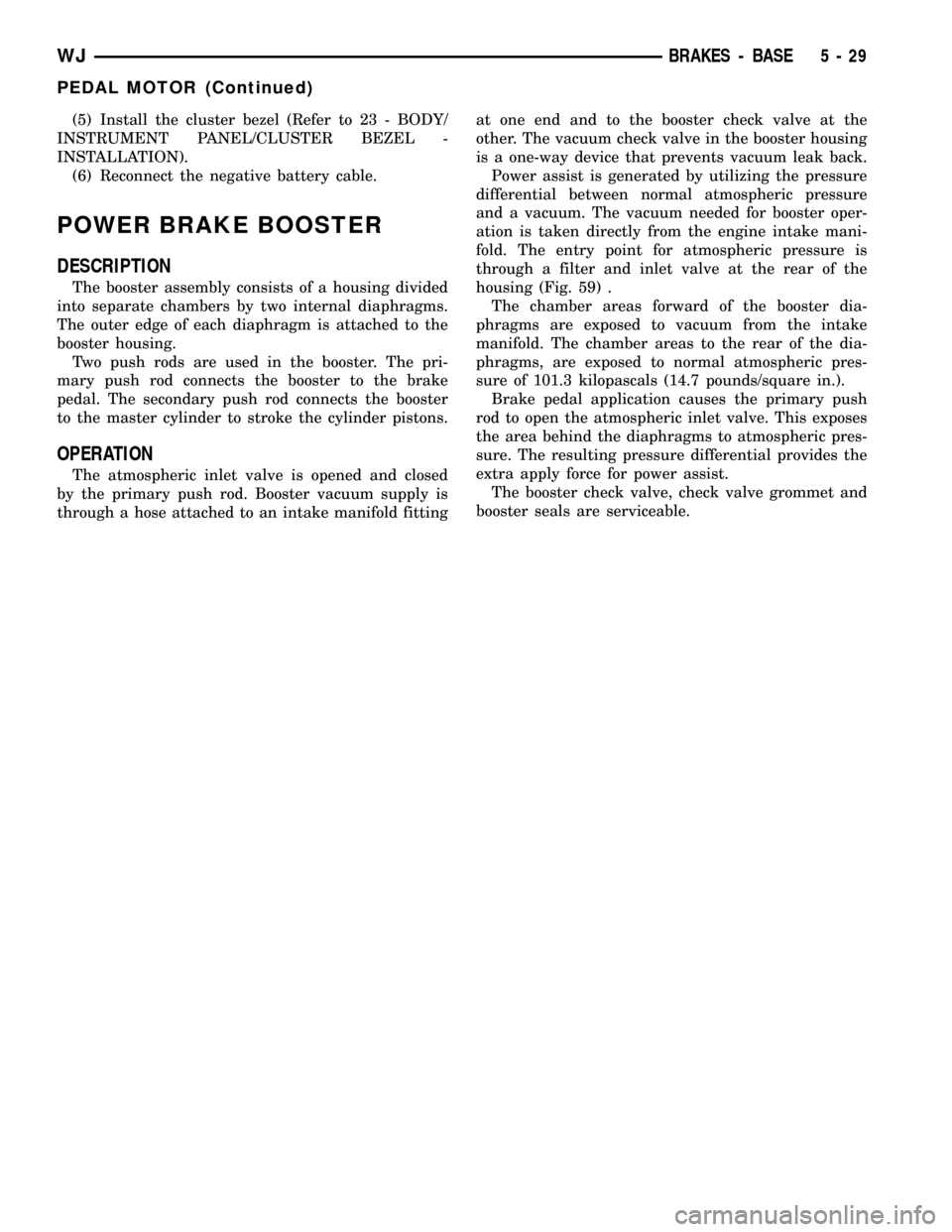
(5) Install the cluster bezel (Refer to 23 - BODY/
INSTRUMENT PANEL/CLUSTER BEZEL -
INSTALLATION).
(6) Reconnect the negative battery cable.
POWER BRAKE BOOSTER
DESCRIPTION
The booster assembly consists of a housing divided
into separate chambers by two internal diaphragms.
The outer edge of each diaphragm is attached to the
booster housing.
Two push rods are used in the booster. The pri-
mary push rod connects the booster to the brake
pedal. The secondary push rod connects the booster
to the master cylinder to stroke the cylinder pistons.
OPERATION
The atmospheric inlet valve is opened and closed
by the primary push rod. Booster vacuum supply is
through a hose attached to an intake manifold fittingat one end and to the booster check valve at the
other. The vacuum check valve in the booster housing
is a one-way device that prevents vacuum leak back.
Power assist is generated by utilizing the pressure
differential between normal atmospheric pressure
and a vacuum. The vacuum needed for booster oper-
ation is taken directly from the engine intake mani-
fold. The entry point for atmospheric pressure is
through a filter and inlet valve at the rear of the
housing (Fig. 59) .
The chamber areas forward of the booster dia-
phragms are exposed to vacuum from the intake
manifold. The chamber areas to the rear of the dia-
phragms, are exposed to normal atmospheric pres-
sure of 101.3 kilopascals (14.7 pounds/square in.).
Brake pedal application causes the primary push
rod to open the atmospheric inlet valve. This exposes
the area behind the diaphragms to atmospheric pres-
sure. The resulting pressure differential provides the
extra apply force for power assist.
The booster check valve, check valve grommet and
booster seals are serviceable.
WJBRAKES - BASE 5 - 29
PEDAL MOTOR (Continued)
Page 205 of 2199
Fig. 59 Power Brake Booster±Typical
1 - VACUUM CHECK VALVE
2 - FRONT DIAPHRAGM
3 - REAR DIAPHRAGM
4 - HOUSING
5 - SEAL
6 - AIR FILTER
7 - PRIMARY PUSH ROD (TO BRAKE PEDAL)8 - ATMOSPHERIC INLET VALVE ASSEMBLY
9 - BOOSTER MOUNTING STUDS (4)
10 - SECONDARY PUSH ROD (TO MASTER CYLINDER)
11 - MASTER CYLINDER MOUNTING STUD (2)
12 - SPRING
5 - 30 BRAKES - BASEWJ
POWER BRAKE BOOSTER (Continued)
Page 206 of 2199
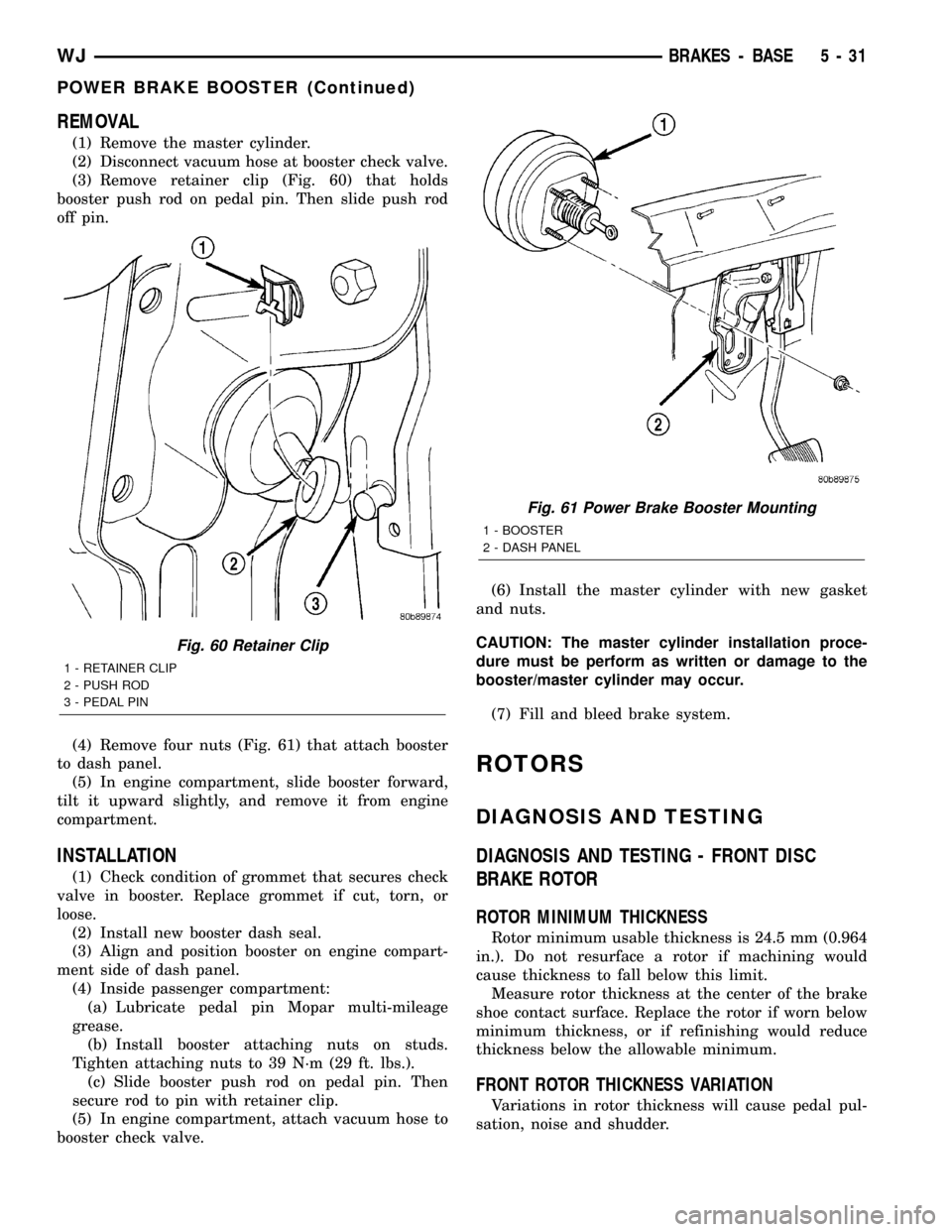
REMOVAL
(1) Remove the master cylinder.
(2) Disconnect vacuum hose at booster check valve.
(3) Remove retainer clip (Fig. 60) that holds
booster push rod on pedal pin. Then slide push rod
off pin.
(4) Remove four nuts (Fig. 61) that attach booster
to dash panel.
(5) In engine compartment, slide booster forward,
tilt it upward slightly, and remove it from engine
compartment.
INSTALLATION
(1) Check condition of grommet that secures check
valve in booster. Replace grommet if cut, torn, or
loose.
(2) Install new booster dash seal.
(3) Align and position booster on engine compart-
ment side of dash panel.
(4) Inside passenger compartment:
(a) Lubricate pedal pin Mopar multi-mileage
grease.
(b) Install booster attaching nuts on studs.
Tighten attaching nuts to 39 N´m (29 ft. lbs.).
(c) Slide booster push rod on pedal pin. Then
secure rod to pin with retainer clip.
(5) In engine compartment, attach vacuum hose to
booster check valve.(6) Install the master cylinder with new gasket
and nuts.
CAUTION: The master cylinder installation proce-
dure must be perform as written or damage to the
booster/master cylinder may occur.
(7) Fill and bleed brake system.
ROTORS
DIAGNOSIS AND TESTING
DIAGNOSIS AND TESTING - FRONT DISC
BRAKE ROTOR
ROTOR MINIMUM THICKNESS
Rotor minimum usable thickness is 24.5 mm (0.964
in.). Do not resurface a rotor if machining would
cause thickness to fall below this limit.
Measure rotor thickness at the center of the brake
shoe contact surface. Replace the rotor if worn below
minimum thickness, or if refinishing would reduce
thickness below the allowable minimum.
FRONT ROTOR THICKNESS VARIATION
Variations in rotor thickness will cause pedal pul-
sation, noise and shudder.
Fig. 60 Retainer Clip
1 - RETAINER CLIP
2 - PUSH ROD
3 - PEDAL PIN
Fig. 61 Power Brake Booster Mounting
1 - BOOSTER
2 - DASH PANEL
WJBRAKES - BASE 5 - 31
POWER BRAKE BOOSTER (Continued)
Page 207 of 2199
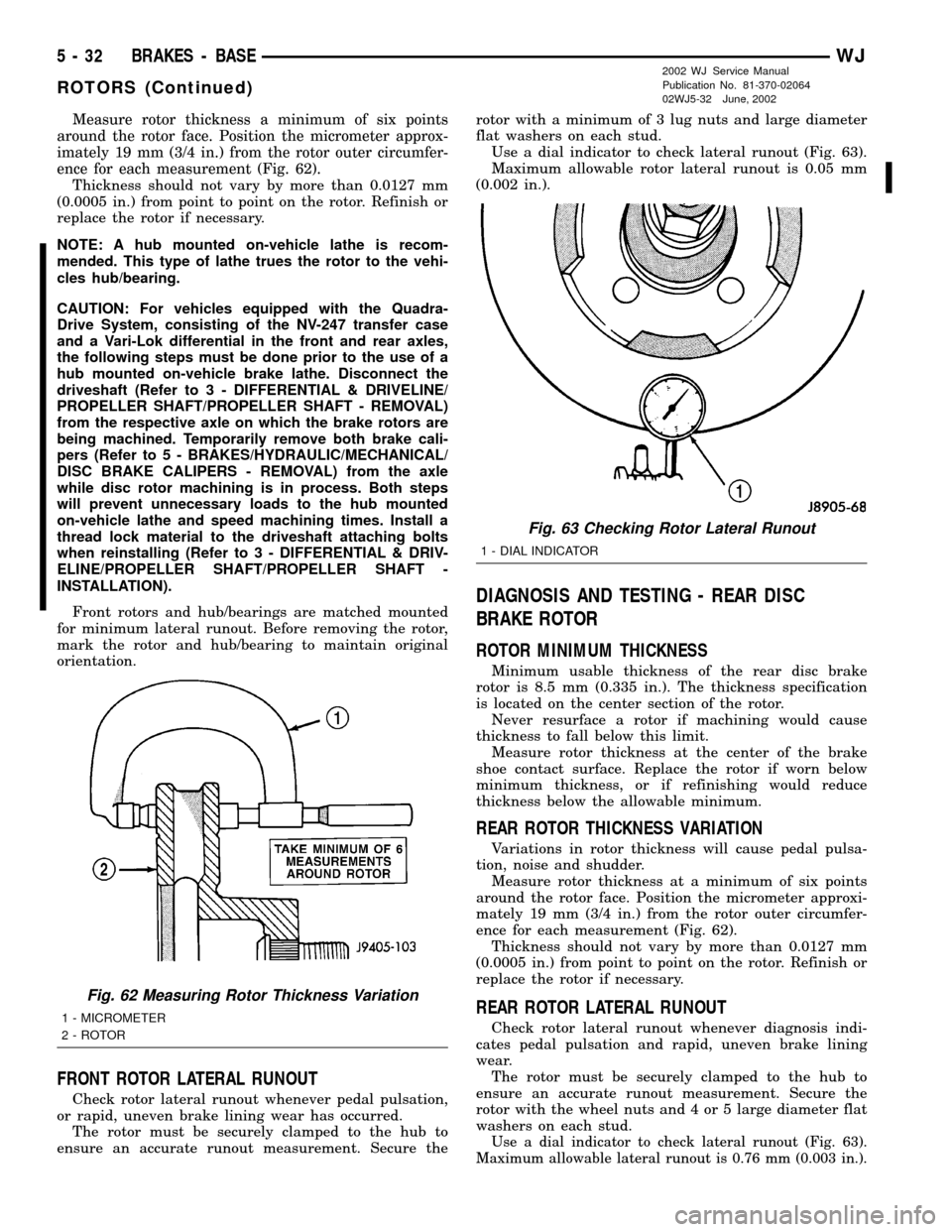
Measure rotor thickness a minimum of six points
around the rotor face. Position the micrometer approx-
imately 19 mm (3/4 in.) from the rotor outer circumfer-
ence for each measurement (Fig. 62).
Thickness should not vary by more than 0.0127 mm
(0.0005 in.) from point to point on the rotor. Refinish or
replace the rotor if necessary.
NOTE: A hub mounted on-vehicle lathe is recom-
mended. This type of lathe trues the rotor to the vehi-
cles hub/bearing.
CAUTION: For vehicles equipped with the Quadra-
Drive System, consisting of the NV-247 transfer case
and a Vari-Lok differential in the front and rear axles,
the following steps must be done prior to the use of a
hub mounted on-vehicle brake lathe. Disconnect the
driveshaft (Refer to 3 - DIFFERENTIAL & DRIVELINE/
PROPELLER SHAFT/PROPELLER SHAFT - REMOVAL)
from the respective axle on which the brake rotors are
being machined. Temporarily remove both brake cali-
pers (Refer to 5 - BRAKES/HYDRAULIC/MECHANICAL/
DISC BRAKE CALIPERS - REMOVAL) from the axle
while disc rotor machining is in process. Both steps
will prevent unnecessary loads to the hub mounted
on-vehicle lathe and speed machining times. Install a
thread lock material to the driveshaft attaching bolts
when reinstalling (Refer to 3 - DIFFERENTIAL & DRIV-
ELINE/PROPELLER SHAFT/PROPELLER SHAFT -
INSTALLATION).
Front rotors and hub/bearings are matched mounted
for minimum lateral runout. Before removing the rotor,
mark the rotor and hub/bearing to maintain original
orientation.
FRONT ROTOR LATERAL RUNOUT
Check rotor lateral runout whenever pedal pulsation,
or rapid, uneven brake lining wear has occurred.
The rotor must be securely clamped to the hub to
ensure an accurate runout measurement. Secure therotor with a minimum of 3 lug nuts and large diameter
flat washers on each stud.
Use a dial indicator to check lateral runout (Fig. 63).
Maximum allowable rotor lateral runout is 0.05 mm
(0.002 in.).
DIAGNOSIS AND TESTING - REAR DISC
BRAKE ROTOR
ROTOR MINIMUM THICKNESS
Minimum usable thickness of the rear disc brake
rotor is 8.5 mm (0.335 in.). The thickness specification
is located on the center section of the rotor.
Never resurface a rotor if machining would cause
thickness to fall below this limit.
Measure rotor thickness at the center of the brake
shoe contact surface. Replace the rotor if worn below
minimum thickness, or if refinishing would reduce
thickness below the allowable minimum.
REAR ROTOR THICKNESS VARIATION
Variations in rotor thickness will cause pedal pulsa-
tion, noise and shudder.
Measure rotor thickness at a minimum of six points
around the rotor face. Position the micrometer approxi-
mately 19 mm (3/4 in.) from the rotor outer circumfer-
ence for each measurement (Fig. 62).
Thickness should not vary by more than 0.0127 mm
(0.0005 in.) from point to point on the rotor. Refinish or
replace the rotor if necessary.
REAR ROTOR LATERAL RUNOUT
Check rotor lateral runout whenever diagnosis indi-
cates pedal pulsation and rapid, uneven brake lining
wear.
The rotor must be securely clamped to the hub to
ensure an accurate runout measurement. Secure the
rotor with the wheel nuts and 4 or 5 large diameter flat
washers on each stud.
Use a dial indicator to check lateral runout (Fig. 63).
Maximum allowable lateral runout is 0.76 mm (0.003 in.).
Fig. 62 Measuring Rotor Thickness Variation
1 - MICROMETER
2 - ROTOR
Fig. 63 Checking Rotor Lateral Runout
1 - DIAL INDICATOR
5 - 32 BRAKES - BASEWJ
ROTORS (Continued)
2002 WJ Service Manual
Publication No. 81-370-02064
02WJ5-32 June, 2002
Page 208 of 2199
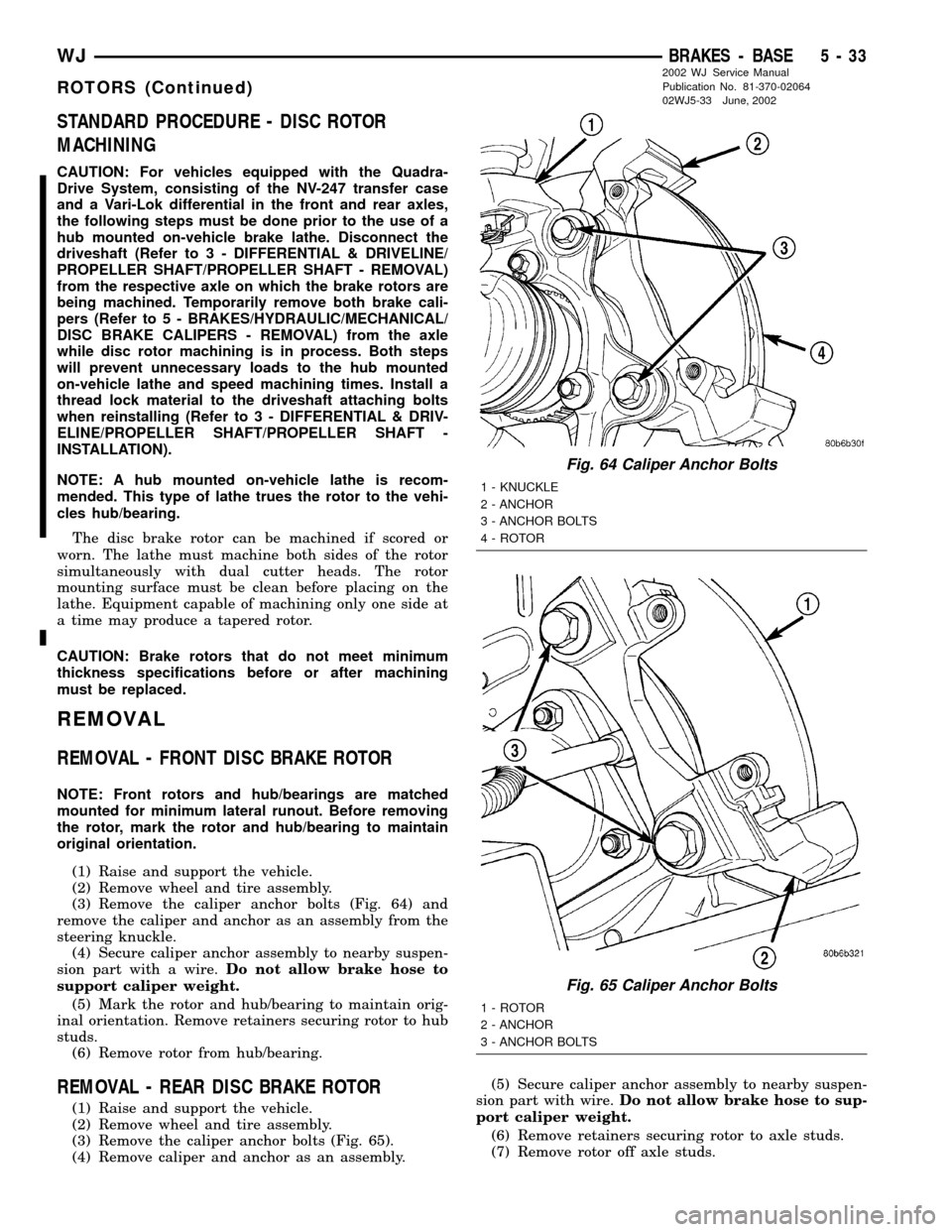
STANDARD PROCEDURE - DISC ROTOR
MACHINING
CAUTION: For vehicles equipped with the Quadra-
Drive System, consisting of the NV-247 transfer case
and a Vari-Lok differential in the front and rear axles,
the following steps must be done prior to the use of a
hub mounted on-vehicle brake lathe. Disconnect the
driveshaft (Refer to 3 - DIFFERENTIAL & DRIVELINE/
PROPELLER SHAFT/PROPELLER SHAFT - REMOVAL)
from the respective axle on which the brake rotors are
being machined. Temporarily remove both brake cali-
pers (Refer to 5 - BRAKES/HYDRAULIC/MECHANICAL/
DISC BRAKE CALIPERS - REMOVAL) from the axle
while disc rotor machining is in process. Both steps
will prevent unnecessary loads to the hub mounted
on-vehicle lathe and speed machining times. Install a
thread lock material to the driveshaft attaching bolts
when reinstalling (Refer to 3 - DIFFERENTIAL & DRIV-
ELINE/PROPELLER SHAFT/PROPELLER SHAFT -
INSTALLATION).
NOTE: A hub mounted on-vehicle lathe is recom-
mended. This type of lathe trues the rotor to the vehi-
cles hub/bearing.
The disc brake rotor can be machined if scored or
worn. The lathe must machine both sides of the rotor
simultaneously with dual cutter heads. The rotor
mounting surface must be clean before placing on the
lathe. Equipment capable of machining only one side at
a time may produce a tapered rotor.
CAUTION: Brake rotors that do not meet minimum
thickness specifications before or after machining
must be replaced.
REMOVAL
REMOVAL - FRONT DISC BRAKE ROTOR
NOTE: Front rotors and hub/bearings are matched
mounted for minimum lateral runout. Before removing
the rotor, mark the rotor and hub/bearing to maintain
original orientation.
(1) Raise and support the vehicle.
(2) Remove wheel and tire assembly.
(3) Remove the caliper anchor bolts (Fig. 64) and
remove the caliper and anchor as an assembly from the
steering knuckle.
(4) Secure caliper anchor assembly to nearby suspen-
sion part with a wire.Do not allow brake hose to
support caliper weight.
(5) Mark the rotor and hub/bearing to maintain orig-
inal orientation. Remove retainers securing rotor to hub
studs.
(6) Remove rotor from hub/bearing.
REMOVAL - REAR DISC BRAKE ROTOR
(1) Raise and support the vehicle.
(2) Remove wheel and tire assembly.
(3) Remove the caliper anchor bolts (Fig. 65).
(4) Remove caliper and anchor as an assembly.(5) Secure caliper anchor assembly to nearby suspen-
sion part with wire.Do not allow brake hose to sup-
port caliper weight.
(6) Remove retainers securing rotor to axle studs.
(7) Remove rotor off axle studs.
Fig. 64 Caliper Anchor Bolts
1 - KNUCKLE
2 - ANCHOR
3 - ANCHOR BOLTS
4 - ROTOR
Fig. 65 Caliper Anchor Bolts
1 - ROTOR
2 - ANCHOR
3 - ANCHOR BOLTS
WJBRAKES - BASE 5 - 33
ROTORS (Continued)
2002 WJ Service Manual
Publication No. 81-370-02064
02WJ5-33 June, 2002