Page 649 of 2199
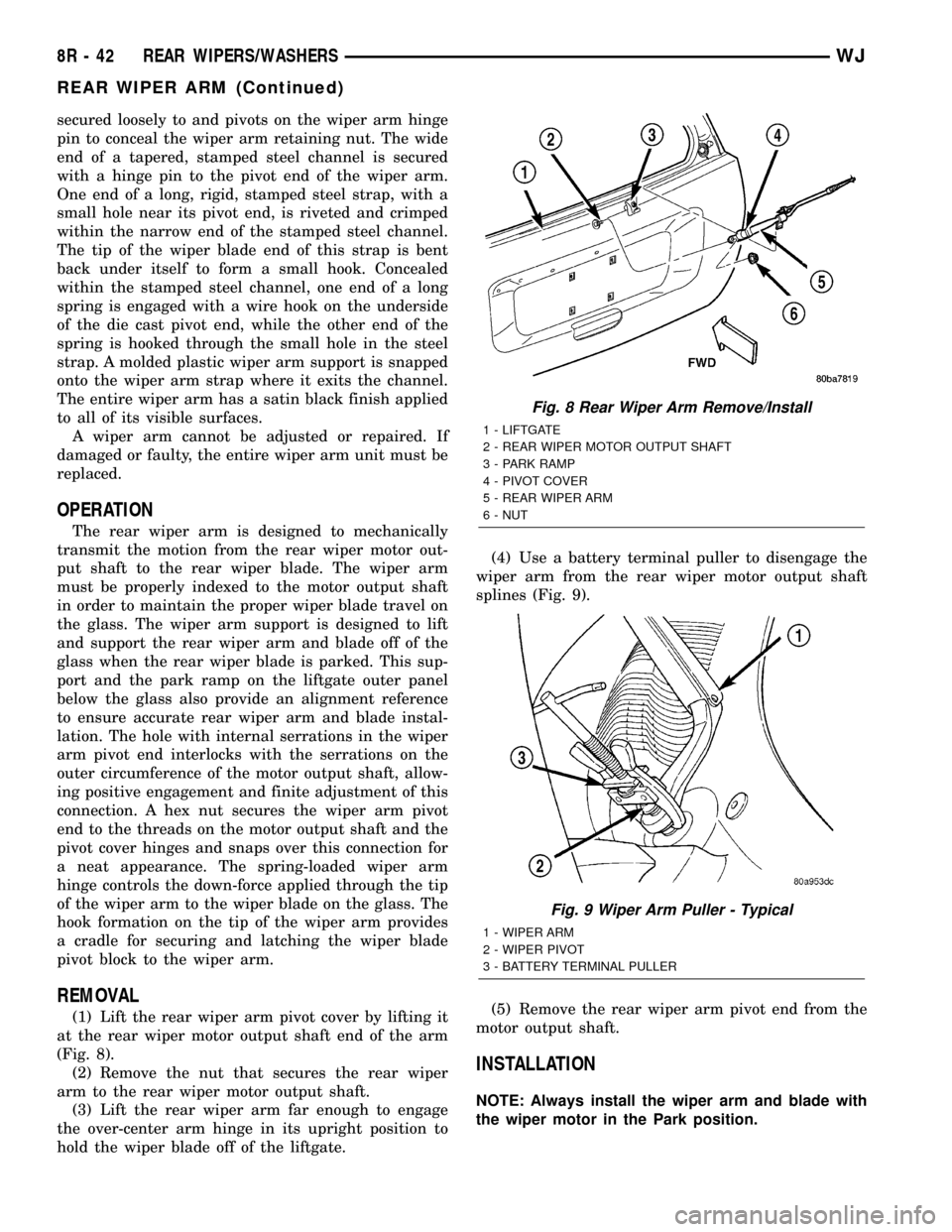
secured loosely to and pivots on the wiper arm hinge
pin to conceal the wiper arm retaining nut. The wide
end of a tapered, stamped steel channel is secured
with a hinge pin to the pivot end of the wiper arm.
One end of a long, rigid, stamped steel strap, with a
small hole near its pivot end, is riveted and crimped
within the narrow end of the stamped steel channel.
The tip of the wiper blade end of this strap is bent
back under itself to form a small hook. Concealed
within the stamped steel channel, one end of a long
spring is engaged with a wire hook on the underside
of the die cast pivot end, while the other end of the
spring is hooked through the small hole in the steel
strap. A molded plastic wiper arm support is snapped
onto the wiper arm strap where it exits the channel.
The entire wiper arm has a satin black finish applied
to all of its visible surfaces.
A wiper arm cannot be adjusted or repaired. If
damaged or faulty, the entire wiper arm unit must be
replaced.
OPERATION
The rear wiper arm is designed to mechanically
transmit the motion from the rear wiper motor out-
put shaft to the rear wiper blade. The wiper arm
must be properly indexed to the motor output shaft
in order to maintain the proper wiper blade travel on
the glass. The wiper arm support is designed to lift
and support the rear wiper arm and blade off of the
glass when the rear wiper blade is parked. This sup-
port and the park ramp on the liftgate outer panel
below the glass also provide an alignment reference
to ensure accurate rear wiper arm and blade instal-
lation. The hole with internal serrations in the wiper
arm pivot end interlocks with the serrations on the
outer circumference of the motor output shaft, allow-
ing positive engagement and finite adjustment of this
connection. A hex nut secures the wiper arm pivot
end to the threads on the motor output shaft and the
pivot cover hinges and snaps over this connection for
a neat appearance. The spring-loaded wiper arm
hinge controls the down-force applied through the tip
of the wiper arm to the wiper blade on the glass. The
hook formation on the tip of the wiper arm provides
a cradle for securing and latching the wiper blade
pivot block to the wiper arm.
REMOVAL
(1) Lift the rear wiper arm pivot cover by lifting it
at the rear wiper motor output shaft end of the arm
(Fig. 8).
(2) Remove the nut that secures the rear wiper
arm to the rear wiper motor output shaft.
(3) Lift the rear wiper arm far enough to engage
the over-center arm hinge in its upright position to
hold the wiper blade off of the liftgate.(4) Use a battery terminal puller to disengage the
wiper arm from the rear wiper motor output shaft
splines (Fig. 9).
(5) Remove the rear wiper arm pivot end from the
motor output shaft.
INSTALLATION
NOTE: Always install the wiper arm and blade with
the wiper motor in the Park position.
Fig. 8 Rear Wiper Arm Remove/Install
1 - LIFTGATE
2 - REAR WIPER MOTOR OUTPUT SHAFT
3 - PARK RAMP
4 - PIVOT COVER
5 - REAR WIPER ARM
6 - NUT
Fig. 9 Wiper Arm Puller - Typical
1 - WIPER ARM
2 - WIPER PIVOT
3 - BATTERY TERMINAL PULLER
8R - 42 REAR WIPERS/WASHERSWJ
REAR WIPER ARM (Continued)
Page 650 of 2199
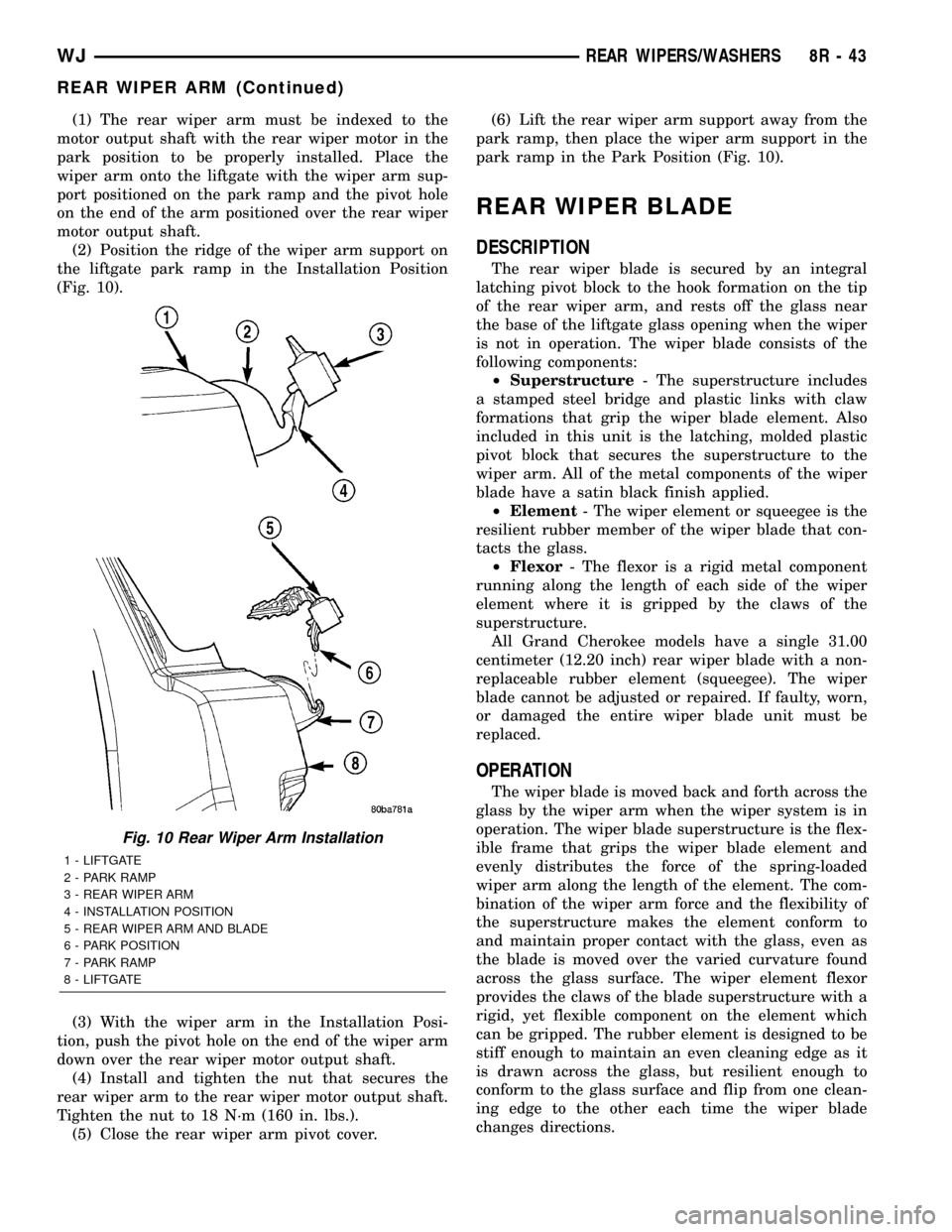
(1) The rear wiper arm must be indexed to the
motor output shaft with the rear wiper motor in the
park position to be properly installed. Place the
wiper arm onto the liftgate with the wiper arm sup-
port positioned on the park ramp and the pivot hole
on the end of the arm positioned over the rear wiper
motor output shaft.
(2) Position the ridge of the wiper arm support on
the liftgate park ramp in the Installation Position
(Fig. 10).
(3) With the wiper arm in the Installation Posi-
tion, push the pivot hole on the end of the wiper arm
down over the rear wiper motor output shaft.
(4) Install and tighten the nut that secures the
rear wiper arm to the rear wiper motor output shaft.
Tighten the nut to 18 N´m (160 in. lbs.).
(5) Close the rear wiper arm pivot cover.(6) Lift the rear wiper arm support away from the
park ramp, then place the wiper arm support in the
park ramp in the Park Position (Fig. 10).
REAR WIPER BLADE
DESCRIPTION
The rear wiper blade is secured by an integral
latching pivot block to the hook formation on the tip
of the rear wiper arm, and rests off the glass near
the base of the liftgate glass opening when the wiper
is not in operation. The wiper blade consists of the
following components:
²Superstructure- The superstructure includes
a stamped steel bridge and plastic links with claw
formations that grip the wiper blade element. Also
included in this unit is the latching, molded plastic
pivot block that secures the superstructure to the
wiper arm. All of the metal components of the wiper
blade have a satin black finish applied.
²Element- The wiper element or squeegee is the
resilient rubber member of the wiper blade that con-
tacts the glass.
²Flexor- The flexor is a rigid metal component
running along the length of each side of the wiper
element where it is gripped by the claws of the
superstructure.
All Grand Cherokee models have a single 31.00
centimeter (12.20 inch) rear wiper blade with a non-
replaceable rubber element (squeegee). The wiper
blade cannot be adjusted or repaired. If faulty, worn,
or damaged the entire wiper blade unit must be
replaced.
OPERATION
The wiper blade is moved back and forth across the
glass by the wiper arm when the wiper system is in
operation. The wiper blade superstructure is the flex-
ible frame that grips the wiper blade element and
evenly distributes the force of the spring-loaded
wiper arm along the length of the element. The com-
bination of the wiper arm force and the flexibility of
the superstructure makes the element conform to
and maintain proper contact with the glass, even as
the blade is moved over the varied curvature found
across the glass surface. The wiper element flexor
provides the claws of the blade superstructure with a
rigid, yet flexible component on the element which
can be gripped. The rubber element is designed to be
stiff enough to maintain an even cleaning edge as it
is drawn across the glass, but resilient enough to
conform to the glass surface and flip from one clean-
ing edge to the other each time the wiper blade
changes directions.
Fig. 10 Rear Wiper Arm Installation
1 - LIFTGATE
2 - PARK RAMP
3 - REAR WIPER ARM
4 - INSTALLATION POSITION
5 - REAR WIPER ARM AND BLADE
6 - PARK POSITION
7 - PARK RAMP
8 - LIFTGATE
WJREAR WIPERS/WASHERS 8R - 43
REAR WIPER ARM (Continued)
Page 651 of 2199
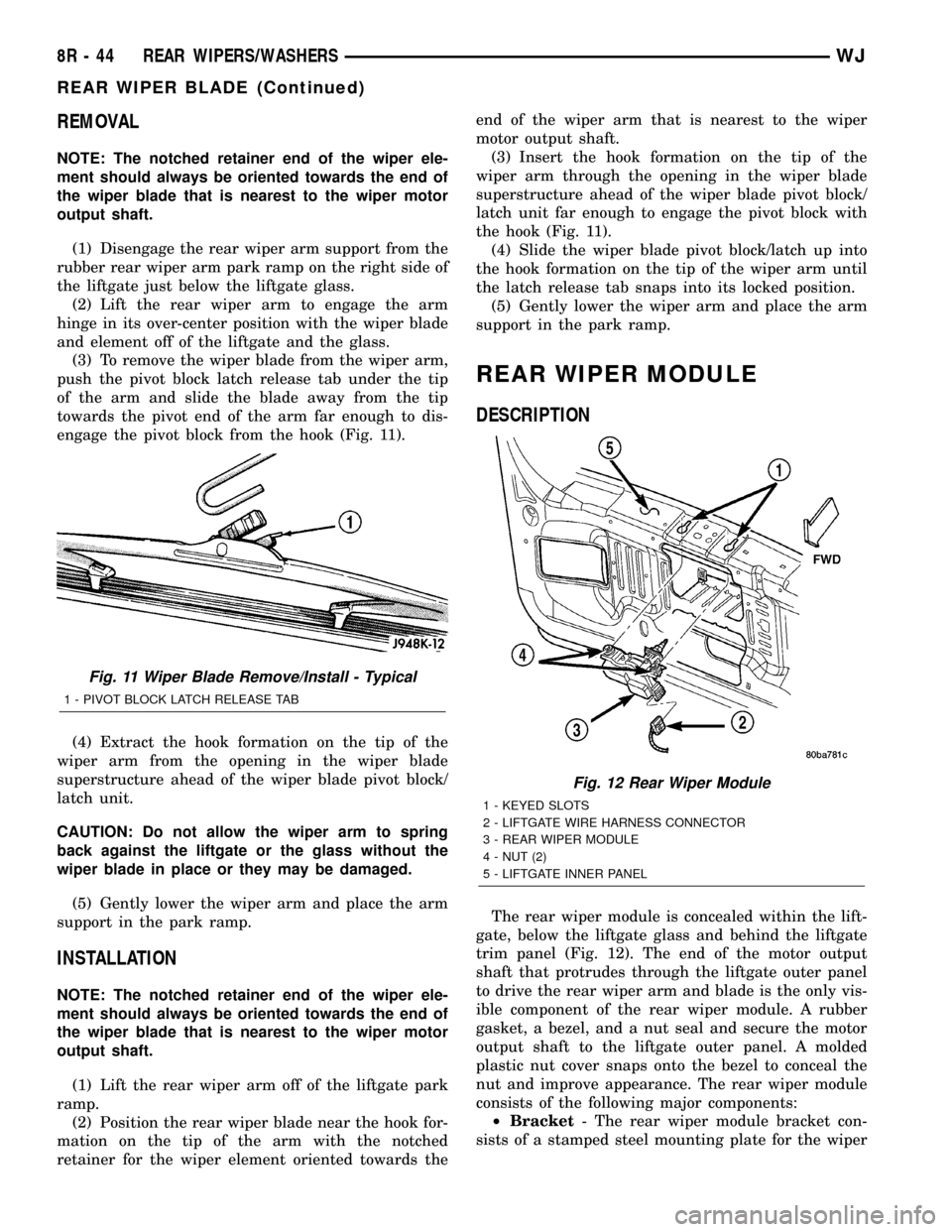
REMOVAL
NOTE: The notched retainer end of the wiper ele-
ment should always be oriented towards the end of
the wiper blade that is nearest to the wiper motor
output shaft.
(1) Disengage the rear wiper arm support from the
rubber rear wiper arm park ramp on the right side of
the liftgate just below the liftgate glass.
(2) Lift the rear wiper arm to engage the arm
hinge in its over-center position with the wiper blade
and element off of the liftgate and the glass.
(3) To remove the wiper blade from the wiper arm,
push the pivot block latch release tab under the tip
of the arm and slide the blade away from the tip
towards the pivot end of the arm far enough to dis-
engage the pivot block from the hook (Fig. 11).
(4) Extract the hook formation on the tip of the
wiper arm from the opening in the wiper blade
superstructure ahead of the wiper blade pivot block/
latch unit.
CAUTION: Do not allow the wiper arm to spring
back against the liftgate or the glass without the
wiper blade in place or they may be damaged.
(5) Gently lower the wiper arm and place the arm
support in the park ramp.
INSTALLATION
NOTE: The notched retainer end of the wiper ele-
ment should always be oriented towards the end of
the wiper blade that is nearest to the wiper motor
output shaft.
(1) Lift the rear wiper arm off of the liftgate park
ramp.
(2) Position the rear wiper blade near the hook for-
mation on the tip of the arm with the notched
retainer for the wiper element oriented towards theend of the wiper arm that is nearest to the wiper
motor output shaft.
(3) Insert the hook formation on the tip of the
wiper arm through the opening in the wiper blade
superstructure ahead of the wiper blade pivot block/
latch unit far enough to engage the pivot block with
the hook (Fig. 11).
(4) Slide the wiper blade pivot block/latch up into
the hook formation on the tip of the wiper arm until
the latch release tab snaps into its locked position.
(5) Gently lower the wiper arm and place the arm
support in the park ramp.
REAR WIPER MODULE
DESCRIPTION
The rear wiper module is concealed within the lift-
gate, below the liftgate glass and behind the liftgate
trim panel (Fig. 12). The end of the motor output
shaft that protrudes through the liftgate outer panel
to drive the rear wiper arm and blade is the only vis-
ible component of the rear wiper module. A rubber
gasket, a bezel, and a nut seal and secure the motor
output shaft to the liftgate outer panel. A molded
plastic nut cover snaps onto the bezel to conceal the
nut and improve appearance. The rear wiper module
consists of the following major components:
²Bracket- The rear wiper module bracket con-
sists of a stamped steel mounting plate for the wiper
Fig. 11 Wiper Blade Remove/Install - Typical
1 - PIVOT BLOCK LATCH RELEASE TAB
Fig. 12 Rear Wiper Module
1 - KEYED SLOTS
2 - LIFTGATE WIRE HARNESS CONNECTOR
3 - REAR WIPER MODULE
4 - NUT (2)
5 - LIFTGATE INNER PANEL
8R - 44 REAR WIPERS/WASHERSWJ
REAR WIPER BLADE (Continued)
Page 652 of 2199
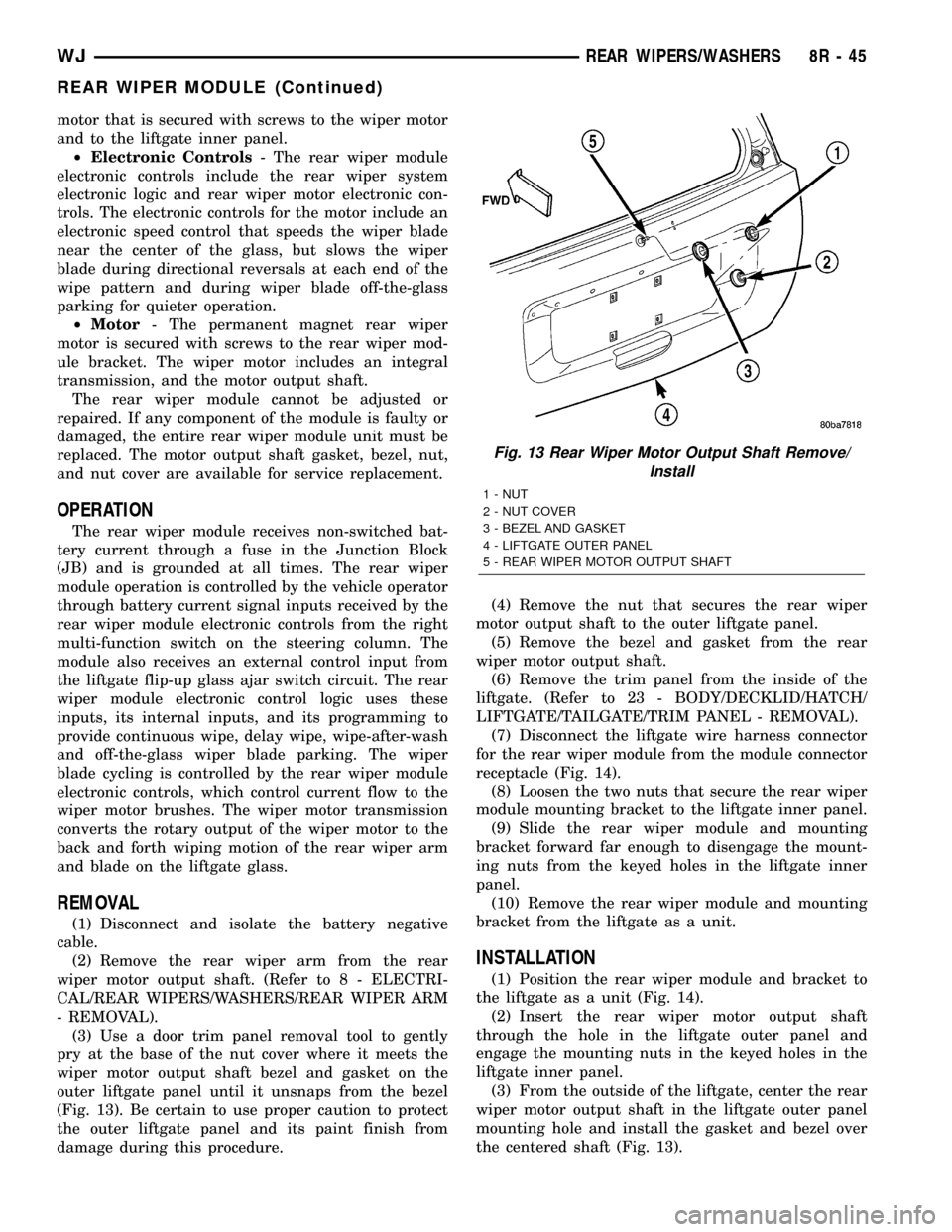
motor that is secured with screws to the wiper motor
and to the liftgate inner panel.
²Electronic Controls- The rear wiper module
electronic controls include the rear wiper system
electronic logic and rear wiper motor electronic con-
trols. The electronic controls for the motor include an
electronic speed control that speeds the wiper blade
near the center of the glass, but slows the wiper
blade during directional reversals at each end of the
wipe pattern and during wiper blade off-the-glass
parking for quieter operation.
²Motor- The permanent magnet rear wiper
motor is secured with screws to the rear wiper mod-
ule bracket. The wiper motor includes an integral
transmission, and the motor output shaft.
The rear wiper module cannot be adjusted or
repaired. If any component of the module is faulty or
damaged, the entire rear wiper module unit must be
replaced. The motor output shaft gasket, bezel, nut,
and nut cover are available for service replacement.
OPERATION
The rear wiper module receives non-switched bat-
tery current through a fuse in the Junction Block
(JB) and is grounded at all times. The rear wiper
module operation is controlled by the vehicle operator
through battery current signal inputs received by the
rear wiper module electronic controls from the right
multi-function switch on the steering column. The
module also receives an external control input from
the liftgate flip-up glass ajar switch circuit. The rear
wiper module electronic control logic uses these
inputs, its internal inputs, and its programming to
provide continuous wipe, delay wipe, wipe-after-wash
and off-the-glass wiper blade parking. The wiper
blade cycling is controlled by the rear wiper module
electronic controls, which control current flow to the
wiper motor brushes. The wiper motor transmission
converts the rotary output of the wiper motor to the
back and forth wiping motion of the rear wiper arm
and blade on the liftgate glass.
REMOVAL
(1) Disconnect and isolate the battery negative
cable.
(2) Remove the rear wiper arm from the rear
wiper motor output shaft. (Refer to 8 - ELECTRI-
CAL/REAR WIPERS/WASHERS/REAR WIPER ARM
- REMOVAL).
(3) Use a door trim panel removal tool to gently
pry at the base of the nut cover where it meets the
wiper motor output shaft bezel and gasket on the
outer liftgate panel until it unsnaps from the bezel
(Fig. 13). Be certain to use proper caution to protect
the outer liftgate panel and its paint finish from
damage during this procedure.(4) Remove the nut that secures the rear wiper
motor output shaft to the outer liftgate panel.
(5) Remove the bezel and gasket from the rear
wiper motor output shaft.
(6) Remove the trim panel from the inside of the
liftgate. (Refer to 23 - BODY/DECKLID/HATCH/
LIFTGATE/TAILGATE/TRIM PANEL - REMOVAL).
(7) Disconnect the liftgate wire harness connector
for the rear wiper module from the module connector
receptacle (Fig. 14).
(8) Loosen the two nuts that secure the rear wiper
module mounting bracket to the liftgate inner panel.
(9) Slide the rear wiper module and mounting
bracket forward far enough to disengage the mount-
ing nuts from the keyed holes in the liftgate inner
panel.
(10) Remove the rear wiper module and mounting
bracket from the liftgate as a unit.
INSTALLATION
(1) Position the rear wiper module and bracket to
the liftgate as a unit (Fig. 14).
(2) Insert the rear wiper motor output shaft
through the hole in the liftgate outer panel and
engage the mounting nuts in the keyed holes in the
liftgate inner panel.
(3) From the outside of the liftgate, center the rear
wiper motor output shaft in the liftgate outer panel
mounting hole and install the gasket and bezel over
the centered shaft (Fig. 13).
Fig. 13 Rear Wiper Motor Output Shaft Remove/
Install
1 - NUT
2 - NUT COVER
3 - BEZEL AND GASKET
4 - LIFTGATE OUTER PANEL
5 - REAR WIPER MOTOR OUTPUT SHAFT
WJREAR WIPERS/WASHERS 8R - 45
REAR WIPER MODULE (Continued)
Page 653 of 2199
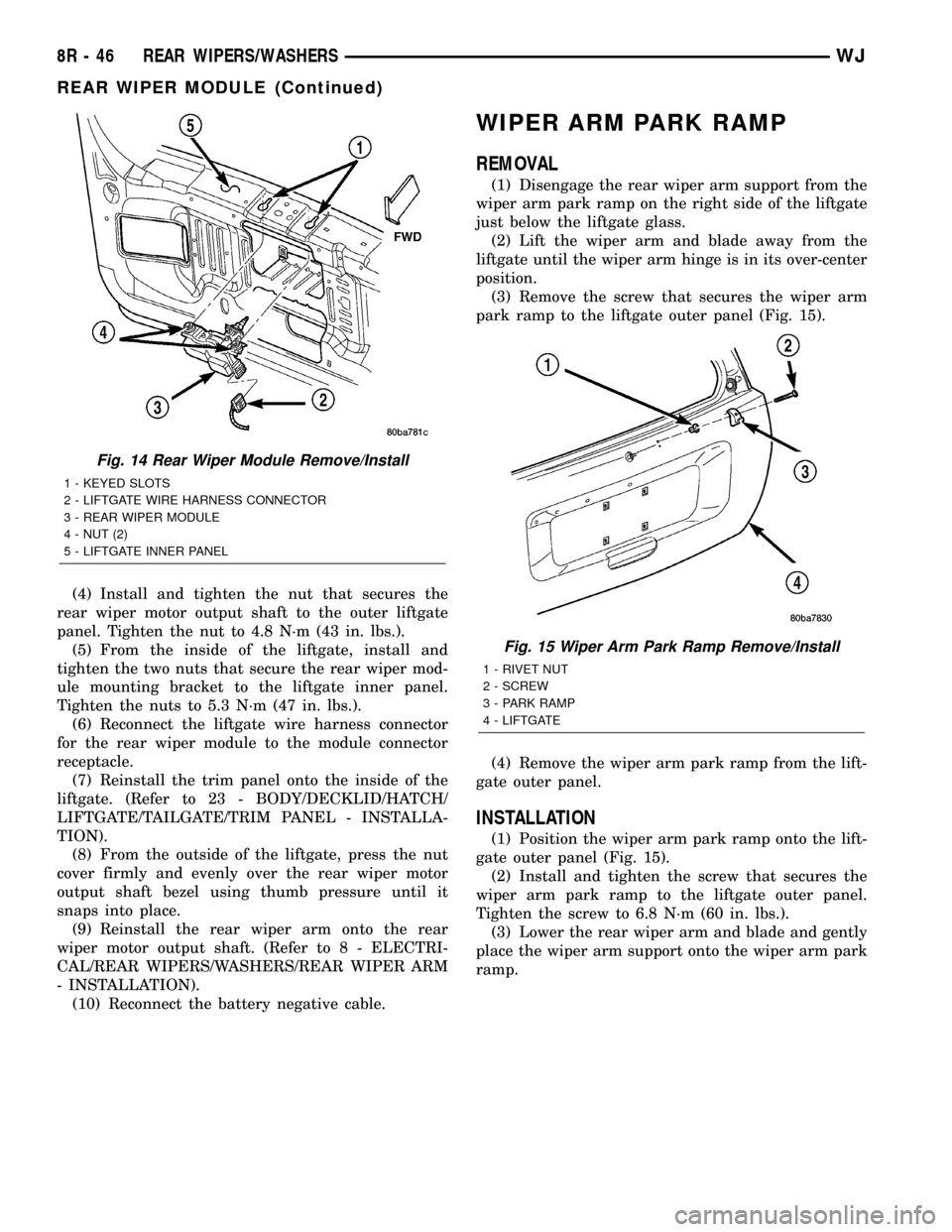
(4) Install and tighten the nut that secures the
rear wiper motor output shaft to the outer liftgate
panel. Tighten the nut to 4.8 N´m (43 in. lbs.).
(5) From the inside of the liftgate, install and
tighten the two nuts that secure the rear wiper mod-
ule mounting bracket to the liftgate inner panel.
Tighten the nuts to 5.3 N´m (47 in. lbs.).
(6) Reconnect the liftgate wire harness connector
for the rear wiper module to the module connector
receptacle.
(7) Reinstall the trim panel onto the inside of the
liftgate. (Refer to 23 - BODY/DECKLID/HATCH/
LIFTGATE/TAILGATE/TRIM PANEL - INSTALLA-
TION).
(8) From the outside of the liftgate, press the nut
cover firmly and evenly over the rear wiper motor
output shaft bezel using thumb pressure until it
snaps into place.
(9) Reinstall the rear wiper arm onto the rear
wiper motor output shaft. (Refer to 8 - ELECTRI-
CAL/REAR WIPERS/WASHERS/REAR WIPER ARM
- INSTALLATION).
(10) Reconnect the battery negative cable.
WIPER ARM PARK RAMP
REMOVAL
(1) Disengage the rear wiper arm support from the
wiper arm park ramp on the right side of the liftgate
just below the liftgate glass.
(2) Lift the wiper arm and blade away from the
liftgate until the wiper arm hinge is in its over-center
position.
(3) Remove the screw that secures the wiper arm
park ramp to the liftgate outer panel (Fig. 15).
(4) Remove the wiper arm park ramp from the lift-
gate outer panel.
INSTALLATION
(1) Position the wiper arm park ramp onto the lift-
gate outer panel (Fig. 15).
(2) Install and tighten the screw that secures the
wiper arm park ramp to the liftgate outer panel.
Tighten the screw to 6.8 N´m (60 in. lbs.).
(3) Lower the rear wiper arm and blade and gently
place the wiper arm support onto the wiper arm park
ramp.
Fig. 14 Rear Wiper Module Remove/Install
1 - KEYED SLOTS
2 - LIFTGATE WIRE HARNESS CONNECTOR
3 - REAR WIPER MODULE
4 - NUT (2)
5 - LIFTGATE INNER PANEL
Fig. 15 Wiper Arm Park Ramp Remove/Install
1 - RIVET NUT
2 - SCREW
3 - PARK RAMP
4 - LIFTGATE
8R - 46 REAR WIPERS/WASHERSWJ
REAR WIPER MODULE (Continued)
Page 654 of 2199
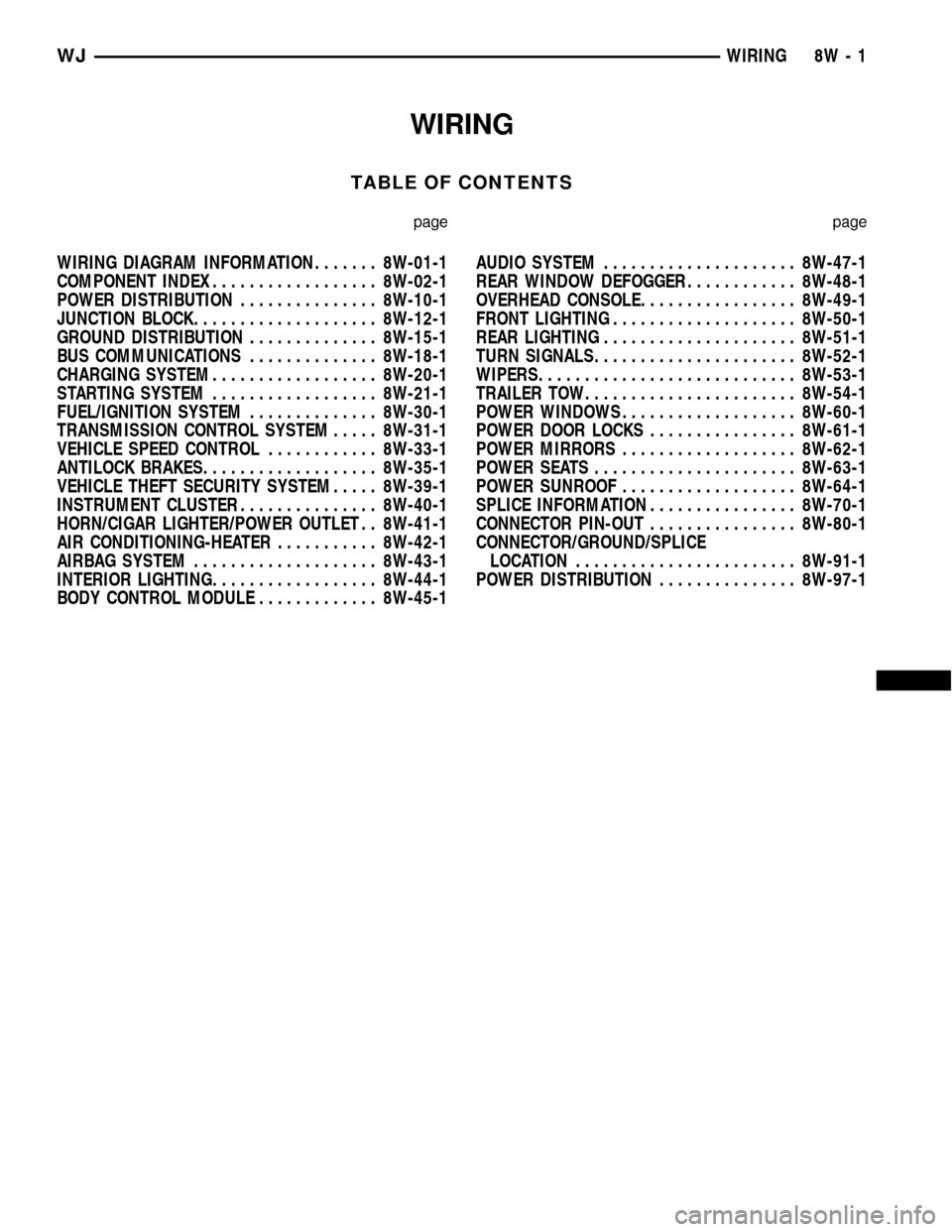
WIRING
TABLE OF CONTENTS
page page
WIRING DIAGRAM INFORMATION....... 8W-01-1
COMPONENT INDEX.................. 8W-02-1
POWER DISTRIBUTION............... 8W-10-1
JUNCTION BLOCK.................... 8W-12-1
GROUND DISTRIBUTION.............. 8W-15-1
BUS COMMUNICATIONS.............. 8W-18-1
CHARGING SYSTEM.................. 8W-20-1
STARTING SYSTEM.................. 8W-21-1
FUEL/IGNITION SYSTEM.............. 8W-30-1
TRANSMISSION CONTROL SYSTEM..... 8W-31-1
VEHICLE SPEED CONTROL............ 8W-33-1
ANTILOCK BRAKES................... 8W-35-1
VEHICLE THEFT SECURITY SYSTEM..... 8W-39-1
INSTRUMENT CLUSTER............... 8W-40-1
HORN/CIGAR LIGHTER/POWER OUTLET . . 8W-41-1
AIR CONDITIONING-HEATER........... 8W-42-1
AIRBAG SYSTEM.................... 8W-43-1
INTERIOR LIGHTING.................. 8W-44-1
BODY CONTROL MODULE............. 8W-45-1AUDIO SYSTEM..................... 8W-47-1
REAR WINDOW DEFOGGER............ 8W-48-1
OVERHEAD CONSOLE................. 8W-49-1
FRONT LIGHTING.................... 8W-50-1
REAR LIGHTING..................... 8W-51-1
TURN SIGNALS...................... 8W-52-1
WIPERS............................ 8W-53-1
TRAILER TOW....................... 8W-54-1
POWER WINDOWS................... 8W-60-1
POWER DOOR LOCKS................ 8W-61-1
POWER MIRRORS................... 8W-62-1
POWER SEATS...................... 8W-63-1
POWER SUNROOF................... 8W-64-1
SPLICE INFORMATION................ 8W-70-1
CONNECTOR PIN-OUT................ 8W-80-1
CONNECTOR/GROUND/SPLICE
LOCATION........................ 8W-91-1
POWER DISTRIBUTION............... 8W-97-1 WJWIRING 8W - 1
Page 655 of 2199
Page 656 of 2199
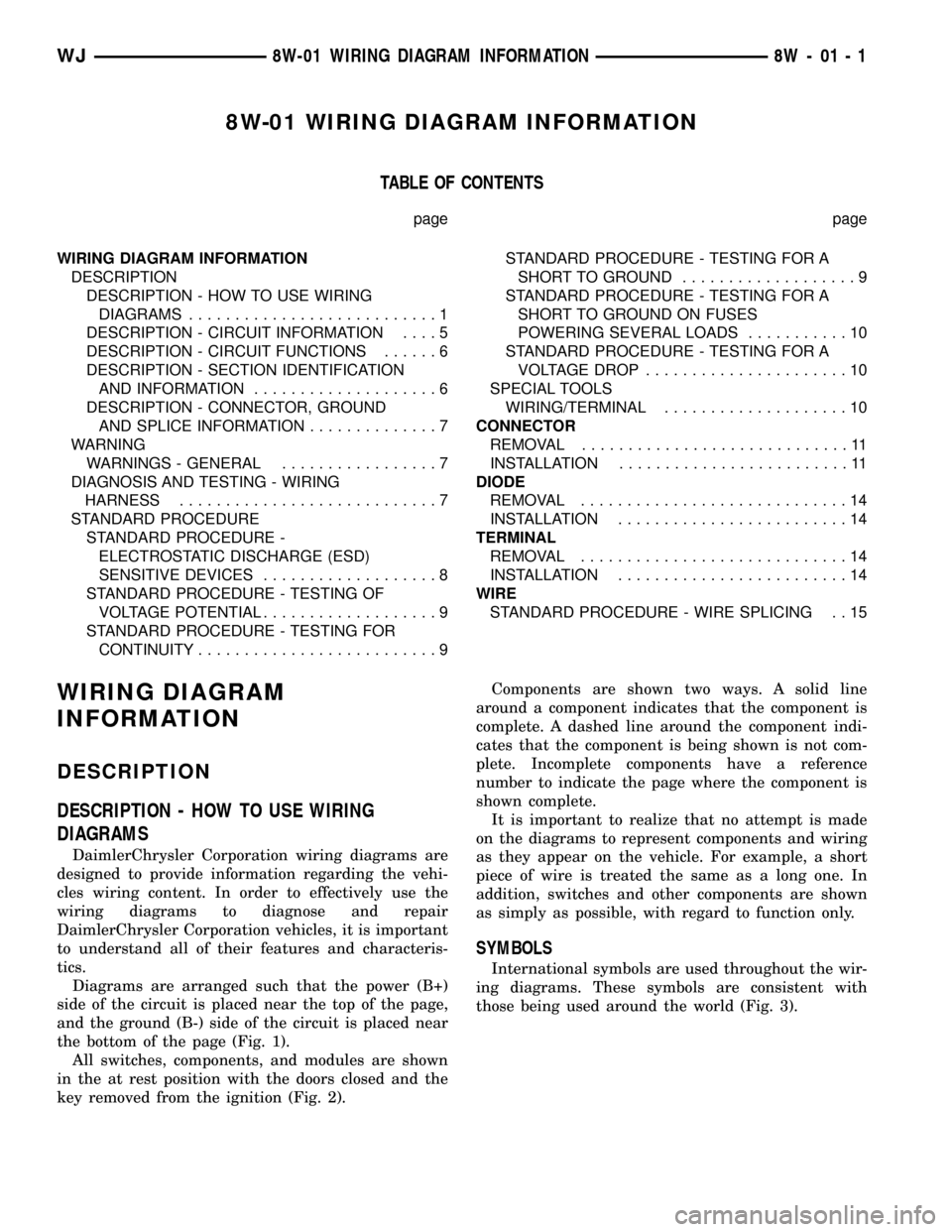
8W-01 WIRING DIAGRAM INFORMATION
TABLE OF CONTENTS
page page
WIRING DIAGRAM INFORMATION
DESCRIPTION
DESCRIPTION - HOW TO USE WIRING
DIAGRAMS...........................1
DESCRIPTION - CIRCUIT INFORMATION....5
DESCRIPTION - CIRCUIT FUNCTIONS......6
DESCRIPTION - SECTION IDENTIFICATION
AND INFORMATION....................6
DESCRIPTION - CONNECTOR, GROUND
AND SPLICE INFORMATION..............7
WARNING
WARNINGS - GENERAL.................7
DIAGNOSIS AND TESTING - WIRING
HARNESS............................7
STANDARD PROCEDURE
STANDARD PROCEDURE -
ELECTROSTATIC DISCHARGE (ESD)
SENSITIVE DEVICES...................8
STANDARD PROCEDURE - TESTING OF
VOLTAGE POTENTIAL...................9
STANDARD PROCEDURE - TESTING FOR
CONTINUITY..........................9STANDARD PROCEDURE - TESTING FOR A
SHORT TO GROUND...................9
STANDARD PROCEDURE - TESTING FOR A
SHORT TO GROUND ON FUSES
POWERING SEVERAL LOADS...........10
STANDARD PROCEDURE - TESTING FOR A
VOLTAGE DROP......................10
SPECIAL TOOLS
WIRING/TERMINAL....................10
CONNECTOR
REMOVAL.............................11
INSTALLATION.........................11
DIODE
REMOVAL.............................14
INSTALLATION.........................14
TERMINAL
REMOVAL.............................14
INSTALLATION.........................14
WIRE
STANDARD PROCEDURE - WIRE SPLICING . . 15
WIRING DIAGRAM
INFORMATION
DESCRIPTION
DESCRIPTION - HOW TO USE WIRING
DIAGRAMS
DaimlerChrysler Corporation wiring diagrams are
designed to provide information regarding the vehi-
cles wiring content. In order to effectively use the
wiring diagrams to diagnose and repair
DaimlerChrysler Corporation vehicles, it is important
to understand all of their features and characteris-
tics.
Diagrams are arranged such that the power (B+)
side of the circuit is placed near the top of the page,
and the ground (B-) side of the circuit is placed near
the bottom of the page (Fig. 1).
All switches, components, and modules are shown
in the at rest position with the doors closed and the
key removed from the ignition (Fig. 2).Components are shown two ways. A solid line
around a component indicates that the component is
complete. A dashed line around the component indi-
cates that the component is being shown is not com-
plete. Incomplete components have a reference
number to indicate the page where the component is
shown complete.
It is important to realize that no attempt is made
on the diagrams to represent components and wiring
as they appear on the vehicle. For example, a short
piece of wire is treated the same as a long one. In
addition, switches and other components are shown
as simply as possible, with regard to function only.
SYMBOLS
International symbols are used throughout the wir-
ing diagrams. These symbols are consistent with
those being used around the world (Fig. 3).
WJ8W-01 WIRING DIAGRAM INFORMATION 8W - 01 - 1