Page 49 of 2199

(3) Rotate the shaft until transmission/transfer
case output yoke bearing cap is facing downward, if
necessary.
NOTE: Always make measurements from front to rear.
(4)Place Inclinometer on yoke bearing cap, or the
pinion flange ring, (A) parallel to the shaft (Fig. 4). Cen-
ter bubble in sight glass and record measurement.
NOTE: This measurement will give you the trans-
mission or Output Yoke Angle (A).
(5) Rotate propeller shaft 90 degrees and place
Inclinometer on yoke bearing cap, or propeller shaft
tube on C/V propeller shaft, parallel to the shaft (Fig.
5). Center bubble in sight glass and record measure-
ment. This measurement can also be taken at the
rear end of the shaft.
NOTE: This measurement will give you the propeller
shaft angle (C).
(6) Subtract smaller figure from larger (C minus
A) to obtain transmission output operating angle.
(7) Rotate propeller shaft 90 degrees and place
Inclinometer on pinion yoke bearing cap parallel to
the shaft (Fig. 6). Center bubble in sight glass and
record measurement.
NOTE: This measurement will give you the pinion
shaft or input yoke angle (B).
(8) Subtract smaller figure from larger (C minus
B) to obtain axle Input Operating Angle.Refer to rules given below and the example in (Fig.
7) for additional information.
²Good cancellation of U-joint operating angles
(within 1É).
²Operating angles less than 3É.
²Operating angles less than 10É for double cardan
U-joint.
²At least 1/2 of one degree continuous operating
(propeller shaft) angle.
Fig. 4 OUTPUT YOKE ANGLE (A)
1 - SLIP YOKE BEARING CAP
2 - INCLINOMETER
Fig. 5 PROPELLER SHAFT ANGLE (C)
1 - SHAFT YOKE BEARING CAP
2 - INCLINOMETER
Fig. 6 INPUT YOKE ANGLE (B)
1 - PINION YOKE BEARING CAP
2 - INCLINOMETER
3 - 4 PROPELLER SHAFTWJ
PROPELLER SHAFT (Continued)
Page 50 of 2199
SPECIFICATIONS
TORQUE SPECIFICATIONS
DESCRIPTION N´m Ft. Lbs. In. Lbs.
Front Shaft - Companion Flange Bolts 32 24 -
4.7L Front Shaft - Axle Yoke Nuts 19 14 -
4.7L Front Shaft - Transfer Case Bolts 27 20 -
Rear Shaft - Yoke Nuts 19 14 -
SPECIAL TOOLS
Fig. 7 U-JOINT ANGLE EXAMPLE
1 - 4.9É Angle (C)
2 - 3.2É Angle (B)
3 - Input Yoke4 - 3.0É Angle (A)
5 - Output Yoke
Inclinometer 7663
WJPROPELLER SHAFT 3 - 5
PROPELLER SHAFT (Continued)
Page 51 of 2199

PROPELLER SHAFT - FRONT
REMOVAL
NOTE: Different length propeller shafts are used for
different drivetrain applications. Ensure that the
correct propeller shaft is used.
(1) Place vehicle on floor or drive-on hoist with full
weight of vehicle on suspension.
(2) Shift the transmission and transfer case, if nec-
essary, into the Neutral position.
(3) Measure the distance from the face of the C/V
joint cup to the end of the C/V joint boot (Fig. 8).
(4) The correct length is 142.7 mm (5.61 in.).
NOTE: If the measurement is not correct, the wrong
shaft may have been installed or a mating compo-
nent (front axle or transfer case) may be installed
incorrectly. Investigate and correct as necessary.
(5) Mark a line across the companion flange at the
transfer case and C/V joint at the rear of the front
propeller shaft for installation reference.
(6) Mark a line across the C/V joints and the pin-
ion companion flanges for installation reference.
(7) Remove bolts from the front C/V joint to the
pinion companion flange.
(8) Remove bolts from the rear C/V joint to the
transfer case companion flange.
(9) Push the propeller shaft forward to clear trans-
fer case companion flange and remove the shaft.
INSTALLATION
NOTE: Different length propeller shafts are used for
different drivetrain applications. Ensure that the
correct propeller shaft is used.
(1) Install the shaft between companion flanges.
(2) The shaft should rotate freely in the pinion
flange.
(3) Align marks on the companion flanges with the
marks on the C/V joints.
(4) Install bolts to the front C/V joint and tighten
bolts to 32 N´m (24 ft. lbs.).
(5) Install the bolts to the rear C/V joint and
tighten bolts to 32 N´m (24 ft. lbs.).
(6) Verify propeller shaft length.
(7) Lower vehicle.
PROPELLER SHAFT - FRONT
4.7L
REMOVAL
(1) Raise and support vehicle.
(2) Remove crossmember/skid plate as necessary to
gain access to the propeller shaft.
(3) Shift transmission and transfer case, if neces-
sary into Neutral.
(4) Mark a line across the yoke at the transfer
case, link yoke and propeller shaft yoke at the rear of
the front propeller shaft for installation reference
(Fig. 9).
(5) Mark a line across the propeller shaft yoke and
pinion shaft yoke for installation reference.
Fig. 8 MEASUREMENT
1 - C/V JOINT CUP
2 - C/V BOOT END
3 - MEASUREMENT
Fig. 9 REFERENCE MARKS ON YOKES
1 - REFERENCE MARKS
3 - 6 PROPELLER SHAFTWJ
Page 52 of 2199
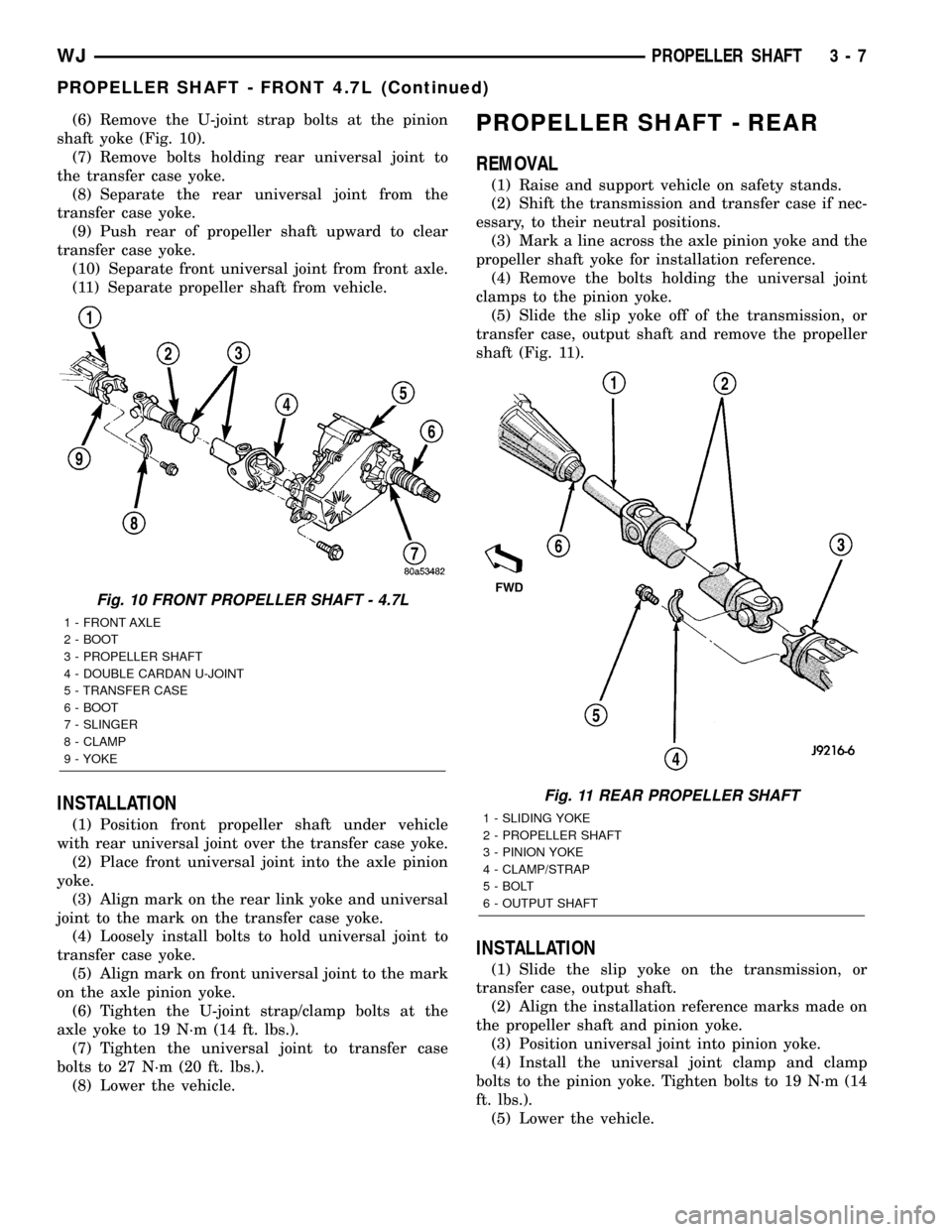
(6) Remove the U-joint strap bolts at the pinion
shaft yoke (Fig. 10).
(7) Remove bolts holding rear universal joint to
the transfer case yoke.
(8) Separate the rear universal joint from the
transfer case yoke.
(9) Push rear of propeller shaft upward to clear
transfer case yoke.
(10) Separate front universal joint from front axle.
(11) Separate propeller shaft from vehicle.
INSTALLATION
(1) Position front propeller shaft under vehicle
with rear universal joint over the transfer case yoke.
(2) Place front universal joint into the axle pinion
yoke.
(3) Align mark on the rear link yoke and universal
joint to the mark on the transfer case yoke.
(4) Loosely install bolts to hold universal joint to
transfer case yoke.
(5) Align mark on front universal joint to the mark
on the axle pinion yoke.
(6) Tighten the U-joint strap/clamp bolts at the
axle yoke to 19 N´m (14 ft. lbs.).
(7) Tighten the universal joint to transfer case
bolts to 27 N´m (20 ft. lbs.).
(8) Lower the vehicle.
PROPELLER SHAFT - REAR
REMOVAL
(1) Raise and support vehicle on safety stands.
(2) Shift the transmission and transfer case if nec-
essary, to their neutral positions.
(3) Mark a line across the axle pinion yoke and the
propeller shaft yoke for installation reference.
(4) Remove the bolts holding the universal joint
clamps to the pinion yoke.
(5) Slide the slip yoke off of the transmission, or
transfer case, output shaft and remove the propeller
shaft (Fig. 11).
INSTALLATION
(1) Slide the slip yoke on the transmission, or
transfer case, output shaft.
(2) Align the installation reference marks made on
the propeller shaft and pinion yoke.
(3) Position universal joint into pinion yoke.
(4) Install the universal joint clamp and clamp
bolts to the pinion yoke. Tighten bolts to 19 N´m (14
ft. lbs.).
(5) Lower the vehicle.
Fig. 10 FRONT PROPELLER SHAFT - 4.7L
1 - FRONT AXLE
2 - BOOT
3 - PROPELLER SHAFT
4 - DOUBLE CARDAN U-JOINT
5 - TRANSFER CASE
6 - BOOT
7 - SLINGER
8 - CLAMP
9 - YOKE
Fig. 11 REAR PROPELLER SHAFT
1 - SLIDING YOKE
2 - PROPELLER SHAFT
3 - PINION YOKE
4 - CLAMP/STRAP
5 - BOLT
6 - OUTPUT SHAFT
WJPROPELLER SHAFT 3 - 7
PROPELLER SHAFT - FRONT 4.7L (Continued)
Page 53 of 2199
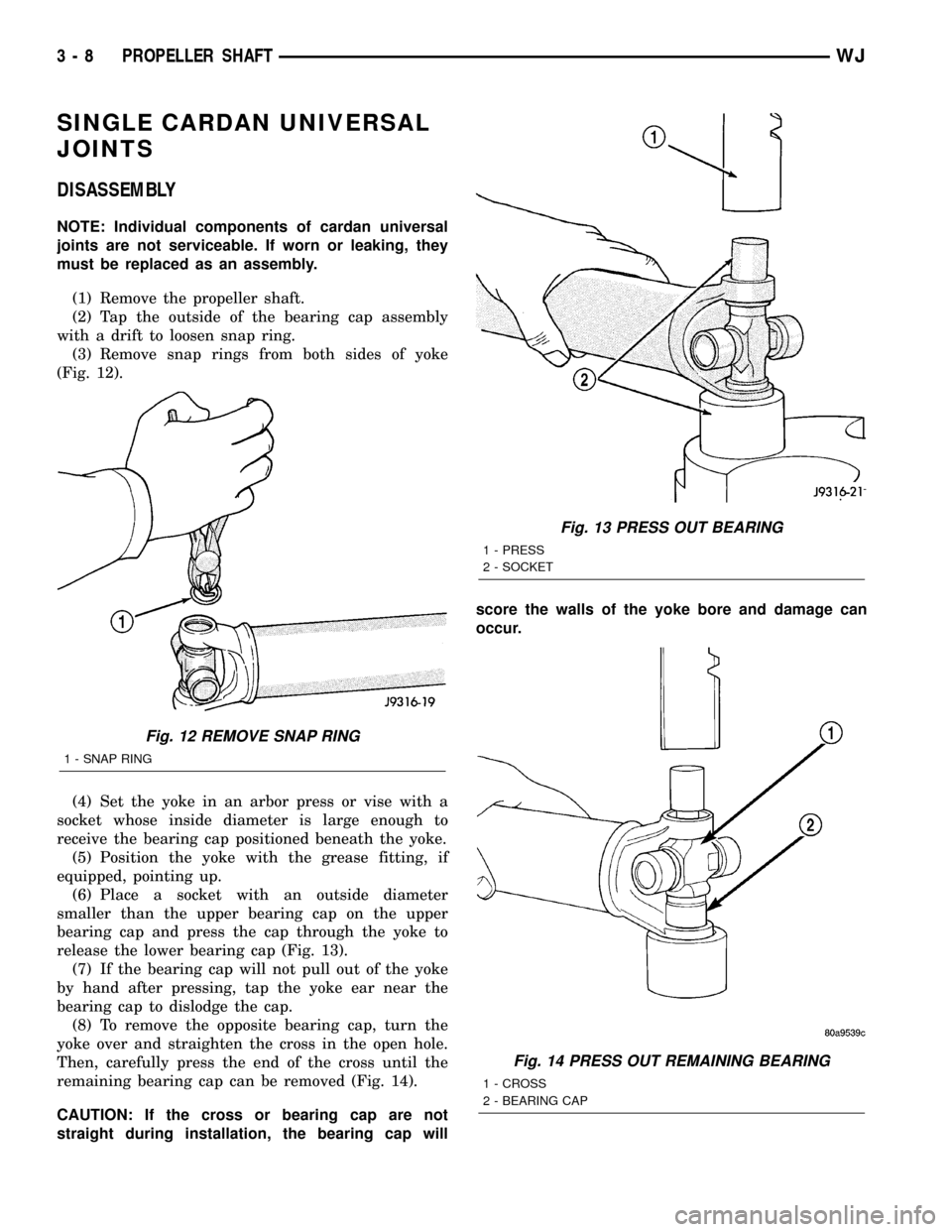
SINGLE CARDAN UNIVERSAL
JOINTS
DISASSEMBLY
NOTE: Individual components of cardan universal
joints are not serviceable. If worn or leaking, they
must be replaced as an assembly.
(1) Remove the propeller shaft.
(2) Tap the outside of the bearing cap assembly
with a drift to loosen snap ring.
(3) Remove snap rings from both sides of yoke
(Fig. 12).
(4) Set the yoke in an arbor press or vise with a
socket whose inside diameter is large enough to
receive the bearing cap positioned beneath the yoke.
(5) Position the yoke with the grease fitting, if
equipped, pointing up.
(6) Place a socket with an outside diameter
smaller than the upper bearing cap on the upper
bearing cap and press the cap through the yoke to
release the lower bearing cap (Fig. 13).
(7) If the bearing cap will not pull out of the yoke
by hand after pressing, tap the yoke ear near the
bearing cap to dislodge the cap.
(8) To remove the opposite bearing cap, turn the
yoke over and straighten the cross in the open hole.
Then, carefully press the end of the cross until the
remaining bearing cap can be removed (Fig. 14).
CAUTION: If the cross or bearing cap are not
straight during installation, the bearing cap willscore the walls of the yoke bore and damage can
occur.
Fig. 12 REMOVE SNAP RING
1 - SNAP RING
Fig. 13 PRESS OUT BEARING
1 - PRESS
2 - SOCKET
Fig. 14 PRESS OUT REMAINING BEARING
1 - CROSS
2 - BEARING CAP
3 - 8 PROPELLER SHAFTWJ
Page 54 of 2199
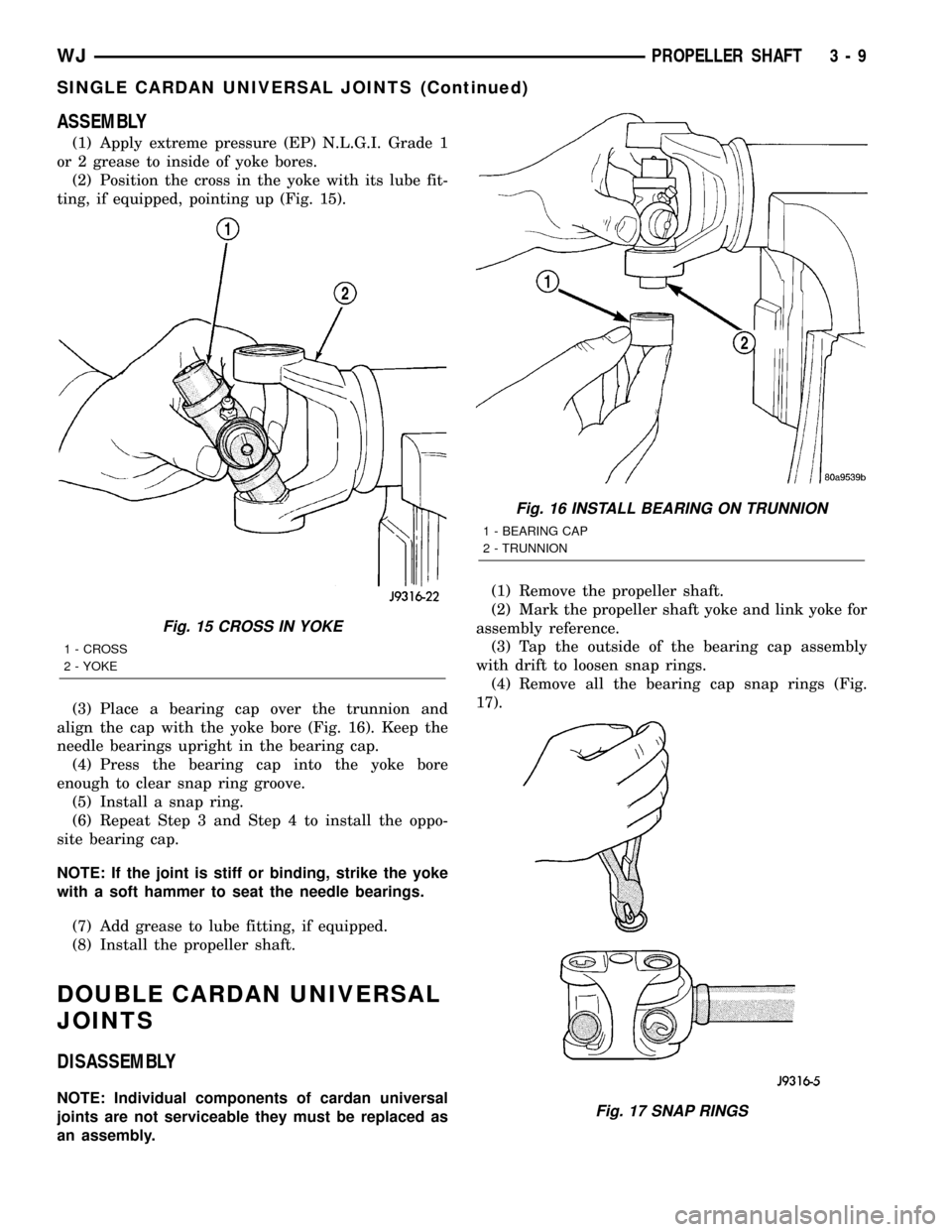
ASSEMBLY
(1) Apply extreme pressure (EP) N.L.G.I. Grade 1
or 2 grease to inside of yoke bores.
(2) Position the cross in the yoke with its lube fit-
ting, if equipped, pointing up (Fig. 15).
(3) Place a bearing cap over the trunnion and
align the cap with the yoke bore (Fig. 16). Keep the
needle bearings upright in the bearing cap.
(4) Press the bearing cap into the yoke bore
enough to clear snap ring groove.
(5) Install a snap ring.
(6) Repeat Step 3 and Step 4 to install the oppo-
site bearing cap.
NOTE: If the joint is stiff or binding, strike the yoke
with a soft hammer to seat the needle bearings.
(7) Add grease to lube fitting, if equipped.
(8) Install the propeller shaft.
DOUBLE CARDAN UNIVERSAL
JOINTS
DISASSEMBLY
NOTE: Individual components of cardan universal
joints are not serviceable they must be replaced as
an assembly.(1) Remove the propeller shaft.
(2) Mark the propeller shaft yoke and link yoke for
assembly reference.
(3) Tap the outside of the bearing cap assembly
with drift to loosen snap rings.
(4) Remove all the bearing cap snap rings (Fig.
17).
Fig. 15 CROSS IN YOKE
1 - CROSS
2 - YOKE
Fig. 16 INSTALL BEARING ON TRUNNION
1 - BEARING CAP
2 - TRUNNION
Fig. 17 SNAP RINGS
WJPROPELLER SHAFT 3 - 9
SINGLE CARDAN UNIVERSAL JOINTS (Continued)
Page 55 of 2199
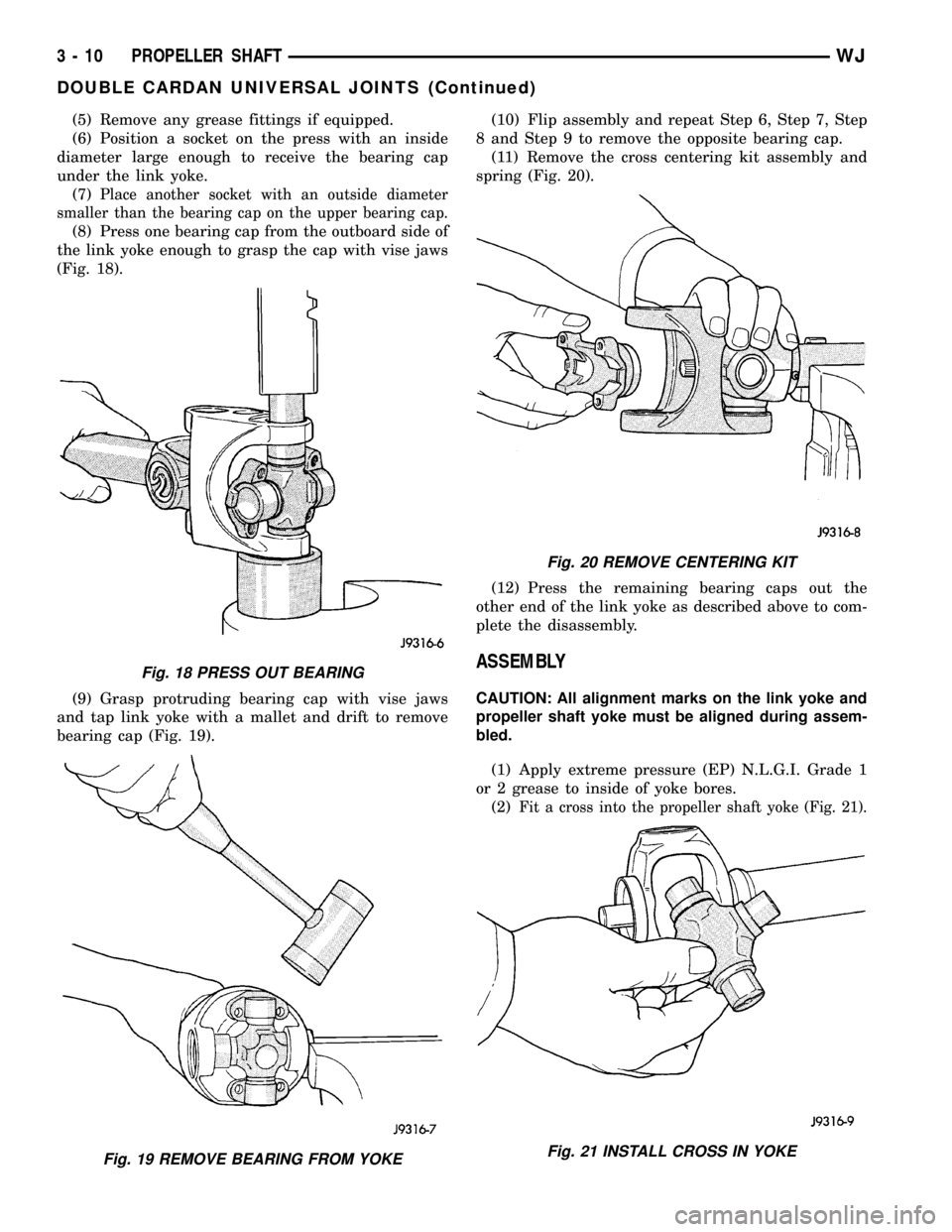
(5) Remove any grease fittings if equipped.
(6) Position a socket on the press with an inside
diameter large enough to receive the bearing cap
under the link yoke.
(7)
Place another socket with an outside diameter
smaller than the bearing cap on the upper bearing cap.
(8) Press one bearing cap from the outboard side of
the link yoke enough to grasp the cap with vise jaws
(Fig. 18).
(9) Grasp protruding bearing cap with vise jaws
and tap link yoke with a mallet and drift to remove
bearing cap (Fig. 19).(10) Flip assembly and repeat Step 6, Step 7, Step
8 and Step 9 to remove the opposite bearing cap.
(11) Remove the cross centering kit assembly and
spring (Fig. 20).
(12) Press the remaining bearing caps out the
other end of the link yoke as described above to com-
plete the disassembly.
ASSEMBLY
CAUTION: All alignment marks on the link yoke and
propeller shaft yoke must be aligned during assem-
bled.
(1) Apply extreme pressure (EP) N.L.G.I. Grade 1
or 2 grease to inside of yoke bores.
(2)
Fit a cross into the propeller shaft yoke (Fig. 21).
Fig. 18 PRESS OUT BEARING
Fig. 19 REMOVE BEARING FROM YOKE
Fig. 20 REMOVE CENTERING KIT
Fig. 21 INSTALL CROSS IN YOKE
3 - 10 PROPELLER SHAFTWJ
DOUBLE CARDAN UNIVERSAL JOINTS (Continued)
Page 56 of 2199
(3) Place a bearing cap over the trunnion and
align the cap with the yoke bore (Fig. 22). Keep nee-
dle bearings upright in the bearing cap.
(4) Press bearing cap into the yoke bore enough to
clear snap ring groove (Fig. 23).
(5) Install a snap ring.(6) Flip propeller shaft yoke and install other bear-
ing cap onto the opposite trunnion and install a snap
ring (Fig. 24).
(7) Fit the link yoke onto the remaining trunnions
and press both bearing caps into place and install
snap rings (Fig. 25).
Fig. 22 INSTALL BEARING CAP
Fig. 23 PRESS BEARING CAP
Fig. 24 PRESS BEARING CAP
Fig. 25 INSTALL LINK YOKE
WJPROPELLER SHAFT 3 - 11
DOUBLE CARDAN UNIVERSAL JOINTS (Continued)