Page 1249 of 1708
Page 1250 of 1708
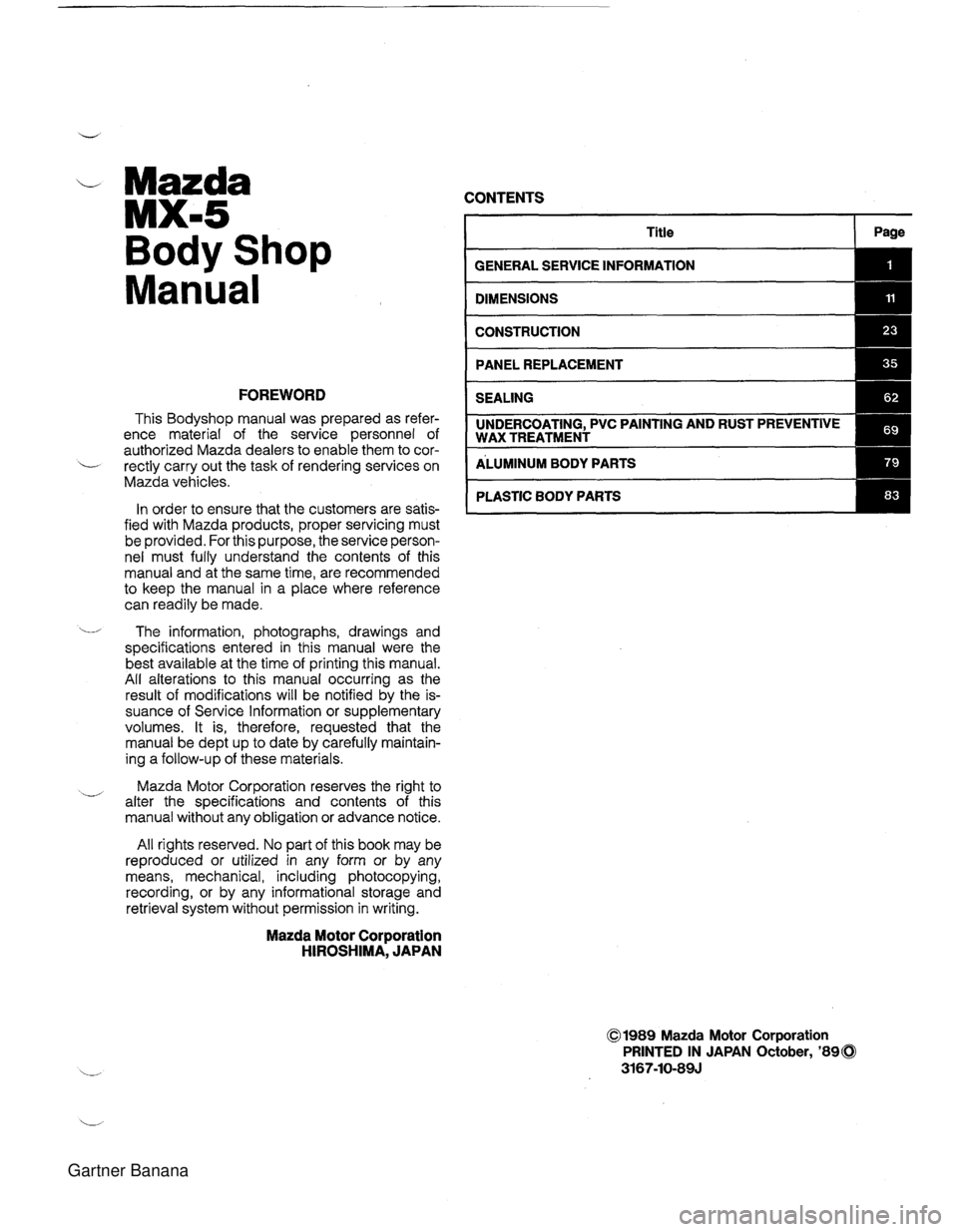
Mazda MX-5 Body Shop Manual - FOREWORD This Bodyshop manual was prepared as refer- ence material of the service personnel of authorized Mazda dealers to enable them to cor- L- rectly carry out the task of rendering services on Mazda vehicles. In order to ensure that the customers are satis- fied with Mazda products, proper servicing must be provided. For this purpose, the service person- nel must fully understand the contents of this manual and at the same time, are recommended to keep the manual in a place where reference can readily be made. CONTENTS i- The information, photographs, drawings and specifications entered in this manual were the best available at the time of printing this manual. All alterations to this manual occurring as the result of modifications will be notified by the is- suance of Service Information or supplementary volumes. It is, therefore, requested that the manual be dept up to date by carefully maintain- ing a follow-up of these materials. Title -W Mazda Motor Corporation reserves the right to alter the specifications and contents of this manual without any obligation or advance notice. Page All rights reserved. No part of this book may be reproduced or utilized in any form or by any means, mechanical, including photocopying, recording, or by any informational storage and retrieval system without permission in writing. Mazda Motor Corporation HIROSHIMA, JAPAN 01989 Mazda Motor Corporation PRINTED IN JAPAN October, '890 3167-10-89J Gartner Banana
Page 1251 of 1708
GENERAL SERVICE INFORMATION SERVICE PRECAUTIONS ............................................ 2 JACKING AND SAFETY STAND POSITIONS ............ 8 VEHICLE LIFT (2-SUPPORT TYPE) POSITIONS ....... 8 TOW CABLE ATTACHMENT POSITIONS .................. 9 IDENTIFICATION NUMBER LOCATIONS ................... 9 VEHICLE DIMENSIONS ................................................ 10 WHEEL ALIGNMENT .................................................... 10 Gartner Banana
Page 1252 of 1708
GENERAL SERVICE INFORMATION V SERVICE PRECAUTIONS V Arrangement of workshop Vehicle protection Arrangement of workshop is important for safe 1. Use seat covers and floor covers. and efficient work. 2. Use heat-resistant protective covers to protect glass areas and seats from heat or sparks during welding. 3. Protect items such as moldings, garnishes, ornaments, with tape when welding. Use of pulling equipment When using pulling equipment, keep away from the pulling area and use safety wires to prevent accidents. Gartner Banana
Page 1253 of 1708
GENERAL SERVICE INFORMATION './ SERVICE PRECAUTIONS Safety precautions Safety Protective head covering and safety shoes The fuel tank must be removed if welding is to should always be worn. Depending upon the be done near it or if an open flame is to be nature of the work, gloves, safety glasses, ear brought near it. protectors, face shield, etc., should also be The connection piping must be plugged to used. -, prevent fuel leakage. Mask C_i Before removing a wire harness or an electri- cal component, disconnect the negative bat- tery cable. Gartner Banana
Page 1254 of 1708
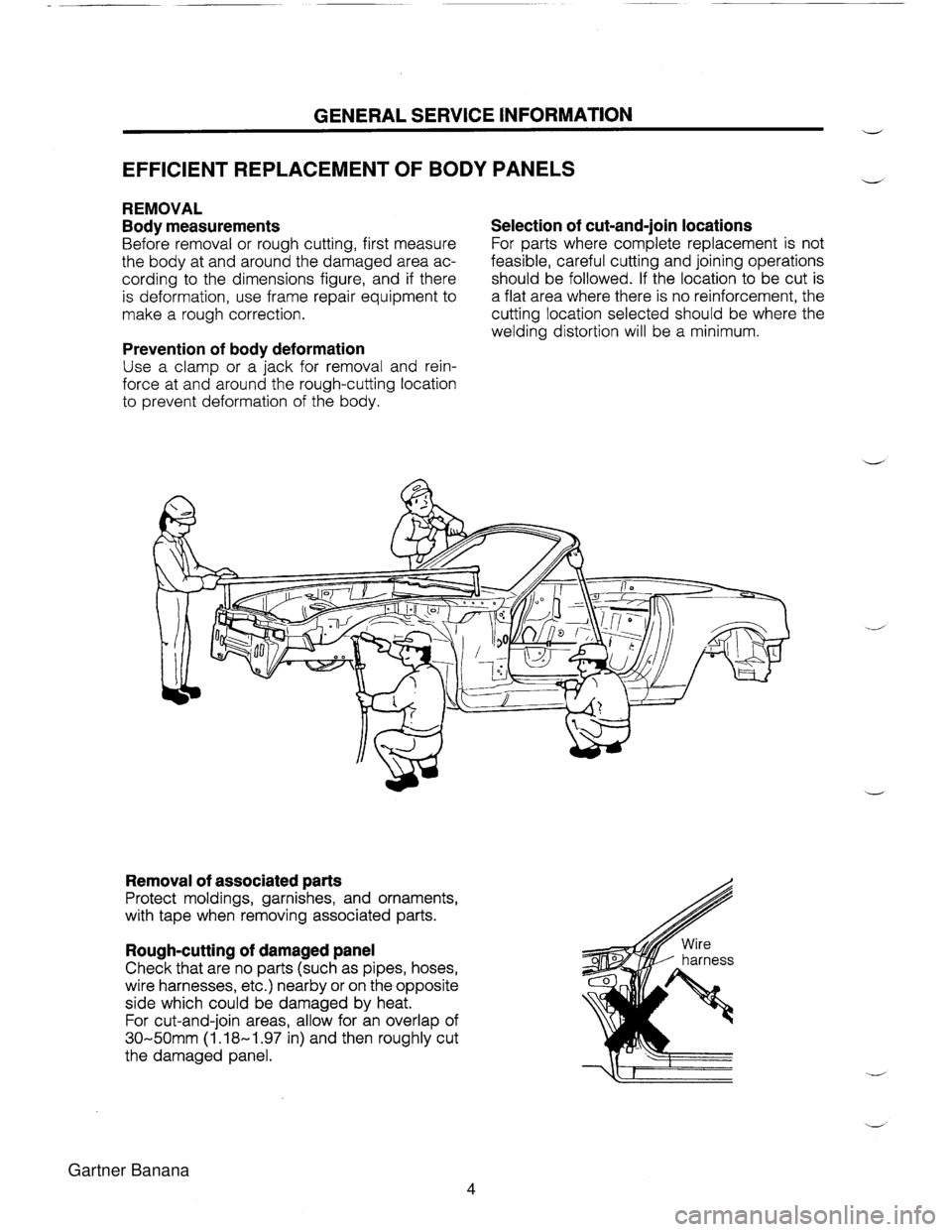
GENERAL SERVICE INFORMATION w EFFICIENT REPLACEMENT OF BODY PANELS V REMOVAL Body measurements Selection of cut-and-join locations Before removal or rough cutting, first measure For parts where complete replacement is not the body at and around the damaged area ac- feasible, careful cutting and joining operations cording to the dimensions figure, and if there should be followed. If the location to be cut is is deformation, use frame repair equipment to a flat area where there is no reinforcement, the make a rough correction. cutting location selected should be where the welding distortion will be a minimum. Prevention of body deformation Use a clamp or a jack for removal and rein- force at and around the rough-cutting location to prevent deformation of the body. Removal of associated parts Protect moldings, garnishes, and ornaments, with tape when removing associated parts. Rough-cutting of damaged panel Check that are no parts (such as pipes, hoses, wire harnesses, etc.) nearby or on the opposite side which could be damaged by heat. For cut-and-join areas, allow for an overlap of 30-50mm (1.18-1.97 in) and then roughly cut the damaged panel. Gartner Banana
Page 1255 of 1708
u GENERAL SERVICE INFORMATION INSTALLATION PREPARATIONS Application of weld-through primer 1 For treatment against cor- rosion, remove paint, grease, and other material from tl ,portion of the new part and body to be welded, and apply weld- Determination of welding method If the total thickness at the area to be welded is 3mm (0.12 in) or more, use a drill to make holes of about 07 for plug welding, then use a CO2 gas shielded-arc welder to make the plug welds. Note Do not attempt to spot weld sections over 3mm (0.12 in) thick, as the weld strength would be too low. or less Making holes for plug-welding Rough cutting of new parts For places that cannot be spot welded, make For cut-and-join areas, allow for an overlap of a hole of 05-06 (at the new part of the body 30-50mm (1.18-1.97 in) and then roughly cut side) using a punch or drill. the new part, using a hand saw or air saw as necessary. 30-50mm (1.18-1.97 in) (1.18-1.97 in) overlap Gartner Banana
Page 1256 of 1708
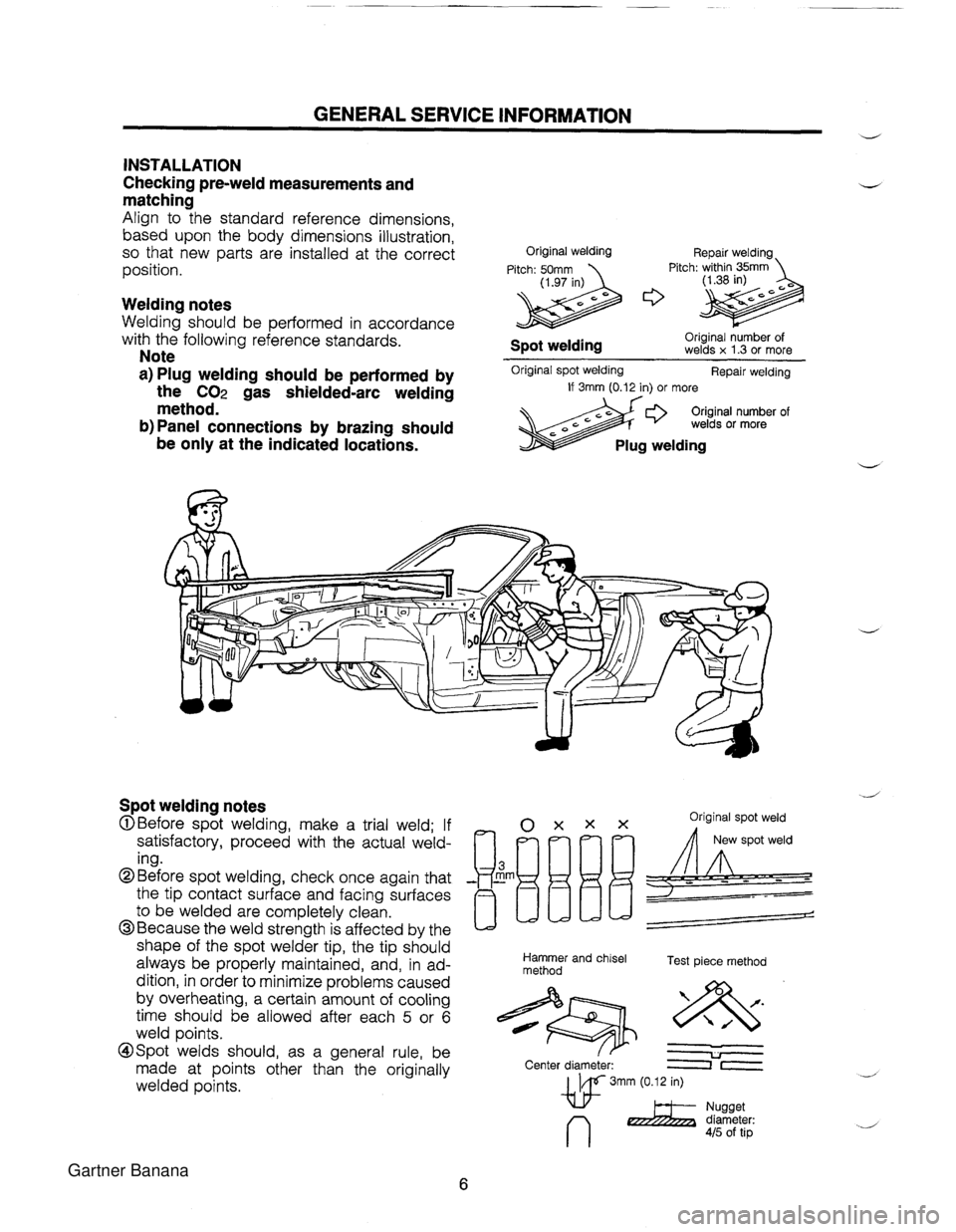
GENERAL SERVICE INFORMATION d INSTALLATION Checking pre-weld measurements and matching Align to the standard reference dimensions, based upon the body dimensions illustration, so that new parts are installed at the correct position. Welding notes Welding should be performed in accordance with the following reference standards. Note a) Plug welding should be performed by the CO2 gas shielded-arc welding method. b) Panel connections by brazing should be only at the indicated locations. Original welding Repair welding Pitch: 50mm Pitch: within 35mm (1.97 in) Original number of Spot welding welds x 1.3 or more Original spot welding Repair welding If 3rnm (0.12 in) or more Original number of welds or more Plug welding Spot welding notes OXXX Original spot weld @Before spot welding, make a trial weld; If satisfactory, proceed with the actual weld- ing. the tip contact surface and facing surfaces ~~[l/jLJL!= @Before spot welding, check once again that - Em -- to be welded are completely clean. @Because the weld strength is affected by the / shape of the spot welder tip, the tip should always be properly maintained, and, in ad- Hammer and chisel Test piece method method dition, in order to minimize problems caused by overheating, a certain amount of cooling time should be allowed after each 5 or 6 weld points. @Spot welds should, as a general rule, be & U made at points other than the originally Center diameter: lr welded points. w 3mm (0.12 in) n 2 Yi'%%Lr: 415 of tip Gartner Banana