Page 129 of 425
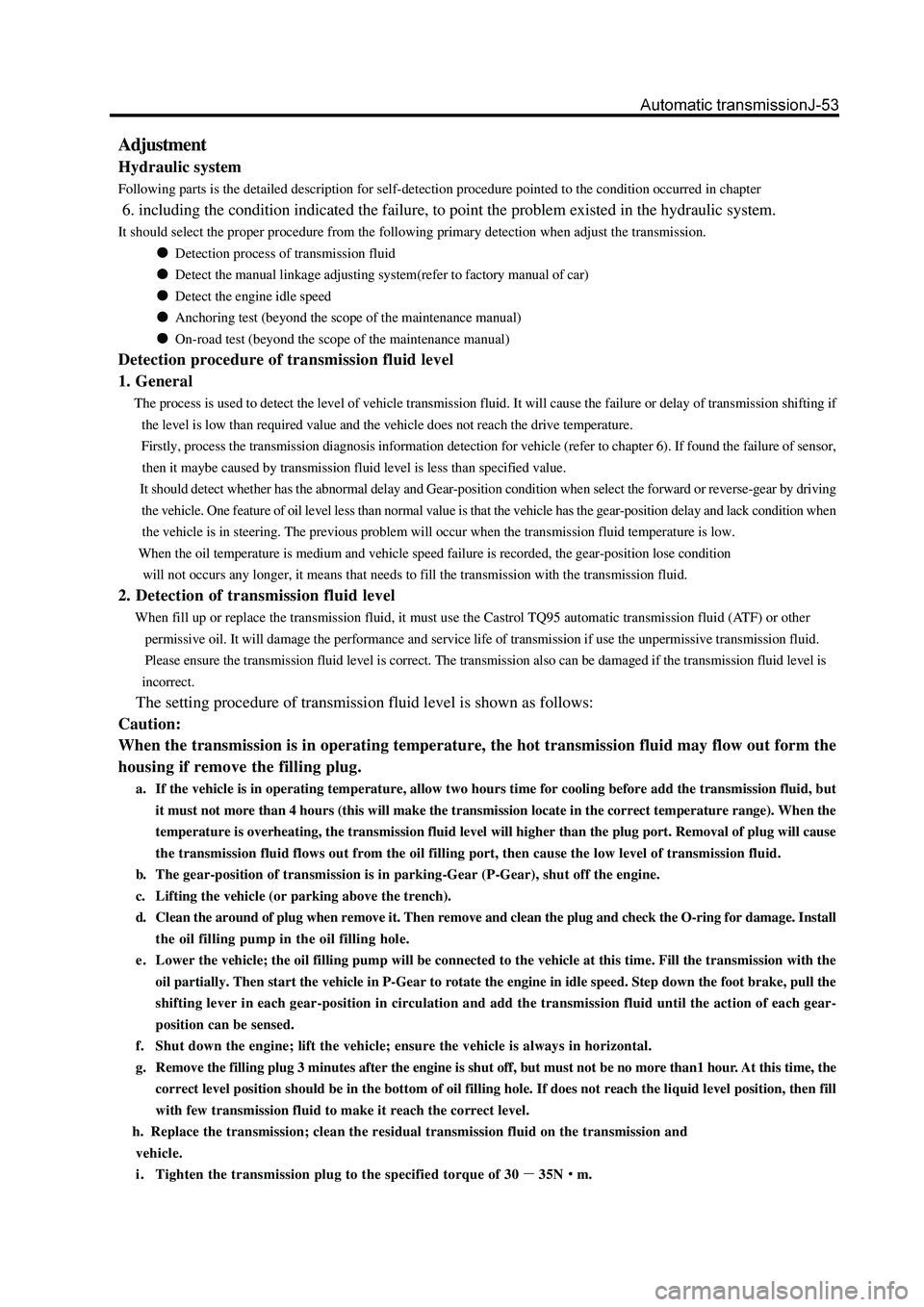
Adjustment
Hydraulic system
Following parts is the detailed description for self-detection procedure pointed to the condition occurred in chapter
6. including the condition indicated the failure, to point the problem existed in the hydraulic system.
It should select the proper procedure from the following primary detection when adjust the transmission.
Detection process of transmission fluid
Detect the manual linkage adjusting system(refer to factory manual of car)
Detect the engine idle speed
Anchoring test (beyond the scope of the maintenance manual)
On-road test (beyond the scope of the maintenance manual)
Detection procedure of transmission fluid level
1. General
The process is used to detect the level of vehicle transmission fluid. It will cause the failure or delay of transmission shifting if
the level is low than required value and the vehicle does not reach the drive temperature.
Firstly, process the transmission diagnosis information detection for vehicle (refer to chapter 6). If found the failure of sensor,
then it maybe caused by transmission fluid level is less than specified value.
It should detect whether has the abnormal delay and Gear-position condition when select the forward or reverse-gear by driving
the vehicle. One feature of oil level less than normal value is that the vehicle has the gear-position delay and lack condition when
the vehicle is in steering. The previous problem will occur when the transmission fluid temperature is low.
When the oil temperature is medium and vehicle speed failure is recorded, the gear-position lose condition
will not occurs any longer, it means that needs to fill the transmission with the transmission fluid.
2. Detection of transmission fluid level
When fill up or replace the transmission fluid, it must use the Castrol TQ95 automatic transmission fluid (ATF) or other
permissive oil. It will damage the performance and service life of transmission if use the unpermissive transmission fluid.
Please ensure the transmission fluid level is correct. The transmission also can be damaged if the transmission fluid level is
incorrect.
The setting procedure of transmission fluid level is shown as follows:
Caution:
When the transmission is in operating temperature, the hot transmission fluid may flow out form the
housing if remove the filling plug.
a. If the vehicle is in operating temperature, allow two hours time for cooling before add the transmission fluid, but
it must not more than 4 hours (this will make the transmission locate in the correct temperature range). When the
temperature is overheating, the transmission fluid level will higher than the plug port. Removal of plug will cause
the transmission fluid flows out from the oil filling port, then cause the low level of transmission fluid.
b. The gear-position of transmission is in parking-Gear (P-Gear), shut off the engine.
c. Lifting the vehicle (or parking above the trench).
d. Clean the around of plug when remove it. Then remove and clean the plug and check the O-ring for damage. Install
the oil filling pump in the oil filling hole.
e. Lower the vehicle; the oil filling pump will be connected to the vehicle at this time. Fill the transmission with the
oil partially. Then start the vehicle in P-Gear to rotate the engine in idle speed. Step down the foot brake, pull the
shifting lever in each gear-position in circulation and add the transmission fluid until the action of each gear-
position can be sensed.
f. Shut down the engine; lift the vehicle; ensure the vehicle is always in horizontal.
g. Remove the filling plug 3 minutes after the engine is shut off, but must not be no more than1 hour. At this time, the
correct level position should be in the bottom of oil filling hole. If does not reach the liquid level position, then fill
with few transmission fluid to make it reach the correct level.
h. Replace the transmission; clean the residual transmission fluid on the transmission and
vehicle.
i. Tighten the transmission plug to the specified torque of 30
35Nm.
Page 130 of 425
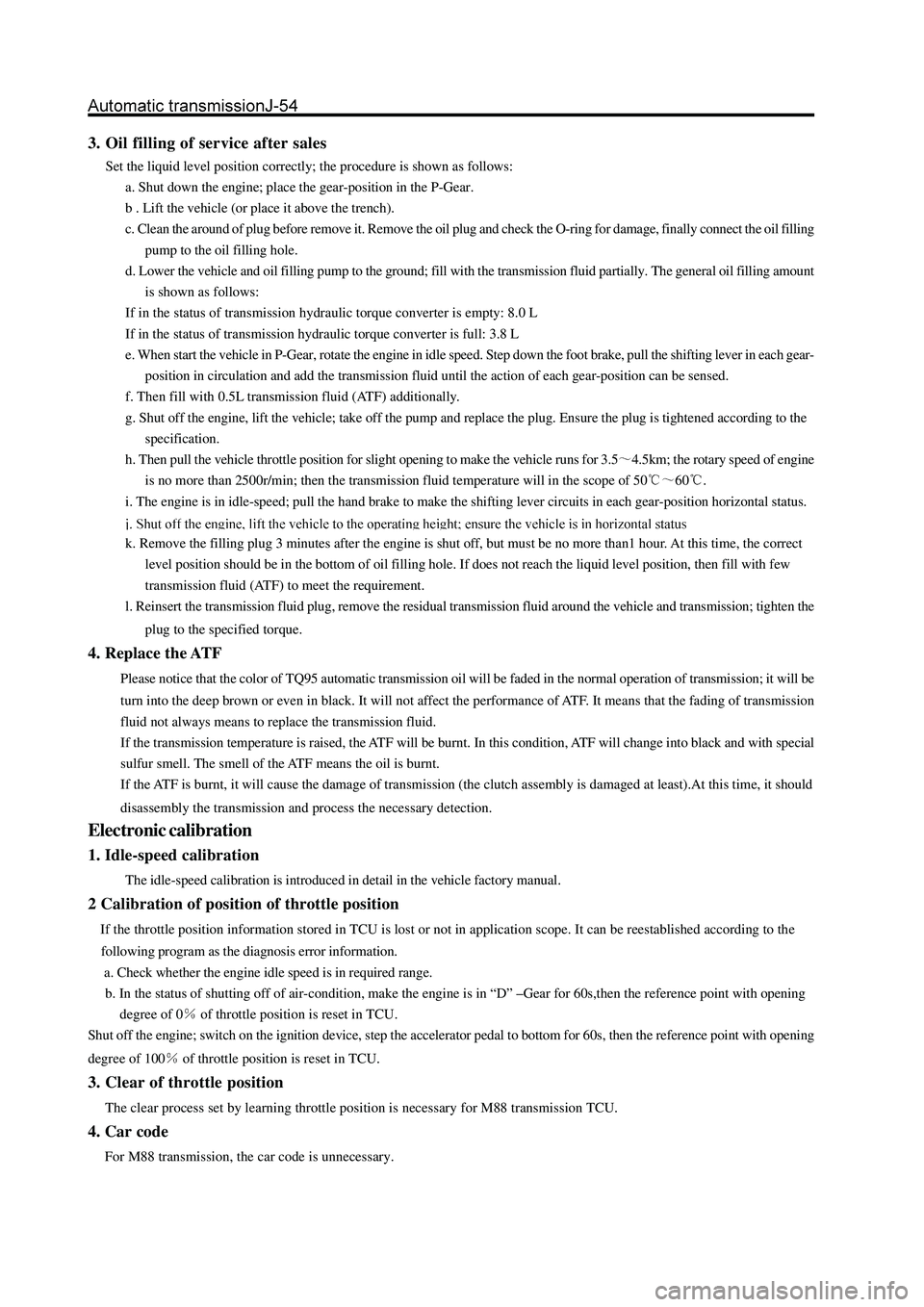
3. Oil filling of service after sales
Set the liquid level position correctly; the procedure is shown as follows:
a. Shut down the engine; place the gear-position in the P-Gear.
b . Lift the vehicle (or place it above the trench).
c. Clean the around of plug before remove it. Remove the oil plug and check the O-ring for damage, finally connect the oil filling
pump to the oil filling hole.
d. Lower the vehicle and oil filling pump to the ground; fill with the transmission fluid partially. The general oil filling amount
is shown as follows:
If in the status of transmission hydraulic torque converter is empty: 8.0 L
If in the status of transmission hydraulic torque converter is full: 3.8 L
e. When start the vehicle in P-Gear, rotate the engine in idle speed. Step down the foot brake, pull the shifting lever in each gear-
position in circulation and add the transmission fluid until the action of each gear-position can be sensed.
f. Then fill with 0.5L transmission fluid (ATF) additionally.
g. Shut off the engine, lift the vehicle; take off the pump and replace the plug. Ensure the plug is tightened according to the
specification.
h. Then pull the vehicle throttle position for slight opening to make the vehicle runs for 3.5
4.5km; the rotary speed of engine
is no more than 2500r/min; then the transmission fluid temperature will in the scope of 50
60.
i. The engine is in idle-speed; pull the hand brake to make the shifting lever circuits in each gear-position horizontal status.
k. Remove the filling plug 3 minutes after the engine is shut off, but must be no more than1 hour. At this time, the correct
level position should be in the bottom of oil filling hole. If does not reach the liquid level position, then fill with few
transmission fluid (ATF) to meet the requirement.
l. Reinsert the transmission fluid plug, remove the residual transmission fluid around the vehicle and transmission; tighten the
plug to the specified torque.
4. Replace the ATF
Please notice that the color of TQ95 automatic transmission oil will be faded in the normal operation of transmission; it will be
turn into the deep brown or even in black. It will not affect the performance of ATF. It means that the fading of transmission
fluid not always means to replace the transmission fluid.
If the transmission temperature is raised, the ATF will be burnt. In this condition, ATF will change into black and with special
sulfur smell. The smell of the ATF means the oil is burnt.
If the ATF is burnt, it will cause the damage of transmission (the clutch assembly is damaged at least).At this time, it should
disassembly the transmission and process the necessary detection.
Electronic calibration
1. Idle-speed calibration
The idle-speed calibration is introduced in detail in the vehicle factory manual.
2 Calibration of position of throttle position
If the throttle position information stored in TCU is lost or not in application scope. It can be reestablished according to the
following program as the diagnosis error information.
a. Check whether the engine idle speed is in required range.
b. In the status of shutting off of air-condition, make the engine is in “D” –Gear for 60s,then the reference point with opening
degree of 0
of throttle position is reset in TCU.
Shut off the engine; switch on the ignition device, step the accelerator pedal to bottom for 60s, then the reference point with opening
degree of 100
of throttle position is reset in TCU.
3. Clear of throttle position
The clear process set by learning throttle position is necessary for M88 transmission TCU.
4. Car code
For M88 transmission, the car code is unnecessary.
Page 131 of 425
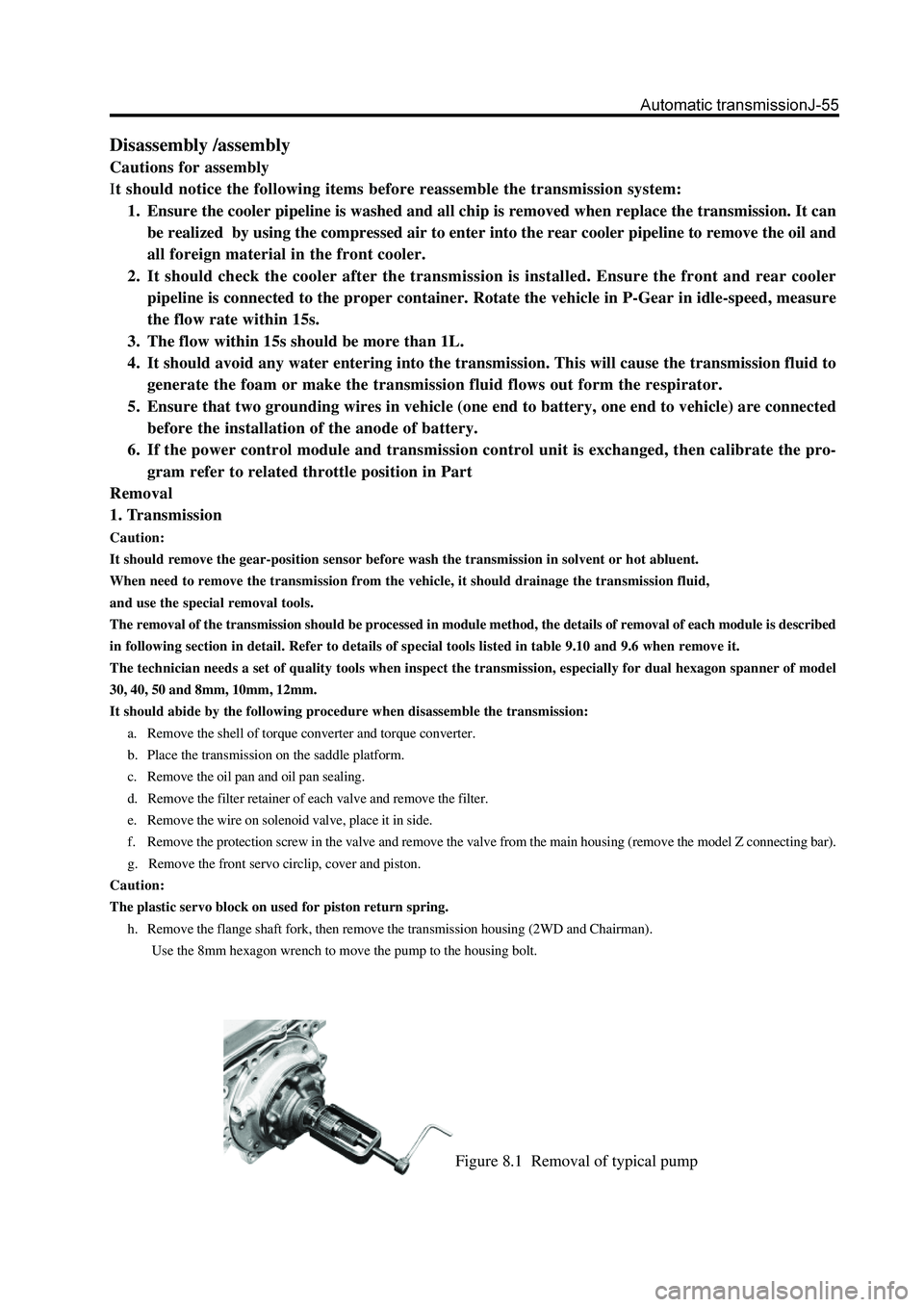
Figure 8.1 Removal of typical pump
Disassembly /assembly
Cautions for assembly
It should notice the following items before reassemble the transmission system:
1. Ensure the cooler pipeline is washed and all chip is removed when replace the transmission. It can
be realized by using the compressed air to enter into the rear cooler pipeline to remove the oil and
all foreign material in the front cooler.
2. It should check the cooler after the transmission is installed. Ensure the front and rear cooler
pipeline is connected to the proper container. Rotate the vehicle in P-Gear in idle-speed, measure
the flow rate within 15s.
3. The flow within 15s should be more than 1L.
4. It should avoid any water entering into the transmission. This will cause the transmission fluid to
generate the foam or make the transmission fluid flows out form the respirator.
5. Ensure that two grounding wires in vehicle (one end to battery, one end to vehicle) are connected
before the installation of the anode of battery.
6. If the power control module and transmission control unit is exchanged, then calibrate the pro-
gram refer to related throttle position in Part
Removal
1. Transmission
Caution:
It should remove the gear-position sensor before wash the transmission in solvent or hot abluent.
When need to remove the transmission from the vehicle, it should drainage the transmission fluid,
and use the special removal tools.
The removal of the transmission should be processed in module method, the details of removal of each module is described
in following section in detail. Refer to details of special tools listed in table 9.10 and 9.6 when remove it.
The technician needs a set of quality tools when inspect the transmission, especially for dual hexagon spanner of model
30, 40, 50 and 8mm, 10mm, 12mm.
It should abide by the following procedure when disassemble the transmission:
a. Remove the shell of torque converter and torque converter.
b. Place the transmission on the saddle platform.
c. Remove the oil pan and oil pan sealing.
d. Remove the filter retainer of each valve and remove the filter.
e. Remove the wire on solenoid valve, place it in side.
f. Remove the protection screw in the valve and remove the valve from the main housing (remove the model Z connecting bar).
g. Remove the front servo circlip, cover and piston.
Caution:
The plastic servo block on used for piston return spring.
h. Remove the flange shaft fork, then remove the transmission housing (2WD and Chairman).
Use the 8mm hexagon wrench to move the pump to the housing bolt.
Page 132 of 425
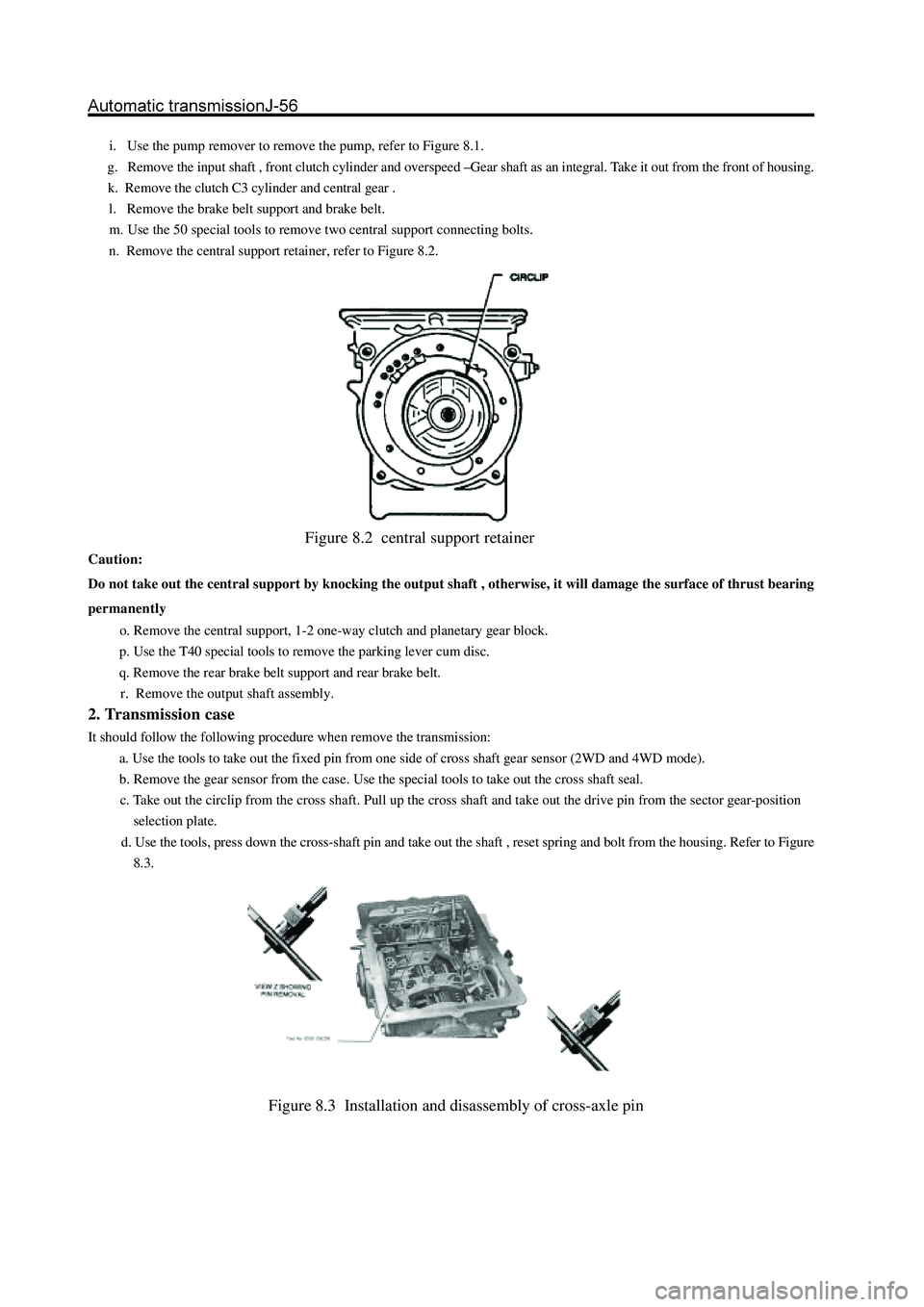
Caution:
Do not take out the central support by knocking the output shaft , otherwise, it will damage the surface of thrust bearing
permanently
o. Remove the central support, 1-2 one-way clutch and planetary gear block.
p. Use the T40 special tools to remove the parking lever cum disc.
q. Remove the rear brake belt support and rear brake belt.
r. Remove the output shaft assembly.
2. Transmission case
It should follow the following procedure when remove the transmission:
a. Use the tools to take out the fixed pin from one side of cross shaft gear sensor (2WD and 4WD mode).
b. Remove the gear sensor from the case. Use the special tools to take out the cross shaft seal.
c. Take out the circlip from the cross shaft. Pull up the cross shaft and take out the drive pin from the sector gear-position
selection plate.
d. Use the tools, press down the cross-shaft pin and take out the shaft , reset spring and bolt from the housing. Refer to Figure
8.3.
Figure 8.3 Installation and disassembly of cross-axle pinFigure 8.2 central support retainer
i. Use the pump remover to remove the pump, refer to Figure 8.1.
g. Remove the input shaft , front clutch cylinder and overspeed –Gear shaft as an integral. Take it out from the front of housing.
k. Remove the clutch C3 cylinder and central gear .
l. Remove the brake belt support and brake belt.
m. Use the 50 special tools to remove two central support connecting bolts.
n. Remove the central support retainer, refer to Figure 8.2.
Page 133 of 425
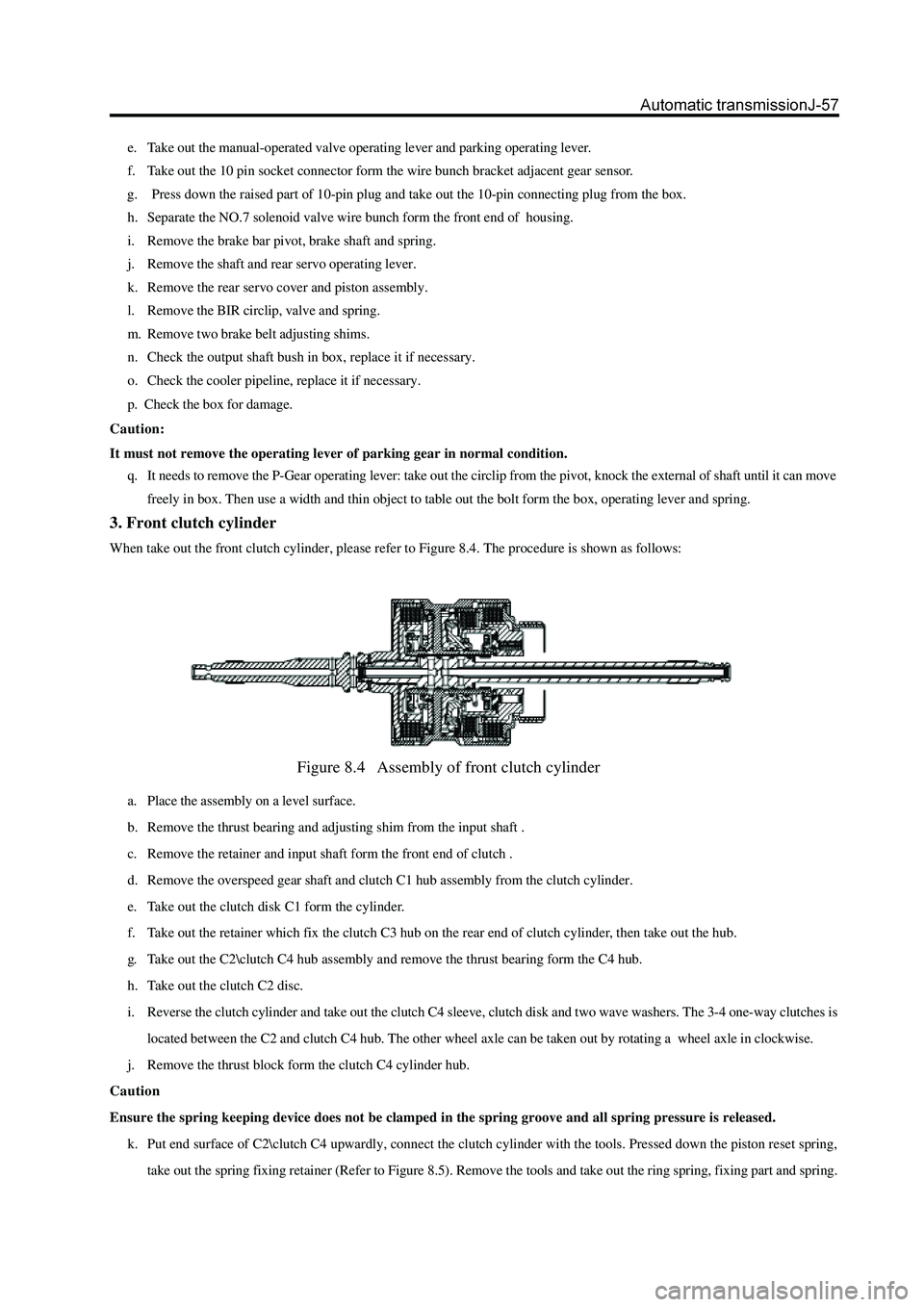
e. Take out the manual-operated valve operating lever and parking operating lever.
f. Take out the 10 pin socket connector form the wire bunch bracket adjacent gear sensor.
g. Press down the raised part of 10-pin plug and take out the 10-pin connecting plug from the box.
h. Separate the NO.7 solenoid valve wire bunch form the front end of housing.
i. Remove the brake bar pivot, brake shaft and spring.
j. Remove the shaft and rear servo operating lever.
k. Remove the rear servo cover and piston assembly.
l. Remove the BIR circlip, valve and spring.
m. Remove two brake belt adjusting shims.
n. Check the output shaft bush in box, replace it if necessary.
o. Check the cooler pipeline, replace it if necessary.
p. Check the box for damage.
Caution:
It must not remove the operating lever of parking gear in normal condition.
q. It needs to remove the P-Gear operating lever: take out the circlip from the pivot, knock the external of shaft until it can move
freely in box. Then use a width and thin object to table out the bolt form the box, operating lever and spring.
3. Front clutch cylinder
When take out the front clutch cylinder, please refer to Figure 8.4. The procedure is shown as follows:
Figure 8.4 Assembly of front clutch cylinder
a. Place the assembly on a level surface.
b. Remove the thrust bearing and adjusting shim from the input shaft .
c. Remove the retainer and input shaft form the front end of clutch .
d. Remove the overspeed gear shaft and clutch C1 hub assembly from the clutch cylinder.
e. Take out the clutch disk C1 form the cylinder.
f. Take out the retainer which fix the clutch C3 hub on the rear end of clutch cylinder, then take out the hub.
g. Take out the C2\clutch C4 hub assembly and remove the thrust bearing form the C4 hub.
h. Take out the clutch C2 disc.
i. Reverse the clutch cylinder and take out the clutch C4 sleeve, clutch disk and two wave washers. The 3-4 one-way clutches is
located between the C2 and clutch C4 hub. The other wheel axle can be taken out by rotating a wheel axle in clockwise.
j. Remove the thrust block form the clutch C4 cylinder hub.
Caution
Ensure the spring keeping device does not be clamped in the spring groove and all spring pressure is released.
k. Put end surface of C2\clutch C4 upwardly, connect the clutch cylinder with the tools. Pressed down the piston reset spring,
take out the spring fixing retainer (Refer to Figure 8.5). Remove the tools and take out the ring spring, fixing part and spring.
Page 134 of 425
l. Reverse the clutch cylinder on the pressure machine; and remove the clutch C1 reset spring with same method.
m. Send the compressed air into the cylinder through the cylinder hole, remove the clutch piston from the clutch cylinder. Refer
to Figure 8.6.
4.clutch C3 cylinder
The procedure of removal of clutch C3 cylinder is shown as follows:
a. Remove the front sun gear assembly, thrust bearing and thrust washer from the clutch C3 cylinder asse bly , shown as Figure
8.7.
b. Remove the nylon thrust bearing, bearing block, needle thrust bearing and thrust bearing . From the clutch cylinder hub.
Figure 8.5 Impressed clutch reset spring
Figure 8.7 Clutch C3 and central gear assemblyFigure 8.6 Removal of C1, C2 and clutch C4 piston
Page 135 of 425
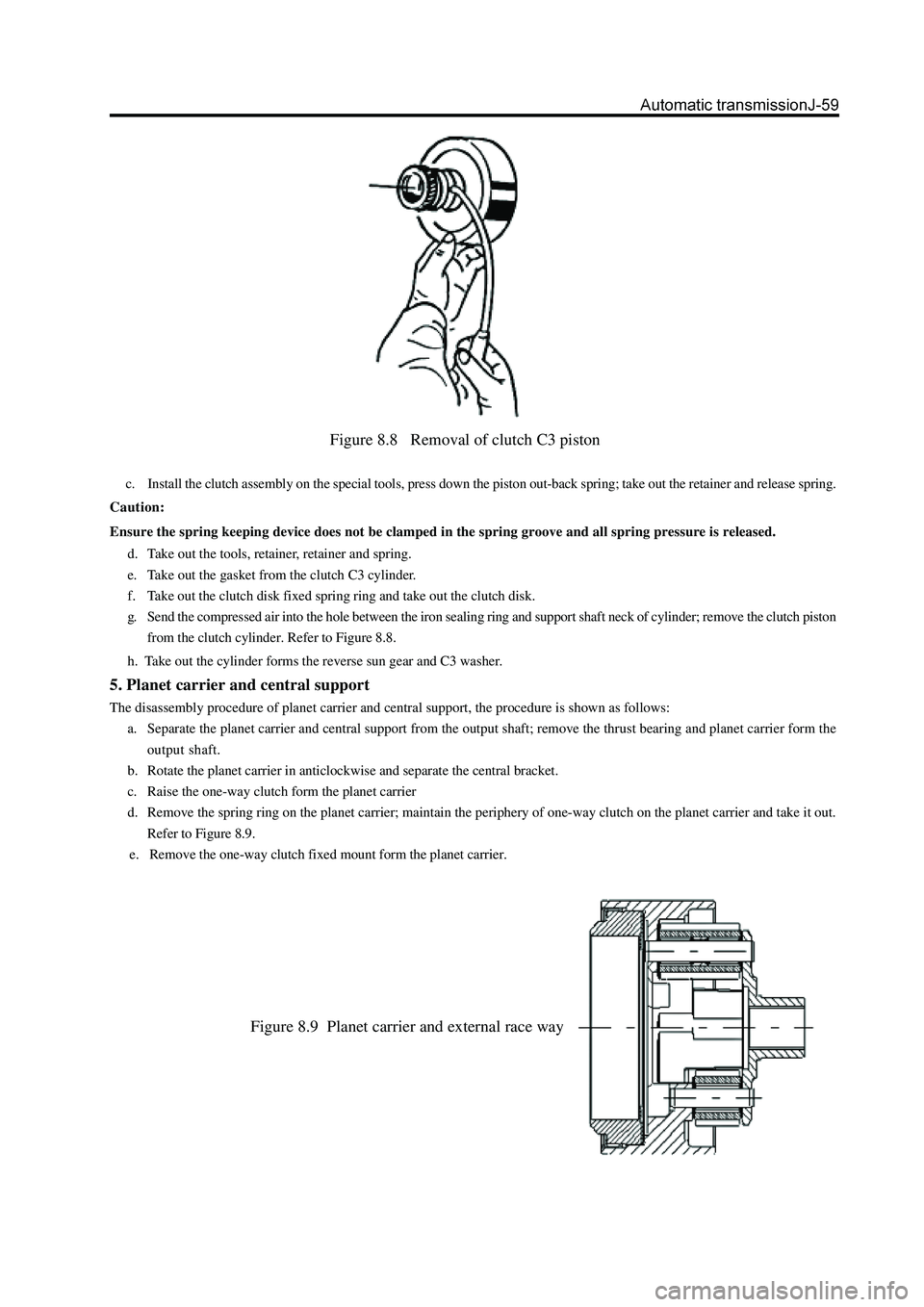
Figure 8.8 Removal of clutch C3 piston
c. Install the clutch assembly on the special tools, press down the piston out-back spring; take out the retainer and release spring.
Caution:
Ensure the spring keeping device does not be clamped in the spring groove and all spring pressure is released.
d. Take out the tools, retainer, retainer and spring.
e. Take out the gasket from the clutch C3 cylinder.
f. Take out the clutch disk fixed spring ring and take out the clutch disk.
g. Send the compressed air into the hole between the iron sealing ring and support shaft neck of cylinder; remove the clutch piston
from the clutch cylinder. Refer to Figure 8.8.
h. Take out the cylinder forms the reverse sun gear and C3 washer.
5. Planet carrier and central support
The disassembly procedure of planet carrier and central support, the procedure is shown as follows:
a. Separate the planet carrier and central support from the output shaft; remove the thrust bearing and planet carrier form the
output shaft.
b. Rotate the planet carrier in anticlockwise and separate the central bracket.
c. Raise the one-way clutch form the planet carrier
d. Remove the spring ring on the planet carrier; maintain the periphery of one-way clutch on the planet carrier and take it out.
Refer to Figure 8.9.
e. Remove the one-way clutch fixed mount form the planet carrier.
Figure 8.9 Planet carrier and external race way
Page 136 of 425
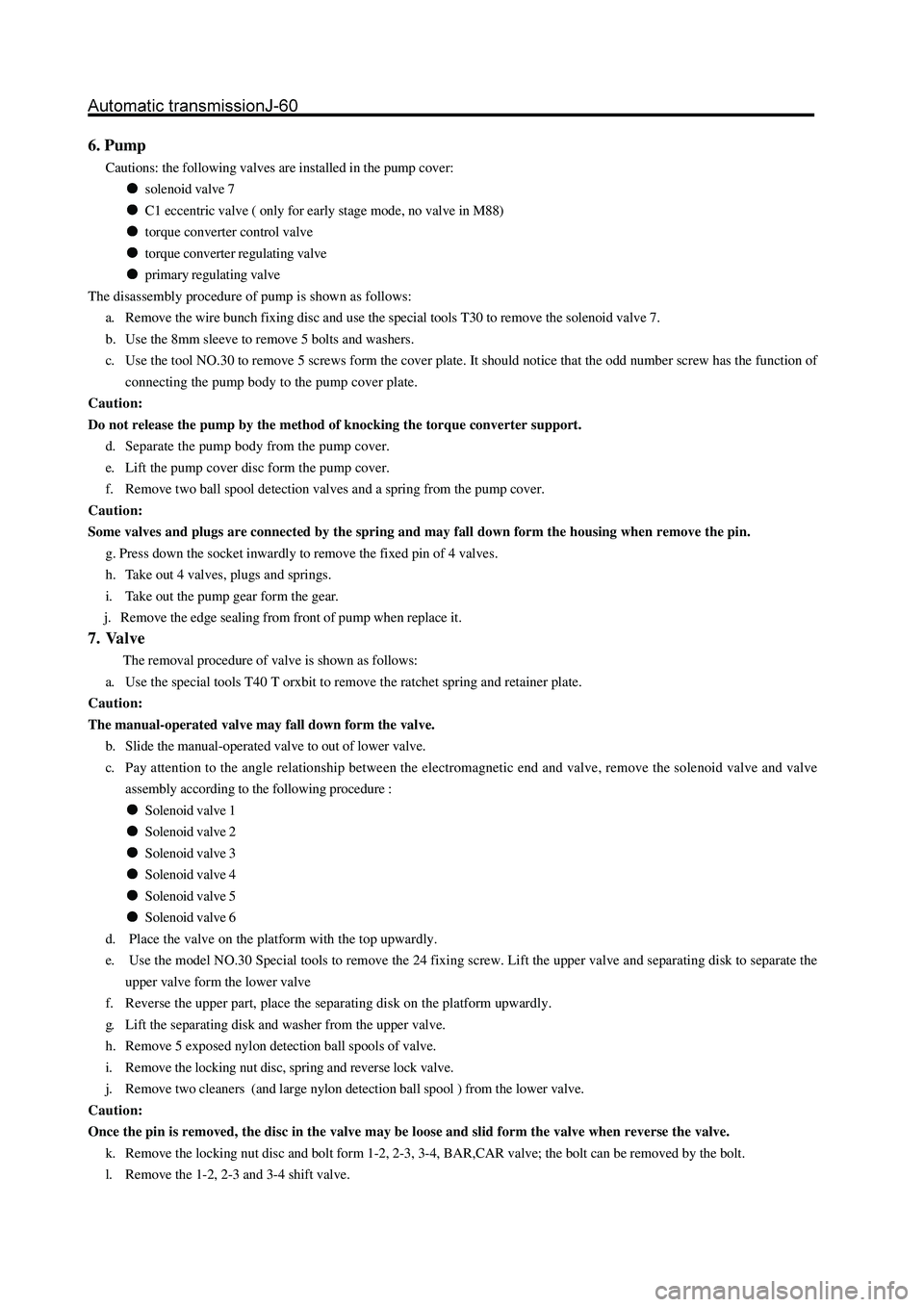
6. Pump
Cautions: the following valves are installed in the pump cover:
solenoid valve 7
C1 eccentric valve ( only for early stage mode, no valve in M88)
torque converter control valve
torque converter regulating valve
primary regulating valve
The disassembly procedure of pump is shown as follows:
a. Remove the wire bunch fixing disc and use the special tools T30 to remove the solenoid valve 7.
b. Use the 8mm sleeve to remove 5 bolts and washers.
c. Use the tool NO.30 to remove 5 screws form the cover plate. It should notice that the odd number screw has the function of
connecting the pump body to the pump cover plate.
Caution:
Do not release the pump by the method of knocking the torque converter support.
d. Separate the pump body from the pump cover.
e. Lift the pump cover disc form the pump cover.
f. Remove two ball spool detection valves and a spring from the pump cover.
Caution:
Some valves and plugs are connected by the spring and may fall down form the housing when remove the pin.
g. Press down the socket inwardly to remove the fixed pin of 4 valves.
h. Take out 4 valves, plugs and springs.
i. Take out the pump gear form the gear.
j. Remove the edge sealing from front of pump when replace it.
7. Valve
The removal procedure of valve is shown as follows:
a. Use the special tools T40 T orxbit to remove the ratchet spring and retainer plate.
Caution:
The manual-operated valve may fall down form the valve.
b. Slide the manual-operated valve to out of lower valve.
c. Pay attention to the angle relationship between the electromagnetic end and valve, remove the solenoid valve and valve
assembly according to the following procedure :
Solenoid valve 1
Solenoid valve 2
Solenoid valve 3
Solenoid valve 4
Solenoid valve 5
Solenoid valve 6
d. Place the valve on the platform with the top upwardly.
e. Use the model NO.30 Special tools to remove the 24 fixing screw. Lift the upper valve and separating disk to separate the
upper valve form the lower valve
f. Reverse the upper part, place the separating disk on the platform upwardly.
g. Lift the separating disk and washer from the upper valve.
h. Remove 5 exposed nylon detection ball spools of valve.
i. Remove the locking nut disc, spring and reverse lock valve.
j. Remove two cleaners (and large nylon detection ball spool ) from the lower valve.
Caution:
Once the pin is removed, the disc in the valve may be loose and slid form the valve when reverse the valve.
k. Remove the locking nut disc and bolt form 1-2, 2-3, 3-4, BAR,CAR valve; the bolt can be removed by the bolt.
l. Remove the 1-2, 2-3 and 3-4 shift valve.