Page 289 of 425
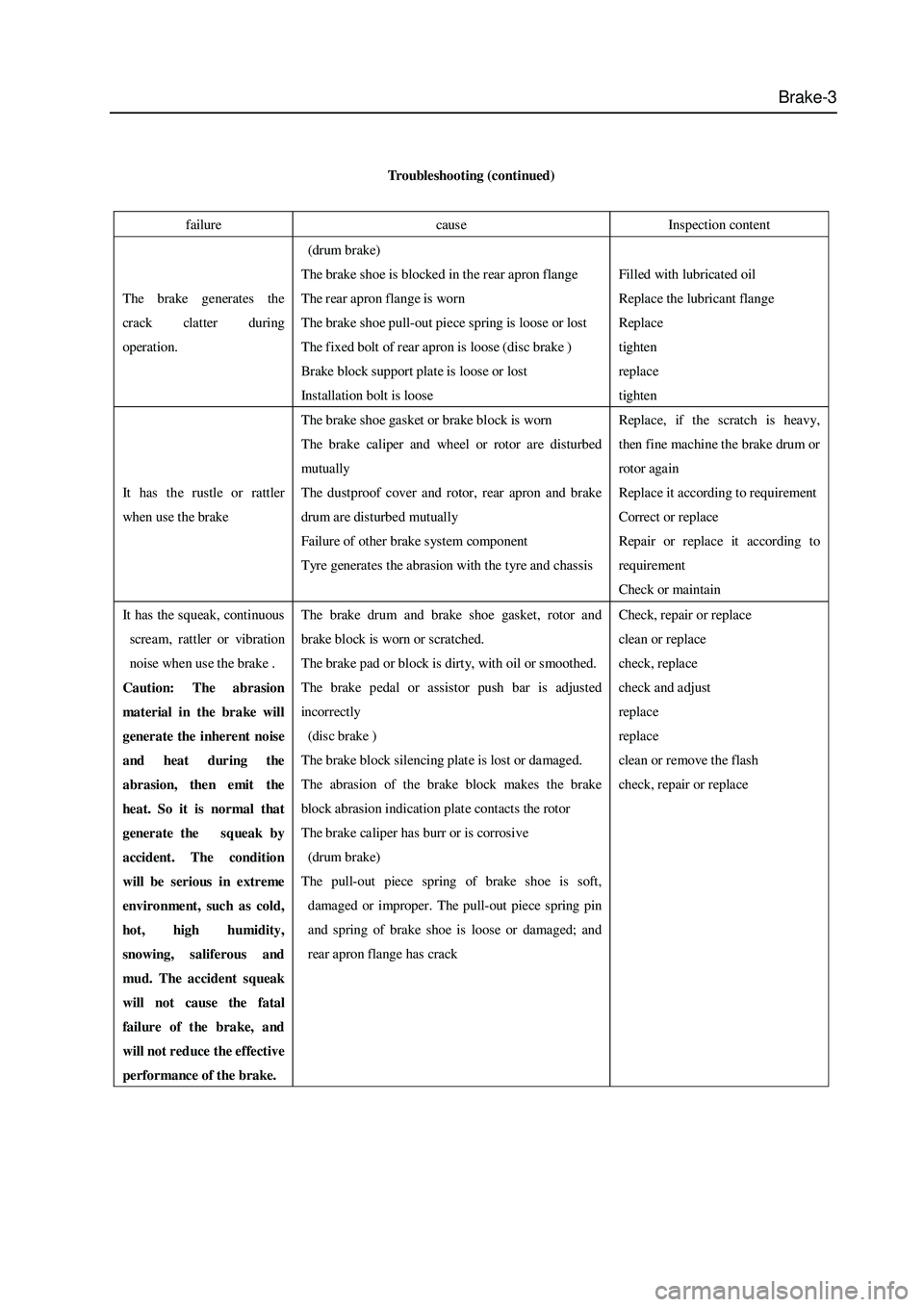
Brake-3
Troubleshooting (continued)
failure caus e Inspection content
The brake generates the
crack clatter during
operation. (drum brake)
The brake shoe is blocked in the rear apron flange
The rear apron flange is worn
The brake shoe pull-out piece spring is loose or lost
The fixed bolt of rear apron is loose (disc brake )
Brake block support plate is loose or lost
Installation bolt is loose
Filled with lubricated oil
Replace the lubricant flange
Replace
tighten
replace
tighten
It has the rustle or rattler
when use the brake The brake shoe gasket or brake block is worn
The brake caliper and wheel or rotor are disturbed
mutually
The dustproof cover and rotor, rear apron and brake
drum are disturbed mutually
Failure of other brake system component
Tyre generates the abrasion with the tyre and chassis Replace, if the scratch is heavy,
then fine machine the brake drum or
rotor again
Replace it according to requirement
Correct or replace
Repair or replace it according to
requirement
Check or maintain
It has the squeak, continuous
scream, rattler or vibration
noise when use the brake .
Caution: The abrasion
material in the brake will
generate the inherent noise
and heat during the
abrasion, then emit the
heat. So it is normal that
generate the squeak by
accident. The condition
will be serious in extreme
environment, such as cold,
hot, high humidity,
snowing, saliferous and
mud. The accident squeak
will not cause the fatal
failure of the brake, and
will not reduce the effective
performance of the brake. The brake drum and brake shoe gasket, rotor and
brake block is worn or scratched.
The brake pad or block is dirty, with oil or smoothed.
The brake pedal or assistor push bar is adjusted
incorrectly
(dis c brake )
The brake block silencing plate is lost or damaged.
The abrasion of the brake block makes the brake
block abrasion indication plate contacts the rotor
The brake ca lip er has burr or is corrosive
(drum brake)
The pull-out piece spring of brake shoe is soft,
damaged or improper. The pull-out piece spring pin
and spring of brake shoe is loose or damaged; and
rear apron flange has crack Check, repair or replace
clean or replace
check, replace
check and adjust
replace
replace
clean or remove the flash
check, repair or replace
Page 290 of 425
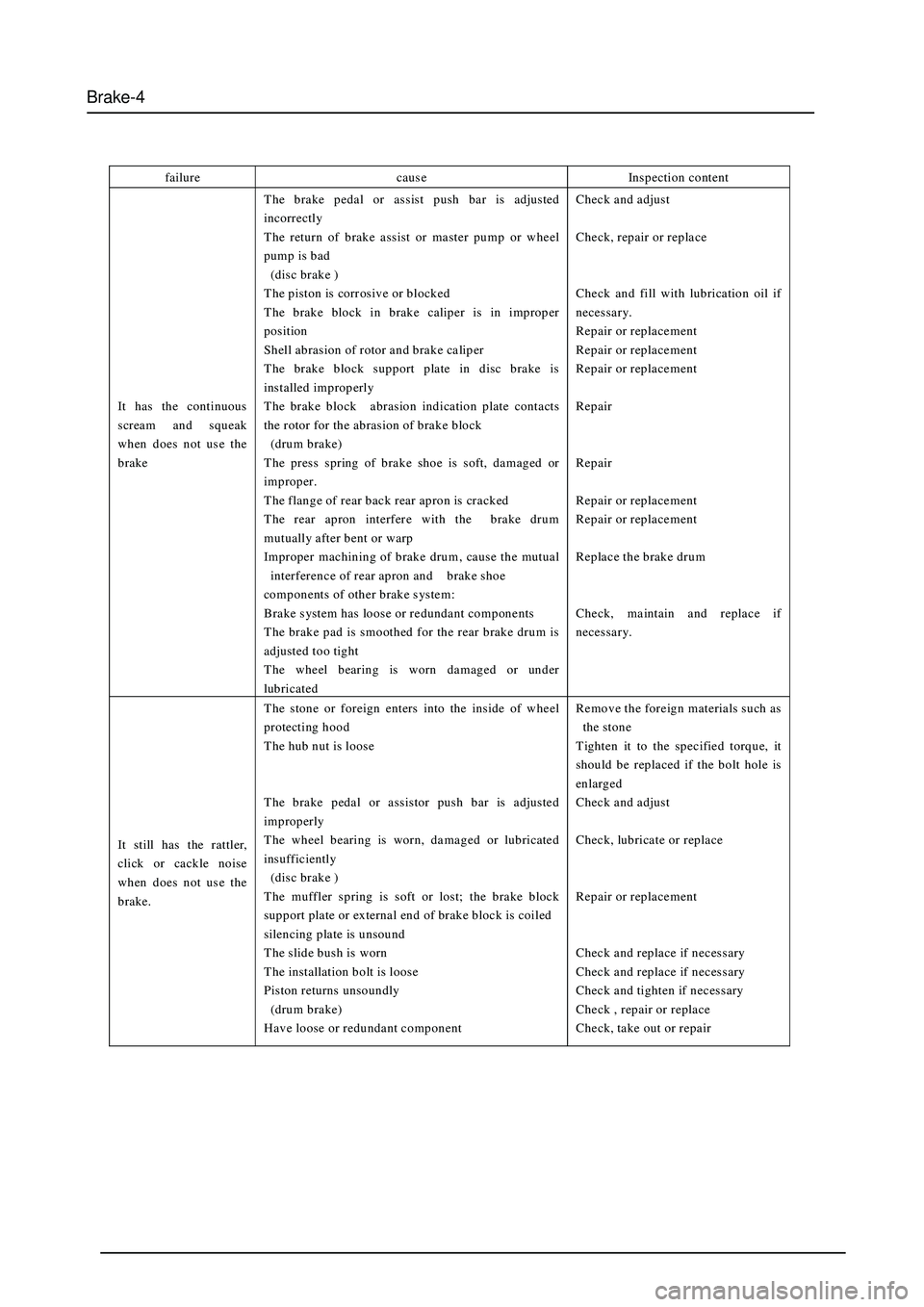
Brake-4
failure caus e Inspection content
It has the continuous
scream and squeak
when does not us e the
brake The brake pedal or assist push bar is adjusted
incorrectly
The return of brake assist or master pump or wheel
pump is bad
(dis c brake )
T he piston is corr osive or blocked
T he brake block in brake calip er is in improp er
position
Shell abrasion of rotor and brake caliper
The brake block support plate in disc brake is
installed improperly
The brake block abrasion indication plate contacts
the rotor for the abrasion of brake block
(drum brake)
The press spring of brake shoe is soft, damaged or
improper.
The flange of rear back rear apron is cracked
T he rear apron interfer e with the brake drum
mutually after bent or warp
Improper machining of brake drum , caus e the mutual
interference of rear apron and brake shoe
components of other brake s ystem :
Brake system has loose or redundant components
T he brake pad is smoothed for the rear brake drum is
adjusted too tight
The wheel bearing is worn damaged or under
lubricated Check and adjust
Check, repair or replace
Check and fill with lubrication oil if
necessary.
Repair or replacement
Repair or replacement
Repair or replacement
Repair
Repair
Repair or replacement
Repair or replacement
Replace the brake drum
Check, maintain and replace if
necessary.
It still has the rattler,
click or cackle noise
when does not us e the
brake. The stone or foreign enters into the inside of wheel
protecting hood
The hub nut is loose
The brake pedal or assistor push bar is adjusted
improperly
The wheel bearing is worn, damaged or lubricated
insufficiently
(dis c brake )
T he muffler spring is soft or lost; the brake block
support plate or external end of brake block is coiled
silencing plate is unsound
T he slide bush is worn
T he installation bolt is loos e
Piston returns unsoundly
(drum brake)
Have loose or redundant component Remove the foreign materials such as
the stone
Tighten it to the specified torque, it
should be replaced if the bolt hole is
enlarged
Check and adjust
Check, lubricate or replace
Repair or replacement
Check and replace if necessary
Check and replace if necessary
Check and tighten if necessary
Check , repair or replace
Check, take out or repair
Page 291 of 425
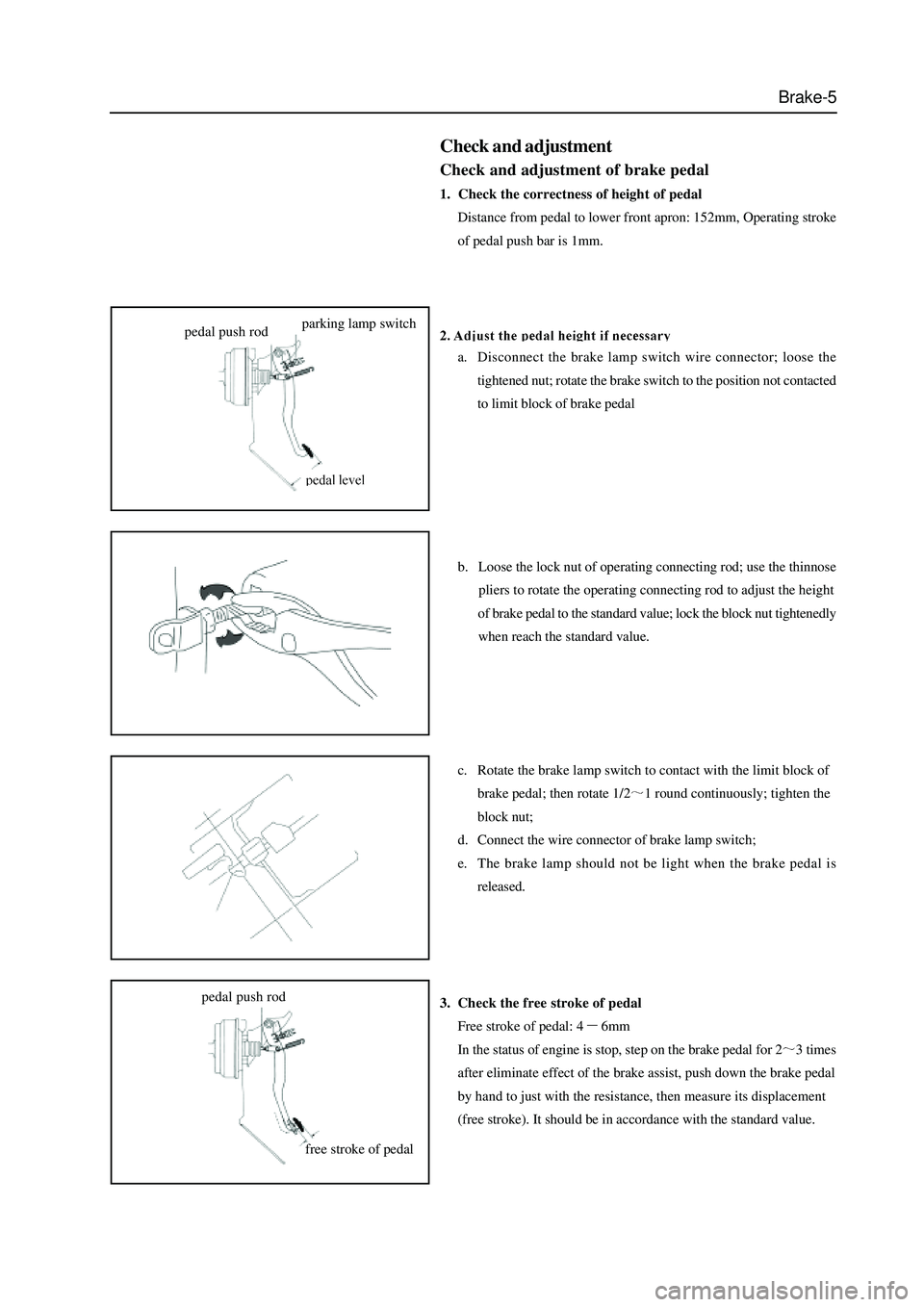
Brake-5
Check and adjustment
Check and adjustment of brake pedal
1. Check the correctness of height of pedal
Distance from pedal to lower front apron: 152mm, Operating stroke
of pedal push bar is 1mm.
a. Disconnect the brake lamp switch wire connector; loose the
tightened nut; rotate the brake switch to the position not contacted
to limit block of brake pedal
b. Loose the lock nut of operating connecting rod; use the thinnose
pliers to rotate the operating connecting rod to adjust the height
of brake pedal to the standard value; lock the block nut tightenedly
when reach the standard value.
c. Rotate the brake lamp switch to contact with the limit block of
brake pedal; then rotate 1/2
1 round continuously; tighten the
block nut;
d. Connect the wire connector of brake lamp switch;
e. The brake lamp should not be light when the brake pedal is
released.
3. Check the free stroke of pedal
Free stroke of pedal: 4
6mm
In the status of engine is stop, step on the brake pedal for 2
3 times
after eliminate effect of the brake assist, push down the brake pedal
by hand to just with the resistance, then measure its displacement
(free stroke). It should be in accordance with the standard value.
pedal push rodparking lamp switch
free stroke of pedal pedal push rod
Page 292 of 425
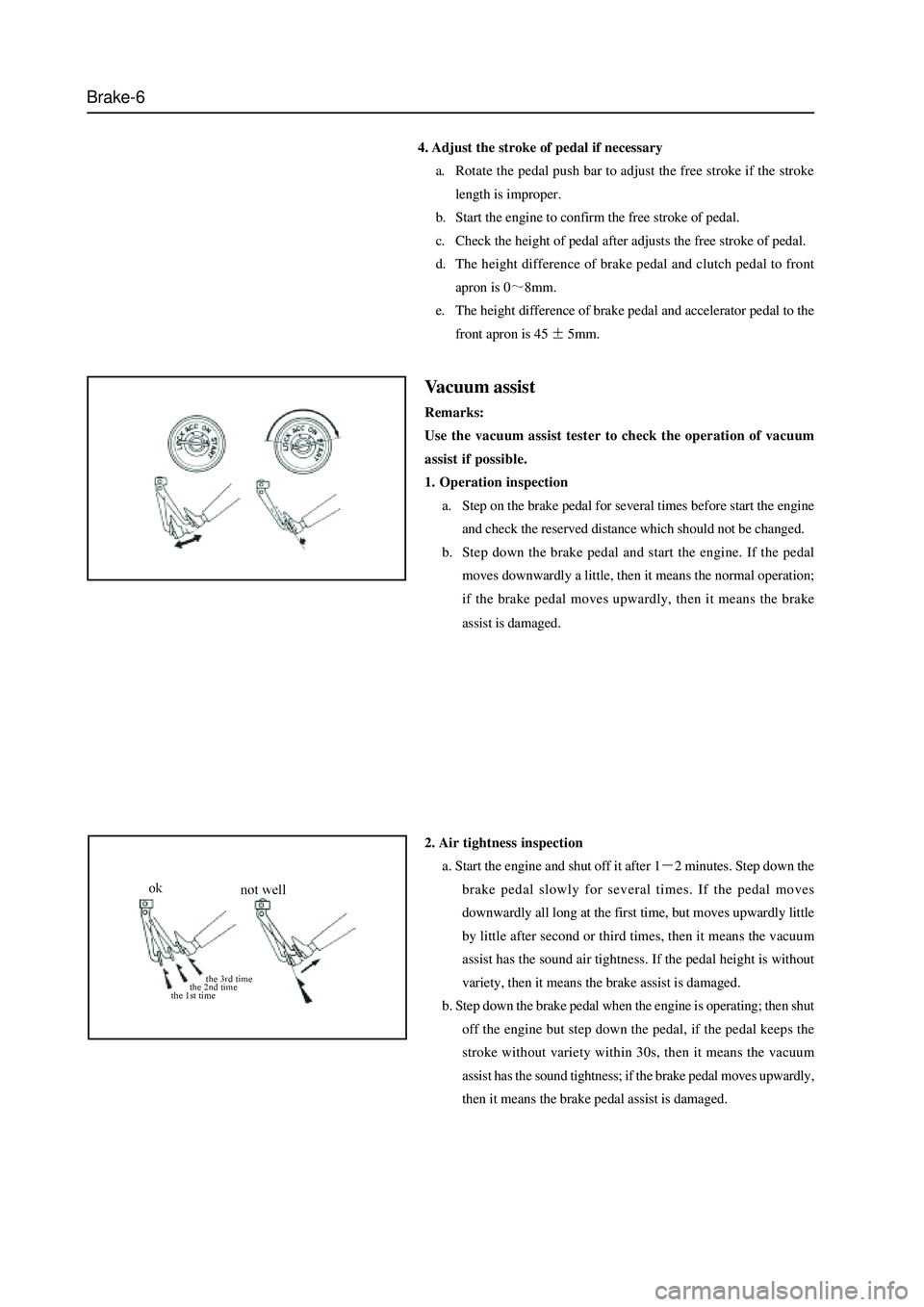
Brake-6
4. Adjust the stroke of pedal if necessary
a. Rotate the pedal push bar to adjust the free stroke if the stroke
length is improper.
b. Start the engine to confirm the free stroke of pedal.
c. Check the height of pedal after adjusts the free stroke of pedal.
d. The height difference of brake pedal and clutch pedal to front
apron is 0
8mm.
e. The height difference of brake pedal and accelerator pedal to the
front apron is 45
5mm.
Vacuum assist
Remarks:
Use the vacuum assist tester to check the operation of vacuum
assist if possible.
1. Operation inspection
a. Step on the brake pedal for several times before start the engine
and check the reserved distance which should not be changed.
b. Step down the brake pedal and start the engine. If the pedal
moves downwardly a little, then it means the normal operation;
if the brake pedal moves upwardly, then it means the brake
assist is damaged.
2. Air tightness inspection
a. Start the engine and shut off it after 1
2 minutes. Step down the
brake pedal slowly for several times. If the pedal moves
downwardly all long at the first time, but moves upwardly little
by little after second or third times, then it means the vacuum
assist has the sound air tightness. If the pedal height is without
variety, then it means the brake assist is damaged.
b. Step down the brake pedal when the engine is operating; then shut
off the engine but step down the pedal, if the pedal keeps the
stroke without variety within 30s, then it means the vacuum
assist has the sound tightness; if the brake pedal moves upwardly,
then it means the brake pedal assist is damaged.
Page 293 of 425
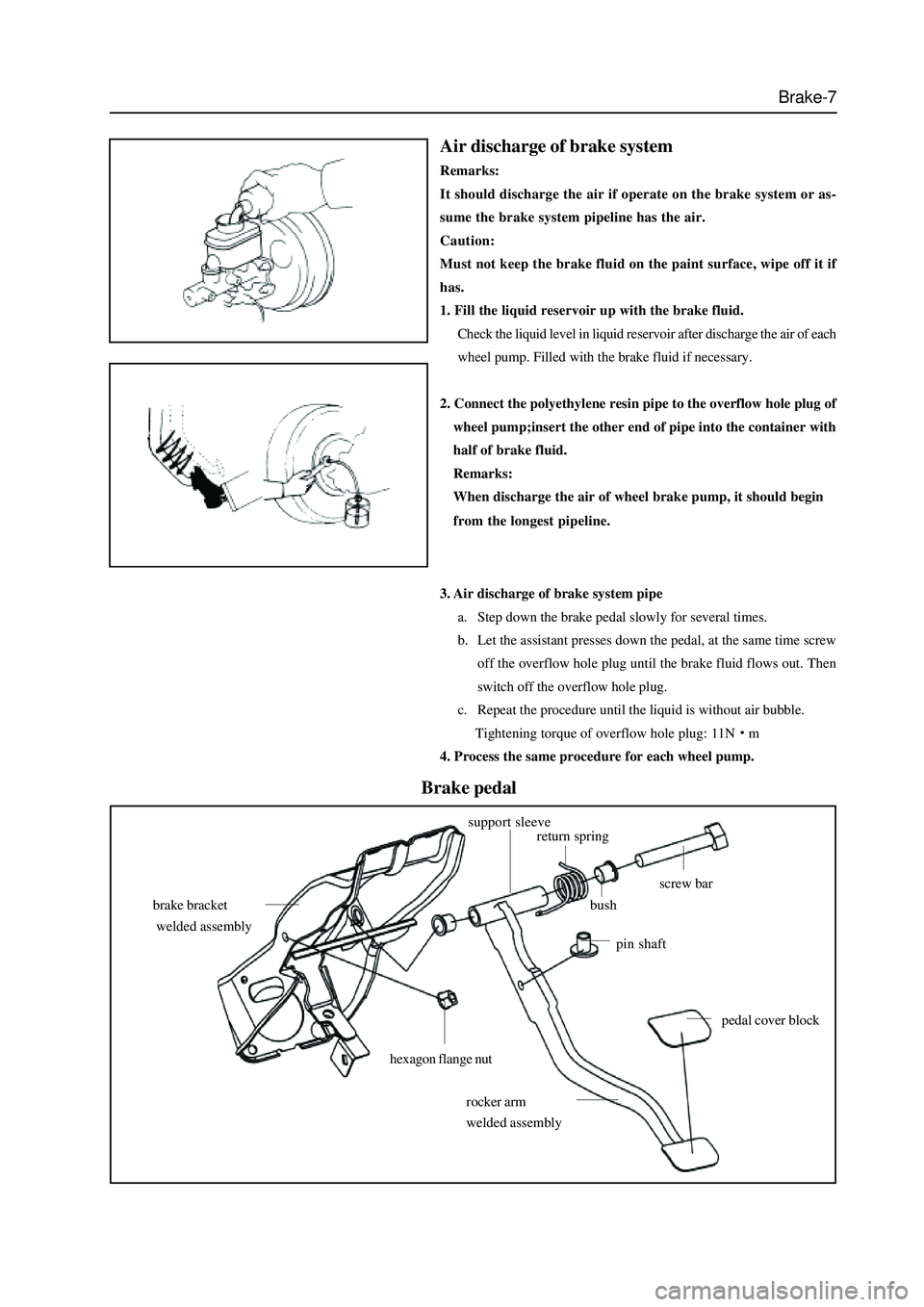
Brake-7
Air discharge of brake system
Remarks:
It should discharge the air if operate on the brake system or as-
sume the brake system pipeline has the air.
Caution:
Must not keep the brake fluid on the paint surface, wipe off it if
has.
1. Fill the liquid reservoir up with the brake fluid.
Check the liquid level in liquid reservoir after discharge the air of each
wheel pump. Filled with the brake fluid if necessary.
2. Connect the polyethylene resin pipe to the overflow hole plug of
wheel pump;insert the other end of pipe into the container with
half of brake fluid.
Remarks:
When discharge the air of wheel brake pump, it should begin
from the longest pipeline.
3. Air discharge of brake system pipe
a. Step down the brake pedal slowly for several times.
b. Let the assistant presses down the pedal, at the same time screw
off the overflow hole plug until the brake fluid flows out. Then
switch off the overflow hole plug.
c. Repeat the procedure until the liquid is without air bubble.
Tightening torque of overflow hole plug: 11N
m
4. Process the same procedure for each wheel pump.
hexagon flange nut
brake bracket
welded assembly
support sleevereturn spring
bush
screw bar
pin shaft
pedal cover block
rocker arm
welded assembly
Brake pedal
Page 294 of 425
Brake-8
Replacement of pin shaft
Remarks:
When the connecting fork pin shaft and pin hole is over worn, it
should replace the pin shaft bush.
Remarks:
When the clearance between the brake pedal shaft and bush is
large, it should remove the pedal and replace the bush.
push barlock nut
inner distance
fork pin shaft
Parking brake
parking crank assembly
switch assembly
rear parking brake pull wire (R)
rear parking brake pull wire (L)
brake pull wire clip
1. Adjust the parking crank assembly in position, 6
8 teeth.
2. When the parking brake pull wire is tightened, the torque should
be no more than 400N
m.
Page 295 of 425
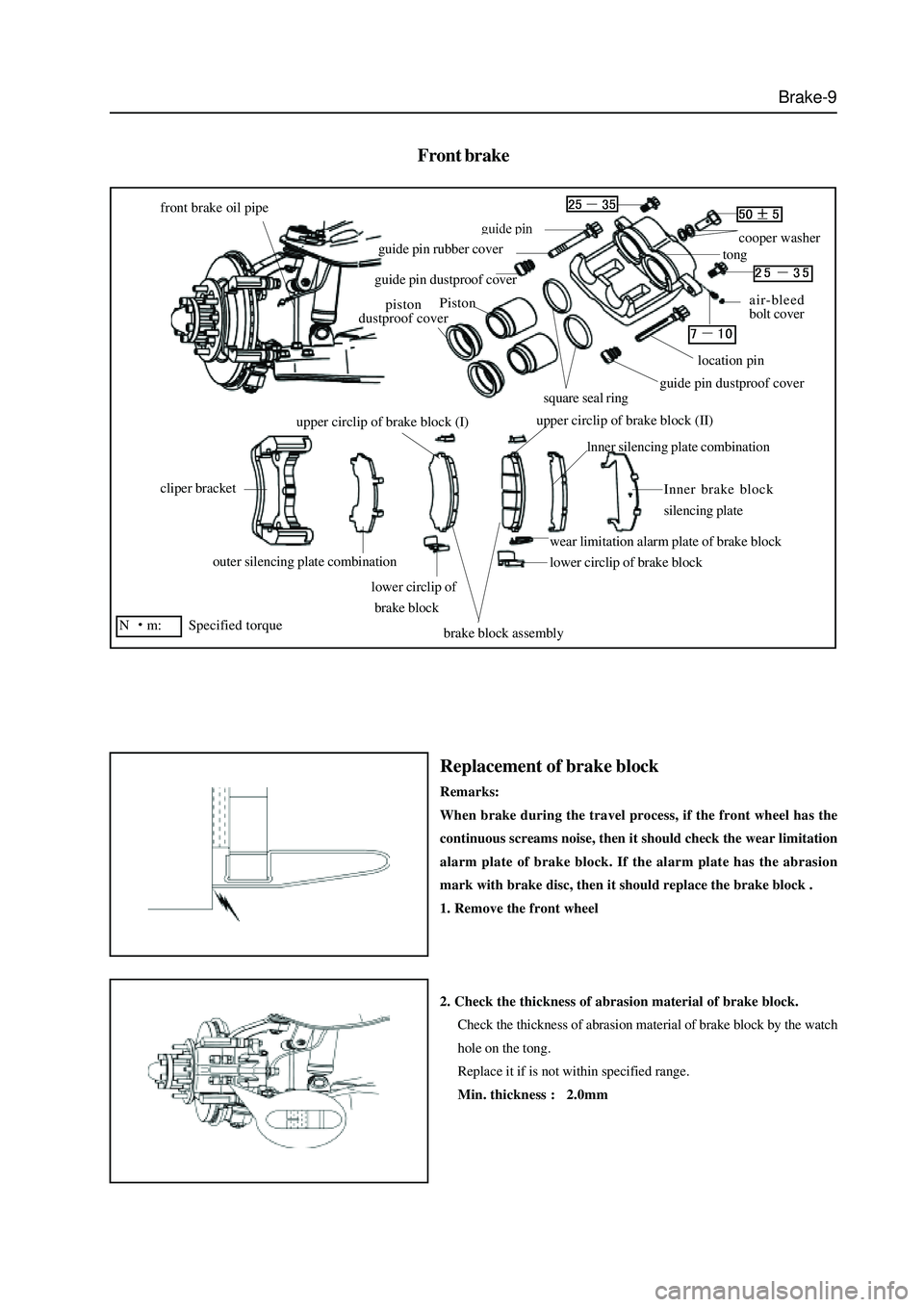
Brake-9
Front brake
front brake oil pipe
cliper bracket
outer silencing plate combination
lower circlip of
brake block
brake block assembly
lower circlip of brake block
wear limitation alarm plate of brake block
lnner silencing plate combination
Inner brake block
silencing plate
upper circlip of brake block (I)upper circlip of brake block (II)
piston
dustproof cover
guide pin dustproof cover
guide pin rubber covercooper washer
tong
air-bleed
bolt cover
location pin
guide pin dustproof coversquare seal ring
N
m: Specified torque
Piston
Replacement of brake block
Remarks:
When brake during the travel process, if the front wheel has the
continuous screams noise, then it should check the wear limitation
alarm plate of brake block. If the alarm plate has the abrasion
mark with brake disc, then it should replace the brake block .
1. Remove the front wheel
2. Check the thickness of abrasion material of brake block.
Check the thickness of abrasion material of brake block by the watch
hole on the tong.
Replace it if is not within specified range.
Min. thickness : 2.0mm
Page 296 of 425
Brake-10
3Lift the main body of brake caliper.
a. Remove the hexagon flange bolt.
b. Lift the brake pump and hang it by rope to protect the brake oil
pipe.
Remarks: Do not screw off the brake oil pipe and bleed plug.
4. Remove the following components
a. Two pieces of brake block
b. One piece of silencing plate
c. Two piece of silencing plate combination
d. One wear limitation alarm plate of brake block
e. Four brake block circlip plates
5. Measure the thickness of brake disc
(Refer to step 2 of “ Inspection of component of front brake” )
6. Measure the circular runout of brake disc.
(Refer to step 3 of “Inspection of component of front brake”)
7. Install the brake block circlip plate