Page 145 of 425
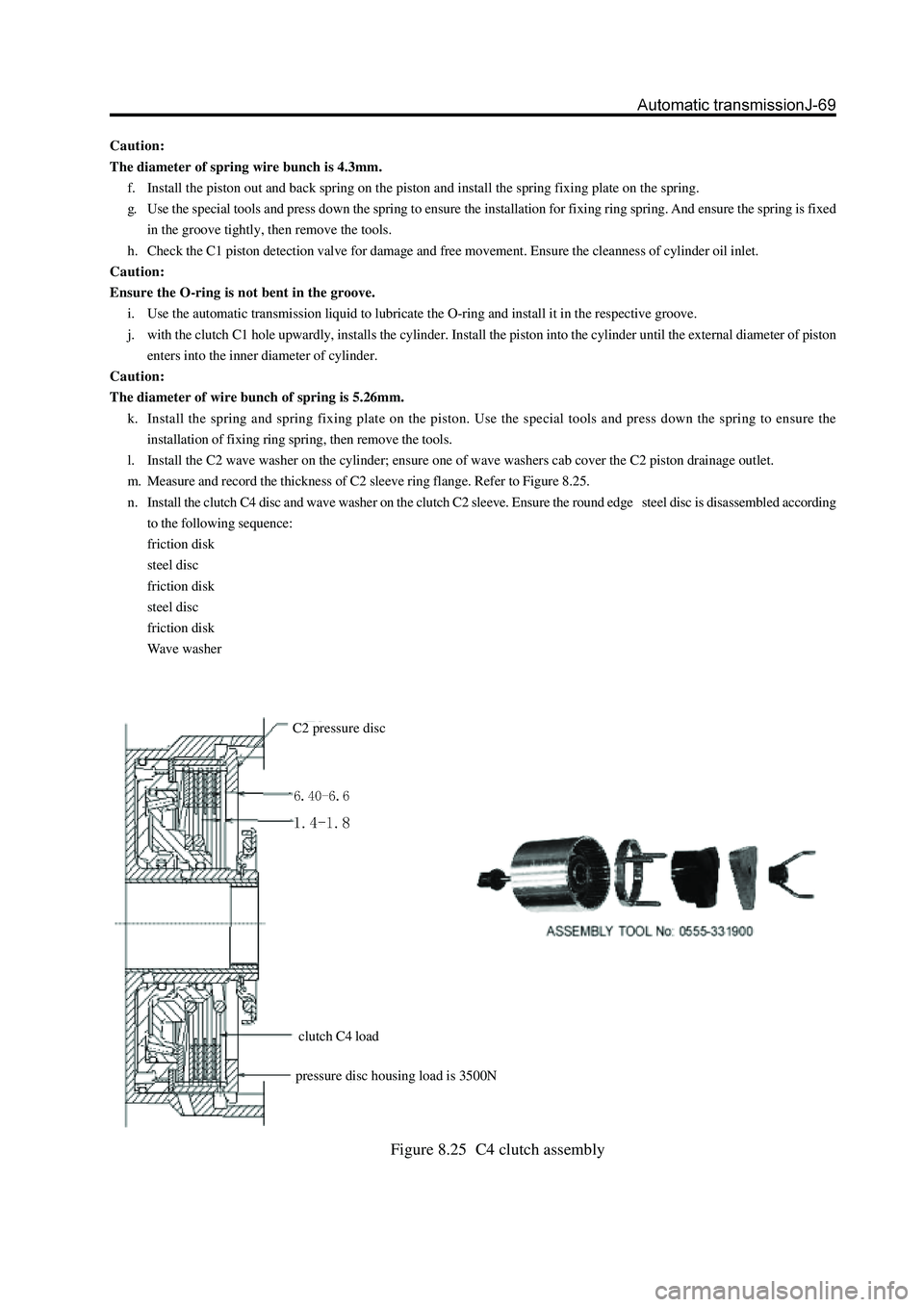
Figure 8.25 C4 clutch assembly
Caution:
The diameter of spring wire bunch is 4.3mm.
f. Install the piston out and back spring on the piston and install the spring fixing plate on the spring.
g. Use the special tools and press down the spring to ensure the installation for fixing ring spring. And ensure the spring is fixed
in the groove tightly, then remove the tools.
h. Check the C1 piston detection valve for damage and free movement. Ensure the cleanness of cylinder oil inlet.
Caution:
Ensure the O-ring is not bent in the groove.
i. Use the automatic transmission liquid to lubricate the O-ring and install it in the respective groove.
j. with the clutch C1 hole upwardly, installs the cylinder. Install the piston into the cylinder until the external diameter of piston
enters into the inner diameter of cylinder.
Caution:
The diameter of wire bunch of spring is 5.26mm.
k. Install the spring and spring fixing plate on the piston. Use the special tools and press down the spring to ensure the
installation of fixing ring spring, then remove the tools.
l. Install the C2 wave washer on the cylinder; ensure one of wave washers cab cover the C2 piston drainage outlet.
m. Measure and record the thickness of C2 sleeve ring flange. Refer to Figure 8.25.
n. Install the clutch C4 disc and wave washer on the clutch C2 sleeve. Ensure the round edge steel disc is disassembled according
to the following sequence:
friction disk
steel disc
friction disk
steel disc
friction disk
Wave washer
C2 pressure disc
pressure disc housing load is 3500N
clutch C4 load
Page 146 of 425
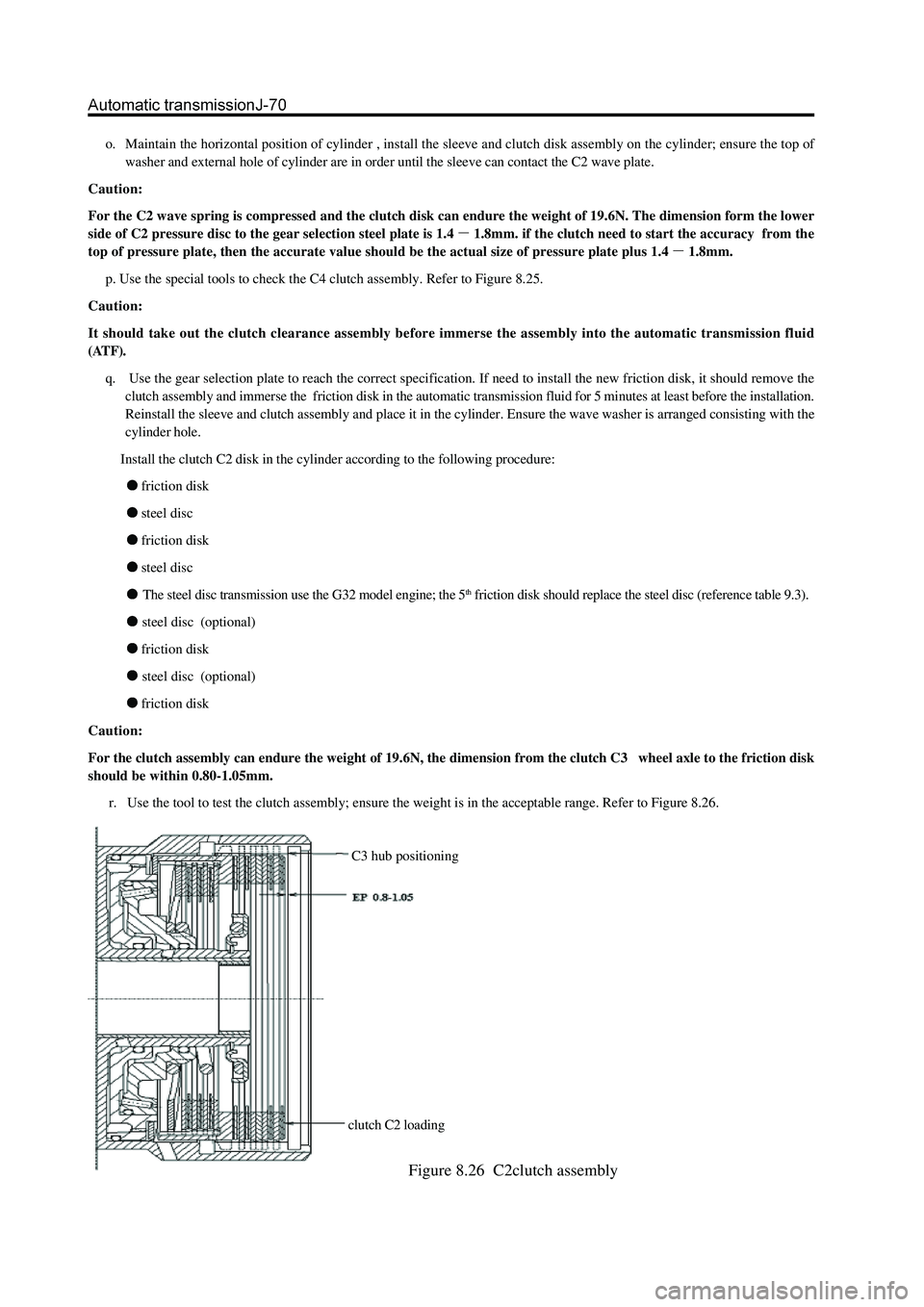
o. Maintain the horizontal position of cylinder , install the sleeve and clutch disk assembly on the cylinder; ensure the top of
washer and external hole of cylinder are in order until the sleeve can contact the C2 wave plate.
Caution:
For the C2 wave spring is compressed and the clutch disk can endure the weight of 19.6N. The dimension form the lower
side of C2 pressure disc to the gear selection steel plate is 1.4
1.8mm. if the clutch need to start the accuracy from the
top of pressure plate, then the accurate value should be the actual size of pressure plate plus 1.4
1.8mm.
p. Use the special tools to check the C4 clutch assembly. Refer to Figure 8.25.
Caution:
It should take out the clutch clearance assembly before immerse the assembly into the automatic transmission fluid
(ATF).
q. Use the gear selection plate to reach the correct specification. If need to install the new friction disk, it should remove the
clutch assembly and immerse the friction disk in the automatic transmission fluid for 5 minutes at least before the installation.
Reinstall the sleeve and clutch assembly and place it in the cylinder. Ensure the wave washer is arranged consisting with the
cylinder hole.
Install the clutch C2 disk in the cylinder according to the following procedure:
friction disk
steel disc
friction disk
steel disc
The steel disc transmission use the G32 model engine; the 5th friction disk should replace the steel disc (reference table 9.3).
steel disc (optional)
friction disk
steel disc (optional)
friction disk
Caution:
For the clutch assembly can endure the weight of 19.6N, the dimension from the clutch C3 wheel axle to the friction disk
should be within 0.80-1.05mm.
r. Use the tool to test the clutch assembly; ensure the weight is in the acceptable range. Refer to Figure 8.26.
C3 hub positioning
clutch C2 loading
Figure 8.26 C2clutch assembly
Page 147 of 425
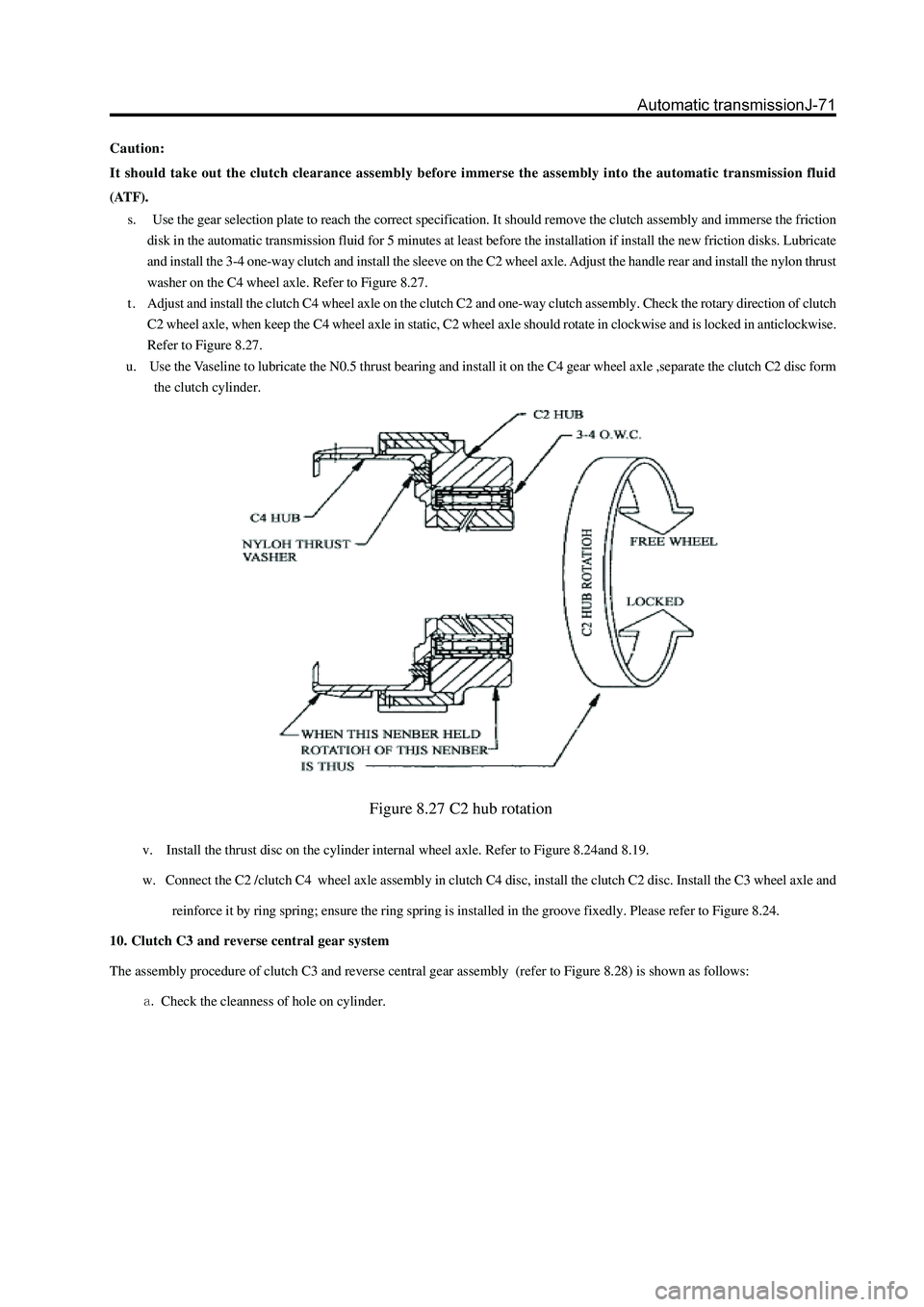
v. Install the thrust disc on the cylinder internal wheel axle. Refer to Figure 8.24and 8.19.
w. Connect the C2 /clutch C4 wheel axle assembly in clutch C4 disc, install the clutch C2 disc. Install the C3 wheel axle and
reinforce it by ring spring; ensure the ring spring is installed in the groove fixedly. Please refer to Figure 8.24.
10. Clutch C3 and reverse central gear system
The assembly procedure of clutch C3 and reverse central gear assembly (refer to Figure 8.28) is shown as follows:
Check the cleanness of hole on cylinder. Caution:
It should take out the clutch clearance assembly before immerse the assembly into the automatic transmission fluid
(ATF).
s. Use the gear selection plate to reach the correct specification. It should remove the clutch assembly and immerse the friction
disk in the automatic transmission fluid for 5 minutes at least before the installation if install the new friction disks. Lubricate
and install the 3-4 one-way clutch and install the sleeve on the C2 wheel axle. Adjust the handle rear and install the nylon thrust
washer on the C4 wheel axle. Refer to Figure 8.27.
t . Adjust and install the clutch C4 wheel axle on the clutch C2 and one-way clutch assembly. Check the rotary direction of clutch
C2 wheel axle, when keep the C4 wheel axle in static, C2 wheel axle should rotate in clockwise and is locked in anticlockwise.
Refer to Figure 8.27.
u. Use the Vaseline to lubricate the N0.5 thrust bearing and install it on the C4 gear wheel axle ,separate the clutch C2 disc form
the clutch cylinder.
Figure 8.27 C2 hub rotation
Page 148 of 425
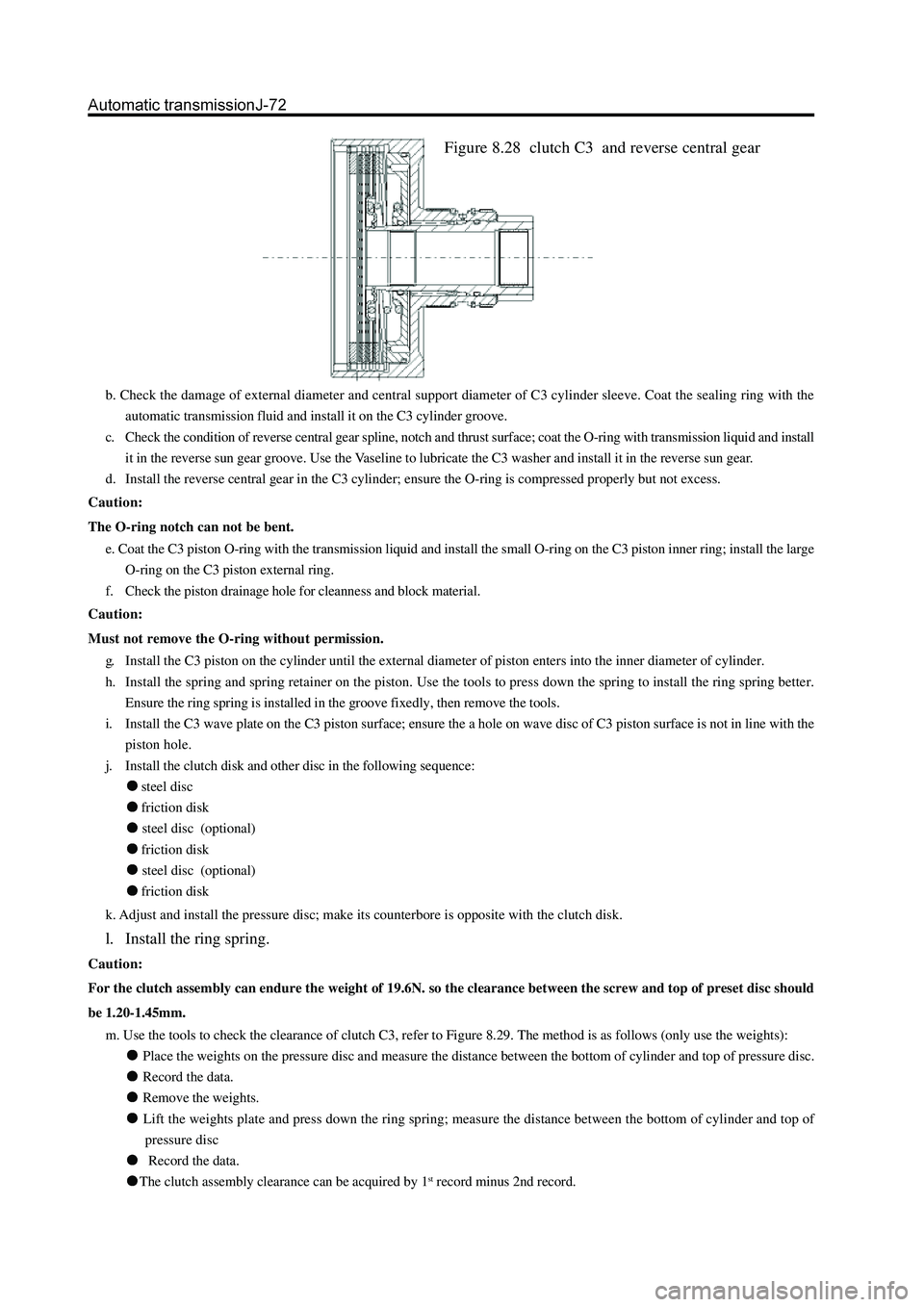
b. Check the damage of external diameter and central support diameter of C3 cylinder sleeve. Coat the sealing ring with the
automatic transmission fluid and install it on the C3 cylinder groove.
c. Check the condition of reverse central gear spline, notch and thrust surface; coat the O-ring with transmission liquid and install
it in the reverse sun gear groove. Use the Vaseline to lubricate the C3 washer and install it in the reverse sun gear.
d. Install the reverse central gear in the C3 cylinder; ensure the O-ring is compressed properly but not excess.
Caution:
The O-ring notch can not be bent.
e. Coat the C3 piston O-ring with the transmission liquid and install the small O-ring on the C3 piston inner ring; install the large
O-ring on the C3 piston external ring.
f. Check the piston drainage hole for cleanness and block material.
Caution:
Must not remove the O-ring without permission.
g. Install the C3 piston on the cylinder until the external diameter of piston enters into the inner diameter of cylinder.
h. Install the spring and spring retainer on the piston. Use the tools to press down the spring to install the ring spring better.
Ensure the ring spring is installed in the groove fixedly, then remove the tools.
i. Install the C3 wave plate on the C3 piston surface; ensure the a hole on wave disc of C3 piston surface is not in line with the
piston hole.
j. Install the clutch disk and other disc in the following sequence:
steel disc
friction disk
steel disc (optional)
friction disk
steel disc (optional)
friction disk
k. Adjust and install the pressure disc; make its counterbore is opposite with the clutch disk.
l. Install the ring spring.
Caution:
For the clutch assembly can endure the weight of 19.6N. so the clearance between the screw and top of preset disc should
be 1.20-1.45mm.
m. Use the tools to check the clearance of clutch C3, refer to Figure 8.29. The method is as follows (only use the weights):
Place the weights on the pressure disc and measure the distance between the bottom of cylinder and top of pressure disc.
Record the data.
Remove the weights.
Lift the weights plate and press down the ring spring; measure the distance between the bottom of cylinder and top of
pressure disc
Record the data.
The clutch assembly clearance can be acquired by 1st record minus 2nd record.
Figure 8.28 clutch C3 and reverse central gear
Page 149 of 425
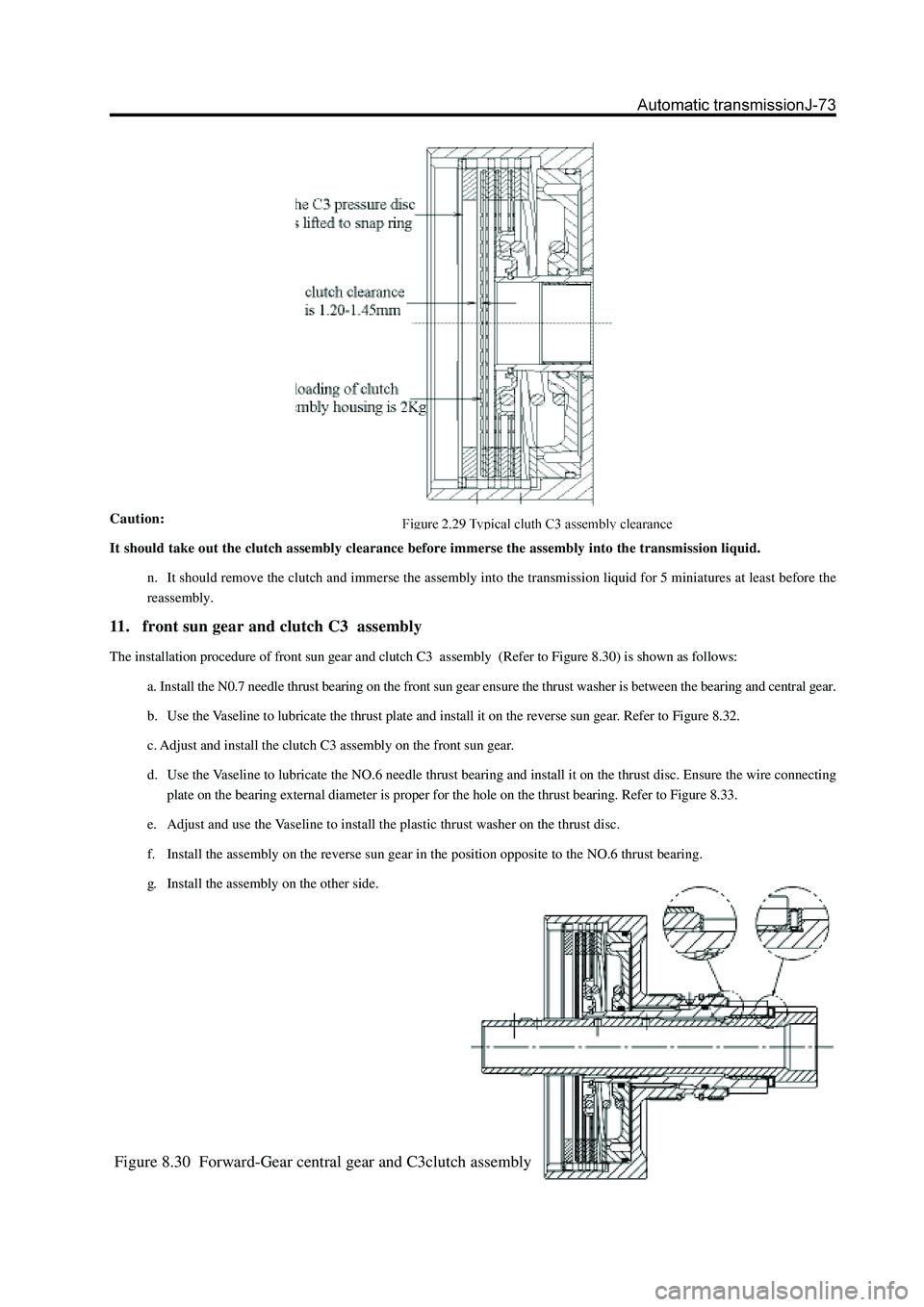
Figure 8.30 Forward-Gear central gear and C3clutch assembly
Caution:
It should take out the clutch assembly clearance before immerse the assembly into the transmission liquid.
n. It should remove the clutch and immerse the assembly into the transmission liquid for 5 miniatures at least before the
reassembly.
11. front sun gear and clutch C3 assembly
The installation procedure of front sun gear and clutch C3 assembly (Refer to Figure 8.30) is shown as follows:
a. Install the N0.7 needle thrust bearing on the front sun gear ensure the thrust washer is between the bearing and central gear.
b. Use the Vaseline to lubricate the thrust plate and install it on the reverse sun gear. Refer to Figure 8.32.
c. Adjust and install the clutch C3 assembly on the front sun gear.
d. Use the Vaseline to lubricate the NO.6 needle thrust bearing and install it on the thrust disc. Ensure the wire connecting
plate on the bearing external diameter is proper for the hole on the thrust bearing. Refer to Figure 8.33.
e. Adjust and use the Vaseline to install the plastic thrust washer on the thrust disc.
f. Install the assembly on the reverse sun gear in the position opposite to the NO.6 thrust bearing.
g. Install the assembly on the other side.
Page 150 of 425
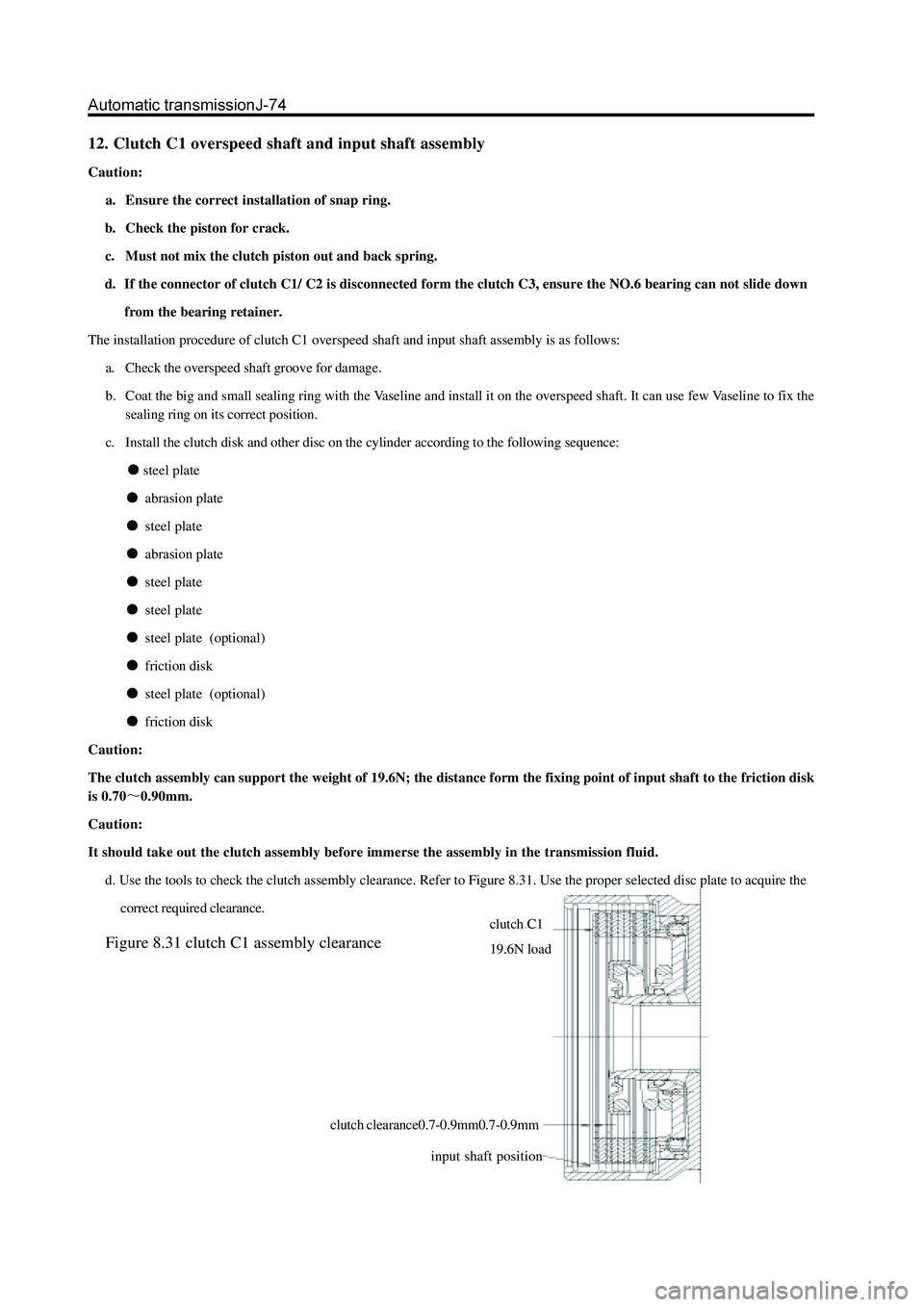
12. Clutch C1 overspeed shaft and input shaft assembly
Caution:
a. Ensure the correct installation of snap ring.
b. Check the piston for crack.
c. Must not mix the clutch piston out and back spring.
d. If the connector of clutch C1/ C2 is disconnected form the clutch C3, ensure the NO.6 bearing can not slide down
from the bearing retainer.
The installation procedure of clutch C1 overspeed shaft and input shaft assembly is as follows:
a. Check the overspeed shaft groove for damage.
b. Coat the big and small sealing ring with the Vaseline and install it on the overspeed shaft. It can use few Vaseline to fix the
sealing ring on its correct position.
c. Install the clutch disk and other disc on the cylinder according to the following sequence:
steel plate
abrasion plate
steel plate
abrasion plate
steel plate
steel plate
steel plate (optional)
friction disk
steel plate (optional)
friction disk
Caution:
The clutch assembly can support the weight of 19.6N; the distance form the fixing point of input shaft to the friction disk
is 0.70
0.90mm.
Caution:
It should take out the clutch assembly before immerse the assembly in the transmission fluid.
d. Use the tools to check the clutch assembly clearance. Refer to Figure 8.31. Use the proper selected disc plate to acquire the
correct required clearance.
Figure 8.31 clutch C1 assembly clearance
clutch C1
19.6N load
input shaft position
clutch clearance0.7-0.9mm0.7-0.9mm
Page 151 of 425
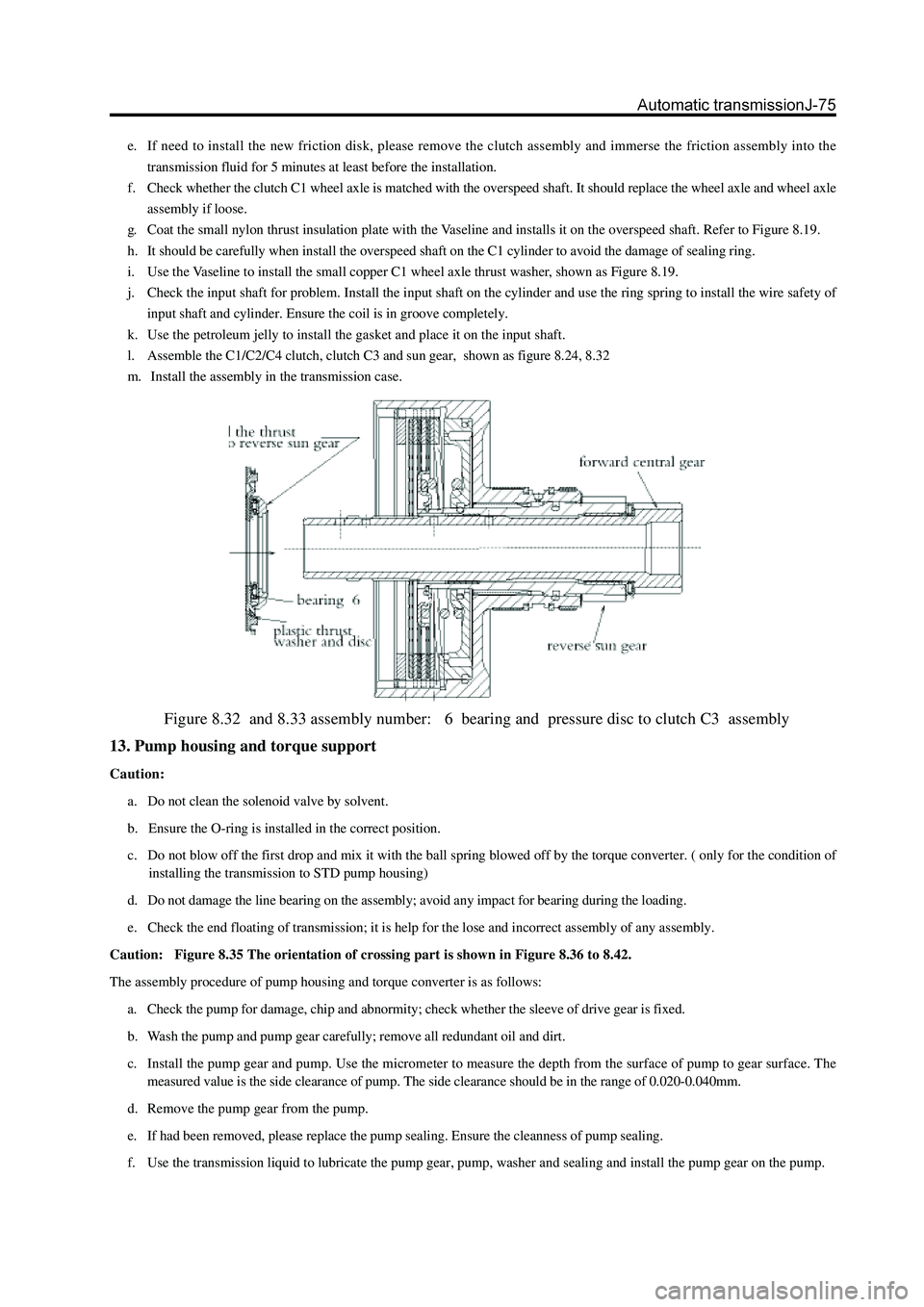
e. If need to install the new friction disk, please remove the clutch assembly and immerse the friction assembly into the
transmission fluid for 5 minutes at least before the installation.
f. Check whether the clutch C1 wheel axle is matched with the overspeed shaft. It should replace the wheel axle and wheel axle
assembly if loose.
g. Coat the small nylon thrust insulation plate with the Vaseline and installs it on the overspeed shaft. Refer to Figure 8.19.
h. It should be carefully when install the overspeed shaft on the C1 cylinder to avoid the damage of sealing ring.
i. Use the Vaseline to install the small copper C1 wheel axle thrust washer, shown as Figure 8.19.
j. Check the input shaft for problem. Install the input shaft on the cylinder and use the ring spring to install the wire safety of
input shaft and cylinder. Ensure the coil is in groove completely.
k. Use the petroleum jelly to install the gasket and place it on the input shaft.
l. Assemble the C1/C2/C4 clutch, clutch C3 and sun gear, shown as figure 8.24, 8.32
m. Install the assembly in the transmission case.
Figure 8.32 and 8.33 assembly number: 6 bearing and pressure disc to clutch C3 assembly
13. Pump housing and torque support
Caution:
a. Do not clean the solenoid valve by solvent.
b. Ensure the O-ring is installed in the correct position.
c. Do not blow off the first drop and mix it with the ball spring blowed off by the torque converter. ( only for the condition of
installing the transmission to STD pump housing)
d. Do not damage the line bearing on the assembly; avoid any impact for bearing during the loading.
e. Check the end floating of transmission; it is help for the lose and incorrect assembly of any assembly.
Caution: Figure 8.35 The orientation of crossing part is shown in Figure 8.36 to 8.42.
The assembly procedure of pump housing and torque converter is as follows:
a. Check the pump for damage, chip and abnormity; check whether the sleeve of drive gear is fixed.
b. Wash the pump and pump gear carefully; remove all redundant oil and dirt.
c. Install the pump gear and pump. Use the micrometer to measure the depth from the surface of pump to gear surface. The
measured value is the side clearance of pump. The side clearance should be in the range of 0.020-0.040mm.
d. Remove the pump gear from the pump.
e. If had been removed, please replace the pump sealing. Ensure the cleanness of pump sealing.
f. Use the transmission liquid to lubricate the pump gear, pump, washer and sealing and install the pump gear on the pump.
Page 152 of 425
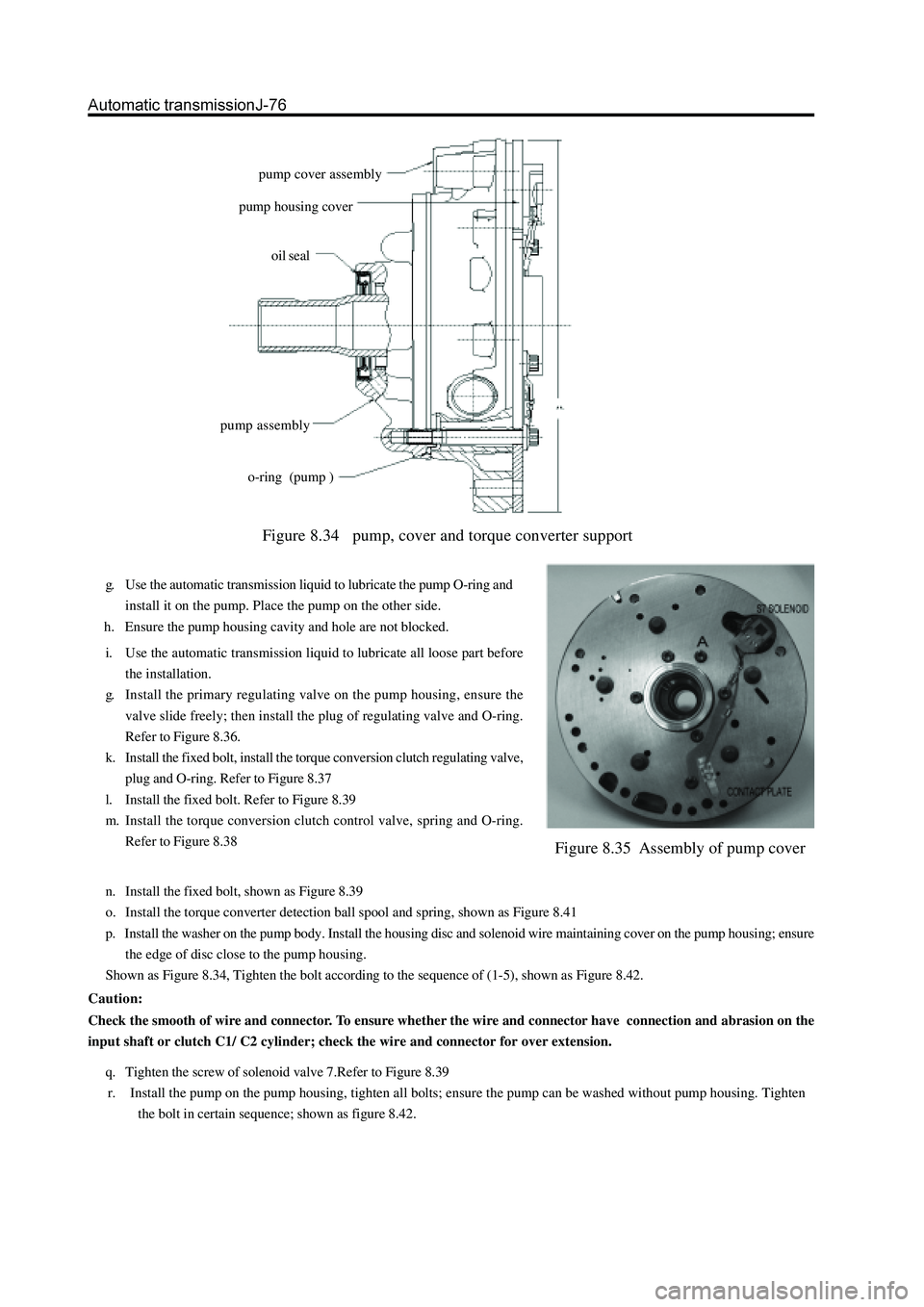
Figure 8.34 pump, cover and torque converter support
g. Use the automatic transmission liquid to lubricate the pump O-ring and
install it on the pump. Place the pump on the other side.
h. Ensure the pump housing cavity and hole are not blocked.
Figure 8.35 Assembly of pump cover
i. Use the automatic transmission liquid to lubricate all loose part before
the installation.
g. Install the primary regulating valve on the pump housing, ensure the
valve slide freely; then install the plug of regulating valve and O-ring.
Refer to Figure 8.36.
k. Install the fixed bolt, install the torque conversion clutch regulating valve,
plug and O-ring. Refer to Figure 8.37
l. Install the fixed bolt. Refer to Figure 8.39
m. Install the torque conversion clutch control valve, spring and O-ring.
Refer to Figure 8.38pump cover assembly
pump housing cover
oil seal
pump assembly
o-ring (pump )
n. Install the fixed bolt, shown as Figure 8.39
o. Install the torque converter detection ball spool and spring, shown as Figure 8.41
p. Install the washer on the pump body. Install the housing disc and solenoid wire maintaining cover on the pump housing; ensure
the edge of disc close to the pump housing.
Shown as Figure 8.34, Tighten the bolt according to the sequence of (1-5), shown as Figure 8.42.
Caution:
Check the smooth of wire and connector. To ensure whether the wire and connector have connection and abrasion on the
input shaft or clutch C1/ C2 cylinder; check the wire and connector for over extension.
q. Tighten the screw of solenoid valve 7.Refer to Figure 8.39
r. Install the pump on the pump housing, tighten all bolts; ensure the pump can be washed without pump housing. Tighten
the bolt in certain sequence; shown as figure 8.42.