Page 33 of 425
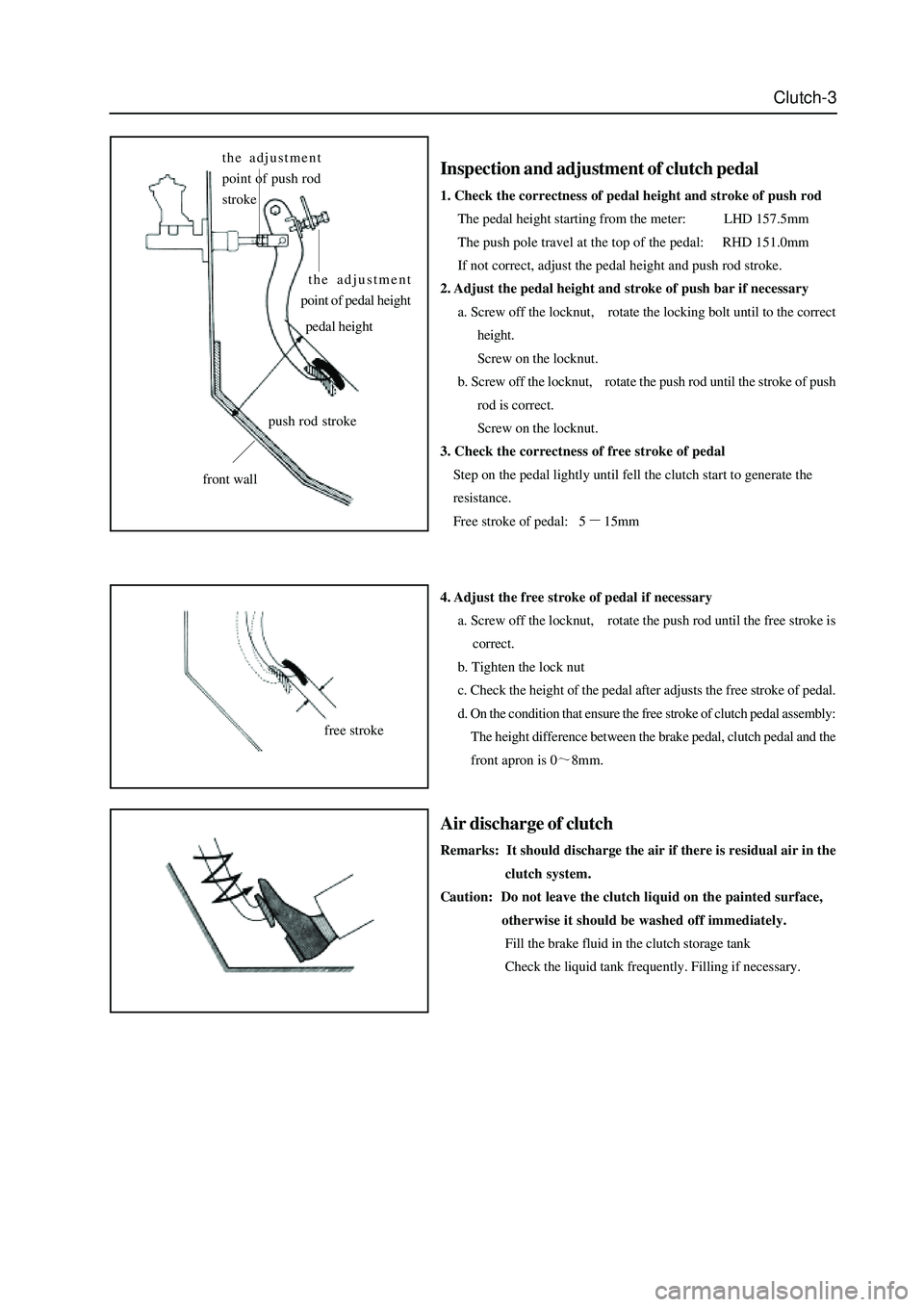
Clutch-3
Inspection and adjustment of clutch pedal
1. Check the correctness of pedal height and stroke of push rod
The pedal height starting from the meter: LHD 157.5mm
The push pole travel at the top of the pedal: RHD 151.0mm
If not correct, adjust the pedal height and push rod stroke.
2. Adjust the pedal height and stroke of push bar if necessary
a. Screw off the locknut, rotate the locking bolt until to the correct
height.
Screw on the locknut.
b. Screw off the locknut, rotate the push rod until the stroke of push
rod is correct.
Screw on the locknut.
3. Check the correctness of free stroke of pedal
Step on the pedal lightly until fell the clutch start to generate the
resistance.
Free stroke of pedal: 5
15mm
4. Adjust the free stroke of pedal if necessary
a. Screw off the locknut, rotate the push rod until the free stroke is
correct.
b. Tighten the lock nut
c. Check the height of the pedal after adjusts the free stroke of pedal.
d. On the condition that ensure the free stroke of clutch pedal assembly:
The height difference between the brake pedal, clutch pedal and the
front apron is 0
8mm.
Air discharge of clutch
Remarks: It should discharge the air if there is residual air in the
clutch system.
Caution: Do not leave the clutch liquid on the painted surface,
otherwise it should be washed off immediately.
Fill the brake fluid in the clutch storage tank
Check the liquid tank frequently. Filling if necessary.
the adjustment
point of push rod
stroke
the adjustment
point of pedal height
pedal height
front wall
free stroke
push rod stroke
Page 34 of 425
Clutch-4
Cluch control mechanism
clutch master cylinder
N
m: specified torque
Page 35 of 425
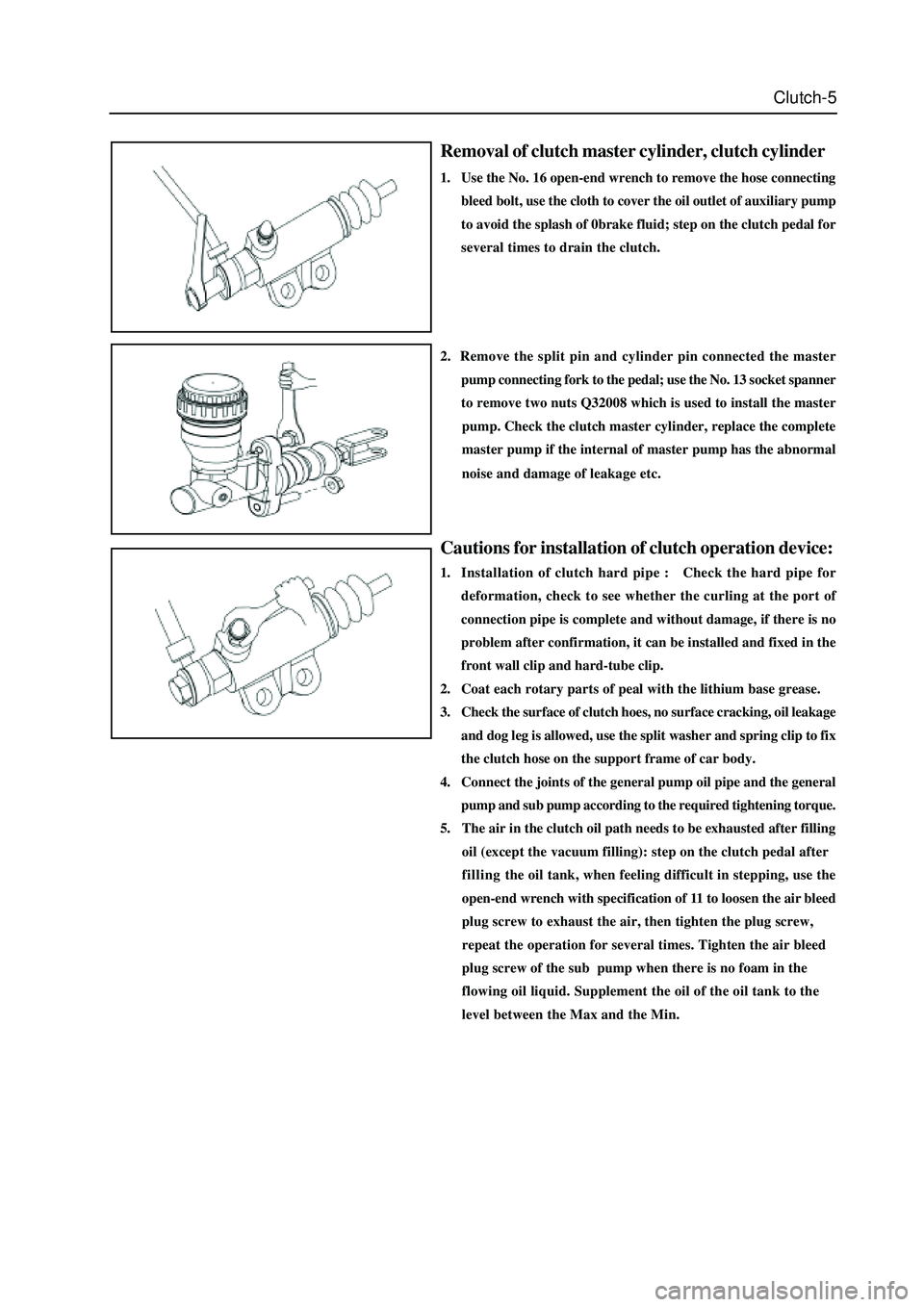
Clutch-5
Removal of clutch master cylinder, clutch cylinder
1. Use the No. 16 open-end wrench to remove the hose connecting
bleed bolt, use the cloth to cover the oil outlet of auxiliary pump
to avoid the splash of 0brake fluid; step on the clutch pedal for
several times to drain the clutch.
Cautions for installation of clutch operation device:
1. Installation of clutch hard pipe : Check the hard pipe for
deformation, check to see whether the curling at the port of
connection pipe is complete and without damage, if there is no
problem after confirmation, it can be installed and fixed in the
front wall clip and hard-tube clip.
2. Coat each rotary parts of peal with the lithium base grease.
3. Check the surface of clutch hoes, no surface cracking, oil leakage
and dog leg is allowed, use the split washer and spring clip to fix
the clutch hose on the support frame of car body.
4. Connect the joints of the general pump oil pipe and the general
2. Remove the split pin and cylinder pin connected the master
pump connecting fork to the pedal; use the No. 13 socket spanner
to remove two nuts Q32008 which is used to install the master
pump. Check the clutch master cylinder, replace the complete
master pump if the internal of master pump has the abnormal
noise and damage of leakage etc.
pump and sub pump according to the required tightening torque.
5. The air in the clutch oil path needs to be exhausted after filling
oil (except the vacuum filling): step on the clutch pedal after
fillingthe oil tank, when feeling difficult in stepping, use the
open-end wrench with specification of 11 to loosen the air bleed
plug screw to exhaust the air, then tighten the plug screw,
repeat the operation for several times. Tighten the air bleed
plug screw of the sub pump when there is no foam in the
flowing oil liquid. Supplement the oil of the oil tank to the
level between the Max and the Min.
Page 36 of 425
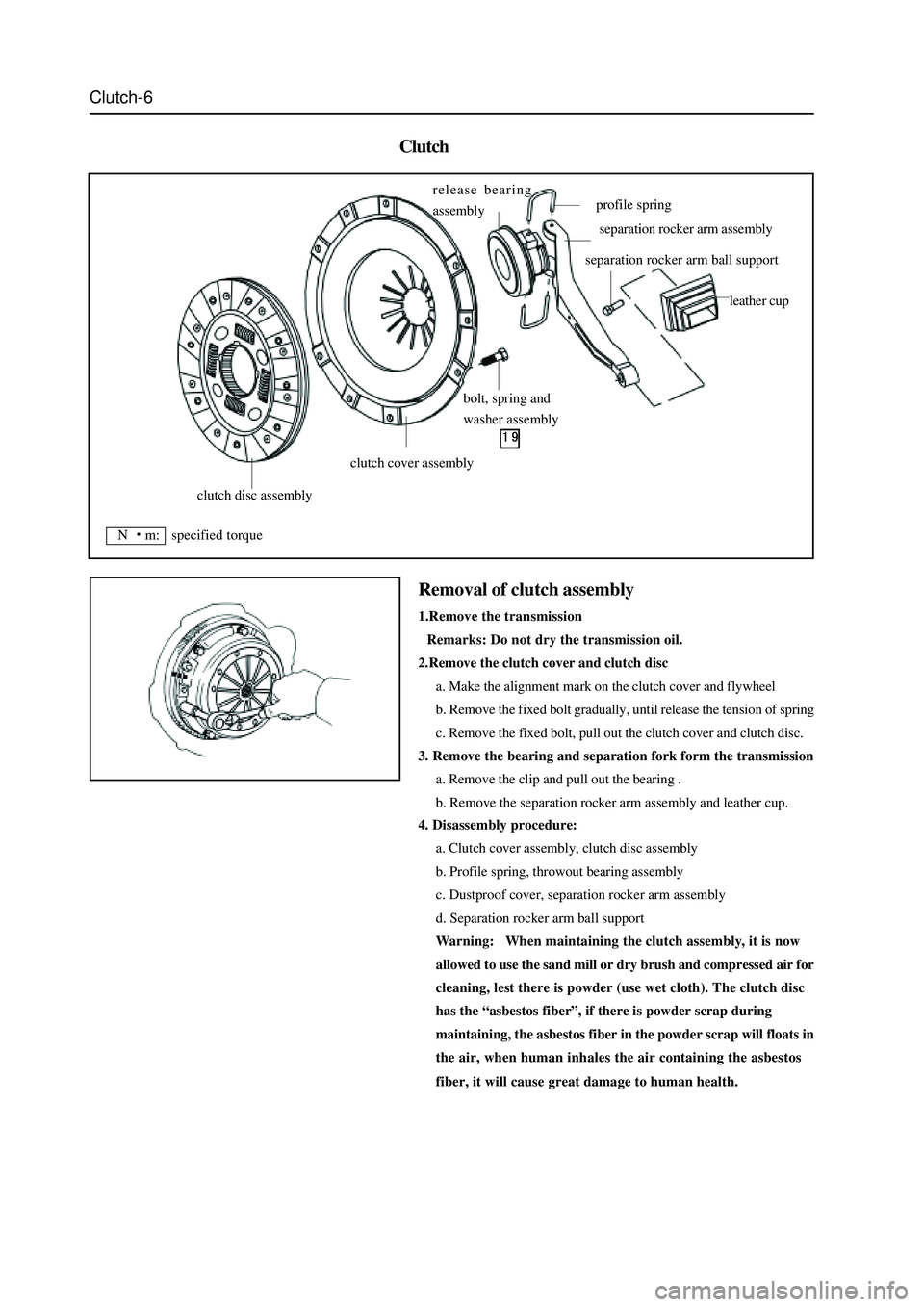
Clutch-6
Clutch
4. Disassembly procedure:
a. Clutch cover assembly, clutch disc assembly
b. Profile spring, throwout bearing assembly
c. Dustproof cover, separation rocker arm assembly
d. Separation rocker arm ball support
Warning: When maintaining the clutch assembly, it is now
allowed to use the sand mill or dry brush and compressed air for
cleaning, lest there is powder (use wet cloth). The clutch disc
has the “asbestos fiber”, if there is powder scrap during
maintaining, the asbestos fiber in the powder scrap will floats in
the air, when human inhales the air containing the asbestos
fiber, it will cause great damage to human health.
Removal of clutch assembly
1.Remove the transmission
Remarks: Do not dry the transmission oil.
2.Remove the clutch cover and clutch disc
a. Make the alignment mark on the clutch cover and flywheel
b. Remove the fixed bolt gradually, until release the tension of spring
c. Remove the fixed bolt, pull out the clutch cover and clutch disc.
3. Remove the bearing and separation fork form the transmission
a. Remove the clip and pull out the bearing .
b. Remove the separation rocker arm assembly and leather cup.
clutch disc assembly
clutch cover assembly
bolt, spring and
washer assembly release bearing
assembly
profile spring
separation rocker arm assembly
separation rocker arm ball support
leather cup
N m: specified torque
Page 37 of 425
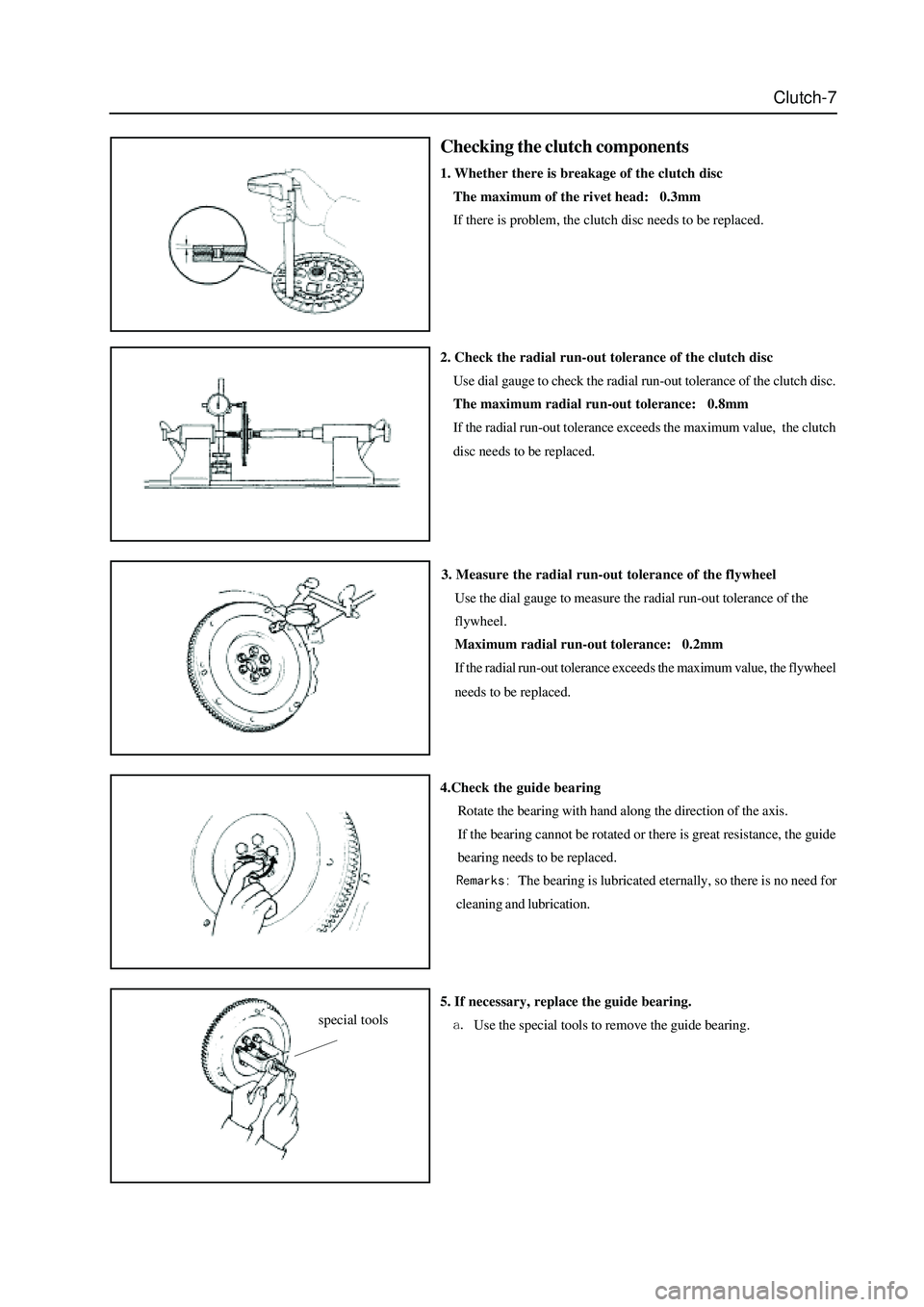
Clutch-7
Checking the clutch components
1. Whether there is breakage of the clutch disc
The maximum of the rivet head: 0.3mm
If there is problem, the clutch disc needs to be replaced.
3. Measure the radial run-out tolerance of the flywheel
Use the dial gauge to measure the radial run-out tolerance of the
flywheel.
Maximum radial run-out tolerance: 0.2mm
If the radial run-out tolerance exceeds the maximum value, the flywheel
needs to be replaced.
4.Check the guide bearing
Rotate the bearing with hand along the direction of the axis.
If the bearing cannot be rotated or there is great resistance, the guide
bearing needs to be replaced.
The bearing is lubricated eternally, so there is no need for
cleaning and lubrication. 2. Check the radial run-out tolerance of the clutch disc
Use dial gauge to check the radial run-out tolerance of the clutch disc.
The maximum radial run-out tolerance: 0.8mm
If the radial run-out tolerance exceeds the maximum value, the clutch
disc needs to be replaced.
5. If necessary, replace the guide bearing.
Use the special tools to remove the guide bearing.special tools
Page 38 of 425
Clutch-8
b. Use special tools to install the guide bearing
Remarks: Install the guide bearing into the flywheel, make
sure that the bearing can rotate well.
6. Check to see whether there is wearing of the diaphragm spring
Use caliper to check the wearing depth and width of the diaphragm
spring
Limit value: maximum depth 0.6mm
Maximum width 5.0mm
7. Check the throwout bearing
Rotate the bearing with hand along the axis direction.
If the bearing can not rotate or the resistance is too large, it is necessary
to replace the throwout bearing.
Remarks: The bearing is permanent lubricated, so cleaning
and lubricating is unnecessary.
special tools
Page 39 of 425
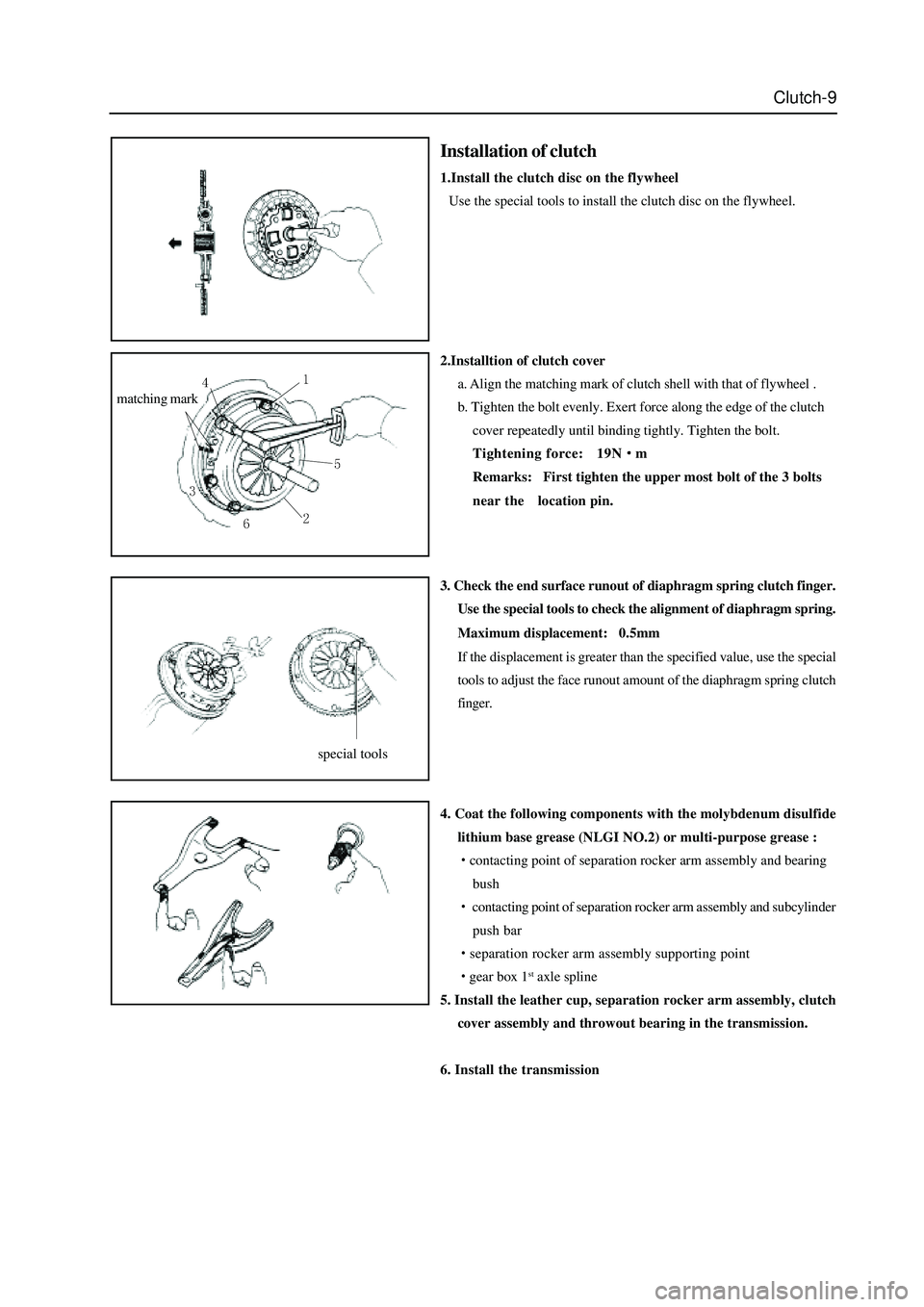
Clutch-9
2.Installtion of clutch cover
a. Align the matching mark of clutch shell with that of flywheel .
b. Tighten the bolt evenly. Exert force along the edge of the clutch
cover repeatedly until binding tightly. Tighten the bolt.
Tightening force: 19N
m
Remarks: First tighten the upper most bolt of the 3 bolts
near thelocation pin.
3. Check the end surface runout of diaphragm spring clutch finger.
Use the special tools to check the alignment of diaphragm spring.
Maximum displacement: 0.5mm
If the displacement is greater than the specified value, use the special
tools to adjust the face runout amount of the diaphragm spring clutch
finger.
4. Coat the following components with the molybdenum disulfide
lithium base grease (NLGI NO.2) or multi-purpose grease :
contacting point of separation rocker arm assembly and bearing
bush
contacting point of separation rocker arm assembly and subcylinder
push bar
separation rocker arm assembly supporting point
gear box 1st axle spline
5. Install the leather cup, separation rocker arm assembly, clutch
cover assembly and throwout bearing in the transmission.
6. Install the transmission
matching mark
Installation of clutch
1.Install the clutch disc on the flywheel
Use the special tools to install the clutch disc on the flywheel.
special tools
Page 40 of 425
Chapter 4
Specification of transmission.......................................................................2
Repair of transmission (SC5M2D
C).....................................................4
Disassembly of transmission (SC5M2D
C)............................................6
Disassembly of transmission housing assembly/bearing housing assembly....18
Operating instruction of transmission (SC5M4D
C).............................24
Repair of transmission (SC5M4D
C)...................................................25
Disassembly of rear housing assembly ......................................................28
Disassembly of transfer case assembly......................................................30
Rear output shaft assembly .......................................................................35