Page 281 of 425
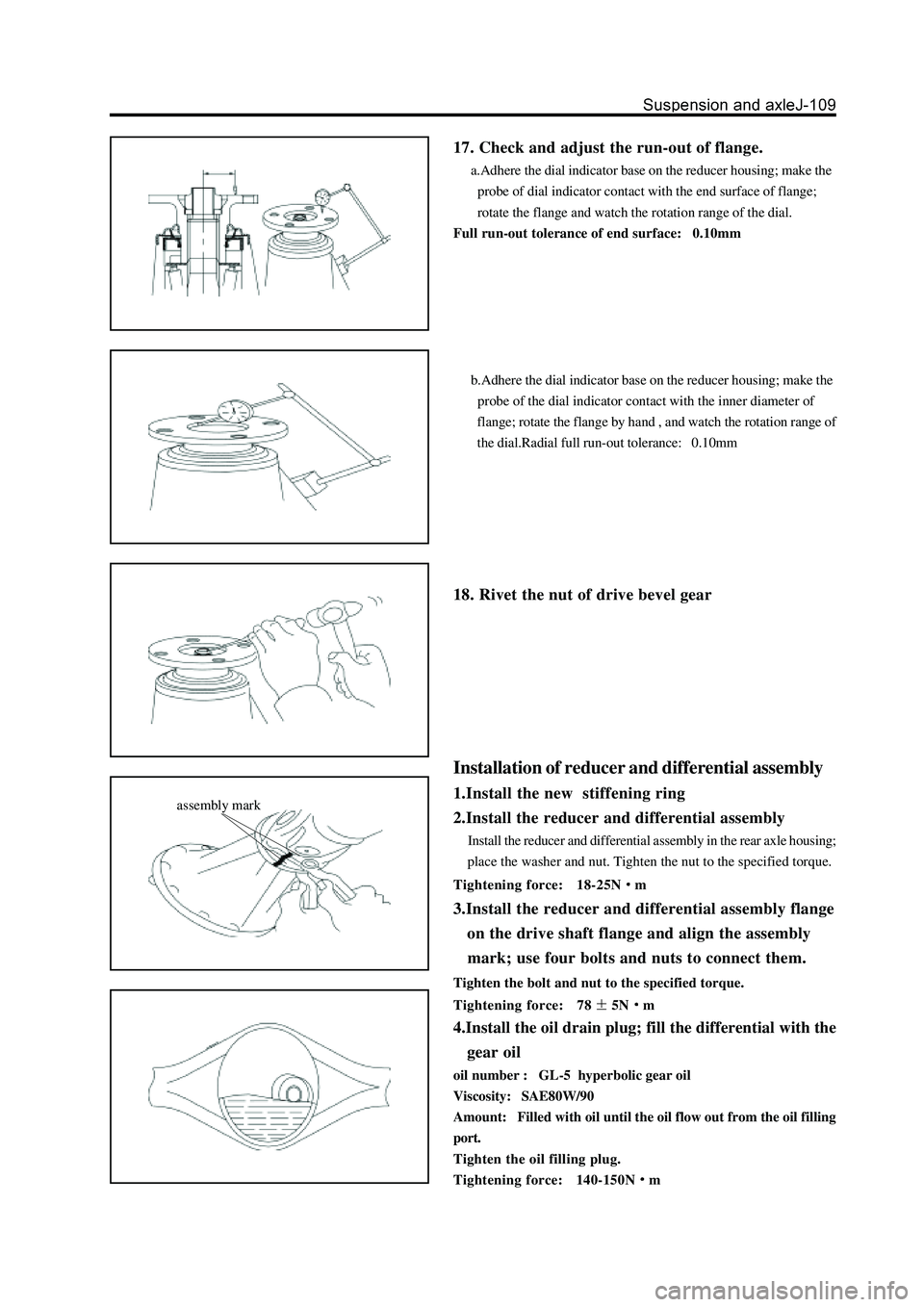
17. Check and adjust the run-out of flange.
a.Adhere the dial indicator base on the reducer housing; make the
probe of dial indicator contact with the end surface of flange;
rotate the flange and watch the rotation range of the dial.
Full run-out tolerance of end surface: 0.10mm
b.Adhere the dial indicator base on the reducer housing; make the
probe of the dial indicator contact with the inner diameter of
flange; rotate the flange by hand , and watch the rotation range of
the dial.Radial full run-out tolerance: 0.10mm
18. Rivet the nut of drive bevel gear
Installation of reducer and differential assembly
1.Install the new stiffening ring
2.Install the reducer and differential assembly
Install the reducer and differential assembly in the rear axle housing;
place the washer and nut. Tighten the nut to the specified torque.
Tightening force: 18-25N
m
3.Install the reducer and differential assembly flange
on the drive shaft flange and align the assembly
mark; use four bolts and nuts to connect them.
Tighten the bolt and nut to the specified torque.
Tightening force: 78
5Nm
4.Install the oil drain plug; fill the differential with the
gear oil
oil number : GL-5 hyperbolic gear oil
Viscosity: SAE80W/90
Amount: Filled with oil until the oil flow out from the oil filling
port.
Tighten the oil filling plug.
Tightening force: 140-150N
m
assembly mark
Page 282 of 425
Differential
Differential
1Remove the reducer and differential assembly
(Refer to “Removal of reducer”)
2Remove the differential from the reducer and dif
ferential assembly.
(Refer to “Disassembly of reducer”)
Replacement of differential components
1.Disassembly of differential
Use the hammer and punch to knock out the pin. Remove the
planetary gear shaft, two half axle gears, two planetary gears and
two lock washers, two thrust plates.
2. Assembly of differential
a.Install the half axle gear and thrust plate of axle shaft gear
(Unit: mm)
b.Install the planetary gear and planetary gear lock washer in the
differential by rolling. (Unit: mm)
differential housing
thrust plate
half axle
gear
straight pin
planetary gear
lock washer
half axle
gear
thrust plateplanetary gear
lock washer
planetary gear shaft
Set NO. 1 2
Thickness 1.2 1.5
Set NO.
Thickness
Page 283 of 425
c.Use the feeler to measure the clearance between the thrust plate
and differential housing; it can be replaced by the thrust plate with
different thickness if the clearance is beyond the specified range.
Standard clearance: 0.45-0.75mm
d.Install the straight pin
Use the hammer and punch to knock in the pin through the hole
on the differential housing and planetary gear shaft. Rivet the pin
with the differential housing.
Installation of differential
1Install the differential assembly in the reducer hous
ing
(Refer to “Assembly of Reducer”)
2Install the differential
(Refer to “Installation of Reducer and Differential Assembly”)
feeler
Page 284 of 425
Rear suspension
N m: specified torque
bush clip
bush
rear stabilizer barrear connecting rod of stabilizer bar assembly
plain washer
short longitudinal
pull-rod fixed bolt
rubber padshort longitudinal
pull-rod fixed bolt
long longitudinal
pull-rod assembly
long longitudinal
pull-rod fixed bolt
long longitudinal
pull-rodassembly
short longitudinal
pull-rod assembly
rear axle
assembly
coil spring
upper support pad
of coil spring
short longitudinal pull-rod assembly
long longitudinal
pull-rod assembly
rear vibration damper
cross pull-rod assembly
cross pull-rod
connecting bolt
Page 285 of 425
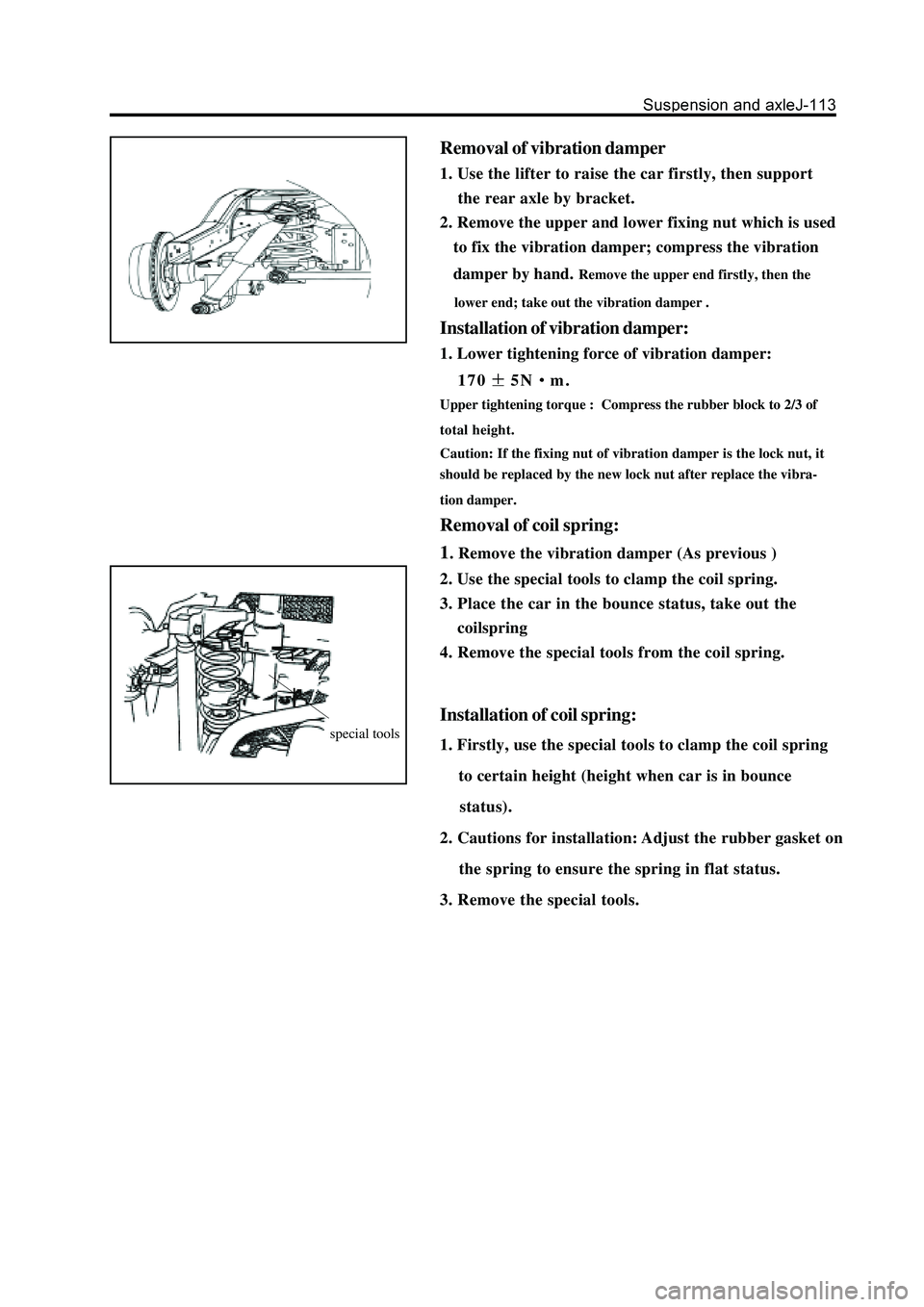
Removal of vibration damper
1. Use the lifter to raise the car firstly, then support
the rear axle by bracket.
2. Remove the upper and lower fixing nut which is used
to fix the vibration damper; compress the vibration
damper by hand.
Remove the upper end firstly, then the
lower end; take out the vibration damper .
Installation of vibration damper:
1. Lower tightening force of vibration damper:
170
5Nm.
Upper tightening torque : Compress the rubber block to 2/3 of
total height.
Caution: If the fixing nut of vibration damper is the lock nut, it
should be replaced by the new lock nut after replace the vibra-
tion damper.
Removal of coil spring:
1
. Remove the vibration damper (As previous )
2. Use the special tools to clamp the coil spring.
3. Place the car in the bounce status, take out the
coilspring
4. Remove the special tools from the coil spring.
Installation of coil spring:
1. Firstly, use the special tools to clamp the coil spring
to certain height (height when car is in bounce
status).
2. Cautions for installation: Adjust the rubber gasket on
the spring to ensure the spring in flat status.
3. Remove the special tools.special tools
Page 286 of 425
Removal of connecting rod of stabilizer bar:
1.Shown as figure, firstly screw off the nut in the con
necting place between the connecting rod of stabi
lizer bar and carriage. (Need the inner hexagon
spanner ).
2.Screw off the nut connected to stabilizer bar in same
method; screw off the connecting rod.
Installation of connecting rod of stabilizer bar:
Tighten it to the specified torque during installation:
63
5Nm
Page 287 of 425
Brake-1
Chapter 8
Brake
Cautions...................................................................................... 2
Troubleshooting............................................................................2
Check and adjustment..................................................................5
Brake pedal..................................................................................7
Parking brake...............................................................................8
Front brake...................................................................................9
Rear brake...................................................................................16
Rear parking brake......................................................................22
Sensor load proportional valve.....................................................29
Antilock Braking System (ABS)..................................................31
Page 288 of 425
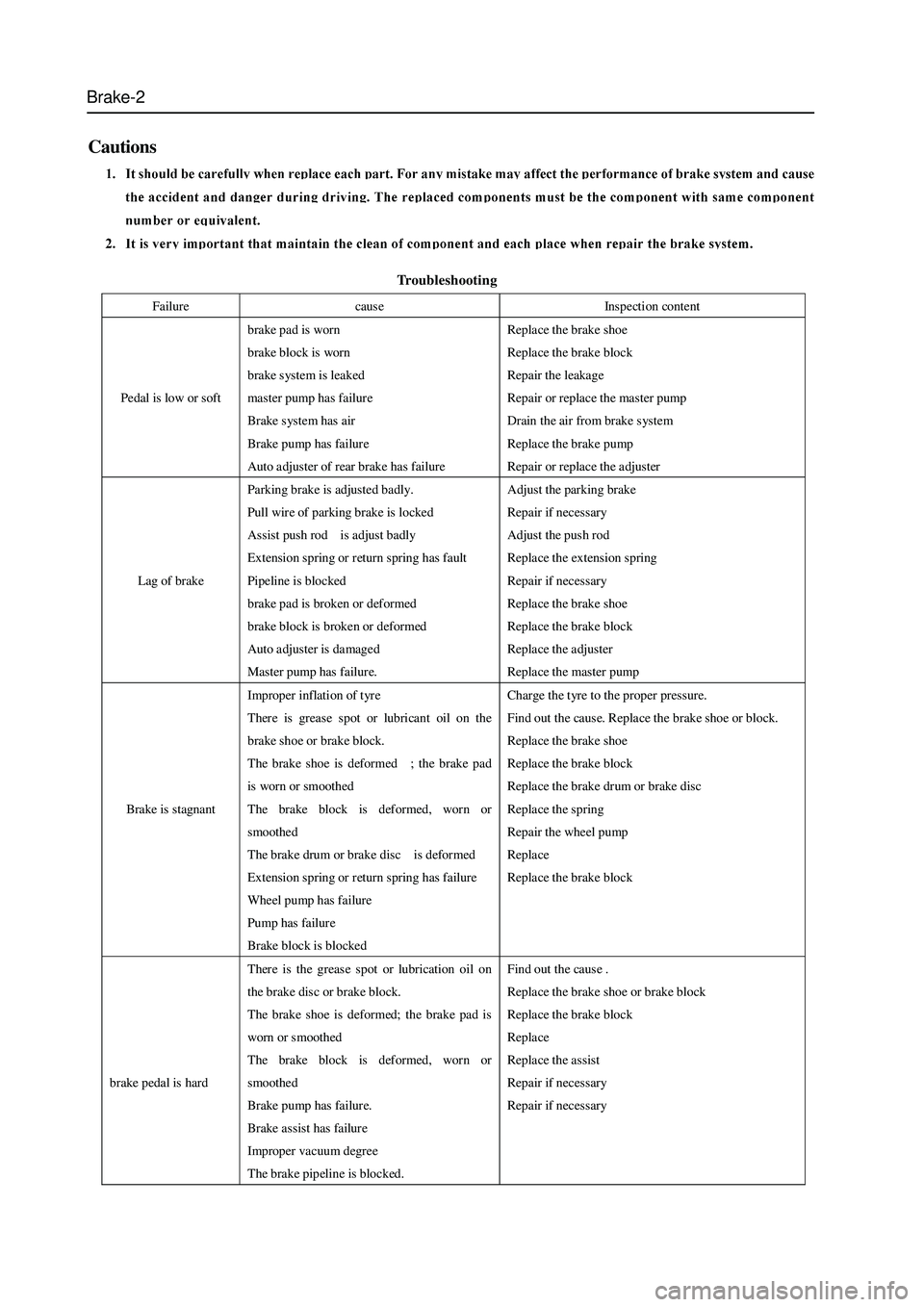
Brake-2
Troubleshooting
Cautions
Failure cause Inspection content
Pedal is low or soft brake pad is worn
brake block is worn
brake system is leaked
master pump has failure
Brake system has air
Brake pump has failure
Auto adjuster of rear brake has failure Replace the brake shoe
Replace the brake block
Repair the leakage
Repair or replace the master pump
Drain the air from brake system
Replace the brake pump
Repair or replace the adjuster
Lag of brake Parking brake is adjusted badly.
Pull wire of parking brake is locked
Assist push rod is adjust badly
Extension spring or return spring has fault
Pipeline is blocked
brake pad is broken or deformed
brake block is broken or deformed
Auto adjuster is damaged
Master pump has failure. Adjust the parking brake
Repair if necessary
Adjust the push rod
Repla ce the extension spring
Repair if necessary
Replace the brake shoe
Replace the brake block
Repla ce the a djuster
Repla ce the master pump
Brake is stagnant Improper inflation of tyre
There is grease spot or lubricant oil on the
brake shoe or brake block.
The brake shoe is deformed ; the brake pad
is worn or smoothed
The brake block is deformed, worn or
smoothed
The brake drum or brake disc is deformed
Extension spring or return spring has failure
Wheel pump has failure
Pump has failure
Brake block is blocked Charge the tyre to the proper pressure.
Find out the cause. Replace the brake shoe or block.
Replace the brake shoe
Replace the brake block
Replace the brake drum or brake disc
Repla ce the spring
Repair the wheel pump
Replace
Replace the brake block
brake pedal is hard There is the grease spot or lubrication oil on
the brake disc or brake block.
The brake shoe is deformed; the brake pad is
worn or s moothed
The brake block is deformed, worn or
smoothed
Brake pump has failure.
Brake assist has failure
Improper vacuum degree
The brake pipeline is blocked. Find out the caus e .
Replace the brake shoe or brake block
Replace the brake block
Replace
Replace the assist
Repair if necessary
Repair if necessary