Page 33 of 419
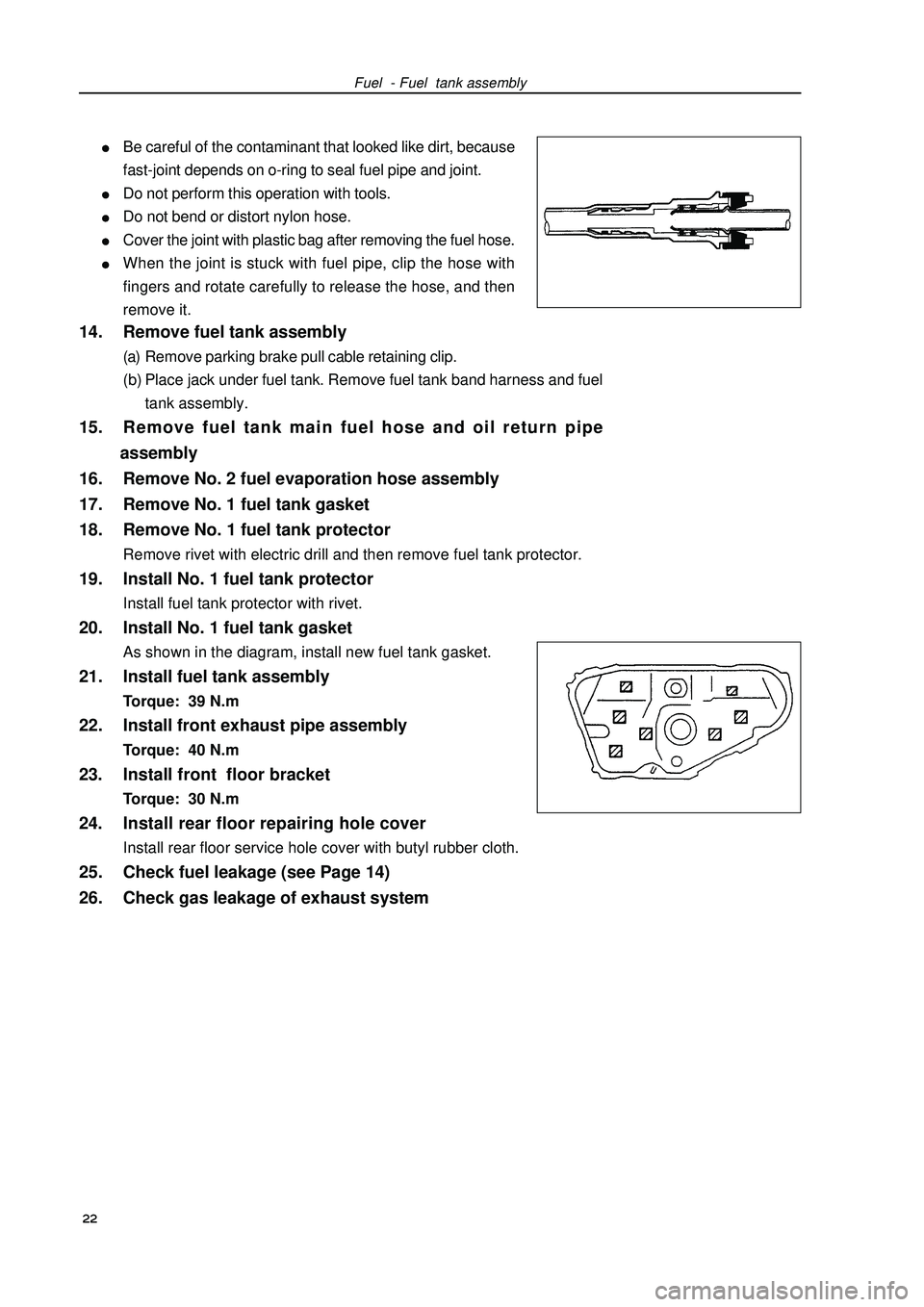
Fuel - Fuel tank assemblyBe careful of the contaminant that looked like dirt, because
fast-joint depends on o-ring to seal fuel pipe and joint.Do not perform this operation with tools.Do not bend or distort nylon hose.Cover the joint with plastic bag after removing the fuel hose.When the joint is stuck with fuel pipe, clip the hose with
fingers and rotate carefully to release the hose, and then
remove it.14. Remove fuel tank assembly(a) Remove parking brake pull cable retaining clip.
(b) Place jack under fuel tank. Remove fuel tank band harness and fuel
tank assembly.15. Remove fuel tank main fuel hose and oil return pipe
assembly
16. Remove No. 2 fuel evaporation hose assembly
17. Remove No. 1 fuel tank gasket
18. Remove No. 1 fuel tank protectorRemove rivet with electric drill and then remove fuel tank protector.19. Install No. 1 fuel tank protectorInstall fuel tank protector with rivet.20. Install No. 1 fuel tank gasketAs shown in the diagram, install new fuel tank gasket.21. Install fuel tank assemblyTorque: 39 N.m22. Install front exhaust pipe assemblyTorque: 40 N.m23. Install front floor bracketTorque: 30 N.m24. Install rear floor repairing hole coverInstall rear floor service hole cover with butyl rubber cloth.25. Check fuel leakage (see Page 14)
26. Check gas leakage of exhaust system
22
Page 34 of 419
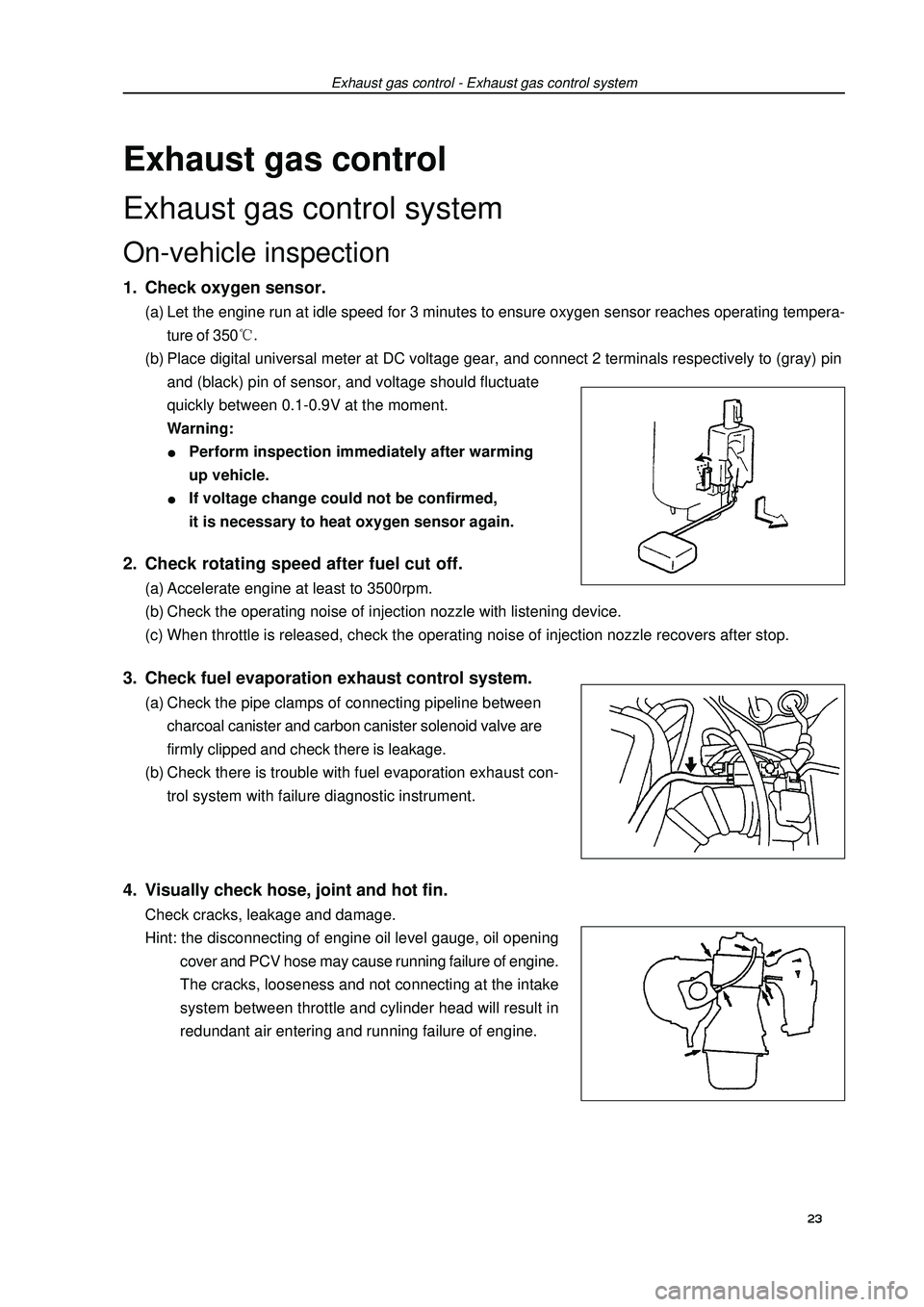
Exhaust gas controlExhaust gas control systemOn-vehicle inspection1. Check oxygen sensor.(a) Let the engine run at idle speed for 3 minutes to ensure oxygen sensor reaches operating tempera-
ture of 350(b) Place digital universal meter at DC voltage gear, and connect 2 terminals respectively to (gray) pin
and (black) pin of sensor, and voltage should fluctuate
quickly between 0.1-0.9V at the moment.
Warning:Perform inspection immediately after warming
up vehicle.If voltage change could not be confirmed,
it is necessary to heat oxygen sensor again.Exhaust gas control - Exhaust gas control system2. Check rotating speed after fuel cut off.(a) Accelerate engine at least to 3500rpm.
(b) Check the operating noise of injection nozzle with listening device.
(c) When throttle is released, check the operating noise of injection nozzle recovers after stop.3. Check fuel evaporation exhaust control system.(a) Check the pipe clamps of connecting pipeline between
charcoal canister and carbon canister solenoid valve are
firmly clipped and check there is leakage.
(b) Check there is trouble with fuel evaporation exhaust con-
trol system with failure diagnostic instrument.4. Visually check hose, joint and hot fin.Check cracks, leakage and damage.
Hint: the disconnecting of engine oil level gauge, oil opening
cover and PCV hose may cause running failure of engine.
The cracks, looseness and not connecting at the intake
system between throttle and cylinder head will result in
redundant air entering and running failure of engine.23
Page 35 of 419
5. Check heater resistance of heated oxygen sensor.(a) Uncouple oxygen sensor joint.
(b) Place digital universal meter at ohm gear, and connect 2 terminals respectively to 1# (white) pin and
2# (black) pin, and the resistance under normal temperature is 166. Check fuel tank cover.Visually check fuel tank cover and gasket are distorted or damaged.Exhaust gas control - Exhaust gas control system 24 Oxygen sensor
Main relay
Page 36 of 419
 Blow air into valve from cylinder side and check the air is
easy to get through.
Warning: do not suck against th GEELY FC 2008 Workshop Manual Exhaust gas control - Exhaust gas control system3. PCV valve assembly [4G18-1014110](a) Blow air into valve from cylinder side and check the air is
easy to get through.
Warning: do not suck against th](/manual-img/58/57161/w960_57161-35.png)
Exhaust gas control - Exhaust gas control system3. PCV valve assembly [4G18-1014110](a) Blow air into valve from cylinder side and check the air is
easy to get through.
Warning: do not suck against the valve, because the
gasoline left in the valve will make you be
injured.
(b) Blow air into valve from intake manifold side and check
the air is hard to get through.
Hint: if the function does not conform to the standard, PCV
valve should be replaced.Inspection1. Carbon canister assembly [4G18-1129020]Carbonl canister assembly. Check the function of carbon can-
ister according to the following tables.
Standard:2. Carbon canister control valve(a) For carbon canister control valve, check the conduction be-
tween terminals.
Resistance: (b) Check the control valve operates.
(1) Supply battery voltage to its terminal.
(2) Check air is flown as the arrow direction on valve body. 25Inspection Methods Standard
Close B hole and C hole and then
supply vacuum to A hole No leakage
Close C hole and then supply vacuum Air flown out
to A hole from B hole
Close C hole and then blow air Air flown out
into A hole from B hole
Blow air into A hole Air flown out from B hole
and C holeClean hose Cylinder side
Intake manifold side
Page 37 of 419
![GEELY FC 2008 Workshop Manual Engine mechanismEngine assemblyInspection1. Check coolant.
2. Check engine oil.
3. Check battery.
4. Check air filter assembly.
5. Check spark plug [4G18-3705113].
6. Check drive belt [4G18-1307107].H GEELY FC 2008 Workshop Manual Engine mechanismEngine assemblyInspection1. Check coolant.
2. Check engine oil.
3. Check battery.
4. Check air filter assembly.
5. Check spark plug [4G18-3705113].
6. Check drive belt [4G18-1307107].H](/manual-img/58/57161/w960_57161-36.png)
Engine mechanismEngine assemblyInspection1. Check coolant.
2. Check engine oil.
3. Check battery.
4. Check air filter assembly.
5. Check spark plug [4G18-3705113].
6. Check drive belt [4G18-1307107].Hint: do not check belt tension, because automatic tensioner is applied.7. Check ignition timing.(a) Warm up engine.
(b) Connect timing lamp to engine.
(c) Check ignition timing at idle speed.
Ignition timing: before top dead center Note: when checking ignition timing, place
transmission at neutral position.
Hint: After run the engine for 5 seconds with rotating
speed of 1000-1300rpm, check the engine could
recover to idle running.8. Check engine idle speed.(a) Warm up engine and run it at idle speed.
(b) Read engine rotating number in data flow with diagnostic instrument.
(c) Check idle speed.
Idle speed: about 750-850rpm
Notes:When checking idle speed, place cooling fan at OFF position.Turn off all auxiliary devices and air conditioner.Engine mechanism - Engine assemblyK-line 26
Page 38 of 419
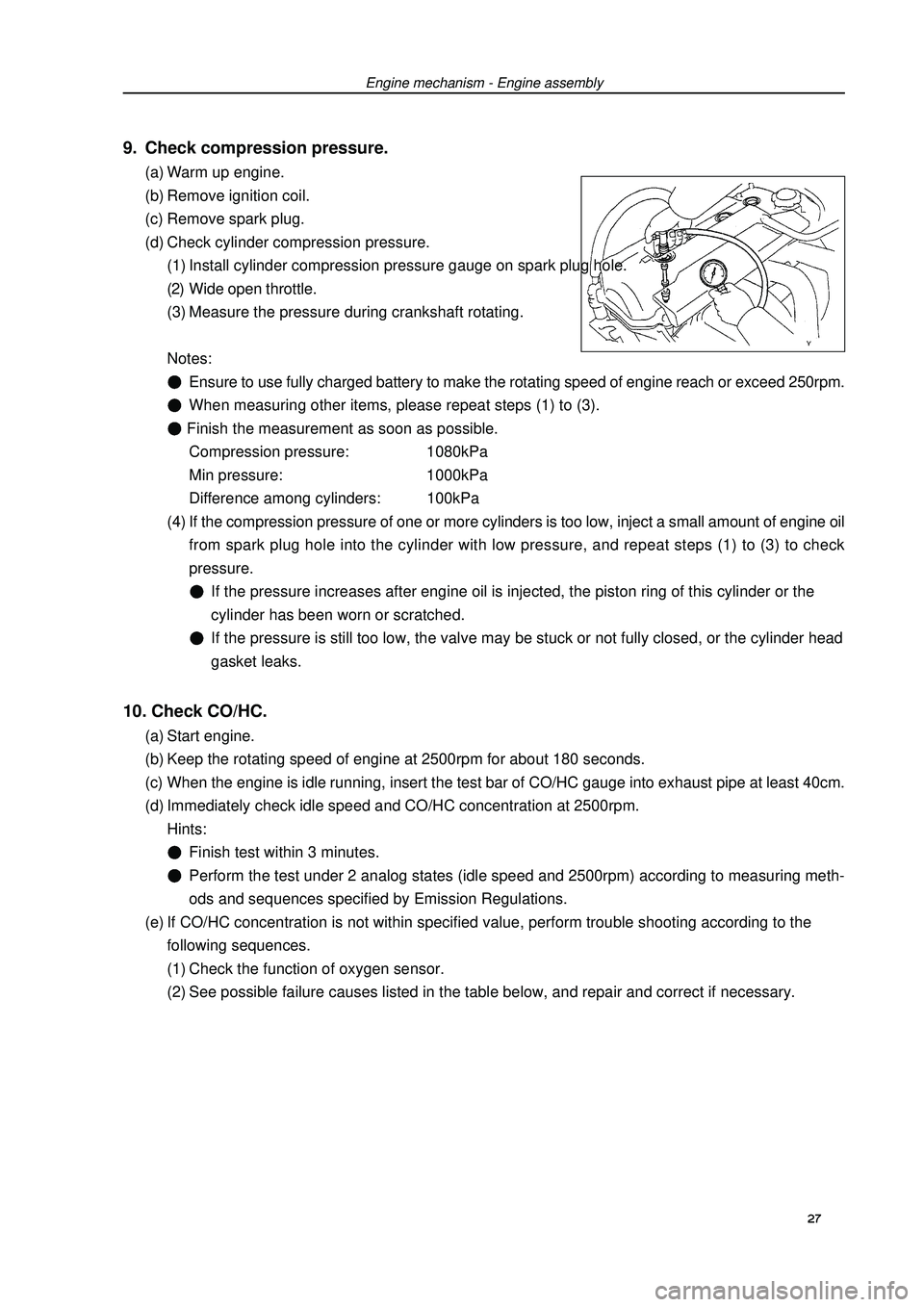
9. Check compression pressure.(a) Warm up engine.
(b) Remove ignition coil.
(c) Remove spark plug.
(d) Check cylinder compression pressure.
(1) Install cylinder compression pressure gauge on spark plug hole.
(2) Wide open throttle.
(3) Measure the pressure during crankshaft rotating.
Notes:Ensure to use fully charged battery to make the rotating speed of engine reach or exceed 250rpm.When measuring other items, please repeat steps (1) to (3). Finish the measurement as soon as possible.
Compression pressure: 1080kPa
Min pressure: 1000kPa
Difference among cylinders: 100kPa
(4) If the compression pressure of one or more cylinders is too low, inject a small amount of engine oil
from spark plug hole into the cylinder with low pressure, and repeat steps (1) to (3) to check
pressure.If the pressure increases after engine oil is injected, the piston ring of this cylinder or the
cylinder has been worn or scratched.If the pressure is still too low, the valve may be stuck or not fully closed, or the cylinder head
gasket leaks.10. Check CO/HC.(a) Start engine.
(b) Keep the rotating speed of engine at 2500rpm for about 180 seconds.
(c) When the engine is idle running, insert the test bar of CO/HC gauge into exhaust pipe at least 40cm.
(d) Immediately check idle speed and CO/HC concentration at 2500rpm.
Hints:Finish test within 3 minutes.Perform the test under 2 analog states (idle speed and 2500rpm) according to measuring meth-
ods and sequences specified by Emission Regulations.
(e) If CO/HC concentration is not within specified value, perform trouble shooting according to the
following sequences.
(1) Check the function of oxygen sensor.
(2) See possible failure causes listed in the table below, and repair and correct if necessary.Engine mechanism - Engine assembly27
Page 39 of 419
Engine mechanism - Engine assemblyCO HC Trouble occurrence Possible causes 28 Normal HighUnstable idle speed
Low HighUnstable idle speed
(HC readings not stable)
High HighUnstable idle speed
(black smoke emission)1. Ignition system malfunctionIgnition timing incorrect Spark plug too dirty, short circuit or clearance
incorrect
2. Valve clearance incorrect
3. Air inlet and exhaust valve leaky
4. Cylinder leaky
1. Vacuum leak:PCV hoseIntake manifoldThrottle bodyIdle speed stepping motorVacuum booster and pipelines
2. Fire caused by too thin mixing ratio
1. Air filter core blocked
2. PCV valve blocked
3. EFI system malfunctionFuel pressure regulator malfunctionWater temperature sensor malfunctionIntake pressure sensor malfunctionECU malfunctionInjection nozzle malfunctionThrottle position sensor malfunction
Page 40 of 419
Engine mechanism - Drive beltDrive beltReplacement1. Remove engine right bottom shield.
2. Remove drive beltSlowly turn drive belt tensioner clockwise to loosen it.
Then remove drive belt and put back drive belt tensioner slowly
and gently.3. Install drive beltSlowly turn drive belt tensioner clockwise to loosen it.
Then install drive belt and put back drive belt tensioner slowly
and gently.29