Page 561 of 828
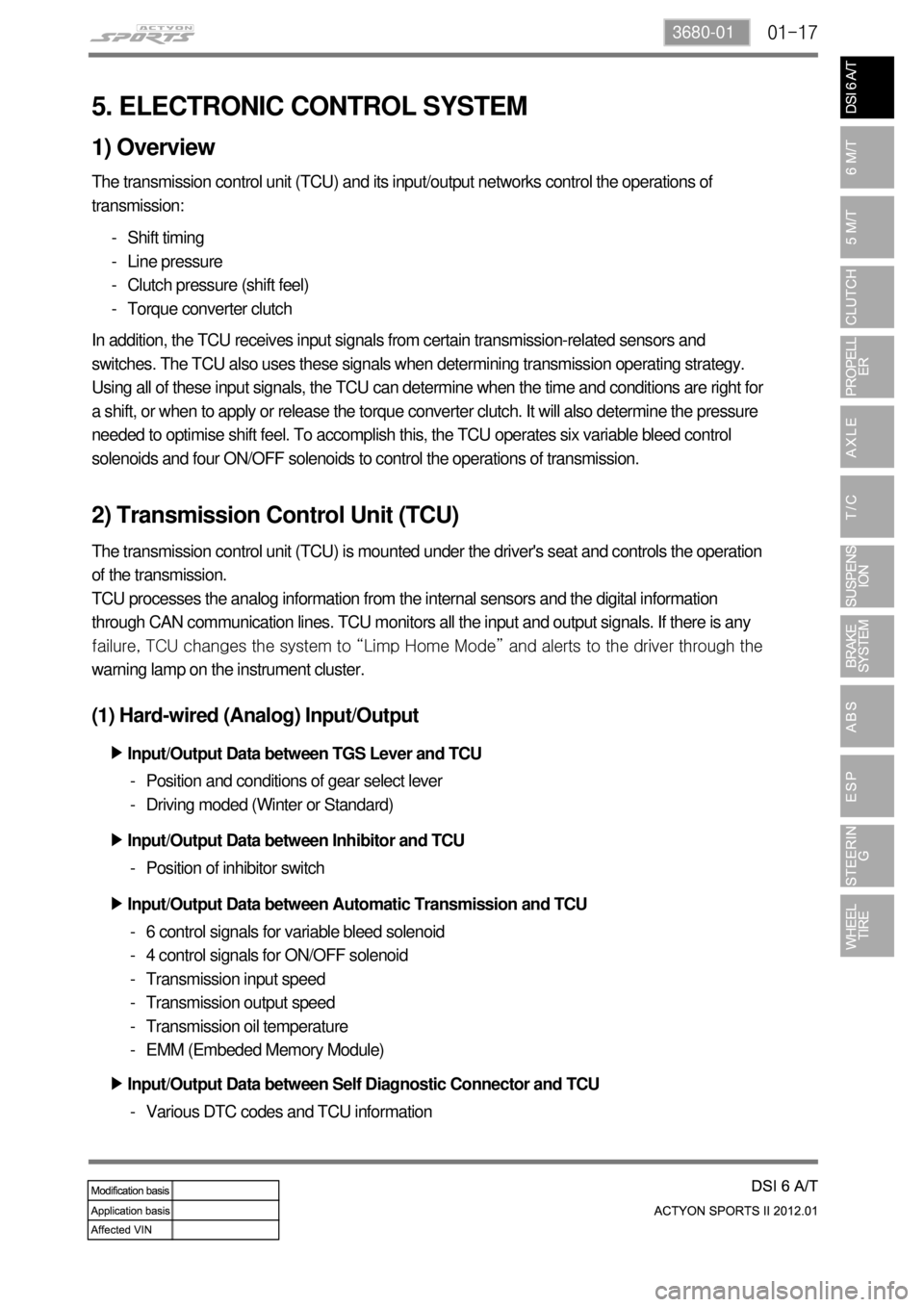
01-173680-01
5. ELECTRONIC CONTROL SYSTEM
1) Overview
The transmission control unit (TCU) and its input/output networks control the operations of
transmission:
Shift timing
Line pressure
Clutch pressure (shift feel)
Torque converter clutch -
-
-
-
In addition, the TCU receives input signals from certain transmission-related sensors and
switches. The TCU also uses these signals when determining transmission operating strategy.
Using all of these input signals, the TCU can determine when the time and conditions are right for
a shift, or when to apply or release the torque converter clutch. It will also determine the pressure
needed to optimise shift feel. To accomplish this, the TCU operates six variable bleed control
solenoids and four ON/OFF solenoids to control the operations of transmission.
2) Transmission Control Unit (TCU)
The transmission control unit (TCU) is mounted under the driver's seat and controls the operation
of the transmission.
TCU processes the analog information from the internal sensors and the digital information
through CAN communication lines. TCU monitors all the input and output signals. If there is any
<008d008800900093009c0099008c00530047007b006a007c0047008a008f00880095008e008c009a0047009b008f008c0047009a00a0009a009b008c00940047009b0096004702c800730090009400970047006f00960094008c004700740096008b008c02
c9004700880095008b004700880093008c0099009b009a0047>to the driver through the
warning lamp on the instrument cluster.
(1) Hard-wired (Analog) Input/Output
Input/Output Data between TGS Lever and TCU ▶
Position and conditions of gear select lever
Driving moded (Winter or Standard) -
-
Position of inhibitor switch - Input/Output Data between Inhibitor and TCU ▶
6 control signals for variable bleed solenoid
4 control signals for ON/OFF solenoid
Transmission input speed
Transmission output speed
Transmission oil temperature
EMM (Embeded Memory Module) -
-
-
-
-
- Input/Output Data between Automatic Transmission and TCU ▶
Input/Output Data between Self Diagnostic Connector and TCU ▶
Various DTC codes and TCU information -
Page 562 of 828
01-18
(2) CAN Input/Output
TCU receives and sends the data among the units through P-CAN communication.
CAN Input/Output Data between Engine ECU and TCU ▶
Page 563 of 828
01-193680-01
CAN Input/Output Data between ABS/ESP and TCU ▶
CAN Input/Output Data between TCCU and TCU ▶
CAN Input/Output Data between ICM and TCU ▶
Page 564 of 828
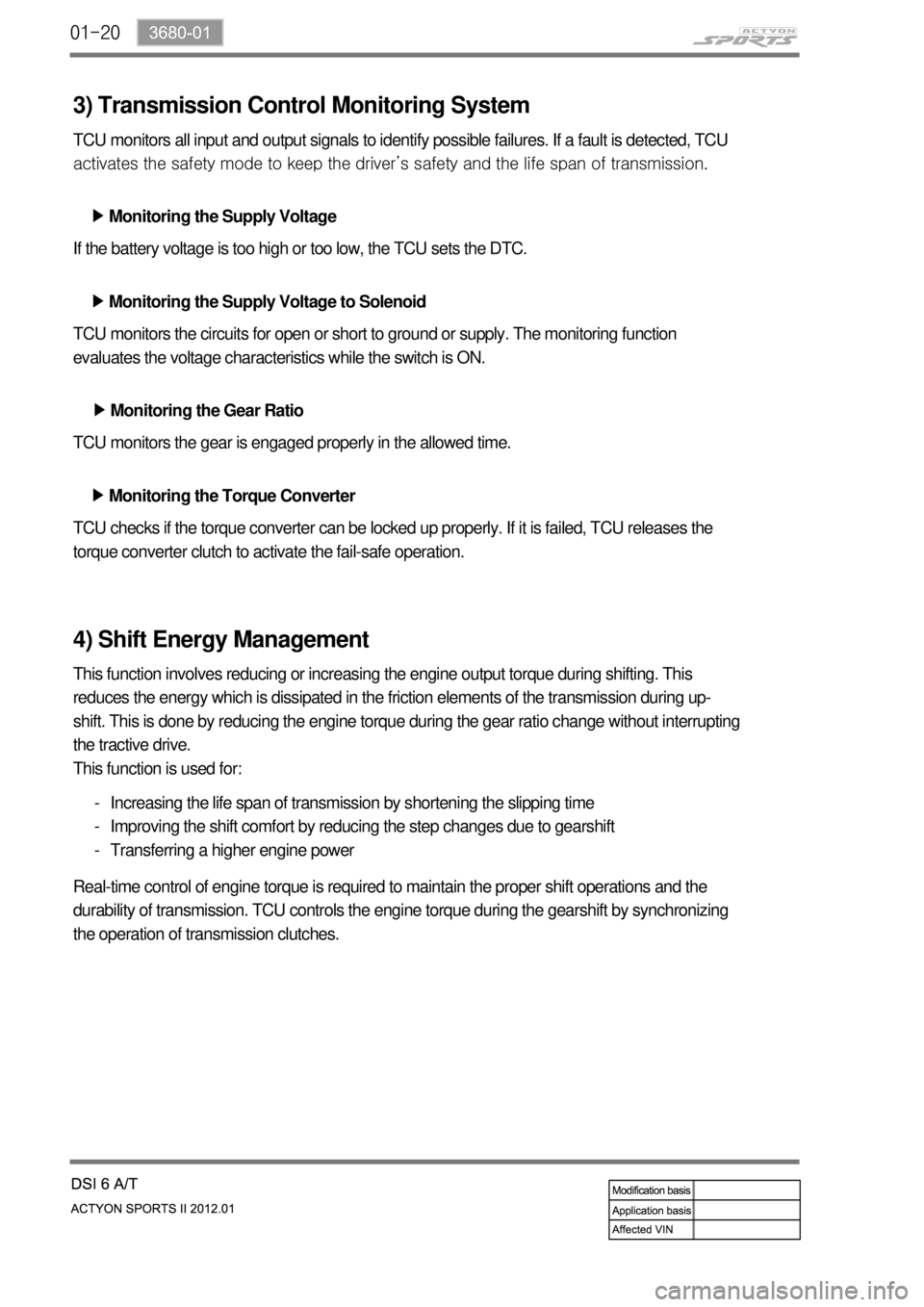
01-20
3) Transmission Control Monitoring System
TCU monitors all input and output signals to identify possible failures. If a fault is detected, TCU
<0088008a009b0090009d0088009b008c009a0047009b008f008c0047009a0088008d008c009b00a0004700940096008b008c0047009b009600470092008c008c00970047009b008f008c0047008b00990090009d008c009902c5009a0047009a0088008d00
8c009b00a0004700880095008b0047009b008f008c00470093>ife span of transmission.
Monitoring the Supply Voltage ▶
Monitoring the Supply Voltage to Solenoid ▶
Monitoring the Gear Ratio ▶
Monitoring the Torque Converter ▶ If the battery voltage is too high or too low, the TCU sets the DTC.
TCU monitors the circuits for open or short to ground or supply. The monitoring function
evaluates the voltage characteristics while the switch is ON.
TCU monitors the gear is engaged properly in the allowed time.
TCU checks if the torque converter can be locked up properly. If it is failed, TCU releases the
torque converter clutch to activate the fail-safe operation.
4) Shift Energy Management
This function involves reducing or increasing the engine output torque during shifting. This
reduces the energy which is dissipated in the friction elements of the transmission during up-
shift. This is done by reducing the engine torque during the gear ratio change without interrupting
the tractive drive.
This function is used for:
Increasing the life span of transmission by shortening the slipping time
Improving the shift comfort by reducing the step changes due to gearshift
Transferring a higher engine power -
-
-
Real-time control of engine torque is required to maintain the proper shift operations and the
durability of transmission. TCU controls the engine torque during the gearshift by synchronizing
the operation of transmission clutches.
Page 565 of 828
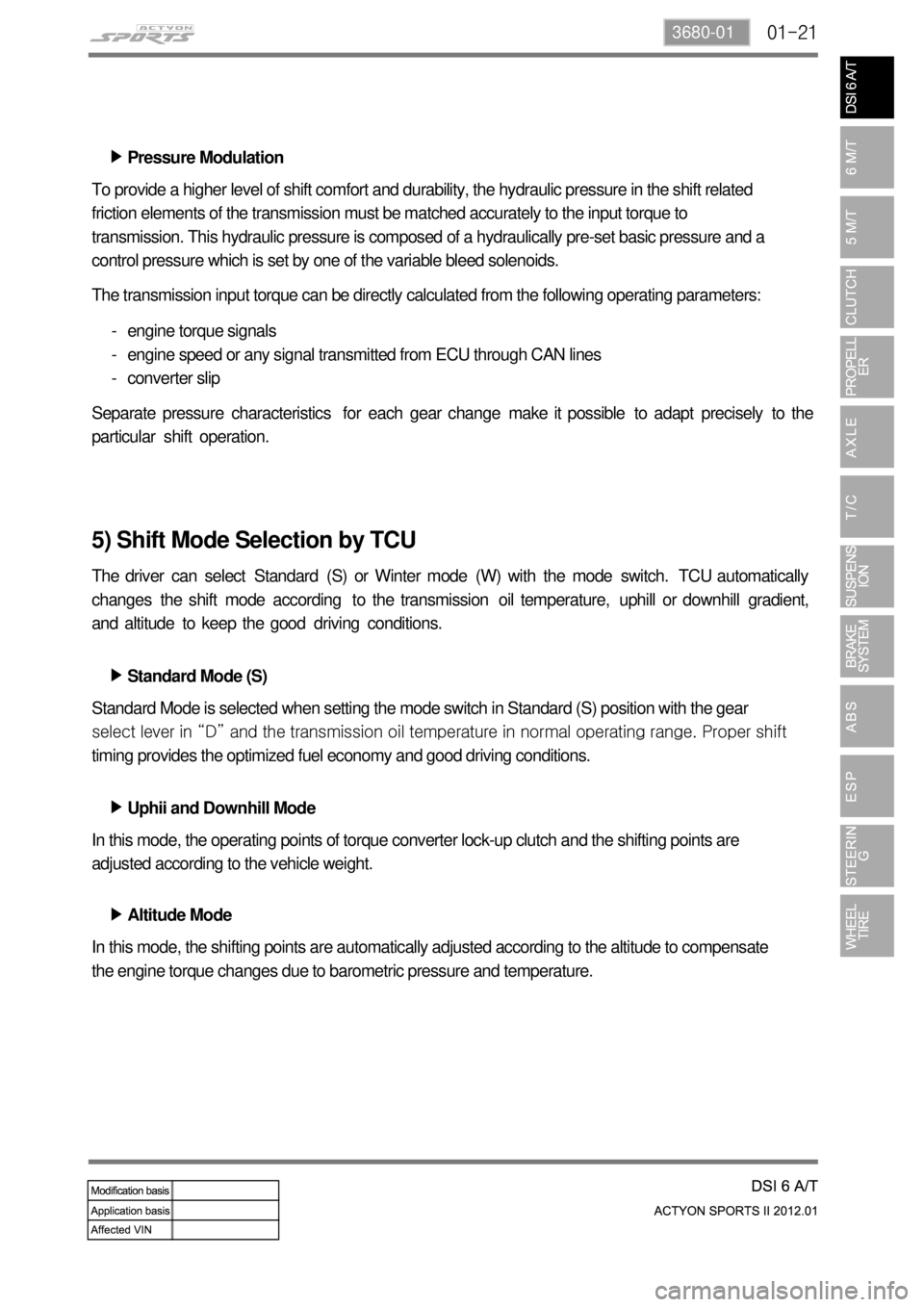
01-213680-01
Pressure Modulation ▶
To provide a higher level of shift comfort and durability, the hydraulic pressure in the shift related
friction elements of the transmission must be matched accurately to the input torque to
transmission. This hydraulic pressure is composed of a hydraulically pre-set basic pressure and a
control pressure which is set by one of the variable bleed solenoids.
The transmission input torque can be directly calculated from the following operating parameters:
engine torque signals
engine speed or any signal transmitted from ECU through CAN lines
converter slip -
-
-
Separate pressure characteristics for each gear change make it possible to adapt precisely to the
particular shift operation.
5) Shift Mode Selection by TCU
The driver can select Standard (S) or Winter mode (W) with the mode switch. TCU automatically
changes the shift mode according to the transmission oil temperature, uphill or downhill gradient,
and altitude to keep the good driving conditions.
Standard Mode (S) ▶
Uphii and Downhill Mode ▶
Altitude Mode ▶ Standard Mode is selected when setting the mode switch in Standard (S) position with the gear
<009a008c0093008c008a009b00470093008c009d008c0099004700900095004702c8006b02c9004700880095008b0047009b008f008c0047009b009900880095009a00940090009a009a00900096009500470096009000930047009b008c00940097008c00
990088009b009c0099008c0047009000950047009500960099>mal operating range. Proper shift
timing provides the optimized fuel economy and good driving conditions.
In this mode, the operating points of torque converter lock-up clutch and the shifting points are
adjusted according to the vehicle weight.
In this mode, the shifting points are automatically adjusted according to the altitude to compensate
the engine torque changes due to barometric pressure and temperature.
Page 566 of 828
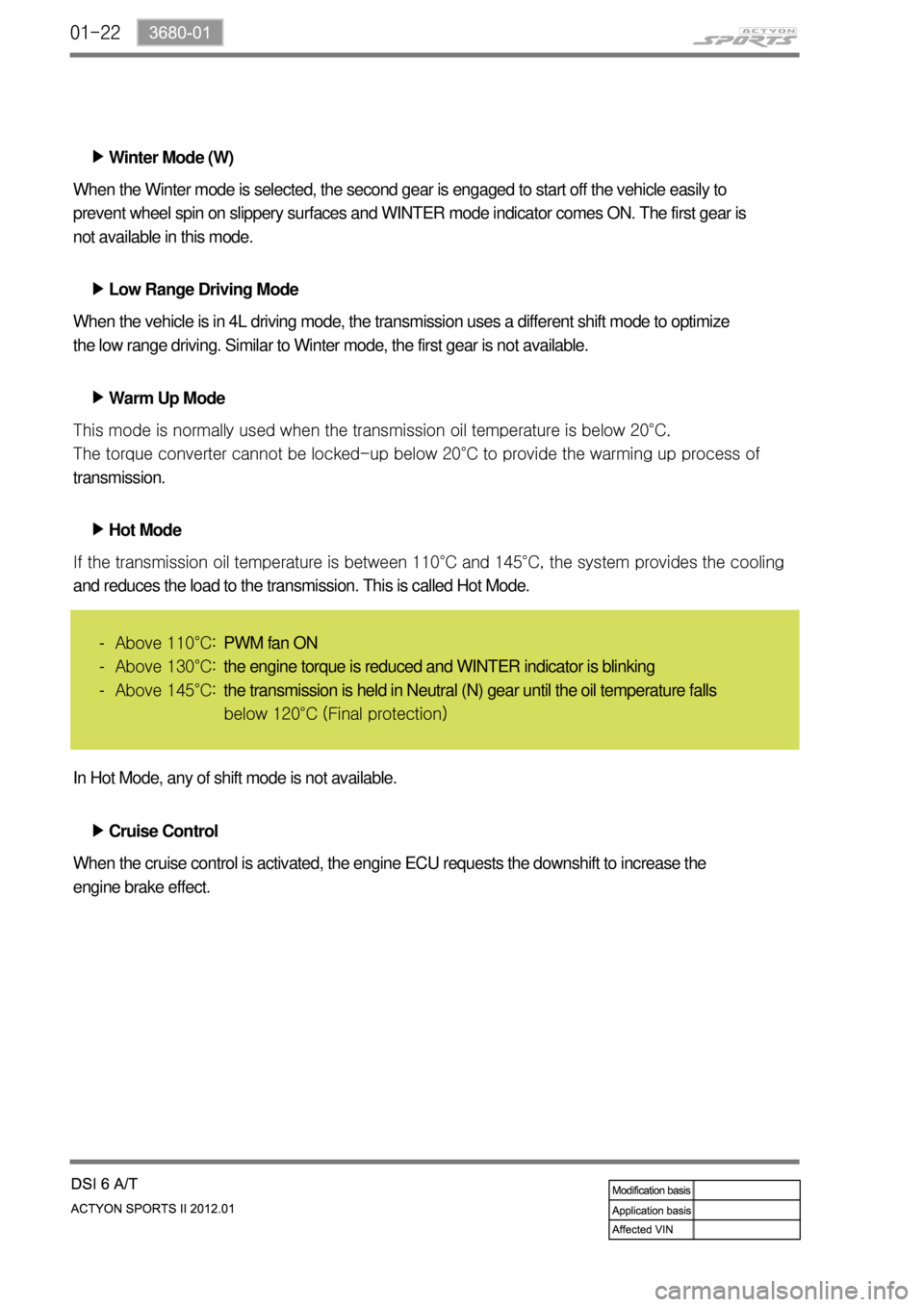
01-22
Winter Mode (W) ▶
Low Range Driving Mode ▶
Warm Up Mode ▶ When the Winter mode is selected, the second gear is engaged to start off the vehicle easily to
prevent wheel spin on slippery surfaces and WINTER mode indicator comes ON. The first gear is
not available in this mode.
When the vehicle is in 4L driving mode, the transmission uses a different shift mode to optimize
the low range driving. Similar to Winter mode, the first gear is not available.
This mode is normally used when the transmission oil temperature is below 20°C.
<007b008f008c0047009b009600990098009c008c0047008a00960095009d008c0099009b008c00990047008a0088009500950096009b00470089008c004700930096008a0092008c008b0054009c009700470089008c00930096009e00470059005700b600
6a0047009b00960047009700990096009d0090008b008c0047>the warming up process of
transmission.
Hot Mode ▶
<0070008d0047009b008f008c0047009b009900880095009a00940090009a009a00900096009500470096009000930047009b008c00940097008c00990088009b009c0099008c00470090009a00470089008c009b009e008c008c0095004700580058005700
b6006a004700880095008b00470058005b005c00b6006a0053> the system provides the cooling
and reduces the load to the transmission. This is called Hot Mode.
Above 110°C:
Above 130°C:
Above 145°C: -
-
-
In Hot Mode, any of shift mode is not available.
Cruise Control ▶
When the cruise control is activated, the engine ECU requests the downshift to increase the
engine brake effect.PWM fan ON
the engine torque is reduced and WINTER indicator is blinking
the transmission is held in Neutral (N) gear until the oil temperature falls
below 120°C (Final protection)
Page 567 of 828
01-233680-01
6. POWER FLOW
Power flows in gears:
Power flow - 1st gear (M)
Power flow - 1st gear (D)
Power flow - 2nd gear (D)
Power flow - 2nd gear (D) ? lockup (D)
Power flow - 3rd gear (D)
Power flow - 4th gear (D) - 4th gear (D) in Limp home mode
Power flow - 5th gear (D)
Power flow - 6th gear (D) -
-
-
-
-
-
-
-
GearGear ratioEngaged element (clutch & band)
C1 C2 C3 B1 B2 1-2OWC
M1 3.53 ON ON
1st 3.53 ON ON
2nd 2.14 ON ON
3rd 1.48 ON ON
4th 1.16 ON ON
5th 0.87 ON ON
6th 0.68 ON ON
Reverse -3.09 ON ON
Gear
S1 S2 S3 S4 S5(A) S6(A) S7(A) S8(A) S9(A) S10(A)
M1 ON 1 0 1
1st ON 1 0 0-1
2nd ON ON 1 0 1 0-1
3rd ON ON 1 0 1 0-1
4th 0 0 0-1
5th ON 0 1 1 0-1
6th ON ON 0 1 1 0-1
Reverse ON ON ON 1 1 1 0-1
Gear Selection and Engaged Element ▶
Variable bleed solenoid valve - VBS ON/OFF solenoid valve
Page 568 of 828
01-24
Hydraulic Circuit Diagram ▶