Page 697 of 828
10-18
4) ABS Control Pattern
The ABS control is performed by comparing the reference speed with each wheel speed. Firstly,
it is determined whether the vehicle is in the deceleration or acceleration state using the wheel
speed change ratio. Then, a signal is transmitted to the valve.
Finally, the brake pressure is adjusted via the signal.
△V: Vehicle speed
Vref: Vehicle speed reference
Vw: Wheel speed
Page 698 of 828
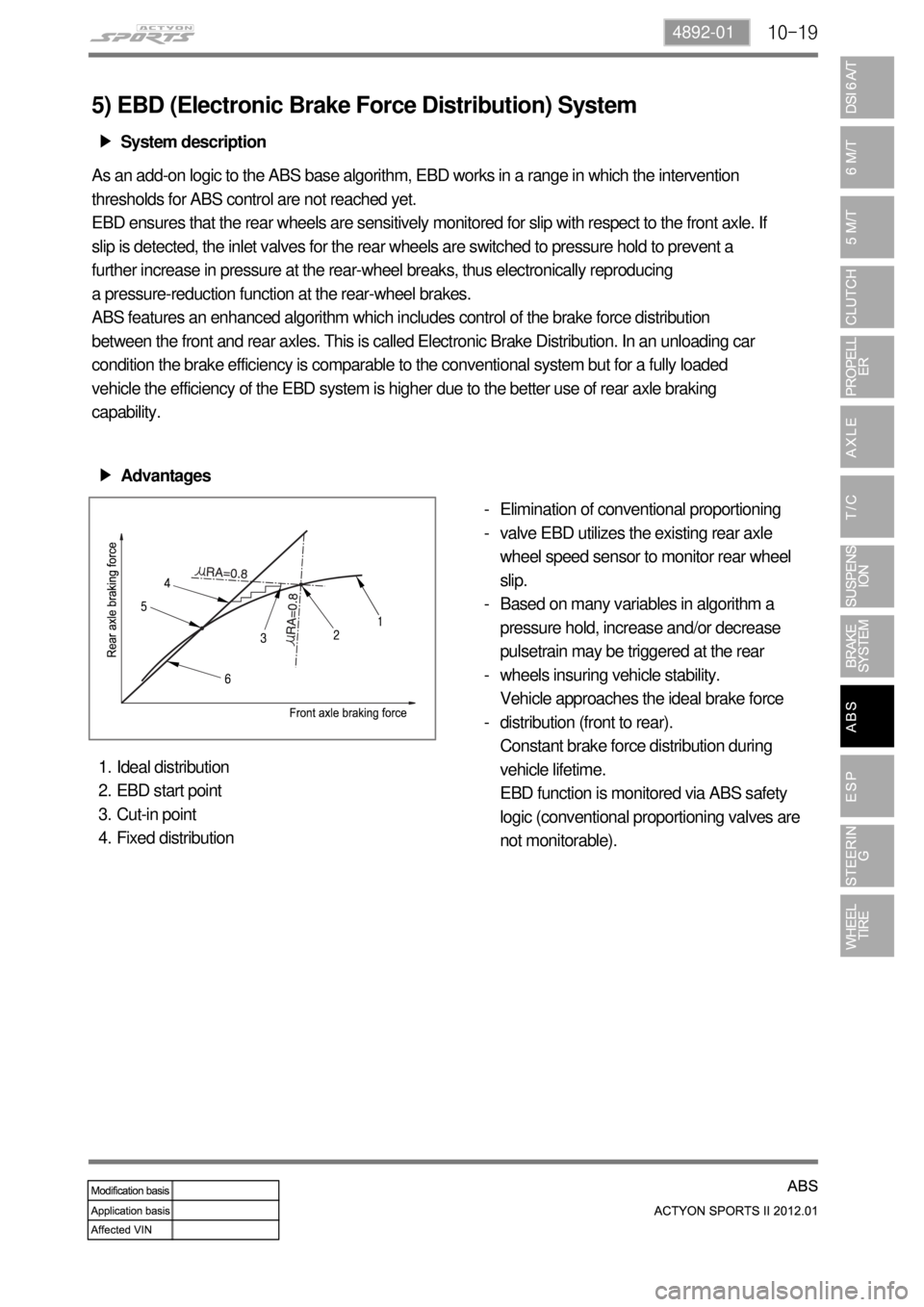
10-194892-01
5) EBD (Electronic Brake Force Distribution) System
System description ▶
As an add-on logic to the ABS base algorithm, EBD works in a range in which the intervention
thresholds for ABS control are not reached yet.
EBD ensures that the rear wheels are sensitively monitored for slip with respect to the front axle. If
slip is detected, the inlet valves for the rear wheels are switched to pressure hold to prevent a
further increase in pressure at the rear-wheel breaks, thus electronically reproducing
a pressure-reduction function at the rear-wheel brakes.
ABS features an enhanced algorithm which includes control of the brake force distribution
between the front and rear axles. This is called Electronic Brake Distribution. In an unloading car
condition the brake efficiency is comparable to the conventional system but for a fully loaded
vehicle the efficiency of the EBD system is higher due to the better use of rear axle braking
capability.
Advantages ▶
Elimination of conventional proportioning
valve EBD utilizes the existing rear axle
wheel speed sensor to monitor rear wheel
slip.
Based on many variables in algorithm a
pressure hold, increase and/or decrease
pulsetrain may be triggered at the rear
wheels insuring vehicle stability.
Vehicle approaches the ideal brake force
distribution (front to rear).
Constant brake force distribution during
vehicle lifetime.
EBD function is monitored via ABS safety
logic (conventional proportioning valves are
not monitorable). -
-
-
-
-
Ideal distribution
EBD start point
Cut-in point
Fixed distribution 1.
2.
3.
4.
Page 699 of 828
10-20
6. HYDRAULIC CIRCUIT OF ABS
1) Normal Brake Operation (ABS is not working) Mode
If the driver depress the brake pedal so that the ABS does not operate, the hydraulic pressure in
the master cylinder increases through the vacuum booster and it is delivered to the wheel via the
normal open inlet valve. At this moment, the normally-closed outlet valve is closed The speed of
the wheel that hydraulic pressure is delivered reduces gradually.
Solenoid valve Valve Open/Close Pump motor
Inlet valve - Normal open (NO) valve Open
OFF
Outlet valve - Normal close (NC) valve Close
Page 700 of 828
10-214892-01
2) DUMP (ABS is working) Mode
Even when the hydraulic pressure on each circuit is constant, the wheel can be locked as the
wheel speed decreases. This is when the ABS HECU detects the wheel speed and the vehicle
speed and gives the optimized braking without locking the wheels. In order to prevent the
hydraulic pressure from increasing, the inlet valve will be closed, the outlet valve will be opened
and the oil will flow into the low pressure chamber. In addition, the ABS HECU operates the pump
to circulate the oil in the low pressure chamber to the master cylinder. This may make the driver to
feel the brake pedal vibration and some
Solenoid valve Valve Open/Close Pump motor
Inlet valve - Normal open (NO) valve Close
ON
Outlet valve - Normal close (NC) valve Open
Page 701 of 828
10-22
3) HOLD (ABS is working) Mode
As hydraulic pressure on each wheel increases, the wheel tends to lock. In order to prevent the
wheel from locking, the hydraulic valve modulator operates the inlet valve control solenoid to stop
increasing the hydraulic pressure by closing the inlet valve. At this moment, the outlet valve is
closed. This procedure helps the wheel to maintain a constant hydraulic pressure.
Solenoid valve Valve Open/Close Pump motor
Inlet valve - Normal open (NO) valve Close
OFF
Outlet valve - Normal close (NC) valve Close
Page 702 of 828
10-234892-01
4) RISE (ABS is working) Mode
As the wheel speed increases, the inlet valve opens and the wheel's pressure increases due to
the master cylinder pressure. In addition, the pump circulates the oil in the low pressure chamber
to the wheel. As the hydraulic pressure to the wheel increases, the wheel speed will reduce. This
operation continues repetitively until there are no signs that the ABS HECU tends to lock the
wheels. Since the ABS hydraulic pressure control process takes place repeatedly for a short time,
there may be some vibration and noises at the brake pedal.
Solenoid valve Valve Open/Close Pump motor
Inlet valve - Normal open (NO) valve Open
ON
Outlet valve - Normal close (NC) valve Close
Page 703 of 828
Page 704 of 828
11-34890-10
1. SPECIFICATION
1) Specification of Active Wheel Sensor
Description Specification Remark
Supplying voltage 4.5 ~ 16.0V
Output current (at 2.75 km/h of
vehicle speed)7mA(Lo) ~ 14mA(Hi)
Tightening torqueFront: 7.8 to 11.8 Nm
Rear: 7.8 to 11.8 Nm
Operating temperature-40 ~ 150℃
Operating frequency 1 ~ 2,500Hz
UnitDescription
Specification
ABS ESP
HECU Clock frequency: 32 MHz Clock frequency: 50 MHz
Memory: 128 KB Memory: 256 KB
Wheel speed
sensorActive type Active type Output: 7~14
mA
Steering wheel
angle sensorNone Max. detection angle speed:
1500 °/SecPulse duty:
50±10%
Operating voltage: 9 to 12 V
Sensor cluster None Yaw rate sensor + lateral G
sensor + longitudinal G sensor
(4WD)Mounting
direction should
be kept (CAN
communcation)
Longitudinal G
sensor4WD only None
Pressure
sensorNone HECU integrated