Page 321 of 828
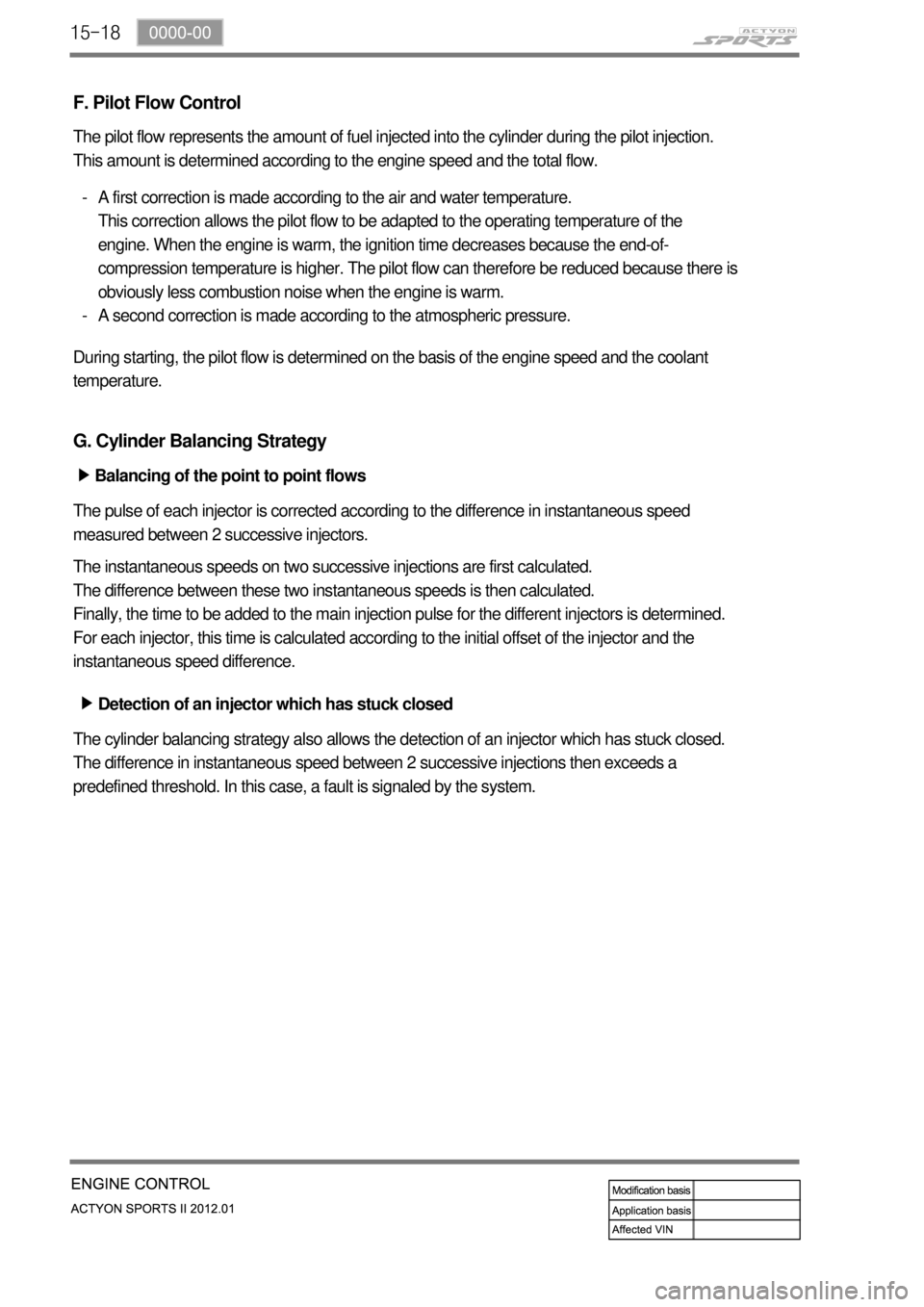
15-18
F. Pilot Flow Control
The pilot flow represents the amount of fuel injected into the cylinder during the pilot injection.
This amount is determined according to the engine speed and the total flow.
A first correction is made according to the air and water temperature.
This correction allows the pilot flow to be adapted to the operating temperature of the
engine. When the engine is warm, the ignition time decreases because the end-of-
compression temperature is higher. The pilot flow can therefore be reduced because there is
obviously less combustion noise when the engine is warm.
A second correction is made according to the atmospheric pressure. -
-
During starting, the pilot flow is determined on the basis of the engine speed and the coolant
temperature.
G. Cylinder Balancing Strategy
Balancing of the point to point flows ▶
The pulse of each injector is corrected according to the difference in instantaneous speed
measured between 2 successive injectors.
The instantaneous speeds on two successive injections are first calculated.
The difference between these two instantaneous speeds is then calculated.
Finally, the time to be added to the main injection pulse for the different injectors is determined.
For each injector, this time is calculated according to the initial offset of the injector and the
instantaneous speed difference.
Detection of an injector which has stuck closed ▶
The cylinder balancing strategy also allows the detection of an injector which has stuck closed.
The difference in instantaneous speed between 2 successive injections then exceeds a
predefined threshold. In this case, a fault is signaled by the system.
Page 322 of 828
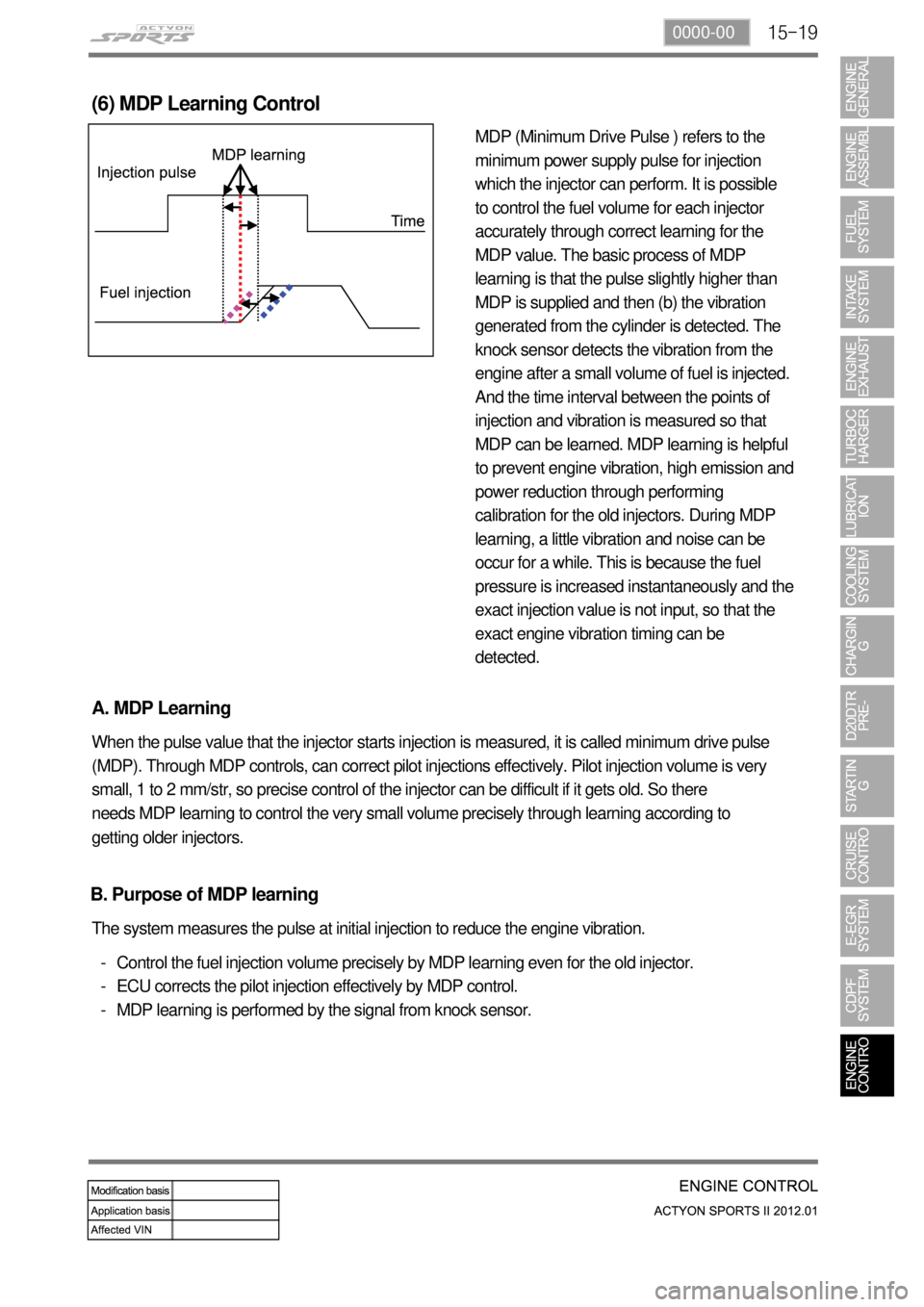
15-190000-00
MDP (Minimum Drive Pulse ) refers to the
minimum power supply pulse for injection
which the injector can perform. It is possible
to control the fuel volume for each injector
accurately through correct learning for the
MDP value. The basic process of MDP
learning is that the pulse slightly higher than
MDP is supplied and then (b) the vibration
generated from the cylinder is detected. The
knock sensor detects the vibration from the
engine after a small volume of fuel is injected.
And the time interval between the points of
injection and vibration is measured so that
MDP can be learned. MDP learning is helpful
to prevent engine vibration, high emission and
power reduction through performing
calibration for the old injectors. During MDP
learning, a little vibration and noise can be
occur for a while. This is because the fuel
pressure is increased instantaneously and the
exact injection value is not input, so that the
exact engine vibration timing can be
detected.
(6) MDP Learning Control
A. MDP Learning
When the pulse value that the injector starts injection is measured, it is called minimum drive pulse
(MDP). Through MDP controls, can correct pilot injections effectively. Pilot injection volume is very
small, 1 to 2 mm/str, so precise control of the injector can be difficult if it gets old. So there
needs MDP learning to control the very small volume precisely through learning according to
getting older injectors.
Control the fuel injection volume precisely by MDP learning even for the old injector.
ECU corrects the pilot injection effectively by MDP control.
MDP learning is performed by the signal from knock sensor. -
-
- The system measures the pulse at initial injection to reduce the engine vibration.
B. Purpose of MDP learning
Page 323 of 828
15-20
C. Learning Conditions
Idle MDP learning Drive MDP learning
Coolant temperatureover 60℃ over 60℃
Vehicle speedIdling over 50km/h (over 5 seconds)
Engine rpm2,000 to 2,500 rpm
Fuel temperature0 < Fuel temperature < 80℃
Learning2 times for each cylinder (every
5 seconds)2 times for each cylinder
(every 5 seconds)
If MDP learning is not properly performed, engine vibration and injection could be occurred.
MDP learning should be performed after replacing ECU, reprogramming and replacing
injector. -
-
D. Injector characteristic curve for rail pressure
Page 324 of 828
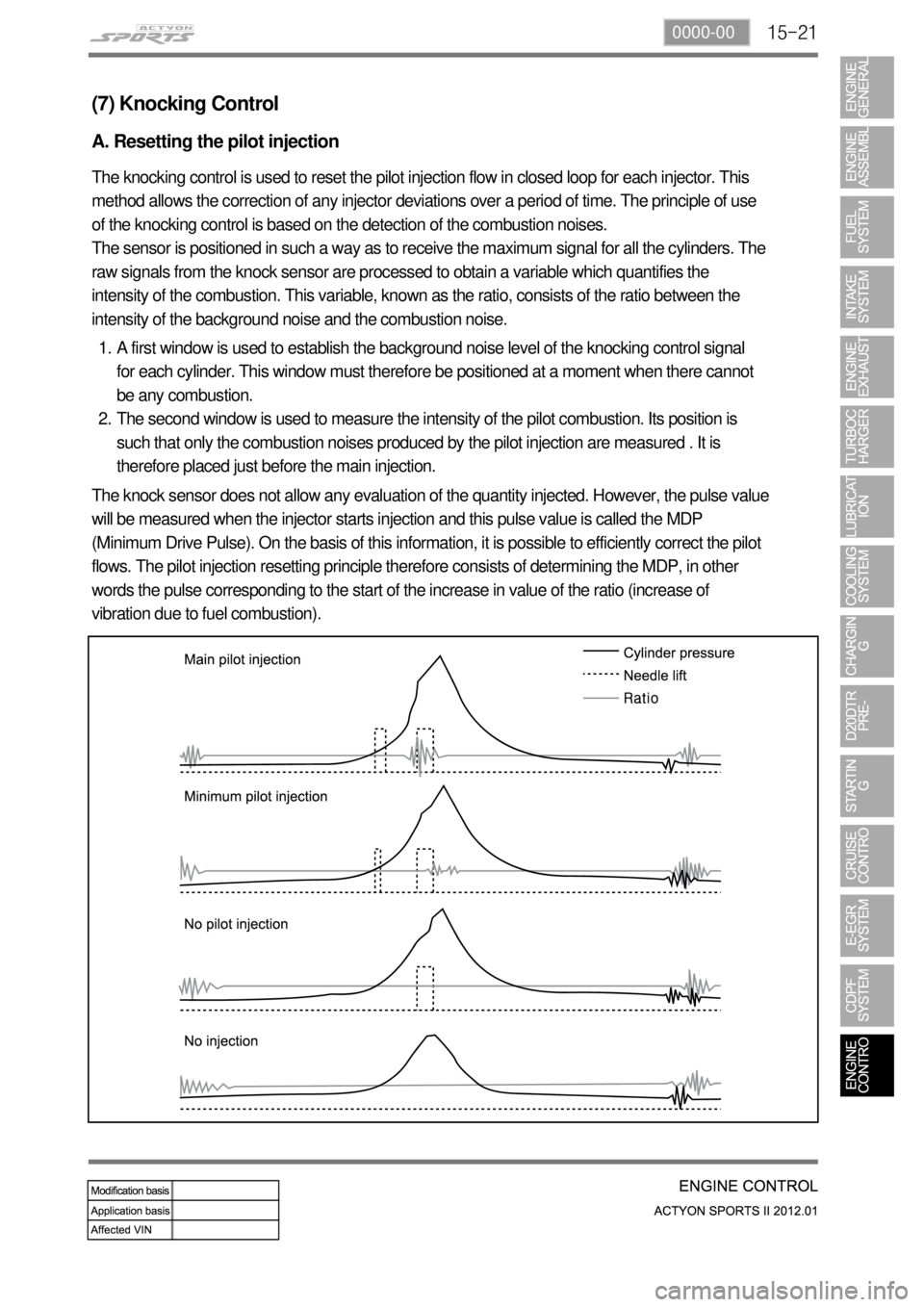
15-210000-00
(7) Knocking Control
A. Resetting the pilot injection
The knocking control is used to reset the pilot injection flow in closed loop for each injector. This
method allows the correction of any injector deviations over a period of time. The principle of use
of the knocking control is based on the detection of the combustion noises.
The sensor is positioned in such a way as to receive the maximum signal for all the cylinders. The
raw signals from the knock sensor are processed to obtain a variable which quantifies the
intensity of the combustion. This variable, known as the ratio, consists of the ratio between the
intensity of the background noise and the combustion noise.
A first window is used to establish the background noise level of the knocking control signal
for each cylinder. This window must therefore be positioned at a moment when there cannot
be any combustion.
The second window is used to measure the intensity of the pilot combustion. Its position is
such that only the combustion noises produced by the pilot injection are measured . It is
therefore placed just before the main injection. 1.
2.
The knock sensor does not allow any evaluation of the quantity injected. However, the pulse value
will be measured when the injector starts injection and this pulse value is called the MDP
(Minimum Drive Pulse). On the basis of this information, it is possible to efficiently correct the pilot
flows. The pilot injection resetting principle therefore consists of determining the MDP, in other
words the pulse corresponding to the start of the increase in value of the ratio (increase of
vibration due to fuel combustion).
Page 325 of 828
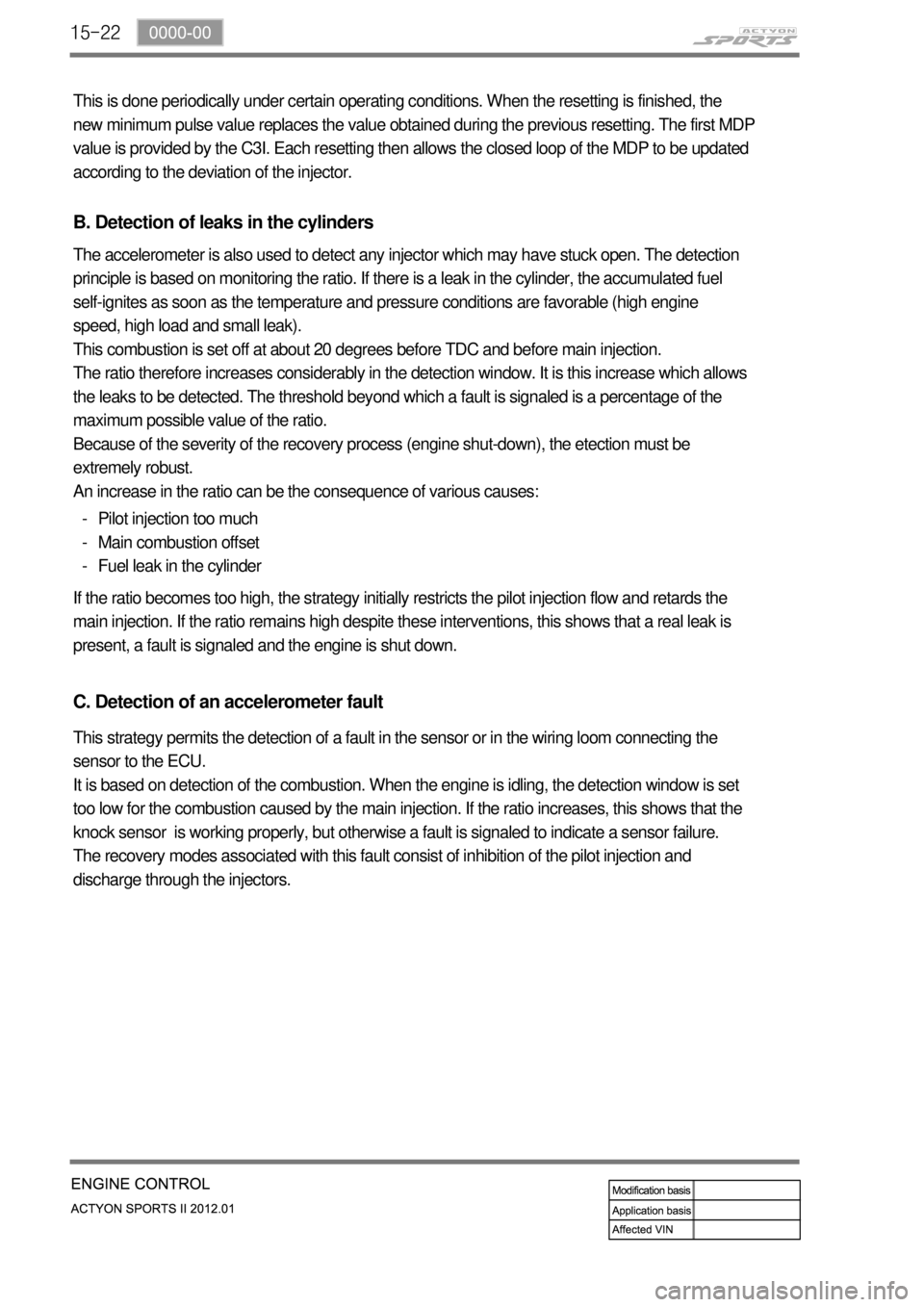
15-22
This is done periodically under certain operating conditions. When the resetting is finished, the
new minimum pulse value replaces the value obtained during the previous resetting. The first MDP
value is provided by the C3I. Each resetting then allows the closed loop of the MDP to be updated
according to the deviation of the injector.
B. Detection of leaks in the cylinders
The accelerometer is also used to detect any injector which may have stuck open. The detection
principle is based on monitoring the ratio. If there is a leak in the cylinder, the accumulated fuel
self-ignites as soon as the temperature and pressure conditions are favorable (high engine
speed, high load and small leak).
This combustion is set off at about 20 degrees before TDC and before main injection.
The ratio therefore increases considerably in the detection window. It is this increase which allows
the leaks to be detected. The threshold beyond which a fault is signaled is a percentage of the
maximum possible value of the ratio.
Because of the severity of the recovery process (engine shut-down), the etection must be
extremely robust.
An increase in the ratio can be the consequence of various causes:
Pilot injection too much
Main combustion offset
Fuel leak in the cylinder -
-
-
If the ratio becomes too high, the strategy initially restricts the pilot injection flow and retards the
main injection. If the ratio remains high despite these interventions, this shows that a real leak is
present, a fault is signaled and the engine is shut down.
C. Detection of an accelerometer fault
This strategy permits the detection of a fault in the sensor or in the wiring loom connecting the
sensor to the ECU.
It is based on detection of the combustion. When the engine is idling, the detection window is set
too low for the combustion caused by the main injection. If the ratio increases, this shows that the
knock sensor is working properly, but otherwise a fault is signaled to indicate a sensor failure.
The recovery modes associated with this fault consist of inhibition of the pilot injection and
discharge through the injectors.
Page 326 of 828
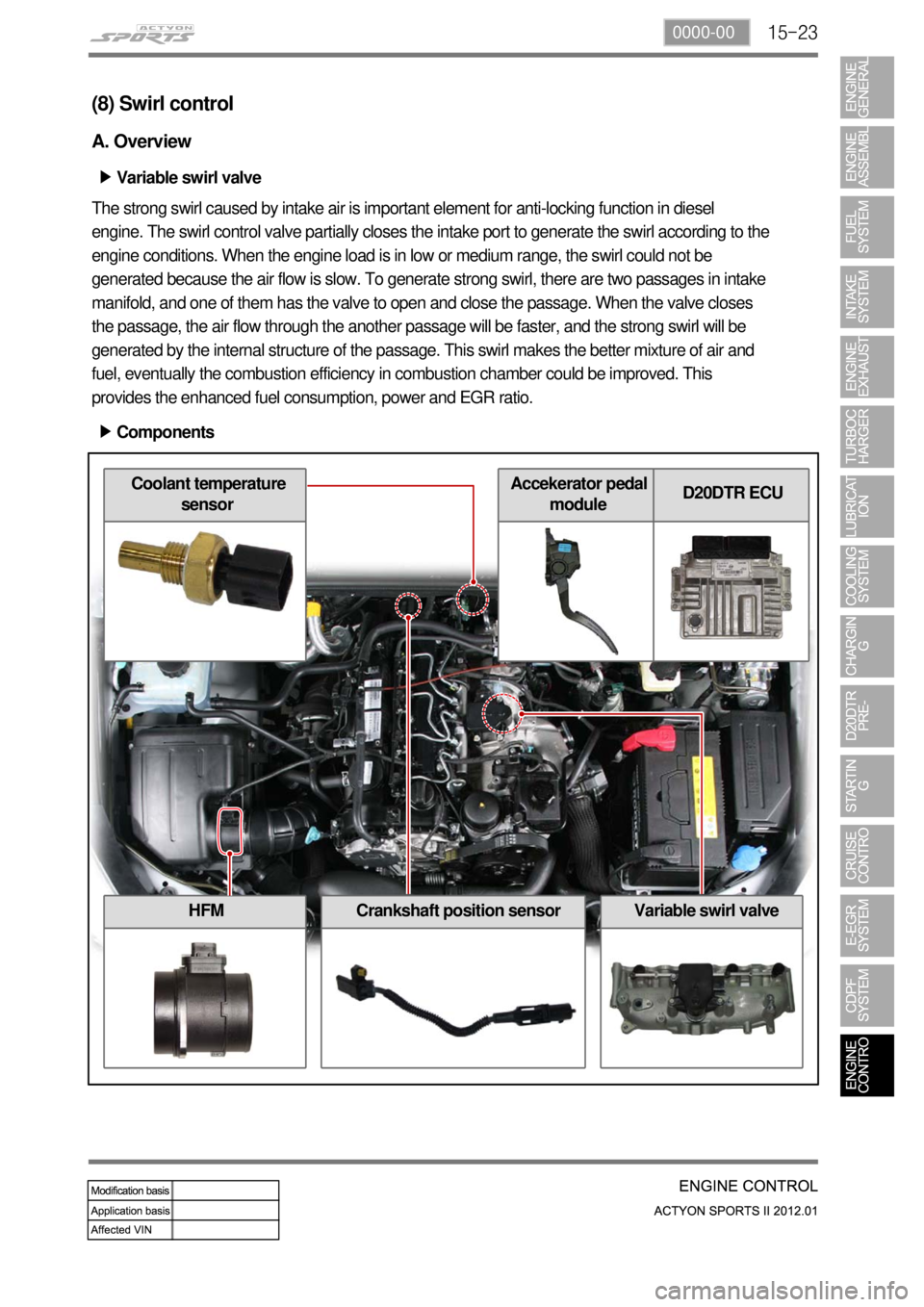
15-230000-00
(8) Swirl control
A. Overview
Variable swirl valve ▶
The strong swirl caused by intake air is important element for anti-locking function in diesel
engine. The swirl control valve partially closes the intake port to generate the swirl according to the
engine conditions. When the engine load is in low or medium range, the swirl could not be
generated because the air flow is slow. To generate strong swirl, there are two passages in intake
manifold, and one of them has the valve to open and close the passage. When the valve closes
the passage, the air flow through the another passage will be faster, and the strong swirl will be
generated by the internal structure of the passage. This swirl makes the better mixture of air and
fuel, eventually the combustion efficiency in combustion chamber could be improved. This
provides the enhanced fuel consumption, power and EGR ratio.
Components ▶
HFMCrankshaft position sensorVariable swirl valve
Coolant temperature
sensorAccekerator pedal
moduleD20DTR ECU
Page 327 of 828
15-24
B. Input/Output for variable swirl valve
Page 328 of 828
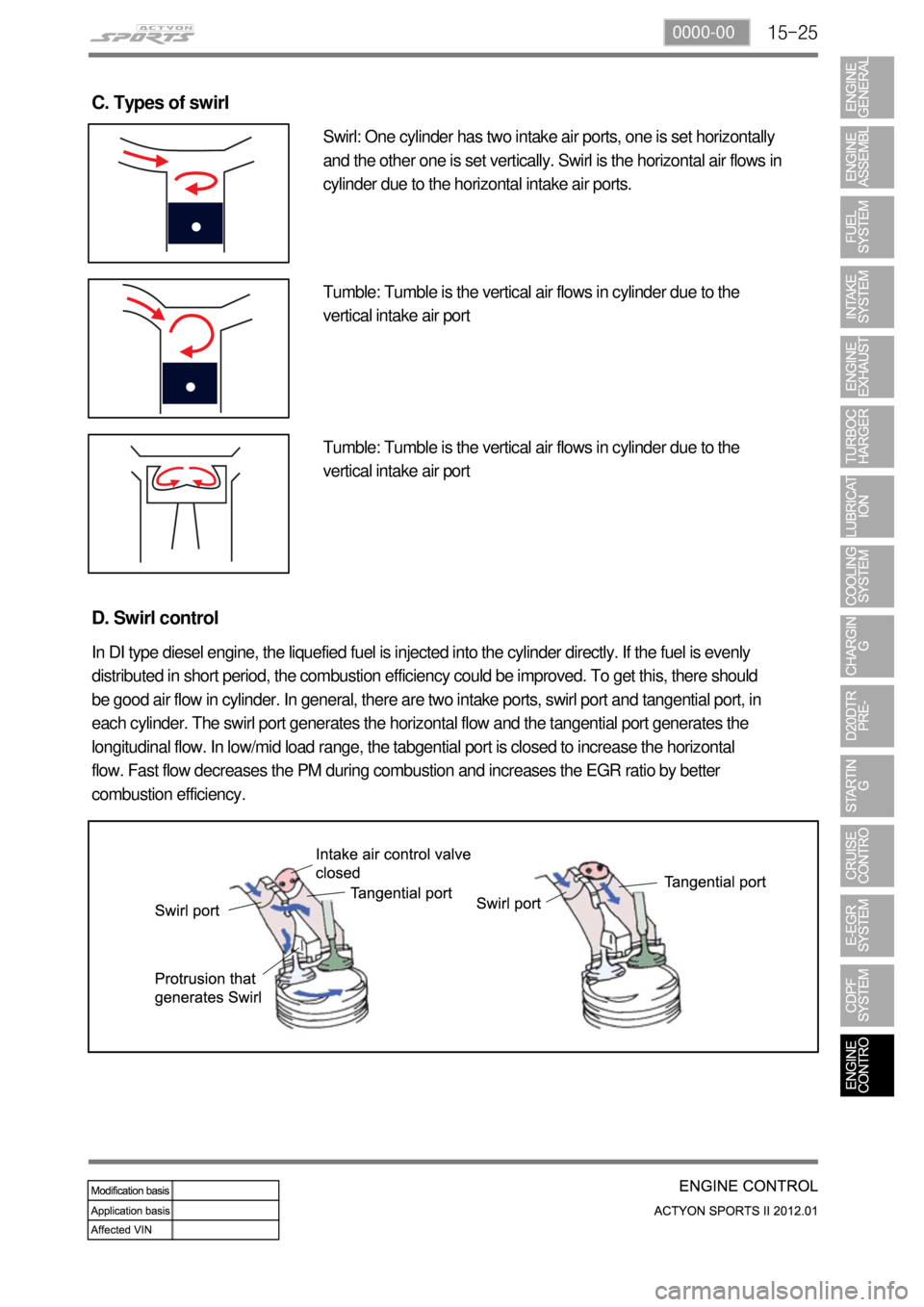
15-250000-00
C. Types of swirl
Swirl: One cylinder has two intake air ports, one is set horizontally
and the other one is set vertically. Swirl is the horizontal air flows in
cylinder due to the horizontal intake air ports.
Tumble: Tumble is the vertical air flows in cylinder due to the
vertical intake air port
Tumble: Tumble is the vertical air flows in cylinder due to the
vertical intake air port
D. Swirl control
In DI type diesel engine, the liquefied fuel is injected into the cylinder directly. If the fuel is evenly
distributed in short period, the combustion efficiency could be improved. To get this, there should
be good air flow in cylinder. In general, there are two intake ports, swirl port and tangential port, in
each cylinder. The swirl port generates the horizontal flow and the tangential port generates the
longitudinal flow. In low/mid load range, the tabgential port is closed to increase the horizontal
flow. Fast flow decreases the PM during combustion and increases the EGR ratio by better
combustion efficiency.