Page 617 of 828
Page 618 of 828
04-33010-01
1. SPECIFICATION
Description Specification
Operating type Hydraulic type
Clutch pedal Type Suspended type
Max. operating travel 145 mm
Pedal free play (Longitudinal)159 ± 5 mm
Pedal free play (Transverse) 5 ~ 15 mm
Clutch disc Type Dry type single diaphragm
Diameter of facingOuter: Ø250 mm
Inner: Ø160 mm
Numbers of disc 2
Thickness of discFree: 8.7 ± 0.3 mm
When loaded: 8.0 ± 0.2 mm
Setting load of clutch cover assembly At least 7,800 N
Clutch master
cylinderOperating travel 27mm
Inner diameterØ17.46 mm
Concentric slave
cylinderMaximum operating travel Max. 20 mm
Operating pressure Max. 2,200 N
Clutch fluid Type DOT 3 or DOT 4
Capacity As required
Page 619 of 828
04-4
1. OVERVIEW
The hydraulic clutch transmits the force required to operate the clutch pedal to the concentric
slave cylinder fitted to the clutch housing as a hydraulic pressure.
(The hydraulic pressure is transmitted in the following order: Clutch pedal - Clutch master
cylinder - Clutch pipe - Clutch damper - Clutch pipe and hose - Concentric slave cylinder -
Pressure plate - Flywheel.)
If a driver depress the clutch pedal, the hydraulic pressure is generated in the master cylinder. It
is transmitted to the concentric slave cylinder through the pipe, resulting in the cylinder being
forced out. At this time, the clutch disc is forced against the cylinder by pushing the cover. This,
in turn, remove the flywheel from the pressure plate. As a consequence, the power from the
engine will be cut off and the gear change can be carried out.
Page 620 of 828
04-53010-01
2. SATIC (SELF ADJUSTING TECHNOLOGY WITH
INTEGRATED CASSETTE)
1) System Description
Function ▶
On the conventional clutch, the pedal force
tends to increase in proportion to the degree
of disc run-out. However, the SATIC clutch
has the adjusting function which activates the
cassette system inserted to the clutch cover
to maintain a constant pedal force and
clearance when the disc runs out. (Unlike SAT
type, SATIC type does not need SST for
clutch cover removal.)
Operation ▶
Diaphragm spring rotates the adjusting
equipment as clutch disc is wearing and so,
pressure plate is pushed to clutch disc side at
the amount of wear.
Disc wear (Free
play) → Diaphragm spring (1)
→ Adjusting equipment (2, 3) → Pressure
plate (4)
Page 621 of 828
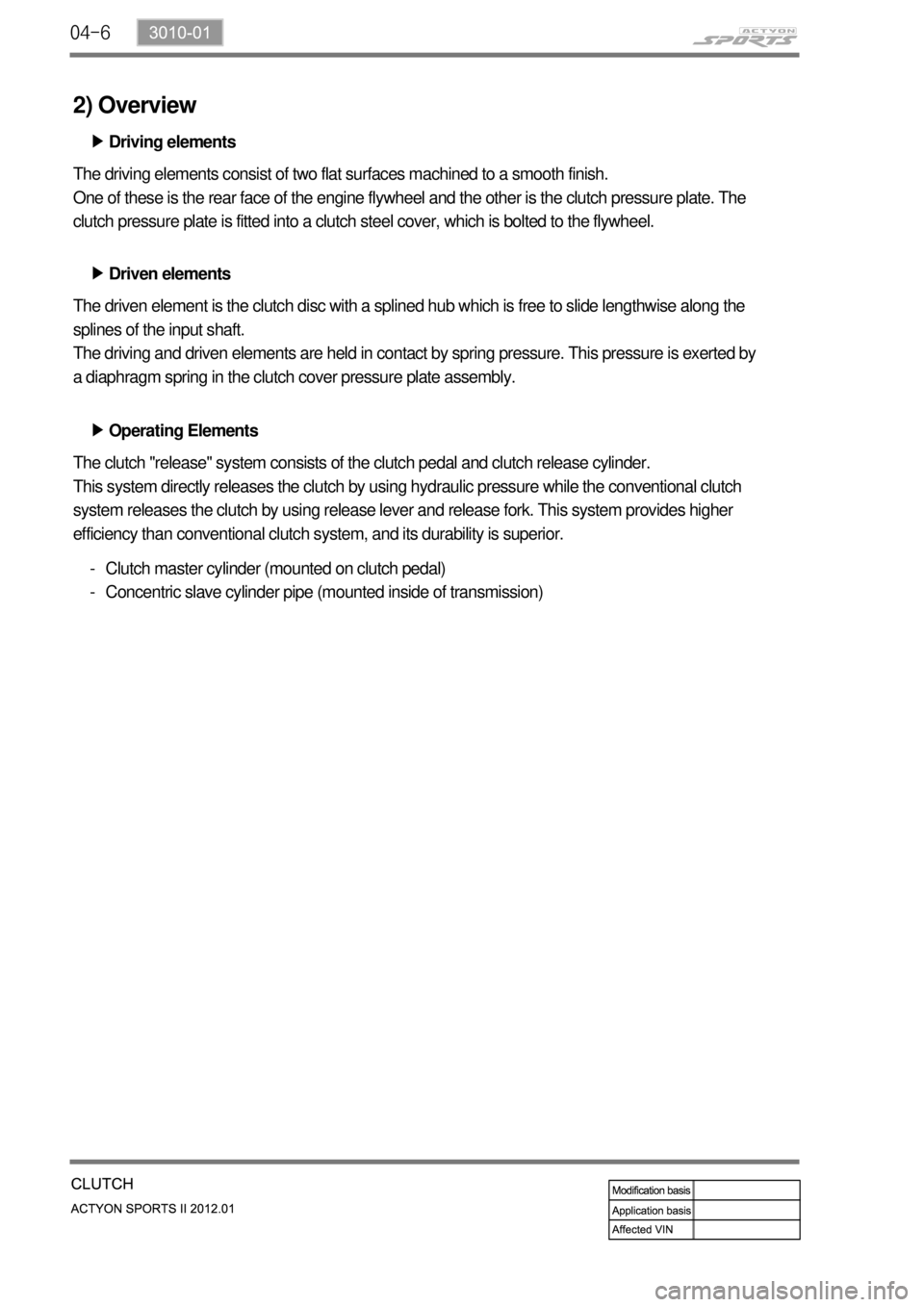
04-6
2) Overview
Driving elements ▶
The driving elements consist of two flat surfaces machined to a smooth finish.
One of these is the rear face of the engine flywheel and the other is the clutch pressure plate. The
clutch pressure plate is fitted into a clutch steel cover, which is bolted to the flywheel.
Driven elements ▶
The driven element is the clutch disc with a splined hub which is free to slide lengthwise along the
splines of the input shaft.
The driving and driven elements are held in contact by spring pressure. This pressure is exerted by
a diaphragm spring in the clutch cover pressure plate assembly.
Operating Elements ▶
The clutch "release" system consists of the clutch pedal and clutch release cylinder.
This system directly releases the clutch by using hydraulic pressure while the conventional clutch
system releases the clutch by using release lever and release fork. This system provides higher
efficiency than conventional clutch system, and its durability is superior.
Clutch master cylinder (mounted on clutch pedal)
Concentric slave cylinder pipe (mounted inside of transmission) -
-
Page 622 of 828
04-73010-01
3) Layout
Clutch discClutch cover assembly
Dual mass flywheel (DMF)Concentric slave cylinder
Centering pin
Page 623 of 828
04-8
3. DUAL MASS FLYWHEEL (DMF)
The dual mass flywheel (DMF) is of having a mass divided into two halves.
While one mass is connected to the engine crankshaft, which is affected by the mass moment of
inertia of the engine, the other mass is affected by one of the transmission.
The divided dual masses are connected to the coil spring and damping system internally.
The DMF has the following benefits: ▶
Reducing fuel consumption by lowering engine speed
Reducing rattling noise and vehicle vibration in all driving ranges
Reducing synchronization wear
Facilitating gear change
Protecting power train parts by preventing excessive load from being delivered -
-
-
-
-
Primary flywheel
Secondary flywheel
Arc damper spring
Torque limiter
Ring gear 1.
2.
3.
4.
5.
Page 624 of 828
05-33310-00
1. SPECIFICATION
Description Specification
Structure Universal joint with yoke arm and
spider
Number of spiders Front Part time T/C Two
Rear Three
Runout Max. 0.3mm
Unbalance Max. 18 g.cm / 4,500 rpm
Dimension of front
propeller shaft (Length x
Dia.) (mm)A/T 552.3*Φ63.5 (Compressed)
M/T 603.8*Φ63.5 (Compressed)
Dimension of front
propeller shaft (Length x
Dia.) (mm)2WD Front1136.0*Φ63.5
Rear743.*Φ63.5(Compressed)
4WD(M/T) Front785.1*Φ63.5
Rear743.*Φ63.5(Compressed)
4WD(A/T) Front836.8*Φ63.5
Rear743.*Φ63.5(Compressed)
2. TIGHTENING TORQUE
Fastener Tightening torque
Mounting bolts for front/rear axle 66.7 ~ 73.5Nm
Mounting bolts for T/M and T/C 79.4 ~ 87.2Nm
Mounting bolts for center bearing 78.4 ~93.1Nm