Page 113 of 281
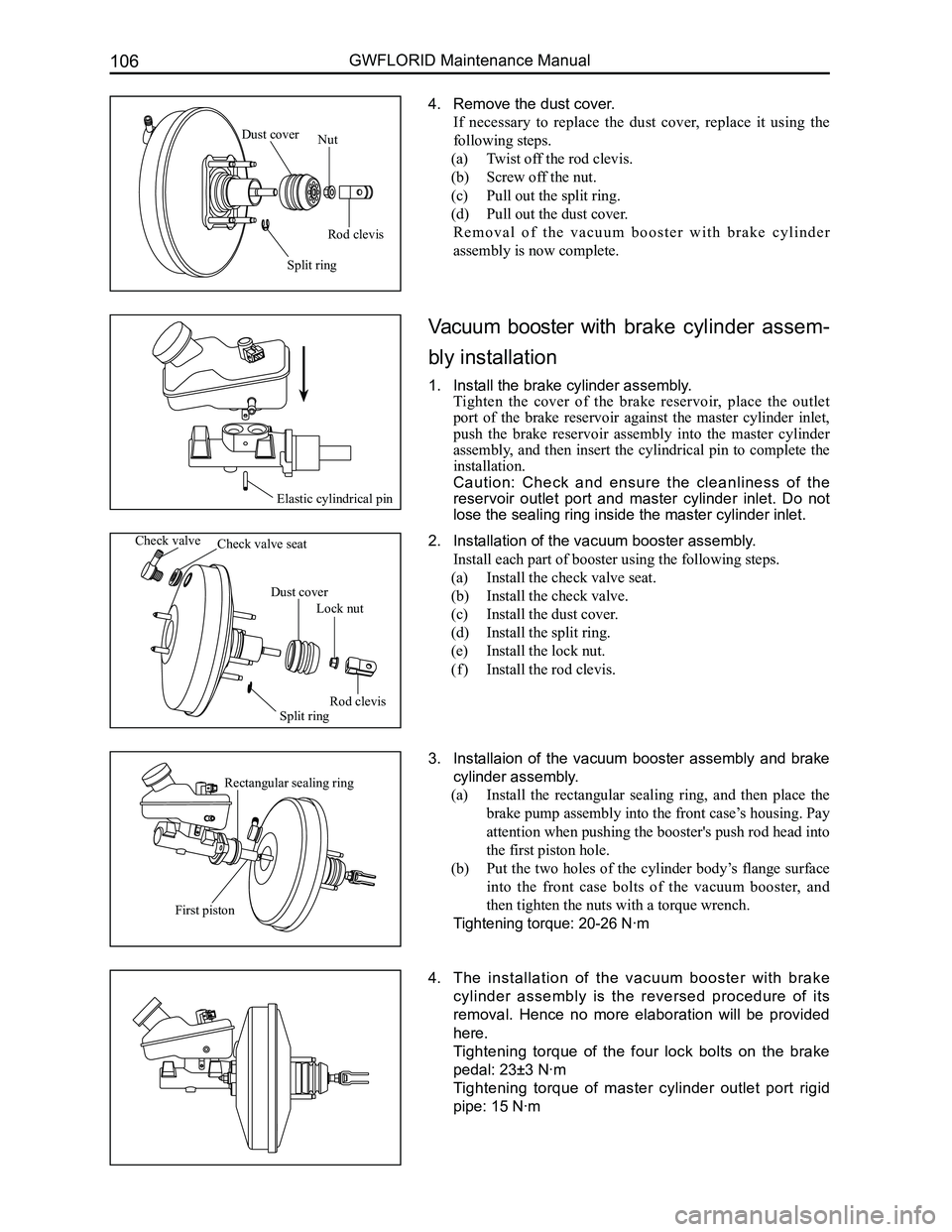
Downloaded from www.Manualslib.com manuals search engine GWFLORID Maintenance Manual106
4. Remove the dust cover.
If necessary to replace the dust cover, replace it using the
following steps.
(a) Twist off the rod clevis.
(b) Screw off the nut.
(c) Pull out the split ring.
(d) Pull out the dust cover.
R e m o v a l o f t h e v a c u u m b o o s t e r w i t h b r a k e c y l i n d e r
assembly is now complete.
Vacuum booster with brake cylinder assem-
bly installation
1. Install the brake cylinder assembly.
Tighten the cover of the brake reservoir, place the outlet
port of the brake reservoir against the master cylinder inlet,
push the brake reservoir assembly into the master cylinder
assembly, and then insert the cylindrical pin to complete the
installation.
Caution: Check and ensure the cleanliness of the
reservoir outlet port and master cylinder inlet. Do not
lose the sealing ring inside the master cylinder inlet.
2. Installation of the vacuum booster assembly.
Install each part of booster using the following steps.
(a) Install the check valve seat.
(b) Install the check valve.
(c) Install the dust cover.
(d) Install the split ring.
(e) Install the lock nut.
( f ) Install the rod clevis.
3. Installaion of the vacuum booster assembly and brake
cylinder assembly.
(a) Install the rectangular sealing ring, and then place the
brake pump assembly into the front case’s housing. Pay
attention when pushing the booster's push rod head into
the first piston hole.
(b) Put the two holes of the cylinder body’s flange surface
into the front case bolts of the vacuum booster, and
then tighten the nuts with a torque wrench.
Tightening torque: 20-26 N·m
4. The installation of the vacuum booster with brake
cylinder assembly is the reversed procedure of its
removal. Hence no more elaboration will be provided
here.
Tightening torque of the four lock bolts on the brake
pedal: 23±3 N·m
Tightening torque of master cylinder outlet port rigid
pipe: 15 N·m
Rod clevis
Nut
Split ring
Dust cover
Elastic cylindrical pin
Check valveCheck valve seat
Lock nut
Rod clevis
Split ring
Dust cover
Rectangular sealing ring
First piston
Page 114 of 281
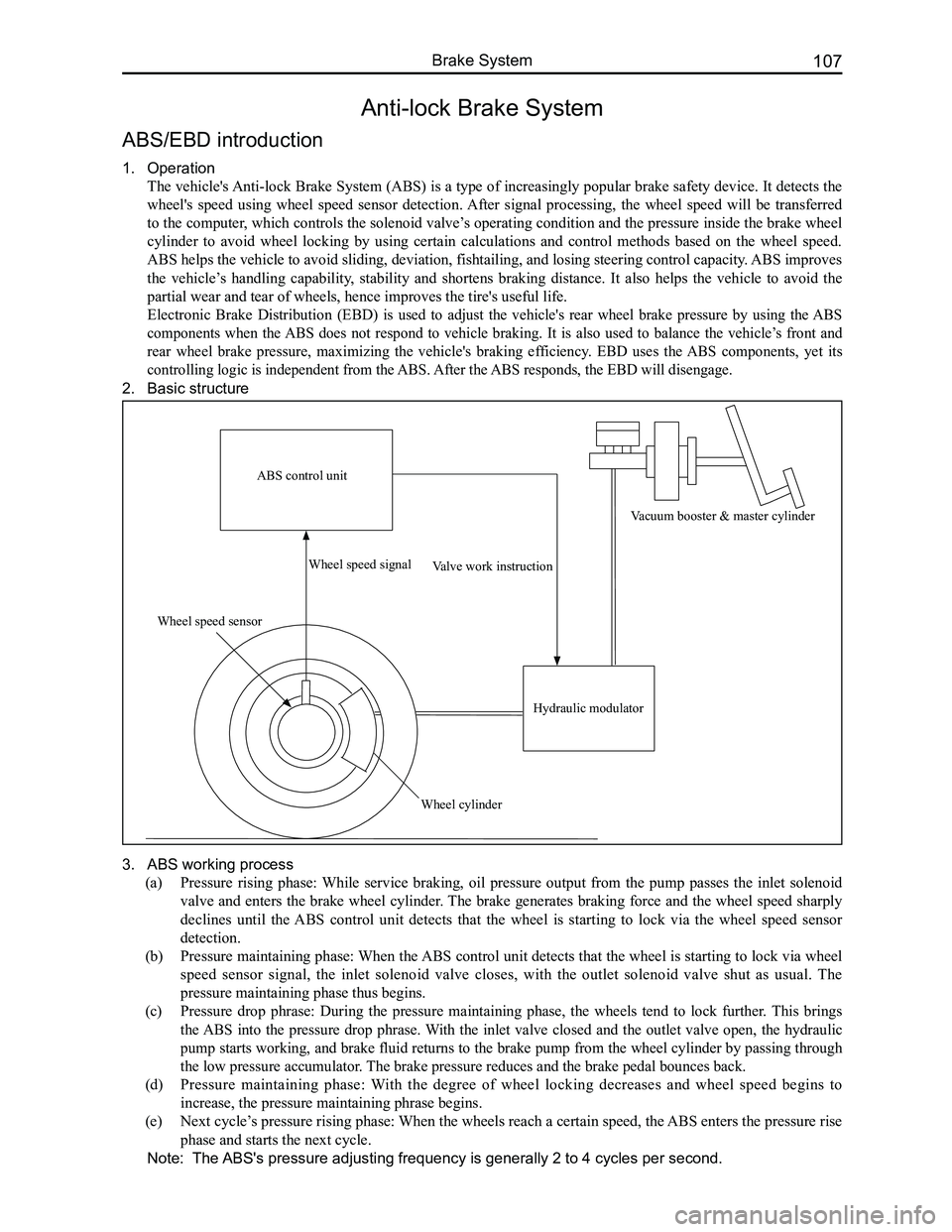
Downloaded from www.Manualslib.com manuals search engine 107Brake System
Anti-lock Brake System
ABS/EBD introduction
1. Operation
The vehicle's Anti-lock Brake System (ABS) is a type of increasingly popular brake safety device. It detects the
wheel's speed using wheel speed sensor detection. After signal processing, the wheel speed will be transferred
to the computer, which controls the solenoid valve’s operating condition and the pressure inside the brake wheel
cylinder to avoid wheel locking by using certain calculations and control methods based on the wheel speed.
ABS helps the vehicle to avoid sliding, deviation, fishtailing, and losing steering control capacity. ABS improves
the vehicle’s handling capability, stability and shortens braking distance. It also helps the vehicle to avoid the
partial wear and tear of wheels, hence improves the tire's useful life.
Electronic Brake Distribution (EBD) is used to adjust the vehicle's rear wheel brake pressure by using the ABS
components when the ABS does not respond to vehicle braking. It is also used to balance the vehicle’s front and
rear wheel brake pressure, maximizing the vehicle's braking efficiency. EBD uses the ABS components, yet its
controlling logic is independent from the ABS. After the ABS responds, the EBD will disengage.
2. Basic structure
3. ABS working process
(a) Pressure rising phase: While service braking, oil pressure output from the pump passes the inlet solenoid
valve and enters the brake wheel cylinder. The brake generates braking force and the wheel speed sharply
declines until the ABS control unit detects that the wheel is starting to lock via the wheel speed sensor
detection.
(b) Pressure maintaining phase: When the ABS control unit detects that the wheel is starting to lock via wheel
speed sensor signal, the inlet solenoid valve closes, with the outlet solenoid valve shut as usual. The
pressure maintaining phase thus begins.
(c) Pressure drop phrase: During the pressure maintaining phase, the wheels tend to lock further. This brings
the ABS into the pressure drop phrase. With the inlet valve closed and the outlet valve open, the hydraulic
pump starts working, and brake fluid returns to the brake pump from the wheel cylinder by passing through
the low pressure accumulator. The brake pressure reduces and the brake pedal bounces back.
(d) Pressure maintaining phase: With the degree of wheel locking decreases and wheel speed begins to
increase, the pressure maintaining phrase begins.
(e) Next cycle’s pressure rising phase: When the wheels reach a certain speed, the ABS enters the pressure rise
phase and starts the next cycle.
Note: The ABS's pressure adjusting frequency is generally 2 to 4 cycles per second.
ABS control unit
Wheel speed sensor
Wheel speed signal
Wheel cylinder
Valve work instruction
Hydraulic modulator
Vacuum booster & master cylinder
Page 115 of 281

Downloaded from www.Manualslib.com manuals search engine GWFLORID Maintenance Manual108
4. EBD working process
The EBD comes into effect when the wheel brakes are lightly applied. The wheel speed sensor detects the speed
of the wheels, and the ECU calculates the speed. If the rear wheel's slip ratio increases, adjust the brake pressure
to maintain or reduce the rear wheel's braking force. The EBD guarantees the rear wheel's lateral force and even
brake force distribution. If the ABS fails to respond, the electronic brake distribution system can still adjust the
rear wheel's braking force to guarantee the rear wheels do not lock before the front wheels, in order to ensure
vehicle safety.
The EBD's working process for lifting and holding pressure is completely the same as it of the ABS working
process. However, the process for lowering pressure is quite different. When the rear wheel has a tendency to
lock up, the normally open valve of the rear wheel closes, the normally closed valve opens, and the rear wheel
pressure reduces. The difference with ABS is that the hydraulic pump does not operate at this time, and the brake
fluid released during depressurization is temporarily stored in the low pressure accumulator. After braking,the brake
pedal is loosened, and the brake pressure inside the pump drops to zero. Open the normally closed valve one more
time at this point. The brake fluid inside the low pressure accumulator returns to the pump by passing through the
normally closed valve and normally open valve. Empty the low pressure ac\
cumulator to prepare for the next brake.
ABS installation
1. Install the ABS controller assembly.
(a) Use three hexagon bolts for flange face (Q1840825) to
fix the ABS bracket assembly onto the vehicle body.
(b) Fix the shock pad of the ABS hydraulic pump onto the
mounting holes of the ABS bracket assembly.
(c) Insert the mount pin of the ABS controller assembly
into the shock pad holes by simply inserting the two
anchor pins into the bracket.
2. Install the ABS front wheel speed sensor with bracket
assembly.
(a) Use a hexagon head bolt, spring washer, and flat
washer subassembly to connect the sensor and the
steering knuckle.
(b) Use a hexagon head bolt and a flat washer subassembly
(M8) to connect the sensor bracket and the damper.
(c) Use a hexagon head bolt and a flat washer subassembly
(M6) to connect the sensor bracket and vehicle body.
ABS controller assembly
ABS hydraulic pressure pump shock pad
ABS mounting bracket assembly
Wheel speed sensor with bracket assembly
Steering knuckle
Propeller shaft
Wheel slippage
Vehicle speed
Wheel speed
Master cylinder pressure
Wheel cylinder brake pressure
Page 116 of 281
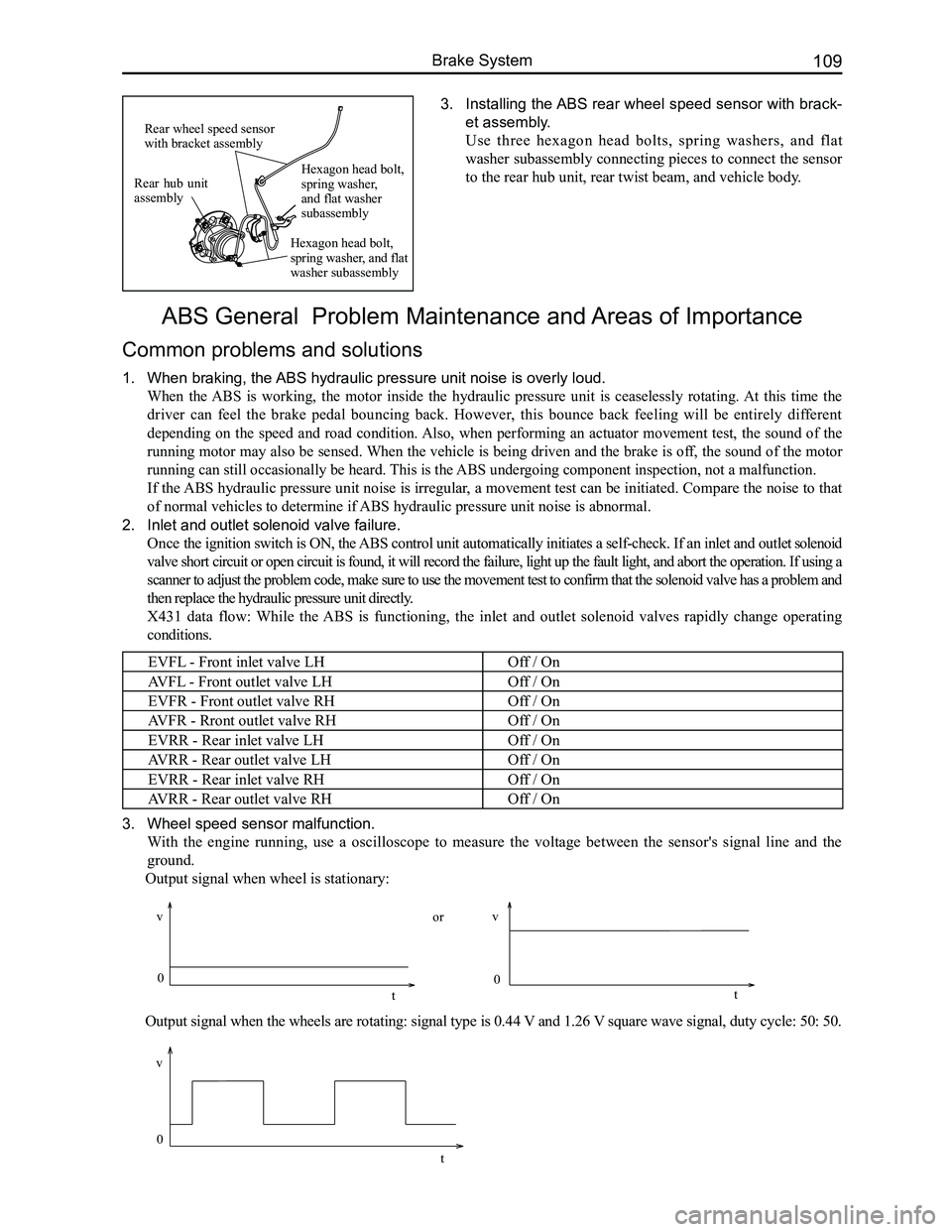
Downloaded from www.Manualslib.com manuals search engine 109Brake System
3. Installing the ABS rear wheel speed sensor with brack-
et assembly.
Use three hexagon head bolts, spring washers, and flat
washer subassembly connecting pieces to connect the sensor
to the rear hub unit, rear twist beam, and vehicle body.
ABS General Problem Maintenance and Areas of Importance
Common problems and solutions
1. When braking, the ABS hydraulic pressure unit noise is overly loud.
When the ABS is working, the motor inside the hydraulic pressure unit is ceaselessly rotating. At this time the
driver can feel the brake pedal bouncing back. However, this bounce back feeling will be entirely different
depending on the speed and road condition. Also, when performing an actuator movement test, the sound of the
running motor may also be sensed. When the vehicle is being driven and the brake is off, the sound of the motor
running can still occasionally be heard. This is the ABS undergoing component inspection, not a malfunction.
If the ABS hydraulic pressure unit noise is irregular, a movement test can be initiated. Compare the noise to that
of normal vehicles to determine if ABS hydraulic pressure unit noise is abnormal.
2. Inlet and outlet solenoid valve failure.
Once the ignition switch is ON, the ABS control unit automatically initiates a self-check. If an inlet and outlet solenoid
valve short circuit or open circuit is found, it will record the failure, light up the fault light, and abort the operation. If using a
scanner to adjust the problem code, make sure to use the movement test t\
o confirm that the solenoid valve has a problem and
then replace the hydraulic pressure unit directly.
X431 data flow: While the ABS is functioning, the inlet and outlet solenoid valves rapidly change operating
conditions.
EVFL - Front inlet valve LHOff / On
AVFL - Front outlet valve LHOff / On
EVFR - Front outlet valve RHOff / On
AVFR - Rront outlet valve RHOff / On
EVRR - Rear inlet valve LHOff / On
AVRR - Rear outlet valve LHOff / On
EVRR - Rear inlet valve RHOff / On
AVRR - Rear outlet valve RHOff / On
3. Wheel speed sensor malfunction.
With the engine running, use a oscilloscope to measure the voltage between the sensor's signal line and the
ground.
Output signal when wheel is stationary:
Output signal when the wheels are rotating: signal type is 0.44 V and 1.26 V square wave signal, duty cycle: 50: 50.
Rear hub unit assembly
Rear wheel speed sensor with bracket assembly
Hexagon head bolt, spring washer, and flat washer subassembly
Hexagon head bolt, spring washer, and flat washer subassembly
0
v
t
vv
0 0
tt
or
Page 117 of 281
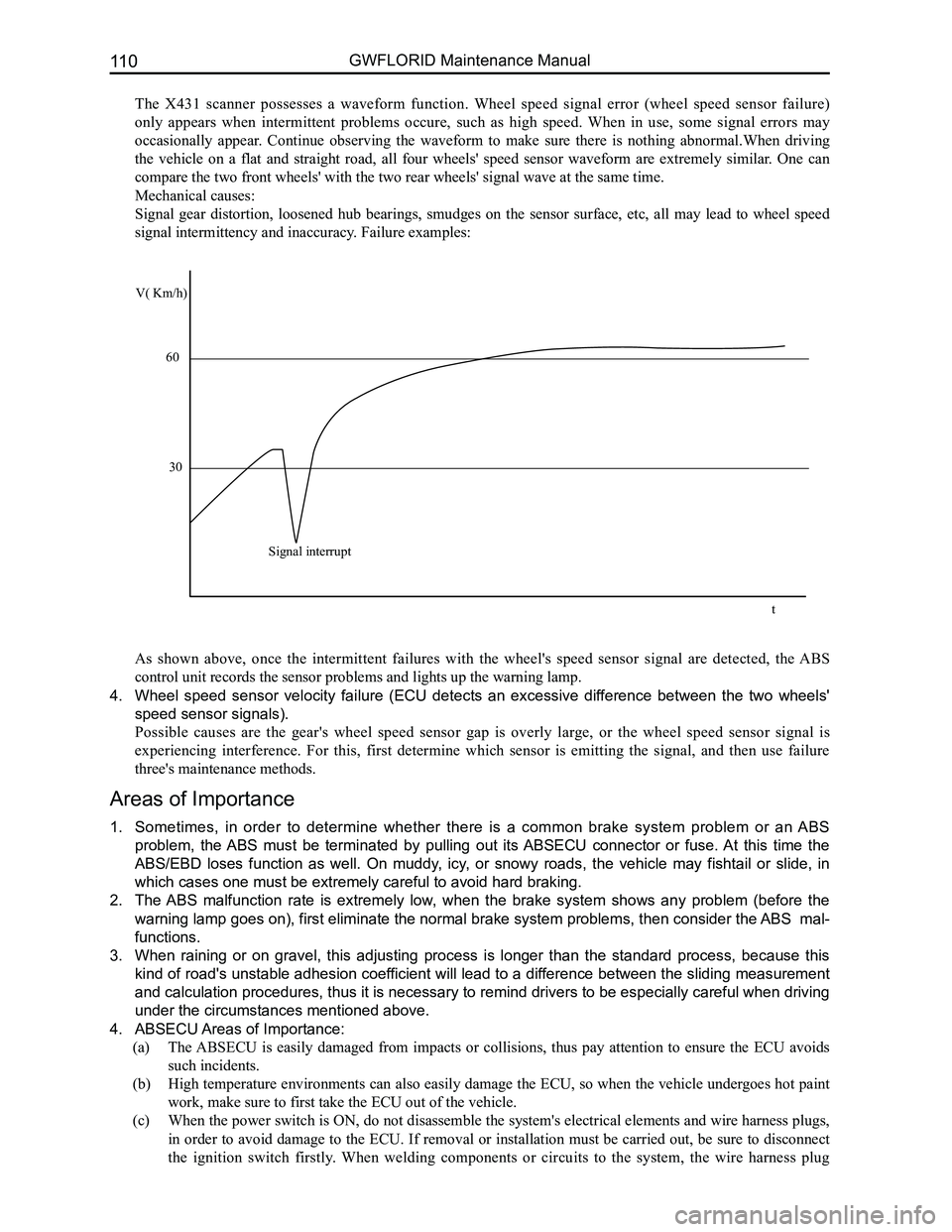
Downloaded from www.Manualslib.com manuals search engine GWFLORID Maintenance Manual110
The X431 scanner possesses a waveform function. Wheel speed signal error (wheel speed sensor failure)
only appears when intermittent problems occure, such as high speed. When in use, some signal errors may
occasionally appear. Continue observing the waveform to make sure there is nothing abnormal.When driving
the vehicle on a flat and straight road, all four wheels' speed sensor waveform are extremely similar. One can
compare the two front wheels' with the two rear wheels' signal wave at t\
he same time.
Mechanical causes:
Signal gear distortion, loosened hub bearings, smudges on the sensor surface, etc, all may lead to wheel speed
signal intermittency and inaccuracy. Failure examples:
As shown above, once the intermittent failures with the wheel's speed sensor signal are detected, the ABS
control unit records the sensor problems and lights up the warning lamp.\
4. Wheel speed sensor velocity failure (ECU detects an excessive difference between the two wheels'
speed sensor signals).
Possible causes are the gear's wheel speed sensor gap is overly large, or the wheel speed sensor signal is
experiencing interference. For this, first determine which sensor is emitting the signal, and then use failure
three's maintenance methods.
Areas of Importance
1. Sometimes, in order to determine whether there is a common brake system problem or an ABS
problem, the ABS must be terminated by pulling out its ABSECU connector or fuse. At this time the
ABS/EBD loses function as well. On muddy, icy, or snowy roads, the vehicle may fishtail or slide, in
which cases one must be extremely careful to avoid hard braking.
2. The ABS malfunction rate is extremely low, when the brake system shows any problem (before the
warning lamp goes on), first eliminate the normal brake system problems, then consider the ABS mal-
functions.
3. When raining or on gravel, this adjusting process is longer than the standard process, because this
kind of road's unstable adhesion coefficient will lead to a difference between the sliding measurement
and calculation procedures, thus it is necessary to remind drivers to be especially careful when driving
under the circumstances mentioned above.
4. ABSECU Areas of Importance:
(a) The ABSECU is easily damaged from impacts or collisions, thus pay attention to ensure the ECU avoids
such incidents.
(b) High temperature environments can also easily damage the ECU, so when the vehicle undergoes hot paint
work, make sure to first take the ECU out of the vehicle.
(c) When the power switch is ON, do not disassemble the system's electrical elements and wire harness plugs,
in order to avoid damage to the ECU. If removal or installation must be carried out, be sure to disconnect
the ignition switch firstly. When welding components or circuits to the system, the wire harness plug
V( Km/h)
60
30
Signal interrupt
t
Page 118 of 281
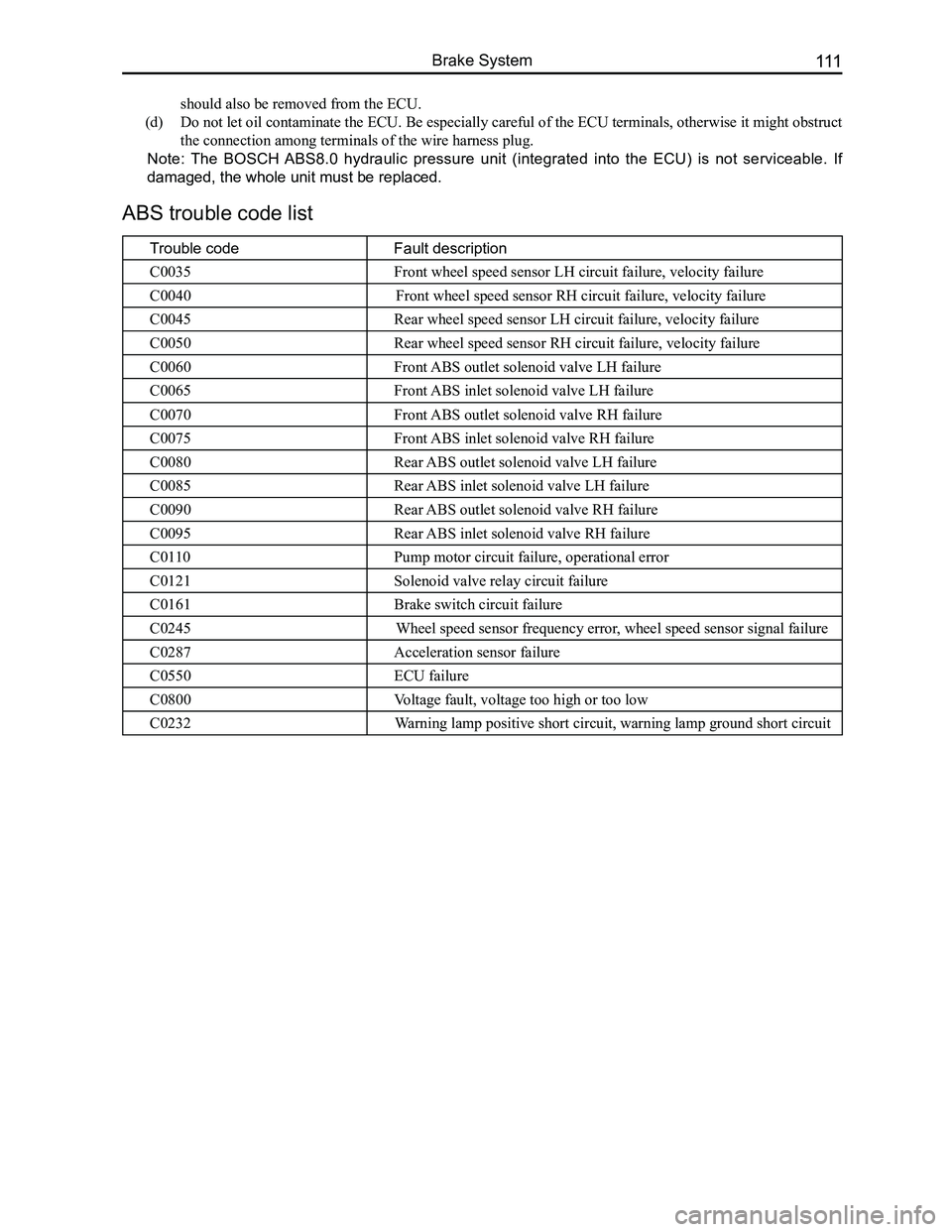
Downloaded from www.Manualslib.com manuals search engine 111Brake System
ABS trouble code list
Trouble codeFault description
C0035Front wheel speed sensor LH circuit failure, velocity failure
C0040Front wheel speed sensor RH circuit failure, velocity failure
C0045Rear wheel speed sensor LH circuit failure, velocity failure
C0050Rear wheel speed sensor RH circuit failure, velocity failure
C0060Front ABS outlet solenoid valve LH failure
C0065Front ABS inlet solenoid valve LH failure
C0070Front ABS outlet solenoid valve RH failure
C0075Front ABS inlet solenoid valve RH failure
C0080Rear ABS outlet solenoid valve LH failure
C0085Rear ABS inlet solenoid valve LH failure
C0090Rear ABS outlet solenoid valve RH failure
C0095Rear ABS inlet solenoid valve RH failure
C0110Pump motor circuit failure, operational error
C0121Solenoid valve relay circuit failure
C0161Brake switch circuit failure
C0245Wheel speed sensor frequency error, wheel speed sensor signal failure
C0287Acceleration sensor failure
C0550ECU failure
C0800Voltage fault, voltage too high or too low
C0232Warning lamp positive short circuit, warning lamp ground short circuit
should also be removed from the ECU.
(d) Do not let oil contaminate the ECU. Be especially careful of the ECU terminals, otherwise it might obstruct
the connection among terminals of the wire harness plug.
Note: The BOSCH ABS8.0 hydraulic pressure unit (integrated into the ECU) is not serviceable. If
damaged, the whole unit must be replaced.
Page 119 of 281
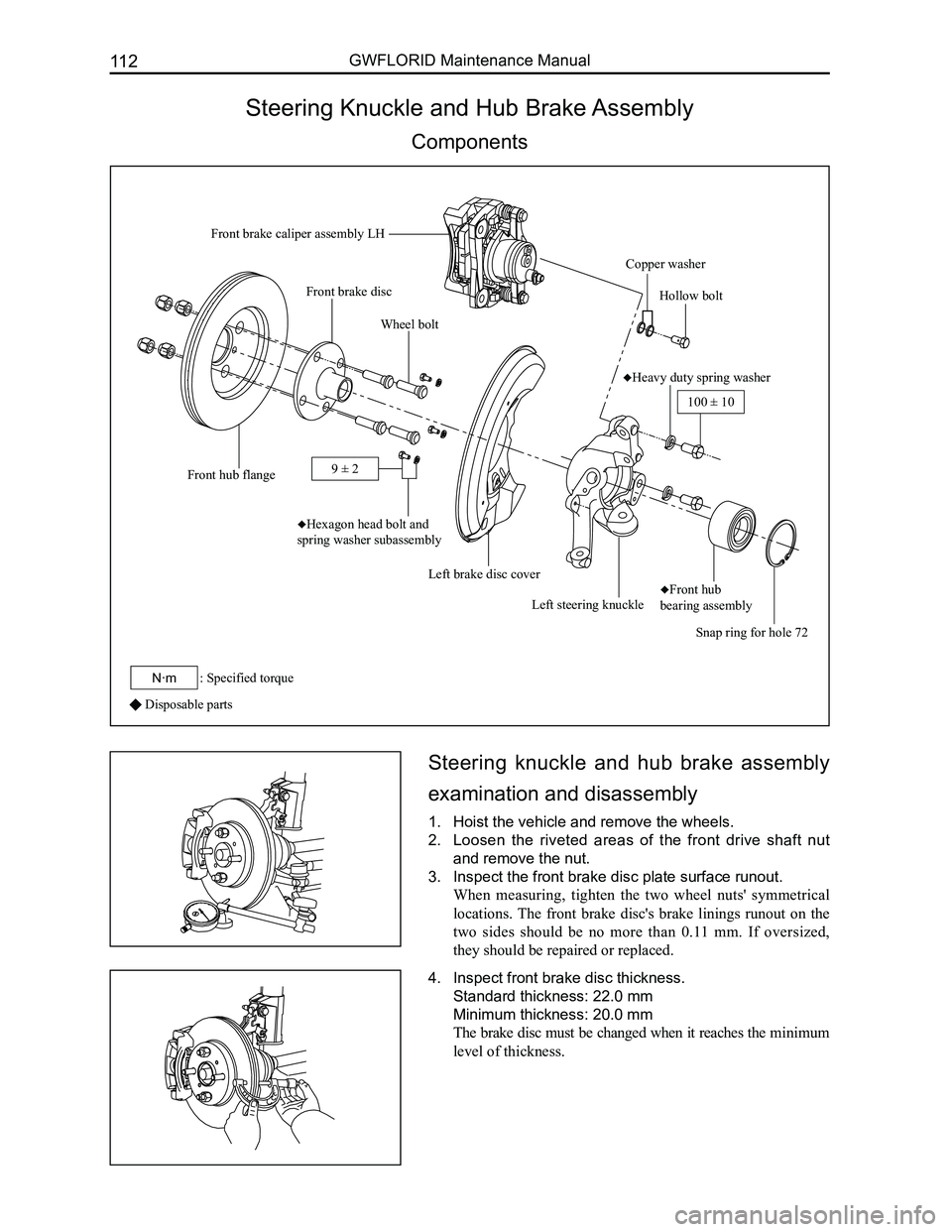
Downloaded from www.Manualslib.com manuals search engine GWFLORID Maintenance Manual112
Steering Knuckle and Hub Brake Assembly
Components
Disposable parts
Steering knuckle and hub brake assembly
examination and disassembly
1. Hoist the vehicle and remove the wheels.
2. Loosen the riveted areas of the front drive shaft nut
and remove the nut.
3. Inspect the front brake disc plate surface runout.
When measuring, tighten the two wheel nuts' symmetrical
locations. The front brake disc's brake linings runout on the
two sides should be no more than 0.11 mm. If oversized,
they should be repaired or replaced.
4. Inspect front brake disc thickness.
Standard thickness: 22.0 mm
Minimum thickness: 20.0 mm
The brake disc must be changed when it reaches the minimum
level of thickness.
Front brake caliper assembly LH
Copper washer
Hollow bolt
♦Heavy duty spring washer
Snap ring for hole 72
♦Front hub
bearing assemblyLeft steering knuckle
Left brake disc cover
♦Hexagon head bolt and
spring washer subassembly
Wheel bolt
Front hub flange
Front brake disc
100 ± 10
: Specified torqueN·m
9 ± 2
Page 120 of 281
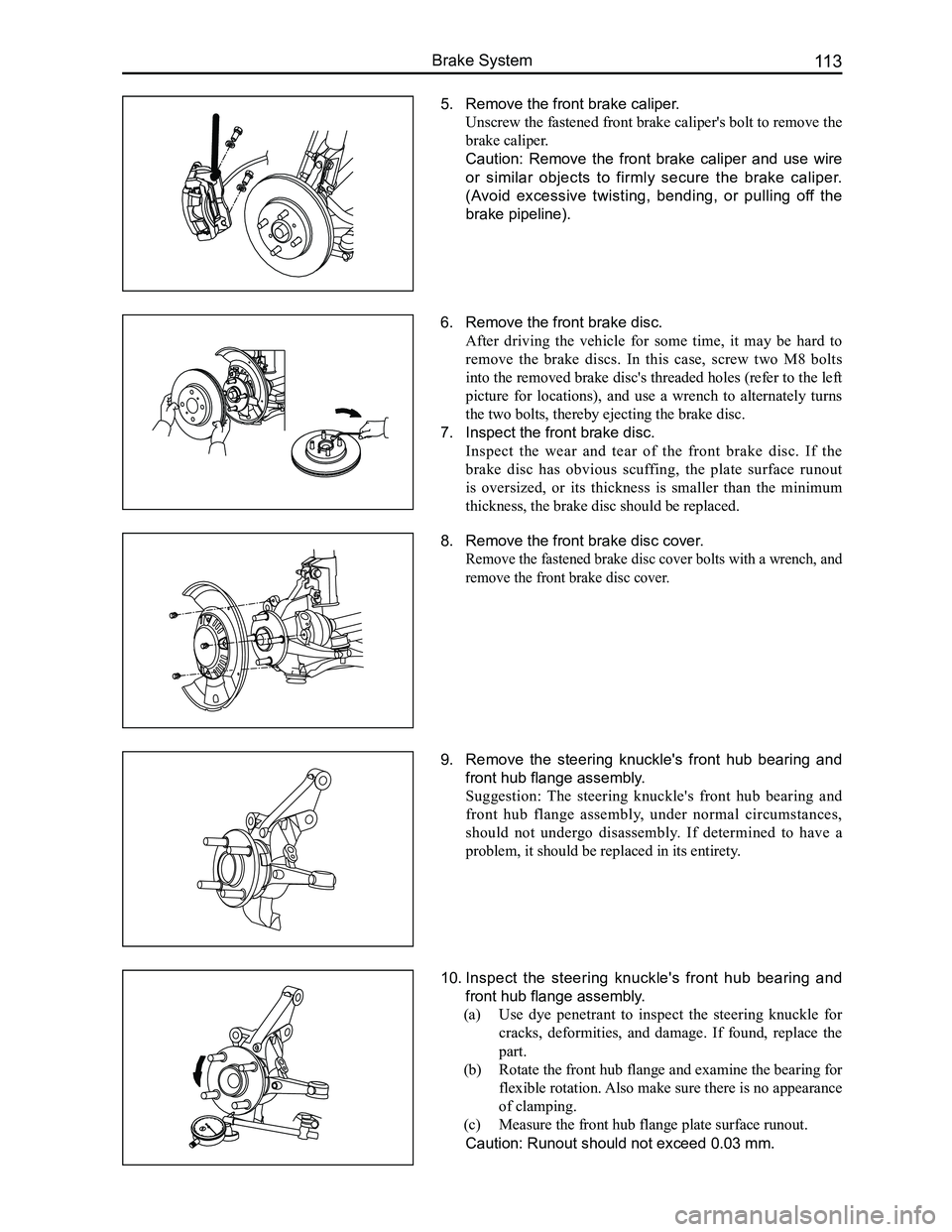
Downloaded from www.Manualslib.com manuals search engine 113Brake System
5. Remove the front brake caliper.
Unscrew the fastened front brake caliper's bolt to remove the
brake caliper.
Caution: Remove the front brake caliper and use wire
or similar objects to firmly secure the brake caliper.
(Avoid excessive twisting, bending, or pulling off the
brake pipeline).
6. Remove the front brake disc.
After driving the vehicle for some time, it may be hard to
remove the brake discs. In this case, screw two M8 bolts
into the removed brake disc's threaded holes (refer to the left
picture for locations), and use a wrench to alternately turns
the two bolts, thereby ejecting the brake disc.
7. Inspect the front brake disc.
Inspect the wear and tear of the front brake disc. If the
brake disc has obvious scuffing, the plate surface runout
is oversized, or its thickness is smaller than the minimum
thickness, the brake disc should be replaced.
8. Remove the front brake disc cover.
Remove the fastened brake disc cover bolts with a wrench, and
remove the front brake disc cover.
9. Remove the steering knuckle's front hub bearing and
front hub flange assembly.
Suggestion: The steering knuckle's front hub bearing and
front hub flange assembly, under normal circumstances,
should not undergo disassembly. If determined to have a
problem, it should be replaced in its entirety.
10. Inspect the steering knuckle's front hub bearing and
front hub flange assembly.
(a) Use dye penetrant to inspect the steering knuckle for
cracks, deformities, and damage. If found, replace the
part.
(b) Rotate the front hub flange and examine the bearing for
flexible rotation. Also make sure there is no appearance
of clamping.
(c) Measure the front hub flange plate surface runout.
Caution: Runout should not exceed 0.03 mm.