Page 145 of 281
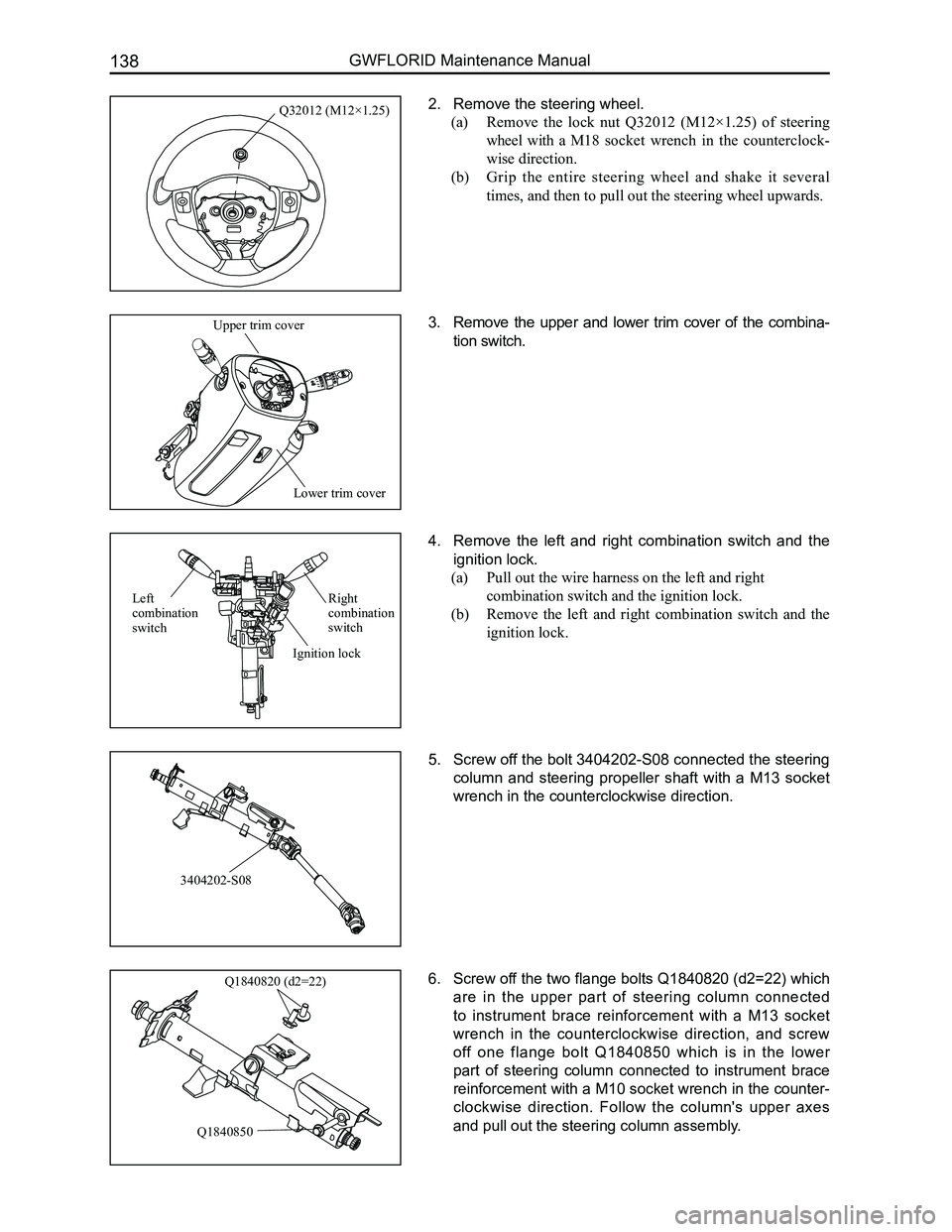
Downloaded from www.Manualslib.com manuals search engine GWFLORID Maintenance Manual138
2. Remove the steering wheel.
(a) Remove the lock nut Q32012 (M12×1.25) of steering
wheel with a M18 socket wrench in the counterclock-
wise direction.
(b) Grip the entire steering wheel and shake it several
times, and then to pull out the steering wheel upwards.
3. Remove the upper and lower trim cover of the combina-
tion switch.
4. Remove the left and right combination switch and the
ignition lock.
(a) Pull out the wire harness on the left and right
combination switch and the ignition lock.
(b) Remove the left and right combination switch and the
ignition lock.
5. Screw off the bolt 3404202-S08 connected the steering
column and steering propeller shaft with a M13 socket
wrench in the counterclockwise direction.
6. Screw off the two flange bolts Q1840820 (d2=22) which
are in the upper part of steering column connected
to instrument brace reinforcement with a M13 socket
wrench in the counterclockwise direction, and screw
off one flange bolt Q1840850 which is in the lower
part of steering column connected to instrument brace
reinforcement with a M10 socket wrench in the counter-
clockwise direction. Follow the column's upper axes
and pull out the steering column assembly.
Q32012 (M12×1.25)
Lower trim cover
Upper trim cover
3404202-S08
Q1840820 (d2=22)
Q1840850
Right combination switch
Left combination switch
Ignition lock
Page 146 of 281
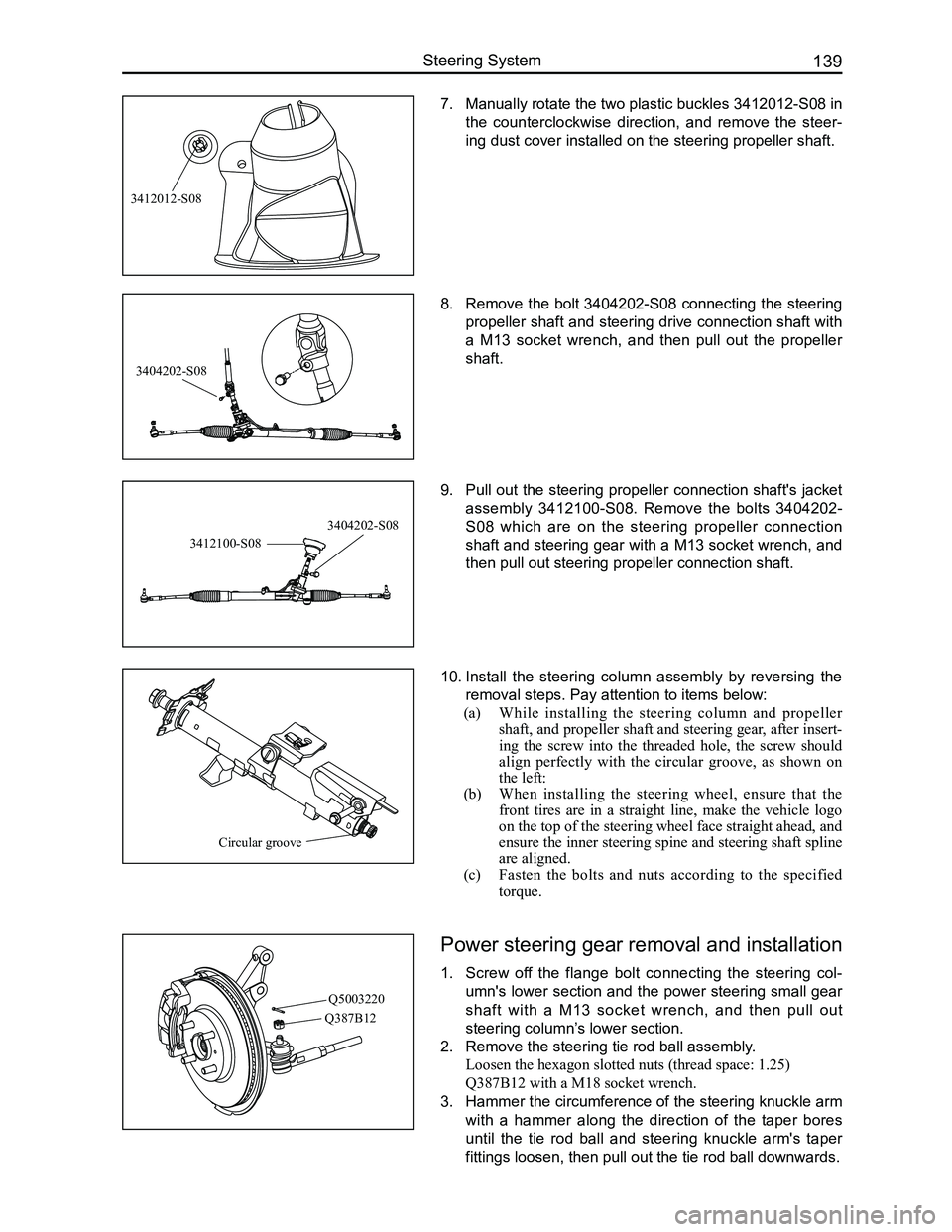
Downloaded from www.Manualslib.com manuals search engine 139Steering System
7. Manually rotate the two plastic buckles 3412012-S08 in
the counterclockwise direction, and remove the steer-
ing dust cover installed on the steering propeller shaft.
8. Remove the bolt 3404202-S08 connecting the steering
propeller shaft and steering drive connection shaft with
a M13 socket wrench, and then pull out the propeller
shaft.
9. Pull out the steering propeller connection shaft's jacket
assembly 3412100-S08. Remove the bolts 3404202-
S08 which are on the steering propeller connection
shaft and steering gear with a M13 socket wrench, and
then pull out steering propeller connection shaft.
10. Install the steering column assembly by reversing the
removal steps. Pay attention to items below:
(a) While installing the steering column and propeller
shaft, and propeller shaft and steering gear, after insert-
ing the screw into the threaded hole, the screw should
align perfectly with the circular groove, as shown on
the left:
(b) When installing the steering wheel, ensure that the
front tires are in a straight line, make the vehicle logo
on the top of the steering wheel face straight ahead, and
ensure the inner steering spine and steering shaft spline
are aligned.
(c) Fasten the bolts and nuts according to the specified
torque.
3412012-S08
Circular groove
3412100-S08
3404202-S08
Power steering gear removal and installation
1. Screw off the flange bolt connecting the steering col-
umn's lower section and the power steering small gear
shaft with a M13 socket wrench, and then pull out
steering column’s lower section.
2. Remove the steering tie rod ball assembly.
Loosen the hexagon slotted nuts (thread space: 1.25)
Q387B12 with a M18 socket wrench.
3. Hammer the circumference of the steering knuckle arm
with a hammer along the direction of the taper bores
until the tie rod ball and steering knuckle arm's taper
fittings loosen, then pull out the tie rod ball downwards.
Q5003220
Q387B12
3404202-S08
Page 147 of 281
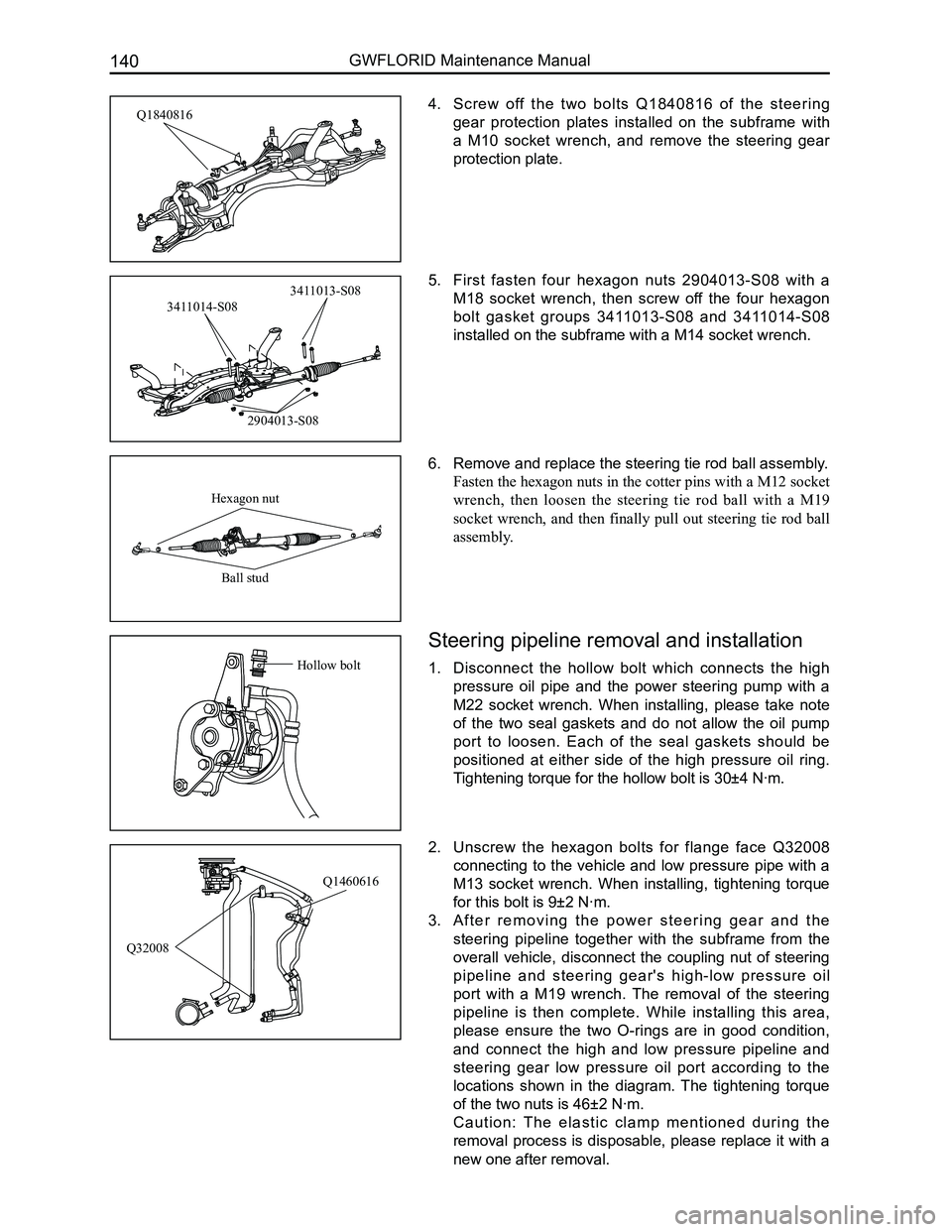
Downloaded from www.Manualslib.com manuals search engine GWFLORID Maintenance Manual140
4. Screw off the two bolts Q1840816 of the steering
gear protection plates installed on the subframe with
a M10 socket wrench, and remove the steering gear
protection plate.
5. First fasten four hexagon nuts 2904013-S08 with a
M18 socket wrench, then screw off the four hexagon
bolt gasket groups 3411013-S08 and 3411014-S08
installed on the subframe with a M14 socket wrench.
6. Remove and replace the steering tie rod ball assembly.
Fasten the hexagon nuts in the cotter pins with a M12 socket
wrench, then loosen the steering tie rod ball with a M19
socket wrench, and then finally pull out steering tie rod ball
assembly.
2. Unscrew the hexagon bolts for flange face Q32008
connecting to the vehicle and low pressure pipe with a
M13 socket wrench. When installing, tightening torque
for this bolt is 9±2 N·m.
3. A f t e r r e m o v i n g t h e p o w e r s t e e r i n g g e a r a n d t h e
steering pipeline together with the subframe from the
overall vehicle, disconnect the coupling nut of steering
pipeline and steering gear's high-low pressure oil
port with a M19 wrench. The removal of the steering
pipeline is then complete. While installing this area,
please ensure the two O-rings are in good condition,
and connect the high and low pressure pipeline and
steering gear low pressure oil port according to the
locations shown in the diagram. The tightening torque
of the two nuts is 46±2 N·m.
C a u t i o n : T h e e l a s t i c c l a m p m e n t i o n e d d u r i n g t h e
removal process is disposable, please replace it with a
new one after removal.
Q1460616
Q32008
Q1840816
2904013-S08
3411014-S08
3411013-S08
Hexagon nut
Ball stud
Steering pipeline removal and installation
1. Disconnect the hollow bolt which connects the high
pressure oil pipe and the power steering pump with a
M22 socket wrench. When installing, please take note
of the two seal gaskets and do not allow the oil pump
port to loosen. Each of the seal gaskets should be
positioned at either side of the high pressure oil ring.
Tightening torque for the hollow bolt is 30±4 N·m.
Hollow bolt
Page 148 of 281
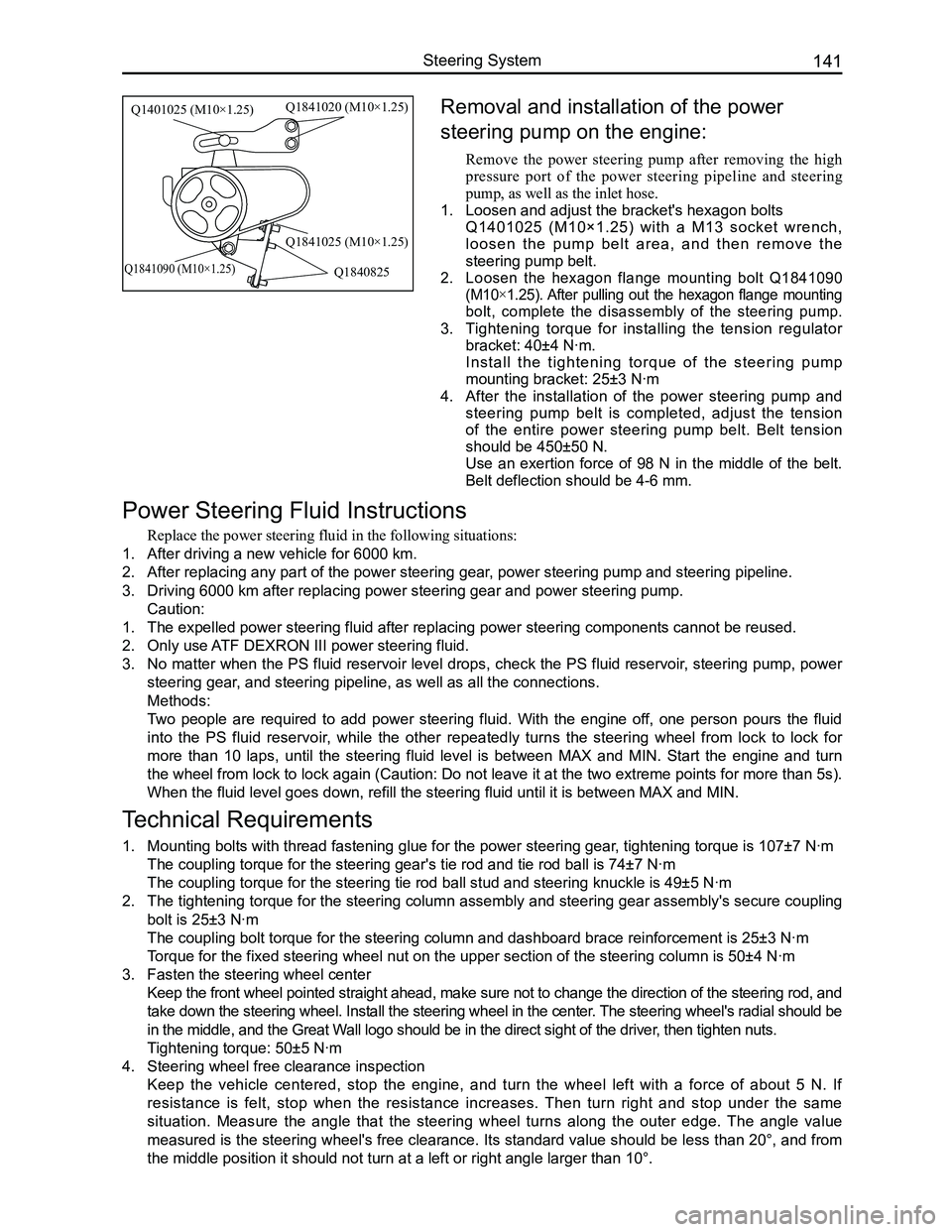
Downloaded from www.Manualslib.com manuals search engine 141Steering System
Removal and installation of the power
steering pump on the engine:
Remove the power steering pump after removing the high
pressure port of the power steering pipeline and steering
pump, as well as the inlet hose.
1. Loosen and adjust the bracket's hexagon bolts
Q1401025 (M10×1.25) with a M13 socket wrench,
l o o s e n t h e p u m p b e l t a r e a , a n d t h e n r e m o v e t h e
steering pump belt.
2. Loosen the hexagon flange mounting bolt Q1841090
(M10×1.25). After pulling out the hexagon flange mounting
bolt, complete the disassembly of the steering pump.
3. Tightening torque for installing the tension regulator
bracket: 40±4 N·m.
Install the tightening torque of the steering pump
mounting bracket: 25±3 N·m
4. After the installation of the power steering pump and
steering pump belt is completed, adjust the tension
of the entire power steering pump belt. Belt tension
should be 450±50 N.
Use an exertion force of 98 N in the middle of the belt.
Belt deflection should be 4-6 mm.
Power Steering Fluid Instructions
Replace the power steering fluid in the following situations:
1. After driving a new vehicle for 6000 km.
2. After replacing any part of the power steering gear, power steering pump and steering pipeline.
3. Driving 6000 km after replacing power steering gear and power steering p\
ump.
Caution:
1. The expelled power steering fluid after replacing power steering compone\
nts cannot be reused.
2. Only use ATF DEXRON III power steering fluid.
3. No matter when the PS fluid reservoir level drops, check the PS fluid reservoir, steering pump, power
steering gear, and steering pipeline, as well as all the connections.
Methods:
Two people are required to add power steering fluid. With the engine off, one person pours the fluid
into the PS fluid reservoir, while the other repeatedly turns the steering wheel from lock to lock for
more than 10 laps, until the steering fluid level is between MAX and MIN. Start the engine and turn
the wheel from lock to lock again (Caution: Do not leave it at the two extreme points for more than 5s).
When the fluid level goes down, refill the steering fluid until it is be\
tween MAX and MIN.
Technical Requirements
1. Mounting bolts with thread fastening glue for the power steering gear, tightening torque is 107±7 N·m
The coupling torque for the steering gear's tie rod and tie rod ball is \
74±7 N·m
The coupling torque for the steering tie rod ball stud and steering knuc\
kle is 49±5 N·m
2. The tightening torque for the steering column assembly and steering gear assembly's secure coupling
bolt is 25±3 N·m
The coupling bolt torque for the steering column and dashboard brace rei\
nforcement is 25±3 N·m
Torque for the fixed steering wheel nut on the upper section of the steer\
ing column is 50±4 N·m
3. Fasten the steering wheel center
Keep the front wheel pointed straight ahead, make sure not to change the direction of the steering rod, and
take down the steering wheel. Install the steering wheel in the center. The steering wheel's radial should be
in the middle, and the Great Wall logo should be in the direct sight of the driver, then tighten nuts.
Tightening torque: 50±5 N·m
4. Steering wheel free clearance inspection
Keep the vehicle centered, stop the engine, and turn the wheel left with a force of about 5 N. If
resistance is felt, stop when the resistance increases. Then turn right and stop under the same
situation. Measure the angle that the steering wheel turns along the outer edge. The angle value
measured is the steering wheel's free clearance. Its standard value should be less than 20°, and from
the middle position it should not turn at a left or right angle larger t\
han 10°.
Q1401025 (M10×1.25)Q1841020 (M10×1.25)
Q1841025 (M10×1.25)
Q1840825Q1841090 (M10×1.25)
Page 149 of 281
Downloaded from www.Manualslib.com manuals search engine GWFLORID Maintenance Manual142
Basic Information on the Electrical System ........................143
Fuse Box ........................................................................\
....144
Overall Vehicle’s Grounding Point Schematics ..................150
Key Electrical Component’s Module Schematics for
the Overall Vehicle..............................................................151
Wire Harness Distribution Chart for the Overall Vehicle .....152
Wire Harness Relationship and Plug-in Connections
Numbered Diagram ............................................................155
Wire Harness Plug-in Connectors and
Pin Function Diagram .........................................................156
Electrical Wiring Diagram for the Overall Vehicle ...............167
Vehicle Body Electrical System
Page 150 of 281
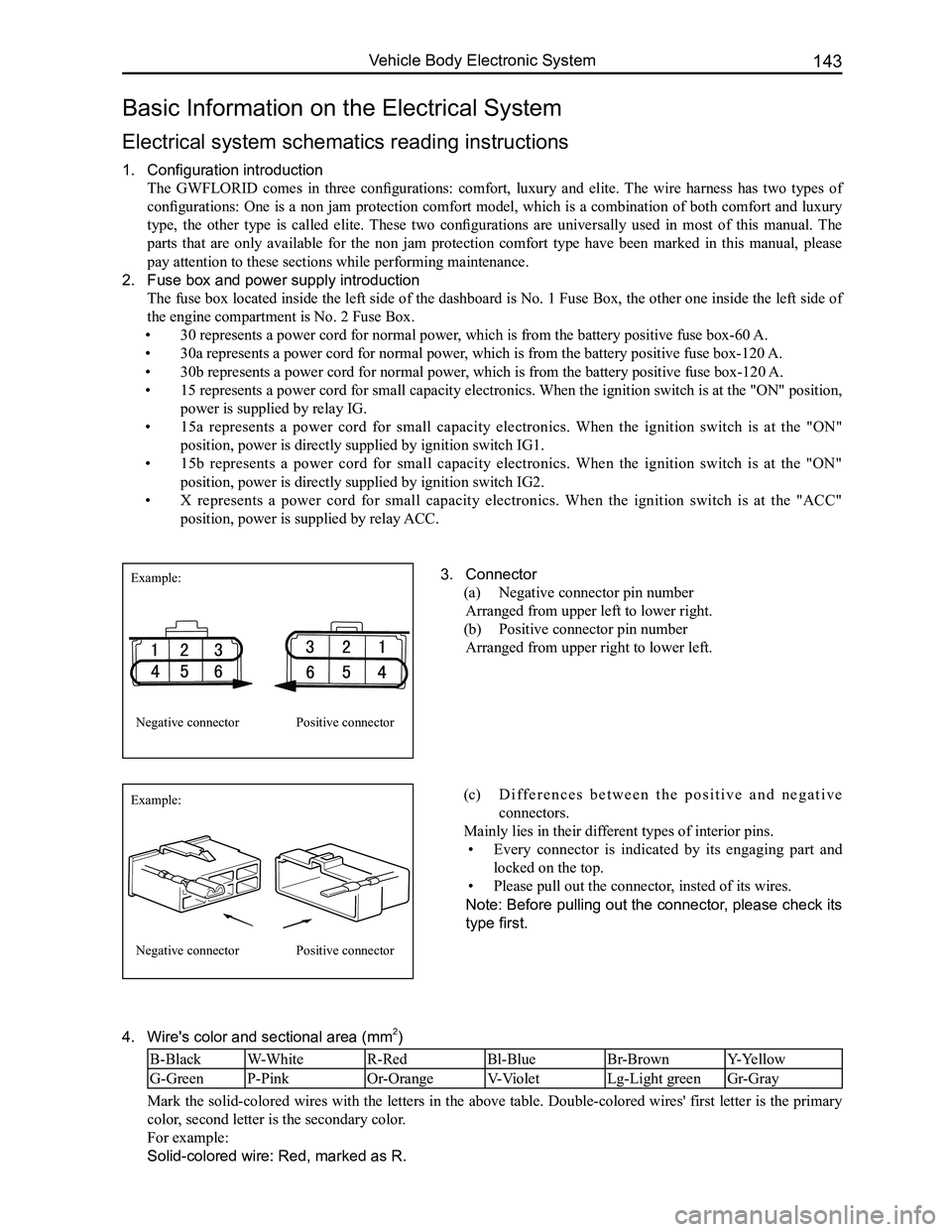
Downloaded from www.Manualslib.com manuals search engine 143Vehicle Body Electronic System
Basic Information on the Electrical System
Electrical system schematics reading instructions
1. Configuration introduction
The GWFLORID comes in three configurations: comfort, luxury and elite. The wire harness has two types of
configurations: One is a non jam protection comfort model, which is a combination of both comfort and luxury
type, the other type is called elite. These two configurations are universally used in most of this manual. The
parts that are only available for the non jam protection comfort type have been marked in this manual, please
pay attention to these sections while performing maintenance.
2. Fuse box and power supply introduction
The fuse box located inside the left side of the dashboard is No. 1 Fuse Box, the other one inside the left side of
the engine compartment is No. 2 Fuse Box.
• 30 represents a power cord for normal power, which is from the battery positive fuse box-60 A.
• 30a represents a power cord for normal power, which is from the battery positive fuse box-120 A.
• 30b represents a power cord for normal power, which is from the battery positive fuse box-120 A.
• 15 represents a power cord for small capacity electronics. When the ignition switch is at the "ON" position,
power is supplied by relay IG.
• 15a represents a power cord for small capacity electronics. When the ignition switch is at the "ON"
position, power is directly supplied by ignition switch IG1.
• 15b represents a power cord for small capacity electronics. When the ignition switch is at the "ON"
position, power is directly supplied by ignition switch IG2.
• X represents a power cord for small capacity electronics. When the ignition switch is at the "ACC"
position, power is supplied by relay ACC.
4. Wire's color and sectional area (mm2)
B-BlackW-WhiteR-RedBl-BlueBr-BrownY-Yellow
G-GreenP-PinkOr-OrangeV-VioletLg-Light greenGr-Gray
Mark the solid-colored wires with the letters in the above table. Double-colored wires' first letter is the primary
color, second letter is the secondary color.
For example:
Solid-colored wire: Red, marked as R.
3. Connector
(a) Negative connector pin number
Arranged from upper left to lower right.
(b) Positive connector pin number
Arranged from upper right to lower left.
Example:
Example:
Negative connector
Negative connector
Positive connector
Positive connector
(c) D i f f e r e n c e s b e t w e e n t h e p o s i t i v e a n d n e g a t i v e
connectors.
Mainly lies in their different types of interior pins.
• Every connector is indicated by its engaging part and
locked on the top.
• Please pull out the connector, insted of its wires.
Note: Before pulling out the connector, please check its
type first.
Page 151 of 281
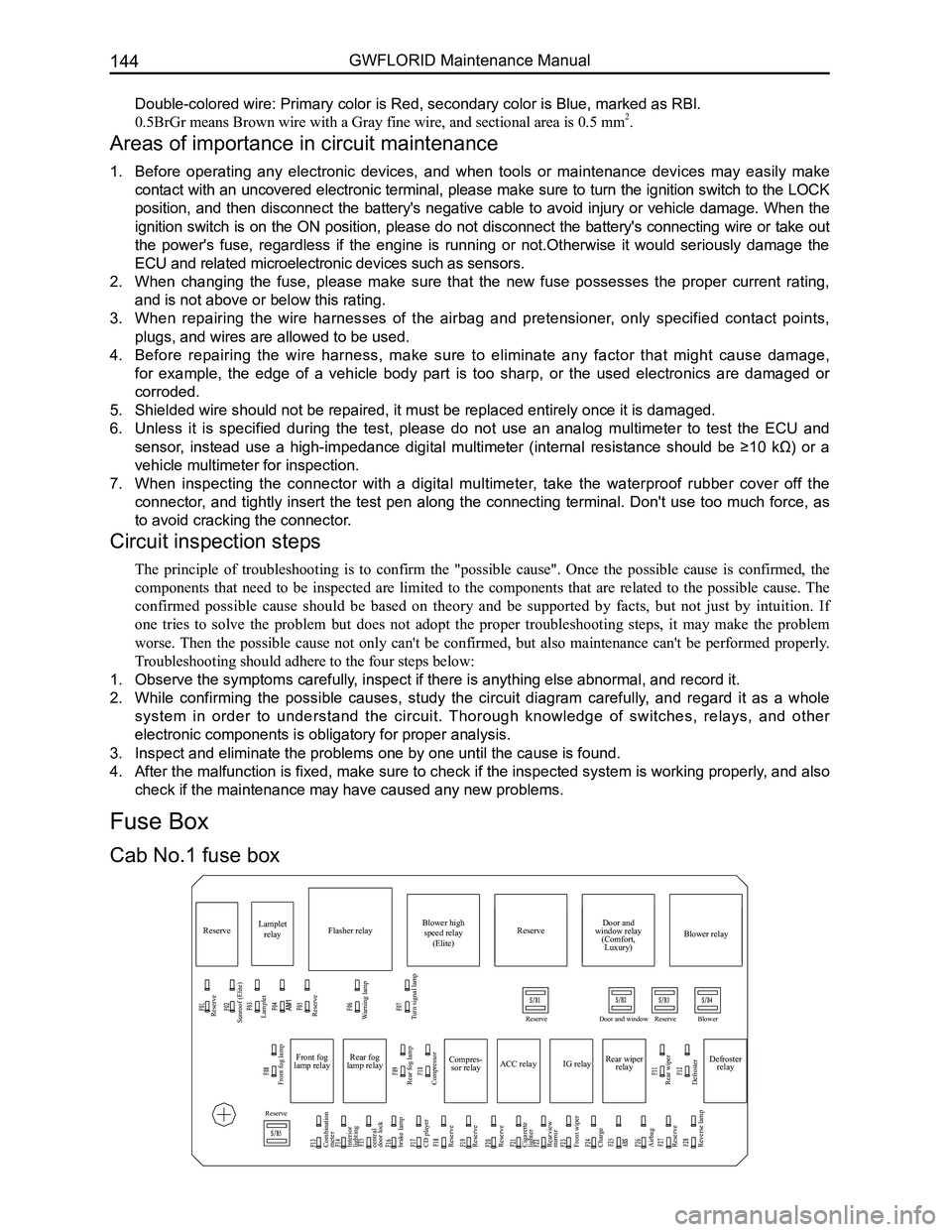
Downloaded from www.Manualslib.com manuals search engine GWFLORID Maintenance Manual144
Double-colored wire: Primary color is Red, secondary color is Blue, mark\
ed as RBl.
0.5BrGr means Brown wire with a Gray fine wire, and sectional area is 0.\
5 mm2.
Areas of importance in circuit maintenance
1. Before operating any electronic devices, and when tools or maintenance devices may easily make
contact with an uncovered electronic terminal, please make sure to turn the ignition switch to the LOCK
position, and then disconnect the battery's negative cable to avoid injury or vehicle damage. When the
ignition switch is on the ON position, please do not disconnect the battery's connecting wire or take out
the power's fuse, regardless if the engine is running or not.Otherwise it would seriously damage the
ECU and related microelectronic devices such as sensors.
2. When changing the fuse, please make sure that the new fuse possesses the proper current rating,
and is not above or below this rating.
3. When repairing the wire harnesses of the airbag and pretensioner, only specified contact points,
plugs, and wires are allowed to be used.
4. Before repairing the wire harness, make sure to eliminate any factor that might cause damage,
for example, the edge of a vehicle body part is too sharp, or the used electronics are damaged or
corroded.
5. Shielded wire should not be repaired, it must be replaced entirely once it is damaged.
6. Unless it is specified during the test, please do not use an analog multimeter to test the ECU and
sensor, instead use a high-impedance digital multimeter (internal resistance should be ≥10 kΩ) or a
vehicle multimeter for inspection.
7. When inspecting the connector with a digital multimeter, take the waterproof rubber cover off the
connector, and tightly insert the test pen along the connecting terminal. Don't use too much force, as
to avoid cracking the connector.
Circuit inspection steps
The principle of troubleshooting is to confirm the "possible cause". Once the possible cause is confirmed, the
components that need to be inspected are limited to the components that are related to the possible cause. The
confirmed possible cause should be based on theory and be supported by facts, but not just by intuition. If
one tries to solve the problem but does not adopt the proper troubleshooting steps, it may make the problem
worse. Then the possible cause not only can't be confirmed, but also maintenance can't be performed properly.
Troubleshooting should adhere to the four steps below:
1. Observe the symptoms carefully, inspect if there is anything else abnormal, and record it.
2. While confirming the possible causes, study the circuit diagram carefully, and regard it as a whole
system in order to understand the circuit. Thorough knowledge of switches, relays, and other
electronic components is obligatory for proper analysis.
3. Inspect and eliminate the problems one by one until the cause is found.
4. After the malfunction is fixed, make sure to check if the inspected system is working properly, and also
check if the maintenance may have caused any new problems.
Compres-
sor relay
Reserve
Sunroof (Elite) Lamplet
Reserve
Reserve
Reserve
Reserve Door and window Reserve Blower
Lamplet
relay Flasher relay Blower high
speed relay (Elite) Door and
window relay (Comfort, Luxury) Blower relay
Reserve
Front fog lamp
Combination
meter
Interior
lighting
central
door lock
brake lamp
CD player
Reserve
Reserve
Reserve
Cigarette
lighter
Rearview
mirror
Front wiper
Charge
Airbag
Reserve
Reverse lamp Rear fog lamp
Rear wiper
Defroster Compressor
ACC relay
IG relayRear wiper
relay Defroster
relay
Front fog
lamp relay Rear fog
lamp relay
Warning lamp
Turn signal lamp
Cab No.1 fuse box
Fuse Box
Page 152 of 281
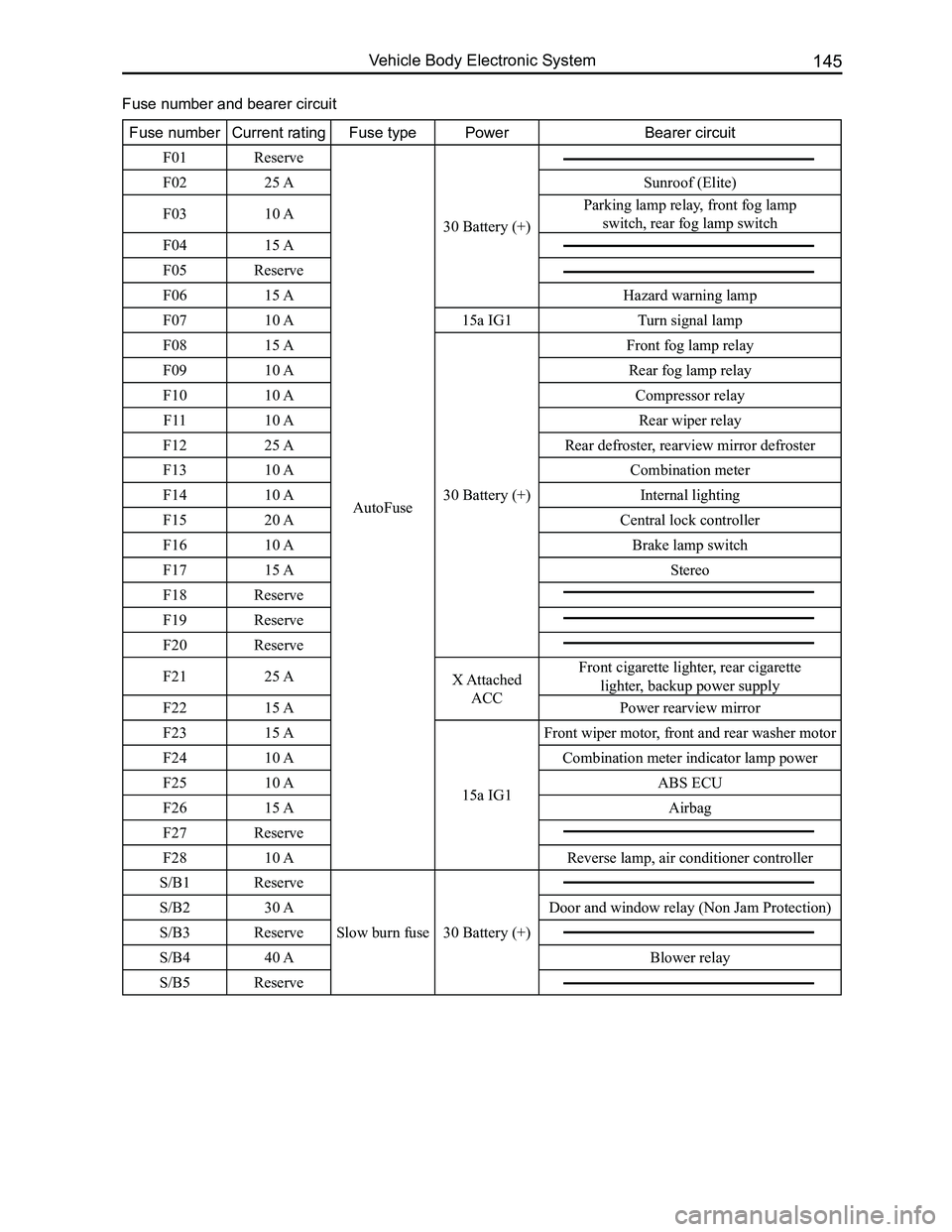
Downloaded from www.Manualslib.com manuals search engine 145Vehicle Body Electronic System
Fuse numberCurrent ratingFuse typePowerBearer circuit
F01Reserve
AutoFuse
30 Battery (+)
F0225 ASunroof (Elite)
F0310 AParking lamp relay, front fog lamp
switch, rear fog lamp switch
F0415 A
F05Reserve
F0615 AHazard warning lamp
F0710 A15a IG1 Turn signal lamp
F0815 A
30 Battery (+)
Front fog lamp relay
F0910 ARear fog lamp relay
F1010 ACompressor relay
F1110 ARear wiper relay
F1225 ARear defroster, rearview mirror defroster
F1310 ACombination meter
F1410 AInternal lighting
F1520 ACentral lock controller
F1610 ABrake lamp switch
F1715 AStereo
F18Reserve
F19Reserve
F20Reserve
F2125 AX Attached
ACC
Front cigarette lighter, rear cigarette
lighter, backup power supply
F2215 APower rearview mirror
F2315 A
15a IG1
Front wiper motor, front and rear washer motor
F2410 ACombination meter indicator lamp power
F2510 AABS ECU
F2615 AAirbag
F27Reserve
F2810 AReverse lamp, air conditioner controller
S/B1Reserve
Slow burn fuse 30 Battery (+)
S/B230 ADoor and window relay (Non Jam Protection)
S/B3Reserve
S/B440 ABlower relay
S/B5Reserve
Fuse number and bearer circuit